注塑缺陷问题大全
注塑成型缺陷及解决方法

注塑成型缺陷及解决方法注塑成型是一种常见的塑料加工方法,广泛应用于各行各业。
然而,在注塑成型过程中,可能会出现一些缺陷。
本文将介绍一些常见的注塑成型缺陷,并提供一些常用的解决方法。
1.短-shot(短充)短-shot指的是注塑件的一部分或全部体积没有完全填满模具腔体的现象。
短-shot的原因可能有:-温度不足:熔融塑料的温度不够高,使得塑料的流动性不佳。
-压力不足:注塑机的射出压力不足,无法将足够的塑料材料推入模具中。
解决方法:-提高温度:提高熔融塑料的温度,以增加其流动性。
-增加压力:增加注塑机的射出压力,以确保足够的塑料材料填充模具腔体。
2. Flash(闪边)Flash是指在注塑成型过程中,塑料溢出模具腔体形成的薄膜或边缘。
Flash的原因主要包括:-模具不平整:模具表面存在间隙或损坏,导致塑料从模具表面溢出。
-压力过高:注塑机的射出压力过高,使得塑料在模具闭合时被挤出。
解决方法:-检查模具:检查模具表面是否平整,并修复损坏的部分。
-调整压力:调整注塑机的射出压力,使其在模具闭合时不会挤出塑料。
3. Sink mark(沉痕)Sink mark是指注塑件表面出现的凹陷或不平整的现象。
Sink mark的原因可能有:-塑料收缩:在注塑件冷却过程中,熔融塑料由于收缩而导致表面出现凹陷。
-总量不足:注塑机注入的塑料总量不足,无法填满模具腔体。
解决方法:-调整冷却时间:延长注塑件的冷却时间,使塑料充分收缩并填满模具腔体。
-增加注塑量:增加注塑机的注塑量,确保塑料充分填充模具腔体。
4. Weld line(焊痕)Weld line是指注塑件表面出现的一条或多条由于不同流动方向的熔融塑料相遇而形成的线缝。
Weld line的原因主要包括:-塑料温度不一致:在注塑过程中,熔融塑料的温度不一致,导致相遇处出现冷凝。
-流动路径过长:塑料在流动过程中,由于流动路径过长而冷却,形成焊痕。
解决方法:-调整温度:调整注塑机的温度控制系统,使塑料熔融温度均匀一致。
注塑模具常见缺陷问题及改进方案
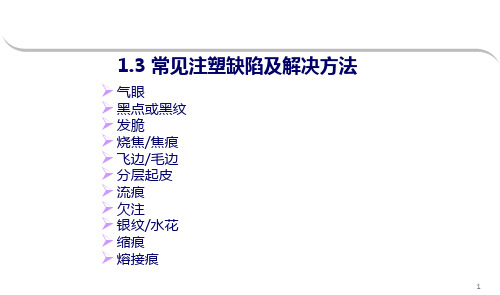
改进方法(2)
注塑机 工艺条件
▪检查止逆阀和料筒内壁是否磨损严重,上述磨损会导致
注塑压力和注塑量损失严重。
▪检查加料口是否有料或是否架桥。
▪增大注塑压力 ▪增大注塑速度,增强剪切热 ▪增大注塑量 ▪增大料筒温度和模具温度
21
成型问题-银丝/水花
银纹是指水分、空气或炭化物顺着流动方向在制件表面呈现发射状分 布的一种表面缺陷。
17
成型问题-欠注(缺料)
•欠注是指模具型腔不能被完全填充满的一种现象。
欠注形成原因
任何阻止聚合物熔体流动或使聚合物注塑量不足的因素均可能导致欠注现象。这 些因素包括:
• 熔体温度、模具温度或注塑压力和速度过低 • 原料塑化不均 • 排气不良 • 原料流动性不足 • 制件太薄或浇口尺寸太小 • 聚合物熔体由于结构设计不合理导致过早硬化
气眼可能引起的问题: 困在型腔内气体不能被及时排出,易导致出现表面 起泡,制件内部夹气,注塑不满等现象。
2
案例 (表面起泡)
Air bubble cut open
3
改进方法
结构设计 模具设计
工艺条件
• 减少厚度的不一致,尽量保证壁厚均匀. ▪ 在最后填充的地方增设排气口 ▪ 重新设计浇口和流道系统. ▪ 保证排气口足够大,使气体有足够的时间和空间排走.
5
改进方法
注塑机 工艺条件
•选择合适的注塑机吨位 •检查料筒内表面、螺杆表面是否刮伤积料. •降低料筒和喷嘴的温度. •清洁注塑过程的各个环节. •避免已经产生黑点/黑纹的料被重新回收利用.
6
案例 (黑纹)
7
改进方法
材料 模具设计
•采用无污染的原材料 •将材料置于相对封闭的储料仓中 •增加材料的热稳定性
注塑常见不良缺陷原因及解决对策

注塑常见不良缺陷原因及解决对策壹.缺料原因一.材料充填不足.状态1.射出压力未到达最高设定值.解决对策:1.增加射出压力.2.增加射出速度.3.增加模温.4.增加料筒温度.5.检查胶口尺寸.6.检查流道尺寸.7.检查喷嘴温度.8.检查喷嘴大小.状态2.射出压力已到达最高设定值.解决对策:1.延长射出行程.2.增加保持压力.3.增加保持时间.状态3.螺杆已到达最前端.解决对策:1.延长射出行程.2.检查螺杆.原因二.排气不良1.改善排气效果.2.减低射出速度.状态2.缺料位于其它部分.解决对策:1.改善排气效果.2.增加射出压力.3.增加缺料部分厚度原因三.包封现象状态1.于产品中心(不在边缘).解决对策:1.增加排气点.2.增加射出压力.3.改变浇口位置.4.增加溢流区,改变塑料流动方向. 原因四.迟滞现象状态1.浇口附近较薄处肋缺料.解决对策:1.增加厚度.2.增加射出速度.3.增加模温.4.增加料温.5.增加保持压力.6.改变浇口位置.7.增加扰流设计.原因一.过度充填状态1.毛边出现在浇口附近解决对策:1.降低射出速度.(尤其通过浇口时的速度).状态2.毛边出现在分离面(parting)且已饱和. 解决对策:1.降低计量长度.(提高切换到饱压).2.降低射出速度(尤其是切换饱压前之速度).3.减低模温.4.减低料温.5.减低保持压力.状态3.浇口附近凹陷但又发生毛边.解决对策:1.降低计量长度.(提高切换到饱压).2.降低射出速度(尤其是切换饱压前之速度).3.减低模温.4.减低料温.5.尝试以上各对策消除毛边后延长保持时间. 原因二.因流阻太大使模腔状态1.毛边又短射.(或流路末端凹陷)解决对策:1.增加模温. 内压(cavaty pressure)2.增加料温.3.增加射速.5.改善塑料料之流动性.原因三.锁模力(clamping force)不足状态1.无过饱和现象解决对策:1.提高锁模力原因四.吻合面间隙太大状态1.特定位置.解决对策:1.修复模具.原因五.模板变形解决对策:1.提早切换至饱压.2.减低饱压.3.提高模板强度及刚性. 参.凹陷.缩水与真空泡原因一.充填量不足状态1.全面性凹陷.解决对策:1.延长计量行程.2.检查螺杆逆止环3.增加射出速度.4.增加保持压力.5.增加流道或浇口尺寸.6.增加模温.状态2.凹陷出现在流路末端或薄的部位.解决对策:1.增加保持压力(尤其是初期).2.提高料筒(cylinder barrel)温度.3.增加模温.4.增加射出速度.5.检查浇口位置(由厚向薄射出).原因二.有效时间不足.状态1.凹陷出现在浇口或厚的部位.解决对策:1.延长保持时间.2.减低模温.3.减低料温.4.减少浇口断面积.原因三.表面固化太慢状态1.厚的部位出现凹陷或光泽.解决对策:1.减低模温.2.减低料温.3.塑流通过厚肉区时减速使固化层较厚.4.调整肉厚(如肋部减薄.厚薄变缓)5.使用低收缩率之塑料.6.添加发泡剂于塑料.#注:表层未凝固成坚固之固化层时.当中心收缩时会将表面熔解而产生光泽.相反的在厚的部份如果表层足够坚固则中心部的收缩会形成真空泡. #备注:第1.2.3.项会增加真空泡的发生机率#原因四.冷却时间太短状态.1.凹陷或真空泡是在开模取出后才发生.解决对策:1.减低模温.2.减低料温.3.增加冷却时间.肆.喷痕原因:发生在塑料流动断面由小急遽变大的位置;当塑料由小断面进入大断面如速度没有适当降低,则塑料像喷射般向前进.这些塑料温度冷却后与后来流入之塑料无法均匀融和而形成外观之不良.解决对策:1.减低射出速2.增加模温.3.增加料温.4.变更胶口位置.5.增加胶口断面6.避免射料方向由上向下.伍.结合线原因:塑料射出时两股以上的胶流相遇,压力与温度不足.相遇胶流之圆形先端无法融合.而形成表面的沟状痕迹.1.增加射出速度.2.增加模温.3.增加料温.4.增加保持压力.5. 变更胶口位置.6.检查排气效果.陆.波纹原因:当胶流进入较冷的模腔,由于冷却速度快,使得靠近模壁部分之塑料形成固化.这固化层妨碍了后续流动之塑料贴近模壁;但此固化层受流动压力拉伸延展,又受到胶流之压力相互挤压.相互作用一再重演在成品外观上流下一成层层之波浪状.解决对策:1.增加射出速度.2.增加射出压力.3.增加模温.4.增加料温.5.避免流道太小.柒.气泡原因:射出时塑料料包含太多气体或混合了空气.则成品内部或接近表面会有空气之现象.解决对策:1.降低松退速度或检小松退量.2.提高背压.4.检查可塑化机构.5.检查计量长度是否太长.捌.烧焦原因:射出进行中因排气不及.气体受到绝热压缩产生极高温度而将塑料料烧黑.状态1.产生于流路末端解决对策:1.减低射出速度.2.改善排气效果.3.减低锁模力.状态2.产生于包封处解决对策:1.调整肉厚.2.改变浇口位置.3.减低射出速度.4.减低锁模力.5.增加排气点.玖.冷却痕原因:在射出过程中.于喷嘴的先端或浇口部分产生冷却.这些冷却料在被射出时如未被挡在流道系统的冷料井或者是再熔解.则在浇口附近留下长条的流痕.1.增加喷嘴孔径.2.增加喷嘴温度.3.减低松退量.5.降低射出到浇口之速度.拾.浇口周围的雾状原因:在浇口(尤其为小浇口)周围高分子配向的凝固层(强度较弱).如在高速的流动场中.受分子炼被拉开而形成一些小.缺孔.很多小缺孔构成浇口周围的雾状.痕迹.解决对策:1.减低射出速度.2.增加浇口的断面积.3.改变浇口位置4.增加模温5.减低料温.拾壹.表层剥落原因:成品的表面层在塑料料流动和固化速度不同的情形下.一层一层的堆积所形成.如果因塑料料含有不均匀的成份或受过高切段力及过热所破坏则层与层间之熔合就不足而产生剥落.解决对策:1.检查塑料料是否含有太多水份.2.增高模温.3.减低射出速度.4.减低料温.5.检查塑料机的性能及设定条件.6.检查塑料料之色剂或添加物是否兼容.7.检查塑料料之是否混入其它材质.拾贰.黑点原因1.塑料料含有杂质或其它不兼容物质.解决对策:1.检查塑料料是否含有杂质.2.降低回收料的添加比例.3.检查塑料料之色剂或添加物是否兼容.原因2.塑料料在制造过程中受到污染.解决对策:1.检查送料管路及烘料筒.2.清洁螺杆及加热筒.3.清洁热流道及喷嘴.原因3.塑料料在制造过程中受到破坏.解决对策:1.减低料温.2.减低塑料料在加热管内停流时间.拾参.焦纹原因:塑料料因热受损分子量会降低或发生热分解.使成品外观出现银色或棕色的纹状瑕疵.同时也会降低强度.解决对策:1.减低料温.2.减低塑料料在加热管内停流时间.3.减低射出速度.4.增加喷嘴孔径..拾肆.湿纹所形成之水气会受流动推挤到模壁而形成成品表面条状的痕迹.解决对策:1.检查塑料材料的干燥度.2.提高背压.3.检查模壁表面是否含有水份.4.检查材料之包装与储存.拾伍.气痕原因:在射出过程中.气体来不及排出.被推往表面或在进料后松退.吸入空气.而在射出时被推往浇口之附近.状态1.出现在浇口附近.解决对策:1.降低松退速度或行程.2.使用可闭喷嘴.状态2.出现在其它部分.解决对策:1.减低射出速度.2.增加被压.3.改变浇口位置.4.设计时避免尖角及凹凸太深之形状拾陆.光泽与光泽差异原因:塑料成型品之表面,光泽决定于模具表.面加工及射出成形.之冷却速率或收缩差异所产生的表面状态1.模具打光面光泽不足.解决对策:1.模面再打光.2.增加射出速度3.增加模温4.增加料温.状态2.咬花面光泽不足.解决对策:1.调整咬花面.2.减低射出速度.3.减低模温.4.减低料温.状态3.接合线处的光泽差异. 解决对策:1.改变浇口位置.2.增加射出速度.3.增加模温.状态4.孔部周围的光泽差异. 解决对策:1.改变浇口位置.2.调整孔部型状.状态5.肋部或厚驳差异急变处. 解决对策:1.增加保持压力.2.足够的保持时间.3.降低通过问题处之速度.4.调整厚薄变化.使其变化趋缓.状态6.在顶针或滑块处光泽差异. 解决对策:1.检查模温之差异.2.避免模腔内压力过高.。
注塑缺陷总结培训
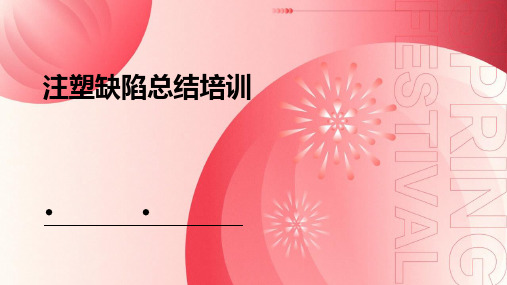
目 录
• 注塑缺陷概述 • 常见注塑缺陷分析 • 特殊注塑缺陷分析 • 注塑缺陷检测与评估 • 注塑缺陷预防措施与改进建议 • 注塑缺陷案例分享与经验交流
01
注塑缺陷概述
定义与分类
定义
注塑缺陷是指在注塑过程中由于 各种原因导致的塑料制品出现的 不符合设计要求或影响使用性能 的问题。
模具设计与制造
总结词
模具设计与制造是影响注塑成型的关键因素,合理的模具设计能够减少缺陷的 产生,提高产品质量。
详细描述
在模具设计阶段,应充分考虑产品的结构、尺寸和工艺要求,合理设计模具结 构、分型面、浇注系统等关键部分。制造过程中,应保证模具的精度和表面质 量,确保模具能够满足生产要求。
工艺参数优化
04
注塑缺察注塑件表面是否存在气泡、缩痕、银纹等缺陷。
要点二
尺寸检测
使用卡尺、千分尺等工具测量注塑件的关键尺寸,确保符 合设计要求。
工具检测
超声波检测
利用超声波检测注塑件内部是否存在空洞、裂纹等缺陷 。
X射线检测
通过X射线穿透注塑件,观察内部结构,检测是否存在气 孔、疏松等缺陷。
解决方案
选用高质量塑料材料、加强材料测试和验证
经验总结
重视塑料材料的选择和测试,确保材料性能符合生产要求
感谢观看
THANKS
总结词
工艺参数的优化是减少注塑缺陷的有效手段,通过对温度、压力、时间等参数的 调整,可以提高产品质量和生产效率。
详细描述
在注塑过程中,应合理设置温度、压力、时间等参数,并根据实际情况进行调整 优化。通过试验和数据分析,找到最佳的工艺参数组合,以减少缺陷的产生和提 高产品质量。
环境与设备管理
注塑常见缺陷及解决方法

注塑常见缺陷及解决方法1. 引言在注塑过程中,由于材料、设备、工艺等多种因素的影响,常常会出现一些缺陷。
这些缺陷不仅会影响产品的质量,还可能导致产品性能下降甚至无法使用。
因此,了解注塑常见缺陷及其解决方法对于提高产品质量至关重要。
2. 注塑常见缺陷2.1 短射短射是指注塑过程中,塑料无法充满模具腔体的情况。
造成短射的原因可能是模具设计不合理、注塑机参数设置不当等。
解决方法包括优化模具结构、增加注射压力等。
2.2 气泡气泡是注塑过程中常见的缺陷之一。
气泡的出现可能是由于塑料中含有气体、注塑过程中存在气体进入等原因。
解决方法包括在塑料中加入消泡剂、提高注射速度等。
2.3 热胀冷缩热胀冷缩是指注塑过程中,塑料在冷却过程中由于体积收缩而导致产生应力。
这种缺陷会导致产品变形、尺寸不稳定等问题。
解决方法包括优化模具结构、增加冷却时间等。
2.4 毛刺毛刺是指注塑制品表面出现的突起或凹陷。
毛刺的产生可能是由于模具表面不光滑、注塑过程中存在杂质等原因。
解决方法包括优化模具表面处理、提高注射速度等。
3. 注塑常见缺陷的解决方法3.1 优化模具结构优化模具结构是解决注塑常见缺陷的重要方法之一。
通过对模具的设计进行改进,可以减少短射、热胀冷缩等缺陷的发生。
3.2 控制注射参数注塑过程中的注射参数设置对于产品质量至关重要。
合理的注射压力、注射速度等参数可以有效地解决短射、气泡等缺陷。
3.3 加入添加剂在注塑过程中,可以加入一些添加剂来改善产品的性能。
例如,在塑料中加入消泡剂可以有效地解决气泡缺陷。
3.4 提高冷却时间热胀冷缩是注塑过程中常见的缺陷之一。
通过增加冷却时间,可以使塑料充分冷却,减少热胀冷缩导致的尺寸变化。
4. 结论注塑过程中常见的缺陷包括短射、气泡、热胀冷缩、毛刺等。
通过优化模具结构、控制注射参数、加入添加剂、提高冷却时间等方法,可以有效地解决这些缺陷,提高产品质量。
在实际生产中,需要根据具体情况选择合适的解决方法,并进行不断的改进和优化,以提高注塑产品的质量和竞争力。
常见注塑件缺陷及解决的方法
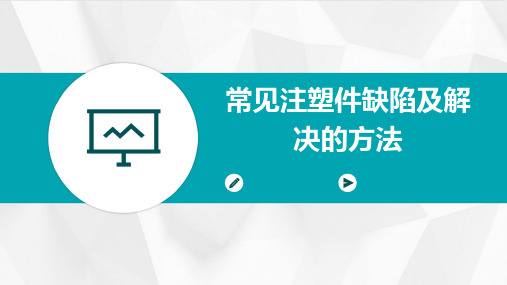
充填不足
01
总结词
充填不足是指注塑件在成型过程中未能完全填满 模具型腔,导致部分区域出现缺料或凹陷。
02
详细描述
充填不足通常是由于注射速度慢、注射压力不足、 模具温度过高或塑料流动性差等原因引起的。
缩痕
总结词
缩痕是指注塑件表面出现凹陷或收缩痕迹,影响 外观和尺寸精度。
详细描述
缩痕通常是由于塑料冷却过程中收缩率不均、模 具温度不均匀或注射压力不足等原因引起的。
常见注塑件缺陷及解 决的方法
目录
• 常见注塑件缺陷 • 注塑件缺陷原因分析 • 解决注塑件缺陷的方法 • 案例分析
01
常见注塑件缺陷
翘曲与扭曲
总结词
翘曲与扭曲是指注塑件形状发生扭曲或弯曲,不符合设 计要求。
详细描述
翘曲与扭曲通常是由于模具设计不合理、塑料收缩率差 异、注射温度和压力不适当等原因引起的。
环境条件的控制Байду номын сангаас
总结词
保持稳定的环境条件对注塑件的质量至关重 要,包括温度、湿度和清洁度等。
详细描述
确保注塑车间温度、湿度稳定,保持环境清 洁、无尘。定期对设备和环境进行清理和消 毒,防止污染和细菌滋生。同时,要关注天 气变化和季节性温差对注塑件质量的影响,
采取相应的措施进行调节。
04
案例分析
案例一:翘曲与扭曲缺陷的解决
材料选择与控制
总结词
选择合适的材料,控制材料质量是解决注塑件缺陷的重要步骤。
详细描述
根据产品使用要求和工艺特性,选择具有良好流动性和成型性的材料。同时, 要确保材料干燥、清洁,无杂质和污染。定期对材料进行质量检查,确保其性 能稳定。
模具优化与维护
注塑常见缺陷及解决方法

注塑常见缺陷及解决方法一、前言注塑是一种常见的加工工艺,广泛应用于塑料制品的生产中。
然而,在注塑过程中,常常会出现一些缺陷问题,如短射、气泡、热裂等。
这些缺陷不仅会影响产品的质量和外观,还可能导致产品失效或损坏。
因此,了解注塑常见缺陷及解决方法对于提高产品质量和生产效率至关重要。
二、注塑常见缺陷及原因1. 短射短射是指在注塑过程中,由于某些原因导致部分模具未被充填满而形成的空洞或缩小区域。
短射的原因主要有以下几点:(1)材料不足:如果注入到模具中的材料不足,则无法填充整个模具。
(2)模具设计问题:如果模具设计不合理或存在毛刺、死角等问题,则会导致材料无法充分填充。
(3)温度控制问题:如果温度控制不当,则可能导致材料在流动过程中凝固或变得过于粘稠而无法充分填充。
2. 气泡气泡是指在注塑过程中,由于材料中存在气体或在模具中注入时,气体被挤压形成的空洞。
气泡的原因主要有以下几点:(1)材料问题:如果材料含有过多的水分、挥发性成分或其他杂质,则会导致气泡产生。
(2)温度问题:如果注塑过程中温度控制不当,则可能导致材料变得过于粘稠或流动性不足,从而产生气泡。
(3)模具设计问题:如果模具设计不合理或存在毛刺、死角等问题,则会导致材料无法充分填充,从而产生气泡。
3. 热裂热裂是指在注塑后产品表面出现裂纹或断裂。
热裂的原因主要有以下几点:(1)温度问题:如果注塑过程中温度控制不当,则可能导致产品表面温度过高或过低,从而引起热裂。
(2)冷却时间问题:如果冷却时间不足或过长,则可能导致产品表面出现应力集中区域,从而引起热裂。
(3)材料问题:如果使用了低质量或不合适的材料,则可能导致产品表面出现裂纹或断裂。
三、注塑常见缺陷的解决方法1. 短射的解决方法(1)增加注塑压力:通过增加注塑压力,可以使材料充分填充整个模具,从而避免短射。
(2)改善模具设计:通过改善模具设计,如加大流道、减少死角等,可以使材料充分填充整个模具。
注塑产品缺陷汇总及解决方法

注塑产品缺陷汇总及解决方法一、溢料飞边故障分析及排除方法(1)合模力不足。
当注射压力大于合模力使模具分型面密合不良时容易产生溢料飞边。
对此,应检查增压是否增压过量,同时应检查塑件投影面积与成型压力的乘积是否超出了设备的合模力。
成型压力为模具内的平均压力,常规情况下以40mpa计算。
生产箱形塑件时,聚乙烯,聚丙烯,聚苯乙烯,及ABS的成型压力值约为30mpa;生产形状较深的塑件时,成型压力值约为36mpa;在生产体积小于10cm3的小型塑件时,成型压力值约为60mpa。
如果计算结果为合模力小于塑件投影面积与成型压力的乘积,则表明合模力不足或注塑定位压力太高。
应降低注射压力或减小注料口截面积,也可缩短保压及增压时间,减小注射行程,或考虑减少型腔数及改用合模吨位大的注塑机。
(2)料温太高。
高温熔体的熔体粘度小,流动性能好,熔料能流入模具内很小的缝隙中产生溢料飞边。
因此,出现溢料飞边后,应考虑适当降低料筒,喷嘴及模具温度,缩短注射周期。
对于聚酰胺等粘度较低的熔料,如果仅靠改变成型条件来解决溢料飞边缺陷是很困难的。
应在适当降低料温的同时,尽量精密加工及修研模具,减小模具间隙。
(3)模具缺陷。
模具缺陷是产生溢料飞边的主要原因,在出现较多的溢料飞边时必须认真检查模具,应重新验核分型面,使动模与定模对中,并检查分型面是否密着贴合,型腔及模芯部分的滑动件磨损间隙是否超差。
分型面上有无粘附物或落入异物,模板间是否平行,有无弯曲变形,模板的开距有无按模具厚度调节到正确位置,导合销表面是否损伤,拉杆有无变形不均,排气槽孔是否太大太深。
根据上述逐步检查的结果,对于产生的误差可采用机械加工的方法予以排除。
(4)工艺条件控制不当。
如果注射速度太快,注射时间过长,注射压力在模腔中分布不均,充模速率不均衡,以及加料量过多,润滑剂使用过量都会导致溢料飞边,操作时应针对具体情况采取相应的措施。
值得重视的是,排除溢料飞边故障必须先从排除模具故障着手,如果因溢料飞边而改变成型条件或原料配方,往往对其他方面产生不良影响,容易引发其他成型故障。