延迟焦化工艺新进展
延迟焦化技术发展
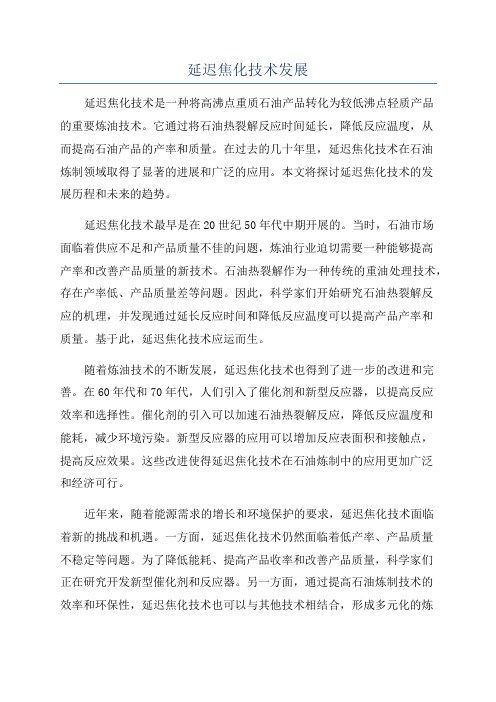
延迟焦化技术发展延迟焦化技术是一种将高沸点重质石油产品转化为较低沸点轻质产品的重要炼油技术。
它通过将石油热裂解反应时间延长,降低反应温度,从而提高石油产品的产率和质量。
在过去的几十年里,延迟焦化技术在石油炼制领域取得了显著的进展和广泛的应用。
本文将探讨延迟焦化技术的发展历程和未来的趋势。
延迟焦化技术最早是在20世纪50年代中期开展的。
当时,石油市场面临着供应不足和产品质量不佳的问题,炼油行业迫切需要一种能够提高产率和改善产品质量的新技术。
石油热裂解作为一种传统的重油处理技术,存在产率低、产品质量差等问题。
因此,科学家们开始研究石油热裂解反应的机理,并发现通过延长反应时间和降低反应温度可以提高产品产率和质量。
基于此,延迟焦化技术应运而生。
随着炼油技术的不断发展,延迟焦化技术也得到了进一步的改进和完善。
在60年代和70年代,人们引入了催化剂和新型反应器,以提高反应效率和选择性。
催化剂的引入可以加速石油热裂解反应,降低反应温度和能耗,减少环境污染。
新型反应器的应用可以增加反应表面积和接触点,提高反应效果。
这些改进使得延迟焦化技术在石油炼制中的应用更加广泛和经济可行。
近年来,随着能源需求的增长和环境保护的要求,延迟焦化技术面临着新的挑战和机遇。
一方面,延迟焦化技术仍然面临着低产率、产品质量不稳定等问题。
为了降低能耗、提高产品收率和改善产品质量,科学家们正在研究开发新型催化剂和反应器。
另一方面,通过提高石油炼制技术的效率和环保性,延迟焦化技术也可以与其他技术相结合,形成多元化的炼油工艺。
例如,可以将延迟焦化技术与催化裂化技术结合,实现高效的石油加工和产品转化。
未来,延迟焦化技术的发展趋势将主要集中在以下几个方面。
首先,随着石油市场的变化和能源需求的增长,石油炼制技术将会更加注重经济可行性和环保性。
延迟焦化技术需要进一步降低能耗、提高产品收率和改善产品质量,以适应未来的发展需求。
其次,新型催化剂和反应器的研发是延迟焦化技术发展的关键。
延迟焦化密闭除焦技术发展现状及展望
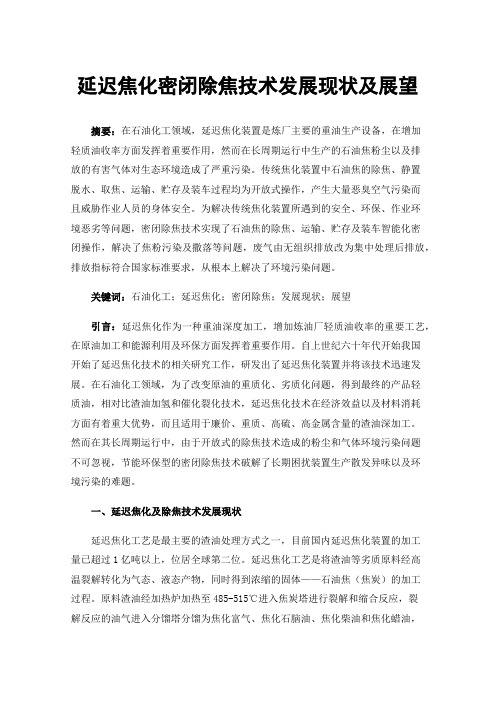
延迟焦化密闭除焦技术发展现状及展望摘要:在石油化工领域,延迟焦化装置是炼厂主要的重油生产设备,在增加轻质油收率方面发挥着重要作用,然而在长周期运行中生产的石油焦粉尘以及排放的有害气体对生态环境造成了严重污染。
传统焦化装置中石油焦的除焦、静置脱水、取焦、运输、贮存及装车过程均为开放式操作,产生大量恶臭空气污染而且威胁作业人员的身体安全。
为解决传统焦化装置所遇到的安全、环保、作业环境恶劣等问题,密闭除焦技术实现了石油焦的除焦、运输、贮存及装车智能化密闭操作,解决了焦粉污染及撒落等问题,废气由无组织排放改为集中处理后排放,排放指标符合国家标准要求,从根本上解决了环境污染问题。
关键词:石油化工;延迟焦化;密闭除焦;发展现状;展望引言:延迟焦化作为一种重油深度加工,增加炼油厂轻质油收率的重要工艺,在原油加工和能源利用及环保方面发挥着重要作用。
自上世纪六十年代开始我国开始了延迟焦化技术的相关研究工作,研发出了延迟焦化装置并将该技术迅速发展。
在石油化工领域,为了改变原油的重质化、劣质化问题,得到最终的产品轻质油,相对比渣油加氢和催化裂化技术,延迟焦化技术在经济效益以及材料消耗方面有着重大优势,而且适用于廉价、重质、高硫、高金属含量的渣油深加工。
然而在其长周期运行中,由于开放式的除焦技术造成的粉尘和气体环境污染问题不可忽视,节能环保型的密闭除焦技术破解了长期困扰装置生产散发异味以及环境污染的难题。
一、延迟焦化及除焦技术发展现状延迟焦化工艺是最主要的渣油处理方式之一,目前国内延迟焦化装置的加工量已超过1亿吨以上,位居全球第二位。
延迟焦化工艺是将渣油等劣质原料经高温裂解转化为气态、液态产物,同时得到浓缩的固体——石油焦(焦炭)的加工过程。
原料渣油经加热炉加热至485-515℃进入焦炭塔进行裂解和缩合反应,裂解反应的油气进入分馏塔分馏为焦化富气、焦化石脑油、焦化柴油和焦化蜡油,缩合反应生成的焦炭留在焦炭塔内。
延迟焦化装置通常采取一个加热炉对应两个个焦塔的生产流程,一个塔完成裂解和缩合的出焦流程,而另一个焦塔则完成焦炭的冷却、除焦和预热流程,两个焦炭塔的轮流切换形成了一个连续的生产过程。
简述延迟焦化的一种新技术

简述延迟焦化的一种新技术
延迟焦化是炼油行业常用的一种重要工艺,它能够将原油加工成高附加值的石化产品。
但是传统的延迟焦化工艺存在一些问题,比如产生大量的二氧化碳和硫化物废气,造成环境污染,同时对设备的磨损也比较大。
为了解决这些问题,石化企业开始研究和开发新的延迟焦化技术。
其中一种新技术被称为“高效延迟焦化技术”,它采用了先进的催化剂和反应技术,可以减少废气排放,提高产品质量,同时延长设备的使用寿命。
这项技术的核心是在延迟焦化反应器中添加催化剂,使反应更为充分,同时减少废气生成。
此外,该技术还可以采用多级反应器来提高转化率和产品选择性,从而获得更高价值的产品。
高效延迟焦化技术不仅可以减少环境污染,还可以提高能源利用效率,降低石化企业的生产成本,促进石油化工行业的可持续发展。
在未来,这种技术有望成为延迟焦化的主流技术,为石油化工行业的发展带来更多的机遇和挑战。
- 1 -。
延迟焦化在炼油工业中的技术优势及进展

延迟焦化在炼油工业中的技术优势及进展引言炼油工业一直是国民经济的支柱产业之一,其技术水平和生产效率直接关系到国家的能源安全和经济发展。
延迟焦化作为炼油工业中的关键技术之一,在提高产品质量、降低能耗、增加产值等方面具有重要意义。
本文将重点介绍延迟焦化在炼油工业中的技术优势及进展。
一、延迟焦化技术优势1. 优化产品结构延迟焦化可以将重油转化为高附加值产品,如汽油、柴油等,通过高温高压下的催化反应,改变油品分子结构,提高产品质量。
这一优势可以帮助炼油企业提高产品附加值,增加经济效益。
2. 降低燃料成本在延迟焦化过程中,废气和废热可以被回收再利用,降低燃料成本。
延迟焦化可以提高原油利用率,减少资源浪费,降低成本。
3. 减少环境污染延迟焦化过程中产生的废气和废水可以通过先进的污染处理技术进行处理,达到国家环保标准。
与传统炼油工艺相比,延迟焦化对环境影响更小。
4. 提高装置稳定性采用延迟焦化技术可以降低炼油装置的生产风险,提高运行稳定性。
这对于保障生产安全,确保供应稳定具有重要意义。
1. 催化剂技术的提升催化剂是延迟焦化过程中的关键因素之一,不断提升催化剂的活性和稳定性可以提高产品质量和产率。
目前,石油化工行业正在加大对新型催化剂的研发投入,以适应市场对高品质产品的需求。
2. 自动化控制技术的应用延迟焦化装置需要复杂的自动化控制系统来确保生产过程的稳定运行。
近年来,随着工业互联网技术的发展,炼油企业对自动化控制技术的应用程度不断提高,有助于提高生产效率和安全性。
3. 能源利用的优化能源在炼油工业中是一个重要的生产成本,延迟焦化技术的发展也包括对能源利用的优化。
通过余热回收、废气处理等技术手段,可以降低能耗,提高能源利用效率。
4. 环保技术的创新随着环保要求的不断提高,炼油企业在延迟焦化技术中也积极探索更多的环保技术。
采用生物降解剂处理废水、引入低排放燃烧技术等,为炼油工业的可持续发展做出贡献。
1. 高效、低排放未来延迟焦化技术的发展方向将更加注重实现高效生产、低排放。
延迟焦化工艺新技术探索

延迟焦化工艺新技术探索我国大部分原油具有重质渣油多、沥青质、残炭量少的特点,采用延迟焦化工艺加工重质渣油,可以得到高达78%的馏分油收率。
所得馏出油中,汽油馏分较少,柴油与汽油的产量比值可达2.3左右,经加氢精制后,产品质量可达到规格要求,比较适合我国市场对中间馏分日益增长的需求状况。
标签:延迟焦化;工艺;新技术焦炭化过程(简称焦化)是以渣油为原料,在高温(500-550℃)下进行深度热裂化反应的一种热加工过程,包括延迟焦化、流化焦化和灵活焦化等多种工艺过程。
反应产物有气体、汽油、柴油、蜡油(重馏分油)和焦炭。
焦化工艺自20世纪30年代开发成功以来,已成为燃料型炼油厂主要的渣油转化过程。
1 延迟焦化产品主要特点焦化汽油的特点是烯烃含量高,安定性差,马达法辛烷值较低。
汽油中的硫、氮和氧的含量较高(与原料性质有关),经过稳定后的焦化汽油只能作为半成品,必须进行精制脱除硫化氢和硫醇后才能作为成品汽油的调和组分。
焦化重汽油组分经过加氢处理后可作为催化重整的原料,以进一步提高质量。
表15-1为阿拉伯重质原料的减压渣油进行焦化时,所得焦化汽油的加氢精制数据以及加氢精制前后的汽油质量比较。
焦化柴油的十六烷值较高,含有一定量的硫、氮和金属杂质;含有一定量的烯烃,性质不安定,必须进行精制脱除硫、氮杂质,使烯烃、芳烃饱和才能作为合格的柴油组分。
焦化过程中,转化为焦炭的烃类所释放的氢转移至蜡油、柴油、汽油和气体之中。
由于原料中的氢转移方向与催化裂化不同,使焦化柴油的质量明显优于催化裂化柴油。
焦化蜡油是指350-500℃的焦化馏出油,也称焦化瓦斯油(CGO)。
焦化蜡油性质不稳定,它与焦化原料油性质和焦化的操作条件有关。
焦化蜡油可作为加氢裂化或催化裂化的原料,有时也用于调和燃料油。
焦炭,即石油焦,是黑色或暗灰色坚硬固体石油产品,带有金属光泽,呈多孔性,是由微小石墨结晶形成粒状、柱状或针状构成的炭体物。
石油焦组分是碳氢化合物,含碳90%-97%,含氢1.5%’-8环,还含有氮、氯、硫及重金属化合物。
延迟焦化在炼油工业中的技术优势及进展

延迟焦化在炼油工业中的技术优势及进展延迟焦化(Delayed Coking)是一种重要的炼油工业技术,它在原油加工过程中具有重要的作用。
延迟焦化工艺可以将重质原油中的高分子碳氢化合物转化为高附加值的产品,具有很高的经济效益。
本文将详细介绍延迟焦化在炼油工业中的技术优势及进展。
延迟焦化工艺是一种将重质原油中的高分子碳氢化合物转化为低碳烯烃和焦油的方法。
在延迟焦化装置中,原油经过加热后,进入一个高温高压的反应器中,在高温条件下,原油分子内部的碳-碳键被断裂,形成烯烃和芳烃,同时生成一定量的焦炭。
经过蒸馏,可以得到低碳烯烃和焦油产品。
延迟焦化工艺的技术优势主要体现在以下几个方面:延迟焦化工艺可以有效提取出较高附加值的产品。
在延迟焦化装置中,原油中的高分子碳氢化合物经过催化裂化反应后,可以得到大量的轻质低碳烯烃和芳烃产品。
这些产品在化工行业中有着广泛的用途,可以用于生产乙烯、丙烯、苯乙烯等重要化工产品,具有很高的经济价值。
延迟焦化工艺可以降低原油的硫含量。
在延迟焦化装置中,高温高压的反应条件能够有效地将原油中的硫化合物转化为可分离的硫化氢,从而有效降低产品中的硫含量。
这对于符合环保要求的产品生产具有非常重要的意义。
延迟焦化工艺还可以充分利用原油中的残渣。
在炼油过程中,原油中的残渣通常被视为难以处理的废物,但延迟焦化工艺可以将这部分残渣有效地转化为有价值的产品,从而实现了资源的充分利用。
延迟焦化工艺在炼油工业中的应用已经有了长足的进展。
随着技术的不断发展,延迟焦化装置的设计和操作水平也在不断提高。
一方面,新型的延迟焦化装置不断出现,可以实现更高的产品收率和更低的能耗;延迟焦化工艺的自动化程度也在不断提高,能够更好地保证生产的安全和稳定性。
延迟焦化工艺也在不断拓展其应用范围。
除了在常规炼油工业中的应用外,延迟焦化工艺还可以用于生产生物柴油和生物乙二醇等生物能源产品。
这些产品具有较高的环保性能和可再生性,能够更好地满足当今社会对清洁能源的需求。
延迟焦化炉的操作及结构改进

延迟焦化炉的操作及结构改进首先,针对延迟焦化炉的操作改进方面,我们可以考虑增加炉内煤料的分布均匀性。
传统的延迟焦化炉中,煤料往往堆积在炉床的中央,导致中央部分的煤料温度过高,而周围区域的温度较低。
为了改进这一点,可以在炉底增加一层可移动的隔板,通过调整隔板的位置来改变煤料的分布情况,使得煤料能够均匀分布在炉床上。
其次,我们还可以对延迟焦化炉的结构进行改进,以提高焦炭的产量和质量。
首先,可以考虑增加炉体的高度,将炉体分成多个层次。
每个层次的高度可以适当调整,从而使得不同层次的温度和气氛条件能够更好地控制。
其次,在炉底设置一层金属网,用于支撑煤料和疏气,增加煤料在炉床上的接触面积,提高利用率。
另外,在炉体的上部可以安装排气设备,以排除焦炭燃烧过程中产生的有害气体,净化环境。
此外,还可以考虑在延迟焦化炉的上部增加预热区。
传统的延迟焦化炉中,煤料是直接投入到高温区域进行焦化的,导致煤料的焦炭化过程不均匀。
通过在炉体的上部增加预热区,可以将煤料在温度较低的区域进行预热,使煤料的温度均匀分布,并预先燃烧部分杨煤,增加焦炭的产量和质量。
另外,可以考虑在延迟焦化炉的控制系统中引入先进的自动化技术,以提高炉内温度、压力等参数的控制精度。
可以通过在炉体的不同位置安装温度、压力等传感器,实时监测炉内参数,并通过控制系统进行调整,使得焦炭的生产过程更加稳定和可控。
总之,通过对延迟焦化炉的操作和结构进行改进,可以提高焦炭的产量和质量,同时还能够降低生产过程中的能耗和环境污染。
以上只是一些改进的想法,具体的实施方案需要根据实际情况进行研究和验证。
探究分析延迟焦化工艺技术及其进展

2017年03月探究分析延迟焦化工艺技术及其进展孙飞杜标(甘肃省玉门市玉门炼化总厂焦化车间,甘肃酒泉735200)摘要:延迟焦化工艺装置在油产品加工中发挥着重要作用,属于常用石油二次加工技术,同时也是世界渣油深度加工的重要方法。
本文分析的是延迟焦化工艺技术及其进展,具体分析中主要从延迟焦化工艺加工能力现状、工艺技术及其进展等方面进行分析。
关键词:延迟焦化工艺技术;研究进展延迟焦化工艺是以渣油、重油等为原料,通过在延迟焦化反应装置中发生一系列的反应,并最终形成气体、柴油、汽油以及焦炭等。
全世界范围内轻质油品需求量的增加对于重油加工工艺提出了更高的要求,在深加工过程中,从技术可行性、经济合理性以及操作便捷性等多角度考虑,延迟焦化工艺技术均有着明显的优势,本文主要根据国内外相关研究报道,就分析延迟焦化工艺技术及其进展分析如下:1延迟焦化工艺加工能力现状斧式、平炉、接触、延迟、流化以及灵活焦化等均属于焦化的主要形式,不同的焦化工艺其在工艺技术、操作便捷性、成本投入、设备复杂度、产品收率等方面都存在着不同,综合不同焦化方法的优缺点,由于延迟焦化操作简单、工艺简单、反应装置灵活等优势,在焦化工艺中得到了重要应用。
根据最新统计资料显示,截止到2012年,全世界范围内焦化能力已经超过了2.35亿吨,其中主要以延迟焦化装置为主,在焦化装置中由于发生的焦化反应是经过延迟并在焦炭塔内完成的,因而叫做延迟焦化。
随着延迟焦化工艺技术的发展,现阶段可采用的原料种类进一步增加,在焦化反应过程中的环保型进一步提高,液体收率明显提高,极大地保证了全球范围内的轻质油供应[1]。
2延迟焦化工艺技术及其进展分析2.1焦化工艺装置的大型化发展伴随着延迟焦化工艺技术的发展,焦化工艺技术进一步成熟,与此同时,焦化工艺装置呈现出了大型化发展趋势,比如上个世纪80年代,世界范围内最大的延迟焦化工作装置,每年的生产能力可达到301顿,而到了90年代,在延迟焦化装置改造的基础上,焦化工艺最大处理能力可达到503万吨,与此同时,我国延迟焦化装置的生产能力也逐渐增加,比如:在2004年我国扬子石化建成了国内最大的延迟焦化装置,年生产能力可达到160万吨。
- 1、下载文档前请自行甄别文档内容的完整性,平台不提供额外的编辑、内容补充、找答案等附加服务。
- 2、"仅部分预览"的文档,不可在线预览部分如存在完整性等问题,可反馈申请退款(可完整预览的文档不适用该条件!)。
- 3、如文档侵犯您的权益,请联系客服反馈,我们会尽快为您处理(人工客服工作时间:9:00-18:30)。
延迟焦化工艺新进展2005.01.28 09:05:59 中国石油信息网放大字体缩小字体打印本页延迟焦化工艺发展重点是优化操作条件,在增加产能的同时追求最大的液体产率、减少生焦率和尽可能处理劣质原料。
福斯特-惠勒公司、大陆石油公司(现大陆菲利浦斯公司)等有关延迟焦化工艺和设备的发展大大改进了延迟焦化技术。
使循环时间已由24hr缩短到18hr以内,从而扩大了现有焦炭塔的处理能力。
焦炭塔清焦的自动化作业提高了安全性,并有助于缩短循环时间。
在低压(0.103MPa)下操作的无重油外部循环的新设计提高了液收,最大量减少了焦炭产率。
循环馏出油代替循环重油,减少了焦炭产率,延长了停工维修之间的运转时间。
新的双燃烧器加热炉设计和改进的炉管材质提高了焦化加热炉温度。
现在标准的焦炭塔直径为8.2~8.5m,9.1m直径的焦炭塔也已投入应用。
延迟焦化的总液收达到57%以上(占减压渣油进料)。
美国Valero炼制公司得克萨斯炼厂投资2.75亿美元,于2003年底投产的248万t/年延迟焦化装置,采用了福斯特-惠勒公司SYDEC工艺,该厂主要加工墨西哥重质、含硫的玛亚原油,延迟焦化装置加工玛亚减压渣油和中东原油沥青混合料,使用该劣质原料,使原料费用减小了1美元/bbl以上,使投资偿还率提高了3%。
延迟焦化装置可灵活加工各种原料,包括直馏、减粘、加氢裂化渣油、裂解焦油和循环油、焦油砂、FCC油浆、炼厂污油(泥)等60余种原料。
处理原料油的CCR为3.8%~45%(m),API重度2 O~20O。
委内瑞拉利用延迟焦化和加氢处理工艺对奥利诺柯原油进行改质,生产API 16 O~32 O、含硫<0.1%(m)的合成油。
较老的延迟焦化装置循环周期为12~14hr,目前新设计的循环周期一般为18~20hr,鲁姆斯公司的设计操作周期为<18hr。
延迟焦化的循环式操作带来许多操作问题,例如压力变动、温度变动和操作不稳等。
为了减轻这些问题的严重程度,美国焦化技术公司开发了一种专有技术MaxCoking,可用于延迟焦化装置以提高其操作效率,并可改进下游操作。
该技术在提高焦化处理能力、提高液体产品收率、降低焦收率、降低硅抗泡剂的用量及费用、提高装置操作稳定性等方面进行了有益的改进。
该技术还具有投资少、对现有操作影响小等优点。
MaxCoking是一套专有的过程控制程序,用于改进延迟焦化的操作稳定性、可靠性和获利能力。
此技术的好处集中在压力控制系统和焦炭塔升温系统。
由于焦炭塔是轮换操作,在焦化周期的切换和升温阶段有大量压力损失。
此压力损失会加重焦炭塔内的泡沫生成,导致分馏塔干板压降损失,打乱分馏塔的温度和压力分布。
发泡失控会导致泡沫溢出,可能使装置停工。
轻度的泡沫溢出会缩短运转周期并带来大的维修问题。
泡沫会减小焦炭塔容积。
分馏塔异常会导致增加循环和损失液体产品回收量。
MaxCoking技术稳定焦炭塔压力的方法是在焦化周期中的升温和切换阶段将轻/重瓦斯油或石脑油从分馏塔循环至在线的热焦炭塔顶部,使轻瓦斯油或石脑油闪蒸增加焦炭塔内的热气体积,从而稳定焦炭塔压力,维持一个上升的压力分布。
在压力控制所需流率下,没有轻瓦斯油和石脑油冷凝,焦炭质量未降低。
MaxCoking技术在美国得克萨斯州帕萨迪纳炼厂得到了成功应用。
帕萨迪纳炼厂焦化装置能力为69万t/年,有两个焦炭塔,操作周期18hr,每日约产电极焦350t。
为了维持焦炭塔的压力分布,在升温和切换阶段以一定速率向焦炭塔注入石脑油,使系统压力提高27~34kPa。
操作员首先通过选择开关选定运行的焦炭塔,给压力控制阀输入压力设定点,压力变送器将压力信号送至压力控制阀,调节进入焦炭塔的石脑油流量,随压力的波动,控制阀开启或关闭。
由于循环比由1.16降至1,蒸馏塔顶罐压力由116 kPa降至70 kPa(表压),焦炭塔和分馏塔顶罐之间的压差减少21~3 kPa。
较低的焦化操作压力导致液收增加5%~10%(体积百分比),提高了处理量,产焦量减少16%,抗泡剂用量减少75%,加热炉能力提高10%。
该装置的年利润提高了1200万美元,而且投资较少。
进一步认识和评价延迟焦化工艺李家栋崔德春(中国石化集团公司石油化工科学研究院,北京,100083)比较了延迟焦化与催化裂化的经济性,在目前的价格情况下催化裂化的效益略高于延迟焦化。
通过对延迟焦化汽油加氢后与普通直馏汽油的乙烯裂解试验和比较,延迟焦化汽油加氢后可以作乙烯原料。
循环比的变化对产品分布影响很大,但循环比变化对经济效益影响不大。
关键词:延迟焦化工艺认识经济性1 前言延迟焦化是一个相当成熟的减压渣油加工工艺,多年来一直被作为一种普通的深加工手段。
近年来随着原油性质变差(指含硫量增加),焦化能力的趋势很快。
延迟焦化的蜡油在国内一般直接作为催化裂化的原料,但由于其含氮量高不受催化裂化的欢迎。
可有的延迟焦化装置为了以最低的投入扩大生产能力,采用小循环比甚至零循环比来扩大生产能力,造成焦化蜡油数量更多、质量更差,由此成为焦化装置的难点之一。
在未来的5年中,我国的延迟焦化装置还要发展,如何认识和评价延迟焦化装置在炼油厂中的位置显得更为重要。
2 延迟焦化裂化与催化裂化的比较以往催化裂化原料以直馏蜡油为主,而焦化以减压渣油为主要原料,两者由于原料价格不同造成可比性较差;但随着催化裂化掺渣油越来越多,两者的可比性越来越强。
近几年又开发了加工近乎100%减渣(大庆减渣)的催化裂化技术,使两者有很好的可比性。
以下就大庆减渣油为例,对两者进行比较。
表1、2所列的数据为:大庆石化公司延迟焦化装置、前郭炼油厂的渣油催化裂化装置和燕山石化公司催化裂化装置的原料性质和产品分布。
从两者的产品性质上看,随着技术的发展和对产品质量要求的提高,不仅催化裂化的柴油需进一步加工,其汽油也因其烯烃含量过高需进一步加工,和焦化汽柴油需进一步加工相似。
表3为两者的经济效益比较,所采用价格不含税。
为简化,将焦化蜡油采用催化裂化进一步处理,以减少一种产品。
在产品价格的选取上,焦化干气可作制氢原料,选价1 000元/t,催化干气作普通燃料选价800元/t;催化汽油性质优于焦化汽油(加氢后为优质乙烯料),考虑两者差价为80元/t,但催化柴油性质劣于焦化柴油,考虑两者差价为50元/t。
按表3中的价格,前郭的催化裂化的销售收入比焦化高40.68元/t原料,燕山的催化裂化比焦化高54.04远/t,但若考虑催化裂化的单位加工费要高于焦化(一般差20元/t),且燕山石化公司的催化裂化原料中含蜡油14.9%(蜡油与渣油的差价在300元/t以上),全渣油的催化裂化经济效益只略高于延迟焦化。
在前几年,汽油和柴油及汽油和石脑油价格差别较大时,对汽油质量没有烯烃含量要求时,催化裂化的效益是很高的,但现在差价趋小,两者的经济效益也就越接近。
但是并非所有的减渣象大庆减渣那样可大量掺到催化裂话原料中来代替延迟焦化,因而延迟仍起着催化裂化不可替代的作用。
表1 三个装置所采用的原料性质表2 焦化和催化裂化的产品分布表3 经济效益比较3 延迟焦化与乙烯原料的关系随着石油化工的发展,无论是树脂的发展,还是聚脂的发展都需要大量的石脑油为原料。
但我国大量的原油是石脑油含量不高的原油,远远不能满足乙烯工业和催化重整对原料的需求。
为此,需要从减压蜡油和减压渣油中获得石脑油,而加氢裂化与延迟焦化是最合适的手段。
焦化的自由基反应机理决定了焦化汽油和焦化柴油有较多的链烷烃和较少的芳烃。
表4是两个炼厂的焦化汽油经加氢后的性质,表中还列出A的马西拉石脑油的性质以资比较。
其中炼厂A几乎全加工进口原油,其焦化原料(减压渣油)极为复杂,表中的也门马西拉原油就是该厂加工的进口原油之一;炼厂B的焦化石脑油为鲁宁管输原油的减渣经延迟焦化而得。
将两个炼厂的焦化石脑油相比,由于炼厂B的焦化原料是芳香分、胶质和沥青质较高的减渣,因而焦化石脑油中链烷烃略少、芳烃略多,但总的差别不大。
表5列出这三种石脑油进行蒸汽裂解评价试验的结果,焦化汽油的乙烯、丙烯和总三烯收率都很高,可与一般石脑油相比。
大量工业运转经验表明延迟焦化的石脑油经加氢后是很好的乙烯原料,但是依目前国内炼厂焦化装置的规模和操作方式能提供的焦化汽油数量不多,只能作为一种补充。
要使焦化装置能提供更多的乙烯原料,一是要扩大延迟焦化装置的规模,而是要改变延迟焦化的操作方式,适宜提高焦化汽油干点,增加焦化汽油的收率。
表4 加氢后焦化汽油的性质表5 蒸汽裂解性能评价(工业工况)4 延迟焦化的循环比循环比或联合循环比对装置的加工量、产量、焦化产品的分布和性质都有较大影响。
一般延迟焦化装置循环比的设计值为0.4。
在文献中列出了我国两种主要减压渣油焦化时循环比对焦化产品分布的影响。
表6 是以大庆减压渣油为例列出循环比的影响。
表6 循环比对产品产率的影响(%)表6中还列出了以循环比0.2为基准,随循环比增大,焦化蜡油减少的差值与石油焦的增量。
由表6可见,蜡油在焦化的热裂化反应中生焦很少,为3.03%,而汽、柴油产品增加很多。
若以焦化蜡油为基准计算蜡油在反映过程中生成的汽柴油收率,汽油为33.3%,柴油为51.5%。
表7考察了循环比变化对焦化经济性的影响。
该表以年加工1 Mt大庆减压渣油为基准,参考大庆石化公司延迟焦化的收率和文献中的循环比影响数据而得。
由表7可知,焦化蜡油与柴油(或汽油)的比价对经济效益影响很大,本文所取蜡油价格为1 525元/t,蜡油与柴油的比价为0.87,略高于有关部门规定的蜡油(VGO)与柴油的比价;在此蜡油价格下循环比的变化使增加的销售收入与加工费的增加抵消,对经济效益的影响基本为零,即价格为焦化蜡油的临界价格,低于此价格,循环比增加,利润增加。
表7 循环比对焦化经济性的影响(年加工量1 Mt为基准)同时,循环比增加,蜡油的质量变好,对蜡油的下游加工装置是有利的;汽油数量增加为石油提供更多的原料,柴油数量增加了炼厂的汽柴比。
5 结论(1)延迟焦化的经济效益目前略低于渣油催化裂化,随着汽、柴油质量要求的提高和两者价格的接近,延迟焦化的经济效益也就越接近催化裂化。
(2)延迟焦化的汽油经加氢后是优质的乙烯原料,应充分利用。
(3)延迟焦化采用大循环比操作有利于增加乙烯原料和柴油产量;其经济效益处于边际状态。
(4)并非所有的减渣都可大量掺到催化裂化原料中,因而延迟焦化仍起着催化裂化不可替代的作用。
随着随着原油变色变差趋势日夜明显以及产品质量要求的提高,延迟焦化的作用将更为突出。
参考文献1 李志强.我国渣油深加工技术的新进展棗减压渣油催化裂化工艺技术的应用.石油炼制与化工,1999,1:7Having a Better Understanding and Evaluation of Delayed CokingProcessLi Jiadong Cui Dechun(Research Institute of Petrochemical Processing, SINOPEC, Beijing100083)ABSTRACTA comparison of economic indicators between delayed coking and catalytic cracking indicates that, under the condition of current price, the economic benefit of the latter is slightly higher than that of the former. Through the test and comparison of ethylene cracking of hydrogenated delayed coking gasoline and regular grade straight-run gasoline, it is showed that the former can be used as ethylene stock. The change of recycle ratio has quite big influences on the product distribution, but not very big on the economic benefit.Keywords: delayed coking, process, understanding, economic indicator延迟焦化:依靠自主创新实现领先跨越时间:2005-1-21 16:22:00 阅读224次1930年世界上第一套延迟焦化工业装置在美国建成1964年,被誉为新中国炼油技术“五朵金花”之一的我国第一套连续生产的延迟焦化工业装置建成投产2004年,应用具有我国专利特色的两套160万吨/年延迟焦化装置,在扬子石化和金陵石化先后实现一次试车成功去年年末,洛阳石化工程公司采用自行开发的一炉两塔工艺和可灵活调节循环比等技术设计的160万吨/年延迟焦化装置,在扬子石化和金陵石化先后实现了一次试车成功,并生产出了合格产品。