从材料强度学的观点论机械零件疲劳寿命的优化
机械设计中的材料力学与疲劳分析
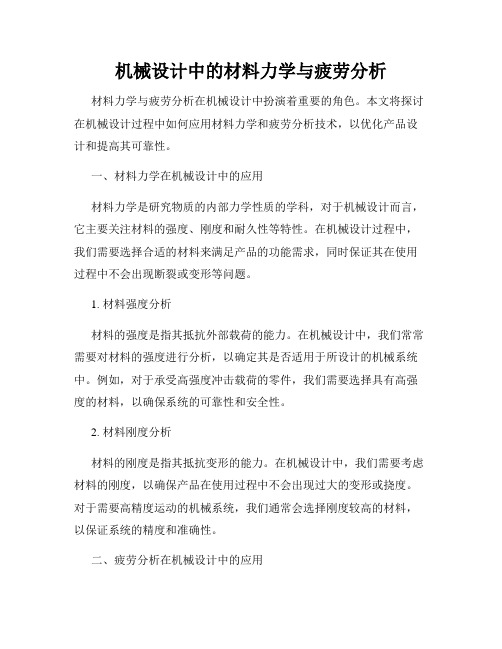
机械设计中的材料力学与疲劳分析材料力学与疲劳分析在机械设计中扮演着重要的角色。
本文将探讨在机械设计过程中如何应用材料力学和疲劳分析技术,以优化产品设计和提高其可靠性。
一、材料力学在机械设计中的应用材料力学是研究物质的内部力学性质的学科,对于机械设计而言,它主要关注材料的强度、刚度和耐久性等特性。
在机械设计过程中,我们需要选择合适的材料来满足产品的功能需求,同时保证其在使用过程中不会出现断裂或变形等问题。
1. 材料强度分析材料的强度是指其抵抗外部载荷的能力。
在机械设计中,我们常常需要对材料的强度进行分析,以确定其是否适用于所设计的机械系统中。
例如,对于承受高强度冲击载荷的零件,我们需要选择具有高强度的材料,以确保系统的可靠性和安全性。
2. 材料刚度分析材料的刚度是指其抵抗变形的能力。
在机械设计中,我们需要考虑材料的刚度,以确保产品在使用过程中不会出现过大的变形或挠度。
对于需要高精度运动的机械系统,我们通常会选择刚度较高的材料,以保证系统的精度和准确性。
二、疲劳分析在机械设计中的应用疲劳是指材料在循环载荷下出现的疲劳损伤和失效现象。
在机械设计中,我们需要对材料的疲劳行为进行分析,以确保产品在长期使用过程中不会出现疲劳失效。
1. 疲劳寿命分析疲劳寿命是指材料在特定载荷下能够承受的循环次数。
在机械设计中,我们可以利用疲劳寿命分析来预测材料在实际使用情况下的寿命。
通过对材料进行疲劳试验和数值模拟,我们可以确定最佳的材料选择和设计参数,以延长产品的使用寿命。
2. 应力集中分析应力集中是指材料中由于几何形状或载荷作用而引起的应力集中区域。
在机械设计中,我们需要对材料的应力集中情况进行分析,以避免应力集中导致的疲劳失效。
通过优化设计和加工工艺,我们可以减小或消除应力集中,提高产品的可靠性和耐久性。
三、材料力学与疲劳分析在机械设计中的综合应用材料力学和疲劳分析技术在机械设计中经常需要综合应用,以确保产品的性能和可靠性。
机械零部件的疲劳寿命分析与优化设计

机械零部件的疲劳寿命分析与优化设计概述机械零部件的疲劳寿命分析和优化设计对于确保机械设备的可靠性和使用寿命至关重要。
疲劳失效是导致机械零部件损坏和事故的主要原因之一。
本文将介绍疲劳寿命的概念和常见分析方法,并探讨如何通过优化设计提高零部件的疲劳寿命。
疲劳寿命概念疲劳寿命是指机械零部件在循环应力的作用下失效之前能够承受的循环应力次数。
循环应力是指零部件在交变荷载作用下所受到的应力变化。
疲劳寿命可以通过应力-寿命(S-N)曲线来表示,该曲线描述了应力水平和所能承受的循环次数之间的关系。
疲劳分析方法1. 应力分析:对于机械零部件,必须首先进行应力分析,确定零部件在使用条件下所受到的应力水平和变化。
2. 材料特性分析:机械材料的疲劳寿命与其材料特性密切相关。
通过对材料的化学成分和热处理工艺等进行分析,可以确定材料的疲劳强度和寿命。
3. 循环载荷分析:确定作用在机械零部件上的循环载荷,包括振动载荷、冲击载荷等。
在实际情况中,往往会有多种载荷同时作用在零部件上,需要综合考虑不同载荷对疲劳寿命的影响。
4. 疲劳寿命预测:根据应力分析和材料特性,利用疲劳寿命预测模型,可以预测机械零部件在给定载荷下的疲劳寿命。
优化设计方法1. 材料选择:选择具有较高疲劳强度和寿命的材料,可以提高零部件的疲劳寿命。
例如,使用高强度钢材代替低强度钢材,可以提高零部件的抗疲劳能力。
2. 结构设计:通过优化零部件的结构设计,可以降低应力集中和应力变化幅度,从而延长疲劳寿命。
例如,合理设计零部件的圆角和倒角,可以缓解应力集中现象。
3. 表面处理:通过表面处理方法,如喷砂、磨削等,可以改善零部件表面的粗糙度和残余应力分布,提高疲劳强度。
4. 使用条件优化:调整机械设备的使用条件,如减小振动幅度、合理控制载荷大小等,可以减小零部件的疲劳应力,延长其寿命。
案例分析以一台发动机连接杆为例,进行疲劳分析和优化设计。
首先,进行应力分析并确定连接杆在使用条件下的应力水平和变化。
机械零部件的材料强度分析与优化设计

机械零部件的材料强度分析与优化设计随着现代工业的发展,机械零部件的强度分析与优化设计对于保证机械设备的性能和寿命具有重要意义。
本文将探讨机械零部件材料强度分析的方法和优化设计的原则,以期为机械工程师提供实践指导。
一、材料强度分析的基本原理材料强度分析主要通过力学原理和材料力学性能参数来评估零部件是否满足工作条件下的荷载要求。
首先,我们需要了解机械零部件所承受的外部荷载,包括静载荷和动载荷。
静载荷指的是零部件在保持静止状态下所承受的荷载,如重力荷载;动载荷则指零部件在运动状态下所承受的荷载,如冲击荷载和旋转惯量。
其次,我们需要获取材料的力学性能参数,如屈服强度、抗拉强度、断裂韧性等。
这些参数可以通过材料试验和数据手册等途径得到。
其中,屈服强度指的是材料承受荷载时发生可逆塑性变形的最大强度;抗拉强度指的是材料承受拉应力时发生破坏的强度;断裂韧性则反映材料在发生断裂时的能量吸收能力。
最后,我们将应用力学原理,如受力分析、应力分析和变形分析等,来评估零部件的应力状态和变形情况。
通过比较零部件所承受的应力和材料的强度,我们可以确定材料是否具有足够的强度来满足设计要求。
二、材料强度分析的方法在进行材料强度分析时,我们可以采用有限元分析(FEA)和经验公式等方法。
有限元分析是一种广泛应用的计算方法,可以通过将零部件划分为许多小的有限元素来近似计算其应力和变形。
通过对有限元分析结果的研究,我们可以了解零部件的强度分布和哪些区域可能存在强度问题,从而进行优化设计。
除了有限元分析,我们还可以使用经验公式进行初步强度估算。
经验公式基于历史数据和经验规律,可以快速估计零部件的强度。
然而,需要注意的是,经验公式只能提供一个大致的估计,精确性相对较低,因此在实际设计中,建议结合有限元分析等方法进行综合评估。
三、材料强度分析的约束条件在进行材料强度分析时,我们还需要考虑约束条件对零部件强度的影响。
约束条件主要包括边界条件和几何条件。
机械设计中的材料强度与疲劳分析
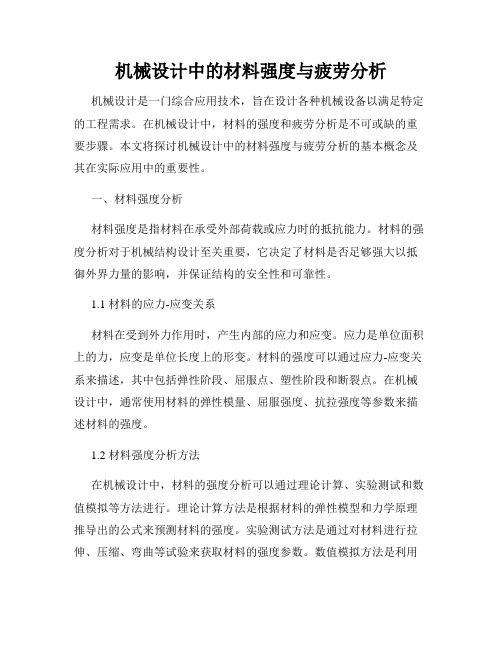
机械设计中的材料强度与疲劳分析机械设计是一门综合应用技术,旨在设计各种机械设备以满足特定的工程需求。
在机械设计中,材料的强度和疲劳分析是不可或缺的重要步骤。
本文将探讨机械设计中的材料强度与疲劳分析的基本概念及其在实际应用中的重要性。
一、材料强度分析材料强度是指材料在承受外部荷载或应力时的抵抗能力。
材料的强度分析对于机械结构设计至关重要,它决定了材料是否足够强大以抵御外界力量的影响,并保证结构的安全性和可靠性。
1.1 材料的应力-应变关系材料在受到外力作用时,产生内部的应力和应变。
应力是单位面积上的力,应变是单位长度上的形变。
材料的强度可以通过应力-应变关系来描述,其中包括弹性阶段、屈服点、塑性阶段和断裂点。
在机械设计中,通常使用材料的弹性模量、屈服强度、抗拉强度等参数来描述材料的强度。
1.2 材料强度分析方法在机械设计中,材料的强度分析可以通过理论计算、实验测试和数值模拟等方法进行。
理论计算方法是根据材料的弹性模型和力学原理推导出的公式来预测材料的强度。
实验测试方法是通过对材料进行拉伸、压缩、弯曲等试验来获取材料的强度参数。
数值模拟方法是利用计算机软件对材料的行为进行模拟和分析,可以提供更详细的应力、应变分布以及材料的破坏情况。
二、疲劳分析疲劳是指在周期性或交变性荷载作用下,材料发生的逐渐累积的微小损伤和失效现象。
疲劳问题在机械设计中经常出现,尤其对于那些在长时间内承受不断循环荷载的机械零件来说,如汽车发动机的曲轴、飞机的机翼等。
2.1 疲劳失效机理疲劳失效是由于材料在应力循环作用下产生微小的裂纹,随着荷载作用次数的增加,裂纹逐渐扩展,并最终导致材料的断裂。
疲劳失效的机理可以通过S-N曲线来描述,其中S表示应力幅,N表示应力循环次数。
S-N曲线是通过实验测试得到的,它描述了不同应力幅下材料的寿命。
2.2 疲劳寿命预测疲劳寿命预测是机械设计中的重要课题。
它利用S-N曲线和应力历程来预测材料在给定载荷条件下的疲劳寿命。
机械设计中的材料的疲劳与寿命研究

机械设计中的材料的疲劳与寿命研究引言:机械设计中的材料疲劳与寿命研究是一门重要而又复杂的学科,它关注的是材料在反复或持续加载作用下的疲劳性能及其寿命预测。
在现代工程中,材料的寿命是非常关键的因素,因为在实际应用中,机械零件和结构往往面临长时间的动态力加载,而疲劳失效是其主要的失效形式之一。
因此,了解机械设计中材料的疲劳与寿命研究对于确保机械的可靠性和安全性至关重要。
材料疲劳特性分析:材料的疲劳特性是指在外界作用下,材料在经历一定的循环次数后发生破坏或变形的性能。
疲劳特性的研究包括强度极限、疲劳强度、疲劳寿命等参数的测定与分析。
其中,强度极限是指材料能够承受的最大应力,疲劳强度是指材料在一定循环次数下承受的最大应力,疲劳寿命是指材料在特定应力水平下能够承受的循环次数。
疲劳失效原因:材料的疲劳失效是由于材料在受到循环载荷作用下,出现微小的裂纹,然后在裂纹的周围应力场的作用下逐渐扩展,最终导致材料的破坏。
疲劳失效具有随机性和蠕变性,即在同一应力水平下,疲劳寿命存在一定的分散性。
疲劳失效的原因主要有材料本身的弱点、裂纹形成和扩展、应力集中等。
材料的寿命预测方法:针对材料的疲劳与寿命研究,科学家们提出了多种预测方法。
其中,最为常用的是基于SN曲线的寿命预测方法。
SN曲线是指应力(S)和循环次数(N)之间的关系曲线。
通过对不同应力水平下材料的疲劳寿命进行试验,可以绘制出SN曲线,并用其来预测在给定应力水平下的疲劳寿命。
此外,还有基于损伤累积理论的疲劳寿命预测方法,它通过考虑裂纹扩展速率、损伤累积等因素来进行寿命预测。
材料寿命设计:在机械设计中,为了确保机械零件的寿命满足工程要求,必须对材料的疲劳寿命进行设计和优化。
一种常用的方法是通过应力分析和有限元分析来评估应力水平,并结合寿命预测方法进行寿命设计。
通过对零件结构进行改进,如改变几何形状、增加半径过渡等,可以减少应力集中,延长材料的疲劳寿命。
材料疲劳寿命的延长方法:在实际工程中,为了延长材料的疲劳寿命,我们可以采取多种方法。
机械结构的疲劳寿命评估与优化设计

机械结构的疲劳寿命评估与优化设计一、引言机械结构是各行业中广泛采用的一种设计形式,它承担着负载并保证系统的正常运行。
然而,由于长期工作负载引起的疲劳现象,机械结构的寿命成为了研究的重点之一。
本文将探讨机械结构的疲劳寿命评估与优化设计,希望能为相关领域的研究和应用提供参考。
二、机械结构的疲劳寿命评估机械结构的疲劳寿命评估是基于疲劳损伤积累的原理,通过对应力、载荷和材料等因素的分析,来评估机械结构在特定工况下的使用寿命。
常用的评估方法包括极限耐久度法和应力寿命法等。
极限耐久度法是通过寻找疲劳破坏的起始点,再利用经验公式或实验数据计算出机械结构的寿命。
它通过试验和统计方法,结合应力集中系数和载荷代表值,来确定结构的疲劳强度。
应力寿命法是通过将应力水平和循环次数的关系绘制成S-N曲线,然后根据实际工况下的应力范围来确定机械结构的疲劳寿命。
这种方法考虑了材料的强度和韧性,更加准确地评估了结构的疲劳寿命。
三、机械结构的优化设计为了提高机械结构的疲劳寿命,优化设计成为一种重要的手段。
优化设计旨在通过调整结构的几何形状、材料选择和工艺参数等,来改善结构的载荷分布和应力集中状况,从而延长机械结构的使用寿命。
在优化设计中,几何形状的调整是经常采用的方法之一。
通过改变结构的断面形状、角度和曲线等,可以减小应力集中和应力梯度,从而降低结构的疲劳损伤。
此外,还可以通过增加结构的支撑点、加强连接方式等手段,改善结构的载荷分布,提高其疲劳寿命。
材料的选择也对疲劳寿命具有重要影响。
不同材料的强度、韧性和疲劳极限等性能不同,在优化设计中需要根据具体工况选择合适的材料。
一般来说,高强度材料可以提高结构的抗疲劳能力,但是也会增加结构的成本和重量,需要综合考虑。
最后,工艺参数的选择也是优化设计的关键。
合理的工艺参数可以保证制造过程中的质量,并减小材料的缺陷和不均匀性,从而提高结构的疲劳寿命。
例如,采用合适的焊接方法和热处理工艺可以提升焊接接头的疲劳强度,延长结构的使用寿命。
机械工程中的材料疲劳与寿命分析
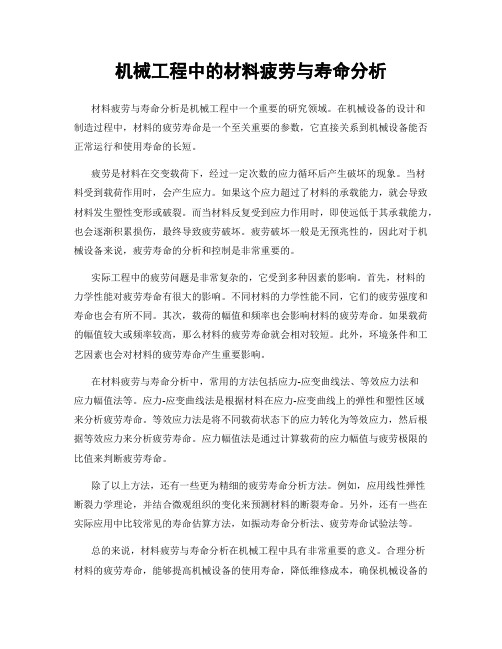
机械工程中的材料疲劳与寿命分析材料疲劳与寿命分析是机械工程中一个重要的研究领域。
在机械设备的设计和制造过程中,材料的疲劳寿命是一个至关重要的参数,它直接关系到机械设备能否正常运行和使用寿命的长短。
疲劳是材料在交变载荷下,经过一定次数的应力循环后产生破坏的现象。
当材料受到载荷作用时,会产生应力。
如果这个应力超过了材料的承载能力,就会导致材料发生塑性变形或破裂。
而当材料反复受到应力作用时,即使远低于其承载能力,也会逐渐积累损伤,最终导致疲劳破坏。
疲劳破坏一般是无预兆性的,因此对于机械设备来说,疲劳寿命的分析和控制是非常重要的。
实际工程中的疲劳问题是非常复杂的,它受到多种因素的影响。
首先,材料的力学性能对疲劳寿命有很大的影响。
不同材料的力学性能不同,它们的疲劳强度和寿命也会有所不同。
其次,载荷的幅值和频率也会影响材料的疲劳寿命。
如果载荷的幅值较大或频率较高,那么材料的疲劳寿命就会相对较短。
此外,环境条件和工艺因素也会对材料的疲劳寿命产生重要影响。
在材料疲劳与寿命分析中,常用的方法包括应力-应变曲线法、等效应力法和应力幅值法等。
应力-应变曲线法是根据材料在应力-应变曲线上的弹性和塑性区域来分析疲劳寿命。
等效应力法是将不同载荷状态下的应力转化为等效应力,然后根据等效应力来分析疲劳寿命。
应力幅值法是通过计算载荷的应力幅值与疲劳极限的比值来判断疲劳寿命。
除了以上方法,还有一些更为精细的疲劳寿命分析方法。
例如,应用线性弹性断裂力学理论,并结合微观组织的变化来预测材料的断裂寿命。
另外,还有一些在实际应用中比较常见的寿命估算方法,如振动寿命分析法、疲劳寿命试验法等。
总的来说,材料疲劳与寿命分析在机械工程中具有非常重要的意义。
合理分析材料的疲劳寿命,能够提高机械设备的使用寿命,降低维修成本,确保机械设备的可靠性和安全性。
随着材料科学和工艺技术的不断发展,材料疲劳与寿命分析方法也在不断创新和完善,为机械工程的发展提供了有力的保障。
机械设计中的疲劳寿命估算

机械设计中的疲劳寿命估算疲劳寿命估算是机械设计中一个重要的任务,它能够帮助工程师评估机械零件在长期使用过程中可能发生的疲劳破坏。
合理的疲劳寿命估算可以减少机械故障的发生,提高机械设备的可靠性和安全性。
本文将从疲劳寿命的定义、影响因素以及估算方法三个方面进行探讨。
一、疲劳寿命的定义疲劳寿命是指机械零件在循环加载下能够承受的次数,即在特定的载荷条件下,零件发生疲劳破坏前所经历的循环次数。
一般来说,疲劳寿命的表达方式为Nf,单位可以是次数、小时或循环。
二、影响疲劳寿命的因素1.应力水平:应力是导致疲劳破坏的主要原因之一,较高的应力水平会导致疲劳寿命的显著缩短。
2.材料性能:材料的强度、韧性等性能对疲劳寿命有着重要影响。
一般来说,强度较高、韧性较好的材料疲劳寿命相对较长。
3.工作环境:工作环境的恶劣程度、温度、湿度等因素也会对零件的疲劳寿命产生影响。
在腐蚀性环境中工作的零件疲劳寿命通常更短。
4.载荷类型:对于不同类型的载荷,疲劳寿命也会有所不同。
多变载荷和单纯应力载荷下的疲劳寿命表现不同。
5.几何形状:零件的形状、尺寸以及表面质量等也会对疲劳寿命造成一定影响。
三、疲劳寿命估算方法1.基于SN曲线的估算方法:SN曲线是疲劳寿命估算方法中最为常用的一种方法。
它通过试验得到零件在不同循环次数下的应力水平,进而建立起应力水平与疲劳寿命之间的关系曲线。
根据实际工况下的应力水平,可以通过插值或外推的方法预估零件在特定条件下的疲劳寿命。
2.统计学方法:统计学方法是一种基于概率统计理论的疲劳寿命估算方法,它考虑到了不确定性因素对疲劳寿命的影响。
通过统计样本数据,建立概率密度函数或累积分布函数,从而得到零件在一定概率范围内的疲劳寿命。
3.有限元方法:有限元方法是一种基于数值模拟的疲劳寿命估算方法。
它通过建立零件的有限元模型,并考虑材料本构关系和载荷工况,利用有限元软件对零件的应力分布进行分析,从而计算出疲劳寿命。
总结:疲劳寿命估算是机械设计中不可忽视的一环,它可以帮助工程师评估零件的使用寿命和可靠性。
- 1、下载文档前请自行甄别文档内容的完整性,平台不提供额外的编辑、内容补充、找答案等附加服务。
- 2、"仅部分预览"的文档,不可在线预览部分如存在完整性等问题,可反馈申请退款(可完整预览的文档不适用该条件!)。
- 3、如文档侵犯您的权益,请联系客服反馈,我们会尽快为您处理(人工客服工作时间:9:00-18:30)。
2、传统的用材观念
“为了使用安全,过份追求材料的塑性和冲击韧性, 不息牺牲强度”;
后果是: (1)使用的材料强度水平低,疲劳寿命低,造成机 器粗大笨重;
(2)追求过大的一次冲击韧性,即使在承受小能量
冲击载荷场合下,使用寿命不长,也并不安全。
4
3、新的材料强度学观点
“材料的多次冲击疲劳抗力主要取决于以
2、降低 3、降低 Si﹤0.05-0.09% Mn﹤0.5%
4、加入Cr、Mo合金元素 5、Al、Ti、Ni或V、Nb微合金化
31
7、某一零件不同部位的应力状态要求不同的强、塑、 韧合理配合
闪光对焊焊头 HRC36 37 39 40
44
46 B处正断部位
A处 剪切断裂部位
1)园环链可能发生的断裂部位
7
13.2 8.7 4.9
二、强、塑、韧合理配合与优化选 材、用材
1、应力状态与合理选材、用材
1)、拉、压、弯扭载荷的应力状态 应力状态的表征: 软性系数α =
t max max
零件在外加载荷作用下,其内部的某一点的最大应 力可分为最大切应力(tmax)和最大正应力σ max
8
“软性”应力状态
1)、当α <1拉伸、弯曲载荷时的材料设计
在适当提高使用强度水平的同时,要求较高塑性、韧性相 配合。 ↑σ s、 σ b+较高的δ、ak、
采用中、低碳钢、合金钢高温或中温回火。
10
2)、当α ﹥1扭转载荷时的材料设计
进一步提高材料使用强度水平,要求一定的塑性、韧性配合。 ↑σ s、 σ b+一定的δ、ak、
1.5Mn13)是制作坦克,拖拉机履带板等的传统材料。 可用低碳马氏体合金钢制作履带板、斗齿等零件。 21
2)、用材——论钢的回火
104 N ↑ 103
A1﹥A2 ﹥A3 ﹥A4 A4 A3 A2 A1
102 300 400 500 600
℃
50钢回火温度及不同能量下的多次冲击断裂周次的关系。 规律是: 随着A↓,所对应的最佳回火向低温方向转移。
多 次 冲 击 断 裂 次 数 N
钝缺口试样 104 滚压力1.5KN 材料40Cr 103
缺口未滚压
102 300 400 500 回火温度℃ 不同回火温度下滚压对提高多次冲击疲劳寿命的效果
在缺口未滚压前,40Cr钢淬火后获得最佳多次冲击疲劳寿命的回火温度为400℃中温回火。 在缺口滚压形变强化后,40Cr钢获得最佳多次冲击疲劳寿命的回火温度为200℃即低温回火。
17
[例1]45钢与球墨铸铁的选择
σ s MPa ﹥600 ﹥600 σ b MPa ﹥340 ﹥420 δ% ﹥16 ﹥2 aKKg-m/cm2 ﹥8 ﹥1.5
冲 击 能 量 A J
5.0
45钢
球墨铸铁 2.5
45钢调质 球墨铸铁 结果说明: 球墨铸铁的塑性、韧性虽说很低,但对于按无限疲劳寿命设 计的某些零件如曲轴、连杆可以采用球墨铸铁取代45钢制 造。
350℃
500℃
最佳da/dn的回火温度向高温
方向移动。
回火温度 40CrNiMO钢 淬火后不同温度回火
25
3)、Kt与钢的疲劳强度
Kt-σ -1、σ
弯 800 曲 疲 600 劳 强 度 400 200 0 600 2000 1500 1000 抗拉强度,σ b(MPa)
-1n的关系
, -1n
强度为主,要求一定的塑性和韧性配合”。
为了获得最佳的疲劳寿命,必须根据零件的
不同服役条件,通过不同的回火温度调节出 最佳的材料强、塑、韧合理配合”。
5
[实例]提高一吨模锻锤锤杆使用寿命的工程试验
锤杆Φ 120×2360mm;205公斤重。
原来使用情况:
30CrMnSi或30CrNi3A优质合金钢, 淬火后650 ℃高温回火,250-300HB 使用寿命 1个月左右
200
经表面形变强化后,最佳回火温度由中温回火向低温回火方向转移。
29
6、提高使用强度σ b水平与延迟断裂强度的关系
1)、延迟断裂的概念
延迟断裂 是在静止应力作用下的 材料,经过一定时间以 后,突然脆性破坏的一 种现象,是氢致脆化的 结果。
2500 延 2000 迟 断 1500 裂 强 1000 度 M 500 P a 0
20
[例4]高锰奥氏体钢与低碳马氏体钢的选择
J
Mn13(奥氏体)
钢种及热处理 Mn13奥化体钢 1050℃淬火 27SiMn低碳马氏体 920 ℃淬火 200 ℃回火
A ↑
3.5 27SiMn低碳马氏体
σs MPa ≥ 560 1670
ψ % ≥ 15 10.1
ak KgM/Cm2 ≥ 20 3.2
σs
MPa 895
σb
MPa 1040
ψ
% 41
60Si2Mn
A(J)
2150
2300
1
104
105
N
内六角凸模(M18-20)冷墩材料: W18Cr4V钢 寿命 ﹤100件 60Si2Mn钢 寿命 1000件 失效形式由断裂转变为磨损。 在高的多次冲击能量作用下,可采用塑 性、韧性好的弹簧钢作冷墩模。
采用中碳钢、中碳合金钢中温回火。
3)、当α ﹥1压缩载荷时的材料设计
要求高的强度、硬度,可以使用应用硬而脆的材料。
11
3)、实例: 举例[1]滚动轴承
用高碳合金钢Gcr15、淬火、低温回火;甚至用陶瓷轴承。
举例[2]弹簧
钢板弹簧受弯曲α =0.75,采用60si2mn,高温回火363-457HB 螺旋弹簧受扭转应力α =1,采用50Crv,中温回火427-514HB
(a)轴承钢(b)20CrMo钢渗碳淬火后不同温度回火 14
3)、滑动磨粒磨损与多次冲击磨粒磨损
各种碳钢经淬火,180 ℃回火后的磨损试验结果 1、滑动磨粒磨损的情况下,钢的含碳量越高,磨损量越小。 2、多次冲击磨粒磨损的情况下,T8钢(0.8%)的磨粒磨损量最小,位于磨损曲线上的低谷。
15
4)、一般常咬合渗碳齿轮的表面硬度要求HRC58-63
当tmax> σ max(α >1)时
“硬性”应力状态
当tmax< σ max(α < 1)时
不同载荷下的α
缺口拉伸 单向拉伸 α=0. 5 硬性应力状态
不同
弯曲 扭转 单向压缩
α=0.25
α=0. 74
较软
α=1
α=2
软性应力状态
应力状态α
不同,选材、用材的原则也不同
9
2)、不同应力状态,有不同的强、塑、韧合理配合
22
不同含碳量的钢多次冲击疲劳抗力高峰所对应的最佳回火温度。 规律是: 1)随着%C↑,最佳回火温度向高温方向转移。 2)反之, %C↓,最佳回火温度向低温方向转移。
23
4、不同应力集中系数(Kt)与选材、用材
1)、缺口应力系数Kt↑,对应最佳多次冲击疲劳 的回火温度向中温回火方向移动。
例如:40钢的多次冲疲劳试验结果
对于承受多次冲击的变速箱换齿轮则须降至HTC56-60 综上,拉,压、弯、扭十多次冲击加载性质时,选材,用 材就略有不同。
16
3、不同的载荷(A冲击能量或σ 应力) 大小与选材、用材
1)、与选材——论按用途分类选材原则的局限性
不同的冲击能量(A)作用下,不同强、塑、韧配合材 料的冲击疲劳抗力不同,选择材料的合理性也不同,例如:
12
2、同一载荷,不同加载性质与选材、用材
当拉、压、弯、扭十多次冲击的场合: 1)、弯曲疲劳(脉动弯曲疲劳与多次冲击弯曲疲劳极 限的差异)
钢号及工艺 45钢正火 40Cr淬火200 ℃回火
缺口脉动弯曲疲劳极限 σ -1 Mpa 225 340
多次冲击弯曲缺口疲劳极限 σ -1 Mpa 105不断为基数 181 282
从材料强度学的观点论机械零 件疲劳寿命的优化
中国工程院院士 四川大学 教授
涂铭旌
2009.04.04
1
一、材料的强度、塑性、韧性 与使用寿命的辩证关系
1、材料的强度与塑、韧性及其异变关系
材料的强度、塑性、韧性判据
强度σs 、 σ b(Mpa) 塑性δ 、ψ (%) 韧性冲击α k (kg-M/cm2 → J); 断裂韧性K1c(Mpa m )
A可能发生剪切断裂。 B处为闪光对焊接头,可能
发生脉动拉应力疲劳断裂。
2)同一零件不同的A、B两部位 由于所处的应力状态不同,相应地各自 所要求的强、塑、韧配合也不同。 A处属软的应力状态; B处属硬的应力状态。
32
3)设计强、塑、韧配合两全的热处理工艺
为了实现热处理后不同部位硬度的有利分布。
2
钢材经淬火、回火后,强度与塑性、韧性比消彼长
σs 、 σ b ↑↓ δ 、 α k ↑↓
40Cr淬火、不同温度回火的机械性能
840℃淬火 后回以温度 200 ℃回火 390 ℃回火 500 ℃回火 670 ℃回火
硬度 HRC 50 45 35 24
σs Mpa 1610 1400 1060 725
6
断口失效分析:
受大压-小拉+弯曲复合交变应力,经历几十 万次多次冲击疲劳断裂。 改进技术措施:
热处理方案 供应状态40Cr钢材 40Cr淬油、650 ℃回火 40Cr淬油、500 ℃回火 40Cr淬油、450 ℃回火 冲击韧性αk kg-M/cm2 9.0 使用寿命 17天(25.5万次) 33天(49.5万次) 半年未断 4个月未断
σb Mpa 2005 1500 1120 810
δ % 6.4 11.1 13.7 22.9
ψ % 15.5 52.3 57.8 68.4