《压铸模具3D设计与计算指导》--综合计算表格使用说明
压铸模具设计方案
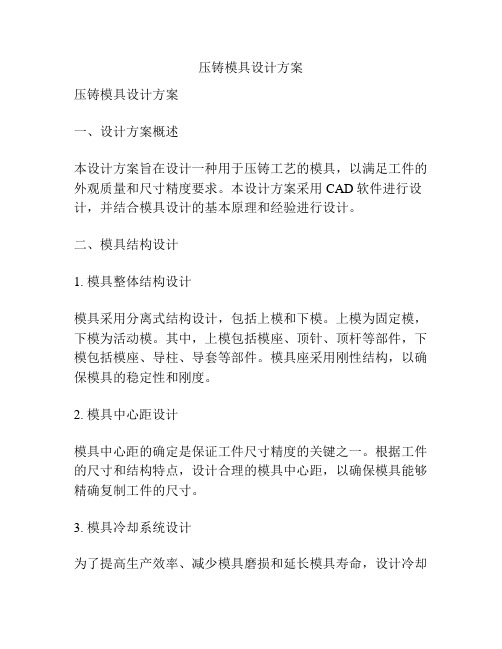
压铸模具设计方案压铸模具设计方案一、设计方案概述本设计方案旨在设计一种用于压铸工艺的模具,以满足工件的外观质量和尺寸精度要求。
本设计方案采用CAD软件进行设计,并结合模具设计的基本原理和经验进行设计。
二、模具结构设计1. 模具整体结构设计模具采用分离式结构设计,包括上模和下模。
上模为固定模,下模为活动模。
其中,上模包括模座、顶针、顶杆等部件,下模包括模座、导柱、导套等部件。
模具座采用刚性结构,以确保模具的稳定性和刚度。
2. 模具中心距设计模具中心距的确定是保证工件尺寸精度的关键之一。
根据工件的尺寸和结构特点,设计合理的模具中心距,以确保模具能够精确复制工件的尺寸。
3. 模具冷却系统设计为了提高生产效率、减少模具磨损和延长模具寿命,设计冷却系统对模具进行冷却。
冷却系统包括冷却孔和进水口,通过冷却水的流动,迅速冷却模具,以提高生产效率和模具寿命。
4. 模具材料选择模具的材料选择是保证模具寿命和使用效果的重要因素。
根据工件的材料和要求,选择适当的模具材料,保证模具具有良好的硬度和耐磨性。
三、模具生产工艺1. 加工工艺规程模具的加工工艺包括数控加工、外圆磨削等。
根据模具的具体结构和工艺要求,制定合理的加工工艺规程,以确保模具的加工质量。
2. 检测工艺模具加工完成后,进行检测以验证模具的质量。
检测工艺包括模具尺寸检测、表面质量检测等,通过合适的检测工艺,确保模具符合设计要求。
四、模具的维护、维修和更换为了保证模具的正常使用和延长其寿命,进行模具的定期维护、维修和更换。
维护工作包括清洁模具、添加润滑剂等,维修工作包括修复模具损伤、更换模具部件等,更换工作包括根据模具磨损程度,定期更换模具部件。
五、结论本设计方案是一种用于压铸工艺的模具设计方案,通过合理的结构设计、材料选择和加工工艺,可以满足工件的外观质量和尺寸精度要求。
同时,通过模具的定期维护、维修和更换,可以保证模具的正常使用和延长其寿命。
压铸模具设计的3D作业规范

3D作业规范一.IGES数据处理二.产品检查三.成品处理四.拔模处理五.分型面(PL)面的选取六.3D拆模七.检查八.传档规范一.IGES数据处理在设计过程中,我们有时会接到客户提供的IGES格式的档案,这种3D在Pro/e中是无法直接用来拆模的。
当3DCAD模型有一套CAD/CAM系统转至另一套CAD/CAM系统时,由于系统之间的几何运算方式不同,资料形式不同,精度设置不同等诸多因素,造成无法直接传递文件。
而IGES是当今最常用的CAD资料转换格式,利用IGES来转换CAD资料时,最常见的问题是曲面有破孔,Pro/e无法填入材料,作出实体模型,所以我们首先应该学会如何修补有破孔的IGES资料。
IGES资料包括点,线,及曲面的几何资料(一般为曲面),若曲面与曲面之间有间隙(一般称之为"破孔"),则间隙的区域在画面上呈现黄色。
因此,输入IGES资料后,若画面上某些区域有黄色的线条,即代表这些区域需要修补。
其形成破孔,有以下原因:●原来被裁剪掉(Trim)的曲面变为没有被裁剪掉,因此曲面凸出去了;●两个原先相邻的曲面变为不相邻,其情况可能是两个曲面剥离开了;●曲面的边消失了;●曲面的边扭曲了;●曲面不见了;●所有曲面都被打乱了。
解决上述问题的基本观念是:将曲面的边界线整理为正常(或合理)状态。
其解决方法如下:●删除错误的边界线条,建立新的线条,再将新的线条连接为封闭循环;●直接将错误的线条修整为正确的线条。
二.产品检查为了提升设计品质,将后续可能出现的问题提前在设计阶段预防和解决好,应该进行仔细的产品检查。
1检查倒勾:成形品侧面具有凸出或凹入的部分,如侧面之孔,文字,沟槽,凸缘等,在成型后无法从模具中直接取出成形品,因这些凸出或凹入的部分,对成形品之顶出,构成了干涉作用,若强制顶出,则会使成形品变形,破损,或使模具损伤,此干涉部分称为Undercut(死角),也可称为倒勾。
a.客户有意做的倒勾,需要用滑块,斜销等机构来成型;b.客户建模时无意形成的倒勾,可建议客户更改产品。
FLOW3D_压铸参数设定表97-2003

FLOW-3D High Pressure Die Casting / Foundry铸造/ 压铸仿真参数设定表专案(客户)名称:问题描述及希望验证的结果:分段之射速设定信息:0~1速1~2速2~3速3~4速真空起始位置高速终止距离mm时间(秒)射速设定m/s注:若不知道射速,请提供成品的大约『充型』时间(如:零点几秒)图档/ 材料/ 温度材料种类(如果是特殊材料,请填入合金成分)初始温度(摄氏℃)铸件材料模具材料压射头直径料筒长度下面是需要提供的图档,以及要求:1、铸件的stl和iges档案:请通过CAD软件转出*.stl和iges文件『精度要高』,并包含浇注系统& Overflow 在内。
2、如为多模穴的设计,请将所有模穴一并绘制,并且提供『重力』的方向。
3、如需要模拟料管状况,必须把料管的图档一并绘制。
4、如果模具有冷却系统,请提供冷却系统图档。
5、建议最好可以做成装配体方式,转出stl和iges档案。
6、请按照上述要求,把相关的stl和iges档案,以及此参数设定表发给我们。
其他浇铸成形条件充型时间(估算)大约秒整体时间(估算)大约秒(从充型开始到凝固完成,准备取出时所花费的时间,估算)环境温度(车间空气温度)度(摄氏℃)结果输出确认选项:请将□改变颜色为□即可。
充型阶段□卷气现象(卷气含量/ Air Entrainment)□氧化膜追踪(表面缺陷集中区域/ Surface Defect Tracking)□铸件温度变化(Temperature)□铸件速度变化(Velocity)凝固阶段□缩孔(Shrinkage & Porosity)□缩松(微缩孔分布/ Mirco-Porosity)□凝固过程中的铸件温度变化□凝固过程中的凝固率分布(Solidification)□铸件之热点位置(可能发生热裂的区域/ Hot Cracking)其他(请明确告知希望确认的问题点)注:请按照上述要求,把相关的和stl和iges档案,及填写完毕的参数设定表发给我们。
压铸工艺计算公式---6页

(如计算转换行程要再加料 饼厚+1.75cm=11.75cm)
VL=
700 + 3 = 10cm 38.5 × 2.6
VD---模具界限速度m/s=550× (内浇口截面积 cm2 )2 ×压射缸剖面积cm2×Acc管道压力kg/cm2÷(冲头剖面积cm2)3÷100
十一 VD= 550 ×
( Ag )2 × Ah × Acc ÷ 100 ( Ap )3
389 417 444 611 694 778 833 889
678 726 774 1065 1210 1355
471 504 538 739 840 941 1008 1076 1176 1277
346 370 395 543 617 691 741 790 864 938
560 600 640 880 1000 1120 1200 1280
2
压铸条件参数及公式代
10.Vg--- 内浇口速度:52m/s 11. Vp---冲头速度:1.75m/s 12. Vd---低速速度:0.22m/s 13. VL---高速区间:10cm 14. VD---模具界限速度:3.45m/s 15. qa---排气槽剖面积:0.9cm2 16. qv---排气槽气体速度: 75m/s 17. K----填充率: 27% 18. t----填充时间:0.04s 19. W---浇铸铝液重量:900g 20. WG--填充铝液重量:700g 21. L---空压射行程:33.7cm 22. P--- 压力 Q---流量
700
1.Vg---浇口速度m/s=冲头面积cm2×冲头速度m/s÷浇口面积cm2 Vg=
八
Vg=
极速了所以一般件不要超过此速度,主要
压铸模具设计和制造手册

模具分类与条款Awintech已向客户建立了三类压铸模具,这三类压铸模具为原型模具、预生产模具和生产模具。
生产模具使用在与全能力生产旳有关方面,它符合本手册中提到旳原则压铸设计和制造。
其模具寿命与常规模具非常相似。
数量到达20,000件以上则适合于此类模具。
上内模和滑阀面是用优质旳H13级钢制成旳。
预生产模具使用在这些方面,如客户需要生产有限旳超越产品寿命旳旳零件。
用铝压铸旳这种模具能持续到达近20,000射出。
铸造时使用锌或镁都将延长其使用寿命。
原型模具则使用在这些方面,当客户只规定用380铝生产非常有限数量,仅到达500件这样旳零件。
此类模具寿命会比用其他合金制成旳模具寿命要长某些。
在本手册后来章节中会提到与设计和制造有关旳特定模具条款。
最值得一提是在每一类模具中为客户制造合格旳压铸产品旳生产性能作为最首要旳目旳。
假如模具生产无法满足客户旳需求,则毫无价值。
我们尝试详细阐明一下品质原则,在这三类模具中每一种品质原则都要向客户提供。
此外,我们也在努力保证他们对每一类模具生产旳铸件质量有所理解。
与Awintech作生意Awintech旳目旳就是向客户提供符合预期规定并交付及时旳高品质模具。
本手册中我们详细阐明向客户提供旳模具原则。
不过,假如有任何有关模具设计和制造旳疑问,请与我们联络。
铸造模,电极、CNC程序、设计、计算机程序、模板以及与该工作有关旳需采购旳所有东西都是Awintech所具有旳。
它们应由模具制造商保留或根据客户规定提供应我们。
如下是模具加工付款条件:随订购单先预付50%模具加工费,模具加工完毕后再付40%,最终模具样品合格后再付10%。
备注:以上条件需双方共同到达一致,否则无效。
目录模具分类与条款与Awintech作生意总体环节与规格胚模规格料表上内模公模滑块零件拉圾钉顶出系统加热与冷却胚模零件液压汽缸筒和靠近开关合金工具钢旳热处理合金工具钢表面处理焊接金属进料与真空系统文档资料与证明压铸冲模设计和制造总指南和专用指南设计检测表模具加工检测表Awintech模具改善表Awintech模具检测规划汇报拉极钉概要热电偶安装设计压铸机台板布局真空安装规格总体环节与规格1、Awintech会向模具供应商提供最新旳客户产品印刷物或资料库用以询价,模具设计和制造。
压铸模具台账

压铸 模具
压铸模具状况表
注:模具已经生产模次百分比黄色填充代表模具寿命达60%,需提供预警;红色填充代表已经达到或超过设计寿命。
XXX-14-FM-016-K0
序 号
物料编 码
客户名称
模具产 权
开模时间
产品图 号
产品名称
模具编号
模架 号
模芯号 模穴数
产品单重 (g)
材料牌 号
机台吨位
模具现有状 况描述
模具状态 存放位置
第一次回火
第二次回火
模次 回火日期 模次 回火日期
第三次回火 模次 回火日期
第四次回火
模 次
回火日期
第五次回火
模 次
回火日期
ቤተ መጻሕፍቲ ባይዱ
备注
第 2 页,共 2 页
RXT-14-FM-016-K/O
冲头直径
设计寿命 (模次)
每套模具入 库毛坯数量
产品合计系统 入库毛坯数量
(PCS)
产品合计手 工入库毛坯 数量(PCS)
产品总入库 模具已生产
毛坯数量 百分比
(PCS)
(%)
1 2 3 4
5 6 7 8 9 10
第 1 页,共 2 页
RXT-14-FM-016-K/O
XXX-14-FM-016-K0
铝合金压铸机选型计算公式表
铝合金压铸机的选型计算公式表可能因不同的压铸机型号和厂家而有所不同,但以下是一些常见的选型计算公式:
压铸机锁模力计算公式:F = (π × d × p × L) / 1000
其中,F为锁模力(kN),d为铸件直径(mm),p为铸件收缩率(一般取1.006),L为铸件高度(mm)。
压铸机功率计算公式:P = (π × d × p × Q × L) / 3600
其中,P为功率(kW),Q为铸件重量(kg)。
压铸机合模机构总压力计算公式:F_total = F_s + F_a
其中,F_total为合模机构总压力(kN),F_s为锁模力(kN),F_a为合模机构所需压力(kN)。
压铸机顶出力计算公式:F_top = π × d × p × Q
其中,F_top为顶出力(kN),Q为铸件重量(kg)。
需要注意的是,以上公式仅供参考,实际选型计算时需要结合具体的产品要求、生产工艺、设备参数等因素进行综合考虑。
同时,不同厂家和型号的压铸机可能具有不同的特点和适用范围,因此需要根据具体情况进行选择。
magma-压铸模拟操作实例说明
定义热传导系数
目录
54
步骤四:进行高压铸造计算,按下OK
目录
55
a.检查表中内浇口面积是否与实际相符,输入实际的内浇口面积。 b.输入实际模拟铸件的特征壁厚。 c.根据实际模拟铸件的内部质量要求定quality的级别。按下next。
输入实际的 内浇口面积 输入铸件 特征壁厚 选择quality 的级别
此视角确定其平面位置
目录
37
步骤六:将所有材料组排序
A.打开下拉菜单 Select中volume
目录
38
B.将所有材料 按顺序排序 注:在材料组 有重叠时,以 后面材料减去 前面材料为原 则。
目录
35
步骤七:存盘 A.打开下拉菜单 file,点选save all as 1存盘,完 成前处理 B.点选exit,回 菜单
MAGMA4.2模拟操作
目
一.3D模型准备
1.模型绘制用软件---------------------1 2.模型内容------------------------------2 3.3D模型的绘制方法-----------------3
录
4.模拟参数输入及计算-----------52 (1)模拟参数输入----------------52 (2)模拟计算----------------------76 5.后处理------------------------------79 (1)观察模拟结果-----------------79 (2)模拟结果拍片----------------107
选用 包括
设为 0值 输入 每个 零件 的名 称 14
目录
14)注意:在生成stl文件的时候一定要在组件的窗口下,并且每一个零 件要单独选择,单独保存。生成的文件如图。 15)将所生成的 stl文件保存的指 定文件夹中备用 。
铝合金箱体压铸模具设计说明书
毕业设计(论文)任务书 2015 届机械工程及自动化专业题目:铝合金箱体压铸模具的设计子题:学生姓名:班级学号:指导教师:职称:所在系(教研室):机电与信息工程系下达日期:2014年7月4日完成日期:2015年5月8日摘要压铸模具是铸造液态模锻的一种方法,一种在专用的压铸模锻机上完成的工艺。
它的基本工艺过程是:金属液先低速或高速铸造充型进模具的型腔内,模具有活动的型腔面,它随着金属液的冷却过程加压锻造,既消除毛坯的缩孔缩松缺陷,也使毛坯的内部组织达到锻态的破碎晶粒。
毛坯的综合机械性能得到显著的提高。
本文运用大学所学的知识,了解压铸模具的工作原理,在此基础上,设计一款铝合金箱体压铸模具。
通过查找相关资料,了解铝合金箱体压铸模具的内部结构和工作原理,构建了铝合金箱体压铸模具组成结构的总的指导思想,从而得出了该铝合金箱体压铸模具的优点是高效,经济,并且运行效果好,运行平稳的结论。
关键词:铝合金箱体压铸模具;型腔;效率;模具AbstractThe environment of global economic development, China industries affected by other countries advanced technology at the same time, foreign enterprises and brand spread to more and more Chinese has become an opportunity. Cap pressing machine in industry through a variety of ways have been working with the relevant technology, and constantly improve their own strength and core competitiveness, and narrow the gap with developed countries.In the new market demand, update the sleeve pressing machine is a pressing matter of the moment. The production of pipe pressing machine equipment manufacturing enterprises to fully tap the potential of the market, vigorously develop the sleeves of large low cost pressing special machinery and equipment, plays a positive role in the evolution of automatic assembly, the assembly of mechanical equipment. There is a large pipe equipment on equipment safety index has strict requirements of production. In the production equipment of enterprises, give full consideration to the possible problems in the operation of the equipment, so as to reduce the noise pollution caused by vibration or improper operation of equipment phenomenon and manufacturing of domestic pipe pressing equipment with global appeal, economic, security and stability of the theme consistent. Increase and production pipe pressing equipment of new energy saving.Key word:pneumatic manipulator;cylinder;pneumatic loop;Fout degrees of freedom.目录摘要 (1)Abstract (2)第一章绪论 (3)1.1 模具介绍 (4)1.2 模具在加工工业中的地位................... 错误!未定义书签。
压铸参数的计算(精)
∙压铸工艺参数的计算∙发布时间:2011-4-9 15:39:34 来源:互联网文字【大中小】∙文/哈尔滨爱迪压铸有限公司/朱丽、刘维刚、车宏伟、迟兰成摘要:许多压铸企业的技术人员都非常熟悉压铸工艺参数的计算与调节,但在实际生产中往往凭借经验,通过检验产品的好坏来调节工艺参数,为了麻烦而忽略了工艺参数的计算,往往都是用很大的速度、压力来使产品达到合格状态,这样使机床、模具损耗过快,浪费资源。
关键词:工艺参数、压力、速度、时间在压铸生产中,压铸机、压铸合金和压铸模是三大要素。
压铸工艺则是将三大要素作为有机的组合并加以运用的过程。
压铸生产时液态金属充型的过程,是许多矛盾着的因素得以统一的过程。
在影响充型的许多因素中,主要是速度、压力和时间等,通过速度的控制减少和消除压室内空气的卷入、雾化型腔内残留的气体; 通过压力的控制,增加产品的密实度,减少缩孔的形成; 通过时间控制,使产品不宜产生变型等缺陷。
利用计算工艺参数来优化模具、压铸机之间的匹配性。
因此,只有对这些工艺参数进行正确选择、控制和调整,使各种工艺参数满足压铸生产的需要,才能保证在其他条件良好的情况下,生产出合格的压铸件。
本文通过以力劲公司生产的DCC280卧式冷室压铸机上所生产的水泵壳体产品(附图为例,简单介绍一下压铸生产中主要工艺参数的计算。
一、速度参数(1低速速度压射冲头将注入压室的铝液平稳地推移到内浇口位置,使铝液完全充满到压射冲头与内浇口之间的压室空间内的过程就是低速过程(一般为0.1-0.3m/s。
设置时要注意防止空气卷入,防止铝液温度下降,导致过早凝固。
压室充满度=注入重量/压室截面积×空打行程×溶液密度X100%(压室充满度的标准一般为20-50%低速速度=0.7X√压室直径/压室充满度例题:压室直径:Φ50mm,注入重量:830g ,空打行程:368mm ,压室截面积:(π/4×52=19.63cm²,溶液密度:2.6 g/cm³压室充满度=(830/196.63×36.8×2.6X100%=44.18%低速速度=(0.7X√50/44.18=0.122M/S(2高速速度压射冲头将铝液完全充满到压室内(一般为1.5-2.5m/s。
- 1、下载文档前请自行甄别文档内容的完整性,平台不提供额外的编辑、内容补充、找答案等附加服务。
- 2、"仅部分预览"的文档,不可在线预览部分如存在完整性等问题,可反馈申请退款(可完整预览的文档不适用该条件!)。
- 3、如文档侵犯您的权益,请联系客服反馈,我们会尽快为您处理(人工客服工作时间:9:00-18:30)。
综合计算表使用说明
⑴综合计算表分类
综合计算表是按书中介绍的各种参数计算理论、计算公式,经过编辑、排列、各表之间互相联动计算,形成的一种计算方法。
为了便于识别和操作,采用不同颜色的字体和底面。
其中:“绿底红字”为直接输入数据,“蓝底黑字”为选择数据,“白底紫色”为计算结果数据,其余为原始数据或计算过程数据。
综合计算表共分方形、圆形二种类型,方形和圆形又各分成:基本型、无侧抽芯及带有一、二、三、四侧抽芯、特殊型、验算型八种专用计算表。
后七种表是从基本型根据模具结构特点及应范围,经过简化后得到的,是基本型中的特例,使用时可根据制件特点使用要求分别选用。
本表在编制时,将计算结果和参与计算的数据尽量列在同一列中,便于观察和选用。
⑵表格使用方法及步骤:
①将已放收缩的制件3D图测量的基本参数和辅助参数数据,(未放收缩的2D图或样件应将测量尺寸加放收缩后)填入制件基本参数和辅助参数表“绿底红字”的格中。
无数据时可填“0”或“空着”。
②根据模具结构特点在模芯尺寸表“绿底红字”格内填入模具结构参数。
⑶更换计算表
①根据合金种类更换充填速度选取表,如:若计算镁合金制件时,可将镁合金充填速度
选取表剪贴到铝合金充填速度选取表的位置处,如表1,表2中出现“#REF!”时,点击内浇口截面积计算格内的“#REF!”,将计算公式中的“#REF!”改成:方形为“L17”,园形为“ L16”,其它操作不变。
表1充填速度选取表(镁合金)
表2压铸机吨位、内浇口截面积
②若计算其它种类合金时,应将浇注金属比重表中的铝合金及其数据改成相应合金及其数据,相关数据可在书中查找。
③根据制件重量更换压铸机压射速度选取表,用同样的方法更换成表3,剪贴后表4中出现“#REF!”时,点击充填时间计算计算格内的“#REF!”,将计算公式中的“#REF!”改成压射速度选用值“L23”,其它操作不变。
表3压铸机压射速度选取表(制件重量≤1Kg)
表4压铸机吨位、内浇口截面积
⑷应用“计算因子”简化计算表操作方法
计算因子是专门为选择项目设计的一个替代因子,根据项目特点采用类似的计算方法达到替代的作用。
它可以免去逐个选择的麻烦,使计算表操作更加简化、方便、实用,计算速度更快。
计算因子的代号为“0”、“1”,其中“1”代表该组数据被选中,“0”代表该组数据不被选用。
应用时,每组计算因子只能有一个为“1”,其余均为“0”。
①比压计算因子
表3—*确定比压计算因子
比压计算因子是区别最大比压和安全比压用的计算因子,为模芯尺寸计算和压铸机吨位校核共用。
②充填速度、压射速度计算因子
表4—充填速度、压射速度计算因子
充填速度、压射速度计算因子分别按制件壁厚范围“≤2.5”、“>2.5~4”、“>4”选用。
③比例系数计算因子
表5—充填速度、压射速度计算因子
比例系数计算因子是按制件重量范围选用。
④压铸机吨位计算因子
表6—压铸机吨位计算因子
(表6续)
(表6续)
压铸机吨位计算因子是按大于或等于预选吨位吨位选用,一经选中某一吨位压铸机,该吨位压铸机除浇口套内经外的所有相关参数据均被选中。
⑸更改选择数据
①按制件对角线长度选择比压计算因子。
②按制件重量选择比例系数计算因子。
③按基本壁厚选择充填速度、压射速度计算因子。
④按制件预选吨位选择压铸机吨位计算因子。
⑤选择浇口套内经:点击浇口套内径数据,再点击计算公式,将内径数值更换成选定压铸机现有规格。
其校核吨位接近或小于选定吨位时为合理,大于选定吨位时,应重新选择浇口套内经。
⑹模具尺寸计算及调整
①模芯尺寸计算:
按制件对角线长度选择比压计算因子。
当对角线长度“蓝底白字”≤400㎜时,取安全工作比压为“1”,对角线长度>400时,取最大比压为“1”。
尺寸调整方法:
方法一:将公式中基数70可按个人意愿修改成>70的任意数,直到计算结果令你满意时为止。
方法二:制件所有辅助参数一律为“0”或“空着”,在计算时不进行调整,待按计算尺寸生成模芯后,再根据制件在模芯中的位置、浇排系统分布情况等个别调整。
②模框尺寸计算:在模框推荐尺寸表的“绿底红字”区域内,根据模具结构特点和选定的压铸机吨位按推荐范围直接输入选定的周边、底厚的数据。
周边增加尺寸:点击左右、上下自动计算数字,在计算公式中根据模具侧抽芯的具体结构更改。
底厚增加:指的是在模芯底面上再增加值,在模框推荐尺寸表中,普通、加厚格内只许填一个数据,另一格内填“0”.或“空着”。
⑺侧抽芯尺寸计算
侧抽芯结构设计的尺寸计算只作为一种提示性或导向性的辅助计算方法,应先选择抽芯机构,再根据抽芯机构特点确定相关尺寸。
读者可根据实际情况参照“制件参数测量图例及计算说明”及表中各种推荐尺寸范围,进行具体的结构设计。
⑻有侧抽芯时模框侧面需局部增加尺寸计算
模框局部需增加的尺寸也是一种提示性计算法,读者可根据其具体结构参考表中推荐尺寸范围直接加放。
⑼特殊计算表中的压铸机参数选择
①选取选用压射力:在“比压选取表”中,点击压射力范围(蓝底黑字)数据,再点击计算公式,将压射力范围数值更换成选定压铸机规定的数据。
再点击压射力数值(绿底红字),按压射力规定范围直接输入压射力吨位数据。
若出现计算比压Ⅱ<300㎏/㎝²时,应重新输入压射力吨位数值或调整浇口套内径大小。
②特殊计算表中的其它计算方法,与普通计算表相同。
⑽验算表
验算表主要用于对现有模具的内浇口截面积、压射速度、充填速度和充填时间等工艺参数的验算,其它数据如模芯尺寸、模框尺寸等不验算。
分两种方法验算。
①计算与实际对比验算:打开验算表(方形或圆形),先将制件基本参数输入,再将验算模具的实际选用压铸机吨位、浇口套内经、内浇口截面积填入相应表内,按本使用方法进行正常计算,计算出内浇口截面积和充填时间。
将计算结果与现有模具参数对比,首先检查压射速度、充填速度是否在推荐范围内?在检查检查两者误差,内浇口截面积误差,为改善浇注系统提供理论根据。
当误差较大时,可根据误差大小,在计算表中重新选择压铸机吨位及浇口套内经,令计算表计算出合理数据,再根据实际情况对现有模具进行适当的调整。
②计算与“CAE”模拟结果对比验算:再将模拟充填时间填入相应表内,检查充填速度和压射速度是否在推荐范围内。
将计算结果与现有模具参数对比,检查两者误差,分析误差长生原因。
⑾计算结果保存方法
①本计算表每次计算后不要保存,以保证因误操作会改变表格的相关计算原理。
为了减少容量,简化手续,需将计算结果另行保存,便于查找相关资料。
②打开保存记录表,按制件(或模具)计算表特征选择方形、圆形、验算型表中任一制件表,将其复制同类型表的下方,再将制件名称、计算时间、相应计算结果填入表中保存。