汽车制动台检测制动力方法探讨
浅析滚筒反力式制动检验台制动性能检测方法

技术改造—346—浅析滚筒反力式制动检验台制动性能检测方法马彩绒(陕西省交通运输技术服务中心,陕西西安710065)摘要:从设备、人员、车辆、检测系统等多方面反映目前滚筒反力式制动检验台制动检测的情况,并对制动力影响因素进行了分析,为保证机动车制动检验检测结果的准确性点明了关键点。
关键词:机动车滚筒制动检测影响因素机动车制动性能台式检验一般有平板式制动检验台和滚筒反力式制动检验台两种,其中滚筒反力式制动检验台应用最为广泛,本文就滚筒反力式制动检验台检测方法做一浅析。
1.滚筒反力式制动检验台基本结构及原理,滚筒反力式制动检验台是由结构完全相同的左右两套车轮制动力测试单元和一套指示、控制装置组成,每一套车轮制动力测试单元有框架、驱动装置、滚筒组、举升装置、测量装置等构成。
其结构图如图1-1。
图1-1滚筒反力式汽车制动试验台结构简图1.电动机2.减速器3.压力传感器4.滚筒装置5.第三滚筒6.转速传感器7.链传动8.测量指示装置(工位机)进行制动力检测时,被检车辆驶上制动检验台,车轮置于主、从动滚筒之间,放下举升器并压下第三滚筒,装在第三滚筒支架下的行程开关被接通。
通过延时电路启动电动机,经减速器、链传动和主、从动滚筒带动车轮低速旋转,待车轮转速稳定后驾驶员踩下制动踏板。
车轮在车轮制动器的摩擦力矩作用下开始减速旋转。
此时电动机驱动的滚筒对车轮轮胎的摩擦力克服制动器的摩擦力矩,维持车轮继续旋转。
同时在车轮轮胎对滚筒表面切线方向施加摩擦力,减速器壳体与测力杠杆一起朝滚筒转动相反方向摆动,测力杠杆一端的压力经传感器转换成与制动力大小成比例的电信号。
从测力传感器送来的电信号经放大滤波后,送往A/D 转换器转换成相应数字量,经计算机采集、存储和处理后,得到检测结果。
2.滚筒反力式制动检验台检验步骤:2.1被检车辆正直居中行驶,依次逐轴停放在轴(轮)重仪上,并按规定时间(不少于3s)停放,测出静态轴(轮)荷;2.2被检车辆正直居中行驶上制动台,将被测试轴停放在制动台滚筒上,变速器置于空挡,松开制动踏板,使制动器处于放松状态,制动数据清零;对于全时四驱和适时四驱车辆,非测试轮应处于适合轴距尺寸、附着系数符合要求的辅助自由滚筒组上,变速器置于空挡(自动变速器处于N 档);对于三轴及三轴以上货车及总质量大于3500kg 的并装双轴和三轴的挂车,采用具有举升功能的滚筒反力式制动检验台时,通过举升台体对测试轴加载,举升至副滚筒上母线离地100mm 或轴荷达到11500kg 时,测得该轴空载轴荷。
滚筒反力式汽车制动检验台日常运用探索
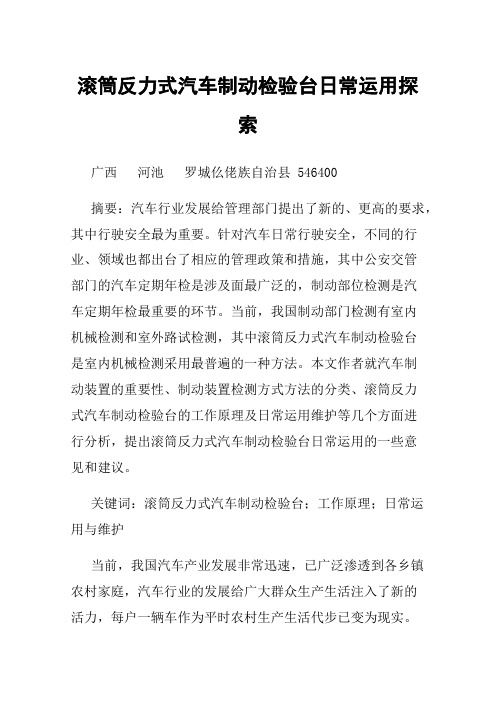
滚筒反力式汽车制动检验台日常运用探索广西河池罗城仫佬族自治县 546400摘要:汽车行业发展给管理部门提出了新的、更高的要求,其中行驶安全最为重要。
针对汽车日常行驶安全,不同的行业、领域也都出台了相应的管理政策和措施,其中公安交管部门的汽车定期年检是涉及面最广泛的,制动部位检测是汽车定期年检最重要的环节。
当前,我国制动部门检测有室内机械检测和室外路试检测,其中滚筒反力式汽车制动检验台是室内机械检测采用最普遍的一种方法。
本文作者就汽车制动装置的重要性、制动装置检测方式方法的分类、滚筒反力式汽车制动检验台的工作原理及日常运用维护等几个方面进行分析,提出滚筒反力式汽车制动检验台日常运用的一些意见和建议。
关键词:滚筒反力式汽车制动检验台;工作原理;日常运用与维护当前,我国汽车产业发展非常迅速,已广泛渗透到各乡镇农村家庭,汽车行业的发展给广大群众生产生活注入了新的活力,每户一辆车作为平时农村生产生活代步已变为现实。
汽车产业的发展给行业管理提出了新的要求,其中汽车日常行驶安全是最为重要,如何确保汽车日常行驶安全,针对不同行业、领域国家出台了很多具有针对性的管理政策及措施。
汽车定期检测是国家强制要求开展的,也是当前我国针对汽车行驶安全采取的最普遍的一种安全保障措施。
检测内容包括制动部位检测、底盘工位检测、灯光检测和人工外部检测等几个方面,其中制动部位检测最为重要。
对于制动部位检测主要有室内机械检测和室外路试检测。
滚筒反力式汽车制动检验台是室内机械检测的一种,下面作者就滚筒反力式汽车制动检验台日常运用过程中其存在的特点进行深入分析,并就如何对其进行保养和维护,提出一些拙见,以与大家共勉。
一、汽车制动装置的重要性。
汽车制动系统是汽车最为重要的部件装置之一,制动系统出现问题,行车事故随时有可能发生,经验丰富的驾驶员平时出车前首要测试的是车辆制动性能,车辆制动性能存在问题,必须立即停车检修,否则后果不堪设想。
正是由于制动系统在行车过程中固有的重要性,所以在国家强制对汽车进行定期检验过程中,把制动检测列为必检项目,且检测要求越来越严格,并针对性地出台了多种检测方式,保证检测工作到位,检测效果达到要求。
驻车制动力的检验方法分析
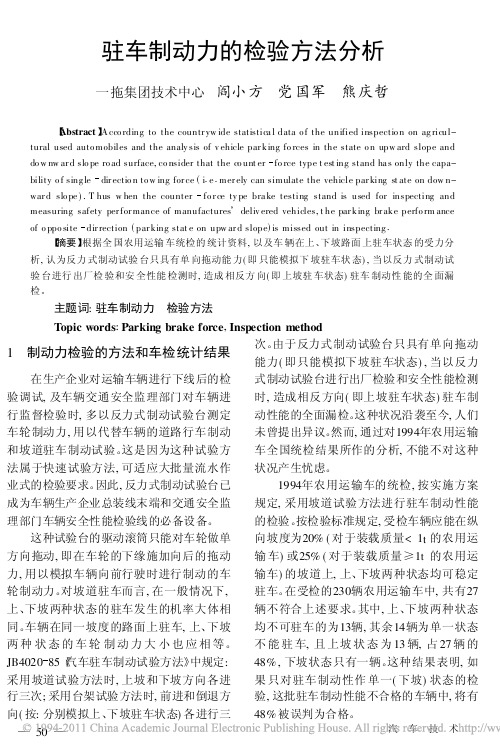
上、下坡两种状态的驻车发生的机率大体相 辆不符合上述要求。其中, 上、下坡两种状态
同。车辆在同一坡度的路面上驻车, 上、下坡 均不可驻车的为13辆, 其余14辆为单一状态 两 种 状 态 的 车 轮 制 动 力 大 小 也 应 相 等。 不 能 驻 车, 且 上坡 状 态 为 13 辆, 占 27 辆 的
某些( 不是全部) 企业, 在车辆下线检验时, 以 反力式制动试验台( 许多小企业还没有这种 设备) 只测定下坡状态的驻车制动力, 造成上 坡状态驻车制动性能漏检所致。
3 结论和建议
如前所述, 在1994年进行的农用运输车 统检中, 发现有13辆农用运输车仅上坡状态 驻车制动性能未达规定要求, 占受检230辆农 用运输车的5. 7% 。这些车辆驻车制动性能的 不合格, 和反力式制动试验台在某些农用运 输车厂的采用密切相关。汽车行业的企业规 模一般远大于农用运输车行业的生产企业, 反力式制动试验台的应用也更加普遍。因而, 就公路行驶的运输车辆大行业而言, 由于反 力式制动试验台的应用, 致使驻车制动性能 不合格产品占产品总量的比例应不小于5% ~6% 。而社会上车辆交通安全监理部门使用 的检测线, 更是装备了这种试验台, 又使这些 车可以毫无阻拦地投入营运, 驶上公路, 从而 对车辆的运行安全构成威胁。
JB4020 85《汽车驻车制动试验方法》中规定: 48% , 下坡状态只有一辆。这种结果表明, 如
采用坡道试验方法时, 上坡和下坡方向各进 果 只对驻车制动性作 单一( 下坡) 状态的检
行三次; 采用台架试验方法时, 前进和倒退方 验, 这批驻车制动性能不合格的车辆中, 将有
向( 按: 分别模拟上、下坡驻车状态) 各进行三 — 50 —
中型和许多轻型运输车辆, 普遍以盘式 或鼓式中央制动器作为驻车制动器。这种专 设的驻车制动器, 根据使用要求, 在设计原理 上应能保证在操纵力一定的情况下, 正、反两 个方向制动能力相同。即, 由驻车制动器制动 能力限定的上、下坡两种状态的驻车极限坡 度角应是相等的。但在实际上因受各种因素 的影响, 这类制动器两个方向的制动能力不 可能绝对相同。因而, 以驻车制动力或驻车极 限坡度角衡量的车辆两个方向的驻车制动性 能不可能绝对相同。而某些轻型车辆是在后 轮的人力操纵液压行车制动器上加装机械操 纵装置, 使其兼作驻车制动器使用。这种制动 器有的从行车制动的使用要求出发, 在设计 原理上就是前进( 下坡) 方向的制动能力较倒 退( 上坡) 方向为高。因此, 对车辆的驻车制动 性能只做单一方向的检验, 不能判定另一方 向的驻车制动性能是否符合要求, 特别是只 做下坡状态的检验, 更不能保证上坡状态的 驻车制动性能符合要求。鉴于这种原因, 认为 如前所述的“趋同”现象, 是由于农用运输车
汽车制动性能检测方法
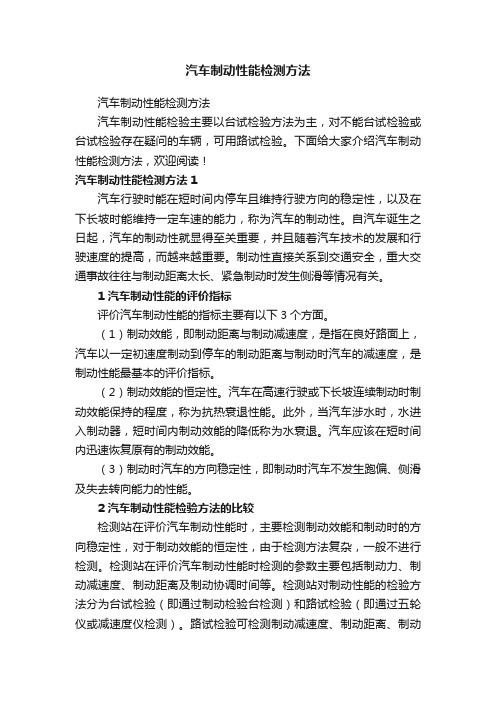
汽车制动性能检测方法汽车制动性能检测方法汽车制动性能检验主要以台试检验方法为主,对不能台试检验或台试检验存在疑问的车辆,可用路试检验。
下面给大家介绍汽车制动性能检测方法,欢迎阅读!汽车制动性能检测方法1汽车行驶时能在短时间内停车且维持行驶方向的稳定性,以及在下长坡时能维持一定车速的能力,称为汽车的制动性。
自汽车诞生之日起,汽车的制动性就显得至关重要,并且随着汽车技术的发展和行驶速度的提高,而越来越重要。
制动性直接关系到交通安全,重大交通事故往往与制动距离太长、紧急制动时发生侧滑等情况有关。
1 汽车制动性能的评价指标评价汽车制动性能的指标主要有以下3个方面。
(1)制动效能,即制动距离与制动减速度,是指在良好路面上,汽车以一定初速度制动到停车的制动距离与制动时汽车的减速度,是制动性能最基本的评价指标。
(2)制动效能的恒定性。
汽车在高速行驶或下长坡连续制动时制动效能保持的程度,称为抗热衰退性能。
此外,当汽车涉水时,水进入制动器,短时间内制动效能的降低称为水衰退。
汽车应该在短时间内迅速恢复原有的制动效能。
(3)制动时汽车的方向稳定性,即制动时汽车不发生跑偏、侧滑及失去转向能力的性能。
2 汽车制动性能检验方法的比较检测站在评价汽车制动性能时,主要检测制动效能和制动时的方向稳定性,对于制动效能的恒定性,由于检测方法复杂,一般不进行检测。
检测站在评价汽车制动性能时检测的参数主要包括制动力、制动减速度、制动距离及制动协调时间等。
检测站对制动性能的检验方法分为台试检验(即通过制动检验台检测)和路试检验(即通过五轮仪或减速度仪检测)。
路试检验可检测制动减速度、制动距离、制动协调时间和稳定性;台试检验可检测制动力、制动力平衡和车轮阻滞力。
2.1制动性能路试检验《机动车运行安全技术条件》(GB 7258-2012)第7、11、3条规定,对台试检验制动性能结果有异议的,在空载状态下按第7、10条(路试检验制动性能)规定进行路试复检;对空载状态复检结果有异议的,以满载路试复检结果为准。
汽车制动实验报告心得

汽车制动实验报告心得1. 引言汽车制动系统是汽车安全性能最重要的部分之一,也是驾驶员操作最频繁的一个系统。
汽车制动实验旨在通过对制动系统的测试,了解车辆制动性能和制动过程中的一些关键指标,从而确保车辆行驶的安全性。
在本次实验中,我们使用了制动试验台进行了一系列的测试,从中获得了许多有益的信息。
2. 实验目的本次实验的目的是测量并分析汽车制动系统的性能,主要包括制动距离、制动时间、制动力分布等指标。
通过对实验结果的分析,能够帮助我们更好地理解制动系统的工作原理和性能特点。
3. 实验过程在实验过程中,我们首先使用了制动力计,通过测量前轮制动力和后轮制动力的分布情况,得到了车辆在制动过程中的动态响应。
然后,在制动试验台上使用了制动距离测量装置,测量了车辆在不同速度下的制动距离和制动时间。
4. 实验结果通过实验测量,我们得到了一系列有关制动系统性能的数据。
其中,最重要的是制动距离和制动时间。
通过对这些数据的分析,我们可以得出一些有用的结论。
首先,制动距离与车辆速度呈正相关关系。
随着车辆速度的增加,制动距离也会增加。
这是因为制动过程需要消耗一定的时间来将车辆的动能转化为制动能量,因此车辆在高速行驶时需要更长的制动距离来停下来。
其次,制动时间与制动压力呈正相关关系。
在相同速度下,当制动压力增加时,制动时间会减小。
这是因为制动压力的增加会加速制动系统的响应速度,使得制动时间缩短。
此外,通过前后轮制动力分布的测量,我们可以得出车辆的制动力分配情况。
通过调整制动系统的参数,可以实现不同的制动力分配方式,以满足不同道路条件和驾驶员的需求。
5. 实验心得通过参与汽车制动实验,我学到了很多关于汽车制动系统的知识。
首先,我深刻认识到汽车制动系统对于行车安全的重要性。
一辆好的汽车制动系统可以在紧急情况下快速停车,避免意外发生。
其次,我了解到制动系统的性能与很多因素有关,包括车辆质量、制动盘和刹车片的磨损程度、制动液的温度等。
汽车制动性能测试方法分析

汽车制动性能测试方法分析汽车制动性能测试是保证车辆行驶安全的重要环节。
本文将分析汽车制动性能测试的方法,探讨测试时需要注意的问题,以及测试结果的解读。
1. 定义汽车制动性能测试是指通过特定的测试方法,测量车辆在一定速度下制动距离和制动时间的指标,并将测试结果与标准要求进行比较,以判断车辆制动性能是否符合国家标准和企业要求。
2. 测试方法常见的汽车制动性能测试方法包括静态制动距离测试、动态制动距离测试、车速指标测试和制动力测试等。
2.1 静态制动距离测试静态制动距离测试是在静止状态下通过行车制动器进行测试。
测试车辆驶入测试区域后,停车后车辆的前轮和后轮都必须垂直于测试道路,测试仪器通过检测车辆从制动器接触到完全停止时所需的距离,来测量车辆静态制动距离。
2.2 动态制动距离测试动态制动距离测试是在一定速度下通过踩刹车测试。
测试车辆驶入测试区域后,进行加速到一定速度后,刹车达到停车状态前所需的时间和距离并计算出动态制动距离。
2.3 车速指标测试车速指标测试是对车辆的动态性能进行测试,主要包括加速能力和最高车速等指标的测试。
测试时可使用加速测试仪器和GPS定位仪器进行测试。
2.4 制动力测试制动力测试是对车辆制动力大小进行测试,测试时可使用汽车制动力测试仪器进行测试。
3. 测试注意事项进行汽车制动性能测试时需要注意以下事项:3.1 测试前准备在进行测试前,需要保证测试仪器和测试区域符合测试标准,测试仪器需进行检修,测试区域必须达到所需的标准,并清理测试区域。
3.2 测试过程测试时需要注意测试过程的记录及数据的准确性。
测试时必须按照标准程序进行测试,并注明测试的日期、时间、测试人员名称和测试车辆等信息,同时确保测试过程不受任何干扰。
3.3 测试结果测试结果的误差会受到多个因素影响,例如测试操作、测试仪器准确度、测试环境和测试车辆等。
需要检查结果对比标准是否符合要求,并对测试数据作出评价和分析。
4. 测试结果解读汽车制动性能测试结果的解读需要参考制动距离、制动时间、制动平均加速度、制动温度和制动能力等指标,并根据标准要求进行评价和分析。
汽车制动性能滚筒试验台与路试对比分析

汽车制动性能滚筒试验台与路试对比分析一、台试制动性能检测方法分析1.滚筒式制动试验台在检测站运用较多的滚筒式制动试验台可理解为汽车静止而路面在车轮下“滚动”。
达到规定的预先检测速度后,提示驾驶员紧急踩下制动踏板。
电机驱动的滚筒驱动车轮,使得滚筒上的受检车轮受到与制动力矩相反的转矩,这时车轮转动停止,直到滚筒与车轮开始滑转时,电机停止转动,滚筒驱动力被切断,测力杠杆同时将力传给测力传感器,这时测力传感器显示力的大小即为该试验台上检测的车轮最大制动力。
滚筒反力式试验台是属于静态检测,由滚筒带动车轮转动,所以不能反映和检测出汽车动态的制动状况(例轴荷转移)下的最大制动力。
2.平板式制动试验台平板式制动试验台可以检测出侧滑、轴重、悬架效能及制动力等评价指标。
是属于动态检测,理论上比滚筒式要好。
在拉力传感器如实的检测出平板上的制动受力,可完全检测出力的变化、汽车的制动过程。
但其也有着致命的缺点,不适合对轴距变化大的汽车进行四轮同时制动检测、多轴车不能测试、在检测时操作人员不易控制制动初速度和制动踏板力、对于车速一般在10km/h以上ABS才起作用等。
其检测范围受限制,对全挂车、半挂车等车型的检测极为困难,测试结果也较不理想,并且对于超重、超长的车辆的制动性能其根本无法检测。
二、路试检测法路试检测法能更加直观、简便和真实地反映出实际制动行驶中汽车的动态制动性能,还可反映出除制动系统外的其他系统结构性能对汽车制动性的影响,比如说悬架系统结构和转向机构等对制动方向稳定性的影响。
而且路试检测法与台架式不同,其不需要大型的设备和厂房的固定环境条件。
然而,它也有不足之处。
同样,因操作员的操作方法迥异、路面行驶状况不一及交通状况不同等对路试的制动距离和制动减速度值的重复检测,测量数据一致性不好,除非在专用的试验仪器情况下,获得的检测结果重复性才相比较好。
另外,路试法只能对受检车辆整车的制动性能状况进行详细检测分析,具体各轮的制动状况和制动力的分配情况等,不易取得定量的數值,也不易诊断出故障发生的具体部位。
一种车辆制动力实时检测方法研究
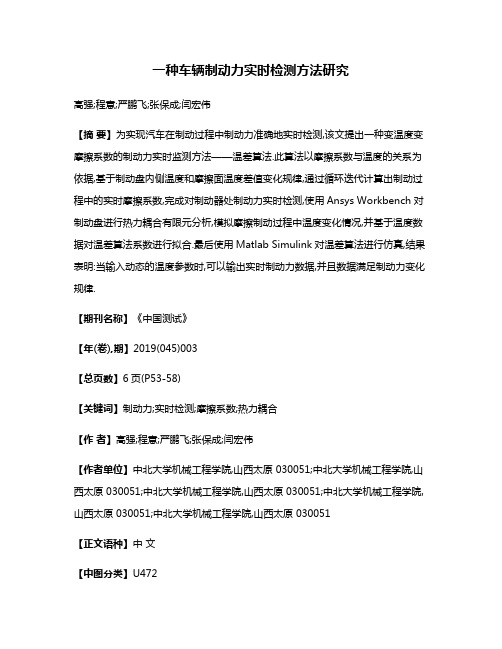
一种车辆制动力实时检测方法研究高强;程意;严鹏飞;张保成;闫宏伟【摘要】为实现汽车在制动过程中制动力准确地实时检测,该文提出一种变温度变摩擦系数的制动力实时监测方法——温差算法.此算法以摩擦系数与温度的关系为依据,基于制动盘内侧温度和摩擦面温度差值变化规律,通过循环迭代计算出制动过程中的实时摩擦系数,完成对制动器处制动力实时检测,使用Ansys Workbench对制动盘进行热力耦合有限元分析,模拟摩擦制动过程中温度变化情况,并基于温度数据对温差算法系数进行拟合.最后使用Matlab Simulink对温差算法进行仿真,结果表明:当输入动态的温度参数时,可以输出实时制动力数据,并且数据满足制动力变化规律.【期刊名称】《中国测试》【年(卷),期】2019(045)003【总页数】6页(P53-58)【关键词】制动力;实时检测;摩擦系数;热力耦合【作者】高强;程意;严鹏飞;张保成;闫宏伟【作者单位】中北大学机械工程学院,山西太原 030051;中北大学机械工程学院,山西太原 030051;中北大学机械工程学院,山西太原 030051;中北大学机械工程学院,山西太原 030051;中北大学机械工程学院,山西太原 030051【正文语种】中文【中图分类】U4720 引言汽车制动力的检测是一个汽车安全行驶的重要保证,自1963年LeJFH[1]提出滚筒式检测方法,学者在汽车制动力检测方面作了大量的研究工作。
滚筒式检测方法由于滚筒原因限制了被测车辆的轴距[2],美国科学家与上世纪90年代又提出平板式检测方法,这种方法通过测量车辆在平板上制动时给予平板的摩擦力,实现对车辆制动力的检测,这种检测方法虽然弥补了滚筒式检测方法的不足之处,但这种检测方法,对测试员的要求较高,高速度制动检测时试验重复性较差[3]。
2003年李金学等[4]提出通过测量制动时轮胎在对地面产生印记来确定分车辆的制动力,但这也无法实现对汽车的制动力的实时检测。
- 1、下载文档前请自行甄别文档内容的完整性,平台不提供额外的编辑、内容补充、找答案等附加服务。
- 2、"仅部分预览"的文档,不可在线预览部分如存在完整性等问题,可反馈申请退款(可完整预览的文档不适用该条件!)。
- 3、如文档侵犯您的权益,请联系客服反馈,我们会尽快为您处理(人工客服工作时间:9:00-18:30)。
汽车制动台检测制动力方法探讨
摘要:反力式滚筒制动试验台是汽车制动性能检测应用较为广泛的检测设备,在检测实践中发现滚筒制动试验台在检测汽车制动力时存在一些路试合格的车辆,台架检测时却不合格的问题。
关键词:汽车滚筒制动试验台制动力检测国标
根据中华人民共和国国家标准GB7258-2004,《机动车运行安全技术条件》中7.14.1.1关于台式车辆制动力检测性能要求:汽车在制动检验台上测出的制动力应符合表1的要求,对空载检测制动力有质疑时,可以用表1规定的满载检验制动力要求进行检验,检验时只允许乘坐一名驾驶员。
同时在7.14.1.2中要求制动力平衡:在制动力增长过程中同时测得的左右轮制动力差的最大值,与全过程中测得的该轴荷的左右最大制动力中大者之比,对前轴不应大于20%,对后轴(用其他轴)在制动力不小于24%,当后轴(用其他轴)制动力小于该轴轴荷的60%时,在制动力增长全过程中同时测得左右轮制动力差的最大值不该大于该轴轴荷的8%。
汽车的制动性能直接关系着汽车的行驶安全,汽车制动性能的检测,是汽车生产企业检测车辆的必检项目。
而反力式滚筒制动试验台以其测试受外界环境影响小、占地少、结构简单、操作安全性能好、检测结果重复性好等优点,同时也满足GB7258-2004制动力检测的要
求。
但是经过长期的检测实践,发现在实际检测过程中仍然存在一些问题,许多整车在制动力检测时达不标准要求,而在标准另一项要求:通过加载、路试测试制动效能又能满足要求,为什么?
首先了解反力式滚筒制动试验台工作原理:
反力式滚筒制动试验台(以下简称为汽车制动检验台)是由结构完全相同的左右两套车轮制动力测试单元和一套指示、控制装置组成。
每一套车轮制动力测试单元由框架、驱动装置、滚筒组、举升装置、测量装置等构成。
进行车轮制动力检测时,被检汽车驶上制动试验台,车轮置于主、从动滚筒之间,放下举升器(或压下第三滚筒,装在第三滚筒支架下的行程开关被接通)。
通过延时电路启动电动机,经减速器、链传动和主、从动滚筒带动车轮低速旋转,待车轮转速稳定后驾驶员踩下制动踏板。
车轮在车轮制动器的摩擦力矩作用下开始减速旋转。
此时电动机驱动的滚筒对车轮轮胎的摩擦力克服制动器的摩擦力矩,维持车轮继
续旋转。
同时在车轮轮胎对滚筒表面切线方向的摩擦力作用下,减速器壳体与测力杠杆一起朝滚筒转动相反方向摆动,测力杠杆一端的力或位移经传感器转换成与制动力大小成比例的电信号。
从测力传感器送来的电信号经放大滤波后,送往A/D转换器转换成相应数字量,经计算机采集存储在数据库中,检测结果可以通过打印机打印出来。
然后从实际检测时车轮的受力分析来看:
假设制动试验台前、后滚筒直径相等且水平安置,被测试车辆前、后轮中心处于同一水平高度,在检测过程中忽略滚动阻力,则测试车轮在滚筒上制动时的受力情况如图1所示。
图中G为被测车轮的轮荷;N1、N2分别为前后滚筒对被测车轮的法向反力;F1、F2分别为前后滚筒与车轮间的切向力,即制动力;F为车桥对车轮轴的水平推力;Mμ为车轮所受制动力矩;α为安置角;D为被检车轮直径;d为滚筒直径;L为滚筒中心距。
根据力学平衡原理,可以列出下列关系式:
(N1-N2)sinα+(F1+F2)cosα=F (1)
(N1+N2)cosα-(F1-F2)sinα=G (2)
假如被测车轮与滚筒间的附着条件得以充分利用,并且两滚筒附着系数φ相同,则F1、F2的最大值应为:
F1=N1×φ,F2=N2×φ (3)
将(3)式代人(1)、(2)式得:
N1(sinα+φcosα)-N2(sinα-φcosα)=F (4)
N1(cosα-φsinα)+N2(cosα+φsinα)=G (5)
联立上式解得:
N1={F(φsinα+cosα)+G(sinα-φcosα)}/(φ2+1)sin2α (6)
N2={F(φsinα-cosα)+G(φcosα+sinα)}/(φ2+1)sin2α (7)
当车轮制动时,制动试验台可能测得的最大制动力为:
Fmax=(N1+N2)×φ=φ×(G+φF)/(φ2+1)cosα (8)
从式(8)中可以看出制动试验台所测得附着力即制动力受水平推力F、安置角α、滚筒表面的附着系数φ等因素的影响。
设备的安置角α在制造时就已经固定了,这样滚筒表面的附着系数φ就影响制动力检测结果正确性,其原因:
制动试验台测量制动力是通过转动的滚筒来模拟汽车在路面上进行行驶制动的过程,因此要求制动试验台滚筒表面必须有较高的附着系数。
不同厂家的制动试验台滚筒表面的附着系数不尽相同,即使是同一制动试验台新旧滚筒的附着系数也不同,不同的附着系数直接影响制动试验台的检测效果;附着系数越大,制动试验台测力能力也越大,测出的制动力效果也越好。
国家标准GB7258-2004规定,附着系数
不得低于0.75,现国内制造的制动试验台大部分为钢质滚筒,表面粘有熔烧铝矾土砂粒,附着系数多为0.8~0.9之间,滚筒材质要求不高,工艺简单,经济性好,受气温和湿度的影响小,对轮胎磨损小。
另外,水平推力F与非测试轮的制动性能和非测试轮与地面的附着系数有关,非测试轮的制动性能越好、地面的附着系数越高,则水平推力F越大。
不同地面的附着系数大小不相同,因此即使非测试车轮的制动力一样,对被检车轮的检测结果影响也不同。
在整车实际检测过程中,由于新车轮胎带少量的橡胶脱模剂,使滚筒表面的铝矾土砂粒间不断粘滞着橡胶脱模剂,降低了滚筒的附着系数,导致整车制动力检测不合格。
清除橡胶脱模剂是极其繁琐耗时的工作,而且在不长时间内滚筒表面的铝矾土砂粒间又被填满,造成附着力降低。
如何用一种简单的方法来修补损失的滚筒的附着系数呢?
通过对GB7258-2004标准的研究,标准中制动性能检测方法附录C:
C2台式制动性能检测方法:
C2.1 用滚筒式制动检测台检验
滚筒式制动检验台滚筒在测量制动时,为了获得足够的附着力,允许在机动车上增加足够的附加质量或施加相当于附加质量的作用力(附加质量或作用力不计入轴荷)。
根据GB7258-2004滚筒式制动检测台检验方法,我们组织一定量N109车辆进行空载与加载不同质量附加物制动力测试:
空载测试,见表2。
可以看出整车制动率的合格率22%。
加载60kg测试,见表3。
这时合格率达到了89%。
继续加载至80kg进行测试,表4
这时合格率已达到100%,满足了GB7258-2004的制动力检测标准。
但是汽车生产企业在实际生产过程中从操作时间、成本上考虑,是不能在每一辆检测车辆上加载附着质量的。
能否用车辆加载后与空载时的质量之比,得出一个制动力修正系数N109的实际重量(含驾驶员体重65kg)1000kg加载80kg比值为1.1,也就是制动力修正系数为1.1。
我们奖滚筒式制动检测台实际检测结果乘以1.1的修正系数,见表5。
检测结果与加载试验结果相差很小,100%地满足了GB7258-2004要求,证明设立制动力修正系数方法是可行的。
由此可车辆制动力检测可以通过实验,确定制动力修正系数的方式检测整车制动力,以满足GB7258-2004要求。
同时其他车型也通过实验的方式获得制动力修正系数,从而使汽车生产企业以最低的成本,最节省的时间生产出合格的产品。
参考文献
[1]中华人民共和国国家标准GB7258-2004.机动车运行安全技术条件[S].。