18螺切分轧制两线差问题的解决
18切分孔型系统新设计

柳钢科技2009年中南·泛珠三角地区第五届1前言2005年安阳钢铁股份有限公司260机组成功开发了18螺纹切分技术,生产出了Φ18mm 螺纹钢,从而使Φ12~18mm全部实现了切分生产。
本文结合260机组生产实践,就18螺纹的切分孔型系统设计的特殊性进行如下分析。
2切分孔型系统的选择和位置的确定2.1孔型系统的选择在260机组设计的两线切分孔型中Φ14mm、Φ16mm带肋钢筋采用的是梅花方孔型系统(见图1);这种孔型系统虽然尺寸控制精度高、孔型延伸系数也较大、且变性相对均匀侧边有凹陷不易出耳子,但是由于精度高,所以对磨损很敏感,而且轧件需要扭转45°影响轧制的稳定性对于规格较大而且延伸率较小的Φ18mm带肋钢筋来说不易控制,且由于Φ18mm带肋钢筋断面较大,对磨损尤其敏感。
因此,260机组在Φ18mm螺纹的切分孔型设计中采用了扁方孔型,这种孔型的缺点是平辊和扁方的控制精度不高,且扁方轧件变形不均匀对切分楔的冲击较大,使切分楔磨损大但是它有K5进K4孔型无需扭转的优点,使轧制的稳定性提高。
生产实践表明,其选择是正确的。
2.2切分位置的确定切分位置的确定要求[1]:(1)尽可能少的改变原有工艺流程设备;(2)根据轧机布置情况,尽可能接近成品机架,减少双线道次;(3)切分后要易于操作;(4)预切分轧件进切分孔型要尽量避免扭转。
根据我机组仅有15架水平布置轧机的实际情况选择13#轧机为切分轧机,这样轧件切分后仅留有2道次必要的成型孔型,较易控制。
3切分孔型系统的设计3.1K6的平辊无孔型压下设计扁方孔型系统具有较小的延伸系数,主要体现在K6平辊压下的设计上。
孔型设计中,圆18切分孔型系统新设计刘雅婕(安阳钢铁公司)摘要结合安阳钢铁股份有限公司第一轧钢厂260机组18两线切分的生产实践,对切分孔型系统的选择和设计进行了详细分析。
关键词棒材切分轧制两线切分孔型设计New Design for Splitting Pass System ofΦ18mm Reinforce BarLIU Ya-jie(Anyang Iron and Steel Company Limited)Abstract The selection and design for slitting pass system were analyzed in detail by combining with the production practice of double-line slitting system ofΦ18mm reinforce bar of Unit260.Key Words Steel Bar Slitting Rolling Double-line Slitting Pass Design1722009年中南·泛珠三角地区第五届图116-1016-1116-1216-1316-1416-15进平辊的最大特点是以宽展为主,延伸和断面收缩较小,Φ18mmK6道次的延伸系数较小,因此改变K6平辊的压下量对轧件的断面面积影响较小,要控制K6轧件的断面面积,必须通过调整K7道次的孔型面积来实现。
螺纹钢筋切分扁方孔型系统优化设计

螺纹钢筋切分扁方孔型系统优化设计潘建洲(福建三钢(集团)闽光股份有限公司棒材厂,三明 365000)摘要: 结合三钢棒材线实际,Φ16/Φ18螺纹切分精轧孔型选择采用扁方孔型系统,通过对切分孔型优化设计,合理选择轧辊材质,能有效地减少工艺事故、提高产量和改善指标,具有显著优越性。
关键词: 螺纹切分孔型设计1前言随着小规格螺纹钢筋(主要指Ф18mm以下,下同)切分轧制技术的发展,改变了小规格材产量不高、生产效率低下的状况,同时也带来了工艺故障复杂、指标下降等一些问题。
工艺设计对于切分轧制成功与否关系重大,孔型设计又是工艺设计中最重要的一环,是工艺设计的核心内容。
孔型设计合理,能有效地减少工艺故障、提高指标、降低轧辊导卫消耗。
对于孔型系统的选择,目前国内大多采用了梅花方和扁方孔型系统,由于两种孔型系统各有利弊,只有根据生产线工艺装备、产品要求等实际情况,确定孔型系统的选用。
基于梅花方孔型系统的论述较多,扁方孔型系统设计论述较少,本文就扁方孔型系统设计作一讨论,以期对此类切分生产线有所帮助。
2三钢闽光公司棒材厂螺纹钢切分情况三钢棒材厂始建于1992年,1995年底开始投入生产,设计年产Φ12—40mm螺纹钢筋和光面圆钢30万吨,经过3次重大技术改造,目前年产达到80万吨以上,生产原料为150*150*12000mm连铸小方坯,采用热装热送工艺,装备有:2座蓄热式加热炉、17架连轧机、7.8*102 m步进式冷床、4900KN冷剪机,并从国外引进倍尺飞剪、自动打捆机等设备,是一条具有九十年代国际先进水平的连续棒材轧钢生产线。
该线精轧6架(12#-17#)呈H/V交替布置,其中15#轧机可通过液压装置实现快捷方便地平立互换,从立式机架出成品(K1前后无平立交叉导管),精轧全部采用“霍太克”导卫。
采用扁方孔型系统生产Φ16、Φ18两种规格,并多次对切分孔型进行改进,逐步消除了K3进出口故障较多、产品表面质量缺陷等设计上的不足,生产更趋稳定,指标明显提高。
钢筋加工中的常见误差及纠正方法

钢筋加工中的常见误差及纠正方法引言:钢筋是建筑领域中重要的材料之一,广泛用于混凝土结构中。
而在钢筋的加工过程中,常常会出现一些误差,这些误差可能会对结构的强度、耐久性和安全性造成潜在的威胁。
因此,本文将探讨钢筋加工过程中常见的误差,并提供纠正方法,以期提高钢筋的质量和加工效率。
一、长度误差在钢筋加工过程中,长度误差是较为常见的问题之一。
这可能是由于测量工具的误差、操作人员的不慎或设备的磨损所引起的。
为了解决这一问题,可以采取以下措施:1. 使用精确的测量工具,如千分尺或激光测距仪,减小测量误差;2. 培训操作人员,提高其操作技能和专业素养;3. 定期检修和维护加工设备,确保其精度和正常运行。
二、直径误差钢筋的直径误差可能是由材料供应商的误差、加工设备的异动或操作人员的不当操作导致的。
为了纠正这一问题,需要注意以下几点:1. 选择质量可靠的钢筋供应商,并与其保持良好的合作关系;2. 定期对加工设备进行校准和调整,确保其正确运行;3. 配备精细的测量工具,对钢筋进行全面的检测和测试。
三、弯曲误差钢筋的弯曲误差可能是由于模具设计的不合理或操作工人技术不过关所致。
要解决这个问题,可以考虑以下几点:1. 优化模具设计,确保弯曲角度和曲率半径的准确性;2. 开展钢筋加工操作人员的培训和技能提升,提高其弯曲钢筋的准确性和一致性;3. 引进先进的弯曲机械设备,可以提高加工效率和精度。
四、切割误差切割误差也是常见的钢筋加工误差之一。
这可能是由于切割工具的磨损、切割速度过高或切割不准确所导致的。
要解决切割误差,可以考虑以下几点:1. 定期检查和更换切割工具,确保其切割刀片的锐利度;2. 调整切割速度,确保切割操作的准确性和稳定性;3. 训练切割操作人员,提高其技术水平和加工质量。
五、弯翘误差在钢筋加工过程中,如果筋材成品弯翘,将会给安装和施工带来困扰。
为了纠正弯翘误差,可以采取以下措施:1. 控制加热温度和时间,以保证钢筋的正常加工和冷却过程;2. 优化加工工艺,尽量减少弯翘的可能性;3. 对弯翘的钢筋进行二次加热和弯制处理,纠正其形状。
螺纹加工常见问题及解决方法
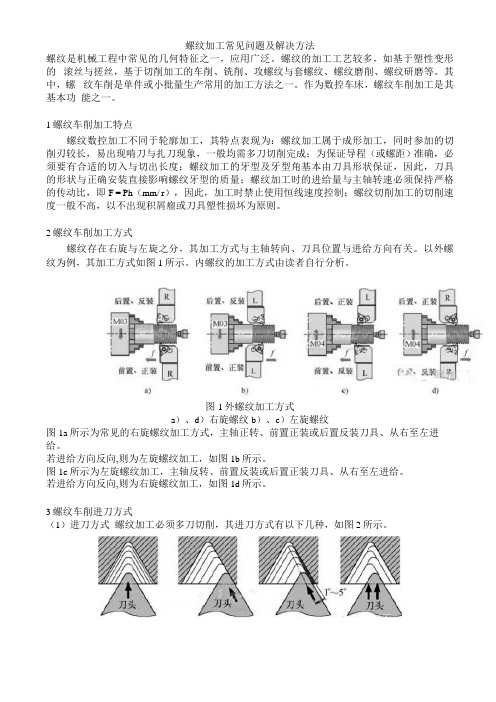
螺纹加工常见问题及解决方法螺纹是机械工程中常见的几何特征之一,应用广泛。
螺纹的加工工艺较多,如基于塑性变形的滚丝与搓丝,基于切削加工的车削、铣削、攻螺纹与套螺纹、螺纹磨削、螺纹研磨等。
其中,螺纹车削是单件或小批量生产常用的加工方法之一。
作为数控车床,螺纹车削加工是其基本功能之一。
1螺纹车削加工特点螺纹数控加工不同于轮廓加工,其特点表现为:螺纹加工属于成形加工,同时参加的切削刃较长,易出现啃刀与扎刀现象,一般均需多刀切削完成;为保证导程(或螺距)准确,必须要有合适的切入与切出长度;螺纹加工的牙型及牙型角基本由刀具形状保证,因此,刀具的形状与正确安装直接影响螺纹牙型的质量;螺纹加工时的进给量与主轴转速必须保持严格的传动比,即F = Ph(mm/ r),因此,加工时禁止使用恒线速度控制;螺纹切削加工的切削速度一般不高,以不出现积屑瘤或刀具塑性损坏为原则。
2螺纹车削加工方式螺纹存在右旋与左旋之分,其加工方式与主轴转向、刀具位置与进给方向有关。
以外螺纹为例,其加工方式如图1所示。
内螺纹的加工方式由读者自行分析。
图1外螺纹加工方式a)、d)右旋螺纹b)、c)左旋螺纹图1a所示为常见的右旋螺纹加工方式,主轴正转、前置正装或后置反装刀具、从右至左进给。
若进给方向反向,则为左旋螺纹加工,如图1b所示。
图1c所示为左旋螺纹加工,主轴反转、前置反装或后置正装刀具、从右至左进给。
若进给方向反向,则为右旋螺纹加工,如图1d所示。
3螺纹车削进刀方式(1)进刀方式螺纹加工必须多刀切削,其进刀方式有以下几种,如图2所示。
a)b)c)d)图2进刀方式a)径向进刀b)侧向进刀c)改进式侧向进刀d)左右侧交替进刀1)径向进刀(图2a)是基础的进给方式,编程简单,左、右切削刃后刀面磨损均匀,牙型与刀头的吻合度高;但切屑控制困难,可能产生振动,刀尖处负荷大且温度高。
适合于小螺距(导程)螺纹的加工以及螺纹的精加工。
2)侧向进刀(图2b)属较为基础的进刀方式,有专用的复合固定循环指令编程,可降低切削力,切屑排出控制方便;但由于纯单侧刃切削,左、右切削刃磨损不均匀,右侧后刀面磨损大。
螺纹加工时的疑难问题及解决办法
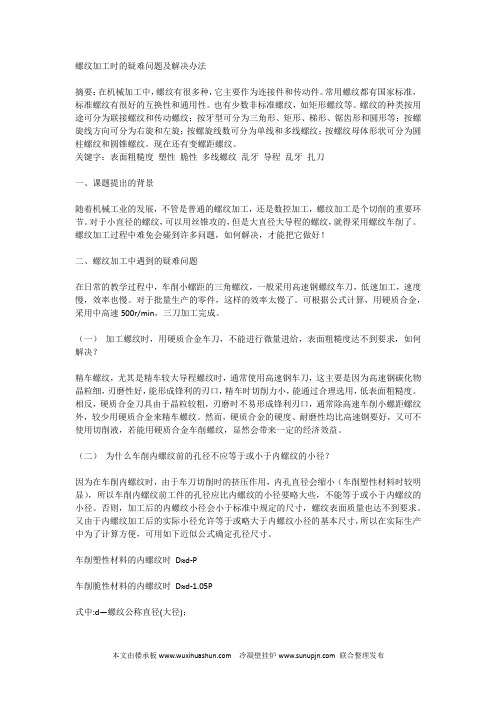
螺纹加工时的疑难问题及解决办法摘要:在机械加工中,螺纹有很多种,它主要作为连接件和传动件。
常用螺纹都有国家标准,标准螺纹有很好的互换性和通用性。
也有少数非标准螺纹,如矩形螺纹等。
螺纹的种类按用途可分为联接螺纹和传动螺纹;按牙型可分为三角形、矩形、梯形、锯齿形和圆形等;按螺旋线方向可分为右旋和左旋;按螺旋线数可分为单线和多线螺纹;按螺纹母体形状可分为圆柱螺纹和圆锥螺纹。
现在还有变螺距螺纹。
关键字:表面粗糙度塑性脆性多线螺纹乱牙导程乱牙扎刀一、课题提出的背景随着机械工业的发展,不管是普通的螺纹加工,还是数控加工,螺纹加工是个切削的重要环节。
对于小直径的螺纹,可以用丝锥攻的,但是大直径大导程的螺纹,就得采用螺纹车削了。
螺纹加工过程中难免会碰到许多问题,如何解决,才能把它做好!二、螺纹加工中遇到的疑难问题在日常的教学过程中,车削小螺距的三角螺纹,一般采用高速钢螺纹车刀,低速加工,速度慢,效率也慢。
对于批量生产的零件,这样的效率太慢了。
可根据公式计算,用硬质合金,采用中高速500r/min,三刀加工完成。
(一)加工螺纹时,用硬质合金车刀,不能进行微量进给,表面粗糙度达不到要求,如何解决?精车螺纹,尤其是精车较大导程螺纹时,通常使用高速钢车刀,这主要是因为高速钢碳化物晶粒细,刃磨性好,能形成锋利的刃口,精车时切削力小,能通过合理选用,低表面粗糙度。
相反,硬质合金刀具由于晶粒较粗,刃磨时不易形成锋利刃口,通常除高速车削小螺距螺纹外,较少用硬质合金来精车螺纹。
然而,硬质合金的硬度、耐磨性均比高速钢要好,又可不使用切削液,若能用硬质合金车削螺纹,显然会带来一定的经济效益。
(二)为什么车削内螺纹前的孔径不应等于或小于内螺纹的小径?因为在车削内螺纹时,由于车刀切削时的挤压作用,内孔直径会缩小(车削塑性材料时较明显),所以车削内螺纹前工件的孔径应比内螺纹的小径要略大些,不能等于或小于内螺纹的小径。
否则,加工后的内螺纹小径会小于标准中规定的尺寸,螺纹表面质量也达不到要求。
Φ18mm螺纹钢筋二线切分轧制工艺开发实践

第2 0卷 第 4期 2o 0 7年 7月
De eo me t& I n v t no c i ey & E e tia P o u t v lp n n o a o fMa hn r i lcr l rd cs c
机 电 产 品 开 发 与 新
文献标 识码 :A 文章编 号 :1 0 — 6 3 (0 7 4 0 5 0 0 2 6 7 2 0 )0 — 5 — 3
0 引言
∞ ∞ 加 ∞ 如 ∞ ∞ 加 m 0
所谓 的切 分 轧 制 。是 指 在 轧 制 过 程 中 利 用 轧 辊 孔
型 、导 卫装 置 中的切 分轮 或其 它 切分装 置 将 轧件 沿纵 向
的 实际情况 ,设 计 开发 了  ̄1mm 大规格 螺 纹钢 筋二 线切 分 轧 制 工 艺 ,对 切 分轧 制孔 型 系统和 8 导 卫装 置的选择 和 设计进 行 了较 为详 细 的分析 。
关 键 词 :切 分 轧 制 ;螺 纹 钢 筋 ; 孔 型 系 统 ; 导 卫 设 计
中图分 类 号 :T 3 5 G 3
损 严重 、产 品质 量不 稳定 等诸 多 问题 。本文 针 对 国 内某
1 2 3 4 5 6 7 8 9 1 l l l l l l 0 l 2 3 4 5 6
轧 制道 次
钢 铁厂棒 材 生产 线 的实际情 况 .对 切分 轧制 工 艺在 应用 过程 中的 问题进 行 了深入研 究 .为 了提 高 大规 格产 品 的 产 量 , 自行设 计 开发 了 1rm 大规 格 螺纹 钢 筋 新 产 品 8 a
切分 轧制 过程 中 的轧 机负 荷如 图 1 示 。 所
收稿 日期 :2 0 — 5 2 0 7 0 —9
我厂二切分轧制生产实践

我厂二切分轧制生产实践陈爱平卢平安钟海清杨世平何水金(新余钢铁有限责任公司棒材厂江西新余338001)摘要:本文主要介绍了我厂切分轧制工艺生产的过程及生产过程中出现的一些问题和改进效果。
关键词:二切分,轧制,生产,问题,改进效果1 前言新余钢铁有限责任公司棒材厂是一条年设计能力为40万吨的棒材半连续生产线,它是在利用现行可靠工艺技术和生产设备设施的基础上建成投产的。
原料:124方、130方、150方主要产品规格:螺纹钢:Φ12—36园钢:Φ16--Φ36其中:Φ12- Φ14螺纹钢轧制总量占20%左右。
由于Φ12- Φ14若单线生产产量太低,能耗高,机架数目多,场地受限,而采用切分轧制,产量可提高至少50%,且能耗低,机架数量少,因而决定Φ12- Φ14采用二切分轧制。
2 切分轧制工艺概述2.1 设备简介我厂是一条半连轧生产线,全线共布置13架水平轧机。
其中粗轧是一架530三辊开坯机,中轧为6架Φ400×4+Φ350×2闭式水平轧机,精轧为6架Φ300×6闭式水平轧机,K7-K2间均设立式活套,K1,K2间不起套。
Φ12,Φ14切分轧制均不甩机架,采用切分轮法。
精轧孔型使用如下:K6为菱形孔,K5为弧边方孔,K4为哑铃预切孔型,K2为椭圆孔,K1为成品孔。
2.2工艺平面布置图3 切分轧轧制生产情况3.1 生产准备3.1.1 车削预切分孔,切分孔轧辊车削精度要高,成品孔,成品前孔轧槽配辊两线间的中心距要保证。
3.1.2 导卫1)导卫安装首先要求检查导卫备件的质量,尺寸公差,表面质量是否符合工艺要求,禁止不合格品进行安装,导卫的开口度每架次用专用样棒进行安装与检测,确保导卫安装质量,即导卫的内腔尺寸,导轮的开口度尺寸符合要求。
2)K6出口DU65为带扭转的滚动导卫,K6轧件进K5孔能自动找正,K5进口导轮尺寸不要将K6轧件夹持很紧,K5出口CTR45度扭转。
3)K4轧件的形状控制对切分轧制的顺利很关键,2个亚铃形的面积要基本一样,防止切分不均匀,K4、K3进口为0930B四辊滚动导卫,导轮间距要合适,以防止料形发生扭转,K4出口为滑动导卫,滑动导板的头部一定要与亚铃形孔相吻合。
_18mm螺纹钢筋二线切分轧制工艺开发实践

1 切分轧制对轧机设备负荷的要求
由于 实 现 了 “一 切 二 ”, 采 用 切 分 轧 制 工 艺 后 , 生 产同一规格产品较单线相比道次变形量增加很大, 这就 必然要求现有设备轧机负荷足够大, 否则会出现轧机电机 跳闸或烧损轧辊轴承等事故。为了预测现实生产线中是否 能实现切分轧制, 必须根据现场的实际情况计算出轧机 的负荷。根据金属变形抗力模型 [3], 计算出材料的变形 抗力, 然后通过现场轧制参数表计算出各项轧制力能参 数 , 最 终 得 出 开 轧 温 度 为 1050℃时 , Φ18mm 螺 纹 钢 筋 切分轧制过程中的轧机负荷如图 1 所示。
轧孔型系统采用与其它产品共用的孔型系统, 以减少轧
辊数量、增大效率; 精轧孔型系统则采用专用的切分孔
型系统, 需
K6
K6
要精确计算
K5
K5
设计如图 3
所示。
K4
K4
这两种
K3
K3
孔型系统的
区别主要在
K2
K2
K6、K5 道 次
上。每种方
K1
K1
案都有各自
( a) 小规格产品孔型
( b) 大规格产品孔型
( 四川省有色冶金研究院, 四川 成都 610081)
摘 要: 棒材连轧生产线可应用切分轧制工艺实现提高产量、节约成本。本文结合某钢铁厂棒材生产线 的实际情况, 设计开发了 Φ18mm 大规格螺纹钢筋二线切分轧制工艺, 对切分轧制孔型系统和 导卫装置的选择和设计进行了较为详细的分析。
关键词: 切分轧制; 螺纹钢筋; 孔型系统; 导卫设计 中图分类号: TG335 文献标识码: A 文章编号: 1002- 6673 ( 2007) 04- 055- 03
- 1、下载文档前请自行甄别文档内容的完整性,平台不提供额外的编辑、内容补充、找答案等附加服务。
- 2、"仅部分预览"的文档,不可在线预览部分如存在完整性等问题,可反馈申请退款(可完整预览的文档不适用该条件!)。
- 3、如文档侵犯您的权益,请联系客服反馈,我们会尽快为您处理(人工客服工作时间:9:00-18:30)。
18螺切分轧制两线差问题的解决
摘要:针对两线轧制两线差问题进行了分析,提出了具体的改进措施和调整方法。
改进后,确保产品质量、定尺率、成材率均提高0.2%以上。
关键词:棒材;切分轧制;孔型设计;两线差。
一、概况
柳钢棒线型材厂一车间自18螺带肋钢筋实施两线切分轧制后,两线差最大长度差达300mm以上。
由于两线轧件在冷床的同一齿条中,冷床的1个动作周期
同时移动2根钢,在对齐辊道上,两线轧件的横筋相互咬合,因此轧件头部不易
对齐,如果强行对齐,会造成轧件弯曲,形成乱钢。
在定尺冷剪时,为了保证每
根轧件的剪成定尺,每手钢有一半必须多切300mm左右,造成剪切废品量增多,且非定尺量增多,剪切周期长。
另外,由于轧件在冷床上对不齐,因而产生较多
非定尺量,降低了定尺率、成材率,同时也给精整后区棒材的分选收集带来较大
难度,降低了精整后区的处理能力,制约了切分产量的提高,产品入库质量也难
以得到有效保障。
二、产生原因分析
对生产中存在两线差进行观察、分析得出:两线差与两线轧件尺寸差有一定的
对应关系。
在钢筋内径上下面尺寸相等情况下,纵筋尺寸较大的一线长度较长。
两线差即轧件切分成2根轧件后,两线金属断面积往往不同,有一定差值,主要
体现为两线轧件内径上下面尺寸相同情况下,纵筋尺寸有差别。
与传统单线轧制
相比,切分轧制调整的难点是要保证两线差尽可能小,而且要保持稳定。
两线差
越小,切分稳定性越高,两线成品尺寸精度越高,轧件两线也越易保持长短一致。
三、解决措施
1、解决切分轧制的两线差问题,首先是保障中轧来料稳定,在料型高度相
同的条件下,头中尾宽度尺寸相差不超过1mm,为稳定精轧两线轧件的尺寸差提供条件。
棒线型材厂一车间精轧切分孔型系统如图1所示。
其中15#轧机轧出的
料形为梅花方形,16#轧机的孔型为预切分孔,哑铃形,17#轧机将轧件切分成2线,切分后的轧件经双线活套器,在18#、19# 轧机进行轧制。
图1 精轧区轧机布置及切分孔型系统
对于两线差的调整控制,主要是针对15#、16#、18#轧机的料形及导卫装置。
15# 轧机轧出的料形很关键。
对15# 轧机的调整,要保证轧出标准的梅花方形,
斜面尽量小;如果料形不正,存在斜面或未充满现象,则在16# 轧机的预切分孔
中料形易发生扭转,导致轧件不易进入17#轧机切分孔,并影响16#轧机预切分
孔两线金属流量预分配的稳定性。
另外,轧件在15# 轧机前轧制时,要求微张力
尽量小,以防出现大头大尾现象,并且要尽量减少15# 轧机的轧制吨位,以确保
孔型形状。
2、16#轧机预切孔基本决定两线金属的流量,在调整中该孔要尽量充满,以
保证料形在孔型中的稳定性。
调整两线差主要是调整16# 轧机的入口导卫装置。
16#、17# 轧机入口导辊要确保扶正轧件,16# 轧机的入口导辊间距应比来料小0.3~0.5mm,17# 轧机的导辊间距要与来料相同或稍小。
16#、17# 轧机入口
导辊扶正轧件的原理同单线轧制有所不同,尤其是17#轧机进口.料形的两侧为
上一道次料形的宽展形成,不可作为导辊扶持轧件的基准面。
16# 、17# 轧机入
口导辊扶正轧件原理如图2所示。
为确保导辊能准确地扶正轧件,制作了16#、
17# 轧机入口导辊专用调整样棒,可精确调整导辊间距。
3、保证17#轧机两线料形高度一样。
18# 轧机轧出的两线轧件上下面尺寸不
一样时会形成两线差,造成双线活套两线轧件的高度差。
18# 轧机辊缝情况和
16#轧机预切情况形成一系列组合,直接决定双线活套两线的高度差,同时形成
两线的尺寸差。
18#轧机辊缝情况和16#轧机预切情况形成的组合较多,因此在换
辊换槽时,一定要保证18#轧机两线料形高度一样,以减少18# 轧机辊缝情况与
16# 轧机预切情况的组合次数,降低调整难度。
在过钢时,可通过观察双线活套
来判断轧件两线差的情况,并进行调整。
若双线活套波动较大,忽高忽低,说明15# 轧机料形不稳定,需调整15# 轧机辊缝、斜面及导辊松紧或调整堆拉钢关系。
在双线活套稳定情况下,可根据成品两线差结合两线套高差判断调整。
例如,在
南北两线轧件内径上下面尺寸相同情况下,假如南线纵筋大,则观察双线活套套
高差情况,若南线高,则调整16#轧机入口导辊,向北打至两线一样高;若南线低,18# 轧机压南线抬北线至两线一样高;假如两线一样高,则16#轧机入口导
辊向北整,同时调整18# 轧机南北辊缝,压南线、抬北线,套仍保持一样高。
按
上述要求调整好两线轧件尺寸后,有时仍会出现两线轧件头部不齐现象,这时可
采用以下3种方法进行调整:一是如果两线轧件上下面尺寸一样,纵筋尺寸相差
不大,可将19# 轧机微抬头部较长的一线,减少宽展量,降低前滑值,使轧件两
线的实际线速度保持一致。
二是如果头部长的一线纵筋或上下面尺寸已较大,再
抬头部较长的一线,会影响负偏差率的均衡,这时只能按调整两线差的方法,对16#轧机导卫装置进行调整,直至两线尺寸差达到允许范围内,再按方法一对轧
件两线头部的长短进行调整。
三是如果轧件头部两线交替长,是因为19#轧机入
口导辊松,或18#轧机轧出的料小,轧件在19#轧机入口导辊中来回摆动造成。
这时根据情况可更换成品导卫装置、调整18# 轧机辊缝。
如果引起双线活套的套
高差,还需调整16#轧机入口导卫,改变两线金属流量。
四、结束语
控制好切分轧件的两线差,解决了成品两线差的问题,实现轧件两线头部平齐,减少剪切量及非定尺,提高了成材率、定尺率;18螺带肋钢筋的成材率由原102.15%升至102.35%,定尺率由原98.2%升至98.5%;同时加快了定尺冷
剪节奏,方便精整后区的平台挑选,使精整的钢材处理能力得到加强,有利于切
分产量的进一步提高,提高了经济效益;产品入库质量也得到有效保障,减少质量
损失。
参考文献: 梁均;陈文勇;王小明;刘爱民.连轧厂两线切分轧制钢筋两线差问题的解决 [J].承钢技术,2006, 第2期。