压铸件产品外观质量验收标准
压铸件外观检验标准
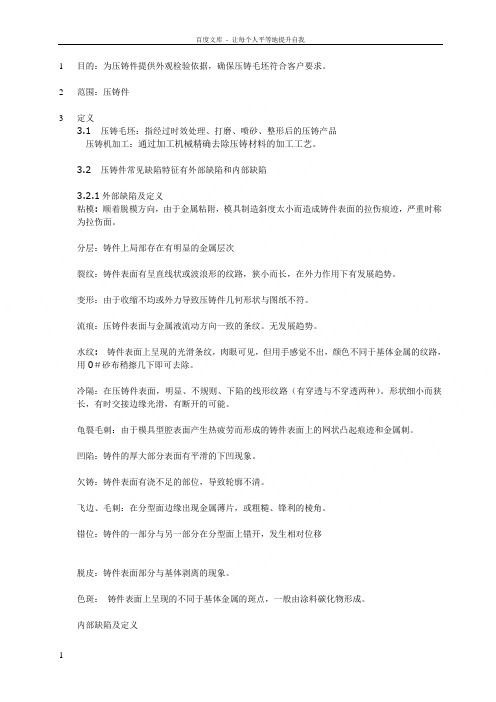
1目的:为压铸件提供外观检验依据,确保压铸毛坯符合客户要求。
2范围:压铸件3定义3.1压铸毛坯:指经过时效处理、打磨、喷砂、整形后的压铸产品压铸机加工:通过加工机械精确去除压铸材料的加工工艺。
3.2压铸件常见缺陷特征有外部缺陷和内部缺陷3.2.1外部缺陷及定义粘模: 顺着脱模方向,由于金属粘附,模具制造斜度太小而造成铸件表面的拉伤痕迹,严重时称为拉伤面。
分层:铸件上局部存在有明显的金属层次裂纹:铸件表面有呈直线状或波浪形的纹路,狭小而长,在外力作用下有发展趋势。
变形:由于收缩不均或外力导致压铸件几何形状与图纸不符。
流痕:压铸件表面与金属液流动方向一致的条纹。
无发展趋势。
水纹: 铸件表面上呈现的光滑条纹,肉眼可见,但用手感觉不出,颜色不同于基体金属的纹路,用0#砂布稍擦几下即可去除。
冷隔:在压铸件表面,明显、不规则、下陷的线形纹路(有穿透与不穿透两种)。
形状细小而狭长,有时交接边缘光滑,有断开的可能。
龟裂毛刺:由于模具型腔表面产生热疲劳而形成的铸件表面上的网状凸起痕迹和金属刺。
凹陷:铸件的厚大部分表面有平滑的下凹现象。
欠铸:铸件表面有浇不足的部位,导致轮廓不清。
飞边、毛刺:在分型面边缘出现金属薄片,或粗糙、锋利的棱角。
错位:铸件的一部分与另一部分在分型面上错开,发生相对位移脱皮:铸件表面部分与基体剥离的现象。
色斑:铸件表面上呈现的不同于基体金属的斑点,一般由涂料碳化物形成。
内部缺陷及定义砂孔:在压铸件中,由于压铸的特殊性,铝合金是在高温、高速、高压的状态下成型的,所以压铸件内部是不可避免的存在孔洞,我们统称这些孔洞为砂孔。
缩孔:铸件凝固过程中,金属补偿不足所形成的呈现暗色、形状不规则的孔洞,即为缩孔气孔:因卷入气体而导致的压铸件内部的孔状缺陷,解剖后外观检查或探伤检查,气孔具有光滑的表面、形状为圆形。
脆性:铸件基体金属晶粒过于粗大或极小,使铸件易断裂或破碎渗漏:压铸件经耐压试验,产生漏气、渗水硬点:机械加工过程或加工后外观检查或金相检查:铸件上有硬度高于金属基体的细小质点或块状物使刀具磨损严重,加工后常常显示出不同的亮度。
压铸件外观通用检验标准(带图实例)
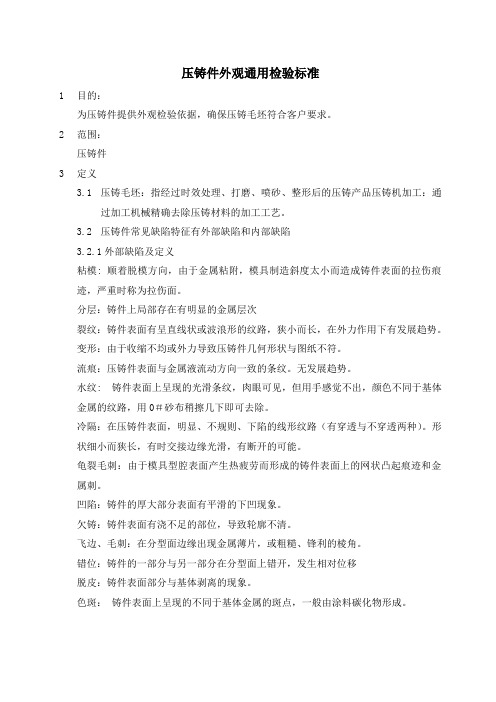
压铸件外观通用检验标准
1目的:
为压铸件提供外观检验依据,确保压铸毛坯符合客户要求。
2范围:
压铸件
3定义
3.1压铸毛坯:指经过时效处理、打磨、喷砂、整形后的压铸产品压铸机加工:通
过加工机械精确去除压铸材料的加工工艺。
3.2压铸件常见缺陷特征有外部缺陷和内部缺陷
3.2.1外部缺陷及定义
粘模: 顺着脱模方向,由于金属粘附,模具制造斜度太小而造成铸件表面的拉伤痕迹,严重时称为拉伤面。
分层:铸件上局部存在有明显的金属层次
裂纹:铸件表面有呈直线状或波浪形的纹路,狭小而长,在外力作用下有发展趋势。
变形:由于收缩不均或外力导致压铸件几何形状与图纸不符。
流痕:压铸件表面与金属液流动方向一致的条纹。
无发展趋势。
水纹: 铸件表面上呈现的光滑条纹,肉眼可见,但用手感觉不出,颜色不同于基体金属的纹路,用0#砂布稍擦几下即可去除。
冷隔:在压铸件表面,明显、不规则、下陷的线形纹路(有穿透与不穿透两种)。
形状细小而狭长,有时交接边缘光滑,有断开的可能。
龟裂毛刺:由于模具型腔表面产生热疲劳而形成的铸件表面上的网状凸起痕迹和金属刺。
凹陷:铸件的厚大部分表面有平滑的下凹现象。
欠铸:铸件表面有浇不足的部位,导致轮廓不清。
飞边、毛刺:在分型面边缘出现金属薄片,或粗糙、锋利的棱角。
错位:铸件的一部分与另一部分在分型面上错开,发生相对位移
脱皮:铸件表面部分与基体剥离的现象。
色斑:铸件表面上呈现的不同于基体金属的斑点,一般由涂料碳化物形成。
压铸件检验标准

文件名称压铸件检验标准生效日期页码 1 of 3 使用状态文件编号版本 A / 0 审核拟定目的确保本公司压铸件制程或进料品质符合客户要求。
范围适应于压铸件制程或进料入库检验。
抽样标准MIL-STD-105E单次Ⅱ级正常检验;CR=0;MA=1.0;MI=2.5。
检验环境在正常光源条件下,距离30cm远检验,以及适宜的角度检验产品。
参照标准1、GB / T2828.1-2003逐批检查计数抽样及抽样表。
2、GB / T 6414-1999铸件尺寸公差。
3、GB/T 11350机械加工余量。
4、GB/T 15115-94铝合金压铸标准。
5、GB 7000.1-2007灯具第一部分:一般要求与试验。
序号检验项目接收标准检验工具及方法缺陷描述缺陷等级致命(CR)严重(MA)轻微(MI)1外观物件的外表面之合模线不能高出平面0.05mm。
目视样板手感卡尺塞规物件的外表面之合模线高出平面0.05mm以上。
√物件的边沿、孔位不能有刺手的披锋及尖角。
物件的边沿、孔位有刺手的披锋及尖角。
√孔位周边披锋,组装后可遮盖。
孔位周边披锋,组装后不能遮盖。
√孔位周边披锋,不影响产品或对内部接线无损伤。
孔位周边披锋,影响产品组装或不能装配。
√影响产品装配,或对内部接线有损伤。
√物件表面不能有明显缩水痕。
物件的主视面,有明显缩水痕。
√物件的次要面缩水面积≤2mm2,缩水深度0.05mm。
√产品外表面及口边不能有缺料痕。
产品外表面及口边,有明显的缺料痕。
√产品孔边缺料,在组装后可遮盖,不影响产品结构。
产品孔边缺料,在组装后不可遮盖,但不影响产品结构。
√产品孔边缺料,在组装后可遮盖,但影响产品的组装、结构。
√缺料面积≤4mm2,不影响产品组装、结构。
√表面龟裂纹明显,但经加工可除去,不影响产品外观。
表面龟裂纹明显,但经加工不可除去,影响产品外观。
√序号检验项目接收标准检验工具及方法缺陷描述缺陷等级致命(CR)严重(MA)轻微(MI)1外观产品外表面花纹痕迹明显,经后续加工可消除。
压铸件外观标准
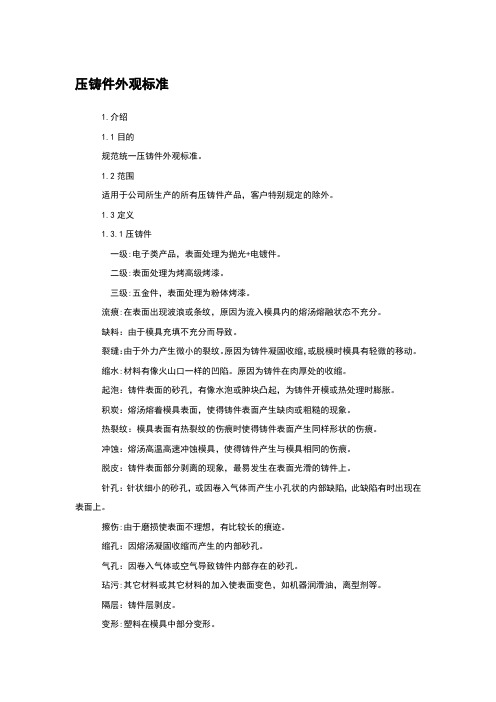
压铸件外观标准1.介绍1.1目的规范统一压铸件外观标准。
1.2范围适用于公司所生产的所有压铸件产品,客户特别规定的除外。
1.3定义1.3.1压铸件一级:电子类产品,表面处理为抛光+电镀件。
二级:表面处理为烤高级烤漆。
三级:五金件,表面处理为粉体烤漆。
流痕:在表面出现波浪或条纹,原因为流入模具内的熔汤熔融状态不充分。
缺料:由于模具充填不充分而导致。
裂缝:由于外力产生微小的裂纹。
原因为铸件凝固收缩,或脱模时模具有轻微的移动。
缩水:材料有像火山口一样的凹陷。
原因为铸件在肉厚处的收缩。
起泡:铸件表面的砂孔,有像水泡或肿块凸起,为铸件开模或热处理时膨胀。
积炭:熔汤熔着模具表面,使得铸件表面产生缺肉或粗糙的现象。
热裂纹:模具表面有热裂纹的伤痕时使得铸件表面产生同样形状的伤痕。
冲蚀:熔汤高温高速冲蚀模具,使得铸件产生与模具相同的伤痕。
脱皮:铸件表面部分剥离的现象,最易发生在表面光滑的铸件上。
针孔:针状细小的砂孔,或因卷入气体而产生小孔状的内部缺陷,此缺陷有时出现在表面上。
擦伤:由于磨损使表面不理想,有比较长的痕迹。
缩孔:因熔汤凝固收缩而产生的内部砂孔。
气孔:因卷入气体或空气导致铸件内部存在的砂孔。
玷污:其它材料或其它材料的加入使表面变色,如机器润滑油,离型剂等。
隔层:铸件层剥皮。
变形:塑料在模具中部分变形。
凹陷:由于不同的材料的结合度和收缩率不同,引起表面凹陷。
拉伤:铸件表面的磨损或磨擦使得表面不理想。
腐蚀:在材质表面有不连续的痕迹,由氧化引起。
凹痕:由于挤压或撞击而产生的凹坑。
毛刺:在孔或边有粗糙和锋利的棱角(相对于材料的厚度和凸起的高度)。
结合线:在两处或更多的材料融合点有线条(并且终止了结合或流动)分模线:在模具的两块或镶块之间有一条明显的线,例如:如果模具安装不当,在模具的主要部分能明显的看到明显的看到微小的凸起的线条。
1.3.2加工件机加工残留铝屑:在加工后的螺牙内卡有铝屑,这会导致通规不通。
滑牙:螺牙不完整或低孔径大而导致的实配不牢固。
压铸件品质检验规范

压铸件质检规范1、目的明确压铸件品质验收规范,规范检验动作,使检验、判定规范能达到一致性2、适用范围本规范适用于公司配套的锌合金压铸件的外观检验,包括毛坯、成品)完成铸造后机械加工的产品)。
3、技术要求3.1压铸件质量要求3.1.1压铸件应符合零件图样的规定。
3.1.2表面质量3.1.2.1压铸件表面粗糙度应符合GB/T6060.1的规定。
3.1.2.2压铸件表面不允许有裂纹、欠铸、疏松、气泡和任何穿透性缺陷。
3.1.2.3压铸件表面允许有擦伤、凹陷、缺肉和网状毛刺等缺陷。
但缺陷必须符合表1规定。
表1压铸件表面质量要求缺陷名称缺陷范围数值备注擦伤深度(mm)≤0.10面积不超过总面积的百分数5凹陷凹入深度(mm)≤0.30缺肉深度(mm)≤0.50长度不大于(mm)2所在面上不允许超过的数量2离压铸件边缘距离(mm)≥4间距(mm)≥10网状毛刺高度(mm)≤0.23.1.2.4压铸件的浇口、飞边、溢流口、隔皮、顶杆痕迹等应清理干净。
但允许留有痕迹。
3.1.2.5若图样无特别规定,有关压铸工艺部分的设置,如顶杆位置、分型线的位置、浇口和溢流口位置等由生产厂自行规定。
3.1.2.6压铸件需要特殊加工的表面,如抛光、喷丸、镀铬、涂覆、阳极氧化、化学氧化等须在图样上注明。
3.1.3压铸件机加工平面加工后的表面质量3.1.3.1不允许有影响使用的局部铸态表皮存在。
3.1.3.2不允许有超过表2规定的孔穴存在。
表2压铸件机加工平面允许的孔穴项目最大直径(mm)最大深度(mm)最多个数/cm2边缘间最小距离(mm)孔穴0.50.2243.1.4压铸件机械加工螺纹的表面质量3.1.4.1压铸件机械加工螺纹的头两扣不允许有任何缺陷,其余部分螺纹不允许有表3所规定的孔穴缺陷。
表3机械加工螺纹规定的孔穴缺陷范围螺距(mm)平均直径(mm)≤螺纹工作长度内个数≤深度(mm)≤两孔的边距(mm)≥≤0.751122>0.75 1.54 1.553.1.4.2压铸件不铸底孔加工后的螺纹表面质量见表4的规定。
压铸件喷涂系列产品外观通用检验标准

页 序: 2/5刮伤、划伤(有感)宽0.20mm以内,长度10mm以内,间距100mm以上,可以接收3处或参照样板宽0.30mm以内,长度20mm以内,间距150 mm以上,可以接收5处或参照样板可接受,但不能对产品造成功能性影响,具体可参照样板。
无感刮/划伤参照磨花、磨痕要求刀痕、砂带痕(包括拉模伤)深度≥0.40mm不接受或参照样板深度≥0.80mm不接受或参照样板可接受,但不能对产品造成功能性影响,具体可参照样板。
凹陷、压伤、碰伤ф≦2 mm,H≦0.2 mm间距(同一个面)≥100mm,不露底可以接收2处,或参照样板ф≦3 mm,H≦0.5 mm间距(同一个面)≥100 mm,不露底可以接收3处,或参照样板可接受,但不能对产品造成功能性影响,具体可参照样板。
顶针印、行位印H≦0.5 mm或参照样板H≦1.0 mm或参照样板可接受,但不能对产品造成功能性影响,具体可参照样板。
不能影响产品组装冷隔、冷纹凹入深度≥0.1 mm面积≥10c㎡不接受参照样板凹入深度≥0.2 mm面积≥20c㎡不接受参照样板可接受,但不能对产品造成功能性影响,具体可参照样板。
印痕、流痕凹入深度≥0.20 mm面积≥10c㎡不接受或参照样板凹入深度≥0.40mm面积≥20c㎡不接受或参照样板可接受,但不能对产品造成功能性影响,具体可参照样板。
孔穴、针孔ф≦0.5间距≥10mm个数≦3可以接受或参照样板ф≦1.0间距≥10mm个数≦6可以接受,或参照样板可接受,但不能对产品造成功能性影响,具体可参照样板。
缺料、崩缺不允许,或参照样板不允许,或参照样板可接受,但不能对产品造成功能性影响,具体可参照样板。
裂纹、裂痕(含龟裂纹)素材裂纹遮盖不住,或涂层龟裂纹,不允许或参照样板H≤0.2 mm 面积≤20c㎡,涂层不允许脱落,可接受,或参照样板可接受,但不能对产品造成功能性影响。
具体可参照样板。
批锋、毛边(含二次批锋)高≥0.15 mm,厚≥0.3mm有利边刮手不接受或参照样板高≥0.3 mm,厚≥0.5mm有利边刮手不接受或参照样板可接受,但不能对产品造成功能性影响,具体可参照样板。
压铸件外观检验标准
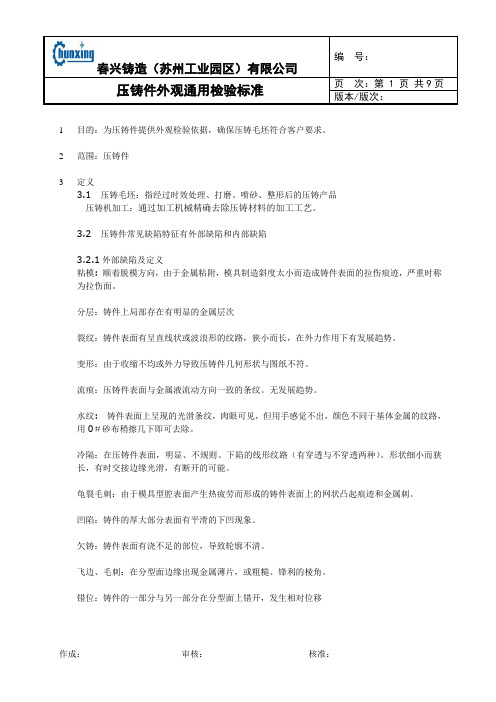
压铸件外观通用检验标准页次:第 1 页共9页版本/版次:1目的:为压铸件提供外观检验依据,确保压铸毛坯符合客户要求。
2范围:压铸件3定义3.1压铸毛坯:指经过时效处理、打磨、喷砂、整形后的压铸产品压铸机加工:通过加工机械精确去除压铸材料的加工工艺。
3.2压铸件常见缺陷特征有外部缺陷和内部缺陷3.2.1外部缺陷及定义粘模: 顺着脱模方向,由于金属粘附,模具制造斜度太小而造成铸件表面的拉伤痕迹,严重时称为拉伤面。
分层:铸件上局部存在有明显的金属层次裂纹:铸件表面有呈直线状或波浪形的纹路,狭小而长,在外力作用下有发展趋势。
变形:由于收缩不均或外力导致压铸件几何形状与图纸不符。
流痕:压铸件表面与金属液流动方向一致的条纹。
无发展趋势。
水纹: 铸件表面上呈现的光滑条纹,肉眼可见,但用手感觉不出,颜色不同于基体金属的纹路,用0#砂布稍擦几下即可去除。
冷隔:在压铸件表面,明显、不规则、下陷的线形纹路(有穿透与不穿透两种)。
形状细小而狭长,有时交接边缘光滑,有断开的可能。
龟裂毛刺:由于模具型腔表面产生热疲劳而形成的铸件表面上的网状凸起痕迹和金属刺。
凹陷:铸件的厚大部分表面有平滑的下凹现象。
欠铸:铸件表面有浇不足的部位,导致轮廓不清。
飞边、毛刺:在分型面边缘出现金属薄片,或粗糙、锋利的棱角。
错位:铸件的一部分与另一部分在分型面上错开,发生相对位移压铸件外观通用检验标准页次:第 2 页共9页版本/版次:脱皮:铸件表面部分与基体剥离的现象。
色斑:铸件表面上呈现的不同于基体金属的斑点,一般由涂料碳化物形成。
32.2内部缺陷及定义砂孔:在压铸件中,由于压铸的特殊性,铝合金是在高温、高速、高压的状态下成型的,所以压铸件内部是不可避免的存在孔洞,我们统称这些孔洞为砂孔。
缩孔:铸件凝固过程中,金属补偿不足所形成的呈现暗色、形状不规则的孔洞,即为缩孔气孔:因卷入气体而导致的压铸件内部的孔状缺陷,解剖后外观检查或探伤检查,气孔具有光滑的表面、形状为圆形。
压铸件质量表面标准(参考资料)

压铸件图纸无特殊要求时,表面质量按二级进行检验,有关内容如下:1、铸件清理后的表面质量⑴铸件的浇口、飞边、溢流口、隔皮等应清理干净,但允许流有清理痕迹。
⑵顶浇口、端浇口、环行浇口的处理按相关规定执行。
⑶在不影响使用的情况下,因去除浇口、溢流口时所形成的缺肉或高出均不得超过壁厚的四分之一,并且不得超过1.5mm。
2、铸件不加工表面的质量⑴不允许有裂纹、欠铸、疏松和任何穿透性的缺陷。
⑵不允许有超过表1 规定范围的花纹、麻面和有色斑点。
表1⑶在不影响使用和装配的情况下网状毛刺和痕迹不超过以下规定:锌合金、铝合金铸件其高度不大于0.2mm,铜合金铸件不大于0.4mm。
⑷由于模具组合镶并或受分形面影响而形成铸件表面高低不平的偏差,不得超过有关尺寸公差。
⑸推杆痕迹凹入铸件表面的深度不得超过该处壁厚的十分之一,并不超过0.4mm。
在不影响铸件使用的情况下,推杆痕迹允许凸起,凸起高度不大于0.2mm。
⑹工艺基准面、配合面上不允许存在任何凸起的痕迹;装饰面上不允许有推杆痕迹。
⑺穿孔顶端的隔皮厚度不允许超过表 2 规定。
表2⑻铸件上的图案、文字、线条、符号必须清晰,文字笔划宽度不小于0.25mm;高度不大于笔划宽度。
⑼各类铸件的表面缺陷详见表3。
3、待加工表面的质量⑴不允许有超过加工余量范围的表面缺陷和痕迹。
⑵不允许有凸起高度超过1mm 以上的推杆痕迹,对工艺基准面上不准有凸起的推杆痕迹。
表34、铸件机械加工后的表面质量⑴不允许有影响使用的局部铸态表皮存在。
⑵不允许有超过表4 所规定的孔穴存在。
表 4每种铸件按标准制作极限样件。
附录名词解释1、孔穴:气孔、缩孔和夹杂物所形成的孔洞。
⑴气孔:卷入压铸件内部的气体所形成的形状较规则的表面光滑的孔洞。
⑵缩孔:压铸件在冷凝过程中,由于内部补偿不足所造成的形状不规则的表面较粗糙的孔洞。
⑶夹杂物:混入压铸件内的金属或非金属杂质。
2、气泡:压铸件皮下气孔中的气体鼓起所形成的泡。
3、凹陷:压铸件平滑表面上出现凹瘪的部分。
- 1、下载文档前请自行甄别文档内容的完整性,平台不提供额外的编辑、内容补充、找答案等附加服务。
- 2、"仅部分预览"的文档,不可在线预览部分如存在完整性等问题,可反馈申请退款(可完整预览的文档不适用该条件!)。
- 3、如文档侵犯您的权益,请联系客服反馈,我们会尽快为您处理(人工客服工作时间:9:00-18:30)。
本标准定义来料或成品外观质量的基本要起,并作为允收/拒收准则。
2 适用范围
来料或成品。
3 检测面的分级:
A级面:使用者经常看到的面,如产品的上表面、正面、需要丝印的面等。
B级面:在不移动的情况下,使用者偶尔能看到的面,如产品的后面、侧面等。
C级面:产品在移动或被打开时才能看到的面,如产品的底面,内部零件的表面等。
4 检测条件
4.1、所有检验均应在正常照明,并模拟最终使用条件下进行。
检测过程中不使用放大镜,所检验表面和
人眼呈45°角。
A级面在检测时应转动,以获得最大反光效果。
B级面和C级面在检测期间不必转动。
光源=40W荧光灯
毫米
了
4.2、A级面停留10秒,B级面停留5秒,C级面停留3秒。
5 金属件外观检验标准
5.1 允收总则
5.1.1 可接受的缺陷不能影响该零件的装配和功能,否则将被拒收。
5.1.2 缺陷允收定义了900mm2的区域内各类缺陷的最大允收数量。
但是,两个区域或两个以上明显缺陷
不能相连。
5.2缺陷定义
5.2.1生锈/氧化:暴露在空气中的金属表面发生的化学反应,包括变黄以及出现其它异常。
5.2.2变色:底色或预期的颜色发生改变,或零件表面的颜色不一致。
5.2.3刮伤:零件表面的呈条状的浅沟,包括露底与不露底。
5.2.4压痕:由尖锐物件在零件表面造成的沟痕,指甲能够感受到。
5.2.5镀痕/流痕:由于镀层厚度不均匀造成零件表面上波纹状或条状异常的区域。
5.2.7灰尘或油脂:在制造过程中产生并留在零件表面上的赃污(未清洗)。
5.2.8斑点/颗粒:涂装面或零件表面任何非预期的异物。
5.2.9凹坑:零件表面弹坑状的缺陷。
5.2.10模压痕:因成形模具在零件表面造成的工艺痕,所有零件的模压痕的位置和大小都一样,均
匀分布
5.3 缺陷允收表每个面的缺陷数量不能超过允收的界限,如下表所示:
缺陷允收表
6.1允收总则
6.1.1所有的等级面应当喷涂完好且满足颜色、光泽度、厚度、附着力等方面的要求。
6.1.2液体喷涂允许补漆,但补漆后的表面应满足喷涂面缺陷允收表中B级面和C级面的允收标准。
6.1.3缺陷允收定义了900 mm2的区域内各类缺陷的最大允收数量。
对于较大的零件表面,可允收数量
和该表面所含900 mm2区域数量成正比,但是,两个或两个以上缺陷不能相连。
6.2缺陷定义
6.2.1杂质:喷涂面上的外来物。
6.2.2凹痕:基体材料压痕造成的喷涂面局部凹陷。
6.2.3掉漆:局部表面掉漆造成的缺陷。
6.2.4刮痕:浅底的沟槽。
6.2.5桔皮:喷涂面因涂料附着力差而导致起皱,象桔子皮样的外观。
6.2.6流痕:喷涂涂料过多且不均匀且干燥导致的流痕。
6.2.7变色:喷涂面颜色不一致。
6.2.8涂层过薄/过厚:涂层厚度不够,小于50um并不能大于200um。
6.2.9气泡:有气泡或无附着力的喷涂区域。
6.2.10污迹:由于基体材料缺陷或不干净而导致零件喷涂表面有污迹或颜色不规则。
6.2.11未保护:产品螺纹空、尺寸精度高德广孔、加工装配缅因未采取有效的措施保护而进粉影响使用
6.3缺陷允收表(喷漆/喷涂面)
每个面缺陷的总数不超过允收的界限,如下表所示:
6.4涂层可靠度试验
所有的零件必需是无尘,无脂,无油和其它物质。
由运输材料引起而且能够被空气吹走的灰尘是可被接收的。
油漆外观接受或退回必须在与样板比较的基础上,样板必须每6个月检查和更新一次。
7 涂层印刷产品(刻字)外观标准
7.1 允收总则
7.1.1所有的等级面应当印刷完好且满足颜色、光泽度、附着力等方面的要求。
7.1.2 可接受的缺陷不能影响该零件的装配和功能,否则,将被拒收。
7.1.3 印刷产品包括:零件表面之丝印、标签之印刷等。
7.2 允收缺陷表(产品印刷)
每个面缺陷的总数不超过允收的界限,如下表所示:
印刷产品缺陷允收表
8.压铸件接收/判退.标准
作业指导书
文件编号
版本号
标题:产品外观质量验收标准页码9/10 9.加工件接受/判退标准
9.1缺陷分类
影响功能的缺陷
螺纹滑牙、烂牙影响扭力,钻孔后不通孔背面鼓起起泡等。
毛刺/锐边
所有孔,缝,边和角必须没有毛刺和锐边.允许的毛刺的高度不能超过0.20㎜
漏工序
漏工序都是不可接受的。
9.2.鉴别标准
加工别不良项目A级面B级面C级面
机加工烂牙不可不可≤整个螺牙的10%
切边缺料/压伤/裂缝同压铸件标准
毛刺
锉伤不可
锉刀痕不可不可深≤0.2㎜
外观油渍不可不可不可
发黑不可不可≤整个产品的5%挂液不可不可≤1处
色差不可不可依11颜色的标准
10 注塑件外观标准
10.1 允收总则
10.1.1所有的等级面应当注塑完好且满足颜色、光泽度、光洁度等方面的要求。
10.1.2 可接受的缺陷不能影响该零件的装配和功能,否则将被拒收。
10.2 允收缺陷表
每个面缺陷的总数不超过允收的界限,如下表所示:
塑胶件缺陷允收表
面积10mm2,不可超过两
处
数量不可超过两个,单个直径2mm 数量不可超过三个,单个
直径4mm
数量不可超过两处,长
度5mm 数量不可超过三处,长度
10mm
面积10mm2,不可超过两
处
11.1允收总则
11.1.1满足颜色、光泽度、厚度、附着力等方面的要求。
11.1.2缺陷允收定义了900 mm2的区域内各类缺陷的最大允收数量。
对于较大的零件表面,可允收数量
和该表面所含900 mm2区域数量成正比,但是,两个或两个以上缺陷不能相连。
11.2缺陷定义
11.2.1起皮:电镀层翘起造成的缺陷。
11.2.2桔皮:电镀层因附着力差而导致起皱,象桔子皮样的外观。
11.2.3变色:电镀层颜色不一致。
11.2.4镀层过薄:露出基体本色。
11.2.5气泡:电镀过程中产生的气泡。
11.2.6污迹:由于基体材料缺陷或不干净而导致零件表面有污迹或颜色不规则。
11.2.7磨花:受到外部磨擦产生的非预期颜色、光泽度、厚度等。
11.2.8刮伤:零件表面的呈条状的浅沟,包括露底与不露底。
11.2.9镀痕/流痕:由于镀层厚度不均匀造成零件表面上波纹状或条状异常的区域。
11.2.10麻点/斑点/颗粒:涂装面或零件表面任何非预期的异物。
11.2.11凹坑:零件表面弹坑状的缺陷。
电镀件表面缺陷允收表。