延迟焦化工艺流程
延迟焦化工艺流程

延迟焦化工艺流程延迟焦化1. 延迟焦化工艺流程:本装置的原料为温度90℃的减压渣油,由罐区泵送入装置原料油缓冲罐,然后由原料泵输送至柴油原料油换热器,加热到135℃左右进入蜡油原料油换热器,加热至160℃左右进入焦化炉对流段,加热至305℃进入焦化分馏塔脱过热段,在此与来自焦炭塔顶的热油气接触换热。
原料油与来自焦炭塔油气中被凝的循环油一起流入塔底,在380~390℃温度下,用辐射泵抽出打入焦化炉辐射段,快速升温至495~500℃,经四通阀进入焦碳塔底部。
循环油和减压渣油中蜡油以上馏分在焦碳塔内由于高温和长时间停留而发生裂解、缩合等一系列的焦化反应,反应的高温油气自塔顶流出进入分馏塔下部与原料油直接换热后,冷凝出循环油馏份;其余大量油气上升经五层分馏洗涤板,在控制蜡油集油箱下蒸发段温度的条件下,上升进入集油箱以上分馏段,进行分馏。
从下往上分馏出蜡油、柴油、石脑油(顶油)和富气。
分馏塔蜡油集油箱的蜡油在343℃温度下,自流至蜡油汽提塔,经过热蒸汽汽提后蜡油自蜡油泵抽出,去吸收稳定为稳定塔重沸器提供热源后降温至258℃左右,再为解吸塔重沸器提供热源后降温至242℃左右,进入蜡油原料油换热器与原料油换热,蜡油温度降至210℃,后分成三部分:一部分分两路作为蜡油回流返回分馏塔,一路作为下回流控制分馏塔蒸发段温度和循环比,一路作为上回流取中段热;一部分回焦化炉对流段入口以平衡大循环比条件下的对流段热负荷及对流出口温度;另一部分进水箱式蜡油冷却器降温至90℃,一路作为急冷油控制焦炭塔油气线温度,少量蜡油作为产品出装置。
柴油自分馏塔由柴油泵抽出,仅柴油原料油换热器、柴油富吸收油换热器后一部分返回分馏塔作柴油回流,另一部分去柴油空冷器冷却至55℃后,再去柴油水冷器冷却至40℃后分两路:一路出装置;另一路去吸收稳定单元的再吸收塔作吸收剂。
由吸收稳定单元返回的富吸收油经柴油富吸收油换热器换热后也返回分馏塔。
分馏塔顶油气经分馏塔顶空冷器,分馏塔顶水冷器冷却到40℃,流入分馏塔顶气液分离罐,焦化石脑油由石脑油泵抽出送往吸收稳定单元。
延迟焦化工艺流程
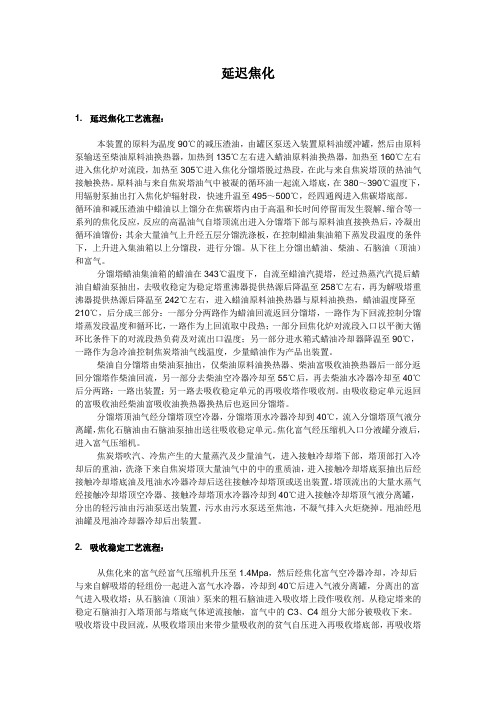
延迟焦化1. 延迟焦化工艺流程:本装置的原料为温度90℃的减压渣油,由罐区泵送入装置原料油缓冲罐,然后由原料泵输送至柴油原料油换热器,加热到135℃左右进入蜡油原料油换热器,加热至160℃左右进入焦化炉对流段,加热至305℃进入焦化分馏塔脱过热段,在此与来自焦炭塔顶的热油气接触换热。
原料油与来自焦炭塔油气中被凝的循环油一起流入塔底,在380~390℃温度下,用辐射泵抽出打入焦化炉辐射段,快速升温至495~500℃,经四通阀进入焦碳塔底部。
循环油和减压渣油中蜡油以上馏分在焦碳塔内由于高温和长时间停留而发生裂解、缩合等一系列的焦化反应,反应的高温油气自塔顶流出进入分馏塔下部与原料油直接换热后,冷凝出循环油馏份;其余大量油气上升经五层分馏洗涤板,在控制蜡油集油箱下蒸发段温度的条件下,上升进入集油箱以上分馏段,进行分馏。
从下往上分馏出蜡油、柴油、石脑油(顶油)和富气。
分馏塔蜡油集油箱的蜡油在343℃温度下,自流至蜡油汽提塔,经过热蒸汽汽提后蜡油自蜡油泵抽出,去吸收稳定为稳定塔重沸器提供热源后降温至258℃左右,再为解吸塔重沸器提供热源后降温至242℃左右,进入蜡油原料油换热器与原料油换热,蜡油温度降至210℃,后分成三部分:一部分分两路作为蜡油回流返回分馏塔,一路作为下回流控制分馏塔蒸发段温度和循环比,一路作为上回流取中段热;一部分回焦化炉对流段入口以平衡大循环比条件下的对流段热负荷及对流出口温度;另一部分进水箱式蜡油冷却器降温至90℃,一路作为急冷油控制焦炭塔油气线温度,少量蜡油作为产品出装置。
柴油自分馏塔由柴油泵抽出,仅柴油原料油换热器、柴油富吸收油换热器后一部分返回分馏塔作柴油回流,另一部分去柴油空冷器冷却至55℃后,再去柴油水冷器冷却至40℃后分两路:一路出装置;另一路去吸收稳定单元的再吸收塔作吸收剂。
由吸收稳定单元返回的富吸收油经柴油富吸收油换热器换热后也返回分馏塔。
分馏塔顶油气经分馏塔顶空冷器,分馏塔顶水冷器冷却到40℃,流入分馏塔顶气液分离罐,焦化石脑油由石脑油泵抽出送往吸收稳定单元。
延迟焦化工艺流程

延迟焦化工艺流程延迟焦化工艺是一种重要的炼油工艺,它能够将石油原油转化为高附加值的产品,如汽油、柴油和航空燃料等。
在延迟焦化工艺中,原油经过一系列的热裂解和重整反应,最终得到所需的产品。
本文将对延迟焦化工艺流程进行详细介绍。
首先,原油进入延迟焦化装置后,经过预热和预处理,进入裂解炉。
在裂解炉中,原油在高温和催化剂的作用下,发生裂解反应,将大分子烃类分解为小分子烃类。
这些小分子烃类是后续生产汽油和柴油的重要原料。
接下来,裂解产物进入分馏塔,经过分馏过程,将不同碳链长度的烃类分离出来。
在分馏塔中,轻质烃类如汽油被分离出来,而重质烃类如柴油则被留在塔底。
这一步骤是为了得到不同种类的产品,以满足市场的需求。
随后,分馏得到的产品进入催化重整装置。
在催化重整装置中,轻质烃类经过重整反应,得到高辛烷值的汽油。
这种汽油具有良好的抗爆性能,适合用于汽车和飞机的燃料。
最后,催化重整得到的汽油和分馏得到的柴油经过精制处理,去除杂质和硫化物,得到高品质的成品油。
这些成品油可以直接用于市场销售,也可以作为化工原料进一步加工。
延迟焦化工艺流程是一个复杂的过程,需要严格控制各个环节的操作参数,以确保产品质量和生产效率。
同时,还需要注重设备的维护和安全管理,确保生产过程安全稳定。
只有做好这些工作,才能保证延迟焦化工艺的顺利进行,为炼油企业创造更大的经济效益。
总之,延迟焦化工艺流程是炼油行业中的重要工艺之一,它能够将原油转化为高附加值的产品,满足市场需求。
在实际生产中,需要严格控制各个环节的操作,确保产品质量和生产效率。
同时,还需要注重设备的维护和安全管理,以保障生产过程的安全稳定。
希望本文的介绍能够对延迟焦化工艺有所了解,对相关行业人士有所帮助。
延迟焦化工艺流程

延迟焦化工艺流程延迟焦化工艺流程是一种能够将重质石油馏分转化为具有高热值和高炭素含量的焦炭的技术。
它是对传统的焦化工艺进行改进和优化,以减少生产焦炭过程中的环境污染和能源浪费。
延迟焦化工艺流程具有高效节能、环保低污染和资源综合利用的特点,在石油化工行业被广泛应用。
1.原料准备:在延迟焦化工艺中,主要原料为重质石油馏分,通常是从石油精炼过程中得到的渣油。
这些渣油首先被送入预处理装置,经过脱硫、脱水和脱盐等处理,以提高其炭含量和降低硫、氮等杂质的含量。
2.煤炭炭化:预处理后的渣油与煤炭混合后,进入煤气化炉进行炭化反应。
煤炭炭化过程中,渣油中的碳分子与煤炭中的碳分子发生化学反应,生成焦炭和煤气。
同时,煤炭中的含硫化合物也得到部分转化或吸附,以减小煤气中硫化物的含量。
3.煤气净化:产生的煤气含有一定的杂质,如硫化物、苯、酚等。
煤气进入净化装置,经过除硫、除苯等处理,使煤气中的有害物质达到排放标准,同时,其中的一部分能源也得到回收利用,用于工艺过程中的煤气加热等。
4.焦炭冷却:经过煤气净化后,煤气中的焦油被分离出来,作为石油化工原料的补充。
随后,焦炭经过冷却装置,使其温度降低至环境空气温度,以保证焦炭的质量和可收回的热能。
1.高效节能:延迟焦化工艺能够充分利用原料中的热能和化学能,使其转化为焦炭和煤气,减少能源浪费。
同时,延迟焦化过程中产生的煤气也能够回收利用,用于工艺过程中的能源供应。
2.环保低污染:延迟焦化工艺通过净化装置等设备对煤气中的有害物质进行处理,使得煤气排放达到环境保护要求。
此外,延迟焦化过程中采用的高效脱硫等技术能够显著降低硫化氢等有害气体的排放。
3.资源综合利用:延迟焦化工艺能够将废弃的重质石油馏分转化为焦炭和煤气,提高了资源的综合利用率。
同时,工艺中产生的焦油和焦炭也能够作为石油化工原料的补充,实现循环利用。
总之,延迟焦化工艺流程是一种高效、环保、资源综合利用的工艺,在石油化工行业有着广泛的应用和发展前景。
延迟焦化工艺流程

延迟焦化工艺流程
《延迟焦化工艺流程》
延迟焦化工艺流程是指在焦炉内将原料煤进行加热、热解、焦化等过程时,采用特定的操作方式和工艺条件,以延长煤在高温条件下的停留时间,达到提高焦炭质量和产量的目的。
在延迟焦化工艺流程中,关键是要掌握好加热速度、保持时间和降温速度。
首先,原料煤要缓慢加热至高温。
经过一定时间的保温,再逐渐升高温度,直至煤体内的挥发分和焦油完全被释放出来。
这样能够避免过快的加热导致焦炭内部形成裂缝或者其他缺陷,影响焦炭的质量。
同时,延长保温时间还能够增加焦炭的焦化程度,提高焦炭的强度和耐磨性。
另外,降温速度也是延迟焦化工艺中需要重视的一点。
在高温煤炭热解后,如果降温速度过快,可能会导致焦炭表面和内部温度差过大,形成热应力,影响焦炭的质量。
因此在降温过程中要采取逐步降温的方式,使焦炭内外温度均匀,减少热应力的产生。
延迟焦化工艺流程通过合理控制加热、保温和降温过程,可以提高焦炭的质量和产量,降低生产成本,对于煤炭加工行业具有重要的意义。
随着技术的不断进步和创新,延迟焦化工艺流程也将不断完善,为煤炭生产带来更多的经济和环保效益。
延迟焦化流程图及相关数据总结

1. 延迟焦化工艺在炼油厂重油深加工中作用
世界重油加工能力构成
2. 延迟焦化工艺特点--产品的灵活性焦炭塔压力及不同渣油焦化产品收率
2. 延迟焦化工艺特点--通过调节温度、压力和循环比等参数增加操作弹性
二. 延迟焦化工艺流程
典型的延迟焦化工艺流程-可调循环比焦化工艺流程
典型的延迟焦化工艺流程--CONOCO焦化零自然循环原则流程
放空系统流程
延迟焦化装置放空系统流程图
放空系统流程-美国ABB Lunnns公司延迟焦化装置放空流程
焦炭处理系统流程--直接装车
延迟焦化装置操作压力对产品收率的影响
焦化产品
12.0 12.4
0.7936 0.7923
1.4 1.3
焦炭塔压力对焦化馏出油产率的影响
联合循环比(TPR)对焦化液体产品收率的影响
联合循环比对大庆减压渣油焦化产品收率的影响
焦化工艺参数优化
延迟焦化产品收率及焦化重瓦斯油的质量比较
焦化工艺参数优化
生产加氢裂化原料的延迟焦化装置产品收率
项目
氮含量,ppm 庚烷不溶物,ppm 康氏残炭值,%(质) 特性因数,(K) 分馏试验,℃
10%(体)
50%(体)
干点
项目
焦化产品收率
干气,%(体)
液化气,%(体)
石脑油,%(体)
焦化轻瓦斯油,%(体) 焦化重瓦斯油,%(体) 焦炭,%(质)
焦化重瓦斯油性质
相对密度
镍+钒,ppm
康氏残炭值,%(质)。
延迟焦化工艺流程
延迟焦化工艺流程
延迟焦化是一种重要的煤炭加工工艺,它可以将煤炭转化为高附加值的产品,如焦炭和煤焦油。
延迟焦化工艺流程是一个复杂的过程,涉及到多种化学和物理反应。
本文将详细介绍延迟焦化工艺流程的各个步骤,以及其在煤炭加工中的重要性。
首先,延迟焦化工艺流程的第一步是原料的准备。
在这一步骤中,煤炭被破碎和研磨,以便于后续的处理。
然后,煤炭被混合和预热,以提高其可塑性和流动性。
这些步骤对于后续的焦化过程非常重要,因为它们可以影响最终产品的质量和产量。
接下来,煤炭被送入延迟焦化炉进行焦化。
在焦化炉中,煤炭经过高温热解,产生焦炭和煤焦油。
这一步骤需要严格控制温度和气氛,以确保产生高质量的产品。
此外,焦化炉的设计和操作也对最终产品的质量有着重要的影响。
在焦化过程中,煤炭中的挥发性物质被释放出来,形成焦炭和煤焦油。
焦炭是一种重要的工业原料,广泛用于冶金和化工行业。
而煤焦油则可以提炼出多种有机化合物,如苯、酚和萘等,具有很高的经济价值。
除了焦炭和煤焦油之外,延迟焦化过程还会产生焦炭气。
焦炭气中含有大量的一氧化碳和氢气,可以作为燃料或化工原料使用。
因此,合理利用焦炭气可以提高整个生产过程的经济效益。
总的来说,延迟焦化工艺流程是一个复杂而重要的煤炭加工过程。
通过严格控制每个步骤,可以获得高质量的焦炭和煤焦油,提高煤炭资源的利用效率和附加值。
同时,合理利用焦炭气也可以提高生产过程的经济效益。
因此,对延迟焦化工艺流程的研究和优化具有重要的意义,可以推动煤炭加工技术的进步,促进煤炭产业的可持续发展。
延迟焦化工艺流程
延迟焦化工艺流程延迟焦化是石油炼制中的一种重要工艺,它可以将重油转化为高附加值的产品,如天然气、汽油、柴油等。
延迟焦化的工艺流程一般包括以下几个步骤:首先是预热。
将原油加热至一定温度,以便提高反应速率和转化率。
预热过程通常采用换热器或者热交换器进行,将高温的尾气和原油进行热交换,使原油温度升高。
接下来是加氢加热。
将已经预热的原油通过加热装置进行加热,使其达到一定温度。
这一步骤主要是用于去除原油中的硫、氮等有害杂质,提高产品的质量。
然后是减压闪蒸。
将加热后的原油进入闪蒸器,通过减压将液体部分迅速蒸发,产生的蒸汽与部分液体一起进入下一步骤。
减压闪蒸可以有效降低凝点,提高原油的流动性。
接着是裂解反应。
将减压闪蒸后的原油进入焦化炉,加入适量的催化剂,进行裂解反应。
在高温和催化剂的作用下,长链烃分子会被打断并重组成短链烃分子,产生大量的裂解气体。
裂解气体中的轻质烃可以被进一步提炼出来,而重质烃则会形成焦炭。
然后是冷却和分离。
裂解反应产生的裂解气体会经过冷却装置,降低温度,使气态产品变成液态。
随后通过分离装置将液态产品和气态产品进行分离,得到焦炭、液体烃和尾气。
最后是产品处理。
焦炭可以用作冶金行业的燃料或者用于电力发电。
液体烃经过进一步的处理,可以得到纯净的汽油、柴油等燃料。
而尾气中含有大量的氢气和烃类物质,可以进行气体回收,回收后的氢气可用于加氢加热等环节,烃类物质则可以再次进入裂解反应进行处理。
总结来说,延迟焦化工艺流程包括预热、加氢加热、减压闪蒸、裂解反应、冷却和分离以及产品处理等步骤。
通过这一工艺流程,可以实现对原油的高效转化,获得高附加值的产品,提高石油炼制的经济效益和产品质量。
同时,延迟焦化工艺还可以通过回收部分气体,降低资源消耗和环境污染,具有重要的环保意义。
延迟焦化工艺流程
延迟焦化工艺流程
延迟焦化是一种重要的炼油工艺,其流程包括原油加热、裂解、冷凝、分馏等多个步骤。
在整个工艺流程中,各个环节的操作和控
制都至关重要,只有严格按照标准操作,才能保证生产出高质量的
产品。
下面将详细介绍延迟焦化工艺流程中的关键步骤。
首先,原油加热。
原油进入加热炉后,通过加热炉内的管道和
换热器进行加热,使其达到裂解温度。
在这一步骤中,需要确保加
热的均匀性和温度的准确控制,以避免原油在加热过程中发生结焦
或者温度过高导致裂解产物质量下降的问题。
其次,裂解。
原油在加热后进入裂解炉,经过高温和催化剂的
作用,发生分子结构的改变,产生裂解气体和液体产物。
在这一步
骤中,需要严格控制裂解温度、催化剂的投加量和裂解时间,以确
保裂解产物的质量和产量。
接着是冷凝。
裂解产物中的裂解气体进入冷凝器,在降温的作
用下,裂解气体中的液态成分被冷凝成液体产物,而气态成分则被
收集回收。
在冷凝过程中,需要保证冷凝器的冷却效果和冷凝温度
的控制,以确保液体产物的纯度和收率。
最后是分馏。
经过冷凝后的液体产物进入分馏塔,根据不同组
分的沸点差异,进行分馏分离,得到不同馏分产品。
在这一步骤中,需要严格控制分馏塔的温度和压力,以确保各个馏分产品的质量和
收率。
总的来说,延迟焦化工艺流程中的每个步骤都至关重要,需要
严格控制各项操作参数,确保产品的质量和产量。
只有通过精细的
操作和严格的控制,才能实现高效、稳定的生产。
希望本文对延迟
焦化工艺流程有所帮助,谢谢阅读。
延迟焦化工艺流程
延迟焦化工艺流程延迟焦化工艺是一种将高炉煤气或燃料油作为原料,通过高温裂解反应,生成焦化气体和焦炭的工艺。
该工艺可以分为两个主要步骤:一次焦化和二次焦化。
一次焦化是将原料经过高温加热,煤气裂解生成一次焦油、一次焦煤气和焦炭的过程。
二次焦化是将一次焦油在高温下经过再次加热,产生二次焦油、二次焦煤气和焦炭的过程。
然而,由于一次焦化和二次焦化反应速度快,设备容易受到气体和液体相互作用的灰尘和腐蚀物的损害,因此需要对延迟焦化工艺进行改进和优化,以提高工艺流程的稳定性和效率。
首先,延迟焦化工艺中的裂解炉是关键设备,对其进行改进和优化可以延缓反应速度。
一种常用的方法是增加炉体的长度和直径,以增加反应物在炉内停留的时间。
此外,还可以调整炉内的温度和压力,控制裂解反应的速率。
其次,通过改变反应物的配比,可以降低反应速率。
延迟焦化工艺中一次焦化反应通常采用恒温恒压裂解反应,通过控制一次焦化反应炉内的煤气与燃料油的混合比例,可以有效降低反应速率,延长裂解反应的时间。
此外,还可以使用添加剂来调节反应速率,如添加碱金属氧化物等。
再次,改进和优化焦化反应过程中的换热器可以提高工艺流程的稳定性和效率。
延迟焦化工艺中,换热器通常用于回收裂解反应产生的热量,并将其用于预热原料。
通过提高换热器的效率和热传导率,可以提高能量回收率,减少能源消耗。
最后,改进和优化焦化反应的控制系统可以提高工艺流程的稳定性。
延迟焦化工艺中,控制系统可以通过监测和调节温度、压力和流量等参数,实时控制和调整反应过程中的各项操作,以确保工艺的正常进行。
通过使用先进的控制算法和仪器设备,可以提高系统的响应速度和控制精度,降低操作风险和能源消耗。
综上所述,延迟焦化工艺流程的改进和优化可以通过调整反应条件、改变配比、优化换热器和改进控制系统等措施来实现。
这些措施可以延缓反应速度,提高工艺流程的稳定性和效率,从而达到节约能源、降低成本和保护环境的目的。
- 1、下载文档前请自行甄别文档内容的完整性,平台不提供额外的编辑、内容补充、找答案等附加服务。
- 2、"仅部分预览"的文档,不可在线预览部分如存在完整性等问题,可反馈申请退款(可完整预览的文档不适用该条件!)。
- 3、如文档侵犯您的权益,请联系客服反馈,我们会尽快为您处理(人工客服工作时间:9:00-18:30)。
炼油厂的炼油工艺流程介绍
上传时间:2009-07-31 12:03 点
击:110
正文:
二、60万吨/年加氢装置
1、反应部分
焦化汽油、焦化柴油从延迟焦化装置直接进料,为控制加氢反应平稳,应严格控制其进料比例。
两种原料进装置后经原料混合罐(D-201)混合,再经原料油泵(P-201/1、2)、过滤器(SR-201/1、2)、原料油脱水罐(D-202)进入原料油缓冲罐(D-203)。
原料油过滤和脱水的目的是为了脱除堵塞反应器上部床层的固体颗粒和影响催化剂强度的水分。
D-201、D-203用氮气气封保护。
D-203中的原料经反应进料泵(P-202/1、2)升压至9.6MPa(A),经流量控制,与来自新氢压缩机(K-201/1、2)和循环氢压缩机(K-202/1、2)的混合氢混合,首先经混氢原料(I)/反应产物换热器(E-204/1、2)换热,再经由混氢原料(Ⅱ)/反应产物换热器(E-201)与反应产物换热至199℃进入反应加热炉(F-201),加热至303℃进入至加氢反应器(R-201)中,该反应器设置二段催化剂床层,两床层间设有注急冷氢设施。
自反应器(R-201)来的反应产物经混氢原料(Ⅱ)/反应产物换热器(E-201)、汽提塔底油/反应产物换热器(E-202)、低分油/反应产物换热器(E203)、混氢原料(I)/反应产物换热器(E-204/1、2)换热,然后依次经反应产物空冷器(EC-201/1、2)、反应产物后冷器(E-207/1、2)冷却至40℃,进入高压分离器(D-204)。
为了防止反应产物中的铵盐在低温部位结晶,通过脱氧水泵(P-207/1、2)将脱氧水注入到(EC-201/1、2)或(E-204/1、2)上游的管道中。
冷却后的反应物在D-204中进行油、气、水三相分离。
高分气(循环氢)经K-202/1、2入口分液罐(D-208)分液后,进入循环氢压缩机(K-202/1、2)升压至8.8MPa(G),然后分两路:一路作为急冷氢进入R-201,一路与来自新氢压缩机(K-201/1、2)的新氢混合,混合氢与原料油混合作为反应进料。
含硫、含氨污水自D-204底排出,至装置外统一处理。
D-204油相在液位控制下,经减压调节阀进入低压分离器(D-205),D-205闪蒸气排至燃料气管网。
低分油经低分油/分馏塔底油换热器(E-206/1、2)和E-203分别与精制重石脑油、反应产物换热至200℃后去分馏部分汽提塔(C-201)。
汽提塔底油经汽提塔底油/分馏塔底油换热器(E-205)和E-202分别与精制重石脑油、反应产物换热至245℃后去分馏部分分馏塔(C-202)。
新氢自制氢装置来,经新氢压缩机入口分液罐(D-207)分液后进入K-201/1、2并经三级升压至
8.8MPa(G),再与K-202/1、2出口的循环氢混合。
2、分馏部分
从反应部分来的低分油经换热后进入C-201。
塔底用0.8MPa过热蒸汽汽提。
塔顶油气经汽提塔顶空冷器(EC-202/1、2)和汽提塔顶后冷器(E-208)冷凝冷却至40℃,进入汽提塔顶回流罐(D-210)进行气、油、水三相分离。
闪蒸出的气体作为燃料进入燃料气管网。
含硫污水送出装置。
油相经汽提塔顶回流泵(P-203/1、2)升压后作为塔顶回流全部返回汽提塔(C-201)。
塔底油自压经E-205与精制重石脑油换热后去反应部分E-202换热器。
从反应部分来的低分油经换热后进入C-202。
塔底用重沸炉提供热源。
塔顶油气经分馏塔顶空冷器(EC-203/1、2)和分馏塔顶后冷器(E-209)冷却至40℃,进入分馏塔顶回流罐(D-211)进行气、油、水三相分离。
闪蒸出的气体通过放空罐至火炬。
含硫污水送出装置。
油相经分馏塔顶回流泵(P-204/1、2)升压后一部分作为塔顶回流,一部分作为精制轻石脑油出装置。
塔底精制重石脑油一小部分经分馏塔底产品泵(P-206/1、2)增压后经E-205和E-206/1、2分别与汽提塔底油、低分油换热至100℃左右,然后进入精制重石脑油后冷器(E-210)冷却至60℃出装置。
塔底精制重石脑油大部分经分馏塔底循环泵(P-205/1、2)增压后用分馏塔底重沸炉(F-202)加热至290℃左右返回分馏塔下部,以补充分馏所需能量。
为了抑制硫化氢对塔顶管道和冷换设备的腐蚀,在塔顶管道注入缓蚀剂。
缓蚀剂自缓蚀剂罐
(D-212)经缓蚀剂泵(P-209/1,2)抽出后分两路,一路注入C-201塔顶管道;另一路注入C-202塔顶管道。
3、催化剂预硫化部分
为了使催化剂具有良好的活性,新鲜的或再生后的催化剂在使用前都必须进行预硫化。
本设计采用湿法硫化,以直馏煤油为硫化油,二硫化碳为硫化剂。
催化剂进行预硫化操作时,系统内氢气经循环氢压缩机(K-202/1、2)按正常操作流程进行全量循环。
二硫化碳自二硫化碳桶用硫化剂泵(P-208)升压后至反应进料泵入口,经反应进料泵(P-202/1、2)后与氢气混合,经反应产物与混氢原料油换热器(E-204/1、2、E-201)换热,经反应进料加热炉(F-201)升温,然后经过催化剂床层,对催化剂进行预硫化。
自反应器底部出来的硫化油和循环氢等经E-201、E-202、E-203、E-204/1、2换热,经EC-201/1、2、E-207/1、2冷却后至高压分离器(D-204)进行气、油、水三相分离。
气体自顶部出来,经D-208入K-202/1、2实现循环氢的循环,硫化油自高分罐(D-204)下部出来经调节阀降压后进入低分罐(D-205)阀蒸分离,液相返至原料油缓冲罐(D-203)入口实现循环流化,闪蒸出来的低分气至燃料气系统,催化剂预硫化过程中产生的水间断从高分罐(D-204)底部排出。
催化剂预硫化结束后,硫化油改进原料油出装置线退出装置。
三、10000标方/小时制氢装置
1、进料系统
由装置外来的干气进入原料气缓冲罐,经过原料气压缩机压缩后进入原料气脱硫部分。
2、脱硫部分
进入脱硫部分的原料气经原料预热炉予热升温至380℃,进入加氢反应器发生反应,使有机硫转化为硫化氢后进入氧化锌脱硫反应器,硫化氢与氧化锌反应生成固体硫化锌被吸收下来。
脱除硫化氢后的气体硫含量小于0.2PPm,进入转化部分。
具体反应如下:
硫醇: RSH+H2→RH+H2s
硫醚: R1SR2+2H2→R1H+R2H+H2S
二硫醚: R1SSR2+3H2→R1H+R2H+2H2S
噻吩: C4H4S+4H2→C4H10+H2S
氧硫化碳: COS+H2→CO+H2S
二硫化碳: CS2+4H2→CH4+2H2S
ZnO(固)+H2S=ZnS(固)+H2O △Ho 298 =-76.62kJ/mol
3、转化部分
精制后的原料气按水碳比3.5与水蒸汽混合,再经转化炉对流段予热至500℃,进入转化炉辐射段。
在催化剂的作用下,发生复杂的水蒸汽转化反应,从而生产出氢气、甲烷、一氧化碳、二氧化碳和水的平衡混合物。
主要反应有:
CnHm+nH2O =nCO+(n+m/2)H2 ①
CO+3H2=CH4+H2O △Ho298
=-206kJ/mol ②CO+H2O=CO2+H2 △Ho298
=-41kJ/mol ③
以甲烷为主的气态烃,蒸汽转化过程较为简单,主要发生上述反应,最终产品气组成由反应②③平衡决定。
而轻石脑油,由于其组成较为复杂,有烷烃、环烷烃、芳烃等,因此,除上述反应外,在不同的催化床层,还发生高级烃的热裂解、催化裂解、脱氢、加氢、积炭、氧化、变换、甲烷化等反应,最终产品气组成仍由反应②③平衡决定。
烃类水蒸汽转化反应是体积增大的强吸热反应,低压、高温、高水碳比有利于上述反应的进行。
反应过程所需热量由转化炉顶部的气体燃料烧嘴提供,出转化炉820℃高温转化气经转化气蒸汽发生器换热后,温度降至360℃,进入中温变换部分。
4、变换部分
由转化部分来的约360℃的转化气进入中温变换反应器,在催化剂的作用下发生变换反应: CO+H2O=CO2+H2。