加氢 制造工艺过程
加氢的精制工艺流程

加氢的精制工艺流程
《加氢的精制工艺流程》
加氢是炼油行业中常用的一种精制工艺,它通过使用氢气将原油中的不饱和烃、硫化物和氮化物等杂质转化为饱和烃,从而提高油品的质量。
下面我们来详细介绍一下加氢的精制工艺流程。
1. 原料预处理
在加氢前,首先要对原油进行预处理。
这一步主要是将原油中的大分子杂质去除,以保护加氢催化剂的稳定性和活性。
通常采用脱蜡、脱沥青、脱硫等方法进行预处理。
2. 加氢反应
将经过预处理的原油送入加氢反应器中,与高压氢气接触,经过加氢反应器内的催化剂作用,不饱和烃、硫化物和氮化物等杂质被加氢转化为饱和烃以及硫化氢和氨。
这一步是整个加氢工艺的关键步骤,需要控制好反应器的温度、压力和氢气流量,才能获得理想的产品质量。
3. 分离和加工
加氢反应后的产物需要进行分离和加工,通常包括减压分离、氢气回收和产品升温卸催化剂等步骤。
其中,减压分离是将反应产物进行分离,得到干净的产品油和硫化氢等气体。
氢气回收可以将反应产生的氢气进行回收利用,节约能源。
产品升温卸催化剂则是将反应器内的催化剂进行再生,以保持其活性和稳定性。
4. 产品处理
最后得到的产品油需要进行进一步的处理,比如脱硫、脱氮、脱脂等工艺,以获得符合环保标准和市场需求的成品油。
通过上述精制工艺流程,原油中的不饱和烃、硫化物和氮化物等杂质得到有效转化和去除,从而提高了油品的质量和降低了环境污染。
加氢工艺成为了炼油行业中不可或缺的精制工艺之一。
加氢裂化工艺流程介绍

加氢裂化工艺流程介绍加氢裂化是一种重要的石油化工工艺,主要用于将重质石油馏分或原油中的长链烃类分子切割成较短链烃类分子,以提高产品的转化率和降低其粘度,从而达到提高产品质量和增加产品产量的目的。
该工艺主要包括催化剂的选择、反应装置的设计、反应条件的控制等几个方面,下面将对加氢裂化工艺的流程进行详细介绍。
一、催化剂的选择加氢裂化反应的催化剂通常为金属催化剂,如镍、钴、铂、钒等。
这些金属催化剂能够在合适的条件下催化烃类分子的裂解反应,生成较短链烃类分子和氢气。
通常还需在催化剂中加入一定量的活性组分,如氧化物、氧化钠、氧化铝等,以增加催化剂的活性和稳定性。
二、反应装置的设计加氢裂化反应通常在催化裂化装置中进行。
这种反应装置通常由裂化炉、加氢装置、冷却装置和分离装置等组成。
裂化炉是反应装置的核心部件,是将原料石油馏分或原油送入裂化反应器进行加热和裂化的地方。
加氢装置用于向裂化反应器中注入氢气,以提高裂化反应的效率和选择性。
冷却装置用于冷却反应产物,并将其中的气态产物液化。
分离装置则用于将反应产物中的各种组分进行分离,并提取所需的产品。
三、反应条件的控制加氢裂化反应的温度、压力、空速、氢油比等条件对反应的效率和选择性具有重要影响。
通常情况下,加氢裂化反应的温度为400-500℃,压力为2-8 MPa,空速为1-10 h-1,氢油比为1000-2000 Nm3/m3。
在这些条件下,可获得较高的产品转化率和较好的产品选择性。
加氢裂化工艺通常包括以下几个步骤:1. 原料处理:原料石油馏分或原油经过脱盐、脱硫等处理后,送入加氢裂化装置进行加热和裂化。
在这个过程中,通过加热将原料加热至裂化反应所需温度,并将其中的一部分烃类分子裂解成较短链烃类分子和氢气。
3. 冷却和分离:经过加氢裂化反应后,产生大量的气态产物和液态产物需要进行冷却和分离。
通过冷却装置将气态产物冷却成液态产物,并通过分离装置将其中的各种组分进行分离,提取所需的产品。
加氢工艺流程图

加氢工艺流程图
加氢工艺流程图是对加氢工艺的整体过程进行图示的工具。
下面是一个简单的加氢工艺流程图:
加氢工艺流程图
一、原料准备
1. 原料进料:石油原料进入加氢装置,经过一系列预处理操作,如脱水、脱硫、脱盐等。
2. 原料加热:将原料加热至合适的温度,以便于后续的加氢反应。
二、加氢反应
1. 催化剂床:将加热后的原料送入加氢反应器,在催化剂床中与氢气进行反应。
2. 加氢反应:在催化剂床中,原料与氢气反应生成较低碳数的烃类。
同时,不饱和烃和硫化物还原为饱和烃和硫化物。
三、分离
1. 分离器:加氢反应后的产物进入分离器,分离出不同碳数的烃类和硫化物。
2. 减压器:将分离器中的液体进行减压蒸馏,得到精制产品。
3. 液气分离:在分离器中,将轻质烃类和氢气进行分离,重新循环使用氢气。
四、产品处理
1. 调整:对产物进行一些调整操作,如调整脱硫剂的用量以降
低硫含量。
2. 分析:对产品进行分析,检测产品的质量指标是否符合要求。
3. 储存:将产品存储在合适的容器中,准备出售或进一步加工。
五、废物处理
1. 处理:对废物进行处理,如处理含有重金属的废水、处理残留催化剂等。
2. 回收:对能够回收利用的废物进行回收,减少资源的浪费。
这是一个简单的加氢工艺流程图,实际的加氢工艺流程可能更加复杂,包括多个单元和反应器。
加氢工艺的目的是降低原料中的不饱和烃和硫化物含量,提高产品的质量。
加氢工艺在石油化工等领域有着广泛的应用,对改善燃料质量、减少环境污染具有积极作用。
加氢工艺流程简述
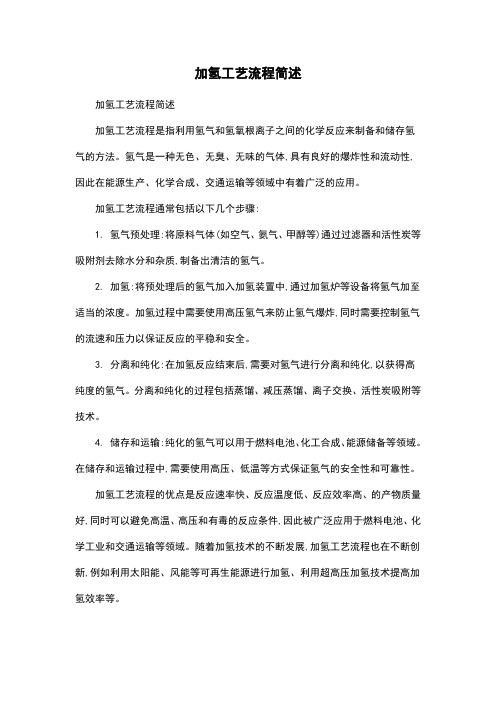
加氢工艺流程简述
加氢工艺流程简述
加氢工艺流程是指利用氢气和氢氧根离子之间的化学反应来制备和储存氢气的方法。
氢气是一种无色、无臭、无味的气体,具有良好的爆炸性和流动性,因此在能源生产、化学合成、交通运输等领域中有着广泛的应用。
加氢工艺流程通常包括以下几个步骤:
1. 氢气预处理:将原料气体(如空气、氨气、甲醇等)通过过滤器和活性炭等吸附剂去除水分和杂质,制备出清洁的氢气。
2. 加氢:将预处理后的氢气加入加氢装置中,通过加氢炉等设备将氢气加至适当的浓度。
加氢过程中需要使用高压氢气来防止氢气爆炸,同时需要控制氢气的流速和压力以保证反应的平稳和安全。
3. 分离和纯化:在加氢反应结束后,需要对氢气进行分离和纯化,以获得高纯度的氢气。
分离和纯化的过程包括蒸馏、减压蒸馏、离子交换、活性炭吸附等技术。
4. 储存和运输:纯化的氢气可以用于燃料电池、化工合成、能源储备等领域。
在储存和运输过程中,需要使用高压、低温等方式保证氢气的安全性和可靠性。
加氢工艺流程的优点是反应速率快、反应温度低、反应效率高、的产物质量好,同时可以避免高温、高压和有毒的反应条件,因此被广泛应用于燃料电池、化学工业和交通运输等领域。
随着加氢技术的不断发展,加氢工艺流程也在不断创新,例如利用太阳能、风能等可再生能源进行加氢、利用超高压加氢技术提高加氢效率等。
加氢反应器工艺流程图

理化检验
堆焊E309L 所有堆焊面 DHT
堆焊E347 密封槽不堆焊E347
6、底部卸料口法兰盖:
MT、HB DT PT PT、HB
、 、 测厚、
PT
、 、 测厚、
外协锻件回厂 机加 性能热处理 性能取试 机加符图 机加密封槽309L符图 密封槽堆焊E347 机加密封槽符图 理化检验 PWHT
堆焊E309L 所有堆焊面 堆焊E347 密封槽不堆焊E347
机加 密封槽
产品焊接试板T-B-1,T-B-2 T-A-1理化检验合格
水压试验
清理
除锈
涂装
发货
注1:筒节在加工时,如果封头未回,则与封头相配的一端可以在堆焊后加工坡口。 注2:下过渡段在加工内外园和凸台时,若毛坯状况满足图纸凸台尺寸要求则可不再进行堆焊凸台等工序,直接进行堆焊309 及 后续工序。 注3:当 钢板的模拟 后的复验的性能数据满足要求时,裙座 部分与设备整体同炉进行 ,否则应调整 工序,使裙座 部分与设备分开进行局部消应热处理。
VT、CT、UT MT、 RT
PT
、 、 测厚、
2、上球形封头部件的组焊:
DT DT
VT、CT、UT MT、 RT
PT
、 、 测厚、
4 7 1 7
组焊卸料管与卸料口法兰
DHT 补堆E309L
DHT
补堆E347
组焊下封头与出口管段、卸料管 组装产品焊接试板T-A-1 清根 焊接
ISR 试板同炉
补堆E309L
DT、 MT
材料复验 焊接
划线下料 含T-A-1 筒节一展长根据封头定 冷卷成形 割纵缝坡口 组装纵缝 含试板
进炉ISR 校园
其余筒节不进行此工序
加氢的精制工艺流程

加氢的精制工艺流程加氢是一种常用的精制工艺,在石油和石化行业中起着很重要的作用。
加氢工艺可以将高硫、高氮和高金属含量的原油转化为低硫、低氮、低金属含量的产品,提高产品的质量和降低环境污染。
下面将介绍关于加氢的精制工艺流程。
加氢的精制工艺主要包括加氢裂化、加氢脱硫和加氢裂化等环节。
加氢裂化是一种将重油在高温和高压下裂解为较轻质的燃料油和裂解气体的过程。
首先,将重油和催化剂一起送入加氢裂化炉,炉内压力一般为30-40MPa,温度为450-500℃。
在高温和高压的条件下,重油中的长链分子会被分解成较小的分子。
同时,催化剂中的金属成分和硫化物会催化分子裂解反应的进行。
裂解产物中主要含有轻质燃料油和裂解气体。
然后,通过冷凝和分离装置,将燃料油和裂解气体分离出来。
最后,燃料油可以作为燃料使用,而裂解气体可以进一步处理和利用。
加氢脱硫是一种将原油中的硫化物转化为氢硫化气体,降低硫含量的过程。
首先,将含有硫化物的原油和催化剂一起送入加氢脱硫反应器,炉内压力一般为10-20MPa,温度为300-400℃。
在催化剂的作用下,硫化物会和氢气反应生成氢硫化气体。
然后,通过冷凝和分离装置,将氢硫化气体和油水分离出来。
最后,氢硫化气体可以进一步处理,而脱硫后的原油可以用于提炼高品质的燃料油和润滑油。
加氢裂化是一种将重油中的长链烷烃分子裂解为较轻质的烃类和裂解气体的过程。
首先,将重油和催化剂一起送入加氢裂化反应器,压力一般为10-30MPa,温度为350-450℃。
在反应器中,大分子烴类和催化剂会发生裂解反应,生成较小的烃类分子。
同时,催化剂中的金属成分和硫化物会催化裂解反应的进行。
然后,通过冷凝和分离装置,将轻质烃类和裂解气体分离出来。
最后,轻质烃类可以进一步提炼和利用,而裂解气体可以用于加热和提供燃料。
通过以上加氢的精制工艺流程,可以将高硫、高氮和高金属含量的原油转化为低硫、低氮、低金属含量的产品,提高产品的质量和降低环境污染。
加氢反应器工艺流程图
VT
外观检查
MT
磁粉检测
HB
布氏硬度
PDF 文件使用 "pdfFactory Pro" 试用版本创建
UT、PT、FN 测厚、CT
UT、 MT
6
7、出口管段、直管、卸料管:
MT PT
8、弯管:
MT、DT、测厚
、
PT
、 、 测厚、
9、下段裙筒 划线 下料
DT
DT
DT
UT、RT VT、DT
UT、 、
Ea3
Ea4
裙筒Ⅰ
Eb2
外协锻件回厂 机加 性能热处理 机加外形符图 性能取试
7
理化检验
堆焊E309L 所有堆焊面 DHT 堆焊E347 外协锻件回厂 外协成型 机加
性能热处理
性能取试
理化检验
机加坡口
堆焊E309L
DHT
堆焊E347
8
材料验收
刨坡口
组焊Ea3,Ea5 (拼缝)
卷制成形
组焊Ea4 组焊Ea6
校园
组焊Eb2
组焊裙座上其余各件
喷砂
9
Ea5
Ea6
裙筒Ⅰ
二、主要零部件的装焊
1、下球形封头部件的组焊:
DT
VT、CT、UT MT、 RT PT、VT
DT DT
UT、PT、FN 测厚、VT
机加 密封槽
产品焊接试板T-B-1,T-B-2 T-A-1理化检验合格
水压试验
清理
除锈
涂装
发货
注1:筒节在加工时,如果封头未回,则与封头相配的一端可以在堆焊后加工坡口。 注2:下过渡段在加工内外园和凸台时,若毛坯状况满足图纸凸台尺寸要求则可不再进行堆焊凸台等工序,直接进行堆焊309 及 后续工序。 注3:当 钢板的模拟 后的复验的性能数据满足要求时,裙座 部分与设备整体同炉进行 ,否则应调整 工序,使裙座 部分与设备分开进行局部消应热处理。
加氢精制装置工艺流程简介
目录一,工艺流程简介 (1)1,装置的生产过程 (1)2,装置流程说明 (1)二,设备列表 (3)三,仪表列表 (4)四,现场阀列表 (10)五,工艺卡片 (12)六,物料平衡 (13)七,复杂控制说明 (14)八,重点设备的操作 (14)九,操作规程 (17)1,正常开工 (17)2,正常停车 (25)3,压缩机K101/K102事故停机 (27)4,停1.0MP A蒸汽 (28)5,反应器R101飞温 (28)6,原料油中断 (29)7,新氢中断 (29)8,高分串压至低分 (30)9,F101炉管破裂 (30)10,燃料气中断 (31)11,过滤器压差超高 (31)12,项目列表 (32)十,流程图画面 (35)十一,加氢精制仿真PI&D图 (37)十二,加氢精制装置DCS流程图 (49)十三,加氢精制装置现场操作画面 (62)1一,工艺流程简介1,装置的生产过程原料油经泵抽入装置后,依次经过自动反冲洗过滤器滤去固体杂质后,进入原料油罐,再经原料油泵升压;新氢进入新氢压缩机升压后,先与来自循环氢压缩机的循环氢混合,再和升压后的原料油混合,换热后进入反应加热炉升温,再进加氢精制反应器。
在反应器中进行加氢脱硫、脱氮、脱氧、烯烃饱和芳烃开环饱和等反应。
反应产物换热后,在高压分离器中经过气、油、水三相分离后,气相经脱硫后再由循环氢压缩机升压后,返回反应系统。
生成油先与产品换热,再与反应产物换热后,经H2S汽提塔后进产品分馏塔。
分馏塔顶油气经冷凝冷却后,进分馏塔顶回流罐进行气、油、水三相分离。
气相即分馏塔顶低压含硫气体送至装置外的火炬系统焚烧处理;水相至含硫污水汽提装置处理;油相即粗汽油由粗汽油泵抽出,将其大部分为回流,少部分作为产品送出装置。
塔底出来的精制柴油经换热后作为产品出装置。
2,装置流程说明(1)反应部分工艺流程混合进料由原料罐区进装置,经原料油升压泵(P-101/A.B)升压后,进入原料油过滤器(SR-101/A.B)进行过滤。
沸腾床加氢工艺
沸腾床加氢工艺
沸腾床加氢工艺是一种高效的加氢反应技术,常用于炼油、化工、石化等领域。
该工艺的特点是反应物在高温高压下通过床层催化剂进行加氢反应,反应过程中床层内的液体和气体混合物被加热并产生沸腾,使反应物与催化剂充分接触,反应速率快,反应效果好。
沸腾床加氢工艺的优点是反应速率快、反应效果好、催化剂利用率高、操作简便、能耗低、生产成本低等。
同时,该工艺还能够处理高硫、高氮、高酸等难处理的原料,具有很强的适应性。
沸腾床加氢工艺的应用范围十分广泛,常用于石油加工、化学品制造、新能源等领域。
在炼油行业中,沸腾床加氢工艺可用于提高汽油和柴油的质量,降低硫含量和芳烃含量。
在化学工业中,该工艺可用于生产烯烃、醇等化学品。
在新能源领域,沸腾床加氢工艺可用于生产氢气、生物柴油等。
总之,沸腾床加氢工艺是一种高效的加氢反应技术,具有广泛的应用前景。
- 1 -。
煤化工中粗苯加氢工艺.
煤化工中粗苯加氢工艺粗苯加氢精制法是将粗苯在氢气的保护下,经多段蒸发系统后进入预反应器,在Ni 和Mo的催化剂作用下,使双烯烃、苯乙烯等加氢饱和,然后经主反应器,在Co和Mo催化剂的作用下催化加氢, 将其中的硫、氮、氧等杂质转化为H2S、NH3、H2O,并进一步使烯烃饱和而得到加氢反应油。
加氢油在汽提塔内脱除溶解的气体后,进入预蒸馏塔,将其分馏成苯-甲苯和二甲苯两种馏分。
苯-甲苯馏分作为萃取蒸馏的原料,用萃取剂N -甲酰吗琳将非芳香烃从芳香烃中脱除出来。
脱非芳香烃后的苯-甲苯馏分经汽提与溶剂分离,再经精馏得到高纯苯和纯甲苯。
萃取塔顶得到的非芳香烃经溶剂回收塔脱除聚合物后,得到非芳香烃和溶剂。
贫溶剂经再生后重复使用。
二甲苯馏分在二甲苯塔内分离成二甲苯和碳9馏分等。
2 粗苯加氢工艺粗苯预蒸馏是将粗苯分离成轻苯和重苯。
轻苯作为加氢原料,预反应器是在较低温度下(200-250℃把高温状态下易聚合的苯乙烯等同系物进行加氢反应,防止其在主反应器内聚合,使催化剂活性降低,在2个主反应器内完成加氢裂解、脱烷基、脱硫等反应。
由主反应器排出的油气经冷凝冷却系统,分离出的液体为加氢油,分离出的氢气和低分子烃类脱除H2S后,一部分送往加氢系统,一部分送往转化制氢系统制取氢气。
预反应器使用Co-Mo催化剂,主反应器使用Cr系,催化剂。
稳定塔对加氢油进行加压蒸馏,除去非芳烃和硫化氢。
白土塔利用SiO2-Al2O3为主要成分的活性白土,吸附除去少量不饱和烃。
经过白土塔净化后的加氢油,在苯塔内精馏分离出纯苯和苯残油,苯残油返回轻苯贮槽,重新进行加氢处理。
制氢系统将反应系统生成的H2和低分子烃混合循环气体通过单乙醇胺(MEA 法脱除硫化氢。
利用一氧化碳变换系统制取纯度99.9%的氢气。
不需要外来焦炉煤气制氢。
莱托法只生产纯苯,纯苯对原料中苯的收率可达110%以上,这是由于原料中的甲苯、二甲苯加氢脱烷基转化成苯造成的,总精制率91.5%,偏低。
- 1、下载文档前请自行甄别文档内容的完整性,平台不提供额外的编辑、内容补充、找答案等附加服务。
- 2、"仅部分预览"的文档,不可在线预览部分如存在完整性等问题,可反馈申请退款(可完整预览的文档不适用该条件!)。
- 3、如文档侵犯您的权益,请联系客服反馈,我们会尽快为您处理(人工客服工作时间:9:00-18:30)。
加氢反应器制造工艺设计一:加氢反应器的设计背景工程科学是关于工程实践的科学基础,现代过程装备与控制工程是工程科学的一个分支,因此,生产实习是工科学习的重要环节。
在兰州兰石集团实习期间,对化工设备的发展前景和各种化工容器如反应釜、换热器、储罐、分液器和塔器等的有所了解和学习。
生产实习的主要任务是学习化工设备的制造工艺和生产流程,将理论知识与生产实践相结合,理论应用于实际。
因此,过程装备与检测的课程设计的设置是十分必要的。
由于我们实习的加工车间正在进行加氢反应器的生产,而加氢反应器是石油化工行业的关键设备,其生产工艺和设计制造在化工设备中具有显著的代表性,为此,选择加氢反应器这一典型的化工设备作为课程设计的设计题目。
二:加氢反应器的主要设计参数1:引用的主要标准及规范国家质量技术监督局颁发的《压力容器安全技术监察规程》(99)版GB150-1998 《钢制压力容器》GB6654-1996 压力容器用钢板(含1、2号修改单)JB4708-2000 钢制压力容器焊接工艺评定JB/T4709-2000 钢制压力容器焊接规程JB4744-2000 钢制压力容器产品焊接试板的力学性能检验JB/T4730-2005 承压设备无损检测JB4726-2000 压力容器用碳素钢和低合金钢锻件JB4728-2000 压力容器用不锈钢锻件GB/4237-2007 不锈钢热轧钢板和钢带GB/T3280-2007 不锈钢冷轧钢板和钢带GB/T3077-1999 合金结构钢GB/T14976-2002 流体输送用不锈钢无缝钢管JB/T4711-2003 压力容器涂敷与运输包装2 主要技术参数表一设计压力 5.75/0.1MPa设计温度375/177℃最高工作压力 4.88MPa最高工作温度343℃容器类别三类容器容积78.2立方米腐蚀裕量0水压试验立式7.47/卧式7.55MPa盛装介质石脑油、油气、氢气、硫化氢主体材质15CrMoR3 结构特点该加氢精制反应器为板焊结构,其内径φ4000㎜,壁厚98㎜,由2节组成;封头内半径2022㎜,壁厚78㎜,总重量94550Kg 。
整个容器位于裙座圈上,总高度约14011㎜,容器内壁(包括封头、筒体、法兰以及接管和弯管)全部堆焊309L+347 不锈钢,反应器设有油气进出口、催化剂卸料口、冷氢进口、热电偶口、人孔等接管孔,所有接管均采用整体补强结构,裙座采用对接结构,各接管密封采用八角垫结构,设备上下各有一个弯管。
容器内部焊有凸台(一周),安装有冷氢盘、分配盘等内件。
4 使用特点及需解决的问题由于热壁加氢反应器是在高温、高压、临氢及硫和硫化氢介质条件下使用的,因此决定了该设备在使用过程中将会出现:氢腐蚀、氢脆、高温高压硫化氢腐蚀、硫化物应力腐蚀开裂、堆焊层的剥离、CrMo 五钢的回火脆性破坏等问题。
5 材料要求5.1 锻件和钢板用15CrMo 钢硬是采用电炉冶炼加炉外精炼炉精炼,和真空脱气等工艺方法生产的本质细晶粒镇静钢5.2 钢板和锻件均应进行正火(允许加速冷却)加回火热处理,热处理工艺应根据材料化学成分和截面尺寸大小由钢材生产厂确定,冷却速度的大小以保证达到力学性能的要求为原则5.3 材料力学性能试板应进行模拟焊后热处理,即模拟制造过程中壳体材料可能经历的最大程度的焊后热处理(Max.PWHT )和最小程度的焊后热处理(Min.PWHT ),包括所有482℃以上的中间和最终焊后热处理过程,其热处理工艺为:封头 热成形 (900-950)℃ ×90分钟正火 910℃×120分钟 回火 690℃×150分钟,空冷热成形 (900-950)℃ ×30分钟正火 910℃×40~50分钟回火 690℃×60~70分钟5.4 筒体 封头用15CrMo 钢板除应满足GB6654-1996(含1、2号修改单)的规定外,尚应满足技术条件的要求5.5 钢板的化学成分符合下表二的规定,熔炼分析按炉(灌)号取样,成品分析按轧制张张取样(可以从室温拉伸试验断裂后的试样上切取),按GB/T223标准规定表二 15CrMoR 钢板的化学成分 (Wt%)5.6 15CrMo 钢板经正火加回火热处理,再经模拟焊后热处理后的力学性能应符合下, 力学性能试验按轧制张逐张进行,其取样位置,试样数量及热处理状态应符合下表四的规定 化学成分CSi Mn P S Cr Mo Cu Ni Sn 熔炼分析 0.05~0.17 0.15~0.40 0.40~0.65 ≤0.010 ≤0.010 0.80~1.15 0.45~0.60≤0.20 ≤0.20 ≤0.012 成品分析 0.04~0.17 0.13~0.45 0.40~0.65 ≤0.012 ≤0.012 0.74~1.21 0.40~0.65≤0.20 ≤0.25 ≤0.015序号试验项目 单位 力学性能值 1 室温拉伸强度 MP 450~585表三 15CrMoR 钢板的力学性能5.7 钢板生产厂必须以试板进行正火加回火加模拟焊后热处理其各项性能均应满足本技术条件的要求5.8 钢板应按JB/T4730.3-2005的规定进行超声检测,必须进行100%扫查,验收标注为Ⅰ级5.9 总图三: 方案论证过程条件 加氢反应是可逆、放热和分子数减少的反应,根据吕·查德里原理,低温、高压有利于化学平衡向加氢反应方向移动。
加氢过程所需的温度决定于所用催化剂的活性,活性高者温度可较低。
对于在反应温度条件下平衡常数较小的加氢反应(如由一氧化碳加氢合成甲醇),为了提高平衡转化率,反应过程需要在高压下进行,并且也有利于提高反应速度。
采用过量的氢,不仅可加快反应速度和提高被加氢物质的转化率,而且有利于导出反应热。
过量的氢可循环使用。
常用的加氢反应器有两类:一类用于高沸点液体或固体(固体需先溶于溶剂或加热熔融)原料的液相加氢过程,如油脂加氢、重质油品的加氢裂解等。
液相加氢常在加压下进行,过程可以是间歇式的,也可以是连续的。
间歇液相加氢常采用具有搅拌装置的压力釜或鼓泡反应器。
连续液相加氢可采用涓流床反应器或气、液、固三相同向连续流动的管式反应器。
另2室温屈服强度 室温延伸率 室温断面收缩率 MP ≥275 3% ≥22 4 % ≥455 Ⅱ1572 0℃夏比冲击功 J三个试样平均值≥41 一个试样最低值≥31 6室温弯曲实验 高温屈服强度 d=2a ,弯曲180°无裂纹 7 MP ≥204一类反应器用于气相连续加氢过程,如苯常压气相加氢制环己烷、一氧化碳高压气相加氢合成甲醇等,反应器的类型可以是列管式或塔式。
工业应用加氢过程在石油炼制工业中,除用于加氢裂化外,还广泛用于加氢精制,以脱除油品中存在的含氧、硫、氮等杂质,并使烯烃全部饱和、芳烃部分饱和,以提高油品的质量。
在煤化工中用于煤加氢液化制取液体燃料。
在有机化工中则用于制备各种有机产品,例如一氧化碳加氢合成甲醇、苯加氢制环己烷、苯酚加氢制环己醇、醛加氢制醇、萘加氢制四氢萘和十氢萘(用作溶剂)、硝基苯加氢还原制苯胺等。
此外,加氢过程还作为化学工业的一种精制手段,用于除去有机原料或产品中所含少量有害而不易分离的杂质,例如乙烯精制时使其中杂质乙炔加氢而成乙烯;丙烯精制时使其中杂质丙炔和丙二烯加氢而成丙烯;以及利用一氧化碳加氢转化为甲烷的反应,以除去氢气中少量的一氧化碳等。
四:制造工艺设计1.选材在高温、高压下,氢与钢材中的碳原子能化合生成甲烷,使钢材变脆,称为氢蚀。
故高压加氢的反应器,必须采用合金钢材。
氢是易燃、易爆物质,加氢过程必须考虑安全措施。
在石油加氢装置中Cr-Mo系低合金耐热抗氢钢得到广泛的使用。
钢15CrMoR(相当于1Cr-0.5Mo)在500~550℃有较高持久强度,长期运行也无石墨化倾向,在石油化工中允许使用温度为350~500℃,有抗氢要求使用下限温度。
1.11 15CrMoR属低碳珠光体耐热钢,有利于工艺性;1.12组织中的铁素体份额高,限制其强度级别为300MP;1.13 钢材中0.5%的Mo提高组织稳定性;1.14 Cr起固溶强化作用,同时组织石墨化倾向。
从操作工况看,该加氢反应器的基材选15CrMoR即满足要求。
封头堆焊层的选择石油化工行业的加氢反应器、原流合成塔、煤液化反应器及核电站的厚壁压力容器等内表面均需大面积堆焊耐高温,抗氧及硫化氢等腐蚀的不锈钢衬里。
带极电渣堆焊是利用导电熔渣的电阻热熔化堆焊材料和母材的,除引线阶段外,整个堆焊过程应设有电弧产生。
随着压力容器日趋大型化、高参数化,促使堆焊技术向更优质更高效的方向发展。
带极电渣堆焊技术具有比带极埋弧难焊更高的生产效率、更低的稀释率和良好的焊缝成形等优点,得到迅速发展和较普遍的应用。
8.典型零件的制作2.油气入口制造工艺过程2.1 装焊人孔盖与塞管1装焊人孔盖(-23-1)与第一段弯管L50°2焊接人孔盖与塞管3炉外消氢,按热处理工艺4打磨焊接接头2.2探伤 1 焊接接头进行100%RT,按GB/T4730.2-2005中Ⅱ级合格2 焊接接头进行100%UT,按GB/T4730.3-2005中I级合格3 焊接接头进行100%MT,按JB/T4730.4-2005中Ⅰ级合格2.3堆焊过渡层1堆焊过渡层,详见焊接工艺说明书2炉外消氢,按热处理工艺3打磨过渡层2.4探伤 1 过渡层进行100%PT,按JB/T4730.5-2005中Ⅰ级合格2.5堆焊表层 1 堆焊表层,详见焊接工艺说明书2 测铁元素体数3 打磨表层2.6探伤1表层进行100%PT,按JB/T4730.5-2005中Ⅰ级合格2堆焊层及熔合面进行100%UT,符合Ⅱ1573-00.JT3堆焊层进行厚度检测,符合图纸要求2.7装焊塞管1装焊第二段塞管(40°)2焊接3炉外消氢,按热处理工艺4打磨焊接接头2.8探伤 1 焊接接头进行100%RT,按GB/T4730.2-2005中Ⅱ级合格2 焊接接头进行100%UT,按GB/T4730.3-2005中I级合格3 焊接接头进行100%MT,按JB/T4730.4-2005中Ⅰ级合格2.9堆焊过渡层1堆焊过渡层,详见焊接工艺说明书2炉外消氢,按热处理工艺3打磨过渡层2.10探伤过渡层进行100%PT,按JB/T4730.5-2005中Ⅰ级合格2.11堆焊表层 1 堆焊表层,详见焊接工艺说明书2 打磨表层2.12探伤1表层进行100%PT,按JB/T4730.5-2005中Ⅰ级合格2堆焊层及熔合面进行100%UT,符合Ⅱ1573-00.JT3堆焊层进行厚度检测,符合图纸要求2.13划线画出弯管端口的加工线及检查线2.14趟坡口按图加工弯管坡口2.15 探伤坡口进行100%MT,按JB/T4730.4-2005中Ⅰ级合格2.16装焊法兰1装焊油气入口接管法兰(-23-4)2焊接3炉外消氢,按热处理工艺4打磨焊接接头2.17探伤 1 焊接接头进行100%RT,按GB/T4730.2-2005中Ⅱ级合格2 焊接接头进行100%UT,按GB/T4730.3-2005中I级合格3 焊接接头进行100%MT,按JB/T4730.4-2005中Ⅰ级合格2.18堆焊过渡层1堆焊过渡层,详见焊接工艺说明书2炉外消氢,按热处理工艺3打磨过渡层2.19探伤过渡层进行100%PT,按JB/T4730.5-2005中Ⅰ级合格2.20 堆焊表层 1 堆焊表层,详见焊接工艺说明书2 打磨表层2.21探伤1表层进行100%PT,按JB/T4730.5-2005中Ⅰ级合格2堆焊层及熔合面进行100%UT,符合Ⅱ1573-00.JT3堆焊层进行厚度检测,符合图纸要求2.22装焊吊耳1按图装焊吊耳2焊接3打磨焊接接头表面2.23探伤焊接接头进行100%MT,按JB/T4730.4-2005中Ⅰ级合格2.24 最终热处理油气出口管进行最终热处理2.25喷砂油气出口管进行喷砂处理,清除表面氧化皮2.26 打磨打磨气体出口弯管外表面2.27 探伤测HB 按Ⅱ1572-00JT中的要求对油气出口管进行UT.MT.PT.HB检测。