16支气流纺纱工艺设计及说明
(完整word版)纺纱工艺设计与质量控制
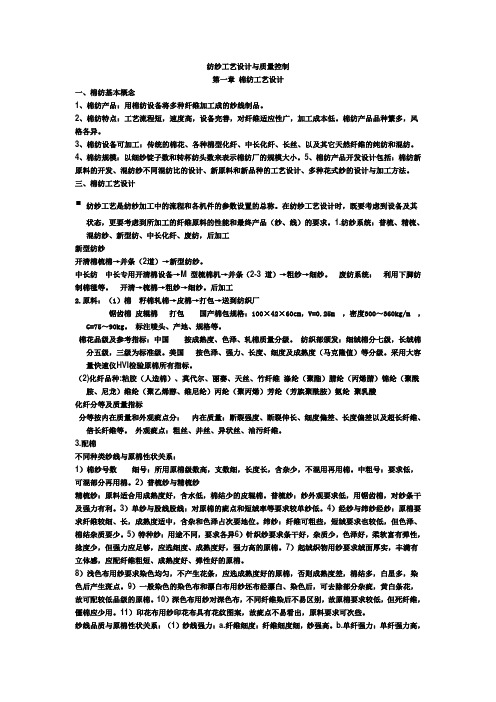
纺纱工艺设计与质量控制第一章棉纺工艺设计一、棉纺基本概念1、棉纺产品:用棉纺设备将多种纤维加工成的纱线制品。
2、棉纺特点:工艺流程短,速度高,设备完善,对纤维适应性广,加工成本低。
棉纺产品品种繁多,风格各异。
3、棉纺设备可加工:传统的棉花、各种棉型化纤、中长化纤、长丝、以及其它天然纤维的纯纺和混纺。
4、棉纺规模:以细纱锭子数和转杯纺头数来表示棉纺厂的规模大小。
5、棉纺产品开发设计包括:棉纺新原料的开发、混纺纱不同混纺比的设计、新原料和新品种的工艺设计、多种花式纱的设计与加工方法。
三、棉纺工艺设计▪纺纱工艺是纺纱加工中的流程和各机件的参数设置的总称。
在纺纱工艺设计时,既要考虑到设备及其状态,更要考虑到所加工的纤维原料的性能和最终产品(纱、线)的要求。
1.纺纱系统:普梳、精梳、混纺纱、新型纺、中长化纤、废纺,后加工新型纺纱开清棉梳棉→并条(2道)→新型纺纱。
中长纺中长专用开清棉设备→M 型梳棉机→并条(2-3 道)→粗纱→细纱。
废纺系统:利用下脚纺制棉毯等。
开清→梳棉→粗纱→细纱。
后加工2.原料:(1)棉籽棉轧棉→皮棉→打包→送到纺织厂锯齿棉皮辊棉打包国产棉包规格:100×42×60cm,V=0.25m܁,密度300~360kg/m܁,G=75~90kg。
标注唛头、产地、规格等。
棉花品级及参考指标:中国按成熟度、色泽、轧棉质量分级。
纺织部颁发:细绒棉分七级,长绒棉分五级,三级为标准级。
美国按色泽、强力、长度、细度及成熟度(马克隆值)等分级。
采用大容量快速仪HVI检验原棉所有指标。
(2)化纤品种:粘胶(人造棉)、莫代尔、丽赛、天丝、竹纤维涤纶(聚酯)腈纶(丙烯腈)锦纶(聚酰胺、尼龙)维纶(聚乙烯醇、维尼纶)丙纶(聚丙烯)芳纶(芳族聚酰胺)氨纶聚乳酸化纤分等及质量指标分等按内在质量和外观疵点分:内在质量:断裂强度、断裂伸长、细度偏差、长度偏差以及超长纤维、倍长纤维等。
外观疵点:粗丝、并丝、异状丝、油污纤维。
喷气纺纱

第二节 喷气纱结构和纱、织物 的性能
二. 喷气纱性能 (六)蓬松度 直径粗于同规格环锭纱,纱体蓬松, 手感厚实,但较粗糙,光洁稍差。
第二节 喷气纱结构和纱、织物 的性能
三. 喷气纱织物性能 (一)拉伸强力 喷经喷纬织物的拉伸强力不低于环经 环纬织物,而且喷气纱织物的纬向强力还 略大于环锭纱织物。 织物的强力不仅取决于单纱强力,还 取决于纱线间的摩擦性能。由于喷气纱的 摩擦系数大且条干均匀,因此织物的拉伸 强力较高。
第三节 喷嘴结构参数及其对成 纱质量的影响
一. 喷射角 (一)喷射角变化的影响 喷射角α减小,VS将增大,轴向吸引 力增大,但切向分量VT将减小,对纱条加 捻不利。
第三节 喷嘴结构参数及其对成 纱质量的影响
一. 喷射角 (二)喷射角的变化范围 为了既要有一定的吸引前罗拉输出纤 维的能力,又要有较大的旋转速度,第一 喷嘴的喷射角在45° ~ 55°范围内,第二喷 嘴的喷射角在80° ~ 90°范围内,以接近90° 为宜。
第一节 喷气纺纱成纱原理
四. 喷气纺纱成纱原理 (二)喷气纺纱的必要条件 1. 在前罗拉出口处要均匀地产生相当 数量的开端边缘纤维,因此,前罗拉输 出的须条要有一定的宽度。
第一节 喷气纺纱成纱原理
四. 喷气纺纱成纱原理 (二)喷气纺纱的必要条件 2. 第二喷嘴气流旋转方向必须与第一 喷嘴的方向相反,且旋转的能量和速度 要大于第一喷嘴,两者转速要有一个最 佳匹配。
第二节 喷气纱结构和纱、织物 的性能
四. 喷气纺纱产品简介 (五)薄型织物 利用喷气纺可纺低线密度涤棉混纺纱、 喷气纱摩擦系数大和吸湿性较好的特点, 可制织夏季衣料及装饰织物。
第二节 喷气纱结构和纱、织物 的性能
四. 喷气纺纱产品简介 (六)针织品 由于喷气纱包缠捻度稳定,故针织性 能好,针织物不易歪斜,且条干好。但手 感较硬,宜作运动衣和外衣,如作内衣需 进行软化处理。
气流纺挡车工操作技术标准

气流纺挡车工操作技术标准一、本工序的主要任务:1、将并条机加工后的熟条,经过开松、除杂分离成单纤维,利用纺杯的高速回转,将分梳辊分梳后的单纤维输送转移纺杯的凝聚槽内形成紧密的纤维环加捻,经卷绕机构的作用,最后卷绕成符合质量要求的筒子纱。
气流纺挡车工的主要任务:接头、倒筒、换条子、做好清洁工作、防捉疵点,把好质量关。
2、分梳、除杂、加捻、卷绕和成形的作用:(1)、分梳:将喂入的棉条经锯齿分梳辊分梳成单根纤维状态。
(2)、除杂:气流纺机都带有除杂机构,在分梳辊将棉条分梳成单根纤维状态时,同时将棉条的杂质除去。
(3)、牵伸:气流纺机的牵伸,不同于粗纱、细纱的罗拉牵伸,它是由喂入罗拉慢速喂入棉条,棉条被分梳成单纤维积聚在纺纱器内,然后由引线罗拉不断的快速引取,经纺纱杯加捻后的纤束,利用喂入及引取的(罗拉)速度差异达到牵伸的目的。
(4)、加捻:由高速回转的纺纱杯,将纱加上适当的捻度,使纱具有一定的强力,以便后道工序加工。
(5)、卷绕和成形:引纱罗拉引出的成纱,经成形机构导向,卷取成筒子,便于后道加工及运输、储藏。
二、小组、个人的生产指标:(一)产量:1、单产:即单位产量,是一千只锭子,一小时生产的棉纱重量,通常称为单产。
用公斤/千锭时表示。
2、台班产量:用公尺/台班表示。
就是一套并条机(前后二台、三台、或四台),在一轮班中所纺出的公尺数,这是反映并条机的供应能力。
3、空锭率:没有棉条喂入的纺纱锭子为空锭。
空锭率指所看机台的空锭数占所看机台总锭数的百分率,即所看机台的空锭数空锭率=——————————×100%所看机台的总锭数(二)质量:1、外形坏筒:花边、成形不良、磨边、重叠及油污筒子等。
2、质量坏筒:竹节纱、粗节纱、羽毛纱及黄白纱等。
(三)操作扣分。
(四)劳动定额:根据所纺品种而定并考虑以下实际情况:不同机型、不同锭数、不同品种、落筒合一或分开等。
(五)节约:1、及时处理断头,减少白花、回花、棉条头,并按规定巡回换棉条,头尾要少拉,少出坏筒。
16支气流纺纱工艺设计及说明
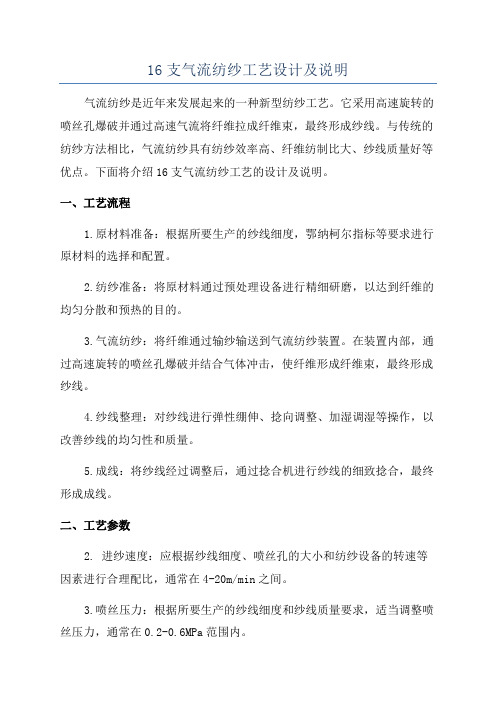
16支气流纺纱工艺设计及说明气流纺纱是近年来发展起来的一种新型纺纱工艺。
它采用高速旋转的喷丝孔爆破并通过高速气流将纤维拉成纤维束,最终形成纱线。
与传统的纺纱方法相比,气流纺纱具有纺纱效率高、纤维纺制比大、纱线质量好等优点。
下面将介绍16支气流纺纱工艺的设计及说明。
一、工艺流程1.原材料准备:根据所要生产的纱线细度,鄂纳柯尔指标等要求进行原材料的选择和配置。
2.纺纱准备:将原材料通过预处理设备进行精细研磨,以达到纤维的均匀分散和预热的目的。
3.气流纺纱:将纤维通过输纱输送到气流纺纱装置。
在装置内部,通过高速旋转的喷丝孔爆破并结合气体冲击,使纤维形成纤维束,最终形成纱线。
4.纱线整理:对纱线进行弹性绷伸、捻向调整、加湿调湿等操作,以改善纱线的均匀性和质量。
5.成线:将纱线经过调整后,通过捻合机进行纱线的细致捻合,最终形成成线。
二、工艺参数2. 进纱速度:应根据纱线细度、喷丝孔的大小和纺纱设备的转速等因素进行合理配比,通常在4-20m/min之间。
3.喷丝压力:根据所要生产的纱线细度和纱线质量要求,适当调整喷丝压力,通常在0.2-0.6MPa范围内。
4.喷丝孔的形状和数量:根据所要生产的纱线细度和纤维的特性等因素进行选择和设计。
5.纺纱温度:根据所要生产的纱线细度、纤维的熔点等因素进行调整,通常在180-280℃之间。
三、工艺优点1.纺纱效率高:气流纺纱设备具有高速旋转喷丝孔和高速气流冲击等特点,有效提高了纺纱的产出量。
2.纤维纺制比大:气流纺纱可以有效利用纤维的长度,降低纤维损耗,提高纤维的利用率。
3.纱线质量好:气流纺纱可以使纤维更好地分散,形成均匀的纤维束,提高纱线的均匀性和质量。
4.适用范围广:气流纺纱适用于各种面料纺纱,如纺织面料、工业面料、健康面料等。
总之,16支气流纺纱工艺具有纺纱效率高、纤维纺制比大和纱线质量好等优点,能够满足各种面料纺纱的需求。
在实际应用中,可以根据实际要求选择不同的设备和工艺参数,以达到最佳的纱线生产效果。
纺织工艺设计与质量控制第六章 纺纱工艺设计
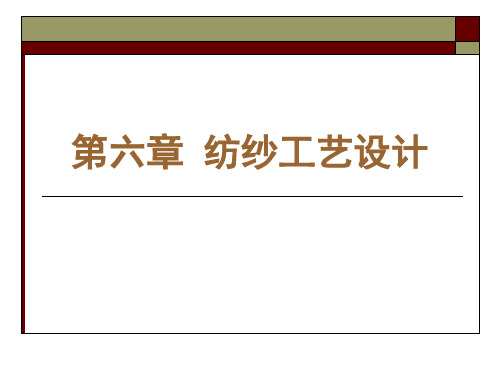
3.2 棉卷重量差异
取样
由运转挡车工逐只称重,使用棉卷专用磅秤或 普通台秤称重。
参考指标
棉卷重量控制范围,标准卷重±(1%~1.5%) 。棉卷正卷率>99%.
3.3 棉卷重量不匀率和伸长率
实验周期
每周每台至少实验一次,各品种每月至少实验3次
实验仪器及工具
棉卷均匀度仪、钢卷尺和米尺
台的开松除杂效能。 加工化纤时,此隔距应适当放大。
③尘棒间的隔距
尘棒间隔距要根据尘棒所处的位置及喂入原料的含杂情况而定 此隔距一般的规律是进口部分较大,可补入气流,也便于大杂先落;
以后可收小尘棒间隔距,近出口部分的隔距可适当放大或反装尘棒, 以补入部分气流回收纤维,节约用棉。
④打手与剥棉刀间的隔距
(4)若采用三刺辊,则第一刺辊转速为 900~992r/min,第二刺辊1200~1540r/min, 第三刺辊1700~2018r/min。这种速度递增式 的“牵引分离”可减少对纤维的损伤。
2.2 刺辊转速
梳棉机常用的锡林和刺辊速度
加工原料
锡林转速(r/min) 刺辊转速(r/min) 表面线速比(锡林/刺辊)
(3)清棉机打手至尘棒及尘棒与尘棒间的 隔距配置见下表.
3 棉卷质量指标
3.1 棉卷回潮率
试验周期:
每天各品种至少一次
取样:
多只棉卷外层均匀取样,不少于60g,取样后放在 隔湿筒内。每个品种取一份试样,每份50g。
参考指标:
棉:中细特纱7%∼8%,中粗特纱7.5%∼8.5%, 涤:0.4 %±0.1%。
制成棉卷干重 喂入原棉干重
100 %
3.6 总除杂率和总落棉率
(4)参考指标
清棉除杂和落棉参考指标
纺纱工艺设计
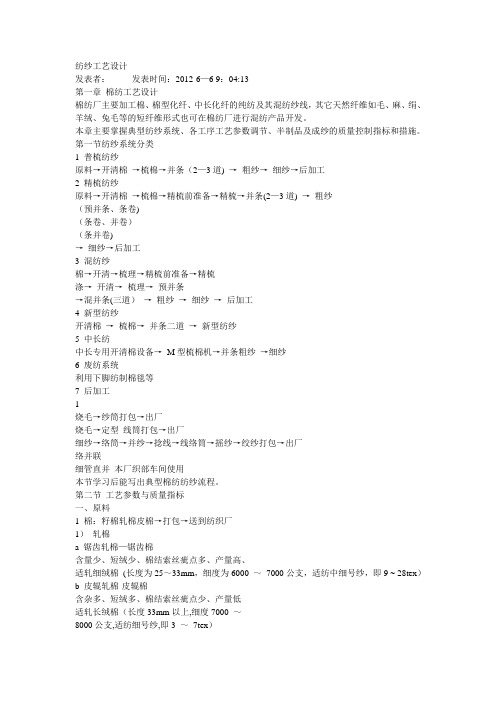
纺纱工艺设计发表者:发表时间:2012-6—6 9:04:13第一章棉纺工艺设计棉纺厂主要加工棉、棉型化纤、中长化纤的纯纺及其混纺纱线,其它天然纤维如毛、麻、绢、羊绒、兔毛等的短纤维形式也可在棉纺厂进行混纺产品开发。
本章主要掌握典型纺纱系统、各工序工艺参数调节、半制品及成纱的质量控制指标和措施。
第一节纺纱系统分类1 普梳纺纱原料→开清棉→梳棉→并条(2—3道) →粗纱→细纱→后加工2 精梳纺纱原料→开清棉→梳棉→精梳前准备→精梳→并条(2—3道) →粗纱(预并条、条卷)(条卷、并卷)(条并卷)→细纱→后加工3 混纺纱棉→开清→梳理→精梳前准备→精梳涤→开清→梳理→预并条→混并条(三道)→粗纱→细纱→后加工4 新型纺纱开清棉→梳棉→并条二道→新型纺纱5 中长纺中长专用开清棉设备→M型梳棉机→并条粗纱→细纱6 废纺系统利用下脚纺制棉毯等7 后加工1烧毛→纱筒打包→出厂烧毛→定型线筒打包→出厂细纱→络筒→并纱→捻线→线络筒→摇纱→绞纱打包→出厂络并联细管直并本厂织部车间使用本节学习后能写出典型棉纺纺纱流程。
第二节工艺参数与质量指标一、原料1 棉:籽棉轧棉皮棉→打包→送到纺织厂1)轧棉a 锯齿轧棉—锯齿棉含量少、短绒少、棉结索丝疵点多、产量高、适轧细绒棉(长度为25~33mm,细度为6000 ~7000公支,适纺中细号纱,即9 ~ 28tex)b 皮辊轧棉-皮辊棉含杂多、短绒多、棉结索丝疵点少、产量低适轧长绒棉(长度33mm以上,细度7000 ~8000公支,适纺细号纱,即3 ~7tex)2)打包规格:例国内包100*42*60cm 体积v=0.25m³密度300 ~ 360kg/m³G=75 ~90kg2、化纤1)品种粘胶莫代尔丽赛天丝2涤纶腈纶锦纶维纶丙纶)芳纶聚乳酸等2)型式长度(mm)细度(旦)棉型33—38 1。
2—1.5中长型51—76 2-3毛型76-102 3-5生产经验公式:L/D=1 L-英寸,D-旦3)分等及质量指标分等按内在质量和外观疵点分:内在质量:断裂强度、断裂伸长、细度偏差、长度偏差以及超长纤维、倍长纤维等. 外观疵点:粗丝、并丝、异状丝、油污纤维二、配棉简介1、不同种类纱线与原棉性状关系1)棉纱号数细号与中粗号的差别。
精纺纱线设计工艺
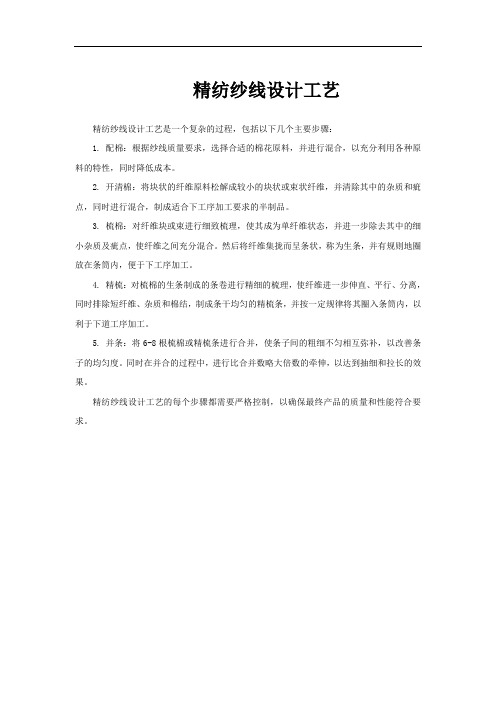
精纺纱线设计工艺
精纺纱线设计工艺是一个复杂的过程,包括以下几个主要步骤:
1. 配棉:根据纱线质量要求,选择合适的棉花原料,并进行混合,以充分利用各种原料的特性,同时降低成本。
2. 开清棉:将块状的纤维原料松解成较小的块状或束状纤维,并清除其中的杂质和疵点,同时进行混合,制成适合下工序加工要求的半制品。
3. 梳棉:对纤维块或束进行细致梳理,使其成为单纤维状态,并进一步除去其中的细小杂质及疵点,使纤维之间充分混合。
然后将纤维集拢而呈条状,称为生条,并有规则地圈放在条筒内,便于下工序加工。
4. 精梳:对梳棉的生条制成的条卷进行精细的梳理,使纤维进一步伸直、平行、分离,同时排除短纤维、杂质和棉结,制成条干均匀的精梳条,并按一定规律将其圈入条筒内,以利于下道工序加工。
5. 并条:将6-8根梳棉或精梳条进行合并,使条子间的粗细不匀相互弥补,以改善条子的均匀度。
同时在并合的过程中,进行比合并数略大倍数的牵伸,以达到抽细和拉长的效果。
精纺纱线设计工艺的每个步骤都需要严格控制,以确保最终产品的质量和性能符合要求。
纺纱(细纱)工艺单

细纱工艺表一、细纱工艺设计的相关知识 1.细纱定量【参照GB/T398—2008】———棉纱 100m 纱线的标准干燥质量:85.1010%)5.81(t t TT G =⨯+=细纱2。
牵伸工艺设计(1) 总牵伸倍数表1-1 细纱机总牵伸倍数参考范围注:纺精梳纱,牵伸倍数可偏上限选用,固定钳口式牵伸的牵伸倍数偏下限选用表1—2 纺纱条件对总牵伸倍数的影响(2) 后牵伸区工艺表1-3 后牵伸区工艺参数3。
捻系数表1—4 影响捻系数的因素表1-5 常用细纱品种捻系数参考范围%100-(%)⨯=前罗拉输出须条长度加捻成纱长度前罗拉须条输出长度捻缩率表1—6 捻缩率与捻系数的关系比例4。
锭速表1-7 不同纺纱特数的参考范围5.卷绕圈距△△是指卷绕层的圈距,一般△为细纱直径的4倍;δtT d 03568.0=当纱条单位体积质量为0。
8g/cm 3时,纱线直径为:t T d 04.0≈△ =t T 16.0 6。
钢领板级升距)2/sin(1202γρtT m =式中:ρ—--管纱卷绕密度,在一般卷绕张力条件下为0。
55g/cm 3 2/γ—-—成形半锥角有关卷绕的其他参数如图所示,参考值见下表: 表1—8 细纱机卷绕部分其他参数7。
纲领与钢丝圈(1)平面纲领与钢丝圈型号的选配表1-9(2)锥面纲领与钢丝圈型号的选配表1-10(3)钢丝圈号数的选择表1-11 纯棉纱钢丝圈号数选用范围(4)钢丝圈轻重的掌握表1-128.罗拉中心距(1)前区罗拉中心距表1-13 前牵伸区罗拉中心距与浮游区长度(2)后区罗拉中心距表1-14后牵伸区罗拉中心距的参考范围9。
胶圈钳口隔距表1—15 胶圈钳口隔距参考范围注:在条件许可下,采用较小的上下销钳口隔距,有利于改善成纱质量. 表1-16纺纱条件对胶圈钳口隔距的影响10。
罗拉加压表1-17 罗拉加压参考范围11。
前区集合器表1-18产品:cJ9。
8T 二、任务实施1. 计算细纱定量及牵伸倍数 (1) 计算细纱定量根据所纺细纱的线密度9.8tex ,公定回潮率为8.5%,实际回潮率为6.3%(在实际生产中,细纱的回潮率控制在6。