波兰2250mm热带钢轧机生产线简介
2250mm热轧水处理系统简介

太钢2250mm热轧水处理系统简介摘要:太钢2250mm热轧水处理系统主要包括加热炉冷却水系统、主电室马达通风、液压站润滑系统、空调等设备的冷却水系统;带钢层流冷却水系统、轧线的直接冷却水和冲氧化铁皮水系统、污泥处理系统。
关键词:水处理冷却循环水系统污泥处理加热炉及间接冷却循环水系统(A系统)一、加热炉却循环水系统:1、加热炉冷却循环水系统工艺主要供加热炉冷却使用,一期冷却水量为600 m3/h二期冷却水量为800 m3/h,使用后的水仅水温升高。
工艺流程如下:●加热炉冷却使用后的水自流进热水池,经提升泵(P103泵组)加压一部分进过滤器过滤,再余压上冷却塔冷却,然后进入冷水池;一部分直接进入冷却塔冷却,然后进冷水池,再用水泵(P101泵组)加压供加热炉冷却使用。
●加热炉的安全供水采用柴油机泵和安全水塔联合供水的方式。
在加热炉给水管道上设置1座200m3的安全水塔,事故发生时安全水塔可保证供给加热炉前15分钟用量的冷却水,同启动柴油机泵,●在整个系统的正常运行过程中,由于冷却塔的飞溅、蒸发,以及系统排污,造成系统的水量减少,需要不定时的向系统按比例补充除盐水和工业新水。
加热炉冷却水工艺流程图:2、加热炉冷却循环水系统主要设备:3、加热炉冷却循环水系统系统控制:3.1加热炉供水泵:●运行方式:2用1备●操作方式:正常时手动启动、停止水泵,当工作泵故障停止时,自动启动备用泵。
3.2加热炉安全供水泵:●操作方式:正常情况下根据自动连锁条件启动或手动启动,停止时手动操作完成●自动连锁条件:加热炉冷却水供水压力3分钟平均值低于0.48 MPa;或停电时,自动启动柴油机泵。
●水泵停止操作由操作人员根据现场情况(当电源恢复正常供电或运行泵运行正常时)手动停止3.3加热炉供水管道过滤器●机电一体化设备,自动运行。
●管道过滤器运行和故障信号远传。
3.4加热炉冷却塔:●操作方式:由操作者手动控制运行或停止。
●自动连锁条件:当风机振动开关动作时,风机自动停止并报警。
轧钢主设备

由于连铸机改变连铸板坯宽度的能力较小,不能满足热轧带钢轧机的各种宽度规格,由粗轧机的立辊根据热轧带钢轧机需要的各种宽度规格的板坯宽度进行控制。热轧带钢轧机发展了立辊轧机,定宽压力机等形式的板坯宽度侧压设备。
5、精轧机组
精轧机组是成品轧机,布置在粗轧机组中间辊道或热卷箱的后面,是带钢热连轧线的核心设备。精轧是决定产品质量的主要工序,带钢的力学性能主要取决于精轧机终轧温度和卷取温度。
2国内的情况
1978年12月投产的武汉钢铁公司1700mm热连轧机计算机系统,是我国引进的第一套带钢热连轧计算机控制系统热带轧机。1989年宝钢2050mm热连轧机的建成投产,使我国热轧宽带钢轧机的生产技术和技术装备又上了一个新的高度。
3带钢热连轧生产工艺流程
原料准备→称重→加热→除鳞→定宽→粗轧→(调头尾)→保温(补热)→剪头尾→除鳞→精轧→层流冷却→卷取→热轧卷(检查、打捆、喷印、包装) →平整→热轧卷→精整→纵切→窄带钢→横切→钢板→酸洗→酸洗卷
四我国热连轧带钢生产采用的先进技术与特色技术
目前国内的热轧宽带钢轧机约有4类,其特色分别如下:
1传统热轧宽带钢轧机
(1)连铸坯热装和直接热装。该技术要求炼钢和连铸机稳定生产无缺陷板坯;热轧车间最好和连铸机直接连接,以缩短传送时间;在输送辊道上加设保温罩及在板坯库中设保温坑;板坯库中要具有相应的热防护措施,以保证板坯温度。应设有定宽压力机,减少板坯宽度种类。加热炉采用长行程装料机,以便于冷坯与热坯交换时可将高温坯装入炉内深处,缩短加热时间。精轧机后2机架采用轧辊轴向串动技术,以增加同宽度带钢轧制量。采用连铸、炼钢、轧钢生产计划的计算机一体化管理系统,以保证物流匹配。
第3阶段,这个阶段实际上是近1~2年开始的,是以提高效益、调整品种结构、满足市场需要和提高企业竞争能力为目的的发展阶段。由于近年国家经济快速发展,对钢材需求不断增加,因此除国营大中型企业外,中小型企业,甚至民营企业都把生产宽带钢作为今后发展的重点,或引进或采用国产技术,或建设传统热连轧宽带钢轧机或建设薄板坯连铸连轧生产线。这个阶段以鞍钢1700mm、2150mm(国产),唐钢1780mm薄板坯和1700mm(国产)、马钢1700mm薄板坯和2250mm、涟钢1700mm薄板坯、莱钢1500mm(国产)、本钢薄板坯、济钢1700mm(国产)、新丰1700mm(国产)、宝钢1800mm、首钢2250mm、武钢2250mm、太钢2250mm轧机为代表。同时,这个阶段对引进的二手轧机和原技术较落后的国产轧机进行了全面技术改造,使其达到了现代化水平。
包钢新体系2250mm热轧过程控制系统的应用与研究

包钢新体系2250mm热轧过程控制系统的应用与研究作者:张晓琳王磊来源:《科技视界》2014年第02期【摘要】作为计算机技术在冶金行业的最成功应用案例,包钢新体系热轧2250产线完整的采用了日本TMEIC公司的过程控制系统,系统控制范围覆盖整条产线的动作,包括除鳞,定宽,粗轧,精轧,层冷和卷取等工序,实现了高效,精确的板带轧制,从而降低生产管理成本,提高产品的竞争力。
【关键词】2250热轧;轧机;过程控制系统;PASolution通常在冶金生产过程的分层结构中,按照功能大体可以分为4级,即传动级,基础自动化级,过程控制级和生产控制级。
过程控制在结构中主要关注生产过程中的控制。
利用高速网络实现控制的实时性,数学模型和模型自学习实现控制的准确性。
1 系统简介包钢新体系2250热轧生产线采用的日本TMEIC公司的过程控制系统,整个系统主要包括非控和模型两个部分。
非控部分主要包括了对轧线现场各种传感器数据的采集,提供准确的模型计算时刻,及时地把模型计算结果传送给轧线设备。
控制部分主要是根据基础自动化级发送的现场数据和来自加热炉的PDI数据。
在规定的时刻进行模型计算,并进行自学习。
2 PASlution平台介绍PASolution是美国GE公司开发的中间件平台,TMEIC公司为适应现代工业自动化过程控制系统而开发的中间件。
开发人员利用它可以完成过程控制系统的通信、数据采集、物料跟踪、进程管理、报警及日志等所有功能开发,为系统开发提供了便利的组态化开发平台,为系统维护提供了人性化的维护环境。
PASolution在包钢新体系2250mm热连轧机过程控制系统开发过程中使用,为TMEIC轧机二级控制系统提供强大的支撑平台。
2.1 IO_service,功能是为系统中的各个进程之间提供信息通讯机制,通讯的内容包括事件和数据,其特点在于可以跨计算机跨系统平台无缝连接各进程,使各进程高效准确的进行协作工作。
功能类似西门子的CORBA通讯中间件subsys实现的进程间通信。
本钢2300mm热轧生产线定宽机轧制板坯侧弯原因分析及解决方法

本钢 2300mm热轧生产线定宽机轧制板坯侧弯原因分析及解决方法摘要:本钢建立了2300mm热轧生产线,提高了产品附加值和生产能力。
但是,该生产线中,定宽机使用时任意出现轧制板坯侧弯问题,本文就该问题进行分析,首先阐述了轧制板坯侧弯机理,其次对其原因进行分析,并提出了相应解决方法,充分发挥生产线作用。
关键词:热轧生产线;定宽机;轧制板坯侧弯引言本钢2300mm热轧生产线装备有德国西马克专利技术的定宽压力机。
该定宽机相对于常规立辊轧机而言,具有减宽量大、轧制所产生边部变形(狗骨)较小及轧制的板坯头尾变形小等优点,但是在本钢2300mm热轧生产线定宽机使用过程中多次出现定宽机轧制后板坯严重侧弯,影响生产稳定。
所以,本文以本钢2300mm热轧生产线定宽压力机为研究对象,对定宽机轧制过程中板坯侧弯产生的原因进行分析,并提出了针对本钢2300mm热轧生产线定宽轧制板坯侧弯问题的解决方法。
1.定宽机轧制板坯侧弯的机理定宽机在对板坯轧制过程中,板坯金属发生塑性变形:厚度方向上由于受锤头的摩擦阻力及上下导向辊的压紧力,变形很小,只在边部隆起形成“狗骨”状;而在板坯轧制方向上阻力较小,所以板坯经定宽机轧制减宽后主要沿长度方向伸长。
板坯在伸长过程中发生了板型侧弯,实质上就是板坯两侧的金属在长度方向上的变形不均匀。
在正常轧制过程中,板坯两侧的变形理论上应该是对称的,影响对称变形的因素主要有两方面:一是板坯两侧温度不均匀,使板坯两侧金属塑性变形抗力大小不同,导致板坯两侧金属变形量不同,最终造成板坯在总体上的侧弯;二是,定宽机两侧锤头对板坯的压下不对称,同样会导致板坯两侧金属变形量不同,造成板坯侧弯[1]。
2.本钢2300mm热轧生产线定宽机板坯侧弯原因分析及解决方法2.1通过对本钢2300mm热轧生产线定宽机轧制板坯温度测量,板坯两侧温度均匀,确定板坯温差不是本钢定宽机侧弯产生的原因,所以本文不再对温度引起的板坯侧弯进行进一步讨论。
毕业论文2150F2精轧机主传动系统设计说明

2150F2精轧机主传动系统设计摘要本次毕业设计的设计对象是2150F2精轧机主传动系统。
轧钢机主传动系统主要由电动机、减速器、齿轮座、连接轴以与联轴节等组成。
对于2150精轧机来说,其轧制要求有较高的精度,板型要有较高的平整度,就要对轧机的各个部件进行精准的设计。
该论文主要以轧机的主传动为主题展开,对轧机主传动的设计就要求对于涉与到传动件的各个部件如电动机、减速器、齿轮座、连接轴、联轴器等进行设计计算,需要对轧机的轧制力、传动力矩和传动功率进行计算,对主电机容量进行选择,对设计好的主减速机的齿轮、轴以与联接轴进行强度校核,直到满足要求。
本文通过几次反复的计算已满足要求。
设计好轧机的尺寸结构以后需要对润滑方式的进行选择,并对轧机的经济性、环保性进行评估。
当各个方面都满足时才是一个合格的设计。
关键词:主传动;设计;校核;减速机;润滑;环保The Design Of The Main Driver Of 2150F2Finishing millABSTRACTThe design of this graduation project is the main drive structure of 2150F2finishing mill. The main drive system of a rolling mill is mainly composed of an electric motor,a reduced, a gear seat,a connecting shaft and a coupling. For the 2150 finishing mill,its rollingrequirements have higher precision,the flatness of the plate must be higher, so it is necessary to carry out precisedesign of each part of the rolling mill.This paper mainly to themaindrive for the theme, design of the m ain drive requires eachcomponent to involvetransmission parts suchas motor, reducer, gear seat and a connecting shaft, coupling des ign and calculation, calculation of rolling force of rolling mill, the required driving torque andthetransmissionpower, the selection of the main thecapacity of motor, reducer design ofthe gear shaft and the connecting shaft and check the strength ,until the meet therequirem ents. After designing the size structure of rolling mill, it is necessary to select the lubrication mode, and evaluate the economi c and environmental protection of the rolling mill. When all aspe cts are satisfied, it is a qualified design.Key words: main drive; design; check; reducer;lubrication; environ mental protection目录摘要IABSTRACTII1 绪论 01.1 轧钢生产的国外发展概况01.2 热带钢连轧机的现状与发展趋势11.3 实习厂情况介绍21.3.1 生产主要设备21.3.2 产品品种21.3.3 本热轧带钢的生产工艺流程22 方案设计52.1 对2150F2精轧机主传动方案进行综合评价与比较 (5)2.1.1 概述52.1.2 方案评价与比较52.2 确定合理的主传动设计方案62.2.1 确定方案62.2.2 轧钢机主传动装置各部分的作用和类型63 主电机容量的选择103.1 轧制力计算103.1.1 设计参数103.1.2 轧辊基本尺寸103.1.3 变形阻力的计算113.1.4 平均单位压力的计算123.1.5 轧制力的计算133.2 传动力矩和传动功率的计算133.2.1 传动力矩133.2.2 电机功率的计算143.3 主电机容量的选择153.3.1 选择电动机容量153.3.2 电机容量校核154 主要零部件强度计算174.1 主减速机齿轮强度的计算 (17)4.1.1 齿轮材料、热处理方式、精度等级和齿数174.1.2 按齿面接触疲劳强度设计174.1.3 按齿根弯曲疲劳强度设计194.1.4 确定齿轮几何尺寸224.1.5 齿根弯曲疲劳强度校核224.2 主减速机轴的强度计算244.2.1 按扭转强度条件初估轴径244.2.2 按弯扭合成强度校核轴的强度245 联接轴计算295.1 相关尺寸295.2 开口式扁头受力分析和强度计算295.3 叉头受力分析和强度计算305.4 万向接轴的许用应力 (31)5.5 轴体切应力的计算 (31)5.6 轴体的许用切应力 (31)6 润滑方式的选择327 安装、试车规程的制定337.1 安装规程的制定337.1.1 轧机安装的工艺流程图337.1.2 施工准备347.1.3 基础验收347.1.4 基准线和基准点设置347.1.5 垫板设置347.2 试车规程的制定357.2.1试车准备357.2.3 安全措施358 环保性与经济性分析378.1 环保性分析378.2 经济性分析37结束语40致41参考文献421 绪论1.1 轧钢生产的国外发展概况中国轧钢生产水平与世界主要生产钢的发达国家比较,技术还相对落后很多。
邯钢2250mm热轧厂提高成材率的研究与应用
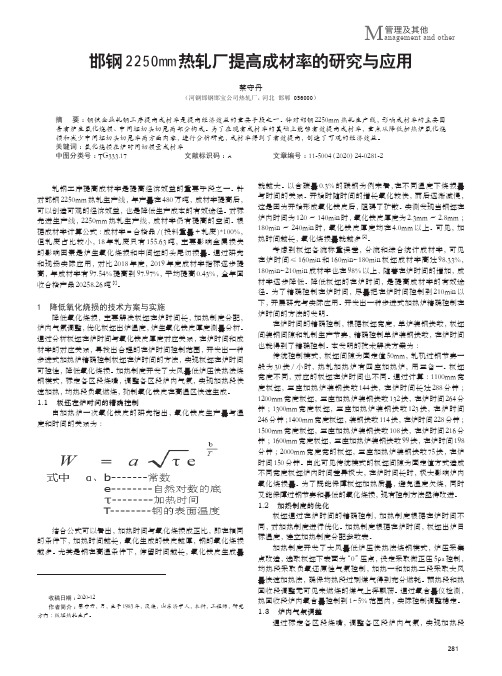
281管理及其他M anagement and other邯钢2250mm 热轧厂提高成材率的研究与应用蔡守丹(河钢邯钢邯宝公司热轧厂,河北 邯郸 056000)摘 要:钢铁企业轧钢工序提高成材率是提高经济效益的重要手段之一。
针对邯钢2250mm 热轧生产线,影响成材率的主要因素有炉生氧化烧损、中间坯切头切尾两部分构成。
为了在现有成材率的基础上能够有效提高成材率,重点从降低加热炉氧化烧损和减少中间坯切头切尾率两方面内容,进行分析研究,成材率得到了有效提高,创造了可观的经济效益。
关键词:氧化烧损在炉时间切损量成材率中图分类号:TG333.17 文献标识码:A 文章编号:11-5004(2020)24-0281-2 收稿日期:2020-12作者简介:蔡守丹,男,生于1983年,汉族,山东济宁人,本科,工程师,研究方向:板坯热轧生产。
轧钢工序提高成材率是提高经济效益的重要手段之一。
针对邯钢2250mm 热轧生产线,年产量在480万吨,成材率提高后,可以创造可观的经济效益,也是降低生产成本的有效途径。
对标先进生产线,2250mm 热轧生产线,成材率仍有提高的空间。
根据成材率计算公式:成材率=合格品/(投料重量+轧废)*100%,但轧废占比较小,18年轧废只有155.63吨,主要影响金属损失的影响因素是炉生氧化烧损和中间坯的头尾切损量。
通过研究和现场实际应用,对比2018年度,2019年度成材率指标逐步提高,年成材率有97.54%提高到97.97%,平均提高0.43%,全年回收合格产品20258.26吨[1]。
1 降低氧化烧损的技术方案与实施降低氧化烧损,主要解决板坯在炉时间长,加热制度分配,炉内气氛调整,优化板坯出炉温度,炉生氧化铁皮厚度测量分析。
通过分析板坯在炉时间与氧化铁皮厚度对应关系,在炉时间和成材率的对应关系,寻找出合理的在炉时间控制范围,开发出一种步进式加热炉精确控制板坯在炉时间的方法,实现板坯在炉时间可控性,降低氧化烧损。
最新冷轧带钢生产线简介
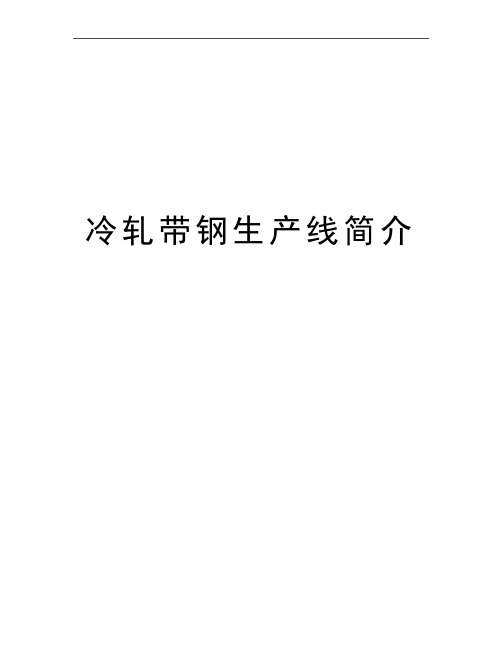
冷轧带钢生产线简介生产线简介冷轧带钢生产线是带材的主要成品工序,所生产的冷轧薄板属于高附加值钢材品种,是汽车、建筑、家电、食品等行业不可缺少的金属材料。
我公司承接的冷轧生产线工程主要包括:六辊可逆冷轧机组、六辊冷连轧机组、四辊可逆冷轧机组、四辊冷连轧机组、二十辊可逆冷轧机组。
典型案例例1型号1450 六辊可逆轧机规格原料:厚度 1.5~ 4.5mm ,宽度: 700~ 1300mm 卷重: 26t;成品:厚度 0.2~ 1.0mm ,宽度: 700~ 1300mm;产品厚度公差:± 0.005mm (δ 0.5mm 以下产品)± 1% δ(δ0.5mm 以上产品)参数最大速度: 1000m /min;轧制力: 18000KN;最大轧制力矩: 150KN.M;装机功率:10500KW;厚度自动控制;工作辊正负弯辊;中间辊正弯辊,并串动;分段冷却;油气润滑。
特点投资少、占地小、生产品种管理灵活,备件管理方便,产量适中;产品板形和厚差好,品种多样;设备运行稳定;操作方便;作业率高。
技术特点1、主轧机、开卷机和机前机后卷取机采用全数字直流调速,可控硅供电。
机组PLC控制。
2、全液压压下,计算机厚度自动控制(AGC)。
液压AGC系统采用两级计算机控制,不仅具有恒辊缝,恒轧制力,厚度监控功能并且具有张力AGC等。
3、轧机具有压下调偏、工作辊正/负弯辊、中间辊正弯辊控制手段;中间辊横移预设定和分段冷却等板形控制手段。
大轧制力、大轧制力矩、大张力轧制等手段有效保证厚差可控。
4、开卷机具有CPC自动对中功能。
卷取机自动卷齐(EPC)准确停车、圈数记忆、带尾自动减速停车。
5、工作辊、中间辊快速换辊。
6、轧机电气系统具有过载保护,断带保护和紧急停车等安全保护系统;主机和卷取机具有带尾自动减速、准确停车功能;圈数记忆功能。
7、轧机速度控制;开卷、卷取机速度/张力控制,数字显示。
8、轧制线标高自动、快速调整。
邯钢2250mm热轧生产线轧制节奏的分析及优化
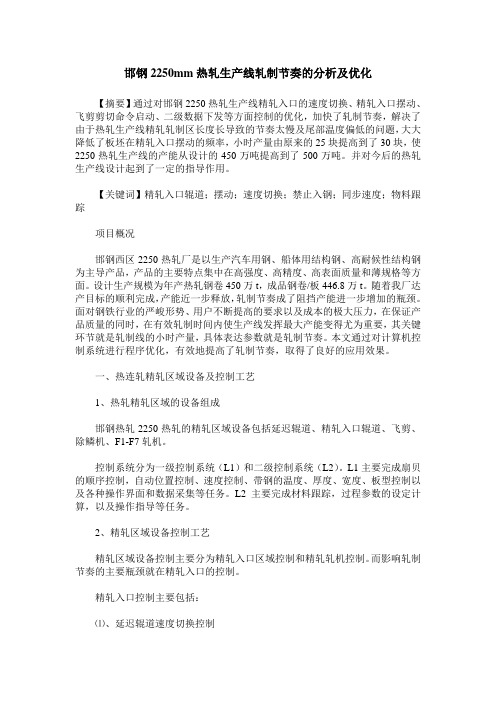
邯钢2250mm热轧生产线轧制节奏的分析及优化【摘要】通过对邯钢2250热轧生产线精轧入口的速度切换、精轧入口摆动、飞剪剪切命令启动、二级数据下发等方面控制的优化,加快了轧制节奏,解决了由于热轧生产线精轧轧制区长度长导致的节奏太慢及尾部温度偏低的问题,大大降低了板坯在精轧入口摆动的频率,小时产量由原来的25块提高到了30块,使2250热轧生产线的产能从设计的450万吨提高到了500万吨。
并对今后的热轧生产线设计起到了一定的指导作用。
【关键词】精轧入口辊道;摆动;速度切换;禁止入钢;同步速度;物料跟踪项目概况邯钢西区2250热轧厂是以生产汽车用钢、船体用结构钢、高耐候性结构钢为主导产品,产品的主要特点集中在高强度、高精度、高表面质量和薄规格等方面。
设计生产规模为年产热轧钢卷450万t,成品钢卷/板446.8万t。
随着我厂达产目标的顺利完成,产能近一步释放,轧制节奏成了阻挡产能进一步增加的瓶颈。
面对钢铁行业的严峻形势、用户不断提高的要求以及成本的极大压力,在保证产品质量的同时,在有效轧制时间内使生产线发挥最大产能变得尤为重要,其关键环节就是轧制线的小时产量,具体表达参数就是轧制节奏。
本文通过对计算机控制系统进行程序优化,有效地提高了轧制节奏,取得了良好的应用效果。
一、热连轧精轧区域设备及控制工艺1、热轧精轧区域的设备组成邯钢热轧2250热轧的精轧区域设备包括延迟辊道、精轧入口辊道、飞剪、除鳞机、F1-F7轧机。
控制系统分为一级控制系统(L1)和二级控制系统(L2)。
L1主要完成扇贝的顺序控制,自动位置控制、速度控制、带钢的温度、厚度、宽度、板型控制以及各种操作界面和数据采集等任务。
L2主要完成材料跟踪,过程参数的设定计算,以及操作指导等任务。
2、精轧区域设备控制工艺精轧区域设备控制主要分为精轧入口区域控制和精轧轧机控制。
而影响轧制节奏的主要瓶颈就在精轧入口的控制。
精轧入口控制主要包括:⑴、延迟辊道速度切换控制⑵、精轧入口速度控制⑶、精轧入口摆动控制⑷、精轧入口前后两块板坯距离控制⑸、精轧区域二级数据下发控制⑹、飞剪的剪切控制当板坯从R2轧制完最后一道次,进入精轧区域,首先延迟辊道以6米/秒的速度将板坯传送到飞剪入口,到达EE23HMD 时速度切换为1.1米/秒的切头部速度,切头完成后,速度切换为精轧机速度进入精轧机轧制。
- 1、下载文档前请自行甄别文档内容的完整性,平台不提供额外的编辑、内容补充、找答案等附加服务。
- 2、"仅部分预览"的文档,不可在线预览部分如存在完整性等问题,可反馈申请退款(可完整预览的文档不适用该条件!)。
- 3、如文档侵犯您的权益,请联系客服反馈,我们会尽快为您处理(人工客服工作时间:9:00-18:30)。
1 波兰2250mm热带钢轧机生产线简介 波兰Mittal 钢铁公司2250 mm 热带钢轧机生产线一期为一座步进加热炉、一架带立辊的四辊粗轧机、保温罩、转鼓式飞剪、F1-F6 六架四辊精轧机、层流冷却装置、两台卷取机。将厚度为220 mm 和250 mm、宽度为750 mm~2100 mm、长度为12 m 的板坯轧制成成品厚度为1.2 mm~25.4 mm、宽度为750 mm~2100 mm 的带钢。最大钢卷重量35 t,最大单位宽度钢卷重21.6 kg /mm。主要生产钢种为结构钢、API 管线钢( X70、X80 )、汽车用钢种( DP、TRIP)、HSLA 钢、硅钢( GO、GNO )、奥氏体和铁素体不锈钢。其生产能力为每年240 万吨。二期工程增加一台加热炉、第七架四辊精轧机( F7 )、一台卷取机,生产线年产量将达450万吨。
2 波兰2250mm热带钢轧机生产工艺流程 该轧线的主要设备有: 步进式加热炉,粗轧除鳞箱,E1 立辊轧机,R1 四辊粗轧机,保温罩,转鼓式飞剪,精轧除鳞箱,F1~F6 精轧机,层流冷却装置,卷取机。轧线工艺布置简图如图1 所示。
1—加热炉2—粗轧除鳞箱3—E1 立辊轧机4—R1 四辊粗轧机5—保温罩6—转鼓式飞剪7—精轧除鳞箱8—F1 ~ F6 精轧机9—层流冷却装置10—卷取机 图1 波兰2 250 mm 热带钢轧机生产线工艺布置图
3 轧线主要设备技术参数、结构特点 3.1 加热炉 轧线设有1 台步进式加热炉,加热炉全长62m,加热板坯能力450t/h,出钢最高温度1250℃,具有先进的炉子优化和控制系统。
3.2 高压水除鳞装置 高压水除鳞装置的主要技术参数见表1。波兰2250 mm 热带钢轧机全线共3 处除鳞点,分别是位于加热炉后的粗轧除鳞箱、R1 四辊粗轧机前后高压水除鳞装置和精轧机组前的精轧除鳞箱。粗轧除鳞箱用于清除板坯上的炉生氧化铁皮。在除鳞箱的罩子内,前后布置了两对集管,上集管高度可调,下集管为固定式,布置了带整流子的高压喷嘴。R1 四辊粗轧机入出口分别布置有两对除鳞集管,用于清除粗轧中间坯的二次氧化铁皮。精轧除鳞箱用于除去轧件表面在粗轧过程中形成的二次氧化铁皮,以保证带钢表面质量,在除鳞箱内布置有两对除鳞集管。在精轧除鳞箱入出口处安装有上下两个夹送辊,上夹送辊由液压缸控制进行开口度调整,出现事故时,可用液压缸的作用力,将带钢从精轧机组中拉出。除鳞采用先进的低压供水高压除鳞系统,可消除除鳞时由于突然输入高压水而产生非常不利的水锤现象,延长设备的使用寿命。这些除鳞措施不仅能减少轧辊不均匀磨损、减少停机换辊次数、提高轧机台时利用率,还能有效地提高热轧带钢表面质量,为后续深加工产品表面质量提供保证。
表1 高压水除鳞装置主要技术参数 3.3 E1 立辊轧机
表2 E1 立辊轧机主要技术参数 E1 立辊轧机位于R1 四辊粗轧机入口,与R1四辊粗轧机紧凑布置,主要用于控制中间坯宽度和形状,同时将板坯的边部由铸态组织变为轧态组织,避免在水平轧制中边裂。E1 立辊轧机机架采用整体铸造结构,在机架的上部和下部通过键与R1 四辊粗轧机机架牢固相连,保证轧制的稳定性。主传动由两台上置立式电机,通过减速机传动万向接轴,驱动轧辊进行轧制,两侧轧辊转动电气同步。侧压装置分布于轧机操作侧和传动侧,每侧采用两个长行程液压缸进行侧压,具有液压宽度自动控制( AWC) 功能和短行程( SSC) 控制功能,AWC、SSC 的控制是用伺服液压系统实现,侧压液压缸固定在机架的内侧,每侧布置1 个平衡液压缸,用于消除各机构之间的间隙。轧辊轴承采用四列圆锥滚子轴承,轧辊为合金铸钢辊。轧机入出口各设置有1 根机架辊,由电机通过鼓形齿接轴传动。轧机主减速机的支承梁上设置有接轴提升装置,由液压缸驱动,实现轧辊和万向接轴的连接与分离,便于轧辊和接轴的更换。轧辊更换用车间吊车通过钢丝绳实现。 3.4 R1 四辊粗轧机 R1 四辊粗轧机的主要技术参数见表3。
表3 R1 四辊粗轧机主要技术参数 R1 四辊粗轧机将原料坯轧制到所需要的中间坯厚度,四辊轧机工作辊直径小,有利于带坯的厚度控制,因有支承辊,减少了工作辊的挠度,可轧制较薄的、厚度均匀的中间坯。轧机主传动由电机直接传动万向接轴,上电机在后下电机在前,接轴为十字头式万向接轴,接轴平衡采用单支点液压平衡。轧机机架采用整铸型式,通过横梁连接。在操作侧机架的外侧安装了工作辊和支承辊轴向锁紧挡板,由液压缸进行挡板的锁紧和打开。在传动侧牌坊的外侧安装有接轴液压抱紧装置,在换辊时,由液压缸驱动卡板支承工作辊接轴。轧机窗口上部设置有支承辊平衡装置,由主平衡缸始终向上拉动平衡梁,给上支承轴承座施加适当的平衡力以消除间隙。在机架窗口中部设置有固定轨道,与操作侧机架外侧轨道相接,用于工作辊更换。压下采用电动压下+ 液压AGC,电动压下由两侧两台电动机通过蜗轮蜗杆减速机传动压下螺丝,带动上辊系升降实现轧辊的辊缝调整,两侧电动压下电气同步; 液压AGC 布置在轧机的下部,用于板坯压下、回松和动态调整轧制线。工作辊为高铬钢,轴承采用四列圆锥滚子轴承,具有承载能力大、寿命长、摩擦系数低的特点。支承辊为锻钢辊,采用摩根油膜轴承。轧机中部设置有工作辊平衡系统。在轧机入出口布置有导卫装置,在导卫入口和出口布置有工作辊冷却集管和除鳞集管。机架辊位于轧机的入、出口侧,各一根,由电机通过鼓形齿接轴传动,接轴上设置有拨叉机构,在换辊时用以脱开机架辊和接轴。机架辊轴承座布置在轧机牌坊的内侧。在轧机的操作侧设置有液压换辊装置,轧机的换辊在主轧跨内进行。 3.5 保温罩 保温罩的主要技术参数见表4。
表4 保温罩主要技术参数 保温罩安装在R1 四辊粗轧机后对中间坯进行保温,可以降低中间坯的温降速度以实现轧制优良产品。 保温罩全长72 m,入口设置有液压导向装置。每段保温罩各自独立,由液压缸实现开闭。
3.6 转鼓式飞剪 转鼓式飞剪的主要技术参数见表5。
表5 转鼓式飞剪主要技术参数 转鼓式飞剪布置在精轧机组前面,用于切去形状不规则的中间坯头尾,减少精轧和卷取的卡钢事故,使成品钢卷有良好的头尾,设有切头切尾优化剪切系统。飞剪由一台电机通过减速机和传动轴驱动下转鼓转动,通过上下转鼓两端的两对同步齿轮带动上转鼓同步转动,完成对中间坯头尾的剪切。两对剪刃成180°分别布置在转鼓上,两对剪刃均为弧形剪刃。在转鼓上布置有锁紧缸,实现剪刃在线更换。剪刃侧隙由电机带动上转毂作轴向运动进行调整。在飞剪入口端设置有1 根辊子用于导向,辊子由电机传动。飞剪下部设置有溜槽和可移动的料头收集车。
3.7 F1 ~ F6 精轧机 F1 ~ F6 精轧机的主要技术参数见表6。 表6 F1 ~ F6 精轧机主要技术参数 精轧机组由6 个机架组成,采用全连轧方式,轧机出口速度高达20.42 m/s,F1~F5 轧机是由主传动电机、减速机、齿轮机座和万向接轴传动工作辊。F6 轧机是由主传动电机、齿轮机座和万向接轴传动工作辊。轧机机架采用整铸型式,通过横梁连接。在操作侧机架的外侧安装了工作辊和支承辊轴向锁紧挡板,由液压缸进行挡板的锁紧和打开。在传动侧牌坊的外侧安装有接轴抱紧装置,在换辊时,由液压缸驱动卡板抱紧工作辊接轴。轧机窗口上部设置有上支承辊平衡装置,由主平衡缸始终向上拉动平衡梁,给上支承轴承座施加适当的平衡力以消除间隙。在机架中部设置有可升降的工作辊换辊轨道,在液压缸的作用下可抬升轨道,与操作侧机架外侧轨道相接,用于工作辊更换。轧机压下系统为液压AGC,能快速有效调整,设置弯辊系统控制板型,减少换辊次数和辊耗,提高作业率和产量。具有工作辊辊形技术,能改进带钢板形和平直度控制,工作辊可窜动以调整辊缝外形,获得理想的板形。工作辊轴承采用四列圆锥滚子轴承,工作辊为高铬球墨铸铁和无限冷硬合金复合轧辊。支承辊轴承采用摩根油膜轴承,支承辊为锻钢辊。为补偿支承辊和工作辊的辊径变化,每台精轧机在下支承辊轴承座下部设有一组用液压缸驱动的阶梯垫。在机架间设置有入出口导卫装置,上面布置有轧辊冷却水、带钢冷却水、F1 ~ F4 入口有轧辊防剥落装置。在机架间设有液压活套用于支撑带钢,形成调节轧机动态速度变化的套量,维持机架间带钢的张力,参与精轧机组的调速控制,保证轧制的稳定性,活套辊为被动辊,装在活套架上。精轧机组设置有快速换辊装置,轧辊的更换在主轧跨内进行。工作辊的拉出与送进以及新旧辊系的横移均采用液压缸驱动,支承辊的拉出与送进采用液压缸驱动。 3.8 层流冷却装置 层流冷却装置的主要技术参数见表7。
表7 层流冷却装置主要技术参数 层流冷却装置的冷却水集管,能根据带钢厚度、钢种及轧制速度,控制开启的喷水组数和调节水量,将带钢由终轧温度冷却至所要求的卷取温度,控制带钢的冶金特性,以获得均匀冷却的带钢。层流冷却由46 根精调上集管( 每根精调上集管对应三根下集管) 、28 根粗调上集管( 每根粗调上集管对应三根下集管) 和24 根过渡区下集管组成。每根上集管有两排U 型管。每两根上集管通过一个翻转液压缸翻到垂直位置,以方便检修。集管的开闭通过气动阀控制。
3.9 卷取机 卷取机的主要技术参数见表8。
表8 卷取机主要技术参数 轧线布置有两台地下卷取机,卷取机为四助卷辊全液压卷取机。4 个助卷辊均采用液压自动踏步控制( AJC) ,可以防止带头冲击助卷辊,防止带钢产生压痕,采用恒张力卷取,保证带钢头几圈卷取质量,降低卷取时噪音。1 号助卷辊为双重式二辊设计,由电机通过减速机、万向接轴分别驱动1 号助卷辊的两根辊子,辊子采用精确的压力控制。2、3、4 号助卷辊均由电机通过万向接轴驱动,设计4 号助卷辊,可以相应缩短导板长度,以减小与引入带钢的摩擦。卷取机卷筒由卷筒电机通过主传动箱带动卷筒旋转,主传动箱为双速比减速机,卷取厚带钢时采用高速比,卷取薄带钢时采用低速比。卷取机机架为分体式机架,由入、出口机架组成。在机架操作侧外部设置有卷