二切分轧钢生产
轧钢切分工艺流程

轧钢切分工艺流程轧钢切分工艺是将钢板按照客户要求的尺寸进行切割的工艺过程。
本文将详细描述轧钢切分工艺流程的步骤和流程。
1. 准备工作在进行轧钢切分工艺之前,需要做一些准备工作,包括: - 检查设备:确保设备正常运转,刀片锋利。
- 检查原材料:检查钢板是否符合质量要求,排除瑕疵。
- 调整设备:根据要求调整设备的刀片间距、送料速度等参数。
2. 设定切割尺寸根据客户的要求和生产订单,设定切割尺寸。
通常情况下,可以通过计算机控制设备来设定切割尺寸,确保准确性和一致性。
3. 上料将原材料钢板放置在切割设备上,通常是在滚轮或切割平台上进行。
确保钢板平整、稳固,并进行固定,以避免在切割过程中产生误差。
4. 切割4.1 切割方式根据要求和设备类型,选择合适的切割方式。
常见的切割方式包括: - 刀片切割:使用钢刀片进行切割,可以通过水冷却刀片来降低温度。
- 激光切割:使用激光束进行切割,高精度高速。
- 火焰切割:使用火焰进行切割,适合厚板材。
4.2 切割操作根据设备的操作面板或计算机控制软件,进行切割操作。
按下切割按钮后,设备将自动进行切割,同时切割刀片或激光束将沿着预设的切割尺寸进行移动。
4.3 切割质量控制切割过程中需要对切割质量进行控制,确保切割尺寸的准确性和切割表面的质量。
常见的切割质量控制方法包括: - 视觉检测:使用相机或传感器进行实时的切割质量检测,如表面平整度、边缘质量等。
- 尺寸测量:使用测量仪器对切割尺寸进行检测,如激光测距仪、坐标测量机等。
5. 分料在切割完成后,将切割好的钢板进行分料。
根据客户要求和生产订单,将钢板按照指定的尺寸和数量进行分堆、码放,以便后续加工或发货。
6. 清理和保养切割完毕后,需要对设备进行清理和保养,以确保设备的正常运行和延长设备的使用寿命。
主要包括: - 清理钢板碎屑等杂物。
- 清理切割设备,如刃口、切割床、导轨等。
- 对刀片进行检查和磨削,保持刀片的锋利度。
棒材20螺2线切分轧制技术的开发与应用
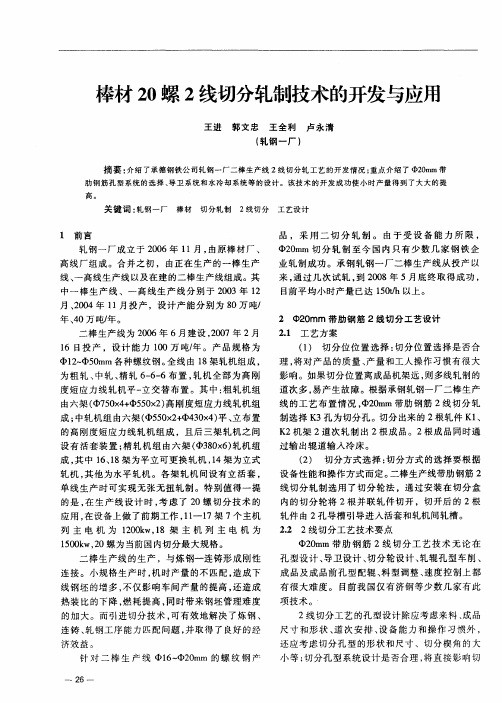
关键 词 : 轧钢一厂 棒材 切分轧制 2 线切分 工艺设计
பைடு நூலகம்1 前 言
品 ,采 用 二 切 分 轧 制 。 由 于 受 设 备 能 力 所 限 ,  ̄2 mm 切 分 轧 制 至 今 国 内 只有 少 数几 家 钢 铁 企 0 业 轧 制 成 功 。承 钢 轧 钢一 厂 二 棒 生产 线 从 投产 以
的高 刚 度短 应力 线 轧 机组 成 ,且后 三 架 轧机 之 间
设 有 活 套装 置 ; 轧机 组 由六 架 ( 8 x ) 机 组 精  ̄3 0 6 轧
道次多 , 易产 生故 障。根 据 承钢 轧钢 一厂 二棒 生产
线 的工 艺 布 置 情 况 , 0 m 带肋 钢 筋 2线 切 分 轧  ̄2 m 制 选 择 K3孔 为切 分 孔 。切 分 出来 的 2根 轧件 Kl 、 K 2机架 2道 次轧 制 出 2根 成 品 。2根成 品 同时通 过 输 出辊 道输 入 冷床 。 ( ) 切分 方 式选 择 : 分 方式 的选 择 要 根据 2 切 设 备 性 能 和操作 方 式而 定 。 二棒 生产线 带肋 钢筋 2 线 切分 轧制 选 用 了 切分 轮 法 ,通 过 安装 在 切 分 盒 内的切 分 轮 将 2根 并 联 轧 件切 开 ,切开 后 的 2根 轧件 由 2孔 导槽 引导进 入 活套 和轧 机 间轧槽 。 22 2线切 分 工艺 技 术要 点 .  ̄2 m 带 肋 钢 筋 2线 切 分 工 艺 技 术 无 论 在 0m
21 工艺 方 案 .
( ) 切 分 位 位 置选 择 : 分位 置选 择是 否 合 1 切 理 , 对 产 品的 质量 、 量 和工 人操 作 习惯 有 很 大 将 产
影 响 。如 果切 分 位 置离 成 品机架 远 , 多线 轧 制 的 则
Φ16mm热轧带肋钢筋两切分技术的开发与应用
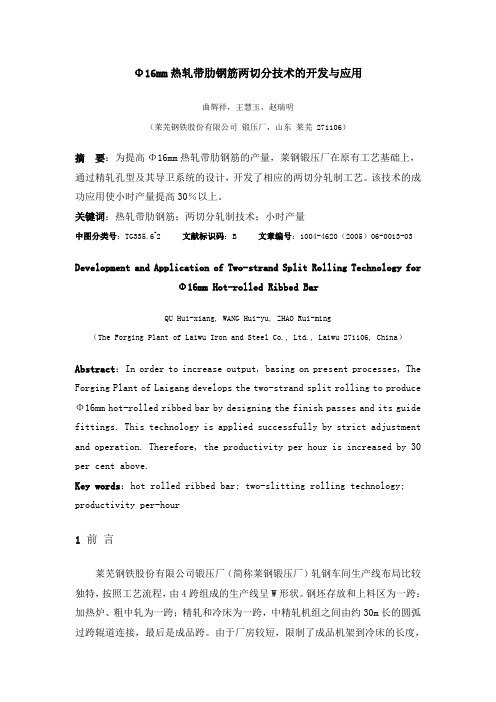
Φ16mm热轧带肋钢筋两切分技术的开发与应用曲辉祥,王慧玉,赵瑞明(莱芜钢铁股份有限公司锻压厂,山东莱芜 271106)摘要:为提高Φ16mm热轧带肋钢筋的产量,莱钢锻压厂在原有工艺基础上,通过精轧孔型及其导卫系统的设计,开发了相应的两切分轧制工艺。
该技术的成功应用使小时产量提高30%以上。
关键词:热轧带肋钢筋;两切分轧制技术;小时产量中图分类号:TG335.6+2 文献标识码:B 文章编号:1004-4620(2005)06-0013-03Development and Application of Two-strand Split Rolling Technology forΦ16mm Hot-rolled Ribbed BarQU Hui-xiang, WANG Hui-yu, ZHAO Rui-ming(The Forging Plant of Laiwu Iron and Steel Co., Ltd., Laiwu 271106, China)Abstract:In order to increase output, basing on present processes, The Forging Plant of Laigang develops the two-strand split rolling to produce Φ16mm hot-rolled ribbed bar by designing the finish passes and its guide fittings. This technology is applied successfully by strict adjustment and operation. Therefore, the productivity per hour is increased by 30 per cent above.Key words:hot rolled ribbed bar; two-slitting rolling technology; productivity per-hour1前言莱芜钢铁股份有限公司锻压厂(简称莱钢锻压厂)轧钢车间生产线布局比较独特,按照工艺流程,由4跨组成的生产线呈W形状。
Ф22mm规格热轧带肋钢筋二切分轧制生产实践
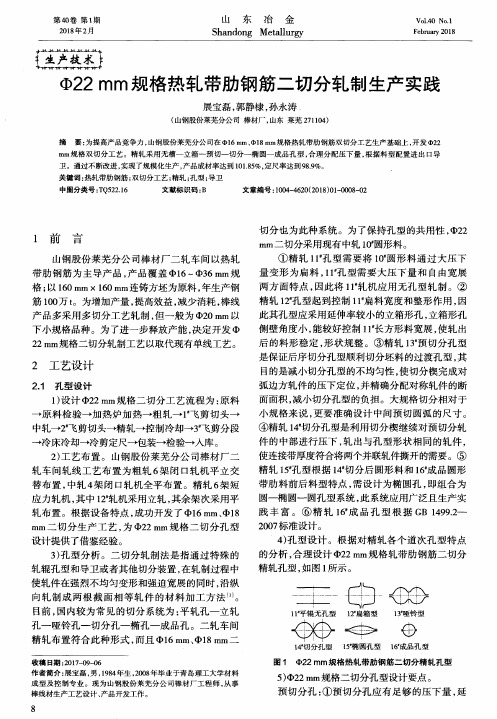
图 1 @22 mm 规 格 热 轧 带 肋 钢 筋 二 切 分 精 轧 孔 型
5)022 mm规 格 二切 分 孔 型设 计要 点 。 预切分孑L:①预切分孔应有足够 的压下量 ,延
8
展宝 磊等
022 mm规格热轧带肋钢筋二切分轧制生产实践
2018年第 1期
伸系数应 为 1.1~1.2;②强迫宽展 系数 为 1.1左右 , 使轧件得到较充分变形 ;③为减小切分楔尖所承受 的轧制力 ,预切分楔尖半径设计为 3.8 mm。
— , 1 —\
. ::
1 切 分 孔 型 l5 i圆孔 型 16 成 品孔 型
收稿 日期 :2017—09—06 作者简 介 :展宝磊 ,男 ,1984年 生 ,2008年毕业于青 岛理工大学材料 成型及 控制 专业 。现为 山钢股 份莱芜分 公司棒 材厂 工程师 ,从事 棒线 材生产工艺设计 、产品开发工作 。
展宝 磊 ,郭 静棣 ,孙永涛
(山钢股份莱 芜分公 司 棒材厂 ,山东 莱芜 27110 4 )
摘 要 :为提高产品竞争力 ,山钢股份莱芜分公 司在 016 mm、018 inm规格 热轧带肋钢筋双切分 工艺生产基础上 ,开发 022
mm规格 双切 分工艺 。精轧 采用无槽 一立 箱一预 切一切 分一椭 圆一 成品孔 型 ,合 理分 配压下 量 ,根 据料 型配置进 出 口导
2 工艺设计
切分也为此种 系统 。为了保持孑L型的共用性 ,022 mm--"切 分 采用 现有 中轧 10"圆形 料 。
①精 轧 1 l 孔型需要 将 10"圆形料 通过大压 下 量 变 形 为扁 料 ,l1 孔 型 需 要 大 压 下 量 和 自由 宽 展 两方面特点 ,因此将 l1 轧机应用无孑L型轧制 。② 精 轧 12"孔 型 起 到 控 制 1 1 扁 料 宽 度 和 整形 作 用 ,因 此其孔型应采用延伸率较小的立箱形孔 ,立箱形孔 侧壁角度小 ,能较好控制 11 长方形料宽展 ,使轧出 后 的料形稳定 ,形状规整 。③精轧 13 预切分孔 型 是保证后序切分孑L型顺利切分坯料的过渡孑L型 ,其 目的是减小切分孔型的不均匀性 ,使切分楔完成对
两线切分轧制技术在阳春新钢铁轧钢厂的应用
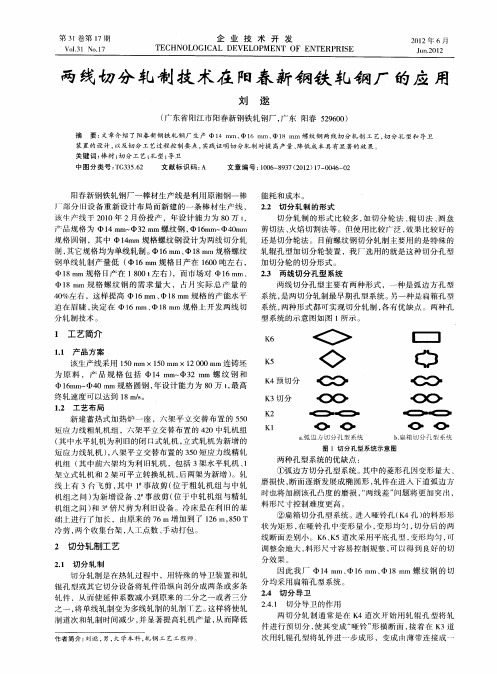
刀处易粘钢 , 从而导致堆钢事故的发生 , 其原因大部分是 前端靠近轧辊处有“ 鼻尖 ” 起引导作用 , 一对切分轮处于 因 为 导 卫 横 梁 标 高 问题 导 致 轧 件 与 导 卫 内 孔 壁 摩 擦 所 中间段 来 撕 开 轧件 , 分 轮后 有 一 把 切 分 刀 , 切 当切 分 轮 未 致 , 因此对导卫对中的安装提出了更高度 的要求 。
12 工 艺布 局 .
K5
◇
.: _ = .: 一 | _ =’ |
C= : l
. I c <
.==I.: . _ = 1 =: | 一| _
K 预切分 4 K 切分 3
K 2
新建蓄热式加热 炉一座 ,六架平立交替 布置 的 50 5 短 应 力线 粗 轧 机 组 ,六 架 平 立交 替 布 置 的 40中轧机 组 2
更 换 成 双通 道 过 渡导 槽 。
从切分道次( 3 出来 的两根并联 圆轧件之 间的连接 K) 3 实际生产控制措施 带 厚度 一 般 为 1m 楔 形 的切 分 轮 边缘 宽度 为 1 m, m, .m 5 而轧件最后是靠切分轮撕开 ,因此切分轮的角度与轧辊
孔 型切 分 楔 的 角度 必 须 严 格 配合 才 能 保 证撕 开 的正 常 完 成 。 型 切分 楔 角 须满 足 轧 件变 形 的要 求 , 切 分轮 的 角 孔 而 度 则直 接 对 能否 将 轧 件 “ 开 ” 切 分 导 卫 的寿 命 产 生 影 撕 及
将 轧件 彻 底撕 开时 , 可通 过 切 分 刀切 开 。 8 1H进 口为滑 动
⑥对于 1H出口扭转导卫扭转辊的角度易跑偏难 紧 8 导 卫 , 口为 R O O * 出 T — B 2型扭 转 导卫 。1H进 口为滚 动 导 固 的问 题 ,采 用 调 整好 角 度 后 再 直 接焊 接 死 的办 法来 得 9 卫 , 口为 方 形滑 动 导卫 。详 细情 况 如 表 1 示 。 出 所 到 了解 决 , 少 了堆 钢 事 故 的发 生 。 减 25 切 分 孔型 的 布 置 . ⑦针对机架及活套 间双通道导槽设计不合理导致频 切分孔型一般布置在精轧道次 ,结合我厂精轧机组 繁堆钢事故 的问题 ,通过优化导槽设计最终得到了很好 的布置形式 ,将 1#和 2#立式轧机 空过 ,7 6 0 1#和 1#平 的解 决 。 8 立可转换轧机全部水平使用 ,9 轧机为终轧道次。孔型 1# 4 效 果 在各 个 机 架 问 的布 置情 况 如 表 2 示 。 所 2 活套 的使 用 及 导槽 的改 进 . 6 自 2 1 年 6月份 开 始 , 步 在 中1 m 、 l m、 00 逐 6m 4m
敬业集团轧钢厂(一、二车间)概况
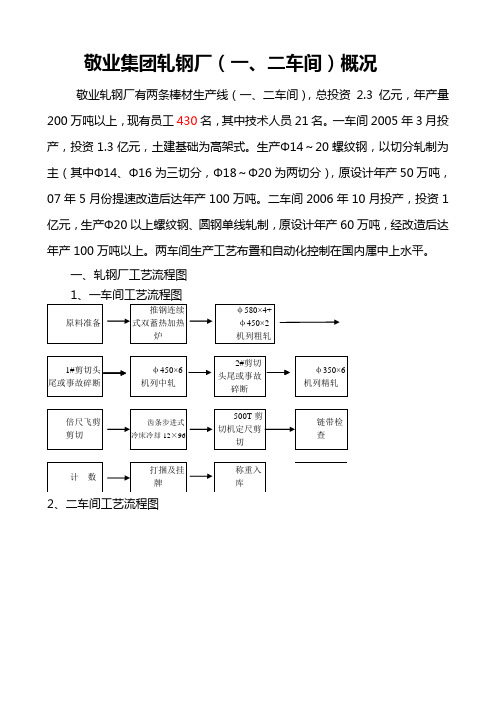
敬业集团轧钢厂(一、二车间)概况敬业轧钢厂有两条棒材生产线(一、二车间),总投资2.3亿元,年产量200万吨以上,现有员工430名,其中技术人员21名。
一车间2005年3月投产,投资1.3亿元,土建基础为高架式。
生产Φ14~20螺纹钢,以切分轧制为主(其中Φ14、Φ16为三切分,Φ18~Φ20为两切分),原设计年产50万吨,07年5月份提速改造后达年产100万吨。
二车间2006年10月投产,投资1亿元,生产Φ20以上螺纹钢、圆钢单线轧制,原设计年产60万吨,经改造后达年产100万吨以上。
两车间生产工艺布置和自动化控制在国内属中上水平。
一、轧钢厂工艺流程图2、二车间工艺流程图二、轧线主要工艺设备及性能:1、两车间加热炉均为端进侧出蓄热式加热炉,一车间加热炉有效尺寸为21 m ×10.6 m ,加热能力120t /h (冷坯),二车间加热炉有效尺寸为29m ×10.6 m ,加热能力150t /h (冷坯)。
燃料是本集团炼铁厂供应的副产品高炉煤气,坯料为150方×10米,由本集团炼钢厂热送。
蓄热式加热和钢坯热送热装两项技术在提高加热质量的同时,又具有显著的经济、节能、减排、环保特色。
2、主轧机:一车间轧机共18架,二车间轧机共16架,均为全平立交替布置。
两车间粗中轧轧机均为Ф580×4+Ф450×8二辊闭口式轧机,一车间精轧机为Ф350×6短应力线轧机,设有5个立活套,二车间精轧机为Ф350×4短应力线轧机,设有3个立活套。
平立交替和活套可实现无扭无张轧制。
3、飞剪:一车间共3台飞剪,1#剪、2#剪分别位于粗、中轧机组之后,用以切头尾或事故碎断,3#剪是倍尺飞剪,位于精轧机组之后;二车间共2台飞剪,1#剪位于粗轧8架之后,用以切头尾或事故碎断,2#剪是倍尺飞剪,位于精轧机组之后4、精整系统由冷床系统、冷剪定尺系统、分捡打捆包装系统及称重标识系统组成。
轧钢切分工艺流程

轧钢切分工艺流程轧钢切分工艺流程是钢铁生产中非常重要的一个环节,它的主要作用是将大块的钢材切割成所需的规格和尺寸,以满足不同客户的需求。
下面将详细介绍轧钢切分工艺流程。
一、原材料准备在轧钢切分工艺流程中,首先需要准备好原材料。
一般来说,原材料是钢板或钢卷,其厚度和宽度根据客户的要求而定。
在准备原材料的过程中,需要对其进行检查,确保其质量符合要求。
二、钢板切割钢板切割是轧钢切分工艺流程中的第一步。
在这一步中,需要将大块的钢板切割成所需的规格和尺寸。
切割的方式有多种,常见的有火焰切割、等离子切割和激光切割等。
不同的切割方式适用于不同的厚度和材质。
三、钢卷切割钢卷切割是轧钢切分工艺流程中的第二步。
在这一步中,需要将大块的钢卷切割成所需的规格和尺寸。
切割的方式有多种,常见的有剪切切割和卷曲切割等。
不同的切割方式适用于不同的厚度和材质。
四、边切割边切割是轧钢切分工艺流程中的第三步。
在这一步中,需要将钢板或钢卷的边缘进行切割,以去除不规则的边缘和毛刺。
这一步的目的是为了使钢材的边缘更加平整,以便后续的加工和使用。
五、定尺切割定尺切割是轧钢切分工艺流程中的第四步。
在这一步中,需要将钢板或钢卷按照客户的要求进行切割,以得到所需的长度和宽度。
这一步的目的是为了使钢材的尺寸更加精确,以满足客户的需求。
六、打标记打标记是轧钢切分工艺流程中的最后一步。
在这一步中,需要在钢材的表面打上标记,以标识钢材的规格、尺寸和批次等信息。
这一步的目的是为了方便后续的追溯和管理。
综上所述,轧钢切分工艺流程是一个非常重要的环节,它直接影响到钢材的质量和使用效果。
在进行轧钢切分工艺流程时,需要严格按照操作规程进行,确保每一步都符合要求,以得到高质量的钢材产品。
22螺两切分改造4页
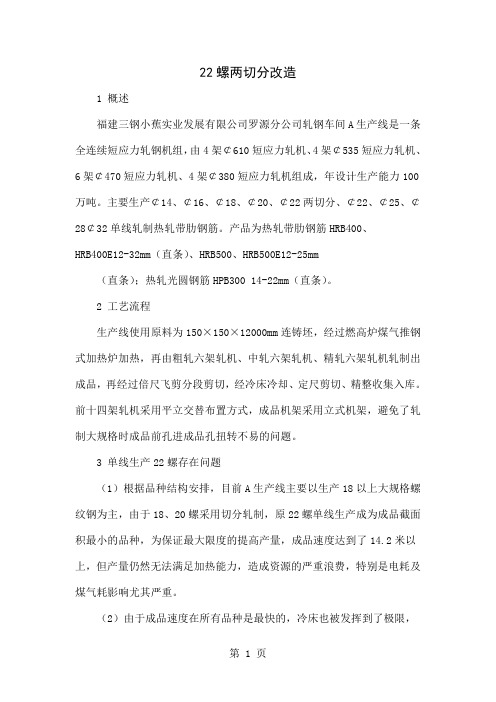
22螺两切分改造1 概述福建三钢小蕉实业发展有限公司罗源分公司轧钢车间A生产线是一条全连续短应力轧钢机组,由4架¢610短应力轧机、4架¢535短应力轧机、6架¢470短应力轧机、4架¢380短应力轧机组成,年设计生产能力100万吨。
主要生产¢14、¢16、¢18、¢20、¢22两切分、¢22、¢25、¢28¢32单线轧制热轧带肋钢筋。
产品为热轧带肋钢筋HRB400、HRB400E12-32mm(直条)、HRB500、HRB500E12-25mm(直条);热轧光圆钢筋HPB300 14-22mm(直条)。
2 工艺流程生产线使用原料为150×150×12000mm连铸坯,经过燃高炉煤气推钢式加热炉加热,再由粗轧六架轧机、中轧六架轧机、精轧六架轧机轧制出成品,再经过倍尺飞剪分段剪切,经冷床冷却、定尺剪切、精整收集入库。
前十四架轧机采用平立交替布置方式,成品机架采用立式机架,避免了轧制大规格时成品前孔进成品孔扭转不易的问题。
3 单线生产22螺存在问题(1)根据品种结构安排,目前A生产线主要以生产18以上大规格螺纹钢为主,由于18、20螺采用切分轧制,原22螺单线生产成为成品截面积最小的品种,为保证最大限度的提高产量,成品速度达到了14.2米以上,但产量仍然无法满足加热能力,造成资源的严重浪费,特别是电耗及煤气耗影响尤其严重。
(2)由于成品速度在所有品种是最快的,冷床也被发挥到了极限,造成冷床上钢故障是所有品种中最多的,严重制约了产能的提升,而成品在冷床停留的时间是最短的,又造成成品还没有完全冷却就到了定尺剪切,很容易造成成品的弯曲,既影响产品表面质量,又不利于负偏差的控制。
4 ¢22螺两切分设计思路(1)充分利用¢20螺两切分的工艺基础进行修改设计:1#用箱形孔、2-5#用平辊轧制,6#采用圆孔进行轧件的收尾,防止开花尾的产生,7-11#采用平辊轧制,取消12#,13、14#采用平辊轧制,15#预切,16#切分同,经过17、18#轧出成品。
- 1、下载文档前请自行甄别文档内容的完整性,平台不提供额外的编辑、内容补充、找答案等附加服务。
- 2、"仅部分预览"的文档,不可在线预览部分如存在完整性等问题,可反馈申请退款(可完整预览的文档不适用该条件!)。
- 3、如文档侵犯您的权益,请联系客服反馈,我们会尽快为您处理(人工客服工作时间:9:00-18:30)。
切分轧制生产实践
摘要:本文对轧厂切分轧制技术做了总结,对生产操作中孔型设计、导卫装置等做了详细分析,为提高产品的成材率及各种规格质量进行了深入探讨。
关键词:螺纹钢生产;二切分;轧制技术要求
1 前言
轧钢厂2002年引进的小型棒材轧机,对Ф12、Φ14、Φ16mm三种规格带肋钢筋采用二切分轧制,轧机小时产量达到70t,接近其它规格平均85t的水平,且与其它产品共用150mm方连铸坯,经Ф500×1/Ф400×2/Ф350×4/Ф300×6十三架轧机15道次轧出成品。
粗轧和中轧道次孔型具有共用性,缩短更换规格停机时间,提高了轧机作业率。
目前,轧厂φ16mm以下规格的建筑用带肋钢筋都采用切分工艺轧制,既保证了轧制小规格具备的条件,又保证了产品质量和产量,更好地满足市场的要求,取得了明显的经济效益。
2切分轧制技术特点
切分轧制是国家推广的新技术,也是今后发展方向。
据不完全统计,在小型棒材的产品中,直径小于φ16mm规格的钢筋约占总量的60%。
而棒材生产率随产品直径的减小而降低,因此要使各种规格产品的生产率基本相等,必须采用切分轧制,从而导致了棒材切分轧制技术的广泛应用。
切分轧制的技术关键在于切分设备的可靠性、孔型设计的合理性、切分后轧件形状的正确性以及产品质量的稳定性。
切分轧制具有以下明显的技术特点:
2.1 均衡不同规格产品的生产能力
使现有加热炉、轧机、冷床及其它辅助设备的生产能力有效利用和充分发挥。
因此,减少了厂房面积,减少了设备投资。
2.2 大幅度提高轧制小规格产品的机时产量
采用切分轧制由于缩短了轧件长度,从而缩短了轧制周期,提高了轧机生产率。
2.3 节约能源、降低成本
采用切分轧制变形量小,电机负荷分配均衡,电机效率趋于最佳状态,电量消耗趋于最低。
节约大量能源,且由于轧制成品长度减短,钢坯的出炉温度可适当降低。
但切分轧制也存在一些问题,主要表现在:棒材切分带容易产生毛刺,如调整不当有可能形成折叠,影响产品质量;对坯料的质量要求较严格,切分后坯料中心部位的缩孔、疏松等易暴露在轧件表面;对导卫、切分装置精度要求很高,在操作上应调整好进、出口导卫及切分轮间距,确保轧件对称地切分。
3切分工艺
3.1切分工艺布置
2×Ф12~16mm带肋钢筋产品的孔型系统如图1所示。
图1中k6、k5、k4、k3孔型分别为菱形、菱方、预切分、切分孔型。
该产品采用150mm方坯,轧制15道次。
粗轧孔型与中轧孔型具有共用性,精轧为切分孔型系统。
图1 2×Ф12—16mm带肋钢筋产品的孔型系统
3.2 轧辊孔型、导卫装置的控制
切分孔型在设计时应充分考虑轧机的弹跳,在预切分、切分孔型中要求并联轧件的连接带很薄,若弹跳值过大,则难以保证切分尺寸的要求。
同时,切分孔楔角应大于预切分的楔角,以保证楔子侧壁有足够的压下量和水平分力。
楔角一般取60°左右,楔子角度和顶部的设计要满足楔子头部耐冲击、抗磨损;在切分孔型中楔子尖部应高于辊面0.2mm左右,保证顶部不被冲坏。
在加工轧辊时,由于菱方孔、预切孔、切分孔形状复杂,车刀不易手工磨出,用数控线切割机加工成型刀具。
轧件在切分孔后被导卫分成两根,即最后两道次分开的轧件同时在两个轧槽中轧制,因此具有两个通道的导卫中心距与该两个轧槽中心距应很好的对正,导卫的制作安装要精确,且同时使用的两道轧槽的间距要准确。
为此在轧槽加工时,使用长跨样板,这样为导卫的调整创造了条件。
由于切分轧制主要是小规格产品,在轧槽加工时,还要保证轧辊上、下轧槽、孔型开口圆角的对称度。
上线前再进行轴向、径向的微调,以消除轴错等偏差。
轧制时,对于菱方孔要认真检查磨损情况,若该道次磨损不均、磨损严重要及时更换,防止轧件形状不对称、不正确,在经出口扭转导卫后不能以正确的角度进入预切孔,而产生堆钢。
该孔型的轧制量应限制在一定的范围内,轧到额定吨位时必须及时更换。
预切孔、切分孔因孔型较相似,都有楔角,由于强迫宽展,楔角顶部极易磨损,使得切分带厚度增大,从而增加切分刀片、切分轮的负荷,且因其受冲击较大易缺损,所以应及时换槽。
导卫方面要注意调整好K3出口切分导卫和K5出口扭转导卫。
切分导卫上、下切分轮间隙十分关键,过小、过大都易造成事故。
一般该间隙应控制在0.4mm左右。
扭转导卫的作用是将菱方形轧件扭转45°导入预切孔型,即导辊孔型,因此要保证扭转角度,否则会在K2—K3、K3—K4、K4--K5之间易产生堆钢,K5进口导卫要设计合理,以确保轧件能够轧出基本对称的菱方形状。
这三个导卫在使用时,还要注意观察切分轮、扭转辊的磨损情况及润滑、冷却状况,并要求及时调整更换。
3.3 轧件尺寸及活套的控制
由于切分轧制,轧件进入精轧后就进入切分的实质性阶段,因此精轧来料的尺寸应符合工艺技术要求。
通过调整K7轧机使轧件尺寸形状准确,保证轧件经扭转导卫以要求的角度进入预切孔。
预切孔、切分孔的辊缝值要及时调整以补偿孔型的磨损量,使切分带厚度控制在一定范围。
活套的控制要设置合适的高度,并通过前、后轧机速度的调整,消除张力,特别是当轧件切分开后,由于单支轧件断面变小,活套控制不当,易产生拉钢或堆钢,造成轧件长短不一,上冷床后难以齐头,甚至将会造成废品或事故。
当切分后的两支轧件起套高度相差较大时,应调整预切孔或切分孔的入口导卫(最好入口导卫横梁为可移动横梁,保证导卫在轧制过程中能够及时得到调整),
使轧件被均匀的切分,保证两根成品的尺寸满足标准要求。
4 需要注意的问题
采用切分轧制,切分孔道次由切分装置配合孔型最终分开两根并联轧件,如果工艺尺寸控制不当在轧件表面被切分部位将产生毛刺,影响成品表面质量;同时导卫在使用时易粘连氧化铁皮而导致生产事故。
并且因切分不均易造成两根轧件的尺寸偏差。
针对这些问题,必须在生产过程中严格控制工艺尺寸、及时调整、更换轧槽和导卫,才能保证良好的产品质量,提高轧机作业率,降低材料消耗。
5 结束语
棒材已成功地进行了二切分轧制生产,产品质量完全符合技术要求。