电子装联工艺技术课件
合集下载
电子装联工艺技术

引线成形一般应有专用工具或设备完成。SMD引线成形必 须由专用工装完成;
保持一定的弯曲半径,以消除应力影响; 保持元器件本体或熔接点到弯曲点的最小距离至少为2倍
的引线直径或厚度,但不得小于0.75mm。 引线成形后的尺寸与PCB安装孔孔距相匹配; 引线直径大于1.3mm时,一般不可弯曲成形,小于1.3mm的硬引线(回火处
3.1 元器件通孔插装(THT)
3.1.2 安装次序 先低后高、先轻后重、先非敏感元器件后敏感元件、先
表面安装后通孔插装、先分立元器件后集成电路。
3.1 元器件通孔插装(THT)
3.1.3安装要求 安装高度要符合产品防震、绝缘、散热等要求及设计文件要求; 元器件加固要求:7g、3.5g及设计工艺文件的规定; 接线端子、铆钉不应作界面或层间连接用,导通孔(金属化孔)不能安装元器件; 一孔一线,孔径与引线直径的合理间隙(0.2~0.4mm) 空心铆钉不能用于电气连接; 元器件之间有至少为1.6mm的安全间距; 元器件安装后,引线伸出板面的长度应为1.5±0.8mm; 元器件安装后,引线端头采用弯曲连接时,引线弯曲长度为3.5 ~5.5d; 如底面无裸露的电路(印制导线);元件可贴板安装(玻璃二极管除外),如底面有裸露电路,
2.2 元器件引线搪锡工艺
锡和锡铅合金为最佳的可焊性镀层,其厚度
为5~7μm。 镀金引线的搪锡(除金):
Cu μm/s
金镀层是抗氧化性很强的镀层,与SnPb焊料
Ag Au
7
有很好的润湿性,但直接焊接金镀层时,
6
Pb
5
SnPb合金对金镀层产生强烈的溶解作用,金
4
Pt 3
与焊料中的Sn金属结合生成AuSn4合金,枝晶 2
对于表面贴装元器件,不管金层厚度为多少,在焊接前,应去除至少95% 被焊表面的金层;
保持一定的弯曲半径,以消除应力影响; 保持元器件本体或熔接点到弯曲点的最小距离至少为2倍
的引线直径或厚度,但不得小于0.75mm。 引线成形后的尺寸与PCB安装孔孔距相匹配; 引线直径大于1.3mm时,一般不可弯曲成形,小于1.3mm的硬引线(回火处
3.1 元器件通孔插装(THT)
3.1.2 安装次序 先低后高、先轻后重、先非敏感元器件后敏感元件、先
表面安装后通孔插装、先分立元器件后集成电路。
3.1 元器件通孔插装(THT)
3.1.3安装要求 安装高度要符合产品防震、绝缘、散热等要求及设计文件要求; 元器件加固要求:7g、3.5g及设计工艺文件的规定; 接线端子、铆钉不应作界面或层间连接用,导通孔(金属化孔)不能安装元器件; 一孔一线,孔径与引线直径的合理间隙(0.2~0.4mm) 空心铆钉不能用于电气连接; 元器件之间有至少为1.6mm的安全间距; 元器件安装后,引线伸出板面的长度应为1.5±0.8mm; 元器件安装后,引线端头采用弯曲连接时,引线弯曲长度为3.5 ~5.5d; 如底面无裸露的电路(印制导线);元件可贴板安装(玻璃二极管除外),如底面有裸露电路,
2.2 元器件引线搪锡工艺
锡和锡铅合金为最佳的可焊性镀层,其厚度
为5~7μm。 镀金引线的搪锡(除金):
Cu μm/s
金镀层是抗氧化性很强的镀层,与SnPb焊料
Ag Au
7
有很好的润湿性,但直接焊接金镀层时,
6
Pb
5
SnPb合金对金镀层产生强烈的溶解作用,金
4
Pt 3
与焊料中的Sn金属结合生成AuSn4合金,枝晶 2
对于表面贴装元器件,不管金层厚度为多少,在焊接前,应去除至少95% 被焊表面的金层;
电装工艺ppt.

≥5
≤45°
≥5
R≥2
≤45°
(a)
三极管及圆形外壳引线成形基本要求 (a) 三极管;(b) 圆形外壳集成电路
(b)
元器件成型应考虑以下几点: 1)造型精致、美观。 2)元器件引线开始弯曲处距元件体至少3mm。 3)元器件的弯曲半径应为引线直径的二倍。 如 图所示:
这几种在元器件引线的弯曲形状中, 图(a)比较简单,适合于手工装配;
B≥5 mm R≥2 d
B B
贴板安装
d
悬空安装:其安装形式如图所示,它适用于发热 元件的安装。元器件距印制基板面要有一定的距离, 安装距离一般为3~8 mm。
A≥5 mm
A
A
45°
45°
悬空安装
垂直安装:其安装形式如图所示,它适用于安装密度较 高的场合。元器件垂直于印制基板面,但大质量细引线的元器 件不宜采用这种形式。 埋头安装:其安装形式如图所示。这种方式可提高元器件 防震能力,降低安装高度。由于元器件的壳体埋于印制基板的 嵌入孔内,因此又称为嵌入式安装。
所谓元器件的处理就是将元器件引线的氧 化膜及污物去掉,然后镀上一层锡。 作法:
用钢锯条或镊子等刮元器件引线。使其露 出原金属本色,引线全刮完后涂助焊剂。一手 用镊子夹住引线,一手执烙铁镀锡。操作时用 电烙铁沾饱焊锡,并用它将被镀锡的元件引脚 压在松香块上,待松香融化后将元器件引脚从 烙铁头与松香之间慢慢抽出,抽出时引脚一定 要在融化的焊锡包裹之中。注意时间不可过长, 并用镊子帮助散热。也可用锡锅浸锡。
对于设计稳定,大批量生产的产品,印制 板装配工作量大,宜采用流水线装配。这种方 式可大大提高生产效率,减少差错,提高产品 合格率。 流水操作是把一次复杂的工作分成若干道 简单的工序,每个操作者在规定的时间内完成 指定的工作量(一般限定每人约6个元器件插件 的工作量)。 每拍元件 ( 约 6 个 ) 插入→全部元器件插入 →一次性切割引线→一次性锡焊→检查。 引线切割一般用专用设备 ——割头机一次 切割完成,锡焊通常用波峰焊机完成。
《电子技术工艺基础》课件:连接工艺
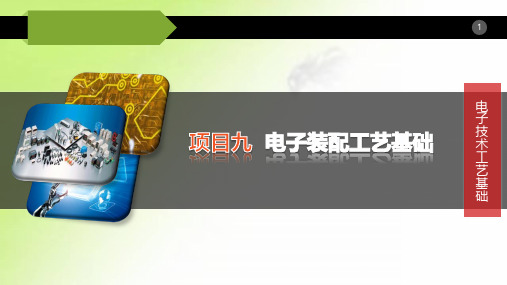
(1)环氧树脂胶:具有耐热、耐水、耐油、不燃烧、剪切强度好的特点。适合于各类金 属、钢材、玻璃和胶木等的胶接。环氧树脂胶由环氧树脂和固化剂组成,存放时应分开放置, 使用时按一定比例将它们充分混合后,即可进行黏接。
知识5 连接工艺
21
(2)环氧快干胶(914):具有黏合强度高、 耐热、耐水和室温快干的特点。适用于木材、陶 瓷、玻璃、胶木和金属等材料的胶接,但不能黏 接聚烯烃类塑料。
知识5 连接工艺
22
(5)101胶(乌利当胶):具有耐水、耐稀 酸、耐油脂以及黏合性好和绝缘性好的特点。 适用于陶瓷、橡胶、皮革、木材、塑料、金属 等的胶接。101胶分为甲、乙两组,使用时要将 两组胶液混合并搅拌均匀。但要注意对于不同 的胶合件,其配比是不相同的。
(6)氯丁-酚醛胶(通常称为88号胶):适 用于橡胶与金属、橡胶与玻璃、橡胶与橡胶、 橡胶与木材等的胶接。使用时,可用乙酸乙酯 和汽油的混合液进行稀释(重量比为2∶1), 黏接施压,在室温下24小时后才能去掉加压器, 然后在同样的室温条件下干燥24小时即可。
公制螺纹按其螺牙的粗细,可分为粗牙螺纹和细牙 螺纹;按螺纹的旋转方向的不同,可分为左旋螺纹和右 旋螺纹。最常用的是右旋粗牙螺纹。 螺纹规格按公制表示。例如,M3、M4、M5、M6分别 表示直径为3 mm、4 mm、5 mm、6 mm的普通螺纹,字 母“M”表示普通螺纹。
知识5 连接工艺
12
3. 螺纹连接时的防松动方法
( 5)被紧固件如果全是金属部件可采用钢性垫圈;如 果是胶木及易碎件可采用软性垫圈。
(6)使用弹簧垫圈时,其四周均要被螺母压住、压平。
知识5 连接工艺
15
二、 铆接
1、 铆接的概念 用铆钉将零部件连接起来的过程就称作铆接。铆接后的零部件是不可拆卸的。
知识5 连接工艺
21
(2)环氧快干胶(914):具有黏合强度高、 耐热、耐水和室温快干的特点。适用于木材、陶 瓷、玻璃、胶木和金属等材料的胶接,但不能黏 接聚烯烃类塑料。
知识5 连接工艺
22
(5)101胶(乌利当胶):具有耐水、耐稀 酸、耐油脂以及黏合性好和绝缘性好的特点。 适用于陶瓷、橡胶、皮革、木材、塑料、金属 等的胶接。101胶分为甲、乙两组,使用时要将 两组胶液混合并搅拌均匀。但要注意对于不同 的胶合件,其配比是不相同的。
(6)氯丁-酚醛胶(通常称为88号胶):适 用于橡胶与金属、橡胶与玻璃、橡胶与橡胶、 橡胶与木材等的胶接。使用时,可用乙酸乙酯 和汽油的混合液进行稀释(重量比为2∶1), 黏接施压,在室温下24小时后才能去掉加压器, 然后在同样的室温条件下干燥24小时即可。
公制螺纹按其螺牙的粗细,可分为粗牙螺纹和细牙 螺纹;按螺纹的旋转方向的不同,可分为左旋螺纹和右 旋螺纹。最常用的是右旋粗牙螺纹。 螺纹规格按公制表示。例如,M3、M4、M5、M6分别 表示直径为3 mm、4 mm、5 mm、6 mm的普通螺纹,字 母“M”表示普通螺纹。
知识5 连接工艺
12
3. 螺纹连接时的防松动方法
( 5)被紧固件如果全是金属部件可采用钢性垫圈;如 果是胶木及易碎件可采用软性垫圈。
(6)使用弹簧垫圈时,其四周均要被螺母压住、压平。
知识5 连接工艺
15
二、 铆接
1、 铆接的概念 用铆钉将零部件连接起来的过程就称作铆接。铆接后的零部件是不可拆卸的。
电子产品装配工艺培训教材(PPT 58页)

第 5章
本章要点
电子产品装配工艺
能描述电子产品组装内容、级别、特点及其发展 能掌握电路板组装方式、整机组装过程 能描述整机连接方式与整机质检内容 会熟练加工与安装元器件 会熟练组装HX108-2型收音机电路板 会熟练装配HX108-2型收音机整机
电子工艺与技能实训教程
- 1-
第 5章
电子产品装配工艺
6.1 组装基础 电子设备的组装是将各种电子元器件、机电元件以及结构件,按照设计 要求,装接在规定的位置上,组成具有一定功能的完整的电子产品的 过程。 6.1.1 组装内容与级别 1 .电子设备组装内容 电子设备的组装内容主要有: 1)单元电路的划分。 2)元器件的布局。 3)各种元件、部件、结构件的安装。 4)整机联装。 2 .电子设备组装级别 在组装过程中,根据组装单位的大小、尺寸、复杂程度和特点的不同, 将电子设备的组装分成不同的等级。电子设备的组装级别如表所示。
Ω
Ω
×1
K
×1
K
IN4148 电子工艺与技能实训教程
IN4148
-22-
第 5章
电子产品装配工艺
区分电容的极性判别如图所示:
根据反接时漏电流小(阻值大),正接时 漏电流大来判断。 +
-
+ 电子工艺与技能实训教程
-+
长 短
-23-
第 5章
电位器阻值的测量
电子产品装配工艺
转动旋钮,1与2, 2与3 间的阻值 应随之改变
大约1- 2 mm
电子工艺与技能实训教程
镊子
-27-
第 5章
元 件 脚 的 弯 制 成
电子产品装配工艺
形 2
立式插法的 元件只要弯 一边
别太短
本章要点
电子产品装配工艺
能描述电子产品组装内容、级别、特点及其发展 能掌握电路板组装方式、整机组装过程 能描述整机连接方式与整机质检内容 会熟练加工与安装元器件 会熟练组装HX108-2型收音机电路板 会熟练装配HX108-2型收音机整机
电子工艺与技能实训教程
- 1-
第 5章
电子产品装配工艺
6.1 组装基础 电子设备的组装是将各种电子元器件、机电元件以及结构件,按照设计 要求,装接在规定的位置上,组成具有一定功能的完整的电子产品的 过程。 6.1.1 组装内容与级别 1 .电子设备组装内容 电子设备的组装内容主要有: 1)单元电路的划分。 2)元器件的布局。 3)各种元件、部件、结构件的安装。 4)整机联装。 2 .电子设备组装级别 在组装过程中,根据组装单位的大小、尺寸、复杂程度和特点的不同, 将电子设备的组装分成不同的等级。电子设备的组装级别如表所示。
Ω
Ω
×1
K
×1
K
IN4148 电子工艺与技能实训教程
IN4148
-22-
第 5章
电子产品装配工艺
区分电容的极性判别如图所示:
根据反接时漏电流小(阻值大),正接时 漏电流大来判断。 +
-
+ 电子工艺与技能实训教程
-+
长 短
-23-
第 5章
电位器阻值的测量
电子产品装配工艺
转动旋钮,1与2, 2与3 间的阻值 应随之改变
大约1- 2 mm
电子工艺与技能实训教程
镊子
-27-
第 5章
元 件 脚 的 弯 制 成
电子产品装配工艺
形 2
立式插法的 元件只要弯 一边
别太短
电子装联技术讲义---杨松林

2、电缆装配技术介绍
2、电缆装配技术介绍
2.1.2、常用的射频电缆以外导体来划分可分为半刚、 半柔、柔性三大类。 2.1.2.1、半刚性电缆:外导体多为无缝紫铜管,内导
体为铜包钢镀银线,在内导体与外导体之间是实芯或
包绕聚四氟乙烯介质,常用的半刚性电缆有:SFT50-3、SFT-50-2;
2、电缆装配技术介绍
2、电缆装配技术介绍
⑥按图4装外壳(1),将衬管(6)旋入外壳用专用扳手扳紧。 ⑦标牌按图要求作标记,安装在距插头尾端30mm处。
图4.
2、电缆装配技术介绍
(3) TNC插头装配工艺(插头TNC-J3,电缆SYV-50-2-1) 同BNC装配工艺相同,唯一区别就是插头外壳的连接形式不一样! (4)N型插头装配工艺(插头N-J5,电缆SYV-50-3) 同BNC装配工艺剥头尺寸存在一定差异,如下:
2、电缆装配技术介绍
2.1.3、射频电缆主要有以下几个参数: (4)相位稳定性:相位稳定性一般是指电缆在弯曲 时相位的变化情况,一般来说电缆弯曲半径越小或 弯曲次数越多,相位变化越大。同时传输信号频率、 电缆介质形式都会对电缆的相位稳定性产生影响。 (5)插损:是衡量电缆信号传输效率的一个重要指 标。同轴电缆的插损是同轴电缆在信号传输时的介 质损耗、外导体损耗、内导体损耗之和。 (6)驻波:驻波通常用电压驻波比(VSWR)来表 征。同时驻波也是表征回波损耗的一个物理量。
④以接地套(2)端面为基准,保留芯线绝缘层0.4mm,剥去其余 的绝缘层(不得损伤芯线),保证芯线长度为4mm,芯线浸锡并用 无水乙醇纱布清洗(参见图4)。 ⑤将插芯(8)焊接孔内用烙铁浸入少量焊锡,插芯(8)插入绝缘 子(7)内再插入芯线进行焊接,焊后用无水乙醇、纱布进行清洗, 要求插芯外表面平滑光洁、无锡锡瘤,插芯焊接良好,无虚焊,多 余的焊锡可用刀片刮去。
电子装联工艺

什么是SMA? 什么是SMA? SMA
一、表面组装工艺
Surface mount
Through-hole
高密度 高可靠 与通孔组装工艺相比SMA的特点: 与通孔组装工艺相比SMA的特点: SMA的特点 低成本 小型化 生产的自动化
一、表面组装工艺
■表面组装基本工艺流程
单面贴装——再流焊工艺 ▲单面贴装 再流焊工艺 印刷焊膏 表面贴装 再流焊 清洗
一、表面组装工艺
▲立碑 又称之为吊桥、曼哈顿和墓 又称之为吊桥、 碑,矩形片式元件的一端焊接在 焊盘上,而另一端则翘立, 焊盘上,而另一端则翘立,这种 现象就称为曼哈顿现象。 现象就称为曼哈顿现象。引起该 种现象主要原因是元件两端受热 不均匀,焊膏熔化有先后所致。 不均匀,焊膏熔化有先后所致。
一、表面组装工艺
▲单面贴片——波峰焊工艺 单面贴片——波峰焊工艺 点胶 波峰焊 表面贴装 固化
翻转
插装
清洗
一、表面组装工艺
▲混合安装工艺
翻转
印刷焊膏 表面贴装 固化
翻转
再流焊 插装
点胶
表面贴装
波峰焊
清洗
双面贴片—再流焊工艺 ▲双面贴片 再流焊工艺 印刷焊膏 表面贴装 再流焊 清洗 再流焊
翻转
印刷焊膏 表面贴装
一、表面组装工艺
▲刮刀压力 刮刀的压力对印刷质量影响很大,压力太小, 刮刀的压力对印刷质量影响很大,压力太小,则Y方向 的力也小,则漏进窗口的锡膏量少,PCB上锡膏量不足 上锡膏量不足, 的力也小,则漏进窗口的锡膏量少,PCB上锡膏量不足,太 大的压力,则导致锡膏印得太薄。一般把刮刀的压力, 大的压力,则导致锡膏印得太薄。一般把刮刀的压力,设定 0.5kg/25mm 在0.5kg/25mm 。
电子部件装配工艺培训课件(PPT 40张)
第八章
精 品 课
电子部件装配工艺
1
电子部件装配工艺
部件装配可分为:功能部件装配和辅 助部件装配。 部件装配采用的连接工艺有:插装、 贴装(片式组件表面安装)、铆装、螺 装、胶接、焊接和无锡焊接等工艺。
精 品 课
电子部件是由材料、零件、元器件 等装配组成的具有一定功能的可拆卸或 不可拆卸的产品,部件装配质量的好坏, 直接影响电子整机装配质量。因此,部 件装配是电子整机装配的一个重要环节。
14
8.1
印制电路板的组装工艺
精 品 课
(6)为了保证整机用电安全,插件时须注 意保持元器件间的最小放电距离,插装的元 器件不能有严重歪斜,以防止元器件之间因 接触而引起的各种短路和高压放电现象,一 般元器件安装高度和倾斜范围如图8.4所示 (单位:mm)。
(7)插装玻璃壳体的二极管时,最好 先将引线绕1~2圈,形成螺旋形以增加 留线长度如图8.5所示.,不宜紧靠根部 弯折,以免受力破裂损坏。
9
8.1
印制电路板的组装工艺
印制电路板机器自动插装 为了提高元器件插件速度、改善插件质量、 减轻操作人员的劳动强度、提高生产效率和产 品质量,印制电路板的组装流水线采用自动装 配机。 自动插装过程中,印制电路板的传递、 插装、检测等工序,都是由计算机按程序进行 控制。
精 品 课
10
8.1
印制电路板的组装工艺
精 品 课
编辑编带 程序
编织插件 料带
自动检 测
检查补 焊
波峰自 动焊
插件检 验
手工插件流 水线 装散热 器
图8.2 自动插装工艺 流程
5
8.1
印制电路板的组装工艺
精 品 课
2.印制电路板组装工艺的基本要求 (1)各个工艺环节必须严格实施工艺文件的规 定,认真按照工艺指导卡操作。 (2)印制电路板应使用阻燃性材料,以满足安 全使用性能要求。 (3)组装流水线各工序的设置要均匀,防止某 些工序组装件积压,确保均衡生产。 (4)印制电路板元器件的插装(或贴装)要正 确,不能有错装、漏装现象。 (5)焊点应光滑无拉尖、无虚焊、假焊、连焊 等不良现象,使组装的印制电路板的各种功能符合 电路的性能指标要求,为整机总装打下良好的基础。
精 品 课
电子部件装配工艺
1
电子部件装配工艺
部件装配可分为:功能部件装配和辅 助部件装配。 部件装配采用的连接工艺有:插装、 贴装(片式组件表面安装)、铆装、螺 装、胶接、焊接和无锡焊接等工艺。
精 品 课
电子部件是由材料、零件、元器件 等装配组成的具有一定功能的可拆卸或 不可拆卸的产品,部件装配质量的好坏, 直接影响电子整机装配质量。因此,部 件装配是电子整机装配的一个重要环节。
14
8.1
印制电路板的组装工艺
精 品 课
(6)为了保证整机用电安全,插件时须注 意保持元器件间的最小放电距离,插装的元 器件不能有严重歪斜,以防止元器件之间因 接触而引起的各种短路和高压放电现象,一 般元器件安装高度和倾斜范围如图8.4所示 (单位:mm)。
(7)插装玻璃壳体的二极管时,最好 先将引线绕1~2圈,形成螺旋形以增加 留线长度如图8.5所示.,不宜紧靠根部 弯折,以免受力破裂损坏。
9
8.1
印制电路板的组装工艺
印制电路板机器自动插装 为了提高元器件插件速度、改善插件质量、 减轻操作人员的劳动强度、提高生产效率和产 品质量,印制电路板的组装流水线采用自动装 配机。 自动插装过程中,印制电路板的传递、 插装、检测等工序,都是由计算机按程序进行 控制。
精 品 课
10
8.1
印制电路板的组装工艺
精 品 课
编辑编带 程序
编织插件 料带
自动检 测
检查补 焊
波峰自 动焊
插件检 验
手工插件流 水线 装散热 器
图8.2 自动插装工艺 流程
5
8.1
印制电路板的组装工艺
精 品 课
2.印制电路板组装工艺的基本要求 (1)各个工艺环节必须严格实施工艺文件的规 定,认真按照工艺指导卡操作。 (2)印制电路板应使用阻燃性材料,以满足安 全使用性能要求。 (3)组装流水线各工序的设置要均匀,防止某 些工序组装件积压,确保均衡生产。 (4)印制电路板元器件的插装(或贴装)要正 确,不能有错装、漏装现象。 (5)焊点应光滑无拉尖、无虚焊、假焊、连焊 等不良现象,使组装的印制电路板的各种功能符合 电路的性能指标要求,为整机总装打下良好的基础。
第5章电子产品装连工艺共41页PPT
奢侈是舒适的,否则就不是奢侈 。——CocoCha nel 62、少而好学,如日出之阳;壮而好学 ,如日 中之光 ;志而 好学, 如炳烛 之光。 ——刘 向 63、三军可夺帅也,匹夫不可夺志也。 ——孔 丘 64、人生就是学校。在那里,与其说好 的教师 是幸福 ,不如 说好的 教师是 不幸。 ——海 贝尔 65、接受挑战,就可以享受胜利的喜悦 。——杰纳勒 尔·乔治·S·巴顿
谢谢!
第5章电子产品装连工艺
11、用道德的示范来造就一个人,显然比用法律来约束他更有价值。—— 希腊
12、法律是无私的,对谁都一视同仁。在每件事上,她都不徇私情。—— 托马斯
13、公正的法律限制不了好的自由,因为好人不会去做法律不允许的事 情。——弗劳德
14、法律是为了保护无辜而制定的。——爱略特 15、像房子一样,法律和法律都是相互依存的。——伯克
谢谢!
第5章电子产品装连工艺
11、用道德的示范来造就一个人,显然比用法律来约束他更有价值。—— 希腊
12、法律是无私的,对谁都一视同仁。在每件事上,她都不徇私情。—— 托马斯
13、公正的法律限制不了好的自由,因为好人不会去做法律不允许的事 情。——弗劳德
14、法律是为了保护无辜而制定的。——爱略特 15、像房子一样,法律和法律都是相互依存的。——伯克
电子产品装配工艺(PPT58页).ppt
1电子工艺与技能实训教程电子工艺与技能实训教程
-11-
第5章 电子产品装配工艺
(1)自动插装工艺 自动插装工艺过程框图如图所示。
(2)自动装配对元器件的工艺要求 自动装配与手工装配不一样,自动装配是由装配机自动完成器件的插装 。
1电子工艺与技能实训教程电子工艺与技能实训教程
-12-
第5章 电子产品装配工艺
后盖
TUNING VOLUME
1电子工艺与技能实训教程电子工艺与技能实训教程
-21-
第5章 电子产品装配工艺
(2)元器件检测 通过500A型指针万用表、DT-890型数字万用表、YY2810型LCR数字电 桥等设备完成对元器件的检测,具体方法请参阅第1章。二极管极性判别 如下图所示:来自ΩΩ×1
×1
K
1电子工艺与技能实训教程电子工艺与技能实训教程
-25-
第5章 电子产品装配工艺
(4)元器件整形、安装与焊接 清除元件表面的氧化层:左手捏住电阻或其他元件的本体,右手用锯条
轻刮元件脚的表面,左手慢慢地转动,直到表面氧化层全部去除
1电子工艺与技能实训教程电子工艺与技能实训教程
-26-
第5章 电子产品装配工艺
R11 1k 棕黑红 R12 220Ω红红棕 R13 24k 红黄橙
1电子工艺与技能实训教程电子工艺与技能实训教程
-14-
第5章 电子产品装配工艺
二极管
IN4148
3个
电解电容
100μF
2个
+- +-
电位器 1个
4.7μF
2个
1电子工艺与技能实训教程电子工艺与技能实训教程
-15-
第5章 电子产品装配工艺 连接线 Lines 4根
电子装联工艺教程-unit4
目标一1,2,3级
连接器与板面紧贴手齐。 连接器引脚的针肩支撑于焊盘上,管
腿伸出焊盘的长度符合标准的规定。
如果需要,定位销要完全的插入/扣住
PCB板。
2004-7-6
SIPIVT
引脚的成形
5.3.1 引脚的成形-弯曲
可接受一1,2,3级
安装在镀通孔中的元件,从器件
的本体、球状连接部分或引脚焊 接部分到器件引脚折弯处的距 离,至少相当于一个引脚的直径 或厚度或0.8毫米中的较大者。
焊接
引脚凸出-1
制程警示一2级(非支撑孔) 缺陷一3级(非支撑孔) 引脚延伸不满足引脚固定角最小 45”的要求。 缺陷一1,2,3级(非支撑孔) 引脚凸出小于0.5毫米[0.020英寸]。 引脚凸出违反允许的最小电气间隙。
2004-7-6
SIPIVT
可接受一1,2,3级 引脚伸出焊盘在最大和最小允 许范围(L)之内 表6—l),且未违反允许的最小电 气间隙。 制程警示一 2级(支撑孔) 缺陷一3级(支撑孔) 引脚凸出不满足表6-1的要 求。 缺陷一1,2,3级(支撑孔) 引脚凸出违反允许的最小电气 间隙。
5.2.4安装-垂直-轴向引脚-支撑孔
目标一1,2,3级 元器件本体到焊盘之间的距离(H)大 于0.4毫米,小于1.5毫米。 元器件与板面垂直。 元器件的总高度不超过规定的范围.。
2004-7-6
SIPIVT
2 轴向元件-垂直- 安装-
5.2.4安装-垂直-轴向引脚-支撑孔
可接受一1,2,3级 元器件本体与板面的间隙符合表5-l的 规定。 元器件引腿的倾斜角度()满足最小电 气间隙要求。
SIPIVT
AXIAL元件垂直定位 (5.1.2 定位-垂直)
连接器与板面紧贴手齐。 连接器引脚的针肩支撑于焊盘上,管
腿伸出焊盘的长度符合标准的规定。
如果需要,定位销要完全的插入/扣住
PCB板。
2004-7-6
SIPIVT
引脚的成形
5.3.1 引脚的成形-弯曲
可接受一1,2,3级
安装在镀通孔中的元件,从器件
的本体、球状连接部分或引脚焊 接部分到器件引脚折弯处的距 离,至少相当于一个引脚的直径 或厚度或0.8毫米中的较大者。
焊接
引脚凸出-1
制程警示一2级(非支撑孔) 缺陷一3级(非支撑孔) 引脚延伸不满足引脚固定角最小 45”的要求。 缺陷一1,2,3级(非支撑孔) 引脚凸出小于0.5毫米[0.020英寸]。 引脚凸出违反允许的最小电气间隙。
2004-7-6
SIPIVT
可接受一1,2,3级 引脚伸出焊盘在最大和最小允 许范围(L)之内 表6—l),且未违反允许的最小电 气间隙。 制程警示一 2级(支撑孔) 缺陷一3级(支撑孔) 引脚凸出不满足表6-1的要 求。 缺陷一1,2,3级(支撑孔) 引脚凸出违反允许的最小电气 间隙。
5.2.4安装-垂直-轴向引脚-支撑孔
目标一1,2,3级 元器件本体到焊盘之间的距离(H)大 于0.4毫米,小于1.5毫米。 元器件与板面垂直。 元器件的总高度不超过规定的范围.。
2004-7-6
SIPIVT
2 轴向元件-垂直- 安装-
5.2.4安装-垂直-轴向引脚-支撑孔
可接受一1,2,3级 元器件本体与板面的间隙符合表5-l的 规定。 元器件引腿的倾斜角度()满足最小电 气间隙要求。
SIPIVT
AXIAL元件垂直定位 (5.1.2 定位-垂直)
- 1、下载文档前请自行甄别文档内容的完整性,平台不提供额外的编辑、内容补充、找答案等附加服务。
- 2、"仅部分预览"的文档,不可在线预览部分如存在完整性等问题,可反馈申请退款(可完整预览的文档不适用该条件!)。
- 3、如文档侵犯您的权益,请联系客服反馈,我们会尽快为您处理(人工客服工作时间:9:00-18:30)。
3.1 元器件通孔插装(THT)
3.1.1 安装原则
元器件在PCB上安装的形式多样,但都必须符合产品质量和可靠性要求,遵守有关原则:
元器件安装应满足产品力学和气候环境条件的要求; 疏密均匀、排列整齐、不允许立体交叉和重叠; 轴向引线元器件必须平行于板面安装,非轴向引线的元器件原则上不得水平安装; 金属壳体元器件应能与相邻印制导线和导体元器件绝缘。 元器件之间要保持合理的安全间隙或套套管; 大质量元器件的加固; 大功率元器件的散热和悬空安装; 热敏元器件安装,应远离发热元件或隔热措施; 静电敏感元器件安装,采取防静电措施; 元器件安装后,不得挡住其它元器件引线,以便于拆装、清洗;
小型,超小型器件的出现和推广应用,促进了高密度组装技术的发展,也模糊了一 级封
装和二级组装之间的界限。同时对电子产品的设计、组装工艺、组装设备等提出了更新 更高的要求。
1.2 电子产品的分级
按IPC-STD-001“电子电气组装件焊接要求”标准规定,根据产品最终使用条 件进行分级。
1级(通用电子产品):指组装完整,以满足使用功能主要要求的产品。 2级(专用服务类电子产品):该产品具有持续的性能和持久的寿命。需要不 间断的服务,但不是主要的。通常在最终使用环境下使用不会失效。 3级(高性能电子产品):指具有持续的高性能或能严格按指令运行的设备和 产品,不允许停歇,最终使用环境异常苛刻。需要时产品必须有效,例如生 命救治和其它关键的设备系统。
配合的唯一性。
热剥工艺造成的绝缘层变色是允许的,但不应烧焦发黑。 化学剥除绝缘层仅适用于单股实芯导线的端头处理,处理后应立即进行中和、 清洗;
屏蔽导线屏蔽层的处理应符合产品技术要求,处理方法应符合有关标准的要求。
2.6 PCB组装前的预处理
PCB的复验
组装前要求
3 印制电路板组装工艺
3.2 元器件表面安装(SMT)
3.2.4 焊膏 焊膏的技术要求
焊膏的成分符合国家标准的要求(GJB3243 5.3.2.2条) 在储存期内焊膏的性能保持不变 焊膏中金属颗粒与焊剂不分层 室温下连续印刷时,焊膏不易干燥,印刷性好 焊膏粘度要保证印刷时具有良好的脱模性,又要保证良好的触变性,印刷后焊膏 不产生塌陷 严格控制金属微粉和金属氧化物焊料,避免焊接时随溶剂、气体挥发而飞溅,形 成锡珠 焊接时润湿性良好
3.2 元器件表面安装(SMT)
SMC 元器件 SMD 有铅焊膏 焊膏 贴装材料 贴片胶 基板材料 印制电路板 表 面 安 装 技 术 电路图形设 计 焊膏印刷 网板设计、制作 表面贴装 贴装工艺 表面贴装和通孔插装混合安装 波峰焊接 焊接工艺 手工焊接 再流焊接(红外再流焊,热风再流焊,汽相再流焊,激光再流焊等) 清洗技术 清洗剂 清洗工艺 检测技术:焊点质量检测,在线测试,功能测试 设备:印刷机,贴片机,再流焊炉,清洗设备,检测设备,维修设备 SMT设计 SMT管理:质量,生产,设备,工艺等 无铅焊膏
电子管时代 晶体管时代
表面安装
集成电路时代
微组装
表面安装时代
微组装时代
装联工艺技术的三次革命 通孔插装 器件封装技术的发展
电子产品的装联工艺是建立在器件封装形式变化的基础上,即一种新型器件的出现, 必
然会创新出一种新的装联技术和工艺,从而促进装联工艺技术的进步。 QFP BGA CSP(μBGA) DCA MCM ……
3.2 元器件表面安装(SMT)
焊膏的管理和使用
焊膏应储存在5~10℃的环境条件下 使用前必须经回温处理,常温下会温2 ~4h 使用前应充分搅拌 印刷后应及时完成焊接,根据焊膏厂商推荐参数,
一般情况下应在4h内完成焊接
3.2 元器件表面安装(SMT)
焊膏的成分
选购要求:
根据设计和工艺要求,选择元器件种类、尺寸和封装形式;
元器件包装形式适合贴装机自动贴装; 元器件焊端(引脚)应涂镀厚度不小于7.5μm的锡铅合金(Sn含量58~68%); 包装开封后在25±5℃,HR55~70%条件下,在存放48小时内焊接仍能满足焊接技 术要求; 元器件在40℃的清洗溶剂中,至少能承受4min的浸泡时间; 元器件能承受10个再流焊周期,每个周期为215℃,时间为60s,并能承受在 260 ℃ 的熔融焊料中10s的浸泡时间; 元器件引线歪斜度误差不大于0.8mm; 元器件引线共平面度误差不大于0.1mm。 无铅元器件镀层识别(IPC-1066) 湿敏器件的处理规定(IPC-020、IPC-033)
表面组装元器件
电路基板 组装设计
组装工艺
组装材料:粘接剂、焊料、焊剂、清洗剂等; 组装工艺:组装方式、组装工艺流程、焊接技术、检测技术等; 组装技术:涂覆技术、贴装技术、焊接技术、清洗技术、检测技术等; 组装设备:涂覆设备、贴装机、焊接机、清洗机、测试设备等; 组装生产线或系统组成、控制与管理等;
组装系统控制与管理
1.3 电子装联工艺的组成
随着电子技术的不断发展和新型元器件的不断出现,电子装联技术也在不断 变化和发展。
电子装联工艺的组成
电子装联工艺的质量控制
电子装联工艺的组成
电子装联质量控制
2 装联前的准备工艺
2.1 元器件引线的可焊性检查
可焊性是衡量元器件和PCB焊接部位是否可以顺利发生焊接过程的重要特征之一,是保证
印刷工艺 装联工艺
3.2 元器件表面安装(SMT)
3.2.2元器件(SMC/SMD)
基本要求:
外形适合自动化贴装要求; 尺寸、形状标准化,并具有良好的互换性; 元器件焊端和引脚的可焊性符合要求; 符合再流焊和波峰焊的耐高温焊接条件;
可承受有机溶剂的清洗;
3.2 元器件表面安装(SMT)
2.2 元器件引线搪锡工艺
锡和锡铅合金为最佳的可焊性镀层,其厚度 为5~7μm。
Cu
镀金引线的搪锡(除金): 金镀层是抗氧化性很强的镀层,与SnPb焊料 有很好的润湿性,但直接焊接金镀层时, SnPb合金对金镀层产生强烈的溶解作用,金 与焊料中的Sn金属结合生成AuSn4合金,枝晶
μm/s Ag Au 7 6 5 4 3 2 1 ℃ 0 200 300 400 500 Pt Ni 过直径10%的变形。 扁平封装器件(如QFP等)应先搪锡后成形。 成形不当或不符合要求时,原弯曲半径在1~2倍引线直径内,可以矫直后在原处再弯曲 一次。
2.5 导线端头处理工艺要求
导线端头绝缘层剥除应使用热控型剥线工具,限制使用机械(冷)剥 线工具。 采用机械剥线工具,应采用不可调钳口的精密剥线钳,并做到钳口与导线规格
状结构,其性能变脆,机械强度下降。为防
止金脆现象出现,镀金引线在焊接前必须经 过搪锡除金处理。
Sn-Pb焊料中各种金属的溶解速度
2.3 IPC-J-STD-001D对镀金引线除金的规定
对于具有2.5μm或更厚金层的通孔元件引线,在焊接前,应去除至少95%被 焊表面的金层; 对于表面贴装元器件,不管金层厚度为多少,在焊接前,应去除至少95% 被焊表面的金层; 针对镀金层厚度大于或等于有2.5μm的元器件,可采用二次搪锡工艺或波峰 焊接工艺去除焊接端头表面的金层。 针对采用化学浸镍金(ENIG)工艺的印制板,印制板表面镀金层可免除除 金要求。
1 概述
电子产品装联工艺是指用规定的电子元器件和零、部(组)经过电子 及机械的装配和连接,使电子产品满足设计任务书要求的工艺技术。 因此,没有一整套较为先进成熟的、可操作性的电子装联工艺技术, 是不可能保证电子装联的高质量和电子产品的可靠性。
1.1 电子装联工艺技术的发展概况
装联工艺的发展阶段
3.2 元器件表面安装(SMT)
3.2.3印制电路板(PCB)
PCB基材一般选用FR4环氧玻璃纤维板,或FR4改性、FR5板; 板面平整度好,翘曲度≤0.75%,安装陶瓷基板器件的PCB翘曲度≤0.5%; 焊盘镀层光滑平整,一般不采用贵金属为可焊性保护层; 阻焊膜的厚度不大于焊盘的厚度; 安装焊盘可焊性优良,表面的润湿性应大于95%; 焊盘图形符合元器件安装要求,不允许采用共用焊盘; PCB能进行再流焊和波峰焊 PCB生产后,72小时内应进行真空包装。
3.1 元器件通孔插装(THT)
3.1.4安装形式 水平贴板安装,水平悬空安装,立式安装(非轴向) 支架固定,嵌入式安装(圆壳封装IC,有高度限制的元器件)
3.1.5元器件插装方法
手工插装 半自动插装 全自动插装
3.2 元器件表面安装(SMT)
3.2.1 SMT的主要内容: 设计:结构尺寸、端子形式、耐焊接热等; 制造:各种元器件的制作技术; 包装:编带式、棒式、托盘、散装等; 单(多)层印刷电路板、陶瓷、瓷釉金属板、夹层板等; 电设计、热设计、元器件布局、基板图形布线设计等;
焊点质量,防止焊点缺陷的重要条件。
可焊性检查主要有以下三种方法
焊槽法(垂直浸渍法) 焊球法(润湿时间法)
润湿称量法(GB/T2423.32-2008)
IEC60068-2-58试验Td:表面安装元器件的可焊性、金属化层耐熔蚀和耐焊接热 标准试验条件:可焊性试验温度235℃ 耐焊接热试验温度260℃
3.1 元器件通孔插装(THT)
3.1.2 安装次序
先低后高、先轻后重、先非敏感元器件后敏感元件、先 表面安装后通孔插装、先分立元器件后集成电路。
3.1 元器件通孔插装(THT)
3.1.3安装要求 安装高度要符合产品防震、绝缘、散热等要求及设计文件要求; 元器件加固要求:7g、3.5g及设计工艺文件的规定; 接线端子、铆钉不应作界面或层间连接用,导通孔(金属化孔)不能安装元器件; 一孔一线,孔径与引线直径的合理间隙(0.2~0.4mm) 空心铆钉不能用于电气连接; 元器件之间有至少为1.6mm的安全间距; 元器件安装后,引线伸出板面的长度应为1.5±0.8mm; 元器件安装后,引线端头采用弯曲连接时,引线弯曲长度为3.5 ~5.5d; 如底面无裸露的电路(印制导线);元件可贴板安装(玻璃二极管除外),如底面有裸露电路, 至少有0.25mm间距,最大为1mm; 元器件安装应做到不妨碍焊料流向金属化孔另一面; 跨接线应看作轴向引线元件,并符合轴向引线元件的安装要求; 双列直插IC安装在导电电路上时,元器件底面离板面的间隙最大为1mm或肩高; 陶瓷封装的双列IC安装后,引线可以弯曲30°,每侧二根。
3.1.1 安装原则
元器件在PCB上安装的形式多样,但都必须符合产品质量和可靠性要求,遵守有关原则:
元器件安装应满足产品力学和气候环境条件的要求; 疏密均匀、排列整齐、不允许立体交叉和重叠; 轴向引线元器件必须平行于板面安装,非轴向引线的元器件原则上不得水平安装; 金属壳体元器件应能与相邻印制导线和导体元器件绝缘。 元器件之间要保持合理的安全间隙或套套管; 大质量元器件的加固; 大功率元器件的散热和悬空安装; 热敏元器件安装,应远离发热元件或隔热措施; 静电敏感元器件安装,采取防静电措施; 元器件安装后,不得挡住其它元器件引线,以便于拆装、清洗;
小型,超小型器件的出现和推广应用,促进了高密度组装技术的发展,也模糊了一 级封
装和二级组装之间的界限。同时对电子产品的设计、组装工艺、组装设备等提出了更新 更高的要求。
1.2 电子产品的分级
按IPC-STD-001“电子电气组装件焊接要求”标准规定,根据产品最终使用条 件进行分级。
1级(通用电子产品):指组装完整,以满足使用功能主要要求的产品。 2级(专用服务类电子产品):该产品具有持续的性能和持久的寿命。需要不 间断的服务,但不是主要的。通常在最终使用环境下使用不会失效。 3级(高性能电子产品):指具有持续的高性能或能严格按指令运行的设备和 产品,不允许停歇,最终使用环境异常苛刻。需要时产品必须有效,例如生 命救治和其它关键的设备系统。
配合的唯一性。
热剥工艺造成的绝缘层变色是允许的,但不应烧焦发黑。 化学剥除绝缘层仅适用于单股实芯导线的端头处理,处理后应立即进行中和、 清洗;
屏蔽导线屏蔽层的处理应符合产品技术要求,处理方法应符合有关标准的要求。
2.6 PCB组装前的预处理
PCB的复验
组装前要求
3 印制电路板组装工艺
3.2 元器件表面安装(SMT)
3.2.4 焊膏 焊膏的技术要求
焊膏的成分符合国家标准的要求(GJB3243 5.3.2.2条) 在储存期内焊膏的性能保持不变 焊膏中金属颗粒与焊剂不分层 室温下连续印刷时,焊膏不易干燥,印刷性好 焊膏粘度要保证印刷时具有良好的脱模性,又要保证良好的触变性,印刷后焊膏 不产生塌陷 严格控制金属微粉和金属氧化物焊料,避免焊接时随溶剂、气体挥发而飞溅,形 成锡珠 焊接时润湿性良好
3.2 元器件表面安装(SMT)
SMC 元器件 SMD 有铅焊膏 焊膏 贴装材料 贴片胶 基板材料 印制电路板 表 面 安 装 技 术 电路图形设 计 焊膏印刷 网板设计、制作 表面贴装 贴装工艺 表面贴装和通孔插装混合安装 波峰焊接 焊接工艺 手工焊接 再流焊接(红外再流焊,热风再流焊,汽相再流焊,激光再流焊等) 清洗技术 清洗剂 清洗工艺 检测技术:焊点质量检测,在线测试,功能测试 设备:印刷机,贴片机,再流焊炉,清洗设备,检测设备,维修设备 SMT设计 SMT管理:质量,生产,设备,工艺等 无铅焊膏
电子管时代 晶体管时代
表面安装
集成电路时代
微组装
表面安装时代
微组装时代
装联工艺技术的三次革命 通孔插装 器件封装技术的发展
电子产品的装联工艺是建立在器件封装形式变化的基础上,即一种新型器件的出现, 必
然会创新出一种新的装联技术和工艺,从而促进装联工艺技术的进步。 QFP BGA CSP(μBGA) DCA MCM ……
3.2 元器件表面安装(SMT)
焊膏的管理和使用
焊膏应储存在5~10℃的环境条件下 使用前必须经回温处理,常温下会温2 ~4h 使用前应充分搅拌 印刷后应及时完成焊接,根据焊膏厂商推荐参数,
一般情况下应在4h内完成焊接
3.2 元器件表面安装(SMT)
焊膏的成分
选购要求:
根据设计和工艺要求,选择元器件种类、尺寸和封装形式;
元器件包装形式适合贴装机自动贴装; 元器件焊端(引脚)应涂镀厚度不小于7.5μm的锡铅合金(Sn含量58~68%); 包装开封后在25±5℃,HR55~70%条件下,在存放48小时内焊接仍能满足焊接技 术要求; 元器件在40℃的清洗溶剂中,至少能承受4min的浸泡时间; 元器件能承受10个再流焊周期,每个周期为215℃,时间为60s,并能承受在 260 ℃ 的熔融焊料中10s的浸泡时间; 元器件引线歪斜度误差不大于0.8mm; 元器件引线共平面度误差不大于0.1mm。 无铅元器件镀层识别(IPC-1066) 湿敏器件的处理规定(IPC-020、IPC-033)
表面组装元器件
电路基板 组装设计
组装工艺
组装材料:粘接剂、焊料、焊剂、清洗剂等; 组装工艺:组装方式、组装工艺流程、焊接技术、检测技术等; 组装技术:涂覆技术、贴装技术、焊接技术、清洗技术、检测技术等; 组装设备:涂覆设备、贴装机、焊接机、清洗机、测试设备等; 组装生产线或系统组成、控制与管理等;
组装系统控制与管理
1.3 电子装联工艺的组成
随着电子技术的不断发展和新型元器件的不断出现,电子装联技术也在不断 变化和发展。
电子装联工艺的组成
电子装联工艺的质量控制
电子装联工艺的组成
电子装联质量控制
2 装联前的准备工艺
2.1 元器件引线的可焊性检查
可焊性是衡量元器件和PCB焊接部位是否可以顺利发生焊接过程的重要特征之一,是保证
印刷工艺 装联工艺
3.2 元器件表面安装(SMT)
3.2.2元器件(SMC/SMD)
基本要求:
外形适合自动化贴装要求; 尺寸、形状标准化,并具有良好的互换性; 元器件焊端和引脚的可焊性符合要求; 符合再流焊和波峰焊的耐高温焊接条件;
可承受有机溶剂的清洗;
3.2 元器件表面安装(SMT)
2.2 元器件引线搪锡工艺
锡和锡铅合金为最佳的可焊性镀层,其厚度 为5~7μm。
Cu
镀金引线的搪锡(除金): 金镀层是抗氧化性很强的镀层,与SnPb焊料 有很好的润湿性,但直接焊接金镀层时, SnPb合金对金镀层产生强烈的溶解作用,金 与焊料中的Sn金属结合生成AuSn4合金,枝晶
μm/s Ag Au 7 6 5 4 3 2 1 ℃ 0 200 300 400 500 Pt Ni 过直径10%的变形。 扁平封装器件(如QFP等)应先搪锡后成形。 成形不当或不符合要求时,原弯曲半径在1~2倍引线直径内,可以矫直后在原处再弯曲 一次。
2.5 导线端头处理工艺要求
导线端头绝缘层剥除应使用热控型剥线工具,限制使用机械(冷)剥 线工具。 采用机械剥线工具,应采用不可调钳口的精密剥线钳,并做到钳口与导线规格
状结构,其性能变脆,机械强度下降。为防
止金脆现象出现,镀金引线在焊接前必须经 过搪锡除金处理。
Sn-Pb焊料中各种金属的溶解速度
2.3 IPC-J-STD-001D对镀金引线除金的规定
对于具有2.5μm或更厚金层的通孔元件引线,在焊接前,应去除至少95%被 焊表面的金层; 对于表面贴装元器件,不管金层厚度为多少,在焊接前,应去除至少95% 被焊表面的金层; 针对镀金层厚度大于或等于有2.5μm的元器件,可采用二次搪锡工艺或波峰 焊接工艺去除焊接端头表面的金层。 针对采用化学浸镍金(ENIG)工艺的印制板,印制板表面镀金层可免除除 金要求。
1 概述
电子产品装联工艺是指用规定的电子元器件和零、部(组)经过电子 及机械的装配和连接,使电子产品满足设计任务书要求的工艺技术。 因此,没有一整套较为先进成熟的、可操作性的电子装联工艺技术, 是不可能保证电子装联的高质量和电子产品的可靠性。
1.1 电子装联工艺技术的发展概况
装联工艺的发展阶段
3.2 元器件表面安装(SMT)
3.2.3印制电路板(PCB)
PCB基材一般选用FR4环氧玻璃纤维板,或FR4改性、FR5板; 板面平整度好,翘曲度≤0.75%,安装陶瓷基板器件的PCB翘曲度≤0.5%; 焊盘镀层光滑平整,一般不采用贵金属为可焊性保护层; 阻焊膜的厚度不大于焊盘的厚度; 安装焊盘可焊性优良,表面的润湿性应大于95%; 焊盘图形符合元器件安装要求,不允许采用共用焊盘; PCB能进行再流焊和波峰焊 PCB生产后,72小时内应进行真空包装。
3.1 元器件通孔插装(THT)
3.1.4安装形式 水平贴板安装,水平悬空安装,立式安装(非轴向) 支架固定,嵌入式安装(圆壳封装IC,有高度限制的元器件)
3.1.5元器件插装方法
手工插装 半自动插装 全自动插装
3.2 元器件表面安装(SMT)
3.2.1 SMT的主要内容: 设计:结构尺寸、端子形式、耐焊接热等; 制造:各种元器件的制作技术; 包装:编带式、棒式、托盘、散装等; 单(多)层印刷电路板、陶瓷、瓷釉金属板、夹层板等; 电设计、热设计、元器件布局、基板图形布线设计等;
焊点质量,防止焊点缺陷的重要条件。
可焊性检查主要有以下三种方法
焊槽法(垂直浸渍法) 焊球法(润湿时间法)
润湿称量法(GB/T2423.32-2008)
IEC60068-2-58试验Td:表面安装元器件的可焊性、金属化层耐熔蚀和耐焊接热 标准试验条件:可焊性试验温度235℃ 耐焊接热试验温度260℃
3.1 元器件通孔插装(THT)
3.1.2 安装次序
先低后高、先轻后重、先非敏感元器件后敏感元件、先 表面安装后通孔插装、先分立元器件后集成电路。
3.1 元器件通孔插装(THT)
3.1.3安装要求 安装高度要符合产品防震、绝缘、散热等要求及设计文件要求; 元器件加固要求:7g、3.5g及设计工艺文件的规定; 接线端子、铆钉不应作界面或层间连接用,导通孔(金属化孔)不能安装元器件; 一孔一线,孔径与引线直径的合理间隙(0.2~0.4mm) 空心铆钉不能用于电气连接; 元器件之间有至少为1.6mm的安全间距; 元器件安装后,引线伸出板面的长度应为1.5±0.8mm; 元器件安装后,引线端头采用弯曲连接时,引线弯曲长度为3.5 ~5.5d; 如底面无裸露的电路(印制导线);元件可贴板安装(玻璃二极管除外),如底面有裸露电路, 至少有0.25mm间距,最大为1mm; 元器件安装应做到不妨碍焊料流向金属化孔另一面; 跨接线应看作轴向引线元件,并符合轴向引线元件的安装要求; 双列直插IC安装在导电电路上时,元器件底面离板面的间隙最大为1mm或肩高; 陶瓷封装的双列IC安装后,引线可以弯曲30°,每侧二根。