开题报告-XKM754型精密数控卧式床身铣床的研究与设计
工作报告之数控铣床开题报告
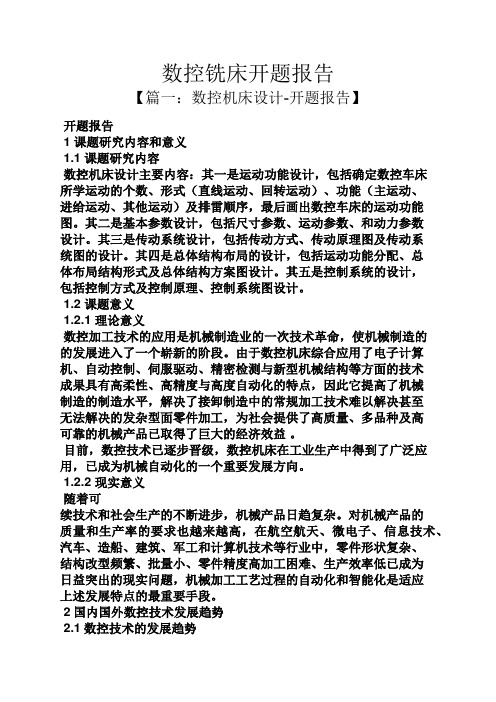
数控铣床开题报告【篇一:数控机床设计-开题报告】开题报告1 课题研究内容和意义1.1 课题研究内容数控机床设计主要内容:其一是运动功能设计,包括确定数控车床所学运动的个数、形式(直线运动、回转运动)、功能(主运动、进给运动、其他运动)及排雷顺序,最后画出数控车床的运动功能图。
其二是基本参数设计,包括尺寸参数、运动参数、和动力参数设计。
其三是传动系统设计,包括传动方式、传动原理图及传动系统图的设计。
其四是总体结构布局的设计,包括运动功能分配、总体布局结构形式及总体结构方案图设计。
其五是控制系统的设计,包括控制方式及控制原理、控制系统图设计。
1.2 课题意义1.2.1 理论意义数控加工技术的应用是机械制造业的一次技术革命,使机械制造的的发展进入了一个崭新的阶段。
由于数控机床综合应用了电子计算机、自动控制、伺服驱动、精密检测与新型机械结构等方面的技术成果具有高柔性、高精度与高度自动化的特点,因此它提高了机械制造的制造水平,解决了接卸制造中的常规加工技术难以解决甚至无法解决的发杂型面零件加工,为社会提供了高质量、多品种及高可靠的机械产品已取得了巨大的经济效益。
目前,数控技术已逐步晋级,数控机床在工业生产中得到了广泛应用,已成为机械自动化的一个重要发展方向。
1.2.2 现实意义随着可续技术和社会生产的不断进步,机械产品日趋复杂。
对机械产品的质量和生产率的要求也越来越高,在航空航天、微电子、信息技术、汽车、造船、建筑、军工和计算机技术等行业中,零件形状复杂、结构改型频繁、批量小、零件精度高加工困难、生产效率低已成为日益突出的现实问题,机械加工工艺过程的自动化和智能化是适应上述发展特点的最重要手段。
2国内国外数控技术发展趋势2.1数控技术的发展趋势数控技术的应用不但给传统制造业带来了革命性的变化,使制造业成为工业化的象征,而且随着数控技术的不断发展和应用领域的扩大,他对国计民生的一些重要行业 it、汽车、轻工、医疗等的发展起着越来越重要的作用。
《数控铣床及加工中心产品设计》开题报告

《数控铣床及加工中心产品设计》开题报告一、课题名称:数控铣床及加工中心产品设计二、选题理由制造技术是各国经济竞争的重要支柱之一,经济的成功在很大程度上得益于先进的制造技术,而机床是机械制造技术重要的载体,它标志着一个国家的生产能力和技术水平。
机床工业是国民经济的一个重要先行部门,担负这为国民经济各部门提供现代化技术装备的任务,以1994年为例,全世界基础的消费额达261.7亿美元。
其中美国的消费额56亿美元、中国33.6亿美元。
所以,在我国国民经济建设中,机床工业起着重要的作用。
然而在机械制造业中,大批大量生产时采用专用机床、组合机床、专用自动线等并配以相应的工装,这些设备的初期投资费用大、生产准备时间长,并且不适应产品的更新换代。
单件小批生产时,由于产品多变而不宜采用专用机床,特别是在国防、航空、航天和深潜的部门,其零件的精度要求非常高,几何形状也日趋复杂,且改型频繁,生产周期短,这就要求迅速适应不同零件的加工。
书空机床就是在这样的背景下产生和发展起来的一种新型自动化机床,它较好的解决了小批量、品种多变化、形状复杂和精度高的零件的自动化加工问题。
随着计算机技术,特别是微型计算机技术的发展及其在数控机床上的应用,机床数控技术正从普通数控向计算机数控发展。
一个国家数控机床的拥有量(相对值),标志着这个国家机械制造业的现代化程度。
数控铣床和加工中心因其特有的加工方式及其加工范围广在数控机床中占有重大的比例,因此研究《数控铣床及加工中心产品设计》具有重大意义。
三、国内外研究现状当今世界,工业发达国家对机床工业高度重视,竞相发展机电一体化、高质量、高精、高效、自动化先进机床,以加速工业和国民经济的发展。
长期以来,欧、美、亚在国际市场上相互展开激烈竞争,已形成一条无形战线,特别是随微电子、计算机技术的进步,数控机床在20世纪80年代以后加速发展,各方用户提出更多需求,早已成为四大国际机床展上各国机床制造商竞相展示先进技术、争夺用户、扩大市场的焦点。
床身铣床的模拟与优化设计
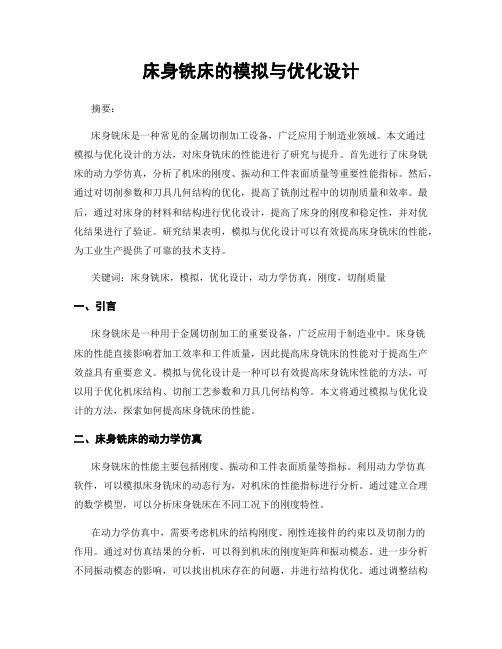
床身铣床的模拟与优化设计摘要:床身铣床是一种常见的金属切削加工设备,广泛应用于制造业领域。
本文通过模拟与优化设计的方法,对床身铣床的性能进行了研究与提升。
首先进行了床身铣床的动力学仿真,分析了机床的刚度、振动和工件表面质量等重要性能指标。
然后,通过对切削参数和刀具几何结构的优化,提高了铣削过程中的切削质量和效率。
最后,通过对床身的材料和结构进行优化设计,提高了床身的刚度和稳定性,并对优化结果进行了验证。
研究结果表明,模拟与优化设计可以有效提高床身铣床的性能,为工业生产提供了可靠的技术支持。
关键词:床身铣床,模拟,优化设计,动力学仿真,刚度,切削质量一、引言床身铣床是一种用于金属切削加工的重要设备,广泛应用于制造业中。
床身铣床的性能直接影响着加工效率和工件质量,因此提高床身铣床的性能对于提高生产效益具有重要意义。
模拟与优化设计是一种可以有效提高床身铣床性能的方法,可以用于优化机床结构、切削工艺参数和刀具几何结构等。
本文将通过模拟与优化设计的方法,探索如何提高床身铣床的性能。
二、床身铣床的动力学仿真床身铣床的性能主要包括刚度、振动和工件表面质量等指标。
利用动力学仿真软件,可以模拟床身铣床的动态行为,对机床的性能指标进行分析。
通过建立合理的数学模型,可以分析床身铣床在不同工况下的刚度特性。
在动力学仿真中,需要考虑机床的结构刚度、刚性连接件的约束以及切削力的作用。
通过对仿真结果的分析,可以得到机床的刚度矩阵和振动模态。
进一步分析不同振动模态的影响,可以找出机床存在的问题,并进行结构优化。
通过调整结构参数或增加支撑件等方式,可以提高床身铣床的刚度,减小振动,从而提高加工精度和表面质量。
三、切削参数和刀具几何结构的优化切削参数和刀具几何结构是影响加工效果的关键因素。
通过模拟与优化设计的方法,可以根据不同的加工要求优化切削参数和刀具几何结构,提高切削质量和效率。
在优化切削参数时,需要考虑切削速度、进给量和切削深度等参数对切削力和表面质量的影响。
《微型精密铣床的研究和设计》范文
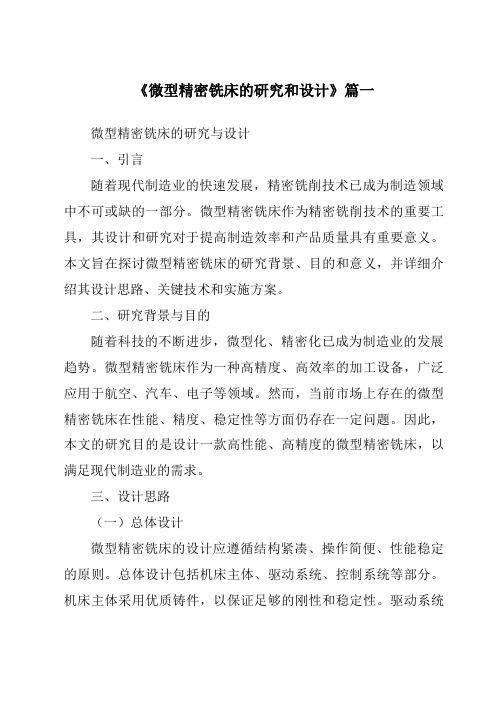
《微型精密铣床的研究和设计》篇一微型精密铣床的研究与设计一、引言随着现代制造业的快速发展,精密铣削技术已成为制造领域中不可或缺的一部分。
微型精密铣床作为精密铣削技术的重要工具,其设计和研究对于提高制造效率和产品质量具有重要意义。
本文旨在探讨微型精密铣床的研究背景、目的和意义,并详细介绍其设计思路、关键技术和实施方案。
二、研究背景与目的随着科技的不断进步,微型化、精密化已成为制造业的发展趋势。
微型精密铣床作为一种高精度、高效率的加工设备,广泛应用于航空、汽车、电子等领域。
然而,当前市场上存在的微型精密铣床在性能、精度、稳定性等方面仍存在一定问题。
因此,本文的研究目的是设计一款高性能、高精度的微型精密铣床,以满足现代制造业的需求。
三、设计思路(一)总体设计微型精密铣床的设计应遵循结构紧凑、操作简便、性能稳定的原则。
总体设计包括机床主体、驱动系统、控制系统等部分。
机床主体采用优质铸件,以保证足够的刚性和稳定性。
驱动系统采用高性能伺服电机和精密丝杠,以确保加工过程中的精度和稳定性。
控制系统采用先进的数控系统,实现自动化加工。
(二)关键技术1. 精密传动技术:采用高精度齿轮和轴承,保证传动精度和稳定性。
2. 数控技术:采用先进的数控系统,实现自动化加工和精确控制。
3. 切削参数优化:通过优化切削参数,提高加工效率和表面质量。
四、关键技术设计与实施方案(一)精密传动系统设计精密传动系统是微型精密铣床的核心部分,其设计直接影响机床的加工精度和稳定性。
设计过程中,应选择高精度齿轮和轴承,以保证传动精度。
同时,采用先进的润滑系统,降低传动系统的摩擦和磨损,延长使用寿命。
(二)数控系统设计数控系统是微型精密铣床的“大脑”,负责自动化加工和精确控制。
设计过程中,应选择性能稳定、功能强大的数控系统,实现加工过程的自动化和智能化。
同时,应具备友好的人机界面,方便操作人员进行参数设置和操作。
(三)切削参数优化设计切削参数的优化对于提高加工效率和表面质量具有重要意义。
《微型精密铣床的研究和设计》范文
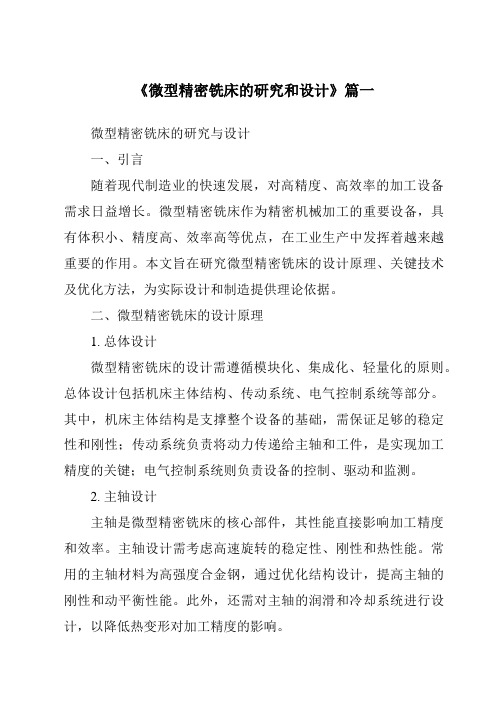
《微型精密铣床的研究和设计》篇一微型精密铣床的研究与设计一、引言随着现代制造业的快速发展,对高精度、高效率的加工设备需求日益增长。
微型精密铣床作为精密机械加工的重要设备,具有体积小、精度高、效率高等优点,在工业生产中发挥着越来越重要的作用。
本文旨在研究微型精密铣床的设计原理、关键技术及优化方法,为实际设计和制造提供理论依据。
二、微型精密铣床的设计原理1. 总体设计微型精密铣床的设计需遵循模块化、集成化、轻量化的原则。
总体设计包括机床主体结构、传动系统、电气控制系统等部分。
其中,机床主体结构是支撑整个设备的基础,需保证足够的稳定性和刚性;传动系统负责将动力传递给主轴和工件,是实现加工精度的关键;电气控制系统则负责设备的控制、驱动和监测。
2. 主轴设计主轴是微型精密铣床的核心部件,其性能直接影响加工精度和效率。
主轴设计需考虑高速旋转的稳定性、刚性和热性能。
常用的主轴材料为高强度合金钢,通过优化结构设计,提高主轴的刚性和动平衡性能。
此外,还需对主轴的润滑和冷却系统进行设计,以降低热变形对加工精度的影响。
三、关键技术研究1. 动力学分析动力学分析是微型精密铣床设计的重要环节。
通过对机床的动态特性进行分析,可以了解机床在加工过程中的振动、变形等情况,为优化设计提供依据。
常用的动力学分析方法包括有限元法、模态分析法等。
2. 精度控制技术精度控制技术是保证微型精密铣床加工精度的关键。
包括误差补偿技术、热误差控制技术等。
误差补偿技术通过对机床误差进行检测和修正,提高加工精度;热误差控制技术则通过优化机床结构、改进润滑和冷却系统等方法,降低热变形对加工精度的影响。
四、优化方法与实施步骤1. 优化方法针对微型精密铣床的设计和制造过程,可采用多种优化方法,如结构优化、材料选择、工艺优化等。
其中,结构优化可通过改变机床的结构布局、减轻重量、提高刚性和稳定性等手段,提高机床的性能;材料选择则需根据实际需求,选择合适的材料以保证机床的耐用性和可靠性;工艺优化则包括对加工工艺的改进和优化,以提高加工效率和精度。
床身铣床的数控系统设计与开发
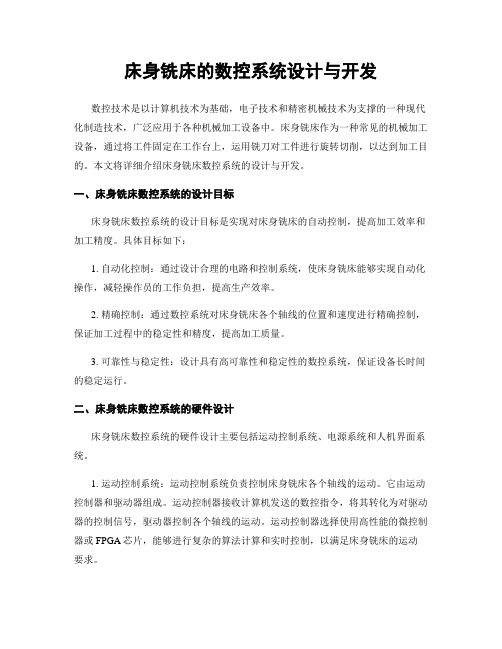
床身铣床的数控系统设计与开发数控技术是以计算机技术为基础,电子技术和精密机械技术为支撑的一种现代化制造技术,广泛应用于各种机械加工设备中。
床身铣床作为一种常见的机械加工设备,通过将工件固定在工作台上,运用铣刀对工件进行旋转切削,以达到加工目的。
本文将详细介绍床身铣床数控系统的设计与开发。
一、床身铣床数控系统的设计目标床身铣床数控系统的设计目标是实现对床身铣床的自动控制,提高加工效率和加工精度。
具体目标如下:1. 自动化控制:通过设计合理的电路和控制系统,使床身铣床能够实现自动化操作,减轻操作员的工作负担,提高生产效率。
2. 精确控制:通过数控系统对床身铣床各个轴线的位置和速度进行精确控制,保证加工过程中的稳定性和精度,提高加工质量。
3. 可靠性与稳定性:设计具有高可靠性和稳定性的数控系统,保证设备长时间的稳定运行。
二、床身铣床数控系统的硬件设计床身铣床数控系统的硬件设计主要包括运动控制系统、电源系统和人机界面系统。
1. 运动控制系统:运动控制系统负责控制床身铣床各个轴线的运动。
它由运动控制器和驱动器组成。
运动控制器接收计算机发送的数控指令,将其转化为对驱动器的控制信号,驱动器控制各个轴线的运动。
运动控制器选择使用高性能的微控制器或FPGA芯片,能够进行复杂的算法计算和实时控制,以满足床身铣床的运动要求。
2. 电源系统:电源系统负责为整个数控系统提供稳定的电源供应。
它由交流电源和直流电源组成。
交流电源负责将市电转化为适合数控系统工作所需的交流电,直流电源负责将交流电转化为数控系统所需的直流电。
3. 人机界面系统:人机界面系统负责将计算机发送的数控指令转化为人类能够理解的形式,并显示在操作界面上。
它通常由液晶显示屏、按键或触摸屏等组成。
操作员可以通过人机界面系统输入加工参数、启动加工过程、监控加工状态等。
三、床身铣床数控系统的软件设计床身铣床数控系统的软件设计主要包括上位机软件和下位机软件。
1. 上位机软件:上位机软件运行在计算机上,负责实现数控编程、数控仿真、加工路径生成和加工指令发送等功能。
铣床设计开题报告

铣床设计开题报告铣床设计开题报告引言:铣床是一种常见的机械设备,广泛应用于制造业中。
本开题报告旨在探讨铣床设计的相关问题,包括设计原则、结构特点以及应用领域等。
通过对铣床设计的深入研究,我们可以更好地理解铣床的工作原理和优化设计方法,为制造业提供更高效、精确的加工工具。
一、铣床的工作原理铣床是一种通过旋转刀具在工件上进行切削加工的机床。
其工作原理是将工件固定在工作台上,通过主轴驱动刀具旋转,并在水平和垂直方向上进行移动,以实现对工件的切削加工。
铣床的切削方式可分为平面铣削、立体铣削和曲面铣削等。
二、铣床设计的原则1. 结构合理性:铣床的设计应考虑结构的合理性,包括机床整体结构的稳定性和刚性,以及各部件之间的配合精度。
合理的结构设计能够提高铣床的工作精度和稳定性。
2. 功能完善性:铣床设计应满足不同加工需求,包括切削功能、进给功能和定位功能等。
同时,还应考虑安全性和操作便捷性等因素,以提高工作效率和操作人员的安全性。
3. 制造成本:铣床的设计应考虑制造成本,包括材料成本、加工成本和装配成本等。
通过合理的设计,可以降低制造成本,提高产品竞争力。
三、铣床的结构特点铣床的结构特点主要包括以下几个方面:1. 机床床身:机床床身是铣床的基础部件,承受着整个机床的重量和切削力。
合理的床身结构能够提高机床的刚性和稳定性。
2. 主轴系统:主轴系统是铣床的核心部件,负责驱动刀具旋转。
高精度的主轴系统能够保证切削加工的精度和效率。
3. 进给系统:进给系统是铣床实现工件加工的关键部件,包括进给轴和进给驱动装置等。
稳定的进给系统能够保证工件的加工精度和表面质量。
4. 控制系统:控制系统是铣床的智能化部分,负责控制整个机床的运行和加工过程。
先进的控制系统能够提高铣床的自动化程度和生产效率。
四、铣床的应用领域铣床广泛应用于制造业中的各个领域,包括航空航天、汽车制造、电子设备和模具制造等。
在航空航天领域,铣床用于加工飞机零部件和发动机部件等;在汽车制造领域,铣床用于加工汽车发动机缸体和底盘部件等;在电子设备领域,铣床用于加工电子产品外壳和连接器等;在模具制造领域,铣床用于加工各种模具和模具零部件等。
《2024年微型精密铣床的研究和设计》范文

《微型精密铣床的研究和设计》篇一微型精密铣床的研究与设计一、引言随着现代制造业的快速发展,精密铣削技术在各种零部件的加工制造中得到了广泛应用。
然而,传统的大型铣床由于其庞大的体积和较高的成本,往往无法满足某些特殊或小批量生产的需求。
因此,微型精密铣床的研发与优化成为了现代机械工程领域的研究热点。
本文旨在研究并设计一款具有高精度、高效率、高稳定性的微型精密铣床,以适应日益增长的微型零件加工需求。
二、需求分析1. 性能需求:考虑到铣削过程的复杂性,微型精密铣床需要具备高精度、高效率和高稳定性的特点。
此外,还需要具备较好的可操作性和可维护性。
2. 工艺需求:设备应能适应多种不同材质的铣削需求,如金属、合金等,以满足市场对多种零件的加工需求。
3. 市场需求:随着科技的发展,对微型零件的需求日益增长,因此,微型精密铣床应具有较高的市场竞争力。
三、设计与研究1. 机械结构设计:采用模块化设计思路,将铣床分为底座、立柱、工作台、驱动系统等模块。
其中,底座和立柱采用高强度材料,以确保设备的稳定性;工作台采用滚珠导轨以提高加工精度;驱动系统采用高性能电机和先进的传动技术。
2. 控制系统设计:采用数字化控制技术,如伺服控制技术和实时监控技术,实现对铣削过程的精确控制。
同时,采用友好的人机交互界面,方便操作人员使用。
3. 精度优化:通过优化机械结构设计和控制系统设计,提高设备的加工精度。
此外,还可以采用误差补偿技术,如热误差补偿和机械误差补偿等,进一步提高设备的稳定性。
4. 工艺优化:针对不同材质的铣削需求,设计不同的工艺流程和参数设置。
同时,通过仿真软件对铣削过程进行模拟和优化,以提高设备的加工效率和产品质量。
四、实验与验证在完成微型精密铣床的设计后,需要进行实验验证其性能和精度。
首先,对设备进行装配和调试,确保各部件的正常运行。
然后,进行一系列的铣削实验,包括不同材质、不同工艺参数下的铣削实验。
通过实验数据的分析和处理,验证设备的性能和精度是否达到预期目标。
- 1、下载文档前请自行甄别文档内容的完整性,平台不提供额外的编辑、内容补充、找答案等附加服务。
- 2、"仅部分预览"的文档,不可在线预览部分如存在完整性等问题,可反馈申请退款(可完整预览的文档不适用该条件!)。
- 3、如文档侵犯您的权益,请联系客服反馈,我们会尽快为您处理(人工客服工作时间:9:00-18:30)。
开题报告1课题名称XKM754型精密数控卧式床身铣床的研究与设计2任务2.1 技术参数工作台工作面面积(长×宽):1000×400mm;行程(X×Y×Z):600×400×500mm;快速移动速度(X、Y、Z):12000mm/min;进给速度范围(X、Y、Z):1~6000mm/min;主轴箱重量:1000kg、工件及工作台重量600kg、滑鞍重量500kg;主电机功率:15KW;主轴计算转速:200r/min;主轴锥孔序号:ISON050;拉刀力:1000kg;定位精度:0.02mm;重复定位精度:0.16mm。
2.2 方案要求(1)机床总体布局;(2)确定导轨型式;(3)确定滚珠丝杠的支撑方式与型号及安装型式;(4)确定主传动系统的驱动方案;(5)确定低档降速比及高档降速比;(6)确定传动轴数,拟定转速图、主轴功率扭矩特性图;(7)确定主轴箱的平衡结构。
2.3 成果形式(1)提交资料:论文;图纸(手工图、CAD图);(2)答辩。
3主传动系统设计方案3.1 概述主传动系统是用来实现机床主运动的传动系统,它应具有一定的转速(速度)和一定的变速范围,以便采用不同材料的刀具,加工不同材料、不同尺寸、不同要求的工件,并能方便地实现运动的开停、变速、换向和制动等。
数控机床主传动系统主要包括电动机、传动系统和主轴部件,与普通机床的主传动系统相比在结构上比较简单,这是因为变速功能全部或大部分由主轴电动机的无级变速来承担,省去了复杂的齿轮变速机构,有些只有二级或三级齿轮变速系统以扩大电动机的恒功率调速的范围。
3.2 技术方案3.2.1 无级变速主传动链数控机床一般都采用直流或交流调速电动机作为驱动源并采用电气无级调速。
由于数控机床主运动的调速范围较宽,一般情况下单靠调速电动机无法满足;另一方面调速电动机的功率和转矩特性也难以直接与机床的功率和转矩要求完全匹配。
因此,需要在无级调速电动机之后串联机械分级变速传动,以满足调速范围和功率、转矩特性的要求。
本主轴箱采用交流主轴伺服电机调速,两档齿轮变速,以实现本床身铣床的无级变速。
(1)主轴电动机加工中心上常用的主轴电动机为交流调速电动机和交流伺服电动机。
交流调速电动机通过改变电动机的供电频率调整电动机的转速。
交流主轴伺服电动机是一种高效能的主轴驱动电动机,其工作原理与交流伺服进給电动机相同,但其工作转速比一般的交流伺服电动机要高。
交流伺服电动机可以实现主轴在任意方向上的定位,并且以很大转矩实现微小位移。
(2)交、直流无级调速电机的功率转矩特性图3-1所示是机床主轴要求的功率特性和转矩特性。
这两条特性曲线是以计算转速n j 为界,从nj至最高转速nmax的区域Ⅰ为恒功率区,恒功率调速范围为RDP,该区域内,任意转速下主轴都可输出额定的功率,最大转矩则随主轴转速的下降而上升。
从最低转速n min 至nj的区域Ⅱ为恒转矩区,恒转矩调速范围为RDT,在该区域内,最大转矩不再随转速下降而上升,任何转速下可能提供的转矩都不能超过计算转速下的转矩,这个转矩就是机床主轴的最大转矩Mmax 。
在Ⅱ区域内,主轴可能输出的最大功率Pmax,则随主轴转速的下降而下降。
通常,恒功率区约占整个主轴变速范围的2/3~3/4;恒转矩区约占1/4~1/3。
如图3-2所示,变速电机的调速范围RD也包括两部分:从额定转速nd 到最高转速nmax的区域Ⅰ为恒功率区(调磁调速范围RDT);从最低转速nmin 至nd的区域Ⅱ为恒转矩区(调压调速范围RDP)。
直流电机的额定转速通常为1000~1500r/min。
从nd 至nmax用调节磁通Φ的办法得到,称为调磁调速;从n min至n d用调节电枢电压的办法得到,称调压调速。
交流调频电机用调节电源频率来达到调速的目的。
额定转速通常为1500r/min。
这两种电机的恒功率转速范围常为2~4;恒转矩变速范围则可达100以上。
显然,变速电机的功率特性与机床主轴的要求不匹配。
变速电机的恒功率范围小而主轴要求的范围大。
因此,单凭总变速范围设计主传动系统是不能满足加工要求的,必须考虑性能匹配问题。
通常采用的办法是在电动机与主轴之间串联一个分级变速箱。
图3-1 主轴的功率扭矩特性图3-2 变速电动机的功率特性(3)床身铣床无级变速的设计显然,变速电机的功率特性与机床主轴的要求不匹配。
变速电机的恒功率范围小而主轴要求的范围大。
因此,单凭总变速范围设计主传动系统是不能满足加工要求的,必须考虑性能匹配问题。
通常采用的办法是在电动机与主轴之间串联一个分级变速箱。
在本床身铣床中,由交流主轴伺服电机实现电机无级调速,由齿轮实现两档变速。
其中,传动轴有四根,Ⅰ轴、Ⅱ轴为固定轴,Ⅲ轴为变速轴,Ⅳ轴为主轴,主轴与编码器通过齿轮传动,将主轴的转速1:1反馈给脉冲编码器。
Ⅲ轴为花键轴,轴上装有二联滑移齿轮,通过长销与轴内的拉杆相连,轴的上端装有变档液压油缸,油缸进油,活塞杆带动拉杆移动,拉杆带动长销在Ⅲ轴的槽内移动,同时带动滑移齿轮移动,从而实现两档变速。
图3-3为主传动系统图,图3-4为主轴的转速图,图3-5为主轴的功率、转矩特性图:图3-3 主传动系统图图3-4 转速图图3-5 功率、扭矩特性图3.2.2 主轴组件设计主轴组件是机床的重要部件之一,它是机床的执行件。
主轴组件包括主轴和主轴轴承。
主轴是主轴组件的重要组成部分。
它的结构尺寸和形状、制造精度、材料及其热处理对主轴组件的工作性能有很大的影响。
同时,主轴结构要保证轴上各个零件定位可靠,工艺性好等要求。
主轴组件应有更高的动、静刚度和抵抗热变形的能力。
(1)主轴本床身铣床的主轴的前端结构形式取决于机床类型和安装夹具或刀具的结构形式。
主轴端部用于安装刀具或夹持工件的夹具,在结构上,应能保证定位准确、安装可靠、连接牢固、装卸方便,并能传递足够的转矩。
图3-6所示为铣、镗类机床主轴的端部,铣刀或刀杆在前端7:24的锥孔内定位,并用拉杆从主轴后端拉紧,而且由前端的端面键传递转矩。
图3-6 主轴部件的结构形式(2)主轴轴承本床身铣床采用的是滚动轴承,支承方式为一端固定,一端游动。
前支承采用的是三个角接触球轴承三联(DBD),前两个轴承大口方向相同朝右,能承受较大的单向轴向载荷。
后支承采用的是两个深沟球轴承,由于在运转中发热,主轴必然产生热膨胀,为了吸收这个膨胀量,后支承为游动形式。
图3-7 主轴轴承配置方式3.2.3 主轴的刀具自动夹紧机构在自动换刀的数控机床中为了实现刀具在主轴内的自动装卸,其主轴必须设计有刀具的自动夹紧机构。
刀杆采用7:24的大锥度锥柄,这样既有利于定心,也为刀具的夹紧和松开带来了方便。
装夹刀具时,锥柄的尾端轴颈被拉紧,同时通过锥柄的定心和摩擦作用将刀杆夹紧于主轴的端部。
在碟形弹簧的作用下,拉杆始终保持约1000kg的拉力,并通过拉杆将刀杆的尾部轴颈拉紧。
换刀时,首先将液压油通入主轴尾部液压缸的左腔,活塞拖动拉杆向右移动,将刀柄松开,同时碟形弹簧被压紧,消除了刀杆上的拉力。
换刀结束后,电磁换向阀动作使液压油通入液压油缸右腔,活塞左移退回原位,碟形弹簧复原又将刀杆拉紧。
3.2.4 主轴箱平衡机构XKM754型精密数控卧式床身铣床主轴箱的平衡机构,采用液压平衡系统。
经过鉴定和生产试验表明,这种液压平衡系统工作可靠,速度转换平稳,满足机床使用性能的要求。
4进给传动系统设计方案4.1 概述在设计数控机床的进给传动系统时,一般已知以下条件:移动部件(即机床执行部件)的总质量(包括移动部件自身的质量、夹具的质量和工件的质量),移动部件的最大移动速度(mm/min),电动机的最高转速(r/min),移动部件的定位精度(mm)和重复定位精度(mm),移动部件的行程(mm)。
进给传动系统设计的主要任务是进行满足上述已知条件的移动部件的结构设计,解决的主要问题是:导轨的选型与设计,滚珠丝杠支撑方式的确定,滚珠丝杠螺母副的选型与计算,进给传动系统的刚度验算、动态特征分析与固有频率计算、误差分析与验算,驱动电动机的选型与计算。
4.2 总体布局XKM754型精密数控卧式床身铣床主要由如下几大部件组成:底座、滑鞍、工作台、立柱、主轴箱。
其总体布局图如图4-1、图4-2。
总体布局图主要反映了各坐标方向的行程、悬出端长度,总体的长宽高,以及各部件在工作时是否干涉等情况。
X轴方向上,工作台的长度1200mm,行程600mm,当工作台到达-X、+X方向行程极限位置时,悬出端200mm,工作台的中心仍在滑鞍导轨跨距之内。
Y轴方向上,滑鞍的宽度540mm,行程400mm,当滑鞍到达-Y、+Y方向行程极限位置时,工作台和滑鞍的边界仍在底座的长度方向的范围内。
并且当滑鞍到达+Y方向行程极限位置时,工作台与主轴不发生干涉,此时滑鞍中心距离主轴端面50mm。
图4-1 布局图(主视)图4-2 布局图(左视)Z轴方向上,行程500mm,当主轴到达+Z方向行程极限位置时,主轴箱顶端与立柱不发生干涉。
当主轴到达-Z方向行程极限位置时,主轴箱底端与立柱不发生干涉,并且主轴与工作台不发生干涉,此时主轴中心距离工作台台面150mm。
在各个坐标上,电机支架、螺母座、轴承座严格要求同轴度,通过控制安装面距离导轨面的尺寸,来控制各零件中心距离导轨面的尺寸,从而保证同轴度。
总体尺寸为1800×2060×2830mm。
4.3 主要技术4.3.1 导轨的设计与选型XKM754型精密数控卧式床身铣床X、Y、Z三个坐标上的导轨均采用矩形导轨(如图4-3),在与之相配的滑动面上贴聚四氟乙烯(PT-FE)导轨板,同时采用斜镶条消除导向面的间隙。
矩形导轨易加工制造,刚度和承载能力大,安装调整方便。
矩形导轨中M面起支撑兼导向作用,起主要导向作用的N面磨损后不能自动补偿间隙,需要有间隙调整装置。
适用于在和大且导向精度要求不高的机床。
图4-3 直线滑动导轨的截面形状4.3.2 滚珠丝杠螺母副的选型(1)预紧方式本数控卧式床身铣床三个坐标轴上滚珠丝杠螺母均采用双螺母垫片调隙式(图4-4),调整垫片的厚度使左右两螺母产生轴向位移,即可消除间隙和产生预紧力。
这种方法结构简单,刚度好,但调整不便,当滚道有磨损时不能随时消除间隙和进行预紧。
图4-4 垫片调隙式(2)支承方式此设计方案中,三个坐标轴上均采用两端固定的支承方式,这种方式丝杠一般不会受压,无压杆稳定问题,机械系统的固有频率比一端固定的要高。
可以预拉伸,预拉伸后可以减少丝杠自重的下垂和补偿热膨胀,但需要设计一套预拉伸机构,结构与工艺都比较困难,适用于对刚度和位移精度要求高的场合。
图4-5 固定端角接触球轴承配对方式4.3.3 驱动电动机的选型进给系统中,驱动电动机采用华中数控GK6交流永磁同步伺服电机,该电机采用自冷式,防护等级为IP64-IP67,具有响应迅速、精度和效率高、负载能力大、控制性能优越等优点,被广泛使用在闭环或半闭环控制的伺服系统中。