电弧炉控制系统方案
《毕业设计(论文)-plc电弧炉控制系统总体设计》[管理资料]
![《毕业设计(论文)-plc电弧炉控制系统总体设计》[管理资料]](https://img.taocdn.com/s3/m/673bf62376eeaeaad0f330b3.png)
摘要电弧炉炼钢是靠电极和炉料间放电产生的电弧,使电能在弧光中转变为热能,并借助辐射和电弧的直接作用加热并熔化金属和炉渣,是冶炼某些特殊金属及合金必须使用的炼钢方法。
论文以40吨电弧炉计算机控制系统为背景,在查阅了大量国内外相关文献的基础上,综述了电弧炉控制技术的发展历程、研究现状及今后的发展趋势。
根据电弧炉熔炼工艺对控制系统的控制要求,给出了控制系统总体设计方案,对电弧炉计算机控制系统的硬件系统配置作了详细的说明。
在电极调节器控制方案设计的基础上给出了实用的控制算法的实现方法,应用日本欧姆龙系列编程软件编写了整个控制系统控制软件,包括电极调节控制单元、液压站控制单元、真空开关合、分闸控制单元、变压器调压换档控制单元和其它逻辑控制单元。
关键词:电弧炉,电极调节,计算机控制,PLCABSTRACTThe steel-making of Electric Arc Furnace transfers the electricity to heat by the arc between electrode and charging. The Arc and its radiation melt the metals along with slag, it is the essential way to produce the special steel and alloy.The thesis is based on the 40-Ton electric arc furnace computer distributed control system of the Second Steel-making plant. The summaries of the historic, present state and perspective trend of control techniques of electric arc furnace are based on consulting a great deal of documentation. According to the control demands of the system, the system’s solving scheme is presented. The thesis thoroughly describes the hardware configuration of the computer distributed control system of electric arc furnace. Based on the design of the electrode’s position control algorithm,the realization method of control algorithm is proposed. The control software is designed with the Omron series programming language produced by Siemens Company, including electrode’s position control unit,hydraulics control unit, vacuum switch on/off control unit, changing the level of transformer control unit, oxygen gun movement control unit and other logical control units.Key words: Electric Arc Furnace, Electrode Regulator, Computer Control.,PLC第一章概述 (4): (5)电弧炉系统 (5)电弧炉炼钢发展概况 (5)电弧炉炼钢的特点 (6)电弧炉炼钢计算机控制发展概况 (7)电弧炉炼钢设备概括 (7)电弧炉炼钢的机械设备 (7)电弧炉炼钢的电气设备 (9)电弧炉炼钢过程及工艺简介 (10)电弧炉炼钢过程 (10)电弧炉炼钢工艺简述 (12)电弧炉工艺对控制系统的要求 (12)电弧炉炼钢工艺对电极调节器的要求 (13)本论文所做的工作 (13)第二章电弧炉控制系统 (14)电极升降自动控制系统 (14)液压、水冷、气动控制系统 (16)液压控制系统 (16)水冷控制系统 (17)气动控制系统 (17)PLC控制系统 (18)计算机在电弧炼钢中的应用 (18)电弧炉PLC控制系统的构成 (19)电弧炉PLC控制系统的功能 (20)第三章电弧炉电极控制的建模 (21)电极系统电气部分建模 (21)单向电极的建模 (22)三相电极的建模 (23)电极工作原理及性能要求 (27)工作原理 (27)性能要求 (28)传动系统的建模 (29)第四章电弧炉控制系统的软硬件设计 (30)变压器保护 (30)液压站控制 (32)炉体操作 (37)水冷系统 (42)事故报警 (44)上料系统 (45)电弧炉控制系统程序的检查和编译 (48)结束语 (50)参考文献 (51)致谢 (52)第一章概述:钢包精炼炉,是用来对初炼炉(电弧炉、平炉、转炉)所熔钢水进行精炼,并且能调节钢水温度,工艺缓冲,满足连铸、连轧的重要冶金设备。
3电弧炉控制系统方案
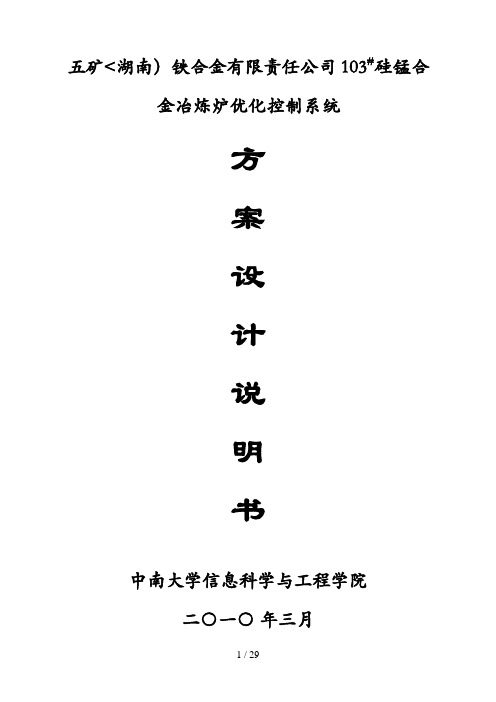
五矿<湖南)铁合金有限责任公司103#硅锰合金冶炼炉优化控制系统方案设计说明书中南大学信息科学与工程学院二○一○年三月一、开发背景五矿<湖南)铁合金集团有限公司103#10000KV A矿热炉主要用于熔炼硅锰合金和碳锰合金,整个生产系统由炉体、供电变压器及保护系统、配加料系统、电极卷扬升降控制系统、电极压放子系统和炉体水冷系统等组成。
目前,配加料子系统采用了计算机自动控制;电极压放子系统依靠人工凭经验综合考虑炉况、二次电压、一次电流、熔炼时间等因素,输入控制信号给PLC,由PLC来完成电极的定长压放;电极升降是依靠人工凭经验综合考虑二次电压、一次电流及炉盖温度等因素进行调节;供电变压器二次侧电压等级靠人工根据炉况和电压、电流、功率等因素凭经验进行调整。
这种靠人工凭经验来控制冶炼过程的方法难以保证矿热炉稳定持续地工作在最佳工作范围内,调节过程相对滞后、工人操作强度大、工作效率低,容易出现电极烧结不好、耗电量大、炉况不稳定等问题,难以保证产品的产量和质量。
二、设计要求针对五矿<湖南)铁合金集团有限公司103#矿热炉熔炼过程控制自动水平低下带来的各种问题,通过现场调研和与工艺技术人员交流沟通,结合生产的实际需要,搭建103#矿热炉优化控制系统,以达到如下目标:1.通过建立电极位置模型,在线检测电极的升降量和压放量,实现电极自动升降和自动压放;并通过采用合理的算法,计算电极长度及其位置,控制电极处于最优位置区域内,使三相有功功率平衡度在原有基础上提高2-3%,提高功率因数。
2.通过建立实时数据库,实时采集熔炼过程数据,实现整个矿热炉控制系统的运行监视、事故报警与记录、统计分析和报表打印、日常生产管理以及安全管理等功能,并实现变压器的继电保护。
3.通过对矿热炉供电网电能质量在线检测与监视,实时监测电极升降压放等操作和供电电流电压、功率因数的对应状态,分析三相不平衡、无功损耗及其对用电设备的影响,分析谐波损耗及其波形畸变用电设备的影响,使电能质量各项指标的监测精度达到2%以上。
HX-3t电弧炉电极控制系统

3系统主要保护 . () 1 电极最大上 升速度 。石 墨电极一旦 和炉 内钢液短路 , 弧 流实际值将远大于设定值 ,此 时 P C输 出电压信号 为负最大 , L 电极 以程序 中设定 的最大速度提升 , 减小弧流 。 调整最大上升速 度 的原则是 电弧炉可在 5 6 消除短路现象。 ~s
流、 弧压实 际值 ,L P C应用程序对这些信号进行转换 、 比较判断 、
块转换为变化 的模拟 电压信号( 1V)分别输入至变频器 1 2 ±0 , 、、
代数运算、I P 运算等处理后 , 给出综合控制信号 , 模转换模 实际值等于设定值, 经数, 此后电极将根据起弧电流设定值不断波动,
3 变频器根据 电压信号 幅度 和极性控制 电机转速和转 向 , , 电机
带动减速器控制三相 电极升降和速度 。
2弧流 调 节 .
压( 功率 ) 不可过高 , 否则 电弧较长 , 易烧坏炉顶 。 点弧阶段结束后 , 电炉进 入熔 化期 , 电极不 断下 降 , 炉料 完 全包 围电弧 , 几乎 吸收全部热量 , 不会破 坏炉衬 , 此时可输入最
T 2 .+ M6 1 3 7
实施 过 程 。
电除尘 系统
文献标 识码
应用
B
中图分类号
~
、
P 实 时 数 据 库 系 统 I
该 系统是美 国 O IS f ae 司开发 的基 于 CS BS结构 S o w r 公 t /、 /
。 互 。
系 统 主
赂 系 统主
系 统 主机 串行 通 信 服 务 器
() 2 堵转保 护。 电极升 降过程 中遇到 障碍 物或不导 电炉料 时, 电机将 堵转 。P C采集电机反馈电流信号 , L 经过运算 、 比较 ,
交流电弧炉电极升降过程控制系统

交流电弧炉电极升降过程控制系统谢良伟龙景文电极升降调节器是炼钢电弧炉的关键设备,一个好的调节器,对降低能耗、电极消耗、设备故障率起着很大的作用。
本文介绍的是一种基于工控机与单片机相结合实现的液压交流电弧炉电极升降自动控制系统。
1 系统的配置与功能系统配置结构图如图1所示。
图1 系统结构图B、C相与A相一致1.1 上位机上位机采用PC 486 DX4-100的基本配置一体化工控机(液晶显示器),主要实现对各种参数的在线调整、修改,弧压、弧流等参数量的动态显示。
1.2 下位机下位机部分为系统的主要调节系统,由三相(A、B、C)调节板、电源与数显板、功放板组成。
三相调节板和电源与数显板均采用AT89C52作为单片机系统。
相调节板每相的弧流、弧压信号经过LEM模块的信号变换,分别把0~300V 的弧压信号和0~5A的弧流信号转换为0~5V的标准信号,把弧流(0~15kA)给定信号也变为0~5V的标准信号一同输入计算机。
单片机通过A/D把它们转换为数字量,然后通过阻抗运算及智能控制算法使D/A输出±5V范围内电压,再经过隔离器、运放输出±10V电压。
此外,板上带485驱动芯片MAX485、参数存储器EEPROM、微处理器监控电路。
电源与数显板由单片机实现档位的显示及调节板来的数据弧流给定显示,并给系统其它各板提供+5V、+24V的电压。
该板LED驱动芯片选用MAX7219作4位2排LED显示档位/档位电压、给定弧流,其原理框图如图2所示。
图2 电源与数显板原理框图功放驱动板相调节板输出的信号,经高压运放处理后,最后输出0~100MA 电流。
1.3 系统的特点(1)上位机采用高分辨率大液晶显示器,受电磁干扰影响小。
(2)输入输出完全隔离,弧压、弧流信号采用霍尔元件(LEM),摒弃了变压器,LEM模块线性度非常好且隔离电压达2500V,这样既保证了信号采集精度,又能保护单片机系统。
模拟量输出采用BB公司的ISO 212隔离,使系统抗干扰能力很强。
电弧炉电极自动控制系统的实现

率的限制 。 当输入 信号 的电压值在参考电压上下波动时, 不能
有效的得到数据。光电耦合器采用P78可以实现与前级的 C1,
隔离, 并且有效地得到数据。当 L33 1 引脚输 出低电位 M9 的 号 时, 光电耦合器 P1 C 导通, L33 I 当 M9 的 号引脚输出高电位时,
保证三相 电流 的平衡输入 , 产品质量非常不稳定 。因此有必 要把电极 自 动控制系统 的实 现加 以推广 , 提高生产效率 。本
文主要介绍在 电弧炉 电极控 制的具体实 现方法 , 对于其它型
号 的电弧炉可 以根据 电流 的不 同选择不 同型号的交 流互 感 器转化为 o5, -A重新调整 电位器设定参考 电压 的数值, 可 就 以实现 电极的 自 控制。 动
电 极 自 动 控 制 系 统 的 实
现
( 贵州大学机械工程学 院,贵州 贵 阳 500) 503
(c o l o eh n c l E gn e i g u zo n vr i y uz o u y n 50 3 Sh o f M c a ia n i e rn ,G i h uU i e s t ,G i hu G ia g 5 0 0 )
1 电极 自动控制 的硬件实现 1 1电流 的交流变送的实现 . 正常工作 时, 现对 A " 0 A变送 : A相 电流小于 实 C030 - 当
个作为备用 。这里使用 比较器得到数据, 就不采用 2D A 而节 约了资源 。当 P1 C 的输 出导通时,L 接受到信号 x, PC 1表明 A
t e c rr nt of a fu ac el tr e an co a wi h t e c mp r to h u e rc rn e ec od d mp re t h o a a r. T n t P wi c nt l th he he LC ll o ro e
电弧炉自动化控制系统介绍

电弧炉自动化控制系统介绍电弧炉自动化控制系统是一种应用现代技术手段进行炉温、炉容、馈电电流、馈电功率等参数自动控制的系统。
它能够有效提高电弧炉的熔炼质量和生产效率,并减少能源的消耗。
本文将详细介绍电弧炉自动化控制系统的原理、组成和优势。
一、原理电弧炉自动化控制系统的核心原理是通过传感器采集电弧炉的各项参数,如温度、电流、功率等,然后将采集到的参数信号传输给控制器进行处理。
控制器根据预设的控制策略,调节炉温、炉容、馈电电流、馈电功率等参数,从而实现对熔炼过程的自动控制。
二、组成1.传感器:传感器主要用于采集电弧炉的各项参数。
常用的传感器包括温度传感器、电流传感器、功率传感器等。
2.信号传输装置:信号传输装置用于将传感器采集到的参数信号传输给控制器。
常用的传输方式有有线传输和无线传输。
3.控制器:控制器是电弧炉自动化控制系统的核心部件,主要负责处理传感器采集到的参数信号,实现对熔炼过程的自动控制。
现在常用的控制器有PLC控制器和微处理器控制器等。
4.执行机构:执行机构根据控制器发出的控制信号,实现对电弧炉各项参数的调节。
常见的执行机构包括电动阀、电动门、变频器等。
三、优势1.提高熔炼质量:自动化控制系统可以精确控制炉温、炉容等参数,避免了人为操作的不稳定因素,提高了熔炼质量的稳定性和一致性。
2.提高生产效率:自动化控制系统可以实现对熔炼过程的实时监测和调节,减少了人工干预的次数和工作量,提高了生产效率。
3.节能减排:自动化控制系统根据实时数据进行智能调控,能够合理分配能源,达到最佳的控制效果,从而降低了能源的消耗和废气的排放。
4.增加安全性:自动化控制系统可以实现对熔炼过程的全程监控,及时发现和处理异常情况,提高了生产安全性。
5.数据分析和故障诊断:自动化控制系统可以对采集到的数据进行存储、分析和处理,提供数据报表和故障诊断功能,帮助企业优化生产过程和维修管理。
总结:电弧炉自动化控制系统是一种应用现代技术手段对电弧炉的熔炼过程进行自动控制的系统。
电弧炉控制系统方案
五矿(湖南)铁合金有限责任公司103#硅锰合金冶炼炉优化控制系统方案设计说明书中南大学信息科学与工程学院二○一○年三月一、开发背景五矿(湖南)铁合金集团有限公司103#10000KVA矿热炉主要用于熔炼硅锰合金和碳锰合金,整个生产系统由炉体、供电变压器及保护系统、配加料系统、电极卷扬升降控制系统、电极压放子系统和炉体水冷系统等组成。
目前,配加料子系统采用了计算机自动控制;电极压放子系统依靠人工凭经验综合考虑炉况、二次电压、一次电流、熔炼时间等因素,输入控制信号给PLC,由PLC来完成电极的定长压放;电极升降是依靠人工凭经验综合考虑二次电压、一次电流及炉盖温度等因素进行调节;供电变压器二次侧电压等级靠人工根据炉况和电压、电流、功率等因素凭经验进行调整。
这种靠人工凭经验来控制冶炼过程的方法难以保证矿热炉稳定持续地工作在最佳工作范围内,调节过程相对滞后、工人操作强度大、工作效率低,容易出现电极烧结不好、耗电量大、炉况不稳定等问题,难以保证产品的产量和质量。
二、设计要求针对五矿(湖南)铁合金集团有限公司103#矿热炉熔炼过程控制自动水平低下带来的各种问题,通过现场调研和与工艺技术人员交流沟通,结合生产的实际需要,搭建103#矿热炉优化控制系统,以达到如下目标:1.通过建立电极位置模型,在线检测电极的升降量和压放量,实现电极自动升降和自动压放;并通过采用合理的算法,计算电极长度及其位置,控制电极处于最优位置区域内,使三相有功功率平衡度在原有基础上提高2-3%,提高功率因数。
2.通过建立实时数据库,实时采集熔炼过程数据,实现整个矿热炉控制系统的运行监视、事故报警与记录、统计分析和报表打印、日常生产管理以及安全管理等功能,并实现变压器的继电保护。
3.通过对矿热炉供电网电能质量在线检测与监视,实时监测电极升降压放等操作和供电电流电压、功率因数的对应状态,分析三相不平衡、无功损耗及其对用电设备的影响,分析谐波损耗及其波形畸变用电设备的影响,使电能质量各项指标的监测精度达到2%以上。
电弧炉操作系统设计介绍
电弧炉操作系统设计介绍电弧炉操作系统是用于控制和监控电弧炉工作的一种软件系统。
它通过实时监测电弧炉的温度、电流、电压等参数,对电弧炉进行自动控制,从而提高生产效率、降低能耗、减少人工操作。
本文将就电弧炉操作系统设计进行详细介绍。
首先,电弧炉操作系统的设计需要考虑到以下几个方面:1.实时监测:电弧炉操作系统需要实时监测电弧炉的温度、电流、电压等参数,以便及时调整工作状态。
这需要使用传感器来采集数据,并将数据传输给操作系统进行处理。
2.自动控制:根据实时监测到的数据,电弧炉操作系统需要自动调整电弧炉的工作状态,以维持合适的温度、电流、电压等参数。
这需要使用控制算法来分析数据,并输出控制信号给电弧炉进行调整。
3.故障诊断:电弧炉操作系统需要能够检测电弧炉的故障,并实时报警。
这需要使用故障检测算法来分析数据,并输出警报信号。
同时,操作系统还需要能够记录故障信息,以便后续分析和改进。
4.界面设计:电弧炉操作系统需要提供人机交互的界面,以方便操作员进行监控和调整。
这需要设计友好的界面,使操作员能够清楚地了解电弧炉的工作状态,并进行相应的调整。
基于以上考虑,电弧炉操作系统的设计可以分为以下几个模块:1.数据采集模块:该模块负责采集电弧炉的温度、电流、电压等参数。
它通过传感器实时监测电弧炉的工作状态,并将采集到的数据传输给后续模块进行处理。
2.数据处理模块:该模块负责对采集到的数据进行处理和分析。
它根据预设的控制算法,分析数据并输出控制信号给电弧炉进行相应的调整。
3.故障检测模块:该模块负责检测电弧炉的故障,并进行实时报警。
它根据预设的故障检测算法,分析数据并输出警报信号。
同时,它还负责记录故障信息,以便后续分析和改进。
4.用户界面模块:该模块负责提供人机交互的界面。
它将电弧炉的工作状态以图形化的方式展示给操作员,使其能够清楚地了解电弧炉的工作状态,并进行相应的调整。
为了确保电弧炉操作系统的可靠性和稳定性,还需要考虑以下几个方面:1.备份与恢复:为了避免数据丢失或系统崩溃造成的停工损失,应该在系统中加入备份与恢复机制。
真空自耗电弧炉控制系统的集散控制方案设计及实现
真空自耗电弧炉控制系统的集散控制方案设计及实现通过集散控制方案在真空自耗电弧炉上的应用,同时运用先进的西门子工业网络通信技术和西门子可编程控制器、直流调速器结合现场变送器实现了真空自耗电弧炉整个生产过程中的自动化控制,使用西门子上位软件完成自动化工艺管理、现场监控、报警显示功能。
标签:集散控制;可编程控制器;工业网络;通信技术;真空自耗电弧炉前言随着钛及钛合金在国防、航空、核设施、能源、化工等高精尖领域的广泛应用,国内外用户对钛产品生产的质量跟踪、实时监控、生产工艺现场控制、设备安全联锁等提出了更高的要求,这也是电弧炉电气自动控制的发展方向。
传统继电控制系统稳定性差、可靠性降低,系统控制方式落后,控制精度低等问题,落后的控制方式使铸锭生产处于熔化不均匀,表面质量较差等低性能高成本运行状态,对生产管理、工艺质量和设备安全运行产生不利的影响。
随着计算机可靠性不断提高以及电气自动控制水平的发展,集散控制系统弥补了传统的集中式控制系统的缺陷,实现了控制室与集散控制站或PLC之间的网络通讯,实现系统监控的实时性,并且大量的减少了控制室与现场之间的电缆数目、设备故障率低。
因此,通过运用集散式控制方案、采用自动控制的先进技术解决了真空自耗电弧炉目前存在的工艺和设备方面的问题,提高了钛铸锭产品的质量和生产的水平。
1 电控系统控制要点真空自耗电弧炉的主要组成包括:由炉体、坩埚、电极杆及传动装置组成的机械系统;还包括真空系统、冷却水系统、液压系统、气压系统、电源部分及其以上系统的电气控制系统。
2 电控系统构成真空自耗电弧炉电气控制系统由计算机控制系统、电气设备、仪器传感器等三个部分组成。
系统采用集散控制方案设计,包括西门子S7300可编程控制系统,循环冷却水控制系统,皮拉尼电阻真空传感器,电子称重系统,伺服控制系统,直流调速系统,摄像监控系统,计算机控制系统。
下位控制器采用西门子S7-300控制系统。
采用主从现场总线的工作方式,包括CPU中央处理器,24V直流开关电源、输入输出模块,ET200总线模块。
103#电弧炉控制系统方案
五矿(湖南)铁合金有限责任公司103#硅锰合金冶炼炉优化控制系统方案设计说明书中南大学信息科学与工程学院二○一○年三月一、开发背景五矿(湖南)铁合金集团有限公司103#10000KVA矿热炉主要用于熔炼硅锰合金和碳锰合金,整个生产系统由炉体、供电变压器及保护系统、配加料系统、电极卷扬升降控制系统、电极压放子系统和炉体水冷系统等组成。
目前,配加料子系统采用了计算机自动控制;电极压放子系统依靠人工凭经验综合考虑炉况、二次电压、一次电流、熔炼时间等因素,输入控制信号给PLC,由PLC来完成电极的定长压放;电极升降是依靠人工凭经验综合考虑二次电压、一次电流及炉盖温度等因素进行调节;供电变压器二次侧电压等级靠人工根据炉况和电压、电流、功率等因素凭经验进行调整。
这种靠人工凭经验来控制冶炼过程的方法难以保证矿热炉稳定持续地工作在最佳工作范围内,调节过程相对滞后、工人操作强度大、工作效率低,容易出现电极烧结不好、耗电量大、炉况不稳定等问题,难以保证产品的产量和质量。
二、设计要求针对五矿(湖南)铁合金集团有限公司103#矿热炉熔炼过程控制自动水平低下带来的各种问题,通过现场调研和与工艺技术人员交流沟通,结合生产的实际需要,搭建103#矿热炉优化控制系统,以达到如下目标:1.通过建立电极位置模型,在线检测电极的升降量和压放量,实现电极自动升降和自动压放;并通过采用合理的算法,计算电极长度及其位置,控制电极处于最优位置区域内,使三相有功功率平衡度在原有基础上提高2-3%,提高功率因数。
2.通过建立实时数据库,实时采集熔炼过程数据,实现整个矿热炉控制系统的运行监视、事故报警与记录、统计分析和报表打印、日常生产管理以及安全管理等功能,并实现变压器的继电保护。
3.通过对矿热炉供电网电能质量在线检测与监视,实时监测电极升降压放等操作和供电电流电压、功率因数的对应状态,分析三相不平衡、无功损耗及其对用电设备的影响,分析谐波损耗及其波形畸变用电设备的影响,使电能质量各项指标的监测精度达到2%以上。
- 1、下载文档前请自行甄别文档内容的完整性,平台不提供额外的编辑、内容补充、找答案等附加服务。
- 2、"仅部分预览"的文档,不可在线预览部分如存在完整性等问题,可反馈申请退款(可完整预览的文档不适用该条件!)。
- 3、如文档侵犯您的权益,请联系客服反馈,我们会尽快为您处理(人工客服工作时间:9:00-18:30)。
五矿(湖南)铁合金有限责任公司103#硅锰合金冶炼炉优化控制系统方案设计说明书中南大学信息科学与工程学院二○一○年三月一、开发背景五矿(湖南)铁合金集团有限公司103#10000KV A矿热炉主要用于熔炼硅锰合金和碳锰合金,整个生产系统由炉体、供电变压器及保护系统、配加料系统、电极卷扬升降控制系统、电极压放子系统和炉体水冷系统等组成。
目前,配加料子系统采用了计算机自动控制;电极压放子系统依靠人工凭经验综合考虑炉况、二次电压、一次电流、熔炼时间等因素,输入控制信号给PLC,由PLC来完成电极的定长压放;电极升降是依靠人工凭经验综合考虑二次电压、一次电流及炉盖温度等因素进行调节;供电变压器二次侧电压等级靠人工根据炉况和电压、电流、功率等因素凭经验进行调整。
这种靠人工凭经验来控制冶炼过程的方法难以保证矿热炉稳定持续地工作在最佳工作范围内,调节过程相对滞后、工人操作强度大、工作效率低,容易出现电极烧结不好、耗电量大、炉况不稳定等问题,难以保证产品的产量和质量。
二、设计要求针对五矿(湖南)铁合金集团有限公司103#矿热炉熔炼过程控制自动水平低下带来的各种问题,通过现场调研和与工艺技术人员交流沟通,结合生产的实际需要,搭建103#矿热炉优化控制系统,以达到如下目标:1.通过建立电极位置模型,在线检测电极的升降量和压放量,实现电极自动升降和自动压放;并通过采用合理的算法,计算电极长度及其位置,控制电极处于最优位置区域内,使三相有功功率平衡度在原有基础上提高2-3%,提高功率因数。
2.通过建立实时数据库,实时采集熔炼过程数据,实现整个矿热炉控制系统的运行监视、事故报警与记录、统计分析和报表打印、日常生产管理以及安全管理等功能,并实现变压器的继电保护。
3.通过对矿热炉供电网电能质量在线检测与监视,实时监测电极升降压放等操作和供电电流电压、功率因数的对应状态,分析三相不平衡、无功损耗及其对用电设备的影响,分析谐波损耗及其波形畸变用电设备的影响,使电能质量各项指标的监测精度达到2%以上。
4.在保证产品质量的前提下,根据用电制度和造渣制度,综合考虑原料成分和品位、产品成分、矿热炉设备参数、熔炼过程状态参数等因数的影响,建立生产过程优化控制模型,优化供电电压等级及电极插入深度,提高稳定运行率5%以上。
三、设计方案3.1系统总体结构五矿(湖南)铁合金集团有限公司103#矿热炉优化控制系统由电极位置自动控制子系统、生产过程参数集中监视子系统、生产设备故障监测与预警子系统、生产过程优化控制子系统、电能质量在线检测与综合分析子系统五部分组成,系统的整体结构如图1所示。
图1103#矿热炉优化控制系统总体结构3.2系统功能介绍电极位置自动控制包括电极位置检测和电极位置控制两大部分。
电极位置检测的目的是建立电极位置模型,通过在线检测电极的升降量和压放量,计算电极长度及其位置。
电极位置检测和长度的计算采用间接测量法求得,电极位置模型为电极长度模型为:式中,0L 为电极的初始位置;sj L ∆为实测电极升降量;y L ∆为电极的压放量;xh L ∆为电极的正常损耗量;yx L ∆为电极异常损耗量;cd L 为电极的长度;cs L 为电极的初始长度。
sj L L ∆+0由绝对式光电编码器检测得到;y L ∆由次数*固定压放量统计得到;xh L ∆由炉料消耗量、生产过程状态参数、产量等推断可得到一个较准确的消耗速率(此速率可以根据路况不同更改),累积超过30mm 提示压放。
yx L ∆可由手动输入估计的异常消耗量,超过30mm 提示压放。
电极位置控制的主要包括电极升降控制和电极的压放控制。
电极升降控制的目标是保持电极插入位置最佳,实现三相熔池有功功率平衡、有功功率大、功率因数高、线路电流小,保持较好的炉况。
电极压放控制的目标是通过压放电极来补充电极的消耗量,以保持电极工作端的长度最佳。
1. 电极升降控制矿热炉冶炼过程中,因为工况复杂,干扰较多,三相电极的最优位置会实时改变。
为使电极稳定工作于最优位置区域内,可通过升降电极来实现三相熔池有功功率平衡、有功功率大、功率因数高、线路电流小,并维持最佳的炉况。
电极升降控制分为手动控制和自动控制两种方式,自动升降控制系统结构如图2所示。
图2电极自动升降系统系统结构图但因为矿热炉冶炼过程复杂,在冶炼过程中可能会出现一些特殊情况。
为了能应对矿热炉冶炼过程中可能出现的各种情况,设置不同的电极调节方法:炉况正常时,采用最优位置控制此时控制信号由电极目前所处位置、最优插入深度和控制算法求得。
最优电极位置可由人工凭经验来设定,也可通过对大量历史数据(如电压、电流、有功功率、功率因数、炉气成分、炉膛温度等)分析,综合专家经验知识,经建模和优化计算得到。
电极最优位置稳定控制结构如图3所示,图3电极最优位置稳定控制结构图其中qw L ∆为电极设定的最优升降量,sj L ∆为电极实际升降量。
控制器根据实际升降量与电极设定最优升降量差值的大小来给定频率和升降时间,当差值较大时采用较高速度升降电极;当差值较小或炉况不稳定时,采用较低速度升降电极。
◆当电流下降或上升幅度过大时,采用恒电流控制此时控制信号由一次侧电流决定,以便使电路中的电流快速地恢复到正常工作范围之内。
◆不可抬升电极的情况处理出铁时,为防止出现塌料,出铁口附近的电极不能上抬;电极出现异常时,如中间凹陷,则一般不能抬升。
◆故障情况下电极的处理当矿热炉自动控制系统出现故障时,系统给出相关状态信息并报警,提示操作人员切换到手动控制,以保证矿热炉的正常生产。
2.电极压放控制因为硅锰合金冶炼是连续进行的,随着冶炼过程的进行,电极会不断消耗,电极的工作端逐渐变短,其插入位置不断上移。
为确保矿热熔炼炉处于最佳的熔炼状态,电极的插入位置必须要在适宜的范围内,因此,需要对电极的消耗不断进行补充。
电极压放控制系统的主要功能是通过压放电极来补充电极的消耗量,从而调整电极的插入位置。
电极压放控制系统原理如图4所示。
图4电极压放控制系统原理图为确保放系统能可靠工作,根据生产的需要,设置了三种不同的压放方式:自动压放、手动压放和现场压放,具体的控制方式描述如下。
(1)自动压放自动压放在电炉操作室内完成,这也是系统的主要运行方式。
相关检测与控制信号与PLC相连,由与PLC相连的上位机据谐波检测仪的分析结果及炉况最优化控制算法输出控制信号,经PLC根据相应状态检测信号自动控制相应电磁阀的起停,从而完成电极压放各环节之间的协调动作,实现电极自动定长压放。
决定电极是否压放的因素包括二次侧电压、一次电流、有功功率、功率因素、及炉况、炉盖温度等。
如二次侧电压过高、二次电流过小或炉盖温度过高时则需要进行压放。
系统三相功率不均衡或功率因素过低时,综合考虑电极升降来作适当的压放操作。
自动压放控制的思想如图5所示。
图5自动压放系统结构电极自动压放的具体工作流程为:工业控制计算机获取谐波检测仪分析所得的电炉一次侧电流、电压、有功功率、功率因素等信号及PLC采集得到的炉况、炉盖温度、液压系统状态等信号,结合当前各项电极位置,据最优化控制算法,判断各相电极是否需要压放并输出相应电极位置控制信号——PLC获取控制信号,开始压放相应电极——输出“上闸松”信号——对上闸液压压力继电器进行采样,直至其反馈状态为“松”,输出“立缸升”信号——对“立缸上限”行程开关进行采样,直至其被触发,输出“上闸紧”信号——对上闸液压压力继电器进行采样,直至其反馈状态为“紧”,输出“下闸松”信号——对下闸液压压力继电器进行采样,直至其反馈状态为“松”,输出“铜瓦松”信号——对铜瓦液压压力传感器进行采样,直至其压力下降至2.5Mpa(待确定),输出“立缸降”信号——对“压放量”通道进行采样,直至压放量达到规定值,输出“下闸紧”信号——对下闸液压压力继电器进行采样,直至其反馈状态为“紧”,输出“铜瓦紧”信号——对铜瓦液压压力传感器进行采样,直至其压力上升至4Mpa。
至此,一次压放过程结束。
期间,若在设定时间内任一路压力继电器或行程开关未能达到期望状态,则停止压放过程并输出相应报警信号。
(2)手动压放手动压放在电炉操作室内完成。
当上位机出现故障或系统中元器件出现故障,不能进行自动压放时,为确保矿热炉生产系统的正常工作,需要人工控制PLC进行电极压放。
在该方式下,由操作人员通过操作面板上的相应切换开关及按钮,将控制信号输入PLC,再由PLC完成电极的压放。
手动压放的思想如图6所示图6电极压放控制系统手动压放系统结构图其具体操作流程为:各切换开关至0°——运行方式选择“手动压放”——按下“试灯”按钮,若所有状态指示灯均正常亮起,继续操作——选相(左45°:A相;右45°B相;右90°:C相)——上闸松(右45°,等待“上闸松”信号灯亮)——立缸升(右45°,等待“立缸上限”信号灯亮)——上闸紧(0°,等待“上闸紧”信号灯亮)——下闸”松(右45°,等待“下闸松”信号灯亮)——铜瓦松(右45°,等待“铜瓦松”信号灯亮)——立缸降(左45°,等待“立缸下限”信号灯亮)——下闸紧(0°,等待“下闸紧”信号灯亮)——铜瓦紧(0°,等待“铜瓦紧”信号灯亮)——立缸手柄回0°——选相开关回0°。
至此,一次压放操作完成。
若操作过程中,某信号灯在较长时间内没达到期望状态,则应立即停止压放操作并检查系统,查找故障。
注:做完每次压放后,所有切换开关需要还原至0°,每次压放之前亦须确保各切换开关均处在0°位置。
(3)现场压放现场压放在液压站内进行。
用于当PLC压放系统出现故障无法工作或特殊情况下需要观察电极情况进行操作时使用。
因为操作过程中可以直接看到电极的升降及上下抱闸和立缸的工作情况,建议使用现场压放完成倒拔电极过程。
在该方式下,由有经验的操作人员直接观察液压站内的油压表读数及电极情况,控制与电磁阀直接相连的切换开关,完成电极压放的相应操作。
该过程不需要PLC或工业控制计算机的参与。
根据实际需要,现场压放分压放和倒拔两个过程,具体操作方法如下:压放过程:运行方式选择“现场压放”——选相——上闸松(右45°,上闸进油压力指示上升至4MPa)——立缸升(右45°,观察立缸上升距离至所要求值,要求不能达到最高位)——立缸手柄回“0”位(垂直位置)——上闸紧(0°,上闸进油压力指示降至0MPa)——下闸松(右45°,下闸进油压力指示上升至4MPa)——铜瓦松(铜瓦进油压力指示降至2.5MPa)——立缸降(左45°,观察立缸下降距离至所要求值,要求至最低位)——立缸手柄回“0”位——下闸紧(0°,下闸进油压力指示降至0MPa)——铜瓦紧(铜瓦进油压力指示上升至4.5MPa),压放完成。