纺纱工艺及织造工艺表
棉、毛、丝、麻纺纱工艺比较
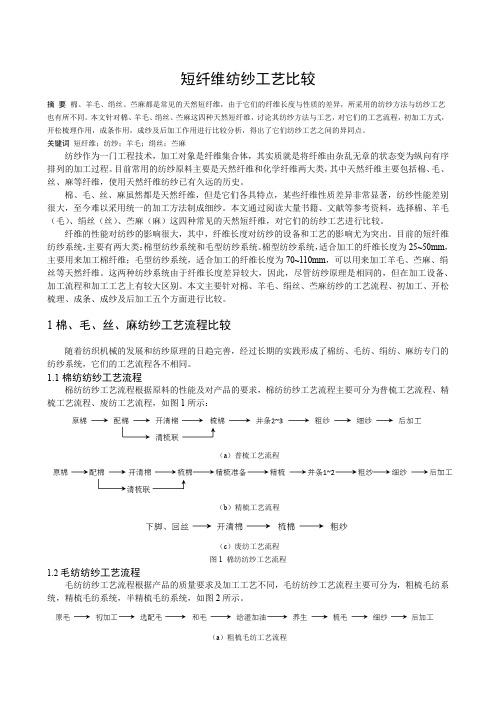
短纤维纺纱工艺比较摘要棉、羊毛、绢丝、苎麻都是常见的天然短纤维,由于它们的纤维长度与性质的差异,所采用的纺纱方法与纺纱工艺也有所不同。
本文针对棉、羊毛、绢丝、苎麻这四种天然短纤维,讨论其纺纱方法与工艺,对它们的工艺流程,初加工方式,开松梳理作用,成条作用,成纱及后加工作用进行比较分析,得出了它们纺纱工艺之间的异同点。
关键词短纤维;纺纱;羊毛;绢丝;苎麻纺纱作为一门工程技术,加工对象是纤维集合体,其实质就是将纤维由杂乱无章的状态变为纵向有序排列的加工过程。
目前常用的纺纱原料主要是天然纤维和化学纤维两大类,其中天然纤维主要包括棉、毛、丝、麻等纤维,使用天然纤维纺纱已有久远的历史。
棉、毛、丝、麻虽然都是天然纤维,但是它们各具特点,某些纤维性质差异非常显著,纺纱性能差别很大,至今难以采用统一的加工方法制成细纱。
本文通过阅读大量书籍、文献等参考资料,选择棉、羊毛(毛)、绢丝(丝)、苎麻(麻)这四种常见的天然短纤维,对它们的纺纱工艺进行比较。
纤维的性能对纺纱的影响很大,其中,纤维长度对纺纱的设备和工艺的影响尤为突出。
目前的短纤维纺纱系统,主要有两大类:棉型纺纱系统和毛型纺纱系统。
棉型纺纱系统,适合加工的纤维长度为25~50mm,主要用来加工棉纤维;毛型纺纱系统,适合加工的纤维长度为70~110mm,可以用来加工羊毛、苎麻、绢丝等天然纤维。
这两种纺纱系统由于纤维长度差异较大,因此,尽管纺纱原理是相同的,但在加工设备、加工流程和加工工艺上有较大区别。
本文主要针对棉、羊毛、绢丝、苎麻纺纱的工艺流程、初加工、开松梳理、成条、成纱及后加工五个方面进行比较。
1棉、毛、丝、麻纺纱工艺流程比较随着纺织机械的发展和纺纱原理的日趋完善,经过长期的实践形成了棉纺、毛纺、绢纺、麻纺专门的纺纱系统,它们的工艺流程各不相同。
1.1棉纺纺纱工艺流程棉纺纺纱工艺流程根据原料的性能及对产品的要求,棉纺纺纱工艺流程主要可分为普梳工艺流程、精梳工艺流程、废纺工艺流程,如图1所示:(a)普梳工艺流程(b)精梳工艺流程(c)废纺工艺流程图1 棉纺纺纱工艺流程1.2毛纺纺纱工艺流程毛纺纺纱工艺流程根据产品的质量要求及加工工艺不同,毛纺纺纱工艺流程主要可分为,粗梳毛纺系统,精梳毛纺系统,半精梳毛纺系统,如图2所示。
纺纱(细纱)实用工艺单

细纱工艺表一、细纱工艺设计的相关知识 1.细纱定量【参照GB/T398-2008】---棉纱 100m 纱线的标准干燥质量:85.1010%)5.81(t t TT G =⨯+=细纱2.牵伸工艺设计(1) 总牵伸倍数表1-1 细纱机总牵伸倍数参考围表1-2 纺纱条件对总牵伸倍数的影响(2) 后牵伸区工艺表1-3 后牵伸区工艺参数3.捻系数表1-4 影响捻系数的因素表1-5 常用细纱品种捻系数参考围%100-(%)⨯=前罗拉输出须条长度加捻成纱长度前罗拉须条输出长度捻缩率表1-6 捻缩率与捻系数的关系比例4.锭速表1-7 不同纺纱特数的参考围5.卷绕圈距△△是指卷绕层的圈距,一般△为细纱直径的4倍;δtT d 03568.0=当纱条单位体积质量为0.8g/cm 3时,纱线直径为:t T d 04.0≈△ =t T 16.0 6.钢领板级升距)2/sin(1202γρtT m =式中:ρ---管纱卷绕密度,在一般卷绕力条件下为0.55g/cm 3 2/γ---成形半锥角有关卷绕的其他参数如图所示,参考值见下表: 表1-8 细纱机卷绕部分其他参数7.纲领与钢丝圈(1) 平面纲领与钢丝圈型号的选配表1-9(2) 锥面纲领与钢丝圈型号的选配表1-10(3) 钢丝圈号数的选择表1-11 纯棉纱钢丝圈号数选用围(4) 钢丝圈轻重的掌握表1-128.罗拉中心距(1)前区罗拉中心距表1-13 前牵伸区罗拉中心距与浮游区长度(2)后区罗拉中心距表1-14后牵伸区罗拉中心距的参考围9.胶圈钳口隔距表1-15 胶圈钳口隔距参考围注:在条件许可下,采用较小的上下销钳口隔距,有利于改善成纱质量。
表1-16纺纱条件对胶圈钳口隔距的影响10.罗拉加压表1-17 罗拉加压参考围11.前区集合器表1-18产品:cJ9.8T 二、任务实施1. 计算细纱定量及牵伸倍数 (1) 计算细纱定量根据所纺细纱的线密度9.8tex ,公定回潮率为8.5%,实际回潮率为6.3%(在实际生产中,细纱的回潮率控制在6.0%~6.5%)细纱定量为:)100/(9032.010%)5.81(8.910%)5.81(m g T G t =⨯+=⨯+=细纱)100/96.0%3.619032.0%3.61m g G G ()()(细纱细纱湿=+⨯=+⨯=(2) 确定牵伸倍数设FA506型细纱机的牵伸配合率为1.02(在实际生产中,工厂根据机械牵伸倍数与实际牵伸倍数计算获得,是个统计值,多数情况为1.02-1.06)。
纺纱厂工艺流程

纺纱厂工艺流程纺纱是将纤维材料经过一系列的加工和处理过程,将其制成纱线的过程。
纱线是制作纺织品的基础材料之一。
下面是一个纺纱厂的典型工艺流程。
1. 原料准备:纺纱工艺的第一步是准备纤维原料。
不同种类的纤维原料包括棉花、亚麻、丝、羊毛等,根据不同的纤维特性和纺纱产品的要求,选择相应的原料。
原料需要经过清洁和分级处理,去除杂质和不符合要求的纤维。
2. 开松:开松是将原料纤维松散开来,提高纤维的柔软度和可纺性。
在开松机上,原料纤维被交织在一起,并且被撕开成小束。
这一步还可以去除原料中的短纤维。
3. 梳理:梳理是将纤维顺序排列,去除短纤维和杂质。
通过梳理机,纤维被精心地梳理,使其成为连续的纤维束。
梳理过程中,不符合要求的纤维被剔除,并且纤维的长度得到进一步整理。
4. 加强:加强是为了提高纤维的连续性和均匀性。
在加强机上,纤维被喷水和喷油,使其更加柔软和顺滑。
这一步还可以去除剩余的短纤维和杂质。
5. 缠绕:缠绕是将纤维转化为纱线的关键步骤。
在缠绕机上,经过牵拉和扭转,纤维被撕开,在撕开的同时,形成一个连续的纱线。
纱线可以分为单纱和复纱两种,根据需要选择不同的缠绕方式。
6. 纺纱:纺纱是将纱线拉伸成细长的线。
纺纱机是一个自动化的机械设备,在纺纱机上,纱线经过多道工序,包括湿法拉伸、干法拉伸、粗纺、细纺等。
这些工序会加强纱线的强度和稳定性,使其达到特定的品质要求。
7. 整理:整理是为了进一步提高纱线的品质和稳定性。
在整理机上,纱线经过拉伸、整平、整粒等工序,得到更加均匀和顺滑的纱线。
整理过程还可以去除纱线中的瑕疵或杂质。
8. 包装:最后一步是将纱线包装成纺织厂需要的形式。
纺纱厂根据客户要求和产品类型,选择合适的包装方式。
通常纱线被包装成小卷或大卷,以便于运输和使用。
纺纱厂工艺流程的每个环节都需要严格控制质量和操作规范,以确保纱线的品质符合要求。
纺纱工艺的每一个步骤都需要经过合理的管理和调整,以提高生产效率和纱线的市场竞争力。
羊毛纺纱工艺流程

羊毛纺纱工艺流程
羊毛纺纱是将从绵羊身上剪下的羊毛经一系列的处理工序,变成纱线的过程。
羊毛纺纱工艺流程一般包括清洗、精梳、粗纺、细纺、捻线等步骤。
首先是清洗。
刚刚剪下的羊毛中含有着许多杂质,比如尘土、沙子等。
在清洗工艺中,首先要将羊毛在清水中浸泡,然后用专门的设备将羊毛进行洗涤。
这样就能将杂质清除干净。
接着是精梳。
精梳是将羊毛纤维进行梳理,使其分叉、结块的部分剔除。
这是一个很重要的工艺环节,通过精梳,可以降低羊毛纤维的条状结构,并提高纤维的柔软度和抗拉强度。
然后是粗纺。
粗纺是将羊毛纤维进行初步的拉伸和粗纺纺制,使其成为粗纺纱。
粗纺纱的特点是纤维粗糙,强度较低,但适合用于制作粗线、粗布等产品。
接下来是细纺。
细纺是将粗纺纱进行针对性的纺制,使其成为细纺纱。
细纺纱的特点是纤维长度较短,纺线密度较高,优质的细纺纱具有柔软度好、强度高等特点,适合制作高档面料。
最后是捻线。
捻线是将细纺纱进行纺制,使其成为捻线产品。
捻线的特点是纤维互相缠结、纺线均匀,捻线后的产品强度更高、耐磨性更好。
捻线的捻度可以根据需要进行调整,不同捻度的线材适用于不同的用途,如织物、编织品等。
以上就是羊毛纺纱的工艺流程。
在实际生产过程中,每个步骤
都需要严格控制,以确保制作出优质的羊毛纺织品。
同时,还需要合理调节工艺参数,如温度、时间等,以及精确控制设备的运行,保证工艺流程的稳定性和可控性。
这样才能制作出优质的羊毛纺织品,满足市场的需求。
棉纺工艺设计表

4 13 若太大,应调整 12 10 一般取6.8
57 (1 58 ) 100
108.5× <57> 参考《棉纺手册》及相关资料
制单人:某某某
班级:纺织071
审核人:易洪雷
第3页,总计11页 设计日期:2012-11-8
服装与艺术设计学院《纺纱学》课程设计用表
60
m/s
mm m/10m % g/10m 号(tex) 倍 齿 齿 倍 齿 倍 % 倍 mm
<70>/<71> 查说明书找与<72>的接近值 查说明书中的有关表格
捻/10cm 捻/10cm 齿
制单人:某某某
班级:纺织071
审核人:易洪雷
第2页,总计11页 设计日期:2012-11-8
服装与艺术设计学院《纺纱学》课程设计用表
<75> <76> <77> <78> <79> 末 道 粗 纱 A 4 5 6 C <80> <81> <82> <83> <84> <85> <86> <87> <88> <89> <90> <91> <92> <93> <94> <95> <96> <97> <98> <99> <100> <101> <102> <103> <104> <105> <106> <107> <57> <58> <59> <60> <61> 捻度阶段变换牙(上铁炮牙) 捻系数 皮圈架长度 纤维品质长度 前罗拉直径 中罗拉直径 后罗拉直径 前罗拉隔距 后罗拉隔距 前皮辊位置 中皮辊位置 皮圈钳口隔距 前集合器开口 前罗拉加压 中罗拉速度 后罗拉加压 锭速 电机轮节经 主轴轮节经 前罗拉转速 粗纱理论产量 计算轴向卷绕密度 轴向卷绕密度 升降变换牙 升降阶段变换牙 升降阶段变换牙 卷绕变换牙(下铁炮牙) 计算径向卷绕密度 径向卷绕密度 成形阶段变换牙 成形变换牙(张力牙) 锥轮皮带每次移动量 每层粗纱平均厚度 干定量 设计回潮率 湿定量 粗纱号数 总机械牵伸 Z4 Z5 Z11 Z3 Dm Do Z2 查说明书中的有关表格 <71>× <73> 34mm棉纺 有配棉提供此数据 28mm 25mm 28mm <77〉-11(不得小于22.5mm) <78>-9(不得小于23.5mm) 前冲2~6mm 一般后移2mm 查说明书中的有关表格 查说明书并结合实际 18-22-26Kg(可调) 14Kg(固定) 14Kg(固定) 查说明书并结合实际 查说明书中的有关表格 查说明书中的有关表格 mm mm mm mm mm mm mm mm mm mm mm Kg/双锭 Kg/双锭 Kg/双锭 r/min mm mm r/min Kg/台时 圈/10cm 圈/10cm 齿 齿 齿 齿 层/10cm 层/10cm 齿 齿 mm mm g/10m % g/10m 号(tex) 倍 齿
纺纱工艺(1)
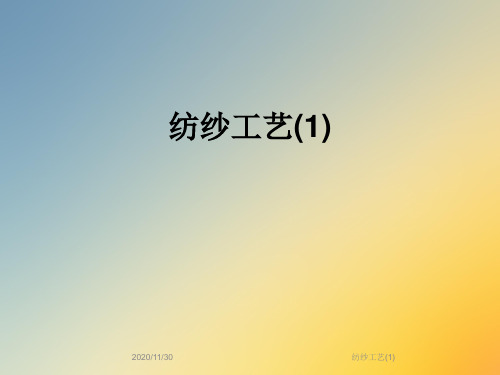
纺纱工艺(1)
梳理前准备
2、自由打击 自由打击:原料在无握持状态下受到高速打击机 件(如刀片、角钉等)的打击作用而实现纤维块 松解。
纺纱工艺(1)
梳理前准备
(二)握持开松 握持开松:原料在被握持状态下,受到
开松机件的作用。
纺纱工艺(1)
梳理前准备
1、握持打击 采用高速回转的刀片打手对握持状态下的 原料进行打击,使原料获得冲量而被开松, 称为握持打击。
纺纱工艺(1)
粗纱
4、捻度矢量 Z捻(右捻,成纱 为顺手纱) S捻(左捻,成纱 为反手纱)。
纺纱工艺(1)
粗纱
粗纱加捻的目的
1、加捻使粗纱强力增加 2、加捻粗纱绕成的管纱,层次清楚,不互 相粘连,搬运和贮存也不易损坏。 3、利于细纱机牵伸过程中纤维运动的控制, 对改善成纱质量有利。
纺纱工艺(1)
喂入负荷 盖板负荷与盖板花负荷 锡林负荷 出机负荷 返回负荷
纺纱工艺(1)
梳理
纺纱工艺(1)
纺纱基本原理
细纱
纺纱工艺(1)
精梳
➢精梳就是指当纤维须从一端被握持时, 另一端受到梳理。 精梳的目的和任务如下: ➢排除条子中的短纤维 ➢排除条子中的杂质和疵点 ➢使条子中纤维伸直,平行和分离 ➢均匀,混和及成条
纺纱工艺(1)
纺纱工艺
纤维从大块而紊乱的初始状态→纤维集合体 →纱 线,需经多道工序、多台机器。
主线 : 开松、梳理、 牵伸、加捻(四大原理) 副线:除杂、混和、并合、精梳等 插入线 :卷绕
纺纱工艺(1)
纺纱基本原理
细纱
纺纱工艺(1)
原料的初加工
轧棉——把籽棉上的纤维和棉籽分离开来 要求 1.保护纤维原有品质; 2.清除纤维中的杂质; 3.按照不同品种、等级分别打包、编批。
纺纱工艺表A4

棉卷罗拉
给棉罗拉与打手隔距mm
打手与尘棒隔距mm(进口×出口)
尘棒与尘棒隔距mm
豪猪
综合
豪猪
综合
豪猪
综合
打手皮带轮D1
风扇皮带轮D2
电机皮带轮D3
铁炮牙Z1/Z2
牵伸对牙Z3/Z4
棉卷罗拉齿轮Z5
压卷罗拉齿轮Z6
开清棉流程:
梳棉工艺
机型
生条干定量g/5m
总牵伸倍数
棉网张力牵伸倍数
锡林与刺辊速比
总牵伸倍数
牵伸倍数分配
机械
实际
e1×e2×e3×e4×e5×e6×e7×e8
锡林定位分度
转速r/min
落棉率%
给棉方式
给棉长度mm
隔距mm
锡林
前罗拉
落棉隔距
顶梳-分离罗拉
主区罗拉握持距
牵伸变换成对齿轮A/B
牵伸变换齿轮C
牵伸变换齿轮D
子母电机皮带盘直径G
输入轴皮带盘直径H
给棉齿轮齿数Z1
给棉棘轮齿数Z2
机型
粗纱干定量g/10m
牵伸倍数
后区牵伸倍数
计算捻度捻/10cm
捻
系数
罗拉中心距mm
罗拉加压N
机械
实际
1~2
3~4
1×2×3
罗拉直径mm
轴向卷绕密度圈/10cm
径向卷绕密度层/cm
转速r/min
锭翼绕纱(圈)
集合器口径(mm)
钳口隔距(mm)
前罗拉
锭子
锭端
压掌
马达盘mm
车头盘直径mm
捻度对牙Z1/Z2
转速r/min
机械
实际
刺辊
棉纺纱的主要工艺流程

介绍:棉纺是将原棉纤维转化为可用纱线或线的过程。
它是纺织业不可或缺的一部分,因为它将棉花植物的天然纤维转化为可用于制造各种产品的材料,包括服装、毛巾、床单等。
棉纺过程涉及多个步骤,每个步骤都对最终产品的整体质量和一致性起着至关重要的作用。
第1 步:清洁和梳理在将棉纤维纺成纱线之前,必须先将它们清洗干净并为加工做好准备。
这涉及从原棉中去除杂质,例如种子、树叶和其他碎屑。
这可以手动完成或使用专用机器完成。
一旦棉花被清洁,它就会经过一个称为梳理的过程,该过程将纤维分离并拉直。
在此步骤中,棉花被送入梳理机,梳理机使用一系列滚筒和刷子来理清和对齐纤维。
这有助于创造更均匀一致的纱线,因为它可以去除任何残留的杂质并确保纤维都朝着同一方向前进。
第2 步:梳理纤维经过梳理后,可能会经过称为精梳的第二道工序。
这一步是可选的,但它通常用于生产质地非常光滑和一致的高质量纱线。
精梳包括将纤维穿过一系列细齿梳,进一步拉直和对齐纤维。
这有助于去除任何残留的杂质和短纤维,从而产生更清洁、更结实、更有光泽的纱线。
第3 步:旋转棉纺工艺的下一步是纱线的实际纺纱。
这通常是使用纺纱机完成的,纺纱机由一系列滚筒和主轴组成。
当纤维被送入机器时,滚筒将它们捻在一起,形成一条连续的纱线。
有几种不同类型的纺纱机,每一种都适用于特定类型的纱线。
例如,环锭纺纱机通常用于生产精细、优质的纱线,而气流纺纱机效率更高,更适合生产大量纱线。
第4 步:缠绕纱线纺出后,必须将其卷绕到线轴或筒管上。
这通常是使用绕线机完成的,它将纱线缠绕在圆柱形芯上。
然后检查纱线是否存在瑕疵,并在准备好进入流程的下一步之前进行任何必要的调整。
第5 步:绞合和扭曲棉纺工艺的最后一步是绞纱和加捻。
绞纱涉及将纱线缠绕成绞纱,绞纱是通过一系列结固定在一起的长纱线环。
加捻涉及向纱线添加额外的捻度,这有助于增强纱线并赋予其更均匀的外观。
结论:棉纺是一个复杂的多步骤过程,包括清洁、梳理、精梳、纺纱、卷绕、绞纱和加捻。
- 1、下载文档前请自行甄别文档内容的完整性,平台不提供额外的编辑、内容补充、找答案等附加服务。
- 2、"仅部分预览"的文档,不可在线预览部分如存在完整性等问题,可反馈申请退款(可完整预览的文档不适用该条件!)。
- 3、如文档侵犯您的权益,请联系客服反馈,我们会尽快为您处理(人工客服工作时间:9:00-18:30)。
3749
4
1008
4032
细纱(纬纱)
32
1
23.13
302
53.39
15000
364
25
0.05394
96
0.05178
151.26
100
1828.5
3
1885
2
1008
2016
14.8tex普梳纱的纺纱工艺设计及机器配备表
工序
线密度
(tex)
合
并
数
牵
伸
倍
数
捻
系
数
捻度
锭速
r/min
罗拉
道夫
速度
r/min
16500
205
25
0.00949
96
0.00911
138.73
100
7461.24
3
7692
8
1008
8064
络筒(经)
10
900
82
0.54
75
0.405
156.18
99.9
385.64
4
402
7.0
900
82
0.54
75
0.405
138.59
99.9
342.2
4
356
6.5
纺纱工艺及织造工艺表
附录A
J13tex(T65/C35)涤棉精梳纱的纺纱工艺设计及机器配备表
工序
线密度
(tex)
合
并
数
牵
伸
倍
数
捻
系
数
捻度
锭速
r/min
罗拉
道夫
速度
r/min
罗拉
道夫
直径
mm
理论
产量
Kg/h
时间
效率
(%)
实际
产量
Kg/h
总生
产量
Kg/h
消
耗
率
(%)
计算
台眼
锭数
停
台
率
(%)
需要
台眼
锭数
配台数
56
364
股线(经)
10×2
2
447
99.95
10000
71
45
0.01321
97
0.01281
155.87
99.7
12168
2.5
12480
30
416
12480
股线(纬)
10×2
2
390
87.21
9000
73
45
0.01376
96
0.01321
138.31
99.7
10470.4
2.5
10739
26
3
2
6
条并卷
55000
24
1.61
60
165
80
132
357.03
121
2.7
3
2.78
3
3
精梳
4422.44
8
99.49
210
26.39
90
23.75
303.92
103
12.8
5
13.5
14
14
后并
3600
6
7.37
200
45
64.8
85
55.08
301.86
102.3
5.48
4
5.7
3
2
6
粗纱
420
102.4
7.82
4
8.1
5
2
10
粗纱
420
1
8.57
64
3.12
700
225
28
0.67
82
0.55
428.51
101.9
779.1
4
812
7
120
840
细纱(经)
13
1
32.31
340
94.3
16800
232
25
0.00911
97
0.00884
278.97
99.9
37782.5
3
38951
39
1008
416
10816
10tex×2纯棉精梳双股线的纺纱工艺设计及机器配备表
32tex普梳纱的纺纱工艺设计及机器配备表
工序
线密度
(tex)
合
并
数
牵
伸
倍
数
捻
系
数
捻度
锭速
r/min
罗拉
道夫
速度
r/min
罗拉
道夫
直径
mm
理论
产量
Kg/h
时间
效率
(%)
实际
产量
Kg/h
总生
产量
Kg/h
消
耗
率
(%)
计算
台眼
锭数
停
台
率
39312
细纱(纬)
13
1
32.31
320
88.75
16500
242
25
0.00949
96
0.00911
141.55
99.9
17943.1
3
18498
19
1008
19152
工序
线密度
(tex)
合
并
数
牵
伸
倍
数
捻
系
数
捻度
锭速
r/min
罗拉
道夫
速度
r/min
罗拉
道夫
直径
mm
理论
产量
Kg/h
时间
效率
(%)
实际
45.5
1.45
3
1.5
2
2
精梳
4422.44
8
99.49
210
26.39
90
23.75
160.64
38.2
6.76
5
7.1
8
8
涤清棉
290.57
69.1
涤梳棉
4200
1
27
706
38.27
92
35.21
277.54
66.0
7.88
5
8.3
9
9
涤预并条
3800
8
8.84
200
45
72.96
85
62.106
罗拉
道夫
直径
mm
理论
产量
Kg/h
时间
效率
(%)
实际
产量
Kg/h
总生
产量
Kg/h
消
耗
率
(%)
计算
台眼
锭数
停
台
率
(%)
需要
台眼
锭数
配台数
总
台
数
规
格
台
眼
锭
数
清棉
116.67
111
梳棉
4400
1
28
706
38.19
92
35.13
130.94
104
3.11
5
3.27
4
4
头道并条
4000
8
8.8
200
45
72
85
1
8.57
64
3.12
700
225
28
0.67
82
0.55
299.5
101.5
544.5
4
567
5
120
600
细纱(经)
10
1
42
350
110.68
16800
198
25
0.00911
97
0.00884
156.34
100
8948.3
3
9225
10
1008
10080
细纱(纬)
10
1
42
330
104.36
275.86
65.6
4.45
4
4.64
3
2
6
混并一
3600
6
6.68
100
45
64.8
85
55.08
430.61
102.4
7.82
4
8.1
5
2
10
混并二
3600
6
6
100
45
64.8
85
55.08
430.61
102.4
7.82
4
8.1
5
2
10
混并三
3600
6
6
100
45
64.8
85
55.08
430.61
68.53
439.39
102
6.41
4
6.7
4
2
8
粗纱
740
1
5.68
95
3.49
850
277
28
1.094
82
0.897
437.23
101.5
487.4
4
508
5
120
600
细纱(经纱)
32
1