模具设计检查表
模具设计检查表(冲压)

18.成型(拉深、成形、弯曲、翻边、整形)
A.压边圈设计的合理性(包括拉深筋等)
B.拉深模、成形模排气系统是否适合
C.气垫顶杆的行程长度是否符合要求
D.到位标记或限位装置确保产品压制到位
19.冲裁(落料、冲孔、切边)
A.模具整体、分段修边周界及间隙设计的合理性
11.冲压力是否计算,压力中心位置在设计图纸中是否标注提示
12.上下模具定位及导向的可靠性
13.定位的可靠性;定位基准与产品基准一致性;前道工序的制件,在下道模具中定位的可靠性
14.U型槽、模柄、顶杆位置及孔径等安装尺寸应与选用机床一致
15.模具顶出和卸料装置、易损件和工作部分的合理性与可靠性
16.斜锲和吊锲结构的尺寸是否符合要求
冲压模具设计审核表
DIEDESIGNREVIEW
零件号:
总成号:
工程更改号:
零件名称:
零件图纸或GD&T图纸号:
零件图纸更改级别:
年型/车型:
零件数模版本号:
模具编号/图纸张数:
零件供应商:
产品工程师(新亚通) :
模具工程师(新亚通):
电话:
电话:
DUNS / Z编号:
模具工程师(供应商):
电话:
模具设计公司:
B.工作部分镶块设计的合理性
C.废料系
E:.刃口有效工作长度是否足够
20.模具的部件必须具有安全措施,特别是进料、出料,模具的安装及搬运装置
21.是否规定的对模具部件标识,如:上下模及重量、工序号、标牌、涂色、顶杆位置等
审核及改进意见:(如审核及改进意见此栏写不开,附表于后)审核栏评价结果:此项目不适用打/合格打√不合格打×
模具设计评审检查表

**-R3.2-01产品名称: 产品图号:模具名称: 模具编号:模具设计师 评审时间模具设计评审项目及内容项目评审内容是否满足模具设计改善方案备注产 品 检 查1.毛刺要求2.是否为外观件3.产品材料明确(材质及料厚)4.各视图的角法有无看错,产品是否对称5.确定原图比例6.工序图定位是否一致7.工序冲压方向一致(工件是否需要翻转)落料及冲孔模具1.展开尺寸的确定2.工序是否漏冲孔或漏折弯3.刃口材料及硬度要求4.凸凹模材料是否公用5.凸凹模是否单向受力及解决措施6.下料模具卸料板有没有加大避空以减少压伤和对模具的损坏;7.压力中心是否考虑8.冲孔凹模的刃口厚度及漏料孔的设计9.凸模结构是否合理10.凹模外形尺寸是否适合,是否存在凹模冲裁开裂风险?或增加加固套环必要性?11.卸料板硬度要求12.卸料板是否起导向作用13.是否需要人工取废料14.卸料是否需要人工脱料15.成品的脱料力是否平均(尤其是弯曲模、多孔模)16.弹簧的脫料力及压缩量是否足夠17.成品是否要浮升梢以防粘模18.废料刀的设计及废料自动脱落19.模具的闭合高度20.模具的冲裁力及使用设备21.冲头是否需要作阶梯式22.侧冲结构的设计23.侧冲的漏料设计24.加工基准孔是否需要25.模具的避位是否充分产品名称: 产品图号:模具名称: 模具编号:模具设计师 评审时间模具设计评审项目及内容项目评审内容是否满足模具设计改善方案备注拉 深 模 具 1.凸凹模材料及硬度是否合理2.凸模的设计方式是否合理3.凹模的设计方式是否合理4.压边圈的设计方式及材料硬度、厚度要求是否合理5.顶杆排步方式是否合理6.顶针板的厚度硬度要求7.预冲孔的设计依据及漏料方式是否合理8.模具的支撑是否排步均匀9.模具是否需要拉延筋及位置10.模具的排气孔的设计有没有考虑11.模具是否选用适用的设备12.拉伸凹模是否需要跟型13.是否需要预冲工艺孔14.有没有加回弹余料15.后工序是否定位可靠16.模具是否需要限位17.预冲孔的设计依据及漏料方式是否合理?18.零件折弯是否单向受力,材料是否会发生流动,如何解决?19.模具定位结构方式是否满足零件关、重要尺寸精度及产品特性要求?20.产品的定位是否会因材料流动而变形?21.成品是否需要浮升销以防粘模?22.后工序的定位是否进行考虑?23.是否考虑模具是否适合叉车运输产品名称: 产品图号:模具名称: 模具编号:模具设计师 评审时间模具设计评审项目及内容项目评审内容是否满足模具设计改善方案备注成型、折 弯 模 具 1.定位支撑是否可靠2.折弯线是否全部是直线3.模具设计是否考虑材料反弹补偿4.凸凹模侧向受力是否有抵消5.折弯是否单向受力,材料是否会发生流动,如何解决6.产品的定位是否因材料流动而变形?7.凸凹模的材料及硬度要求8.凸凹模间隙是否准确?9.卸料力是否满足?10.卸料是否需要人工脱料11.成品是否要浮升梢以防粘模12.搬运吊环设计有无必要,强度是否满足?13.闭合高度是否符合?14.安装T型槽是否需要?15.凹模模芯及顶出孔设计是否合理?16.使用设备规格是否合理17.模具安装方式及规格是否与设备工作台相符18.模具定位结构方式是否满足零件关、重要尺寸精度及产品特性要求?19.后工序的定位是否进行考虑?20.是否考虑模具是否适合叉车运输21.其他产品名称: 产品图号:模具名称: 模具编号:模具设计师 评审时间模具设计评审项目及内容项目评审内容是否满足模具设计改善方案备注产品检查1.毛刺要求2.是否为外观件3.产品材料明确(材质及料厚)4.各视图的角法有无看错,产品是否对称5.确定原图比例全 自 动 模 具 1. 料带设计是否是最理想的?2. 定位导正孔尺寸是否适中?3.模具设计是否考虑材料反弹补偿4. 确认最小冲头尺寸,是否强度足够?5.折弯是否单向受力,材料是否会发生流动,如何解决6.产品的定位是否因材料流动而变形?7.凸凹模的材料及硬度要求8.凸凹模间隙是否准确?9.卸料力是否满足?10. 折弯R/T比值,是否过小?11.成品是否要浮升销以防粘模12产品重要尺寸是否考虑如何保证,比如放回弹,加调整,下料取经验值等13.闭合高度是否符合?14. 压力弹簧数量,强度,排配是否合理?15. 模具结构是否恰当,导向件数量,强度是否足够?16.导位针结构型式,排配,数量是否合理17. 成形工站是否需要调节装置,装置是否可靠及便于调节,是否与导柱等干涉. 18.模具定位结构方式是否满足零件关、重要尺寸精度及产品特性要求?19. 零件强度是否足够,易损件是否有足够备件20.是否考虑模具是否适合叉车运输。
模具设计检查表
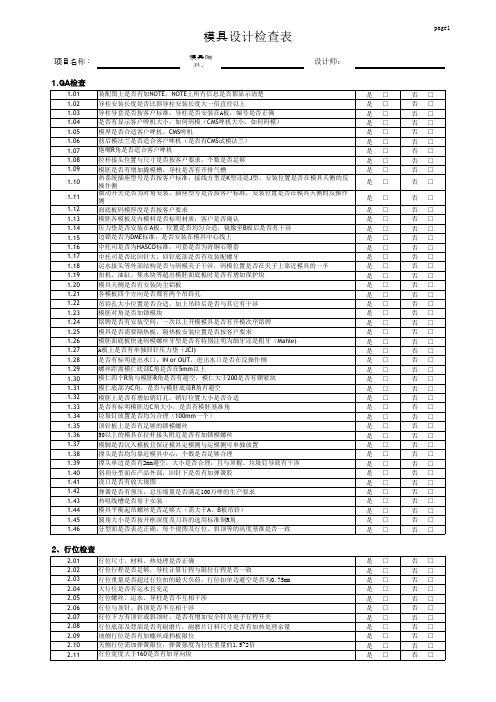
模具设计检查表
项目名称 模具编号: 设计师:
page3
6 、流道系统检查
6.01 6.02 6.03 6.04 6.05 6.06 6.07 6.08 6.09 6.10 是否有流道、浇口放大视图、流道转角处是否有加R角 流道头部是否有按要求设计圆弧过度 入水点与客供资料、3D图是否一致 热咀是否比分型面低1mm 热咀孔径是否有标公差 咀嘴处是否为平面或小于5%的斜面 牛角及潜水平面在产品上是否有做凹坑 入水点头部R处钢料强度是否足够 浇口顶针冷料是否比牛角及潜水冷料长3-5mm 水口顶针在两模仁之中是否有加水口套 是 是 是 是 是 是 是 是 是 是 □ □ □ □ □ □ □ □ □ □ 否 否 否 否 否 否 否 否 否 否 □ □ □ □ □ □ □ □ □ □
模具设计检查表
项目名称: 1.GA 检查
1.01 1.02 1.03 1.04 1.05 1.06 1.07 1.08 1.09 1.10 1.11 1.12 1.13 1.14 1.15 1.16 1.17 1.18 1.19 1.20 1.21 1.22 1.23 1.24 1.25 1.26 1.27 1.28 1.29 1.30 1.31 1.32 1.33 1.34 1.35 1.36 1.37 1.38 1.39 1.40 1.41 1.42 1.43 1.44 1.45 1.46 装配图上是否有加NOTE,NOTE上所有信息是否都显示清楚 导柱安装长度是否比斜导柱安装长度大一倍直径以上 导柱导套是否按客户标准,导柱是否安装在A板,编号是否正确 是否有显示客户啤机大小,如何码模(CMS啤机大小、如何码模) 模厚是否合适客户啤机、CMS啤机 前后模法兰是否适合客户啤机(是否有CMS试模法兰) 炮嘴R角是否适合客户啤机 拉杆接头位置与尺寸是否按客户要求,个数是否足够 模胚是否有增加撬模槽,导柱是否有开排气槽 热系统插座型号是否按客户标准,接线方型是K型还是J型,安装位置是否在模具天侧的反操作 侧 微动开关是否为对角安装,插座型号是否按客户标准,安装位置是否在模具天侧的反操作侧 面底板码模厚度是否按客户要求 模胚各模板及内模料是否标明材质,客户是否确认 压力垫是否安装在A板,位置是否均匀合适,镜像至B板后是否有干涉 边锁是否为DME标准,是否安装在模具中心线上 中托司是否为HASCO标准,司套是否为青铜石墨套 中托司是否比回针大,回针底部是否有攻装配螺牙 运水接头等外部结构是否与码模夹子干涉,码模位置是否在夹子上靠近模具的一半 扣机、油缸、集水块等超出模胚面底板时是否有增加保护块 模具天侧是否有安装防尘铝板 各模板四个方向是否都有两个吊铃孔 吊铃孔大小位置是否合适,加上吊铃后是否与其它有干涉 模胚对角是否加锁模块 铭牌是否有安装空间,一次以上开模模具是否有开模次序铭牌 模具是否需要隔热板,隔热板安装位置是否按客户要求 模胚面底板快速码模螺丝牙型是否有特别注明为细牙还是粗牙(Mahle) A板上是否有单独回针压力垫(JCI) 是否有标明进出水口,IN or OUT,进出水口是否在反操作侧 螺丝距离模仁底部C角是否在5mm以上 模仁四个R角与模胚R角是否有避空,模仁大于200是否有锲紧块 模仁底部为C角,是否与模胚底部R角有避空 模胚上是否有增加销钉孔,销钉位置大小是否合适 是否有标明模胚边C角大小,是否有模胚基准角 垃圾钉放置是否均匀合理(100mm一个) 顶针板上是否有足够的锁模螺丝 50以上的模具在拉杆接头附近是否有加锁模螺丝 模脚是否沉入模板且保证模具定模侧与运模侧可单独放置 撑头是否均匀靠近模具中心,个数是否足够合理 撑头单边是否有2mm避空,大小是否合理,且与顶棍、垃圾钉导致有干涉 斜顶分型面在产品外部,回针下是否有加弹簧胶 浇口是否有放大视图 弹簧是否有预压,总压缩量是否满足100万啤的生产要求 热咀线槽是否易于安装 模具平衡起吊螺丝是否足够大(需大于A、B板吊铃) 圆角大小是否按开框深度及刀具的选用标准倒R角 分型面是否表达正确,每个视图及行位、斜顶等的高度基准是否一致 是 是 是 是 是 是 是 是 是 是 是 是 是 是 是 是 是 是 是 是 是 是 是 是 是 是 是 是 是 是 是 是 是 是 是 是 是 是 是 是 是 是 是 是 是 是 □ □ □ □ □ □ □ □ □ □ □ □ □ □ □ □ □ □ □ □ □ □ □ □ □ □ □ □ □ □ □ □ □ □ □ □ □ □ □ □ □ □ □ □ □ □ 否 否 否 否 否 否 否 否 否 否 否 否 否 否 否 否 否 否 否 否 否 否 否 否 否 否 否 否 否 否 否 否 否 否 否 否 否 否 否 否 否 否 否 否 否 否
模具设计结构检查表

A.是否确实为最新版的成品图?
品名:版次:接图日期:
B.相关的情报是否详实?
材质:收缩率:/1000穴数:
C.成品部是否会造成收缩之处?局部较厚之肉厚缩水痕迹如何克服?
D.脱模斜度是否足够?
E.咬花之花纹型式及番号,脱模斜度是否与花纹深度配合?
咬花番号:
F.制品表面的分模线可有获得客户的承认?
模具结构:
Q.模仁固定螺丝大小,分布位置是否适切?
R.K.O.孔顶出位置是否适切?
S.吊模孔是否与其他零件干涉造成吊模困难?
T.倒勾的行程是否足够?(S1>S2)
U.滑块配置方向是否理想?定位是否安全?(天、地、右、左)
滑块数量:
V.滑块压板是否装设定位梢2支?
W.滑块斜针斜度是否小于滑块束块斜度2°?
□□
PP.浇口之二次加工是否容易?
□□
冷卻系統:
QQ.各部位能达到同时冷却的效果?
冷却水孔Φ径、与成品之距离、水孔间之节距(1:3:5)
□□
RR.冷却回路数是否足够?能合乎客户指定的成型周期之内?
□□
SS.冷却回路之编号是否指示了?(如:IN1 OUT 1)
□□
零件部品:
TT.模座,模仁,及其它零件是否选定了适切的材料?
G.日期章(Date Code).穴号之规格是否客户有指示?
H.与客户检讨事项是否全部执行?
Checklist of Tooling meeting with R&D or Customer
I.试模日期?
T0:T1:
射出機
机型:哥林柱距离:
最小模厚:最大模厚:
□□
K.定位环Φ径。灌嘴之Φ径、R、深度是否适切?
模具验收模具设计-检查表

o o o o o o o o o o o
o o o o o o o o o o o o
o
o o o o o o o
o o o o o o o o o o o o o
o o o o o o o o o o o o o
o o o o o o o o o
7.1模具工作安全性 7.2模具维修及换件方便性 7 7.3铸造及加工工艺性(包括装夹) 模具 7.4模具强度 评估 6.5模具经济性(合理减重)
o o o o o
o o o o o
o o o o o
8.1滑动面间隙 8.2左右件说明及标记 8 技术 8.3热处理,涂漆,标牌等 要求
o o o o
o o o o
o o o o
4.1手工上件位置 钢轮滚道,橡胶轮滚轮,定位板滚轮 4.2托起装置 4 制 件 投 入 与 取 出 型式:气缸,举升器,顶销 结构;橡胶轮滚轮,钢管,吸盘等 4.3手工取件辅助装置 4.31空手槽 4.32杠杆 4.33钢轮滚道 4.34橡胶轮滚道 4.35橡胶轮座 4.4制件投入,取出过程流畅检查
设计: 项 内容 目 1.1工艺数模及工艺补充正确性
1 设计 及 加工 依据
校对:
(FUJI)模具设计/检查表 审核: 项目 内容 5.1闭合高度及模具长,宽 5.2上模U槽及快速定位销 5.3下模U槽及快速定位槽 5.4托杆孔位平衡,工作行程控制(ST) 5.5调试托杆孔位 5.6U槽及孔位数量及平衡 5.7安全行程控制(ST) 6.1上,下模导向防反及对应性 6.2上,下模工作及存放限位/缓冲 6.3上,下模起吊 6 6.4上,下模安全区 端头 结构 6.5上,下模运输连接板 6.6.气路接头固定座
o o o o o o o o o o
模具设计检查表

36
小拉杆行程( ),大拉杆行程( )
开模动作
37
扣机设计是否合理
设计标准
38
有前模行位,特殊机构模具确保动作先后顺序
39
模仁虎口设计是否合理
设计标准
40 模具定位 模胚精定位设计是否合理
设计标准
41
单边行位对侧是否设计定位块平衡模具
设计标准
42
模具合模确保导致最先导向(大于导柱直径)
设计标准
43 模具导向 热流道安装确保导柱先导向(大于导柱直径)
57
模具铭牌,水路铭牌,热咀铭牌的设计
打合资料
58 模具标示 日期章刻印等
打合资料
检查者判定 结果
冷却系统
17
冷却分配器(集水排)设置
打合资料 Core温度 BALANCE(平
衡) 350T 以上
18
水路干涉检查(安全间距>5MM,胶圈间距>3MM)
设计标准
19
顶针方式与打合资料是否一致(注意顶针不可位置)
打合资料
20
顶针是否平衡及数量适当与否
取出平衡
21 顶出系统 顶针强度是否足够,顶针板强度,顶针板螺丝设计
400宽以上模具面板,A板,B板,四面是否设计有吊环螺
50
丝
51
PL面排气开设
设计标准 设计标准 设计标准
52 排气设计 导柱的排气开设
设计标准
53
流道排气开设
设计标准
54
计数器,微动开关,先复位等
55
追加式样
支撑棒设计(要求占顶针板面及15%±5,注意进浇 下方)
56
E.G.P 设置与否
标准化 后模板强度 顶板 动作
模具设计检查表
3.2产品胶位复查结果:平均_____mm 最薄_____mm 最厚_____mm 骨位_____mm 柱位_____mm,火山口:需要○ 不需○ 产品上是否有过厚胶位,肋骨厚度是否小于主胶厚2/3,是否会产生缩水痕迹? 三 产 品 分 析 缩水痕迹解决对策: 3.3 产品薄胶位缺胶对策:________________________________________ 3.4 产品拔模是否适当 ,饰纹位置拔模度数 。
10.2 两条运水间距要3-5倍运水直径,最少30mm。破框的直通运水要在开框前做?(特别注意通到圆镶件的运水)
★10.6 运水接头是否相互干涉,是否和其它零件干涉,是否和注塑机格林柱、码模铁干涉?
11.1 吊模螺丝孔(包含吊环旋转)是否和滑块槽、铲鸡、水嘴等其它机构干涉?螺丝配合长度有1.5倍的直径就刚好。 11.2 吊模螺丝位置是否可使吊模平衡?吊模螺丝 大小是否合适?吊模担的强度 是否足够?
第 1 页,共 2 页
模具编号
SHINY 设计检查表(设计工程师填写)
检查内容 主管/总监确认
、行位 、斜顶 、导套 、耐磨板 、模仁
★★★一.模具各部位所用材料:模胚 ★★★二.标准件按
设计。是否已经切实对照过模具规格书?自己设计的产品是否已审核过2D和3D。 是。 否。
★★★3.1 产品பைடு நூலகம்否为最新产品图
11.3 是否加必要模脚来保护模具下面的相关配件,模脚是否可使A\B板侧单独竖直摆放? 11.4 各模板、模仁及大块镶件是否有做吊装工艺螺丝孔,拆装螺丝孔?不规则零件工艺基准是否有设计? 十 11.5 回针是否单边避空0.25mm?中托司是否单边避空0.25mm、有否加取出镙牙? 一 11.6 撑头大小、位置、数量是否合理? 模 胚 11.7 各模板与模仁等强度是否足够?是否有加工变形或受热、受力变形的倾向? 11.8 各模板之间是否按要求做撬模槽?各板是否有起吊螺丝?导套末端是否有设计排气槽、是否在模具顶部和底部? 11.9各模板之间是否有管钉,管钉是否有取出螺丝? 11.10 顺序开模的动作先后及开模距离正确吗?顺序: 。
模具设计自检表
分模线是否合理,客户是否有确认 □
产品是否会产生模具薄钢
□
检查产品是否有厚胶部位并已预减胶 □
备注
镶拼方法是否合理 □ 不能有倒扣和尖钢 □
材料热处理工艺是否合理 □
有无留出内模锁位 □ 有无基准角 □ 内模定位是否有困难 □
内模长、宽、高较大时是否影响加工 □ 有无装夹位
□
2.内模料
各镶拼件是否有相应字码 □
行位限位方式是否合理 □
行位是否需要耐磨板
□
行位弹簧大小、长度、压缩比是否正确 □ 行位是否有加冷却水
□
行位尺寸较大时,是否有导滑槽
□ 是否需要作镶拼件,是否容易加工 □
行位动力机构为油缸时,油缸的缸径、行程、固定方式是否合理 □
行位出模导致产品变形时,是否有行位顶出机构 □
行位是否影响合模 □
行位是否需要延时机构 □
前模抽芯机构之型芯是否影响流道取出 □
抽芯机构复位动作是否合理
□
6.镶件 镶件定位方式是否合理 □
有无可换镶件
□
大镶件有无运水
□
镶件是否易装、拆模
□
顶针、直顶、斜顶出胶位时,是否会夹住产品 □ 顶针类避免与前模面直接碰撞 □
顶针大小、位置、长度是否合理
□
7.顶出 机构
有托顶针、扁顶针、托位避空是否足够,托位是否标准
□
有没有隔热板
□
热嘴头部有没有冷却水 □
温控连接器,型号、排布位置是否合理 □ 浇道/总重量比率<0.3 □
2
1.产品 5.机构
产品图是否为最新
□
有公差要求尺寸满足公称尺寸在公差带中间 □
行位型芯过长时,有否留出定位,防止型芯变形 □ 滑块导向长度大于全长2/3 □
模具设计评审检查表
零件号数模版本号零件类别材料信息材料牌号公司模具材料牌号类似零件收缩率验证结果OKNOKN/A成型部件斜顶(或顶杆)运动到底,要保证3mm 间隙要保证运动结束时与产品有3mm 间隙运动干涉分析斜顶热处理不应放在容易与对手件干涉或产生异响的区域分型线不可分在零件R 角处或是否获得SGM QD/Design/外观工程师/SQE 批准模具结构不可有“薄铁”、“尖角”斜顶行程斜顶杆直径斜顶座是否是顺序阀分型线抛光斜顶杆衬套斜顶杆需要做淬火处理斜顶杆最大角度模具强度型芯或型腔面皮纹面浇口位置动模采用镶件的方式,抛光时,将镶件安装到定模,镶件与定模的产品面一起抛光(外观面)开模方向都至少有3°脱模斜度门板以上大模具〉=20mm流道的流长电镀级ABS+PC≤200mm电镀级ABS≤250mm分型线处模具配合阶差在SGM的认可清单中选取材料供应商收缩率范围分型线不可在A 面或外分是否获得SGM QD/Design/外观工程师/SQE 批准外分 内分一膜一腔 一膜多腔外饰件 内饰件 电镀件 皮纹件 油漆件 高光件 匹配件模具等级IP 、DP <=15° ,其余<=12°流道脱模斜度浇注系统冷流道满足Moldflow 填充分析的各项指标要求皮纹每增加0.015mm 深度,沿开模方向上在原有脱模斜度上至少增加1°采用标准件浇口类型冷流道长度需控制在80mm 以内后续浇口容易切除,不可对外观面产生损伤Moldflow 填充分析分型线位置模具插穿角度冷料井建议双衬套导向热流道每个冷流道的转角,都须有冷料井分型线处最小插穿角度为7°浇口分型线GM材料标准模具收缩率分析结果确认零件名称模具设计评审资质模具供应商检验项目姓名是否自动脱浇口顺序阀须采用圣万提(Synventive )热流道基本要求能否满足GMW15424(2013版)模具设计评审检查表Mold Design Checklist零件基本信息模具设计工程师模具类型模具钢材信息。
模具设计自检表
OK
无 此
说明:此检查表由模具设计负责人检查工作后填写,要求做到每项内容不出错漏,填写好表格后交给主管签名后存档。存档期一年.
审核:
日 期:
版模 具模 具
A
模胚系列
1
模胚是 否订购
2
唧嘴与 顶棍孔
3
运水出 入口与
4
所有螺 丝运水
5
运水接 头是否
6
山打螺 丝限位
7
需要特 别的配
8
热流道 模胚加
9
顶针头 按要求
10
细水口A 板超过
11
顶出板 行程是
12
撑头是 否足够
13
密集的 顶针和
14
方铁是 否按客
15
撑头, 开框角
B
水口结构
16
水口位 置与客
17
潜水的 流道顶
18
透明产 品流道
C
行位结构
19
行位行 程是否
20
天侧行 位是否
21
行位压 块是否
未 确
东莞市模具
模具设计自检表
模具设 计:
检验项目
OK
无 此
D
22
23
24
E
25
26
27
28
29
30
32
F
32
33
34
35
36
37
3842
检验结果综合
检查日 期:
运 水 运水距离 是否在 塞运水需 按客人要 运水离胶 位不超过 顶 出 顶针不能 在规定的 非平面针 是否有定 水口针是 否符合图 有司筒和 斜顶的需 行位下有 顶针需要 所有顶针 及配件均 顶出不够 需要保留 内 模 成品模穴 确认已乘 模仁尺寸 与订料尺 模仁表面 画好排 晒纹是否 达到要求 模仁是否 刻上編 大面积的 插穿和碰 薄钢料和 细孔需要 分模线是 否按客人 夹线和顶 针披锋不 产品晒字 不能影响 大钢料正 面需要做
- 1、下载文档前请自行甄别文档内容的完整性,平台不提供额外的编辑、内容补充、找答案等附加服务。
- 2、"仅部分预览"的文档,不可在线预览部分如存在完整性等问题,可反馈申请退款(可完整预览的文档不适用该条件!)。
- 3、如文档侵犯您的权益,请联系客服反馈,我们会尽快为您处理(人工客服工作时间:9:00-18:30)。
□50.主流道的冷料段长度为2倍流道直径。
□51.浇口之大小,位置、点数等是否合适。平衡进胶是否考虑了。结合线位置是否合适。
□52.流道取出方式是哪一种:□自动落下□手取□机械手。
□53.唧嘴流道-水口拉针之型式是否合适。
□29.母模导柱(三板模)的大小及长度是否合适。
□30.公模导柱的大小()mm,及长度是否合适。
□31.模仁排气是否设计,排气的方式及位置是否适合。
□32.内、外拉杆的大小及行程是否足够,以及内拉杆弹簧规格是否正确。
□33.三板模抓料梢的尺寸及固定方式是否适当。
□34.是否须加隔热板(PC料),两板模是否有防开板。
□35.公模板及承板间是否加定位梢及定位螺钉。
□36.滑块配置方向是否理想。定位是否安全。(天、地、右、左)
□37.滑块压板是否装设定位梢2支。
□38.滑块斜导柱斜度是否小于滑块铲机斜度2°。
□39.滑块耐磨板位置是否适切。是否标准化(厚度8 or 10mm)。
□40.滑块的行程是否足够,滑座大小、斜梢大小是否适当。
□11.顶出方式及位置是否正确,是否平衡,有否做位置记号。
□12.回位梢的大小()mm。
□13.回位弹簧的选取Φ径、长度及强度、偷孔大小、深度是否正确。
□14.顶板导柱是否已安装,其位置及大小是否合适,最少2支,其直径要大过回位梢。
□15.限位柱是否已设计,其尺寸及位置是否合适。
□17.顶针是否凹入成品,位置、大小是否合适,长度是否正确,有否做防转设计。
□66.是否放置流道及浇口放大图。
□67.BOM表上的资料是否正确。
□68.模具零件部号、名称、材质、数量是否正确,是否需要热处理。
□69.图面是否全部放置于指定位置。
□70.图面是否依1∶1的实际尺寸绘制,并存档于电脑中。
* 打“√”表示该项目通过打“×”表示该项未能通过打“/”表示未涉及此项目
编制/日期审核/日期批准/日期:
□54.针点状胶口、香蕉胶口等是否做了凹形位。
□55.三板模之流道以机械手取出时,是否要设计机械手之抓水口。
□56.顶出行程是否足够。牛角浇口时, 顶出行程是否足够。
□57.水口之二次加工是否容易。
五.冷却系统
□58.冷却水路大小( ),是否足够,且平衡。注意不可与任何零件干涉而产生破孔。
□59.水咀接头的规格型号、避空孔是否符合要求。
□22.产品顶出距离是否足够。(注意:顶出量不可超过塑料机之最大顶出量。)
□23.是否有先复位机构。是否装设行程开关。
三.模具结构
□24.是否翻图。
□25.模具的分模面是否与客户要求的內容一致。
□26.模肉固定螺丝大小, 分布位置是否合适。
□27.吊模孔是否与其它零件干涉造成吊模困难。
□28.吊模孔螺丝大小, 分布位置是否合适。
明记工业设计
模具设计检查表
表单编号:
检查人
模具编号
项目编号
部门
设计者
日期
一.产品资料事项
□1.是否确认为最新版的产品图。品名:版本:接图日期:
□2.塑料:(),缩水率:()/1000,模穴数:()穴。
□3.产品内厚是否平均,是否会造成缩水。局部较厚胶位缩水痕迹如何克服。
□4.脱模斜度是否足够。
□5.咬花之花纹型式及纹号, 脱模斜度是否与花纹深度配合。咬花纹号( )。
□6.日期章、穴号之规格、位置及字样,须凹入成品,是否客户有指示。
□7.重要公差(外径、平面度、偏摆度、同心度)要特别注意。单向公差是否有处理。
□8.与客户检讨事项是否全部执行。
□9.注意易变形及缩水的地方。
□10.模具表面处理:□咬花□喷砂□刻字□印刷□打光□电镀考虑是否需要预留加工余量。
二.顶出机构
□18.顶针及套筒长度是否正确,套筒针在下ቤተ መጻሕፍቲ ባይዱ定板上不可使用无头螺钉固定。
□19.KO孔的大小Φ()mm,数量()个,及位置是否符合机台。
□20.机台吨数()Tons。模座的大小是否适合机台生产。模图上是否有表达哥林柱位置、大小。
□21.定位环的大小Φ()mm,是否符合机台。唧嘴之Φ径、R、深度是否合适。
□41.斜梢的长度是否足够。
□42.压板螺钉不可与水孔干涉。
□43.是否有加定位钢珠或弹簧,止动螺钉。
□44.斜顶是否有定位平面。
□45.斜顶是否安置耐磨板。
□46.插穿面小于3度时,是否使用直身管位块。
四.流道系统
□47.进浇方式:□潜水式□边浇口□小点进浇□其他(),是否与客户要求相同。
□48.流道的大小是否合理:□圆形直径,□U形,□梯形规格,是否平衡。
□60.O型密封圈之规格大小、数量是否正确。
□61.冷却回路之编号是否指示了。(如: IN1 、OUT1)。
六.其它
□62.模架,模肉,及其它零件是否选定了合适的材料。
模架:前模肉:后模肉:滑 块:斜 顶:
□63.各零件的热处理之硬度是否合适。
□64.前后模主视图是否表示完整,剖视图是否表示完整。
□65.是否放置产品3D示意图于装配图。