加工余量、工序尺寸与工序公差的确定
3-5加工余量、工序间尺寸及其公差的确定

例: 某车床主轴箱箱体的主轴孔的设计要求是:
180
,R 0.018
0.007
a
1.25m,试确定孔加工的加工方案及
工序尺寸。
解:从孔的最终要求 Ra 1.25m
T 0.018 (0.007) 0.025
可确定孔的终加工方法。
180 0.018 0.007
内孔表面加工方案及其经济精度
加工总余量与工序余量的关系
n
Z0 Z1 Z2 Zn Zi i 1
● 单边余量与双边余量
双边余量:对于外圆和孔等旋转表面而言,加工余量
是从直径上考虑的,即加工余量在直径方向上是对称
分布的,实际所切除的金属层厚度是直径上加工余量
的一半,故称为对称余量(即双边余量)。
双边余量
工序尺寸及 偏差
浮动镗
0.2
IT6 T=0.025
Φ180
180 0.018 0.007
精镗孔
0.6
IT7 T=0.04
Φ179.800 179 .800.040
半精镗孔
3.2
粗镗孔
6
毛坯孔
IT9 T=0.10 IT11 T=0.25
Φ179.200 Φ176.000
Φ168.000
179 .200.100
双边余量
轴
z1 2
50
0 0.011
z1 2
54
0 0.10
被包容尺寸
孔
z1
50
0.10 0
z1
2
54
0.011 0
2
包容尺寸
单边余量:对于平面的加工, 余量则是单边余量,它等于实 际所切除的金属层厚度。
加工余量及工序尺寸和公差的确定
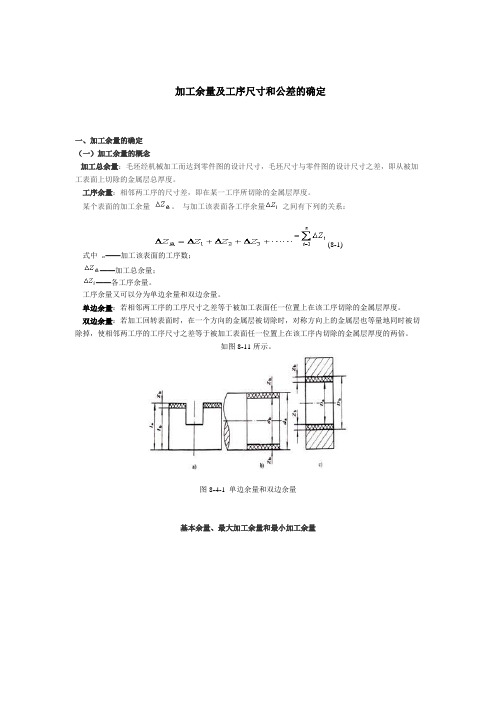
加工余量及工序尺寸和公差的确定一、加工余量的确定(一)加工余量的概念加工总余量:毛坯经机械加工而达到零件图的设计尺寸,毛坯尺寸与零件图的设计尺寸之差,即从被加工表面上切除的金属层总厚度。
工序余量:相邻两工序的尺寸差,即在某一工序所切除的金属层厚度。
某个表面的加工余量。
与加工该表面各工序余量之间有下列的关系:(8-1)式中——加工该表面的工序数;——加工总余量;——各工序余量。
工序余量又可以分为单边余量和双边余量。
单边余量:若相邻两工序的工序尺寸之差等于被加工表面任一位置上在该工序切除的金属层厚度。
双边余量:若加工回转表面时,在一个方向的金属层被切除时,对称方向上的金属层也等量地同时被切除掉,使相邻两工序的工序尺寸之差等于被加工表面任一位置上在该工序内切除的金属层厚度的两倍。
如图8-11所示。
图8-4-1 单边余量和双边余量基本余量、最大加工余量和最小加工余量a) b)图8-4-2 基本余量、最大余量和最小余量加工余量变化的公差等于上道工序的工序尺寸公差与本工序的工序尺寸公差之和。
即(8-2)各个加工余量与相应加工尺寸的关系如图8-4-3所示。
图8-4-3 加工余量与相应加工尺寸(二)影响加工余量的因素1.上道工序加工表面(或毛坯表面)的表面质量包括表面粗糙度高度和表面缺陷层深度;2.上道工序的尺寸公差3.上道工序的位置误差4.本工序的安装误差(三)确定加工余量的方法1. 计算法此法是根据一定的资料,对影响加工余量的各项因素进行分析计算,然后综合考虑计算出来的,多用于大批大量生产,计算公式如下:对双边余量:(8-3)对单边余量:(8-4)一般取2. 查表法以工厂的实际生产经验及工艺实践积累的有关加工余量的资料数据为基础,结合具体加工方法进行适当修正而得到加工余量的方法。
3. 经验法根据工艺人员的经验来确定加工余量的方法。
二、工序尺寸和公差的确定一般情况下,加工某表面的最终工序的尺寸及公差可直接按零件图的要求来确定。
工序余量与工序尺寸及其公差的关系余量公差

1.上工序留下的表面粗糙度值 R(Z 表 面轮廓的最大高度)和表面缺陷层深度Ha
本工序必须把上工序留下的表面粗糙
度和表面缺陷层全部切去,如果连上一道
工序残留在加工表面上的表面粗糙度和表
面缺陷层都清除不干净,那就失去了设置
本工序的本意了。由此可知,本工序加工余
量必须包括 R z和 Ha这两项因素。
2.上工序的尺寸公差 Ta 由于上工序加工表面存在尺寸误差, 本工序加工余量必须包括 Ta 项。
第三节 加工余量与工序尺寸的确定
一、加工余量 (一)概述 用去除材料方法制造机器零件时,一
般都要从毛坯上切除一层材料之后最后才 能制得符合图样规定要求的零件。
加工余量:毛坯上留作加工用的材料 层,称为加工余量。
加工 总余量 余量 工序余量 单边余量:如图a)
双边余量:如图b)、c)
对于非对称表面,其加工余量用单边余 量 Zb 表示。对于外圆与内圆这样的对称表 面,其加工余量用双边余量2 Zb表示。
3.Ta 值没有包括的上工序留下的空间位
置误差 e a
工件上有一些形状误差和位置误差是没
有包括在加工表面的工序尺寸公差范围之内
的。在确定加工余量时,必须考虑它们的影
响,否则本工序加工将无法全部切除上工序
留在加工表面上的表面粗糙度和缺陷层。
4.本工序的装夹误差 b
如果本工序存在装夹误差 b(包括定位误差、 夹紧误差),则在确定本工序加工余量时还应考虑
由于工序尺寸有偏差,各工序实际切除 的余量值是变化的,故工序余量有:
公称余量(简称余量); 最大余量和最小余量。 例:
工序余量与工序尺寸及其公差的关系
余量公差:Tz=Zmax-Zmin=Ti+Ti-1 例:
加工余量、工序尺寸及其公差的确定
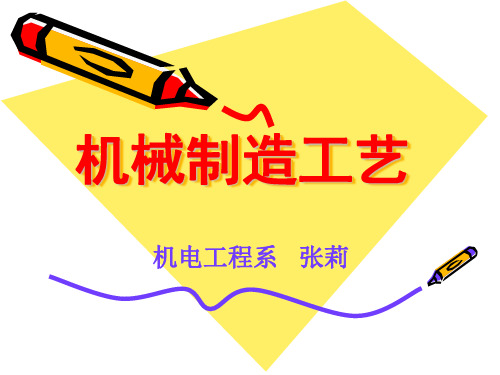
4.工序尺寸及其公差的确定
1)基准重合时,工序尺寸及其公差的计算 基准重合时, 生产上绝大部分加工面都是在基准重合( 生产上绝大部分加工面都是在基准重合(工艺基准和设计 基准重合)的情况下进行加工的, 基准重合)的情况下进行加工的,基准重合情况下工序尺寸与 公差的确定过程如下: 公差的确定过程如下: (1)确定毛坯总余量和各加工工序的工序余量 (2)确定工序基本尺寸 (3)确定工序公差 (4)标注工序尺寸公差 最终加工工序尺寸的公差按设计尺寸标注 的公差按设计尺寸标注, 最终加工工序尺寸的公差按设计尺寸标注,其余工序尺寸 公差按“入体原则”标注。 公差按“入体原则”标注。
4.工序尺寸及其公差的确定
1)基准重合时,工序尺寸及其公差的计算 基准重合时, 生产上绝大部分加工面都是在基准重合( 生产上绝大部分加工面都是在基准重合(工艺基准和设计 基准重合)的情况下进行加工的, 基准重合)的情况下进行加工的,基准重合情况下工序尺寸与 公差的确定过程如下: 公差的确定过程如下: (1)确定毛坯总余量和各加工工序的工序余量 (2)确定工序基本尺寸 (3)确定工序公差 最终加工工序尺寸公差等于设计尺寸公差, 最终加工工序尺寸公差等于设计尺寸公差,其余各加工 等于设计尺寸公差 工序按各自所采用加工方法的加工经济精度确定工序尺 寸公差。 寸公差。
3、加工余量的确定 1)分析计算法 2)查表修正法
根据生产实践和试验研究, 根据生产实践和试验研究,已将毛坯余量和各种工序的工 序余量数据汇集于手册。确定加工余量时,可从手册中获 序余量数据汇集于手册。确定加工余量时, 得所需数据,然后结合工厂的实际情况进行修正。 得所需数据,然后结合工厂的实际情况进行修正。查表时 公称值, 应注意表中的数据为公称值 对称表面(轴孔等) 应注意表中的数据为公称值,对称表面(轴孔等)的加工 余量是双边余量,非对称表面的加工余量是单边余量。 余量是双边余量,非对称表面的加工余量是单边余量。这 双边余量 的加工余量是单边余量 种方法目前应用最广。 种方法目前应用最广。
加工余量工序尺寸与工序公差的确定

加工余量工序尺寸与工序公差的确定加工余量是指在零件加工过程中为了保证零件尺寸精度而故意留下的一定尺寸余量。
而工序尺寸和工序公差的确定则是指在加工零件时,根据零件的设计要求和加工工艺,确定每个加工工序的尺寸和公差范围。
这两个问题在零件加工过程中起着非常重要的作用,对于保证零件的质量和精度具有至关重要的意义。
首先,我们来看看加工余量的作用。
在零件加工过程中,由于材料的变形、工艺的限制、加工设备的精度等因素,很难保证每个零件的尺寸都能精确到设计要求的尺寸。
因此,为了保证零件的尺寸精度,加工余量就显得非常重要了。
通过在零件尺寸上留下一定的余量,可以在后续的加工工序中进行修正,从而保证零件的最终尺寸能够达到设计要求。
同时,加工余量还可以在一定程度上弥补加工过程中可能出现的误差,提高零件的加工精度。
而工序尺寸和工序公差的确定则是在加工零件的每个工序中,根据零件的设计要求和加工工艺,确定每个工序的尺寸和公差范围。
这一步工作对于保证零件的加工精度和质量至关重要。
在确定工序尺寸和公差时,需要考虑到材料的性质、加工工艺的特点、加工设备的精度等因素。
只有合理确定了工序尺寸和公差,才能保证每个工序加工出来的零件都能满足设计要求,从而保证整个零件的质量和精度。
在实际的零件加工过程中,确定加工余量、工序尺寸和公差是一个比较复杂的工作。
首先,需要对零件的设计要求进行充分的了解和分析,明确每个尺寸的重要性和影响因素。
其次,需要对加工工艺和加工设备进行全面的评估,了解其加工精度和加工能力。
最后,需要根据实际情况,结合经验和技术,确定合理的加工余量、工序尺寸和公差范围。
在确定加工余量时,需要考虑到零件的材料、加工工艺和加工设备的精度等因素。
一般来说,对于精密零件,加工余量要尽量小,以减少修正工序的次数,提高加工效率和精度;而对于一般零件,加工余量可以适当放大,以提高加工的容错能力。
在确定工序尺寸和公差时,需要充分考虑到每个工序的加工精度和工艺特点,尽量减小工序间的误差传递,保证每个工序加工出来的零件都能满足设计要求。
加工余量与工序尺寸的确定和基准--2011
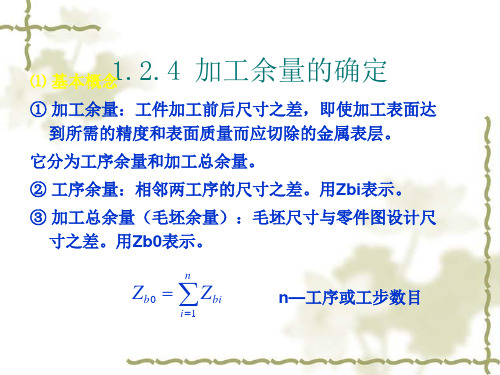
极限尺寸的计算:
A0max Az max Aj min
A0min Az min Aj max
⑵ 工序尺寸及其公差的确定 ① 工序基准与设计基准重合,即对同一表面进行多
次加工
这种工序尺寸计算较简单,只需根据各工序的加 工余量就可以算出各工序的基本尺寸。其计算顺 序是由最后一道工序开始逐步向前推算。 例:加工某一个钢制零件上的一个孔,其设计尺 0 寸为 72.50.03 mm,表面粗糙度为Ra0.4。现经过 粗镗、半精镗、精镗、粗磨和精磨五次加工,计 算各次加工的工序尺寸及其公差。
b
极值法——内表面(平面)加工
Z bj b j S j bmin S min Z b max Tb Z b min TS Z b max bmax S min Z bj Tb Z b min bmin S max Z bj TS TZ Z b max Z b min Tb TS
Z b max S max bmax Z b min S min bmin Z bj Z b max S max bmax S min TS bmin Tb Z b min TS Tb TZ Z b max Z b min TS Tb
max
DS DS
min
2Z bj Tb 2Z bj TS
min
max
2TZ 2 Z b max 2 Z b min Tb TS
误差复映计算法
根据误差复映规律,当上工序的工序尺寸是 最大时,本工序亦将是最大尺寸,反之亦然。
误差复映法——外表面(平面)加工
工序 名称 精磨 粗磨 精镗 半精 镗 粗镗 毛坯
14-4 加工余量、工序间尺寸及公差的确定
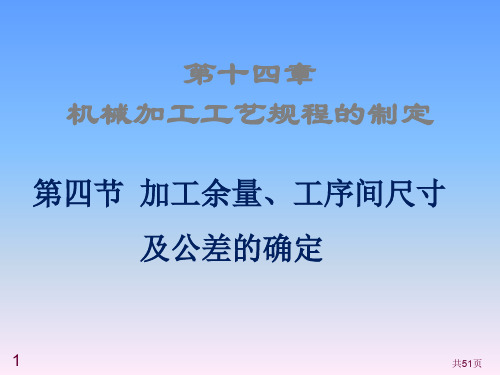
TZ = Zmax – Zmin=Tb+Ta
TZ :工序余量公差; Zmax :工序最大余量;
本道工序基本尺寸
Zmin:工序最小余量; Tb:本道工序的工序尺寸公差;
上道工序基本尺寸
Ta:上道工序的工序尺寸公差。
12
加工方向
共51页
工序尺寸及偏差
一般情况下,工序尺寸的公差按“入体原 则”标注。即 ——对被包容尺寸(轴的外径、实际长、宽、 高),其最大加工尺寸就是基本尺寸,上偏差 为零。 ——对包容尺寸(孔的直径、槽的宽度),其最 小加工尺寸就是基本尺寸,下偏差为零。 ——毛坯尺寸公差按双向对称偏差形式标注。
机床夹具的选择主要考虑生产类型。 (1)单件小批量生产应尽量选用通用夹具; (2)大批大量生产时,应采用高生产效率的专 用机床夹具;
此外,夹具的精度应与零件的加工精度相适应。
42
共51页
3.刀具的选择
刀具的选择主要取决于: 工序所采用的加工方法 加工表面的尺寸大小 工件材料 要求的加工精度 表面粗糙度 生产率 经济性
二、加工余量的确定
3. 经验法
由一些有经验的工程技术人员或工人根 据经验确定加工余量的大小。由经验法 确定的加工余量往往偏大,这主要是因 为主观上怕出废品的缘故。这种方法多 在单件小批生产中采用。
31
共51页
三、工序尺寸与公差的确定
生产上绝大部分加工面都是在基准重合(工艺基准和设计基 准重合)的情况下进行加工。现介绍如下: 1. 确定各加工工序的加工余量
6
共51页
双边余量
2Zi = li–1 – li
式中
Zi——本道工序的工序余量; li——本道工序的基本尺寸; li–1——上道工序的基本尺寸。
加工余量、工序尺寸与及公差的确定
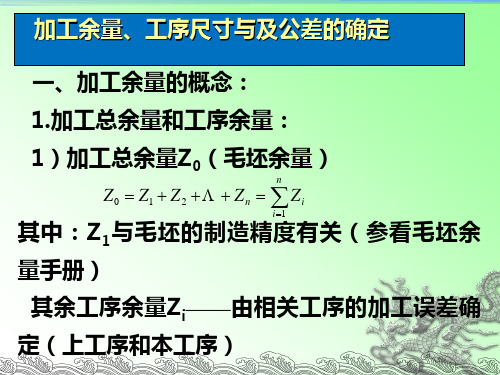
差的选择与标注按:公差等级、配合种类来确 定上下偏差)。
工序余量示意图(图1-40) 1) 轴类尺寸,毛坯 2) 孔类尺寸:毛坯:
2.影响加工余量的因素: 1)上工序的尺寸公差参看图4-21(工序1
余量与毛坯精度有关) 2)上工序的粗糙度Ry和缺陷层Ha(表4-10) 3)上工序的空间误差ea(形状位置误差)
i 1
• 总余量不够,质量得不到保证
• 总余量太大,增加劳动量、消耗、成本
• 总余量与毛坯精度、生产类型、批量大小 有关
机加械工余制量造的工确定艺与机床夹具
2.影响加工余量的因素
• 上道工序的表面质量(包括表面粗糙度Ha 和表面破坏层深度Sa)
• 前道工序的工序尺寸公差(Ta) • 前道工序的位置误差(ρa ) • 本工序工件的安装误差(εb) • 本工序的加工余量必须满足下式:
1、与设计尺寸有关的工序尺寸L01¨、L1¨。 2、中间工序尺寸(与余量有关)Z4、Z5、Z6 3、查找工艺尺寸链,画尺寸链图¨ (三)计算项目 1、确定公差与余量(经济精度与调整) 2、计算余量变动量,平均余量,平均工序尺 寸。 注:粗加工工序毛坯余量较大,可不计算。 3、按“入体”原则标注工序尺寸。
尺寸链中封闭环只有一个,用L0表示。 工艺尺寸链中的封闭环的定义见P.53倒10行。
⑴封闭环一定是工艺过程中间接保证的尺 寸。
⑵封闭环公差值最大,它等于各组成环公 差之和。
3)组成环——尺寸链除封闭外其余各环, 组成环分为增环和减环。
⑴增环—该环变动引起封闭环同向变动。 ⑵减环—该环变动引起封闭环反向变动。
例:图4-22轴线弯曲造成的余量不均匀误差。 各项位置误差造成的影响参看表4-11
- 1、下载文档前请自行甄别文档内容的完整性,平台不提供额外的编辑、内容补充、找答案等附加服务。
- 2、"仅部分预览"的文档,不可在线预览部分如存在完整性等问题,可反馈申请退款(可完整预览的文档不适用该条件!)。
- 3、如文档侵犯您的权益,请联系客服反馈,我们会尽快为您处理(人工客服工作时间:9:00-18:30)。
5.4.2确定加工余量的方法
1.分析计算法
2)无心磨床磨外圆时无装夹误差,公式 可简化为: Z m T ia n 2 ( R y H a ) 2 |a |
砂轮 工件
导轮
托板
5.4.2确定加工余量的方法
3)精密加工方法如研磨、珩磨、 超精加工等,加工时仅去掉上 工序留下的加工痕迹,公式可 简化为:
5.4.1加工余量的概念
工序余量的计算公式:
对于单边余量:
Z m T ia n R y H a |a b |
对于双边余量:
Z m T i a n 2 ( R y H a ) 2 |a b |
5.4.2确定加工余量的方法
1.分析计算法
1)采用浮动镗刀镗孔或浮动铰刀铰孔或拉刀拉孔,由 于这些方法不能纠正位置误差,公式可简化为:
1.6
半精 镗
1.5 H11(00.1大19粗).孔余头5镗m3,量孔m.2余确为为量4定剖.65大:1分.m2-m头0孔.,7=孔,6毛0.的5定坯直为尺径6寸0总.500.19 60.500.15
3.2
粗镗
2
H12(00.44) .偏56差-.31为.5-60010..5..-5771.-5=059.3-0.0509030.=4 2
粗镗—半精镗—精镗 —细镗—滚压
试确定各工序的工序尺 寸及其公差,以及表面 粗糙度。
(1)确定总余量和工序余量
初定工序
工序
以入体单
工序 名称
余量 mm
基本工序尺寸
经济精度 Mm
2粗R)a糙/μ度m确定各工mm序余量
向公差标注 mm
细滚镗压余工量序:余量。根据试验 滚压 0.003 H6(00.018) 查定0表.为4 确0.定00为3m0m.3mm
总余量与工步余量之 间的关系:
粗刨Z1 精刨Z2 磨Z3
n
Z s Z i i 1
H1 H2
Zs H设 H坯
式中:Zs—某加工表面的总余量; n—该表面的机械加工工序(工步)数; Zi—该表面第i个工序(工步)的加工余量。
5.4.1加工余量的概念
设某加工表面上道工序的尺寸为a,本道工序的尺寸 为b,则本道工序的基本余量Zb可以表示为:
余量公差:Tz=Zmax-Zmin=Ta+Tb
5.4.1加工余量的概念
5.4.1加工余量的概念
3.加工余量及工序尺寸公差对机械加工的影响 加工余量过大,不仅增加了机械加工量、降低了生产
效率,而且浪费原材料的能源,增加刀具等到工具 消耗,使加工成本提高。 加工余量过小,则不能保证消除前工序的各种误差和 表面缺陷层。
加工余量、工序尺寸与工序公差的确定
5.4.1加工余量的概念
1.加工总余量与工序(工步)余量
加工总余量(即毛坯余量):是指毛坯尺寸与零件设 计尺寸之差,也就是某加工表面上切除的金属层总厚 度。
工序(工步)余量:是指相邻工序(工步)的尺寸之 差,也就是某道工序(工步)所切除的金属层厚度。
5.4.1加工余量的概念
设计要求
61.500.018
0.4
细镗的下道工序为滚压,
细镗 精镗
0.3 H6(00.018) 0.8 0.7 H9(00.046) 1.6
对于被包容面: Zb=a-b 对于包容面:Zb=b-a
工序余量有单边余量 和双边余量之分。
5.4.1加工余量的概念
5.4.1加工余量的概念
2.最大余量、最小余量、平均余量、余量公差
最大余量:Zmax=amax-bmin(被包容尺寸) Zmax=bmax-amax(包容尺寸)
最小余量:Zmin=amin-bmax (被包容尺寸) Zmin=bmin-amax (包容尺寸)
3)除终加工工序外,根据各工序的加工方法及其经济加 工精度,确定其工序公差和粗糙度。
4)按入体原则以单向偏差方式标注工序尺寸,并可作适 当调整。
5.4.3工序尺寸及公差的确定
例5.1
某连杆大头孔的设计尺
寸为 61.500.018 (IT6),
表面粗糙度Ra0.4μm,
61.500.0
1毛8 坯为锻件,采用的加 工路线为:
ZminRyHa(单边 )
Zmin2(RyHa)(双)边
5.4.2确定加工余量的方法
4)对于抛光,仅用于提高表面粗糙度,因此
Zmin2Ry(双边 ) ZminRy(单边 )
5.4.2确定加工余量的方法
2.查表法
根据《机械加工工艺手册》提供的资料查出各 表面的总余量及不同加工方法的工序余量, 方便迅速,使用广泛。
工序公差给的过小,无形中提高了加工精度,增加了 工序的加工成本。
上工序公差给的过大,会使余量变动量大,有可能会 影响本工序的加工质量;当用夹具定位夹紧时,可 能会因尺寸变动太大而不能确保安装。
5.4.1加工余量的概念
4.影响工序余量的因素 1)前工序留下的表面粗糙度Ry和表面缺陷层深
度Ha 2)前工序的尺寸公差Ta 3)前工序留下的需单独考虑的空间误差εa 4)本工序的安装误差εb
3.经验法
由一些有经验的工艺设计人员或工人根据经验 确定余量。一般用于单件小批生产。
5.4.3工序尺寸及公差的确定
步骤: 1)确定该加工表面的总余量,再根据加工路线确定各工
序的基本余量,并核对第一道工序的加工余量是否合 理。
2)自终加工工序起,即从设计尺寸开始,至第一道工序 ,逐次加上(对被包容面)或减去(对包容面)各工 序的基本余量,便可得到各道工序的基本工序尺寸。
调整后的工序尺寸
工序尺寸 mm
粗糙度 Ra/μm
61.500.018
0.4
细镗
0.3 H6(00.018) 0.8
61.5 61.5-0.003=61.497 61.49700.018
0.015 0.003
0.8
精镗
0.7 H9(00.04半6) 1查精根精)1表镗 据镗.6确并余该余定根量厂量6总1据:资.:4余97大料-0量.3头定=61为孔.2 为0.7剖m6m分1.200.046 61.200.05
59
0.4 0
6.3
锻 Z总=4.5
59-2=57
5710..57
(2)确初定定工各序 工序的加工经济精度和粗糙调整度后的工序尺寸
工序
以入体单
工序 名称
余量
经济精度 粗糙度
基本工序尺寸 mm
向公差标注
ቤተ መጻሕፍቲ ባይዱ
工序尺寸 粗糙度
mm
mm
Ra/μm
滚压为最mm终工序,m应m 达到Ra/μm
滚压 0.03 H6(00.018) 0.4