炼钢主要设备及其工艺参数
炼钢厂工艺技术操作规程
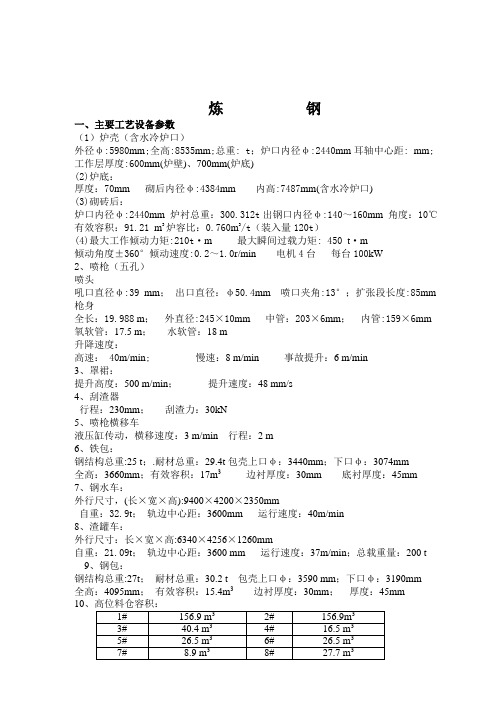
炼钢一、主要工艺设备参数(1)炉壳(含水冷炉口)外径φ:5980mm;全高:8535mm;总重: t;炉口内径φ:2440mm耳轴中心距: mm; 工作层厚度:600mm(炉壁)、700mm(炉底)(2)炉底:厚度:70mm砌后内径φ:4384mm内高:7487mm(含水冷炉口)(3)砌砖后:炉口内径φ:2440mm炉衬总重:300.312t出钢口内径φ:140~160mm角度:10℃有效容积:91.21 m3炉容比:0.760m3/t(装入量120t)(4)最大工作倾动力矩:210t·m 最大瞬间过载力矩: 450 t·m倾动角度±360°倾动速度:0.2~1.0r/min电机4台每台100kW2、喷枪(五孔)喷头吼口直径φ:39 mm;出口直径:φ50.4mm 喷口夹角:13°;扩张段长度:85mm枪身全长:19.988 m;外直径:245×10mm中管:203×6mm;内管:159×6mm氧软管:17.5 m;水软管:18 m升降速度:高速: 40m/min; 慢速:8 m/min 事故提升:6 m/min3、罩裙:提升高度:500 m/min;提升速度:48 mm/s4、刮渣器行程:230mm;刮渣力:30kN5、喷枪横移车液压缸传动,横移速度:3 m/min 行程:2 m6、铁包:钢结构总重:25 t;.耐材总重:29.4t包壳上口φ:3440mm;下口φ:3074mm全高:3660mm;有效容积:17m3边衬厚度:30mm 底衬厚度:45mm7、钢水车:外行尺寸,(长×宽×高):9400×4200×2350mm自重:32.9t;轨边中心距:3600mm 运行速度:40m/min8、渣罐车:外行尺寸:长×宽×高:6340×4256×1260mm自重:21.09t;轨边中心距:3600 mm 运行速度:37m/min;总载重量:200 t9、钢包:钢结构总重:27t;耐材总重:30.2 t 包壳上口φ:3590 mm;下口φ:3190mm全高:4095mm;有效容积:15.4m3边衬厚度:30mm;厚度:45mm1011二、常见钢种化学成分:(见后表)三、主要原材料技术条件:1、铁水入炉温度≥1280℃冶炼优质钢:入炉温度≥1300℃S≤0.030%;Si:0.40~0.60% 带渣量≤0.5% 无大块2、废钢废钢按分类装斗,数量准确,炉炉过秤特殊成分的废钢要单独存放废钢残余合金元素:Ni≯0.030%;Cr≯0.030%;Cu≯0.030% 铁块S≤0.070%注意:废钢中无封闭容器、爆炸物、耐火材料、泥砂、橡胶及有色金属,不得带水,不得有除铁或钢以外的杂物及油污。
炼钢工艺设备技术及工程施工要点
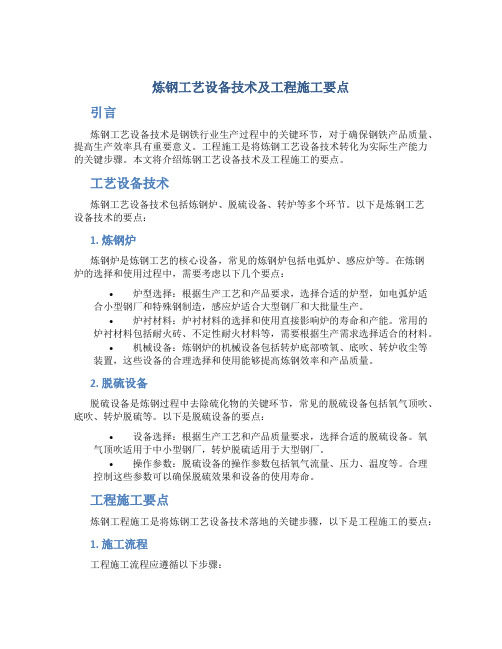
炼钢工艺设备技术及工程施工要点引言炼钢工艺设备技术是钢铁行业生产过程中的关键环节,对于确保钢铁产品质量、提高生产效率具有重要意义。
工程施工是将炼钢工艺设备技术转化为实际生产能力的关键步骤。
本文将介绍炼钢工艺设备技术及工程施工的要点。
工艺设备技术炼钢工艺设备技术包括炼钢炉、脱硫设备、转炉等多个环节。
以下是炼钢工艺设备技术的要点:1. 炼钢炉炼钢炉是炼钢工艺的核心设备,常见的炼钢炉包括电弧炉、感应炉等。
在炼钢炉的选择和使用过程中,需要考虑以下几个要点:•炉型选择:根据生产工艺和产品要求,选择合适的炉型,如电弧炉适合小型钢厂和特殊钢制造,感应炉适合大型钢厂和大批量生产。
•炉衬材料:炉衬材料的选择和使用直接影响炉的寿命和产能。
常用的炉衬材料包括耐火砖、不定性耐火材料等,需要根据生产需求选择适合的材料。
•机械设备:炼钢炉的机械设备包括转炉底部喷氧、底吹、转炉收尘等装置,这些设备的合理选择和使用能够提高炼钢效率和产品质量。
2. 脱硫设备脱硫设备是炼钢过程中去除硫化物的关键环节,常见的脱硫设备包括氧气顶吹、底吹、转炉脱硫等。
以下是脱硫设备的要点:•设备选择:根据生产工艺和产品质量要求,选择合适的脱硫设备。
氧气顶吹适用于中小型钢厂,转炉脱硫适用于大型钢厂。
•操作参数:脱硫设备的操作参数包括氧气流量、压力、温度等。
合理控制这些参数可以确保脱硫效果和设备的使用寿命。
工程施工要点炼钢工程施工是将炼钢工艺设备技术落地的关键步骤,以下是工程施工的要点:1. 施工流程工程施工流程应遵循以下步骤:•前期准备:制定详细的施工计划,安排人员、机械设备和材料的准备工作。
•施工准备:检查施工现场,确保施工材料、设备齐全,并按照工艺要求进行安装准备。
•设备安装:按照设备安装图纸和标准要求进行设备的安装和调试工作。
•系统联调:各个设备之间的管道、电气等系统进行联调和试运行。
•调试和验收:设备调试和试生产,确保设备正常运行和产品质量达标。
炼钢用电弧炉主要技术参数
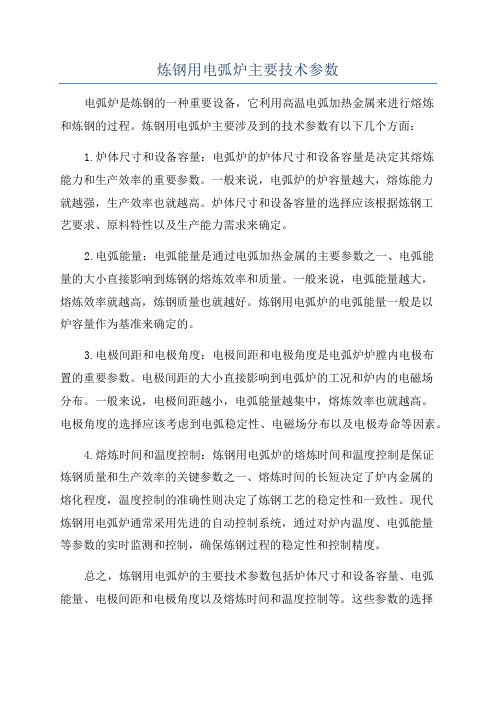
炼钢用电弧炉主要技术参数电弧炉是炼钢的一种重要设备,它利用高温电弧加热金属来进行熔炼和炼钢的过程。
炼钢用电弧炉主要涉及到的技术参数有以下几个方面:1.炉体尺寸和设备容量:电弧炉的炉体尺寸和设备容量是决定其熔炼能力和生产效率的重要参数。
一般来说,电弧炉的炉容量越大,熔炼能力就越强,生产效率也就越高。
炉体尺寸和设备容量的选择应该根据炼钢工艺要求、原料特性以及生产能力需求来确定。
2.电弧能量:电弧能量是通过电弧加热金属的主要参数之一、电弧能量的大小直接影响到炼钢的熔炼效率和质量。
一般来说,电弧能量越大,熔炼效率就越高,炼钢质量也就越好。
炼钢用电弧炉的电弧能量一般是以炉容量作为基准来确定的。
3.电极间距和电极角度:电极间距和电极角度是电弧炉炉膛内电极布置的重要参数。
电极间距的大小直接影响到电弧炉的工况和炉内的电磁场分布。
一般来说,电极间距越小,电弧能量越集中,熔炼效率也就越高。
电极角度的选择应该考虑到电弧稳定性、电磁场分布以及电极寿命等因素。
4.熔炼时间和温度控制:炼钢用电弧炉的熔炼时间和温度控制是保证炼钢质量和生产效率的关键参数之一、熔炼时间的长短决定了炉内金属的熔化程度,温度控制的准确性则决定了炼钢工艺的稳定性和一致性。
现代炼钢用电弧炉通常采用先进的自动控制系统,通过对炉内温度、电弧能量等参数的实时监测和控制,确保炼钢过程的稳定性和控制精度。
总之,炼钢用电弧炉的主要技术参数包括炉体尺寸和设备容量、电弧能量、电极间距和电极角度以及熔炼时间和温度控制等。
这些参数的选择和控制对于炼钢工艺的效果和产能都有重要影响,因此必须经过精心的设计和调整,以满足生产的要求和提高炼钢效率。
炼钢工艺知识
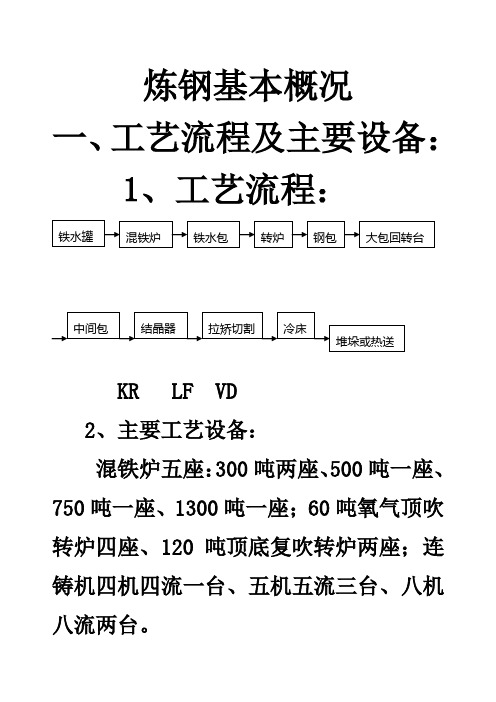
炼钢基本概况一、工艺流程及主要设备:1、工艺流程:KR LF VD2、主要工艺设备:混铁炉五座:300吨两座、500吨一座、750吨一座、1300吨一座;60吨氧气顶吹转炉四座、120吨顶底复吹转炉两座;连铸机四机四流一台、五机五流三台、八机八流两台。
炼钢主厂房内有炉渣跨、加料跨、转炉跨、过渡跨、连铸跨、精整跨、第二出坯跨、另有处理转运钢渣的渣跨。
3、主要产品及规格:钢坯断面mm:130×130 、150×150 、矩形坯165×225 、165×280 ;钢坯定尺:2.9-12m4、冶炼钢种:Q195、Q215、Q235、Q345B、HPB235、HRB335、HRB400、30MnSi、45钢H(hot rolled)表示热轧、R (ribbed)表示带肋、P(plain)表示光圆、B(bars)表示钢筋。
热轧带肋钢筋分为HRB335、HRB400、HRB500三个牌号,分别相当于Ⅱ、Ⅲ、Ⅳ级钢筋。
二.各工序的基本任务:1. 各工序的基本任务混铁炉:主要是将高炉供应的铁水均匀其成份和温度,并负责向冶炼连续供应铁水;转炉:将铁水、废钢等在一定的条件下冶炼成钢水;连铸:将钢水浇注成钢坯;精整:按照质量标准和用户要求将不合格品清除;码垛:按炉号标识将钢坯入库。
2.钢和铁的概念:钢:含碳小于 2.11%的铁碳合金。
其主要元素有C、Si、Mn、P、S。
铁:含碳大于 2.11%的铁碳合金。
并含有其它元素的可变形的铁碳合金。
3.炼钢的主要任务①脱碳:把转炉熔池中碳降至所炼钢种的要求;②去P和去S:P和S是钢中的有害元素,必须降低到规定的范围内。
③去除气体和非金属夹杂物:气体和非金属夹杂物对钢的性能有影响,必须降低到规定的范围之内;④脱氧合金化:脱氧是把钢中的氧降低到所需的水平,合金化是在脱氧的同时,根据所炼钢种加入各种合金,使元素达到规定范围。
⑤调整温度和成份。
三、原料1、主原料1)铁水:化学成份要求Si:0.6-1.25%、S≤0.070%、P≤0.150%铁水温度≥12500C,带渣量≤1%。
炼钢技术设备与工艺
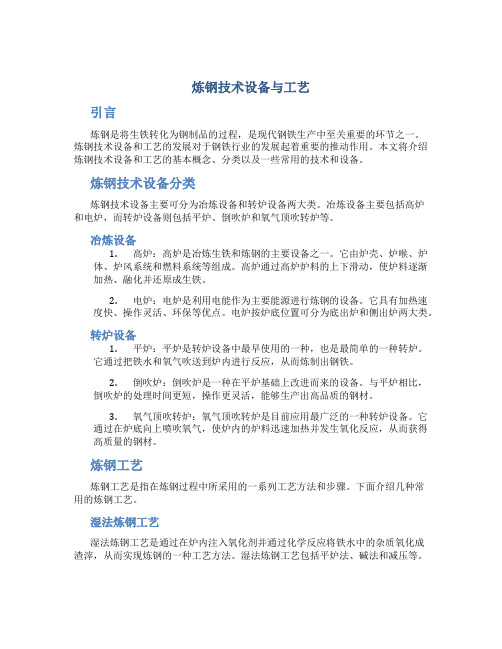
炼钢技术设备与工艺引言炼钢是将生铁转化为钢制品的过程,是现代钢铁生产中至关重要的环节之一。
炼钢技术设备和工艺的发展对于钢铁行业的发展起着重要的推动作用。
本文将介绍炼钢技术设备和工艺的基本概念、分类以及一些常用的技术和设备。
炼钢技术设备分类炼钢技术设备主要可分为冶炼设备和转炉设备两大类。
冶炼设备主要包括高炉和电炉,而转炉设备则包括平炉、倒吹炉和氧气顶吹转炉等。
冶炼设备1.高炉:高炉是冶炼生铁和炼钢的主要设备之一。
它由炉壳、炉喉、炉体、炉风系统和燃料系统等组成。
高炉通过高炉炉料的上下滑动,使炉料逐渐加热、融化并还原成生铁。
2.电炉:电炉是利用电能作为主要能源进行炼钢的设备。
它具有加热速度快、操作灵活、环保等优点。
电炉按炉底位置可分为底出炉和侧出炉两大类。
转炉设备1.平炉:平炉是转炉设备中最早使用的一种,也是最简单的一种转炉。
它通过把铁水和氧气吹送到炉内进行反应,从而炼制出钢铁。
2.倒吹炉:倒吹炉是一种在平炉基础上改进而来的设备。
与平炉相比,倒吹炉的处理时间更短,操作更灵活,能够生产出高品质的钢材。
3.氧气顶吹转炉:氧气顶吹转炉是目前应用最广泛的一种转炉设备。
它通过在炉底向上喷吹氧气,使炉内的炉料迅速加热并发生氧化反应,从而获得高质量的钢材。
炼钢工艺炼钢工艺是指在炼钢过程中所采用的一系列工艺方法和步骤。
下面介绍几种常用的炼钢工艺。
湿法炼钢工艺湿法炼钢工艺是通过在炉内注入氧化剂并通过化学反应将铁水中的杂质氧化成渣滓,从而实现炼钢的一种工艺方法。
湿法炼钢工艺包括平炉法、碱法和减压等。
干法炼钢工艺干法炼钢工艺是将冶炼过程中产生的炉渣与其他原料一起进行混合,并进行高温熔融,从而得到炼钢的一种工艺方法。
干法炼钢工艺主要有电弧炉法、感应炉法和气体炉法等。
碱碱熔炼法碱碱熔炼法是一种在炼钢过程中用碱性或碱性流体来操控反应平衡的工艺方法。
通过在炉内添加适量的碱性物质,可以减少炉内杂质的含量,从而得到高品质的钢材。
结论炼钢技术设备和工艺是钢铁生产中不可或缺的环节。
炼钢技术—设备与工艺
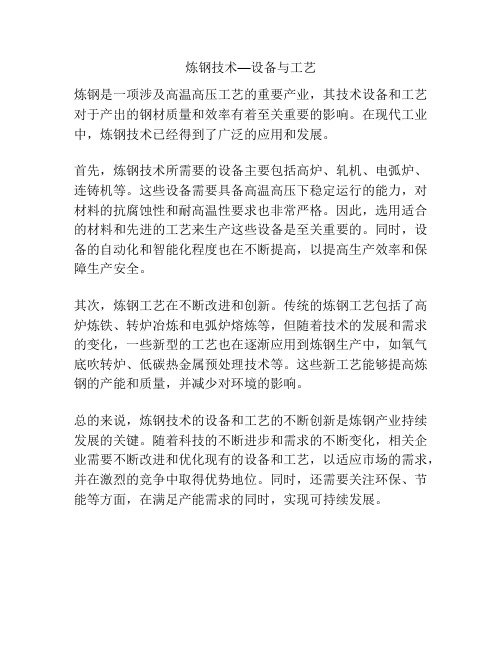
炼钢技术—设备与工艺
炼钢是一项涉及高温高压工艺的重要产业,其技术设备和工艺对于产出的钢材质量和效率有着至关重要的影响。
在现代工业中,炼钢技术已经得到了广泛的应用和发展。
首先,炼钢技术所需要的设备主要包括高炉、轧机、电弧炉、连铸机等。
这些设备需要具备高温高压下稳定运行的能力,对材料的抗腐蚀性和耐高温性要求也非常严格。
因此,选用适合的材料和先进的工艺来生产这些设备是至关重要的。
同时,设备的自动化和智能化程度也在不断提高,以提高生产效率和保障生产安全。
其次,炼钢工艺在不断改进和创新。
传统的炼钢工艺包括了高炉炼铁、转炉冶炼和电弧炉熔炼等,但随着技术的发展和需求的变化,一些新型的工艺也在逐渐应用到炼钢生产中,如氧气底吹转炉、低碳热金属预处理技术等。
这些新工艺能够提高炼钢的产能和质量,并减少对环境的影响。
总的来说,炼钢技术的设备和工艺的不断创新是炼钢产业持续发展的关键。
随着科技的不断进步和需求的不断变化,相关企业需要不断改进和优化现有的设备和工艺,以适应市场的需求,并在激烈的竞争中取得优势地位。
同时,还需要关注环保、节能等方面,在满足产能需求的同时,实现可持续发展。
炼钢-精炼工艺介绍
1、精炼过程用原料
1.4常用气体 1.4.1惰性气体 氮气、氩气等为冶金用惰性气体。主要用于二次钢水的保
护与隔离,以及对钢水精炼时的搅拌、吸气、去杂质等。 对人体的危害表现为窒息性伤害,浓度达到25g/m3时有危 险。 要求:干燥、干净、无杂质、水分<1%、纯度≥99.9%、 氧气<6PPm、氮气<20PPm、氧气+氮气≯20PPm 1.5钢包炉用材料 1.5.1冶金石灰: 采用转炉炼钢用活性石灰,保存期不得大于10天。
1.5.3埋弧渣:
化学指标 物理指标
CaO% 40~60
SiO2% 3~7
熔点(℃)
≥1320
杂质总和% ≤3.0
MgO% 4~10
Al2O3% ≤5
灼减(%)
≥35
粒度mm 10~50
S%
H2O%
≤0.1
≤1.0
粒度(mm)
≥3
1、精炼过程用原料
1.5.4电极
1#LF炉:Φ450mm高功率石墨电极(长度1800±100 mm)
转炉挡渣出钢 钢包内渣层过厚回对CAS处理带来不良影响:底吹排渣效
果差甚至无法裸露出钢液面,从而造成浸罩内残留渣量多 甚至无法进行CAS处理;成份调节时,合金元素收得率降 低;钢水脱氧效果差甚至出现钢水回鳞现象等。对于CAS 处理最好将钢包钢水顶渣厚度控制在≤50mm。
钢包渣改质
4、CAS工艺
求如何确定? 2、各类材料、介质等对钢水作用?在使用中应注意哪些事项?
2、钢包吹氩工艺
2.1钢包吹氩主要工艺参数 钢包吹氩应根据钢种性质、钢水状态、精炼目的,来选择合适
炼钢厂工艺流程与设备规格性能
炼钢厂工艺流程与设备规格性能一、炼钢厂工艺流程图二、炼钢厂示意图1、转炉示意图及工艺参数工艺参数转炉炉体1.1炉体总高(包括炉壳支撑板):7050mm1.2炉壳高度:6820mm1.3炉壳外径:Φ4370mm1.4高宽比: H/D=1.561.5炉壳内径:Φ4290mm1.6公称容量:50t1.7有效容积:39.5m31.8熔池直径: Φ3160mm1.9炉口内径:Φ1400mm1.10出钢口直径:140mm1.11出钢口倾角(与水平):20°1.12炉膛内径:Φ3160mm1.13炉容比:0.79m3 /t.s1.14熔池深度:1133mm1.15炉衬厚度:熔池:500mm 炉身:500mm 炉底:465mm 炉帽:550mm 1.16炉壳总重:77.6t1.17炉衬重量:120t1.18炉口结构:水冷炉口1.19炉帽结构:水冷炉帽1.20挡渣板结构:双层钢板焊接式1.21托圈结构:箱式结构(水冷耳轴)倾动装置型式:四点啮合全悬挂扭力杆式最大工作倾动力矩:100t*m最大事故倾动力矩:300t*m倾动角度:±360°倾动速度:0.2~1r/min二、方坯连铸示意图大包中包方坯弧形连铸机铸机基本参数:机型:全弧形铸机弧型半径:R6000/12000mm;机~流:5~5流间距:1250mm弯曲:连续弯曲矫直:连续矫直铸坯规格:120mm × 120mm;150mm × 150mm;100mm × 173mm;130mm × 173mm;拉速:120mm × 120mm 3.2~3.76 m/min;150mm × 150mm 2.0~3.0 m/min;100mm × 173mm; 2.8~3.4 m/min;130mm × 173mm; 2.0~3.0 m/min;冶金长度: 14.69 m(全凝固矫直);17.27 m(带液芯矫直)铸机长度:16.16m(铸机外弧基准线至固定挡板)定尺长度:3~6m铸机有效作业率:85%钢水收得率:96.8%设计年产量:80万吨/年三、板坯连铸大包中包结晶器板坯连铸机示意图铸机基本参数:机型:立弯式连铸机铸机弧型半径:6000mm;机~流:2~2流间距:4700mm弯曲:8点弯曲,R65000mm、R30600mm、R19300mm、R14000mm、R11000mm、R9000mm、R7200mm、R6000mm矫直:6点矫直,R6000mm、R7200mm、R9000mm、R11700mm、R16700mm、R31600mm 铸坯规格:150mm × 350~680mm;180mm × 350~680mm;200mm × 350~680mm;拉速:150mm × 350~680mm; V max:1.6 m/min; 180mm × 350~680mm; V max:1.5 m/min;200mm × 350~680mm; V max:1.2 m/min;冶金长度:17.43 m铸机长度:17.43 m定尺长度:6500m铸机有效作业率:82%钢水收得率:97%设计年产量:60万吨/年。
炼钢基础知识
二 、炼钢部分
石灰是炼钢主要造渣材料,具有脱硫 要影响。 因此,要求石灰CaO含量要高,SiO2含量和杂质含量要低,石 灰的生过烧率要低,活性度要高,并且要有适当的块度,此 外,石灰还应保证清洁、干燥和新鲜。 SiO2会降低石灰中有效(CaO)含量,降低石灰的有效脱硫能力。 石灰中杂质越多越降低它的使用效率,增加渣量,恶化转炉 技术经济指标。石灰的生烧率过高,说明石灰没有烧透,加 入熔池后必然继续完成焙烧过程,这样势必吸收熔池热量, 延长成渣时间;若过烧率高,说明石灰死烧,气孔率低,成 渣速度也很慢。 石灰的渣化速度是转炉炼钢过程成渣速度的关键,所以对炼 钢用石灰的活性度也要提出要求。石灰的活性度(水活性) 是石灰反应能力的标志,也是衡量石灰质量的重要参数。
二、炼钢部分
炼钢用原材料
炼钢用原材料分为主原料、辅原料和各种铁合金。氧气顶吹 转炉炼钢用主原料为铁水和废钢(生铁块)。炼钢用辅原料通 常指造渣剂(石灰、萤石、白云石、合成造渣剂)、冷却剂 (铁矿石、氧化铁皮、烧结矿、球团矿)、增碳剂以及氧气、 氮气、氩气等。炼钢常用铁合金有锰铁、硅铁、硅锰合金、硅 钙合金、金属铝等。
三、炼钢部分
氧化铁皮的作用
氧气顶吹转炉炼钢过程的热量有富余,因而根据热 平衡计算需加入适量的冷却剂,以准确地命中终点 温度。氧气顶吹转炉用冷却剂有废钢、生铁块、铁 矿石、氧化铁皮、球团矿、烧结矿、石灰石和生白 云石等,其中主要为废钢、铁矿石。 上述冷却剂的冷却效应从大到小排列顺序为:铁矿 石、氧化铁皮、球团矿、烧结矿、石灰石和生白云 石、废钢、生铁块。 转炉炼钢用氧化铁皮来自轧钢和连铸过程产生的氧 化壳层,其主要成分是氧化铁。因此,氧化铁皮可 改善熔渣流动性,也有利于脱磷,并且可以降温。
石灰的作用
炼钢厂设备简介
炼钢厂主体设备简介一、电炉区域本厂电炉炼钢主体设备为两台70吨高功率三相交流电弧炉,两座容量为3.5MVA变压器,设计年产量为100万吨,电炉本体采用偏心底(EBT)出钢技术,有效的控制了钢水的质量,炉壁采用分段式的水冷炉壁,大大提高了电弧炉的使用寿命,并且维修方便,效率高,大大降低了炉衬耐材成本,为了加强冶炼,缩短冶炼周期,采用了先进的炉内供氧系统,即每座炉配备了一支水冷液压机械手炉门氧枪,三支固定的炉壁氧枪,大大缩短了冶炼周期,从原来冶炼周期4小时左右,缩短到目前的1.5小时,电炉配备了一套喷碳粉系统,可以快速的造好泡沫渣,有效降低各类消耗,每台电炉各配置一套独立的上料系统,操作人员可以根据炉内情况,及时加入石灰,减轻了工人劳动强度。
二、精炼区域本厂精炼主体设备为一座70吨LF精炼炉,采用三相交流变压器,变压器容量为1MVA,双工位冶炼,采用水冷大炉盖和集心圆小炉盖(耐火材料),大大提高了炉盖使用寿命,并且炉盖更换方便,缩短维修时间,精炼配备了两台先进的喂丝机,提高了钢水质量,同时增加了精炼可以冶炼的钢种,提高经济效益,LF 精炼炉配备了钢包底吹氩气系统,均匀了钢水成分和温度,大大缩短了冶炼周期,提高了钢水质量,同时还配置了合金上料系统,合金回收率稳定,大大降低了工人劳动强度。
三、连铸区域本厂连铸机由武汉大西洋提供及安装两机两流R6.5m直弧型板坯连铸机。
其主要参数及性能:连铸机机型,链式引锭杆、直弧型;半径:6.5m(连续弯曲、连续矫直)、铸坯断面:180*(450~~700)m;铸坯定尺长度:6m。
水—气水二次冷却;平均拉速0.6~(1.2~1.4)M/min、最大拉速:1.8M/min;配置有涡流传感器液面检测、塞棒自动控制(伺服电动缸驱动);浇铸钢种:普碳钢:Q195、Q235、20#等,合金钢:20G、16Mn、45#等;平均连续炉数:16炉;收得率:99%;年作业率:85%;年产能力:合金钢:~70Wt、普钢:~100Wt。
- 1、下载文档前请自行甄别文档内容的完整性,平台不提供额外的编辑、内容补充、找答案等附加服务。
- 2、"仅部分预览"的文档,不可在线预览部分如存在完整性等问题,可反馈申请退款(可完整预览的文档不适用该条件!)。
- 3、如文档侵犯您的权益,请联系客服反馈,我们会尽快为您处理(人工客服工作时间:9:00-18:30)。
主要设备及其工艺参数混铁炉设备主要工艺参数公称容量: G 600t炉容铁量:G 526t熔池最大深度: h 3.122m炉体外形尺寸: L×B×H9545㎜×7897㎜×7520㎜炉壳重量: 113.475 t炉衬重量: 349t最大操作角度: +24.5°炉体向前倾动极限角度: + 47°炉体向后倾动极限角度:-5°炉顶燃烧温度: 1200℃铁水出炉温度: 1250℃转炉设备主要工艺参数:2.1 转炉炉体转炉公称容量: 60t炉体总高: 7000㎜炉壳高度: 6800㎜炉壳外径: 4700㎜炉壳内径: 4610㎜炉壳壁厚: 45㎜炉壳高度/炉壳外径: H/D=6800/4700=1.45炉膛内高/炉膛直径: H/D=6652/3480=1.91有效容积: 47 m3炉容比: V/t=0.78熔池深度: 900㎜炉口直径:Ф1440㎜出钢口直径:Ф125㎜出钢口与水平夹角: 10°炉衬厚度: 500㎜炉壳总重: 71000㎏炉衬总重: 153t(包括135.7t镁碳砖,17.3烧镁砖) 转炉净环冷却水:总给水量:70t/h 水压p≥0.3MPa T≤60℃2.2 托圈及倾动部分托圈结构:水冷箱型;托圈与炉壳间隙:100㎜,耳轴部位50㎜电机: 45KW×4台最大操作力矩:~1000N·m倾动转速: 0.1-1.22r/min倾动角度: ±360 °倾动减速机比:一次:98.821 二次:8.1176额定制动力矩: 1000N·m×42.3 氧枪系统a. 氧枪系统:氧枪总长度: 17.730m喷头:四孔拉瓦尔型枪直径Ф219㎜喉口Ф30.5㎜出口Ф39.5㎜马赫数 M=1.95 α= 11°50´~12°三层同心套管:内:Ф133㎜×5㎜中:Ф180㎜×5㎜外:Ф219㎜×7㎜供水压力>1.2MPa,进水温度≤35℃,出水温度≤50℃,供水量≥100t/h供氧压力: 0.7~0.9MPa氧枪总重: 2030㎏(包括枪内水量480㎏)b.提升机构提升能力: 55KW升降速度: V快=40m/min V慢=3.5m/min升降行程:工作行程:13900㎜c.横移装置:横移速度: 4m/min横移行程: 2500㎜连铸机设备主要设备工艺参数连铸机台数: 3台机型:2#机:四机四流R8m全弧形方坯连铸机3#机:五机五流R7m矩坯连铸机4#机:三机三流R6.5m直弧形板坯连铸机铸机流间距: 1.25m、 1.4m、 3.2m铸流断面: 2#机: 150×180 150×2203#机: 150×260 150×320 150×3304#机: 150×(330~650)中间包容量: 2#机: 18t 3#机:20t 4#机:25t引锭杆型式: 2#、3#机:钢性引锭杆 4#机:柔性引锭杆钢包转台:a) 钢包最大(单臂)承重:2#连铸机100t,3#连铸机90t,4#连铸机100tb) 钢包转台中心回转半径: 3.5 mc) 钢包回转速度: 1转/分中间包车:a) 行走速度: 2.9~13 m/minb)中间包车轨矩: 2#、3# 5670㎜ 4#6300㎜c)车长: 2#7600 ㎜、3#9200㎜、4#9800㎜结晶器振动装置:a) 型式:四连杆仿弧b) 振幅: 4~8㎜c)振动频率: 0~200次/min拉矫机:a) 型式: 2#、3#机双驱动五辊拉矫机4#机 7组拉矫机,4点矫直b) 辊子开口度: 2#、3#机最小106㎜,最大480㎜4#机 150㎜切割机:a) 型式:火焰切割b) 工作行程: 2#、3#机 2.1m,4#机4.65mc)切割速度: 0.3~0.4m/min4、 60t钢包尺寸包壳:上口2640㎜,下口2300㎜,全高3350㎜打结好钢包:上口2200㎜,下口1880㎜,内高2850㎜常用原材料基本技术要求(一)基本检测1、原材料计量入炉铁水必须经吊车电子秤称量。
入炉废钢或铁块必须经吊车电子秤称量。
入炉造渣剂必须经对应的称量斗称量后入炉。
炼钢用各种合金上料前必须对块度和化验成分进行检查核实,然后再经合金料仓磅称称量后,方可使用。
2、气体计量。
吹炼用氧必须经压力表,瞬时流量表及累计流量表计量方可使用,氧气压力及流量必须符合工艺要求。
转炉溅渣护炉用氮气必须经过压力表,气体压力流量必须符合工艺要求。
钢包吹氩必须经压力表、瞬时流量表及累计流量表计量。
每班要定时检查各种计量仪表,发现仪表故障、要停止吹炼,严禁各种气体无计量或计量表不全进行操作。
3、测温吹炼前应知道铁水温度(每班至少测两次)。
吹炼终点必须测温。
钢包吹氩前后必须测量温度。
4、枪位指示定期按工艺要求测量及调整氧枪标尺,以保证吹炼枪位准确。
5、化学分析冶炼前应知道铁水的化学成份,混铁炉内铁水成份至少每班分析两次。
吹炼终点必须取样分析、分析项目包括C、S、P(使用高锰铁块或有回炉钢时分析余Mn),出钢结束后必须取样分析和看脱氧。
终点炉渣成份每班分析两次,分析项目:CaO、MgO、SiO2 、FeO。
(二)主要原材料技术条件和标准1、铁水(1)铁水成份 GB/T717-1998牌号 L04 L08 L10化学成分 C ≥3.5Si0.3~0.6 ≤0.45>0.45~0.85 >0.85~1.25 一组≤0.40二组>0.40~1.00三组>1.00~2.00<特级≤0.100一级>0.100~0.15二级>0.150~0.250三级>0.250~0.400<特类≤0.020一类>0.020~0.030二类>0.030~0.050三类>0.050~0.070(2)高炉铁水温度≥1250℃。
(3)铁水带渣量应≤0.50%。
(4)入炉铁水必须符合工艺要求。
对于硫高的铁水,当硫含量小于0.090%时,可以兑入混铁炉进行成分中和,但不能连续兑入,间隔10包以上,一次兑入量不能超过200吨。
超出200吨的部分、间隔不够或S≥0.090%时做铸铁处理。
2、废钢根据GBT4221-1996要求入炉废钢符合以下规定:废钢尺寸及单重:废钢类型单重(Kg )外型尺寸(mm)重型废钢≯1000 <600×500×400中型废钢 30~100 <500×400×300小型废钢<30 <500×400×300钢屑冷压块比重≥2.5g/cm3<600×500×400轻型废钢打包块比重≥2.5g/cm3<600×500×400未压实或严重氧化的轻薄料不得使用。
废钢中不得有杂物、废耐火材料、封闭容器、爆炸物及有色金属。
废钢及铁块中磷、硫含量不得大于0.080%。
废钢中不得带水及冰雪入炉。
渣钢中含渣量不得大于15%(按体积估算)。
废钢中的易燃、易爆、毒品等不安全因素,经安全处理后方可入炉。
废钢必须清洁、干燥,无泥沙、油污、橡胶等。
3、铁合金及脱氧剂严禁不同牌号、类别的合金相混,铁合金粉屑必须经烘干袋装使用、每炉用量必须控制在总合金量的20%以内。
合金块度要求在30~60㎜,且应保持干燥、干净。
(1)硅铁合金的牌号及化学成份(GB2272—1987)牌号化学成份%Si Al Ca Mn Cr P S C范围不大于SiFe75-A 74~80 __ __ 0.4 0.3 0.035 0.02 0.1SiFe75-B 74~80 __ __ 0.4 0.3 0.04 0.02 0.1SiFe75-C 72~80 __ ___ 0.6 0.5 0.04 0.02 0.2(2)硅锰合金牌号及化学成份(GB/T4008—1996)牌号化学成份%PⅠⅡⅢ不大于%FeMn64si27 60~67 25~28 0.5 0.10 0.15 0.25 0.04.FeMn67si23 63~70 22~25 0.7 0.10 0.15 0.25 0.04FeMn68si22 65~72 20~23 1.2 0.10 0.15 0.25 0.04FeMn64si27 60~67 20~25 1.2 0.10 0.15 0.20 0.04(3)锰铁牌号及化学成份(GB/T3795—1996)牌号化学成份%Si PⅠⅡⅠⅡ不大于%FeMn78 75~82 7.5 1.0 2.0 0.3 0.50 0.03 FeMn74 70~77 7.5 1.0 2.0 0.4 0.50 0.03 FeMn68 65~72 7.0 1.0 2.5 0.4 0.60 0.03 FeMn64 60~67 7.0 1.0 2.5 0.5 0.60 0.03 (4)脱氧用铝(GB1196—83)牌号化学成份%Al Fe Si Cu不小于不大于Al98 98.0 1.1 1.0 0.05(5)脱氧用硅铝钡(YB/T066-1995)牌号化学成份%Si Al Ba C P SFeAL30Ba6Si20 ≥20≥30≥6≥0.2≤0.02≤0.05FeAL26Ba9Si25 ≥25≥26≥9≥0.2≤0.02≤0.05FeAL16Ba12Si32 ≥32≥16≥12≥0.2≤0.02≤0.05FeAL12Ba15Si35 ≥35≥12≥15≥0.2≤0.02≤0.05用量为1.0~1.5kg/t。
增[Si]量为0.026~0.030%。
块度为30~50mm。
(6)增碳剂(执行GB3070—1982)C S 灰份挥发份水份粒度>95% <0.50% <0.80% <2.5% <0.5% 2~6mm4、造渣材料(1)白云石执行ZBD52002—90成份级别 MgO% CaO% SiO2 块度一级品≥19≥29≤2 5~20mm二级品≥19≥29≤3.5 5~20mm三级品≥18≥29≤4 5~20mm四级品≥16≥29≤5 5~20mm(2)冶金石灰技术条件执行YB/T042-2004类别化学成份(%)活性度指标 CaO CaO+MgO MgO SiO2 P S CO2 灼减品级不小于不大于不小于普通石灰特级品 92.0 —< 1.5 0.01 0.025 360一级品 90.0 — 2.5 0.02 0.10 5 300二级品 85.0 — 3.5 0.03 0.15 7 250三级品 80.0 5.0 0.04 0.20 9 180 高镁石灰特级品— 93.0 ≥ 1.5 0.01 0.025 260一级品— 91.0 2.5 0.02 0.10 6 280二级品- 86.0 3.5 0.03 0.15 8 230三级品 81.0 5.0 0.04 0.20 10 180 石灰块度30~60mm,小于30mm的粉粒不超过15%,应保持干燥,不得混入杂物,雨天运输时应有防雨措施,石灰存放,冬季不超过4天,夏季不超过2天。