硅烷偶联剂处理金属表面
硅烷化处理及其在金属表面处理中的应用分析

通过硅烷化处理与传统磷化处理相比较,能够省去表调及磷 化前后的水洗工序,处理时间大大缩短,并减少了污水处理量。
1 硅烷化处理的原理 硅烷化处理是以有机硅烷为主要原料对金属或非金属材料
进行表面处理的过程,该过程通过引入硅烷基与基材形成共价 键连接,在金属表面形成高致密的保护膜。
硅烷是一类含硅基的有机/无机杂化物,其基本分子式为 X-R-SiY3,其中的Y指的是与硅原子连接的可水解基团,其中 R则是指非水解脂肪族链,其中的X指的是可以和有机材料实现 反应的基团,例如乙烯基以及氨基等[2]。
TECHNOLOGY AND INFORMATION
工业与信息化
硅烷化处理及其在金属表面处理中的应用分析
汪洋 包英俊 中国船舶重工集团第七一五研究所 浙江 杭州 311400
摘 要 工业生产中,将耐腐蚀的有机物涂覆在金属表面,经固化成膜后制备的有机涂层具有屏蔽、缓蚀及电化学 保护三方面的作用,防腐效果好。由于涂料具有选择性宽、可用范围广、节约能源、应用施工方便等优点,是现今 最有效、最经济和研究最多的表面防护方法之一。对工作表面进行强化热处理,可在不改变零件内部组织和性能的 前提下,达到工作心部与表层在组织结构、性能等的最佳配合。本文结合硅烷化处理剂的制备及金属表面处理方法 的对比,来分析硅烷化处理方法的优势和应用情况。 关键词 硅烷化;金属表面;处理工艺;应用分析
硅烷化处理相比传统的处理工艺有以下优势: (1)硅烷化金属表面处理工艺路线相比传统工艺省去了 表调和磷化前后两道水洗工序,减少了废水的排放量,减轻了 环境污染程度,降低了生产成本。 (2)在使用温度方面,由于硅烷成膜过程为常温化学反 应,因为在日常使用中槽液无须加热即可达到理想处理效果。 此方面相比较来说,为行业应用节省了大量能源并减少了燃料 废气排放。 (3)硅烷化反应中无沉淀反应,所以在日常处理中不产 生沉渣,消除了前处理工序中的固体废物处理问题并有效地延 长了槽液的倒槽周期。 (4)在配槽用量方面,硅烷化较磷化工艺也减少了 20%~50%,更关键的是在每平方米单耗方面硅烷化的消耗量 为传统磷化工艺的15%-20%。在处理时间上硅烷化较磷化也有 较大幅度的缩短,从而提高了生产率,降低了设备持续运作成 本。 (5)电沉积硅烷化金属表面处理工艺除具有硅烷化金属 表面处理工艺的优点外,还可以通过对沉积过程电化学参数的 调节,实现对硅烷化膜结构的可控制备。 (6)通过对现有磷化处理设备的简单改造,投入少量资 金,即可将磷化金属表面生产线改装成硅烷化和电沉积硅烷化
不锈钢金属表面硅烷化处理的应用研究

不锈钢金属表面硅烷化处理的应用研究徐方流(江苏兴达钢帘线股份有限公司,江苏兴化225700)显著的环保优势是不锈钢金属表面硅烷化处理技术的主要特点,金属表面进行有机硅烷溶液处理的一个过程就是金属表面硅烷化处理的本质,为了更好的对不锈钢金属表面硅烷化处理进行应用,就需要进行详细的分析。
一、不锈钢金属表面硅烷化处理工艺的优点不锈钢金属表面利用有机硅的特殊分子结构进处理的过程就是不锈钢金属表面硅烷化处理,这种处理方式具有很多的工艺优点,主要包括以下几点。
首先,在对不锈钢金属表面进行硅烷化处理时,有害或者磷等重金属离子不会应用在其中。
其次,该表面处理的工艺比较容易控制,并且时间短、流程简单。
再次,在不锈钢金属表面硅烷化的处理过程中,不会进行加温操作,也不会有沉渣的产生,这样就能够循环使用槽液。
然后就是还能够使得基材与油漆的结合率得到提升。
最后,不锈钢金属表面硅烷化处理能够对多种基材进行共线处理,例如铝、锌以及铁等。
由于不锈钢金属表面硅烷化处理工艺的优点很多,这就使得被广泛的应用在普通工业中。
此外,在进行不锈钢金属表面硅烷化制备时,其制备工艺会谁硅烷膜性能造成很大的影响。
硅烷偶联剂水解时间、硅烷液浓度、金属基体在硅烷液的浸渍时间、硅烷液PH 值、处理后老化时间以及老化温度等都是影响不锈钢金属表面硅烷膜性能的主要影响因素。
二、不锈钢金属表面硅烷化处理的应用(一)硅烷处理技术原理。
化学官能团是硅烷分子主要含有的,并且通常其化学官能团有两种。
一种化学官能团能够个无机材料表面的羟基发生化学反应,形成共价键,例如玻璃纤维、金属氧化物、金属以及硅酸盐等。
另一种化学官能团可以与树脂发生化学反应,形成共价键。
为了能够有效的提高复合材料的性能,就可以将性质不同的两种材料进行有机的结合。
在硅烷处理技术的成膜过程中,首先先进行硅烷偶联剂的水解,水解完成之后就能够得到Si-O-Me 共价键,主要是由硅烷联合水解后得到的硅醇与金属基体表面存在的MeOH 所反应生成的。
硅烷偶联剂的作用原理
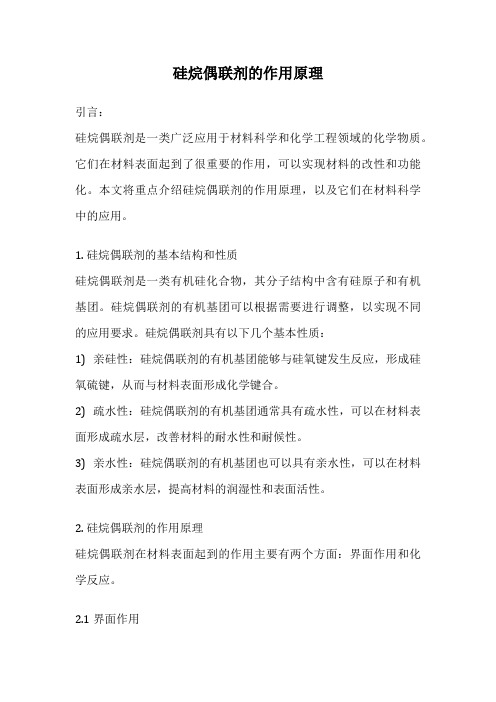
硅烷偶联剂的作用原理引言:硅烷偶联剂是一类广泛应用于材料科学和化学工程领域的化学物质。
它们在材料表面起到了很重要的作用,可以实现材料的改性和功能化。
本文将重点介绍硅烷偶联剂的作用原理,以及它们在材料科学中的应用。
1. 硅烷偶联剂的基本结构和性质硅烷偶联剂是一类有机硅化合物,其分子结构中含有硅原子和有机基团。
硅烷偶联剂的有机基团可以根据需要进行调整,以实现不同的应用要求。
硅烷偶联剂具有以下几个基本性质:1) 亲硅性:硅烷偶联剂的有机基团能够与硅氧键发生反应,形成硅氧硫键,从而与材料表面形成化学键合。
2) 疏水性:硅烷偶联剂的有机基团通常具有疏水性,可以在材料表面形成疏水层,改善材料的耐水性和耐候性。
3) 亲水性:硅烷偶联剂的有机基团也可以具有亲水性,可以在材料表面形成亲水层,提高材料的润湿性和表面活性。
2. 硅烷偶联剂的作用原理硅烷偶联剂在材料表面起到的作用主要有两个方面:界面作用和化学反应。
2.1 界面作用硅烷偶联剂的有机基团可以与材料表面发生相互作用,形成一层有机膜。
这层有机膜可以增加材料表面的疏水性或亲水性,改变材料的表面性质。
例如,硅烷偶联剂可以在玻璃表面形成一层疏水膜,使其具有防水和防污染的功能;同时,硅烷偶联剂也可以在金属表面形成一层亲水膜,提高其润湿性和涂覆性。
2.2 化学反应硅烷偶联剂的有机基团中的官能团可以与材料表面的官能团发生化学反应,形成化学键合。
这种化学键合可以增强材料与硅烷偶联剂之间的结合强度,并实现材料的改性。
例如,硅烷偶联剂可以与聚合物表面的官能团发生缩合反应,从而使聚合物表面形成一层化学交联网络,增加其力学强度和耐磨性;同时,硅烷偶联剂也可以与无机材料表面的官能团发生反应,形成一层化学键合的界面层,提高材料的界面附着力和耐候性。
3. 硅烷偶联剂的材料应用硅烷偶联剂在材料科学中有着广泛的应用。
以下是几个常见的应用领域:3.1 玻璃纤维增强塑料硅烷偶联剂可以增强玻璃纤维与塑料基体之间的结合强度,提高增强塑料的力学性能和耐候性。
两种硅烷偶联剂修饰的铝合金表面超疏水性能研究

表面技术第52卷第9期两种硅烷偶联剂修饰的铝合金表面超疏水性能研究李文艳1,2,杨含铭3,夏祖西1,2,彭华乔1,2,石涛1,2*(1.中国民航局第二研究所,成都 610041;2.民航航油航化产品适航与绿色发展重点实验室, 成都 610041;3.西南交通大学 地球科学与环境工程学院,成都 611756)摘要:目的探究硅烷偶联剂对铝合金超疏水表面性能的影响。
方法通过化学刻蚀并结合硅烷偶联剂修饰,在AMS 4037铝合金上制备超疏水表面。
首先,通过HCl/H2O2混合液对铝合金进行刻蚀,在其表面构造具有多级蜂巢状的微/纳复合结构,再分别采用硅烷偶联剂和含氟硅烷进行疏水改性。
详细研究2种改性剂的浓度对刻蚀铝合金表面润湿性的影响。
采用接触角测量仪对材料表面润湿性和表面自由能进行测试,通过扫描电镜、能谱仪、激光共聚焦显微镜对表面微观结构和化学成分进行表征。
同时,对2种硅烷偶联剂修饰的铝合金超疏水表面进行液滴冻结时间、防覆冰及自清洁行为测试。
结果铝合金表面的疏水性并不总是与改性剂的浓度呈正相关。
当改性剂的质量分数为0.5%时,经硅烷偶联剂修饰后其刻蚀表面的接触角为156.3°,但滚动角大于30°,而经含氟硅烷修饰后其表面的接触角可达164.4°,滚动角为6°。
液滴在硅烷偶联剂和含氟硅烷修饰后的超疏水表面的冻结时间分别为37、45 s。
结论相较于硅烷偶联剂修饰的刻蚀表面,含氟硅烷改性后其表面能更低,疏水效果更好。
相较于未处理的铝合金表面,经硅烷偶联剂修饰后铝合金超疏水表面可显著抑制液滴的冻结过程,具有更长的冻结时间和延迟覆冰的能力,并且含氟硅烷修饰后表面的防冰性能更佳。
自清洁实验也证明经含氟硅烷修饰后的表面具有更好的自清洁性能,其表面的微小灰尘颗粒更易被带走。
关键词:铝合金;超疏水;冻结时间;结霜;自清洁中图分类号:O69 文献标识码:A 文章编号:1001-3660(2023)09-0340-11DOI:10.16490/ki.issn.1001-3660.2023.09.030Superhydrophobic Properties of Aluminum Alloy SurfacesModified by Two Silane Coupling AgentsLI Wen-yan1,2, YANG Han-ming3, XIA Zu-xi1,2, PENG Hua-qiao1,2, SHI Tao1,2*(1. The Second Research Institute of Civil Aviation Administration of China, Chengdu 610041, China; 2. Key Laboratory ofAviation Fuel & Chemical Airworthiness and Green Development, Civil Aviation Administration of China, Chengdu 610041, China; 3. Faculty of Geosciences and Environmental Engineering, Southwest Jiaotong University, Chengdu 611756, China)ABSTRACT: In order to investigate the effects of the silane coupling agent on properties of superhydrophobic aluminum alloy surfaces, superhydrophobic surfaces were prepared on AMS 4037 aluminum alloy by chemical etching combining with收稿日期:2022-09-11;修订日期:2023-02-24Received:2022-09-11;Revised:2023-02-24基金项目:国家自然科学基金(U1833202)Fund:National Natural Science Foundation of China (U1833202)引文格式:李文艳, 杨含铭, 夏祖西, 等. 两种硅烷偶联剂修饰的铝合金表面超疏水性能研究[J]. 表面技术, 2023, 52(9): 340-350.LI Wen-yan, YANG Han-ming, XIA Zu-xi, et al. Superhydrophobic Properties of Aluminum Alloy Surfaces Modified by Two Silane Coupling第52卷第9期李文艳,等:两种硅烷偶联剂修饰的铝合金表面超疏水性能研究·341·modification of two kinds of silane coupling agents. Via an etching process with hydrochloric acid and hydrogen peroxide mixed solution, hierarchical honeycomb micro/nano structures were formed on AMS 4037 aluminum alloy surfaces. Then, the etched surface was treated with different concentrations of silane and fluorosilane, respectively. The effect of silane coupling concentration on wettability was also investigated systematically. The wettability and surface free energy of as-prepared samples were characterized and calculated by a contact angle meter. The microscopic appearance and chemical composition were analyzed by SEM, LSCM and energy spectrum. Meanwhile, the freezing process of water droplets on the surface with various wettability was observed with a high speed camera and the freezing time was calculated based on the video images. Anti-icing and self-cleaning behaviors of the surfaces treated with two modifiers were tested respectively. The results showed that the hydrophobicity of as-prepared samples was not always positively related to the concentration of the silane coupling. When the modifier was 0.5wt.%, the contact angle of the etched surface treated with silane coupling agent was 156.3°, but the sliding angle was more than 30°, while the fluorosilane-modified surface reached a maximum contact angle of 164.4° and a rolling angle of 6°, which was definitely a superhydrophobic surface. When the concentration of modifiers continued to increase, the hydrophobicity of both surfaces became worse, which may be due to the effect of the way in which the surface modifier molecules were packed. The freezing time of water droplets with a volume of 5 μL on the superhydrophobic surface modified by silane coupling agent and the fluorosilane was divided into 37 s and 45 s, respectively. And the lower freezing front speed on the surface with better hydrophobicity was observed. The anti-icing for the superhydrophobic surface attributed to the quite small contact area and the high thermal resistance between the liquid-solid interfaces. The anti-icing test illustrated that compared with the original aluminum alloy surface, the superhydrophobic surfaces had longer freezing time and could delay icing, and the surface modified by fluorosilane had better anti-icing performance. It was found that the size of areas frozen was negatively correlated with hydrophobicity of surface. Under the same conditions, the better the hydrophobicity, the less ice is covered on the surface of the aluminum alloy. The frozen area of the etched surface modified with silane coupling agent is smaller than that of the untreated surface. The frozen area of the etched surface modified by the fluorosilane coupling agent is smaller than that of the surface modified by the silane coupling agent. This fact can be explained by the reduction of solid-droplet interface and increase of thermal resistance resulting from trapped gas. The self-cleaning experiments also prove that the surface modified by fluorosilane has better self-cleaning performance than the silane-modified surface, and the small dust particles on the surface are easier to remove.KEY WORDS: aluminum alloy; superhydrophobic; freezing time; frosting; self-cleaning超疏水材料通常指与水的接触角大于150°、滚动角小于10°的材料。
硅烷偶联剂应用现状及金属表面处理新应用

1 硅烷试剂的特征和作用机理硅烷试剂的一般结构式为:Y -R-SiX3,其中:X 是结合在硅原子上的水解性基团,如氯基、甲氧基、乙氧基、乙酰氧基等;Y 为有机官能团,如氨基,环氧基等;R 是具有饱和或不饱和键的碳链。
所以它分布在无机物与有机物界面上时,在相互没有亲和力而难以相容的界面之间起着“乳化剂”的作用[2~5] 。
由于界面现象非常复杂,单一的理论往往难以充分说明,对于硅烷试剂在界面的作用机理就有多种解释。
已经提出的关于硅烷试剂在无机物表面行为的理论主要有化学结合理论、物理吸附理论、氢键形成理论、可逆平衡理论等[4] 。
Arkies 提出的理论模式被认为是最接近实际的一种理论,硅烷试剂按这一机理在无机物表面上的反应过程如图1 所示;硅烷试剂首先接触空气中的水分而发生水解反应,进而发生脱水反应形成低聚物,这种低聚物与无机物表面的羟基形成氢键,通过加热干燥,发生脱水反应形成部分共价键,最终结果是无机物表面被硅烷覆盖。
从上述作用机理还可以看出,无机物的表面上不具有羟基时,就很难发挥出相应的作用或效果。
对于有机体系,大多数分子中都具有特定的官能团而表现出该聚合物的特性。
SA同聚合物有机宫能团发生化学反应,从而产生偶联效果,一般认为SA 对于固化过程中伴随着化学反应的热固性树脂效果最为明显,而对于缺乏反应性和极性基团的热塑性树脂效果差[5 ] 。
文献[3~5 ] 还给出了SA 与无机和有机物质的典型应用配合。
2 硅烷试剂的使用方法将硅烷试剂均匀地包覆在填料上大致可分为干法和湿法[6 ] 。
硅烷试剂的处理可根据填料的比表面积大小进行调整,一般是填料重量的1 % , 实际上处理时最好是用水、溶剂稀释后再进行使用。
最近因高速捏合机的改进及成本的降低,也有用硅烷试剂原液直接处理的。
处理后填料的干燥条件也是影响复合材料性能的重要因素之一,因为当干燥不充分时,还有许多氢键成为残留状态很容易从外部吸入水分,影响复合材料的物性。
金属表面改性硅烷化处理研究进展

山东化工SHANDONG CHEMICAL IDUSTRY・72・2021年第50卷金属表面改性硅烷化处理研究进展刘颖1>2,王修春2,江荣岩1(1.山东建筑大学材料科学与工程学院,山东济南250101;2.齐鲁工业大学(山东省科学院)山东省科学院新材料研究所山东省轻质高强金属材料重点实验室,山东济南250014)摘要:硅烷化处理是以硅烷偶联剂为主要原料的新型表面处理技术,常用于涂装前处理以提高金属基体与有机涂层的结合力或将其直接作为防腐蚀涂层’单纯的硅烷膜膜层较薄、表面有缺陷及裂纹,影响了其对金属的防护性能,需要对其进一步改性’综述了近年来国内外对硅烷化处理改性工艺的研究,详述了各种改性工艺对硅烷膜性能的影响,对耐蚀机理进行阐述,指出各种改性工艺存在的不足并提出进一步的研究方向’双层硅烷膜、添加纳米粒子、无机缓蚀剂、有机缓释剂以及硅烷与树脂复配等工艺明显提高了硅烷膜的性能,将多种改性工艺相结合可得到综合性能更加优异的硅烷膜’但还需要进一步研究改性机理,提高硅烷膜对不同基体的适用性及与涂装体系的配套性’关键词:硅烷化处理;改性处理;纳米粒子;缓蚀剂;耐蚀性中图分类号:TG174.4文献标识码:A文章编号:1008-021X(2021)03-0072-07Research Progress of Modified Silanization Treatment on Metal SurfaceLin Ying1,2,Wang XiucCun2,Jiang Rongya$(1.School of Material Science and Engineering,Shandong Jianzhu University,Jinan250101,China;2.Shandong Provincial Key Labomtom of HRhsOength LRhtweRht Metal/v Materials,Advanced Materials enstitute,Qilu University of Technology!Shandong Academy of Sciences),Jinan250014,China)Abstrach:Silanization treatoent which used the silane coupling aaent as the main material had become a new type of surface treatoent technology.It was commonly utilized in coating pretreatoent to improve the adhesion between the meol/v substrate and the oryanic coating or directly used as the anticorrosion film.However,pure silane fTni showed poor corrosion resistance because of the thin thickness and the defects/cracks on the surface.As a result,further modifications of the silane-based films were necessary before the application.In this paper,various modOications of the silanization treatoents in the world such as the double -eayee)oeanefoem,addotoon ofnanopaetocee),onoeganocgoeganoccoeo)oon onhobotoeand)oeanegee)on compo)oteweee)ummaeozed.Efectofdofeeentmodofocatoon)on thepeefoemanceofthe)oeane-ba)ed foem)and theeeeeeantcoeo)oon ee)otancemechanom) weeedocu)ed on detaoeand thedoadeantage)ofeaeoou)modofocatoon method)weeeaeoondocated.Themodofocatoon mechanom) )houed befuethee)tudoed on depth,toompeoeethecoeo)oon ee)otancepeefoemance,theappeocaboeotytodofeeent)ub)teate)and thecompatoboeotywoth thecoatong)y)tem ofthe)oeane-ba)ed foem.Ke e words:silanization;modification treatment;nanopar/cles;corrosion inhibitor;corrosion resistance随着无辂无磷钝化技术的推进,绿色、环保的硅烷化处理技术引起了人们的广泛关注,有望替代辂酸盐钝化及磷化处理〔7」。
硅烷偶联剂在金属表面处理的应用
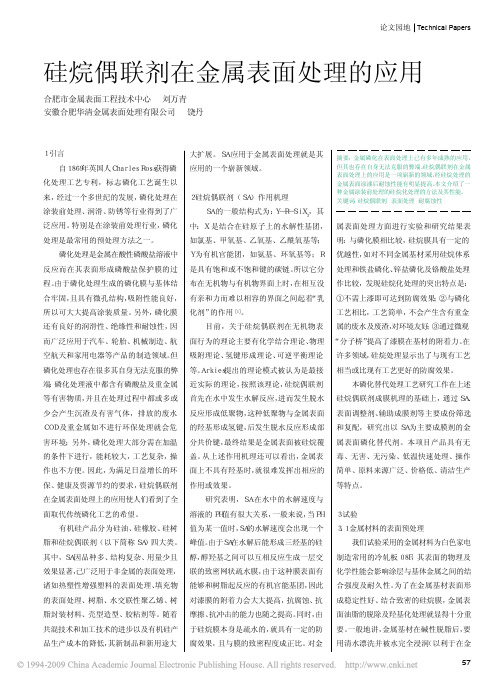
论文园地T echnical P apers57硅烷偶联剂在金属表面处理的应用合肥市金属表面工程技术中心 刘万青安徽合肥华清金属表面处理有限公司 饶丹1 引言自1869年英国人Charles Ross获得磷化处理工艺专利,标志磷化工艺诞生以来,经过一个多世纪的发展,磷化处理在涂装前处理、润滑、防锈等行业得到了广泛应用。
特别是在涂装前处理行业,磷化处理是最常用的预处理方法之一。
磷化处理是金属在酸性磷酸盐溶液中反应而在其表面形成磷酸盐保护膜的过程。
由于磷化处理生成的磷化膜与基体结合牢固,且具有微孔结构,吸附性能良好,所以可大大提高涂装质量。
另外,磷化膜还有良好的润滑性、绝缘性和耐蚀性,因而广泛应用于汽车、轮胎、机械制造、航空航天和家用电器等产品的制造领域。
但磷化处理也存在很多其自身无法克服的弊端:磷化处理液中都含有磷酸盐及重金属等有害物质,并且在处理过程中都或多或少会产生沉渣及有害气体,排放的废水COD及重金属如不进行环保处理就会危害环境;另外,磷化处理大部分需在加温的条件下进行,能耗较大,工艺复杂,操作也不方便。
因此,为满足日益增长的环保、健康及资源节约的要求,硅烷偶联剂在金属表面处理上的应用使人们看到了全面取代传统磷化工艺的希望。
有机硅产品分为硅油、硅橡胶、硅树脂和硅烷偶联剂(以下简称SA)四大类。
其中,SA因品种多、结构复杂、用量少且效果显著,已广泛用于非金属的表面处理,诸如热塑性增强塑料的表面处理、填充物的表面处理、树脂、水交联性聚乙烯、树脂封装材料、壳型造型、胶粘剂等。
随着共混技术和加工技术的进步以及有机硅产品生产成本的降低,其新制品和新用途大摘要:金属磷化在表面处理上已有多年成熟的应用,但其也存在自身无法克服的弊端。
硅烷偶联剂在金属表面处理上的应用是一项崭新的领域,经硅烷处理的金属表面涂漆后耐蚀性能有明显提高。
本文介绍了一种金属涂装前处理的硅烷化处理的方法及其性能。
关键词:硅烷偶联剂 表面处理 耐腐蚀性大扩展。
硅烷偶联剂在金属表面处理上的应用

剂的机组 , 它们 的 L C C P伉 相差 并 不大 , 在家用 酬 和汽 车空| 采用 H C l4 培 J F —3 a系统 的 L C C P伉甚至 比 C, O 还要低 。 以 C N衡 量 , F 一 3a的 C WN 若 WE H C 14 E 伉仅 为 1 , G 4 但 WP伉 为 13 4 0 因此 , 采川 不 同的 价指 标 结果相 差 巨大 ,这 也使 得人 们对 以 G WP为
・
值来 评价 温室 气体 对 全球 变 暖 的影 响 , 利用 不 I气 西 1 体的 G WP值 ,可 以 计算 山一 定 H期 内排放 的温室 寸
气体 总量 , 方便 了小 同时期 或小 I 区之 问的 ” 排 司地 碳
个选 定年 份 巾产 生千 等 的仝球 平均温 影响 开
20 0 8年 9 1口,联 合 气候 化 架公 约》 爿 《 ( NF C U C C)执 行 秘书伊 沃 c德 博埃 尔 至信 IC P C辛 席. 希望 IC C对 其 它衡 量指 标 , G P替代 G , PC 如 T WI 的 可 能性进 行 评 估 , 以满 足 《 都 议定 书》 京 附件 f 缔 约 方进 一步 承诺 特 设工 作 组 相关 议题 谈 判 的需要 . .
的f .  ̄效应 (n i 【 f ()从 I 更仝 面 更科 学 的 1 4 1dl Et - , 『 ・ e t l j 角度 对整 个 系统 及其 过 程进 行 价 , 样 它们 的变 这
暖效应值 要明 的 比原 来 的 G WP值 小许 多或相
若以 L C C P衡量 ,使川 H C l4 , s C ? F — 3 aHC 和 O 制冷
素造 成的碳排 放 。 ) WP反映 的是 某一 同定 时 问范 2G 闱内 (0 5 、0 、0 2 、0 10 5 0年 ) 的增 温 效 果 , 有 考 虑 剑 没 评 价 时 问 与 温 室 气 体 的 大 气 生 命 情 期 的关 系 以 J 10年 为 例 . WP没 有 考 虑 剑 大 气 停 时 间超 过 0 G 10年 的气 体仍 然仔 在 着变 暖效 应 。 , 种 气体 被 0 如 某
- 1、下载文档前请自行甄别文档内容的完整性,平台不提供额外的编辑、内容补充、找答案等附加服务。
- 2、"仅部分预览"的文档,不可在线预览部分如存在完整性等问题,可反馈申请退款(可完整预览的文档不适用该条件!)。
- 3、如文档侵犯您的权益,请联系客服反馈,我们会尽快为您处理(人工客服工作时间:9:00-18:30)。
硅烷偶联剂是一种具有特殊结构的有机硅化合物,它可以在金属表面形成一层致密的保护膜,提高金属的耐腐蚀性、抗氧化性和耐磨性。
同时,硅烷偶联剂还可以增强金属与涂层之间的附着力,提高涂层的抗脱落性能。
使用硅烷偶联剂处理金属表面可以提高金属的表面能,使其更容易被润湿和附着,从而改善涂层的附着力和耐久性。
此外,硅烷偶联剂还可以与无机填料反应,改善其与有机聚合物的相容性,提高复合材料的性能。
在金属表面处理中,硅烷偶联剂的应用范围广泛,可用于钢铁、铝、铜等金属表面的处理。
例如,在钢铁表面处理中,硅烷偶联剂可以通过化学反应在钢铁表面形成一层致密的保护膜,提高钢铁的耐腐蚀性和抗氧化性。
在铝表面处理中,硅烷偶联剂可以改善铝表面的润湿性和附着力,提高涂层的附着力和耐久性。
总之,使用硅烷偶联剂处理金属表面可以提高金属的耐腐蚀性、抗氧化性和耐磨性,同时还可以改善金属与涂层之间的附着力,提高涂层的抗脱落性能。