发动机热管理系统优化外文文献翻译、中英文翻译、外文翻译
热能 外文翻译 外文文献 英文文献 火力发电厂先进的蒸汽温度调节控制算法
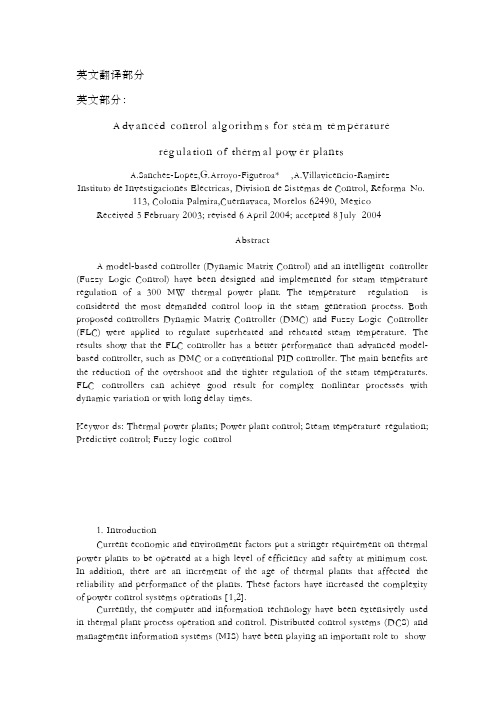
英文翻译部分英文部分:A dv anced control a lg orithm s for stea m te m peraturereg u l a tion of therm a l pow e r plantsA.Sanchez-Lopez,G.Arroyo-Figueroa* ,A.Villavicencio-Ramirez Instituto de Investigaciones Electricas, Division de Sistemas de Control, Reforma No.113, Colonia Palmira,Cuernavaca, Morelos 62490, Mexico Received 5 February 2003; revised 6 April 2004; accepted 8 July 2004AbstractA model-based controller (Dynamic Matrix Control) and an intelligent controller (Fuzzy Logic Control) have been designed and implemented for steam temperature regulation of a 300 MW thermal power plant. The temperature regulation is considered the most demanded control loop in the steam generation process. Both proposed controllers Dynamic Matrix Controller (DMC) and Fuzzy Logic Controller (FLC) were applied to regulate superheated and reheated steam temperature. The results show that the FLC controller has a better performance than advanced model-based controller, such as DMC or a conventional PID controller. The main benefits are the reduction of the overshoot and the tighter regulation of the steam temperatures. FLC controllers can achieve good result for complex nonlinear processes with dynamic variation or with long delay times.Keywor ds: Thermal power plants; Power plant control; Steam temperature regulation; Predictive control; Fuzzy logic control1.IntroductionCurrent economic and environment factors put a stringer requirement on thermal power plants to be operated at a high level of efficiency and safety at minimum cost. In addition, there are an increment of the age of thermal plants that affected the reliability and performance of the plants. These factors have increased the complexity of power control systems operations [ 1,2].Currently, the computer and information technology have been extensively used in thermal plant process operation and control. Distributed control systems (DCS) and management information systems (MIS) have been playing an important role to showthe plant status. The main function of DCS is to handle normal disturbances and maintain key process parameters in pre-specified local optimal levels. Despite their great success, DCS have little function for abnormal and non-routine operation because the classical proportional-integral-derivative (PID) controlis widely used by the DCS. PID controllers exhibit poor performance when applied to process containing unknown non-linearity and time delays. The complexity of these problems and the difficulties in implementing conventional controllers to eliminate variations in PID tuning motivate the use of other kind of controllers, such as model-based controllers and intelligent controllers.This paper proposes a model-based controller such as Dynamic Matrix Controller (DMC) and an intelligent controller based on fuzzy logic as an alternative control strategy applied to regulate the steam temperature of the thermal power plant. The temperature regulation is considered the most demanded control loop in the steam generation process. The steam temperature deviation must be kept within a tight variation rank in order to assure safe operation, improve efficiency and increase the life span of the equipment. Moreover, there are many mutual interactions between steam temperature control loops that have been considered. Other important factor is the time delay. It is well know that the time delay makes the temperature loops hard to tune. The complexity of these problems and difficulties to implement PID conventional controllers motivate to research the use of model predictive controllerssuch as the DMC or intelligent control techniques such as the Fuzzy Logic Controller (FLC) as a solution for controlling systems in which time delays, and non-linear behavior need to be addressed [3,4]. The paper is organized as follows. A brief description of the DMC is presented in Section 2. The FLC design is described in Section 3. Section 4 presents the implementation of both controllers DMC and FLC to regulate the superheated and reheated steam temperature of a thermal power plant. The performance of the FLC controller was evaluated against two other controllers, the conventional PID controller and the predictive DMC controller. Results are presented in Section 5. Finally, the main set of conclusions according to the analysis and results derived from the performance of controllers is presented in Section 6.2.Dynamic matrix controlThe DMC is a kind of model-based predictive control (Fig. 1). This controller was developed to improve control of oil refinement processes [5]. The DMC and other predictive control techniques such as the Generalized Predictive Control [ 6] or Smith predictor [ 6] algorithms are based on past and present information of controlled and manipulated variables to predict the future state of the process.The DMC is based on a time domain model. This model is utilized to predict the future behavior of the process in a defined time horizon (Fig. 2). Based on this precept the control algorithm provides a way to define the process behavior in the time, predicting the controlled variables trajectory in function of previous control actions and current values of the process [ 7]. Controlled behavior can be obtained calculating the suitable future control actions. To obtain the process model, the system isperturbed with an unitary step signal as an input disturbance (Fig. 3).This method is the most common and easy mean to obtain the dynamic matrix coefficients of the process. The control technique includes the followings procedures:(a)Obtaining the Dynamic Matrix model of the process. In this stage, a step signal is applied to the input of the process. The measurements obtained with this activity represent the process behavior as well as the coefficients of the process state in time. This step is performed just once before the operation of the control algorithmin the process.(b)Determination of deviations in controlled variables. In this step, the deviation between the controlled variables of the process and their respective set points is measured.(c)Projection of future states of the process. The future behavior of each controlled variable is defined ina vector. This vector is based on previous control actions and current values of the process.(d)Calculation of control movements. Control movements are obtained using the future vector of error and the dynamic matrix of the process. The equation developed to obtain the control movements is shown below:where A represents the dynamic matrix, AT the transpose matrix of A X the vector of future states of the process, f a weighting factor, I the image matrix and D he future control actions. Further details about this equation are found in Ref. [ 5].(e)Control movements’implementation. In this step the first element of the control movements’vector is applied to manipulated variables. A DMC controllerallows designers the use of time domain information to create a process model. The mathematical method for prediction matches the predicted behavior and the actual behavior of the process to predict the next state of the process. However, the process model is not continuously updated because this involves recalculations that can lead to an overload of processors and performance degradation.Discrepancies in the real behavior of the process and the predicted state are considered only in the current calculation of control movements. Thus, the controller is adjusted continuously based on deviations of the predicted and real behavior while the model remains static.3.Fuzzy logic controlFuzzy control is used when the process follows some general operating characteristic and a detailed process understanding is unknown or process model become overly complex. The capability to qualitatively capture the attributes of a control system based on observable phenomena and the capability to model the nonlinearities for the process are the main features of fuzzy control. The ability of Fuzzy Logic to capture system dynamics qualitatively and execute this qualitative schema in a real time situation is an attractive feature for temperature control systems [8]. The essential part of the FLC is a set of linguistic control rules related to the dual concepts of fuzzy implication and the compositional rule of inference [ 9].Essentially, the fuzzy controller provides an algorithm that can convert the linguistic control strategy, based on expert knowledge, into an automatic control strategy. In general, the basic configuration of a fuzzy controller has five main modules as it is shown in Fig. 4.In the first module, a quantization module converts to discrete values and normalizes the universe of discourse ofvarious manipulated variables (Input). Then, a numerical fuzzy converter maps crisp data to fuzzy numbers characterized by a fuzzy set and a linguistic label (Fuzzification). In the next module, the inference engine applies the compositional rule of inference to the rule base in order to derive fuzzy values of the control signal from the input facts of the controller. Finally, a symbolic-numerical interface knownas defuzzification module provides a numerical value of the control signal or increment in the control action. This is integrated by a fuzzy-numerical converter and a dequantization module (output).Thus the necessary steps to build a fuzzy control system are Refs. [ 10,11]: (a) input and output variables representation in linguistic terms within a discourse universe;(b)definition of membership functions that will convert the process input variables to fuzzy sets;(c)knowledge base configuration;(d)design of the inference unit that will relate input data to fuzzy rules of the knowledge base; and(e)design of the module that will convert the fuzzy control actions into physical control actions.4.ImplementationThe control of the steam temperature is performed by two methods. One of them is to spray water in the steam flow,mainly before the super-heater (Fig. 5). The sprayed water must be strictly regulated in order to avoid the steam temperature to exceed the design temperature range of G1% G5 8C). This guaranties the correct operation of the process, improvement of the efficiency and extension of the lifetime of the equipment. The excess of sprayed water in the process can result in degradation of the turbine. The water in liquid phase impacts on the turbine’s blades. The other process to control the steam temperature is to change the burner slope in the furnace, mainly in the reheated. The main objective ofthis manipulation is to keep constant the steam temperature when a change in load is made. The DMC, fuzzy logic and PID controllers were implemented in a full model simulator to control the superheated and reheated steam temperature. The simulator simulates sequentially the main process and control systems of a 300 MW fossil power plant. The simulator has the full models of each main element of the generation unit. These models let the simulator display the effects of a disturbance in each process variable.Dynamic matrix control (DMC)The matrix model of the process is the main component of the DMC. In this case the matrix model was obtained by a step signal in both the sprayed water flow and the burners’position.Fig.6 shows a block diagram of the DMC implementation in the steam superheating and reheating sections. The temperature deviations were used as the controller’s input. The sprayed water flow and slope of burners were used as the manipulated variables or controller’s output. The DMC performance was implemented using a prediction horizon of 10 s, a weighting factor in the last control actions of 1.2 and considering the last 30 movements executed. These parameters belong to the best available for this application in the study of the DMC performance [7].Fuzzy logic control (FLC)Seven fuzzy sets were chosen to define the states of the controlled and manipulated variables. The triangular membership functions and their linguistic representation are shown in Fig. 7. The fuzzy sets abbreviators belong to: NBZnegative big, NMZnegative medium, NSZnegative short, ZEZzero, PSZpositive short, PMZpositive medium and PBZpositive big.The design of the rule base in a fuzzy system is a very important part and a complex activity for control systems. Li et al. [ 11] proposed a methodology to develop the set of rules for a fuzzy controller based on a general model of a process rather than a subjective practical experience of human experts. The methodology includes analyzing the general dynamic behavior of a process, which can be classified as stable or unstable.In Fig. 7 the range of fuzzy sets are normalized to regulate the temperature within the 20% above or below the set point, the change of error within the G10%, and the control action are considered to be moved from completelyclose or 08 inclination to completely open or 908 of inclination in water flow valve and slope of burners, respectively. In the case of regulation of temperature, if therequirements change to regulate the temperature within a greater range, the methodology proposed by Li et al. [ 11] considers to apply a scale factor in the fuzzy sets. A time step response of a process can be classified as stable or unstable, as shown in Fig. 8. Characteristics of the four responses are contained in the responseshown by the second stable response. The approach also uses an error state space representation to show the inclusion of the four responses in the second stableone (Fig.9).A set of general rules can be built by using the general step response of a process (second order stable system):1.If the magnitude of the error and the speed of change is zero, then it is not necessary to apply any control action (keep the value of the manipulated variable).2.If the magnitude of the error is close to zero in a satisfactory speed, then it is not necessary to apply any control action (keep the value of the manipulated variable).3.If the magnitude of the error is not close to the system equilibrium point (origin of the phase plane diagram) then the value of the manipulated variable is modified in function of the sign and magnitude of the error and speed of change. The fuzzy control rules were obtained observing the transitions in the temperature deviations and their change rates considering a general step response of a process instead of the response of the actual process to be controlled. The magnitude of the control action depends on the characteristics of the actual process to be controlled and it is decided during the construction of the fuzzy rules. A coarse variable (few labels or fuzzy regions) produces a large output or control action, while a fine variable produces small one.Fig. 10 shows a representative step response of a secondorder system. Based on this figure, a set of rules can be generated. For the first reference range (I), it is necessary to use a fuzzy rule in order to reduce the rise time of the signal:Where E means the deviation, DE denotes the change rate and OA determinesthe output action required to regulate the controlled variable. Another rule can be obtained for this same region (I). The objective of this rule will be to reduce the overshoot in the system response:Analyzing the step response is possible to generate the fuzzy rule set for each region and point in the graph. Table 1shows the set of rules obtained using this methodology. The second and third columns represent the main combinations between the error and its change rate of eachvariable. The forth column indicates the necessary control action to control the process condition. The last column shows the reference points and ranges that belong to each fuzzy rule.5. Controllers performanceIn every case, the system was submitted to an increment in load demand [ 12]. The disturbance was a kind of ramp from 70 to 90% in the load. The load change rate was 10 MW /min, which represents the maximum speed of change in the load. The performance parameters evaluated belong to overshoot amplitude, response time, maximum value, integral error square, integral absolute error. Figs. 11 and 12 show the graphic results obtained by each controller in the superheated and reheated steam temperature control, respectively. In both cases the stability of the steam temperature is widely improved by the advanced control algorithms. In the same way, the steam temperature deviation from the set point is tightly regulated. Numerical results of the three controllers in the superheated and reheated steam temperature control are shown in Tables 2 and 3 respectively.The DMC reduced the superheated steam temperature overshoot almost 30% andthe response time 15% in relation to the PID controller response. The maximum deviation observed with respect to the reference is reduced 30% in relation to the PID controller. In the re-heater, the DMC reduced the steam temperature deviation almost 65% and the response time 60% in relation to the PID controller. The maximum value reached by the steam temperature is reduced significantly in the same comparison (65%). When a fuzzy controller is applied to the superheated steam temperature with the same disturbance as described before, the overshoot is reduced almost 80% in relation to the PID controller performance or 70% in relation to the DMC performance. There is no response time because the fuzzy controller keeps the steam temperature within a tight variation rank. The maximum deviation observed with respect to the reference is strongly reduced in relation to both the PID controller (80%) and the DMC (70%).。
汽车发动机外文文献翻译中英文参考
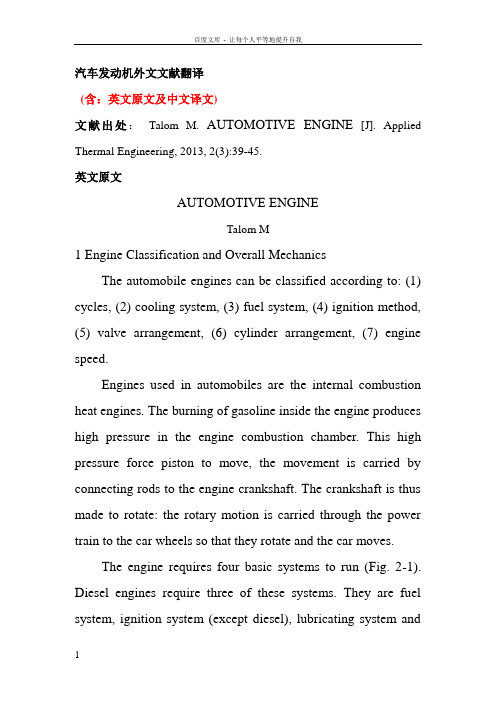
汽车发动机外文文献翻译(含:英文原文及中文译文)文献出处:Talom M. AUTOMOTIVE ENGINE[J]. Applied Thermal Engineering, 2013, 2(3):39-45.英文原文AUTOMOTIVE ENGINETalom M1 Engine Classification and Overall MechanicsThe automobile engines can be classified according to: (1) cycles, (2) cooling system, (3) fuel system, (4) ignition method, (5) valve arrangement, (6) cylinder arrangement, (7) engine speed.Engines used in automobiles are the internal combustion heat engines. The burning of gasoline inside the engine produces high pressure in the engine combustion chamber. This high pressure force piston to move, the movement is carried by connecting rods to the engine crankshaft. The crankshaft is thus made to rotate: the rotary motion is carried through the power train to the car wheels so that they rotate and the car moves.The engine requires four basic systems to run (Fig. 2-1). Diesel engines require three of these systems. They are fuel system, ignition system (except diesel), lubricating system andcooling system. However, three other related systems are also necessary. These are the exhaust system, the emission-control system, and the starting system. Each performs a basic job in making the engine run.2 Engine Operating PrinciplesThe term “stroke” is used to describe the movem ent of the piston within the cylinder. The movement of the piston from its uppermost position (TDC, top dead center) to its lowest position (BDC, bottom dead center) is called a stroke. The operating cycle may require either two or four strokes to complete. Most automobile engines operate on the four stroke cycle.In four-stroke engine, four strokes of the piston in the cylinder are required to complete one full operating cycle. Each stroke is named after the action. It performs intake, compression, power, and exhaust in that order.The intake strokeThe intake stroke begins with the piston near the top of its travel. As the piston begins its descent, the exhaust valve closes fully, the intake valve opens and the volume of the combustion chamber begins to increase, creating a vacuum. As the piston descends, an air/fuel mixture is drawn from the carburetor into the cylinder through the intake manifold. The intake stroke endswith the intake valve close just after the piston has begun its upstroke.Compression strokeAs the piston is moved up by the crankshaft from BDC, the intake valve closes. The air/fuel mixture is trapped in the cylinder above the piston. Future piston travel compresses the air/fuel mixture to approximately one-eighth of its original volume (approximately 8:1 compression ratio) when the piston has reached TDC. This completes the compression stroke. Power strokeAs the piston reaches TDC on the compression stroke, an electric spark is produced at the spark plug. The ignition system delivers a high-voltage surge of electricity to the spark plug to produce the spark. The spark ignites, or sets fire to, the air/fuel mixture. It now begins to burn very rapidly, and the cylinder pressure increases to as much as 3-5MPa or even more. This terrific push against the piston forces it downward, and a powerful impulse is transmitted through the connecting rod to the crankpin on the crankshaft. The crankshaft is rotated as the piston is pushed down by the pressure above it.Exhaust strokeAt the end of the power stroke the camshaft opens theexhaust valve, and the exhaust stroke begins. Remaining pressure in the cylinder, and upward movement of the piston, force the exhaust gases out of the cylinder. At the end of the exhaust stroke, the exhaust valve closes and the intake valve opens, repeating the entire cycle of events over and over again.3 Engine Block and Cylinder HeadEngine BlockThe engine block is the basic frame of the engine. All other engine parts either fit inside it or fasten to it. It holds the cylinders, water jackets and oil galleries (Fig. 2-4). The engine block also holds the crankshaft, which fastens to the bottom of the block. The camshaft also fits in the block, except on overhead-cam engines. In most cars, this block is made of gray iron, or an alloy (mixture) of gray iron and other metals, such as nickel or chromium. Engine blocks are castings.Some engine blocks, especially those in smaller cars, are made of cast aluminum. This metal is much lighter than iron. However, iron wears better than aluminum. Therefore, the cylinders in most aluminum engines are lined with iron or steel sleeves. These sleeves are called cylinder sleeves. Some engine blocks are made entirely of aluminum.Cylinder SleevesCylinder sleeves are used in engine blocks to provide a hard wearing material for pistons and piston rings. The block can be made of one kind of iron that is light and easy to cast while the sleeves uses another that is better able to stand up wear and tear.There are two main types of sleeves: dry and wet (Fig. 2-5).Dry sleeve Wet sleeveCylinder HeadThe cylinder head fastens to the top of the block, just as a roof fits over a house. The underside forms the combustion chamber with the top of the piston. In-line engine of light vehicles have just one cylinder head for all cylinders; larger in-line engines can have two or more. Just as with engine blocks, cylinder heads can be made of cast iron or aluminum alloy. The cylinder head carries the valves, valve springs and the rockers on the rocker shaft, this part of valve gear being worked by the pushrods. Sometimes the camshaft is fitted directly into the cylinder head and operates on the valves without rockers. This is called an overhead camshaft arrangement.GasketThe cylinder head is attached to the block with high-tensile steel studs. The joint between the block and the head must begas-tight so that none of the burning mixture can escape. This is achieved by using cylinder head gasket. Gaskets are also used to seal joins between the other parts, such as between the oil pan, manifolds, or water pump and the blocks.Oil PanThe oil pan is usually formed of pressed steel. The oil pan and the lower part of cylinder block together are called the crankcase; they enclose, or encase, the crankshaft. The oil pump in the lubricating system draws oil from the oil pan and sends it to all working parts in the engine. The oil drains off and run down into the pan. Thus, there is a constant circulation of oil between the pan and the working parts of the engine.4 Piston Assembly, piston rings, The piston pin ,Connecting Rods, Crankshafts And FlywheelPistonPiston rings and the piston pin are together called the piston assembly.The piston is an important part of a four-stroke cycle engine. Most pistons are made from cast aluminum. The piston, through the connecting rod, transfers to the crankshaft the force created by the burning fuel mixture. This force turns the crankshaft.To withstand the heat of the combustion chamber, the piston must be strong. It also must be light, since it travels at high speeds as it moves up and down inside the cylinder. The piston is hollow. It is thick at the top where it takes the brunt of the heat and the expansion force. It is thin at the bottom, where there is less heat. The top part of the piston is the head, or crown. The thin part is the skirt. Most pistons have three ring grooves at the top. The sections between the ring grooves are called ring lands.piston ringsPiston rings fit into ring grooves near the top of the piston. In simplest terms, piston rings are thin, circular pieces of metal that fit into grooves in the tops of the pistons. In modern engines, each piston has three rings. (Piston in older engines sometimes had four rings, or even five.) The inside surface of the ring fits in the groove on the piston. The ring's outside surface presses against the cylinder walls. Rings provide the needed seal between the piston and the cylinder walls. That is, only the rings contact the cylinder walls. The top two rings are to keep the gases in the cylinder and are called compression rings. The lower one prevents the oil splashed onto the cylinder bore fro m entering the combustion chamber, and is called an oil ring.The piston pinThe piston pin holds together the piston and the connecting rod. This pin fits into th e piston pin holes and into a hole in the top end of the connecting rod. The top end of t he rod is much smaller than the end that fits on the crankshaft. This small end fits inside the bottom of the piston. The piston pin fits through one side of the piston, through the small end of the rod, and then through the other side of the piston. It holds the rod firmly in place in the center of the piston. Pins are made of high-strength steel and have a hollow center. Many pins are chrome-plated to help them wear better. A piston pin fits into a round hole in the piston. The piston pin joins the piston to the connecting rod. The thick part of the piston that holds the piston pin is the pin boss. Connecting RodsThe connecting rod little end is connected to the piston pin.A bush made from a soft metal, such as bronze, is used for this joint. The lower end of the connecting rod f its the crankshaft journal. This is called the big end. For this big-end bearing, steel-backed lead or tin shell bearings are used. These are the same as those used for the main bearings. The split of the big end is sometimes at an angle, so that it is small enough t o be withdrawn through the cylinder bore. The connecting rod ismade from forged alloy steel.CrankshaftsThe crankshaft is regarded as the “backbone” of the engine (Fig. 2-7). The crankshaft, in conjunction with the connecting rod, converts the reciprocating motion of the piston to the rotary motion needed to drive the vehicle. It is usually made from car-bon steel which is alloyed with a small proportion of nickel. The main bearing journals fit into the cylinder block and the big end journals align with the connecting rods. At the rear end of the crankshaft is attached the flywheel, and at the front end are the driving wheels for the timing gears, fan, cooling water and alternator. The throw of the crankshaft, . the distance between the main journal and the big end centers, controls the length of the stroke. The stroke is double the throw, and the stroke length is the distance that the piston travels from TDC to BDC and vice versa.中文译文汽车发动机Talom M1发动机分类和一般力学(1)循环,(2)冷却系统,(3)燃料系统,(4)点火方法,(5)阀门布置,(6)气缸布置,(7)发动机速度。
中英文文献翻译-发动机冷却系统
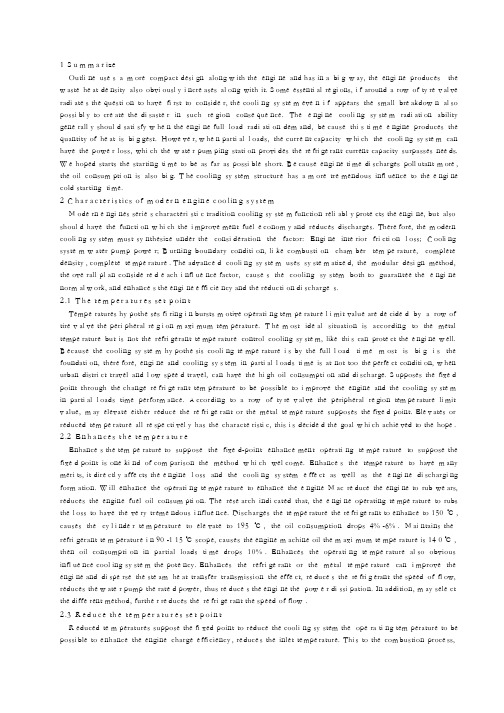
1S u m m a r i z eOutli ne use s a m ore compact desi gn along w ith the engi ne and has in a bi g w ay, the engi ne produces the w aste he at de nsity also obvi ousl y i ncre ases al ong with it. S ome essenti al re gi ons, i f around a row of ty re v al ve radi ate s the questi on to have fi rst to conside r, the cooli ng sy ste m eve n i f appears the small bre akdow n al so possi bl y to cre ate the di saste r in such re gion conse que nce. The e ngi ne cooli ng sy ste m radi ati on ability gene rall y shoul d sati sfy w he n the engi ne full load radi ati on dem and, be cause thi s ti me e ngine produces the quantity of he at is bi g gest. Howe ve r, w he n parti al l oads, the curre nt capacity w hi ch the cooli ng sy ste m can have the powe r loss, whi ch the w ate r pum ping stati on provi des the re fri ge rant current capacity surpasses nee ds. W e hoped starts the starting ti me to be as far as possi ble short. B e cause engi ne ti me di scharges poll utant m ore , the oil consum pti on is also bi g. T he cooling sy stem structure has a m ore tre mendous infl uence to the e ngi ne cold starting ti me.2C h a r a c t e r i s t i c s of m od e r n e n g in e c oo l in g s y s t e mM ode rn e ngi nes serie s characteri sti c tradition cooling sy ste m function reli abl y prote cts the engi ne, but also shoul d have the functi on w hi ch the i mprove ment fuel e conom y and reduces discharges. There fore, the m odern cooli ng sy stem must sy nthesize under the consi deration the factor: Engi ne inte rior fri cti on l oss; C ooli ng syste m w ater pump powe r; B urning boundary conditi on, li ke combusti on cham ber tem pe rature, complete density , complete te mpe rature . The advance d cooli ng sy ste m uses sy ste m atize d, the modular desi gn method, the ove rall pl an conside re d e ach i nfl ue nce factor, cause s the cooling sy stem both to guarantee the e ngi ne norm al w ork, and enhance s the engi ne e ffi cie ncy and the reducti on di scharge s.2 .1 T h e t e m p e r a t u r e s se t p o in tTempe ratures hy pothe ses fi ring i n bursts m otive operati ng tem pe rature l i mit value are de cide d by a row of tire v al ve the peri pheral re g i on m axi mum tem perature. T he m ost ide al situation is according to the metal tempe rature but is not the refri gerant te mpe rature control cooling sy ste m, like thi s can prote ct the e ngi ne w ell.B ecause the cooling sy ste m hy pothe sis cooli ng te mpe rature i s by the full l oad ti me m ost is bi g i s the foundati on, there fore, engi ne and cooling sy s tem in parti al l oads ti me is at not too the perfe ct conditi on, w hen urban distri ct travel and l ow spee d travel, can have the hi gh oil consumpti on and di scharge. S upposes the fixe d point through the change re fri ge rant tem perature to be possible to i mprove the engine and the cooling sy ste m in parti al l oads time perform ance. A ccording to a row of ty re v al ve the peripheral re gion tem pe rature li mit v alue, m ay elevate either reduce the re fri ge rant or the metal te mpe rature supposes the fixe d point. Ele v ates or reduced tem pe rature all re spe cti vel y has the characte risti c, this i s decide d the goal w hi ch achie ved to the hope .2 .2 E n h a n c e s t h e t e m p e r a tu r eEnhance s the tem pe rature to suppose the fixe d-point enhance ment operati ng te mpe rature to suppose the fixe d point is one ki nd of com parison the method w hi ch wel come. Enhance s the tempe rature to have m any meri ts, it dire ctl y affe cts the e ngine l oss and the cooli ng sy stem e ffe ct as well as the e ngi ne di schargi ng form ation. W ill enhance the operati ng te mpe rature to enhance the e ngine M ac re duce the engi ne to rub we ars, reduces the engine fuel oil consum pti on. The rese arch indi cated that, the e ngi ne operating te mpe rature to rubs the l oss to have the ve ry treme ndous i nflue nce. Discharges the te mpe rature the re fri ge rant to enhance to 150 ℃ , causes the cy l i nde r te m perature to ele vate to 195 ℃ , the oil consumption drops 4% -6% . M ai ntains the refri gerant te m perature i n 90 -1 15 ℃ scope, causes the engine m achine oil the m axi mum te mpe rature is 14 0 ℃ , then oil consumpti on in partial loads ti me drops 10% . Enhances the operati ng te mpe rature al so obvious infl ue nce cool ing sy ste m the pote ncy. Enhances the refri ge rant or the metal te mpe rature can i mprove the engi ne and di spe rse the ste am he at transfer transmission the effe ct, re duce s the re fri g erant the speed of fl ow, reduces the w ate r pump the rate d power, thus re duce s the engi ne the pow e r di ssi pation. In addition, m ay sele ct the diffe rent method, furthe r re duces the re fri ge rant the speed of flow .2 .3 R e d u c e th e t e m p e r a t u r e s se t p o i n tR educed te m peratures suppose the fi xed point to reduce the cooli ng sy stem the ope ra ti ng tem perature to be possi ble to e nhance the engine charge e ffi ciency , re duce s the inlet te mpe rature. Thi s to the com bustion proce ss,the fuel oil effi cie ncy and discharges adv antage ousl y . T he reduced tem perature supposes the fi xed poi nt to beall owed to save the engine m ove me nt cost, enhances the part servi ce li fe. The rese arch indi cate d, if the cy linde r he ad te mpe rature re duce s to 50 ℃ , the i gnition angle of advance m ay 3 ℃ A but not have the engi ne knock ahe ad of time , the charge effi cie ncy enhances 2 % , the e ngi ne ope rati onal factor i mprove ment, is hel pfulto the opti mize d com pre ssi on rati o and the paramete r choi ce, obtai ns the bette r fue l oil effi ciency anddischarges the pe rform ance.2 .4 P r e c i se c oolin g sy s t e mPre cise cooling sy stem s pre ci se cooli ng sy ste m mainl y m ani fests i n the cooli ng j acket s tructural desi gn andin the refri gerant spee d of fl ow desi gn. In pre cise cooling system, hot e ssenti al are a, i f around a row of ty re valve, the re fri ge rant has an gre ate r spee d of fl ow , the he at transfer effi cie ncy is hi gh, the refri gerant gradie ntof tem pe ra ture changes sli ghtl y . S uch e ffe ct comes from to re duce these pl ace re fri ge rant channels the l ate ralsecti on, e nhances the spee d of fl ow, re duce s the current capacity . T he pre ci se cooli ng sy ste m desi gn ke y lies inthe de termi nation cooli ng j acke t the size, the choi ce m atch cooling w ate r pum p, guaranteed the sy ste m theradi ati on ability can satisfy w hen the l ow spee d bi g load essenti al re g i on operating te m perature de m and. Theengi ne refri gerant spee d of fl ow range of vari ati on is quite bi g , from ti me 1 m /s to m axi mum w ork rate time 5m /s. The re fore shoul d conside re d the cooli ng j acket and the cooling sy stem whole that, m utuall y suppleme nted, displ ay bi gge st pote nti al. The rese arch indi cate d that, uses the pre cise cooling sy stem , i n the engi ne entirew ork rotational spee d scope , the refri gerant curre nt capacity m ay drop 4 0% . C ove rs the cool ing j acket to theai r cy linde r the pre cise de si gn, m ay m ake the ordi nary spee d of fl ow to e nhance from 1 .4 m /s to 4 m /s , gre atl y enhances the cy l inde r cove r or cap the rm al conducti vity , cy l inde r cove r or cap metal te mpe rature drop to60 ℃ .2 .5 Div e r g e n c e s t y p e s c oolin g s y s t e mDiverge nce s ty pe s cooli ng sy ste m dive rge nce ty pe cooli ng sy stem for othe r one ki nd of cool ing sy ste m. Inthis ki nd of cooli ng sy ste m, the hi ne oil te mpe rature , will cy l i nde r cove r or cap frie ndl y cy li nde r body cools by respective return route , the cyl inder cover or cap friendl y cyli nder body has the di ffe rent tem perature. T hedive rge nce -li ke cooli ng sy ste m has the uni que supe ri ority , m ay cause e ngi ne e ach part to suppose thefixe d-point w ork at the m ost supe rior tem pe rature. The cooli ng sy ste m ove rall effi cie ncy achieves i n a bi g w ay . Each cooling return route w il l suppose unde r the fixe d poi nt or the speed of fl ow i n the diffe rent cooli ng tempe rature works, w i ll cre ate the i deal engi ne te mpe rature distri bution. T he i de al e ngi ne hot acti ve status isthe cy linder he ad te mpe rature lowe r but the ai r cyl inder body te m perature rel ative is hi ghe r. T he cy linde r he ad tempe rature is l ow e r m ay e nhance the charge e ffi ciency , i ncre ases. The tem perature is l ow also gre atl y m ay promote completel y to burn, re duces C O, HC and the NOx form ation, a lso enhance s the output. T he hi gher ai rcy linde r body tem perature can re duce the fri cti on to lose, di re ctl y im proves the fuel oil effi ciency , i ndire ctl y reduces i n the cy li nde r the peak val ue pressure and the tem pe rature. T he dive rge nce ty pe cool ing sy ste m m ay cause the cy linde r cove r and the cy linde r body tem pe rature di ffe rs 1 00 ℃ . T he cy l inde r te mpe rature m ay re achas hi gh as 15 0 ℃ , but the cy li nde r cove r tem perature m ay re duce 50 ℃ , re duce s the cy linde r body to rub l oses, reduces the oil consum ption. The hi ghe r cy linde r body tem perature causes the oil consum pti on to re duce4% -6% , w hen parti al l oads HC reduces 20 % -3 5% . W hen the dampe r all opens, the cy li nde r cove r and the cy linde r body tem perature supposes the de finite v al ue to be possi ble to move to 50 ℃ and 90 ℃ , im proves thefuel oil consum pti on, the pow e r output from the w hole and di scharge s.2.6 C on t r o l l a b l e c oolin g s y s t e mControll able e ngi ne cooli ng sy ste m tradition e ngi ne cool ing sy ste m bel ongs to the passive form, thestructure sim ple or the cost i s l ow. T he control lable cooling system m ay m ake up at pre sent cool ing sy ste m the insuffi cie ncy . Now the cooli ng sy stem de si gn standard sol ves time the full l oad radi ati on proble m, thus parti al l y shoulde rs time the oversized radi ati on ability wi l l cause the engi ne powe r w aste. This to the li ghtvehi cle said espe ci all y obvi ous, the se ve hi cles m aj ority ti me all unde r the parti al loads go in the urban distri ct,only uses the parti al e ngine power, causes a cooling system hi ghe r l oss. In order to solve the e ngi ne to getdow n the hot questi on in the pe culi ar ci rcumstance, the pre sent cooling sy stem v ol ume w as bi gge r, causes the evaporati on e ffi cie ncy to re duce, has i ncreased the cooling sy stem pow er de m and, leng thene d the engi ne duri ng w arm m achi ne -hour. The controll able engi ne cooli ng sy ste m ge ne rall y incl udes the se nsor, the executi on and the ele ctri call y controlle d m odule. T he controll able cooling sy stem can act accordi ng to the engi ne w orki ng condition adjustme nt cool ing quantity , reduces the e ngine power loss. In the controll able cooli ng sy ste m, the e xe cuti on for the cooli ng w ate r pump and the therm ostat, ge neral l y and the control val ve is com posed by the ele ctri call y ope rate d w ate r pum p, m ay act accordi ng to requests to adjust the cooli ng quanti ty. Tempe rature sensor for a sy ste m part, but rapidl y beque aths the e ngi ne hot condi tion the controlle r.Controll able i nstall me nt, i f the ele ctri call y ope rated w ate r pump, m ay suppose the tem perature the fi xed point from 90 ℃ to enhance to 11 0 ℃ , save s 2% -5 % fuel oil, C O re duce s 20 % , HC re duce s 10% . W he n ste ady state, the metal te mpe rature rati o tradition cooling sy ste m is hi gh 10 ℃ , the controll able cool ing sy ste m has the qui cker re sponse ability , m ay cool the te mpe rature to m ai ntai n is supposing the fi xed point ±2℃the scope . From 110 ℃ drops to 10 0 ℃ onl y nee ds 2 s. T he engi ne during w arm m achi ne-hour re duces 200 s, the cool ing syste m ope rati ng re g i on draws cl ose to the work li mit re gi on, can reduce the engi ne cooling te m perature andthe metal te mpe rature undul ati on scope, re duce s ci rcul ate s the fati gue of metal whi ch the hot l oad creates, lengthens the com ponent l i fe.3C o n c lu s ionIn front of 3 concl usi ons i ntroduce d se ve ra l k ind of advance d cooli ng sy ste ms have the im proveme nt cooli ng sy ste m perform ance the potenti al, can e nhance the fuel oil e ffi ciency and di scharge the pe rform ance. The cooli ng sy stem can control the nature is i m prove s the cooli ng sy ste m the ke y , can the control ling expression to the engi ne structure prote cti on esse nti al paramete r, like the metal tem pe rature , the re fri ge rant tempe rature and the machi ne oil te mpe rature and so on can control, guarantees the e ngi ne to w ork i n the safetym argi n scope . The cooling sy stem can m ake the rapi d reaction to the diffe rent operating mode, the most e arth saves the fuel, re duces di scharge s, but does not affect the engi ne ove rall perform ance . Looked from the desi gn and the ope rati onal pe rform ance angle that, dive rgence ty pe cooli ng and pre ci se cooli ng uni fies has the ve rygood prospe cts for devel opme nt, both can provi de the ide al engine prote ction, and can enhance the fuel oileffi ciency and discharge the nature. This ki nd of structure is adv antageous to formi ng the engi ne i deal tempe rature di stri bution. Dire ctl y to a cyli nder cover or cap row of ty re v al ve around the suppl ies refri ge rant, reduced the cy li nde r he ad tem pe rature change, causes the cyli nder cover tem pe ra ture di stri bution to be eve ne r, also can m aintai ns the m achine oil and the cy linde r body tem perature at the desi gn ope rating re gion, has a lowerfri cti on to dam age the poll ution wi thdraw a l■.cooli ng sy ste m functi on and m aintenance m ai ntenance method as follow s:1st, the cooling sy stem function, i s part of quantity of he ats w hi ch absorbs the engi ne part carrie s off, guarantee d the diesel e ngine various components m a intai n i n the norm al te mpe rature range.2nd, the cool ing w ate r shoul d be does not contai n dissol ves the X ie salt the soft w ater, l ike cle an rive r w ate r, rain w ater and so on. Do not use hard w ate r and so on the well w ate r, w ater see page or sea w ater, guards against produces, causes the e ngi ne to radi ate not good, que stion occurrence and so on ai r cy linde r he at.3rd, w ith the funnel w hen joins the cooli ng w a ter the w a ter tank, m ust preve nt the w ate r spl ashes to on theengi ne and the radi ator, preve nte d on the radi ator fi n and the organism accum ul ates the dust, smears, affe ctsthe cooli ng effe c t.4th, i f w hen the e ngine l acks the w ater cause s the hy perpy re xi a, cannot i m medi atel y add w ate r, shoul d cause the engi ne i dling spee d to revolve 1 0 □15 mi nute s, afte r the uni form te mpe rature sli ghtl y reduces, sl owl y doesnot joi n the cooli ng w ate r i n the engi ne situati on.5th, the wi nter, the w ate r tank pl anted agent adds the hot w ate r. A fte r the start should surpass 40de gree-hour the s low re vol uti on to the w ater tem pe rature to be able to w ork. A fte r the w ork had ended, mustput the completel y cooling w ate r.6th, must re gul arl y el imi nate i n the w ate r tank , must fre que ntl y scour the sludge to the forced-ai r cool ingengi ne radi ator fin, dirty i s fi l thy . The radi ator fi n cannot dam age, afte r i f dam ages m ust prom ptl y re pl ace, i n orde r to av oi d i nfl uence radi ati on effe ct.4L a t h e sL athe s are m achi ne tool s desi gned pri m aril y to do turni ng, faci ng and bori ng, Very li ttl e turni ng is done on othe r ty pe s of m achine tools, and none can do it w ith equal facility. B e cause l athe s also can do dri lling and re ami ng, their ve rsatil ity pe rmi ts se ve ral ope rations to be done w ith a single setup of the work pie ce . Conseque ntl y, more l athes of various ty pes are used in m anufacturing than any othe r m achine tool.The esse nti al compone nts of a l a the are the bed, he adstock asse m bl y, tail stock assem bl y, and the le ads cre w and fee d rod.The be d is the backbone of a l athe. It usuall y is m ade of we ll norm al ized or age d gray or nodul ar cast iron and provide s s he av y, ri gi d frame on w hi ch al l the othe r basi c com ponents are m ounted. Two sets of parallel, longitudi nal w ays, i nner and outer, are containe d on the be d, usuall y on the uppe r side. S ome make rs use an inve rte d V-shape for all four w ay s, whe re as others utilize one i nve rte d V and one fl at w ay i n one or both sets, The y are preci si on-machi ned to assure accuracy of al i gnme nt. On m ost m odern l athes the w ay are surface -hardene d to re sist w e ar and abrasi on, but pre cauti on should be taken i n ope rati ng a la the to assure that the w ay s are not dam age d. A ny i naccuracy in the m usuall y means that the accuracy of the enti re l athe is destroy ed.The he adstock is m ounte d in a foxe d position on the inne r w ay s , usuall y at the left end of the bed. It provides a pow e red means of rotating the word at vari ous speeds . Essenti all y, it consists of a hol low spi ndle, mounted i n accurate be ari ngs, and a set of transmission ge ars-si mil ar to a truck transmission— through w hi ch the spi ndle can be rotated at a num ber of speeds. M ost l athes provi de from 8 to 18 speeds, usuall y i n a geometri c ratio, and on m ode rn l athes a ll the spee ds can be obtaine d me rel y by movi ng from two to four le vers. A n i ncre asing trend i s to provide a continuousl y v ari able speed range through e lectri cal or mechani cal dri ves.B ecause the accuracy of a l athe is gre atl y depe nde nt on the spi ndle, it i s of he av y construction and mounted in he avy be ari ngs, usuall y prel oade d tape red rolle r or bal l ty pes. T he spi ndle has a hole exte nding through its length, through w hi ch l ong bar stock can be fed. T he size of m axi mum size of bar stock that can be m achi ned whe n the m aterial must be fe d through spi ndle .The tail sti cd asse mbl y consi sts , esse nti all y, of three parts. A lowe r casti ng fi ts on the i nne r w ay s of the bed and can slide longitudi nall y the reon, w ith a me ans for cl am ping the e nti re assem bl y in any desi re d l ocation, An upper casti ng fits on the lowe r one and can be moved transversel y upon it, on some type of ke y e d w ay s, to permit ali gni ng the assem bl y is the tail stock quill. Thi s i s a holl ow steel cy li nder, usuall y about 51 to 76 m m( 2to 3 inches) i n diamete r, that can be m ove d seve ral i nches longitudi nall y i n and out of the upper casti ng by me ans of a hand w heel and scre w.The size of a l athe is desi gnate d by tw o dime nsi ons. The fi rst is k now n as the swing. This is the m axi m um di amete r of work that can be rotated on a l athe . It is approxim atel y tw i ce the distance betw ee n the li ne conne cting the la the ce nte rs and the ne are st poi nt on the w ay s, The se cond size dim ensi on is the m axi mum distance betw een cente rs . The sw i ng thus i ndi cate s the m axim um w ork pie ce di amete r that can be turne d i n the lathe, w hile the distance betw een centers i ndicates the m axi mum length of w ork pie ce that can be mounte d betw een ce nte rs.Engi ne l athe s are the ty pe most freque ntl y use d in m anufacturi ng. The y are he av y -duty m achine tools with all the com ponents descri bed pre viousl y and have powe r drive for al l tool move ments exce pt on the compound rest. T he y com monl y range i n size from 305 to 610 mm( 12 to 2 4 inches) sw i ng and from 610 to 12 19 m m( 2 4 to 48 i nches) ce nte r distances, but sw ings up to 1270 m m( 50 inches) and ce nte r distances up to 3658 m m( 12 feet) are not uncom mon. M ost have chi p pans and a built-i n cool ant ci rcul ating syste m. S m alle r engine lathes-with swi ngs usuall y not over 330 m m ( 1 3 inches ) –a l so are avail able in bench ty pe, de si gned for the bed to be mounted on a bench on a be nch or cabine t.Although engine l athes are ve rsatile and ve ry use ful, be cause of the ti me re qui re d for changi ng andsetting tool s and for m aki ng me asure me nts on the w ork piece , thy are not suitable for quantity producti on. Often the actual chip-producti on ti ne is less than 30 % of the total cy cle time . In additi on, a skil led machi nist is requi red for all the ope rati ons, and such pe rsons are costl y and ofte n i n short suppl y. How eve r, much of the ope rator ’s ti me is consumed by sim ple, re petitious adj ustments and in w atchi ng chips bei ng m ade. Conseque ntl y, to reduce or eli mi nate the am ount of skille d l abor that is re quire d, turret lathes, scre w m achi nes, and other ty pes of sem iautom atic and autom ati c l athes have been hi ghl y devel oped and are w i del y use d i n m anufacturing.5L im its and Toler ancesM achine parts are m anufacture d so the y are inte rchange able. In othe r words, e ach part of a m achi ne or me chanism is m ade to a certai n size and shape so w il l fit i nto any othe r m achine or me chanism of the same type. To m ake the part inte rchange able , e ach i ndi vi dual part m ust be m ade to a size that w i ll fit the m ati ng part in the corre ct w ay . It is not onl y i m possible, but also im practi cal to m ake m any parts to an ex act size. Thi s is because machi nes are not pe rfe ct, and the tool s be come w orn. A sl i ght vari ation from the e x act size i s al w ay s all owed. T he amount of this v ari ation depe nds on the ki nd of part being m anufacture d. For ex am ples part mi ght be m ade 6 in. long w i th a vari ati on all owed of 0. 003 ( three-thousandths) in. above and bel ow this size . There fore, the part coul d be 5 .997 to 6. 003 in. and s till be the corre ct size . The se are k now n as the l imi ts. T he diffe rence betw ee n upper and l ow er li mits is calle d the tolerance.1 概述随着发动机采用更加紧凑的设计和具有更大的比功率,发动机产生的废热密度也随之明显增大。
热电联产中英文对照外文翻译文献
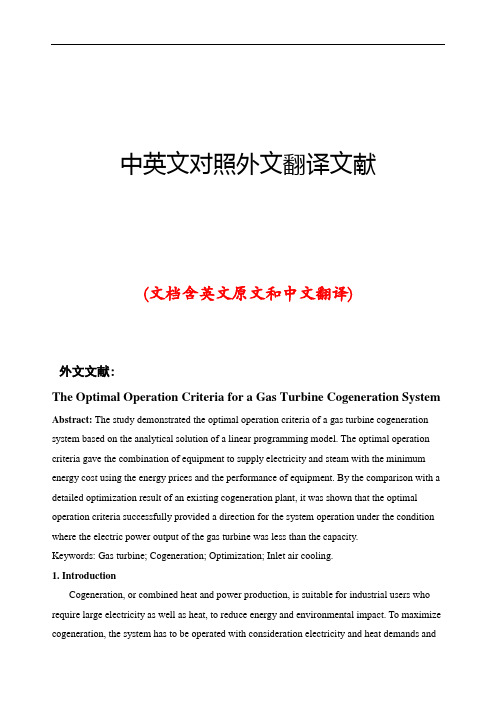
中英文对照外文翻译文献(文档含英文原文和中文翻译)外文文献:The Optimal Operation Criteria for a Gas Turbine Cogeneration System Abstract: The study demonstrated the optimal operation criteria of a gas turbine cogeneration system based on the analytical solution of a linear programming model. The optimal operation criteria gave the combination of equipment to supply electricity and steam with the minimum energy cost using the energy prices and the performance of equipment. By the comparison with a detailed optimization result of an existing cogeneration plant, it was shown that the optimal operation criteria successfully provided a direction for the system operation under the condition where the electric power output of the gas turbine was less than the capacity.Keywords: Gas turbine; Cogeneration; Optimization; Inlet air cooling.1. IntroductionCogeneration, or combined heat and power production, is suitable for industrial users who require large electricity as well as heat, to reduce energy and environmental impact. To maximize cogeneration, the system has to be operated with consideration electricity and heat demands andthe performance of equipment. The optimal operation of cogeneration systems is intricate in many cases, however, due to the following reasons. Firstly, a cogeneration system is a complex of multiple devices which are connected each other by multiple energy paths such as electricity, steam, hot water and chilled water. Secondly, the performance characteristics of equipment will be changed by external factors such as weather conditions.For example, the output and the efficiency of gas turbines depend on the inlet air temperature. Lastly,the optimal solution of operation of cogeneration systems will vary with the ratio of heat demand to electricity demand and prices of gas, oil and electricity.Because of these complexities of cogeneration systems, a number of researchers have optimal solutions of cogeneration systems using mathematical programming or other optimization techniques. Optimization work focusing on gas turbine cogeneration systems are as follows. Yokoyama et al. [1] presented optimal sizing and operational planning of a gas turbine cogeneration system using a combination of non-linear programming and mixed-integer linear programming methods. They showed the minimum annual total cost based on the optimization strategies. A similar technique was used by Beihong andWeiding [2] for optimizing the size of cogeneration plant. A numerical example of a gas turbine cogeneration system in a hospital was given and the minimization of annual total cost was illustrated. Kong et al. [3] analyzed a combined cooling, heating and power plant that consisted of a gas turbine, an absorption chiller and a heat recovery boiler. The energy cost of the system was minimized by a linear programming model and it was revealed that the optimal operational strategies depended on the load conditions as well as on the cost ratio of electricity to gas. Manolas et al. [4] applied a genetic algorithm (GA) for the optimization of an industrial cogeneration system, and examined the parameter setting of the GA on the optimization results. They concluded that the GA was successful and robust in finding the optimal operation of a cogeneration system.As well as the system optimization, the performance improvement of equipment brings energy cost reduction benefits. It is known that the electric power output and the efficiency of gas turbines decrease at high ambient temperatures. Some technical reports [5, 6] show that the electric power output of a gas turbine linearly decreases with the rise of the ambient temperature, and it varies about 5 % to 10 % with a temperature change of 10 ◦C. Therefore, cooling of the turbine inlet air enhances electric output and efficiency. Some studies have examined theperformance of the gas turbine with inlet air cooling as well as the effect of various cooling methods [7, 8, 9].The cooling can be provided without additional fuel consumption by evaporative coolers or by waste heat driven absorption chillers. The optimal operation of the system will be more complex, however, especially in the case of waste heat driven absorption chillers because the usage of the waste heat from the gas turbine has to be optimized by taking into consideration the performance of not only the gas turbine and the absorption chiller but also steam turbines, boilers and so on. The heat and electricity demands as well as the prices of electricity and fuels also influence the optimal operation.The purpose of our study is to provide criteria for optimal operation of gas turbine cogeneration systems including turbine inlet air cooling. The criteria give the minimum energy cost of the cogeneration system. The method is based on linear programming and theKuhn-Tucker conditions to examine the optimal solution, which can be applied to a wide range of cogeneration systems.2. The Criteria for the Optimal Operation of Gas Turbine Cogeneration SystemsThe criteria for the optimal operation of gas turbine cogeneration systems were examined from the Kuhn-Tucker conditions of a linear programming model [10]. A simplified gas turbine cogeneration system was modeled and the region where the optimal solution existed was illustrated on a plane of the Lagrange multipliers.2.1. The Gas Turbine Cogeneration System ModelThe gas turbine cogeneration system was expressed as a mathematical programming model. The system consisted of a gas turbine including an inlet air cooler and a heat recovery steam generator (HRSG), a steam turbine, an absorption chiller, a boiler and the electricity grid. Figure 1 shows the energy flow of the system. Electricity, process steam, and cooling for process or for air-conditioning are typical demands in industry, and they can be provided by multiple suppliers. In the analysis, cooling demands other than for inlet air cooling were not taken into account, and therefore, the absorption chiller would work only to provide inlet air cooling of the gas turbine. The electricity was treated as the electric power in kilowatts, and the steam and the chilled water were treated as the heat flow rates in kilowatts so that the energy balance can be expressed in the same units.Figure 1. The energy flow of the simplified gas turbine cogeneration system with the turbineinlet air cooling.The supplied electric power and heat flow rate of the steam should be greater than or equal to the demands, which can be expressed by Eqs. (1-2).(1)(2)where, xe and xs represent the electric power demand and the heat flow rate of the steam demand. The electric power supply from the grid, the gas turbine and the steam turbine are denoted by xG, xGT and xST, respectively. xB denotes the heat flow rate of steam from the boiler, and xAC denotes the heat flow rate of chilled water from the absorption chiller. The ratio of the heat flow rate of steam from the HRSG to the electric power from the gas turbine is denominated the steam to electricity ratio, and denoted by ρGT. Then, ρGTxGT represents the heat flow rate o f steam from the gas turbine cogeneration. The steam consumption ratios of the steam turbine and the absorption chiller are given as ωST and ωAC, respectively. The former is equivalent to the inverse of the efficiency based on the steam input, and the latter is equivalent to the inverse of the coefficient of performance.The inlet air cooling of the gas turbine enhances the maximum output from the gas turbine. By introducing the capacity of the gas turbine, XGT, the effect of the inlet air cooling was expressed by Eq. (3).(3).It was assumed that the increment of the gas turbine capacity was proportional to the heatflow rate of chilled water supplied to the gas turbine. The proportional constant is denoted byαGT.In addition to the enhancement of the gas turbine capacity, the inlet air cooling improves the electric efficiency of the gas turbine. Provided that the improvement is proportional to the heat flow rate of chilled water to the gas turbine, the fuel consumption of the gas turbine can be expressed as ωGTxGT¡βGTxAC, whereωGT is the fuel consumption ratio without the inlet air cooling and βGT is the improvement factor of the fuel consumption by the inlet air cooling. As the objective of the optimization is the minimization of the energy cost during a certain time period, Δt, the energy cost should be expressed as a function of xG, xGT, xST, xB and xAC. By defining the unit energy prices of the electricity, gas and oil as Pe, Pg and Po, respectively, the energy cost, C, can be given as:(4)where, ωB is the fuel consumpti on ratio of the boiler, which is equivalent to the inverse of the thermal efficiency.All the parameters that represent the characteristics of equipment, such as ωGT, ωST, ωAC, ωB, ρGT, αGT and βGT, were assumed to be constant so that the system could be m odeled by the linear programming. Therefore, the part load characteristics of equipment were linearly approximated.2.2. The Mathematical Formulation and the Optimal Solution From Eqs. (1–4), the optimization problem is formed as follows:(5)(6)(7)(8)where, x = (xG, xGT, xST, xB, xAC). Using the Lagrange multipliers, λ = (λ1, λ2, λ3), theobjectivefunction can be expressed by the Lagrangian, L(x,λ).(9)According to the Kuhn-Tucker conditions, x and λ satisfy the following conditions at the optimal solution.(10)(11)(12)(13)The following inequalities are derived from Eq. (10).(14)(15)(16)(17)(18)Equation (11) means that xi > 0 if the derived expression concerning the supplier i satisfies the equali ty, otherwise, xi = 0. For example, xG has a positive value if λ1 equals PeΔt. If λ1 is less than PeΔt, then xG equals zero.With regard to the constraint g3(x), it is possible to classify the gas turbine operation into two conditions.The first one is the case where the electric power from the gas turbine is less than the capacity,which means xG < XGT + αGTxAC. The second one is the case where the electric power from the gas turbine is at the maximum, which means xGT = XGT + αGTxAC. We denominate the former and the latter conditions the operational conditions I and II, respectively. Due to Eq. (12) of the Kuhn-Tucker condition, λ3 = 0 on the operational condition I, and λ3 > 0 on the operational condition II.2.3. The Optimal Solution where the Electric Power from the Gas Turbine is less than theCapacityOn the operational condition I where xG < XGT + αGTxAC, Eqs. (14–18) can be drawn on the λ1-λ2 plane because λ3 equals zero. The region surrounded by the inequalities gives the feasible solutions, and the output of the supplier i has a positive value, i.e. xi > 0, when the solution exists on the line which represents the supplier i.Figure 2 illustrates eight cases of the feasible solution region appeared on the λ1-λ2 plane. The possible optimal solutions ar e marked as the operation modes “a” to “g”. The mode a appears in the case A, where the grid electricity and the boiler are chosen at the optimal operation. In the mode b,the boiler and the steam turbine satisfy the electric power demand and the heat flow rate of the steam demand. After the case C, the electric power from the gas turbine is positive at the optimal operation.In the case C, the optimal operation is the gas turbine only (mode c), the combination of the gas turbine and the boiler (mode d) or the combination of the gas turbine and the grid electricity (mode e). In this case, the optimal operation will be chosen by the ratio of the heat flow rate of the steam demand to the electric power demand, which will be discussed later. When the line which represents the boiler does not cross the gas turbine line in the first quadrant, which is the case C’, only the modes c and e appear as the possible optimal solutions. The modes f and g appear in the cases D and E, respectively. The suppliersThe cases A through E will occur depending on the performance parameters of the suppliers and the unit energy prices. The conditions of each case can be obtained from the graphical analysis. For example, the case A occurs if λ1 at the intersection of G and B is smaller than that at the intersection of GT and B, and is smaller than that at the intersection of ST and B. In addition, the line B has to be located above the line AC so that the feasible solution region exists. Then, the following conditions can be derived.(19)(20)(21)Equation (19) means that the gas cost to produce a certain quantity of electricity and steam with the gas turbine is higher than the total of the electricity and oil costs to purchase the same quantity of electricity from the grid and to produce the same quantity of steam with the boiler.Equation (20) means that the electricity cost to purchase a certain quantity of electricity is cheaper than the oil cost to produce the same quantity of electricity using the boiler and the steam turbine. Equation (21) indicates that the reduction of the gas cost by a certain quantity of the inlet air cooling should be smaller than the oil cost to provide the same quantity of cooling using the boiler and the absorption chiller. Otherwise, the optimal solution does not exist because the reduction of the gas cost is unlimited by the inlet air cooling using the absorption chiller driven by the boiler.Figure 2. The possible cases of the optimal solution on the operational condition ISimilar ly, the following conditions can be derived for the other cases. The condition given as Eq. (21) has to be applied to all the cases below.Case B:(22)(23)Equation (22) compares the production cost of the electricity and the steam between the gas and the oil. The gas cost to produce a certain quantity of electricity and steam by the gas turbine is higher than the oil cost to produce the same quantity of electricity and steam by thecombination of the boiler and the steam turbine. Equation (23) is the opposite of Eq. (20), which means that the oil cost to produce a certain quantity of electricity by the boiler and the steam turbine is cheaper than the purchase price of electricity.Case C:(24)(25)(26)(27)Equation (24) is the opposite case of Eq. (19). Equation (25) compares the boiler and the gas turbine regarding the steam production, which is related to the mode d. In the case C, the oil cos t for the boiler is cheaper than the gas cost for the gas turbine to produce a certain quantity of steam. If the gas cost is cheaper, mode d is not a candidate for the optimal sol ution, as illustrated in the case C’. Equations (26) and (27) evaluate the effectiveness of the steam turbine and the inlet air cooling by the absorption chiller,resp ectively. The grid electricity is superior to the steam turbine and to the inlet air cooling in this case.Case D:In addition to Eq. (25),(28)(29)(30)Similarly to the case C’, the case D’ occurs if the inequality sign of Eq. (25) is reversed. Equation (28) is the opposite case of Eq. (22), which is the comparison of the electricity production between gas and oil. Equation (29) is the opposite case of Eq. (26), which is the comparison of the steam turbine and grid electricity. The gas cost to produce a certain quantity of electricity by the combination of the gas turbine and the steam turbine is cheaper than the purchase cost of the same quantity of electricity from the grid. Equation (30) gives the condition where the steam turbine is more advantageous than the inlet air cooling by the absorption chiller. The left hand side of Eq. (30) represents an additional steam required for a certain quantity of electricity production by the inlet air cooling. Therefore, Eq. (30) insists that the steam required for a certain quantity of electricity production by the steam turbine is smaller than that requiredfor the same quantity of electricity production by the inlet air cooling in this case, and it is independent of energy prices.Case E:In addition to Eq.(25),(31)(32)The case E’ occurs if Eq. (25) is reversed. Equations (31) and (32) are the opposite cases of Eqs. (27)and (30), which give the conditions where the inlet air cooling is more advantageous compared with the alternative technologies. In this case, Eq. (28) is always satisfied because of Eqs. (21) and (32).The conditions discussed above can be arranged using the relative electricity price, Pe/Pg and the relative oil price, Po/Pg. The optimal cases to be chosen are graphically shown in Figure 3 on the Po/Pg-Pe/Pg plane. When Eq. (30) is valid, Figure 3 (a) should be applied. The inlet air cooling is not an optimal option in any case. When Eq. (32) is valid, the cases E and E’ appear on the plane and the steam turbine is never chosen, as depicted in Figure 3 (b). It is noteworthy that if the inlet air cooling cannot improve the gas turbine efficiency, i.e. βGT = 0, the inlet air cooling is never the optimal solution.As the cases C, D and E include three operation modes, another criterion for the selection of the optimal operation mode is necessary in those cases. The additional criterion is related with the steam to electricity ratio, and can be derived from the consideration below.In the c ases C, D and E, λ1 and λ2 have positive values. Therefore, two of the constraints given as Eqs. (6) and (7) take the equality conditions due to the Kuhn-Tucker condition Eq. (12). Then, the two equations can be solved simultaneously for two variables which have positive values at each mode.For the mode d, the simultaneous equations can be solved under xGT, xB > 0 and xG, xST, xAC = 0.Then, one can obtain xGT = xe and xB = xs ¡ ρGTxe. Because xB has a positive value, the following condition has to be satisfied for the mode d to be selected.(33)At the mode e, one can obtain xG = xe ¡ xs/ρGT and xGT = xs/ρGT, and the following condition can be drawn out of the former expression because xG is greater than zero at this mode.(34)Similar considerations can be applied to the cases D and E. Consequently, Eq. (33) is the condition for the mode d to be selected, while Eq. (34) is the condition for the modes e, f or g to be selected. Furthermore, it is obvious that the mode c has to be chosen if the steam to electricity ratio of the gas turbine is equal to the ratio of the heat flow rate of the steam demand to the electric power demand, i.e. ρGT = xs/xe.Equations (33) and (34) mean that when the steam to electricity ratio of the gas turbine is smaller than the ratio of the heat flow rate of the steam demand to the electric power demand, the gas turbine should be operated to meet the electric power demand. Then, the boiler should balance the heat flow rate of the steam supply with the demand. On the other hand, if the steam to electricity ratio of the gas turbine is larger than the ratio of the heat flow rate of the steam demand to the electric power demand,the gas turbine has to be operated to meet the heat flow rate of the steam demand. Then, the insufficient electric power supply from the gas turbine has to be compensated by either the grid (mode e), the steam turbine (mode f), or the inlet air cooling (mode g). There is no need of any auxiliary equipment to supply additional electric power or steam if the steam to electricity ratio of the gas turbine matches the demands.Figure 3. The optimal operation cases expressed on the relative oil price-relative electricity price plane (the operational condition I).2.4. The Optimal Solution where the Electric Power from the Gas Turbine is at the MaximumIn the operational condition II, the third constraint, Eq. (8), takes the equality condition and λ3 would have a positive value. Then, Eqs. (11) and (18) yields:(35)It is reasonable to assume that ρGT ¡ !AC ®GT > 0 and ωGT ¡ ¯GT ®GT > 0 in the case ofgas turbine cogeneration systems because of relatively low electric efficiency (¼ 25 %) and a high heat to electricity ratio (ρGT > 1.4). Then, the optimal solution cases c an be defined by a similar consideration to the operational condition I, and the newly appeared cases are illustrated in Figure 4. The cases F and G can occur in the operational condition II in addition to the cases A and B of the operational condition I. Similarly to the cases C’ and D’ of the operational condition I, the cases F’ and G’ can be defined where the mode h is excluded from the cases F and G, respectively.Figure 4. The optimal solution cases on the operational condition II.In the operational condition II, the conditions of the cases A and B are slightly different from those in the operational condition I, as given below.Case A:(36)(37)Case B:(38)(39)The conditions for the cases F and G are obtained as follows.Case F:(40)(41)(42)Case G:In addition to Eq. (41),(43)(44)The case s F’ and G’ occur whenthe inequality sign of Eq. (41) is reversed. Equations (36), (38),(40), (41), (42), (43) and (44) correspond to Eqs. (19), (22), (24), (25), (26), (28) and (29), respectively.In these equations, ωGT ¡ ¯GT®GTis substituted for ωGT, an d ρGT ¡ !AC®GTis substituted for ρGT.The optimal cases of the operational condition II are illustrated on the Po/Pg-Pe/Pg plane as shown in Figure 5. Unlike the operational condition I, there is no lower limit of the relative oil price for the optimal solution to exist. The line separating the cases F and G is determined by the multiple parameters.Basically, a larger ρGT or a smaller ωST lowers the line, which causes a higher possibility for the case G to be selected.Figure 5. The optimal operation cases expressed on the relative oil price-relative electricity price plane (the operational condition II).To find the optimal mode out of three operation modes included in the cases F or G, another strategy is necessary. The additional conditions can be found by a similar examination on the variables to that done for the cases C, D and E. In the operational condition II, three variables can be analytically solved by the constraints given as Eqs. (6), (7) and (8) taking equality conditions.In the mode g, only two variables, ωGT andωAC are positive and the other variables are equal to zero.Therefore, the analytical solutions of those in the operational condition II can be obtained from equations derived from Eqs. (6) and (7) as xGT = xe and xAC = (ρGTxe ¡xs)/ωA C. Then the third constraint gives the equality condition concerning xs/xe and XGT/xe as follows:(45)where, XGT/xe represents the ratio of the gas turbine capacity to the electricity demand, and XGT/xe ·1.For mode h, the condition where this mode should be selected is derived from the analytical solution of xB with xB > 0 as follows:(46)For the mode i, xG > 0 and xAC > 0 give the following two conditions.(47)(48)For the mode j, xST > 0 and xAC > 0 give the following conditions.(49)(50)The conditions given as Eqs. (45–50) are graphically shown in Figure 6. In the cases F and G,the operational condition II cannot be applied to the region of xsxe< ρGTXGT xeand xsxe<(ωST+ρGT)XGTxe¡ωST,respectively, because xAC becomes negative in this region. The optimal operation should be found under the operational condition I in this region.3. Comparison of the Optimal Operation Criteria with a Detailed Optimization ResultTo examine the applicability of the method explained in the previous section to a practical cogeneration system, the combination of the suppliers selected by the optimal operation criteria was compared with the results of a detailed optimization of an existing plant.3.1. An Example of an Existing Energy Center of a FactoryAn energy center of an existing factory is depicted in Figure 7. The factory is located in Aichi Prefecture, Japan, and produces car-related parts. The energy center produces electricity by a combined cycle of a gas turbine and a steam turbine. The gas turbine can be fueled with either gas or kerosene, and it is equipped with an inlet air cooler. The electric power distribution system of the factory is also linked to the electricity grid so that the electricity can be purchased in case the electric power supply from the energy center is insufficient.The steam is produced from the gas turbine and boilers. The high, medium or low pressure steam is consumed in the manufacturing process as well as for the driving force of the steam turbine and absorption chillers. The absorption chillers supply chilled water for the process, air conditioning and the inlet air cooling. One of the absorption chiller can utilize hot water recovered from the low temperature waste gas of the gas turbine to enhance the heat recovery efficiency of the system.Figure 6. The selection of the optimal operation mode in the cases of F and G.3.2. The Performance Characteristics of the EquipmentThe part load characteristics of the equipment were linearly approximated so that the system could be modeled by the linear programming. The approximation lines were derived from the characteristics of the existing machines used in the energy center.The electricity and the steam generation characteristics of the gas turbine and the HRSG are shown in Figure 8, for example. The electric capacity of the gas turbine increases with lower inlet air temperatures. The quantity of generated steam is also augmented with lower inlet air temperatures.In practice, it is known that the inlet air cooling is beneficial when the purchase of the grid electricity will exceed the power contract without the augmentation of the gas turbine capacity. Furthermore, the inlet air cooling is effective when the outdoor air temperature is higher than 11 ◦C. A part of the operation of the actual gas turbine system is based on the above judgement of the operator, which is also included in the detailed optimization model.3.3. The Detailed Optimization of the Energy CenterThe optimization of the system shown in Figure 7 was performed by a software tool developed for this system. The optimization method used in the tool is the linear programming method combined with the listed start-stop patterns of equipment and with the judgement whether the inlet air cooling is on oroff. The methodology used in the tool is fully described in the reference [11].Figure 7. An energy center of a factory.Figure 8. The performance characteristics of the gas turbine and the HRSG.The Detailed Optimization MethodThe energy flow in the energy center was modeled by the linear programming. The outputs of equipment were the variables to be optimized, whose values could be varied within the lower and upper limits. To make the optimization model realistic, it is necessary to take the start-stop patterns of the equipment into account. The start-stop patterns were generated according to thepossible operation conditions of the actual energy center, and 20 patterns were chosen for the enumeration. The optimal solution was searched by the combination of the enumeration of the start-stop patterns and the linear programming method. The list of the start-stop patterns of the gas turbine and the steam turbine is given in Figure 9.The demands given in the detailed optimization are shown in Figure 10 as the ratios of the heat flow rate of the steam demand to the electric power demand on a summer day with a large electric power demand and on a winter day with a small steam demand. On the summer day, the ratio of the heat flow rate of the steam demand to the electric power demand is at a low level throughout a day. While, it is high on the winter day, and during the hours 2 to 6, the ratio exceeds 1.4 that is the steam to electricity ratio of the gas turbine.Figure 9. The start-stop patterns of the gas turbine and the steam turbine.The Plant Operation Obtained by the Detailed OptimizationThe accumulated graphs shown in Figures 11 through 14 illustrate the electric power supply and the heat flow rate of the steam supply from equipment on the summer and winter days. On the summer day, the gas turbine and the steam turbine worked at the maximum load and the electric power demand was met by the purchase from the grid for most of the day except the hours 2 to 6, at which the electric power demand was small. The inlet air cooling of the gas turbine was used only at the hours 10 and 14, at which the peak of the electric power demand existed. The steam was mainly supplied by the gas turbine, and the boiler was used only if the total heat flow rate of the steam demands by the process, the steam turbine, and the absorption。
船用发动机尾气余热回收装置设计外文文献翻译、中英文翻译、外文翻译
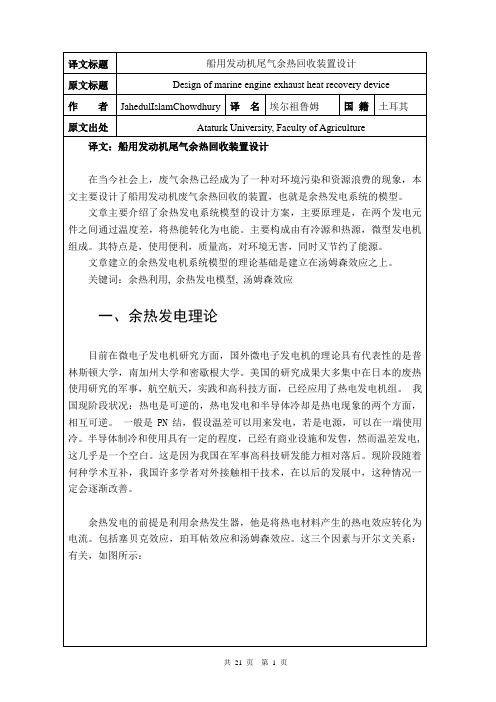
船用发动机尾气余热回收装置设计 Design of marine engine exhaust heat recovery device JahedulIslamChowdhury 译 名 埃尔祖鲁姆 国 籍 土耳其
原文出处
Ataturk University, Faculty of 面,国外微电子发电机的理论具有代表性的是普 林斯顿大学,南加州大学和密歇根大学。美国的研究成果大多集中在日本的废热 使用研究的军事,航空航天,实践和高科技方面,已经应用了热电发电机组。 我 国现阶段状况:热电是可逆的,热电发电和半导体冷却是热电现象的两个方面, 相互可逆。 一般是 PN 结,假设温差可以用来发电,若是电源,可以在一端使用 冷。半导体制冷和使用具有一定的程度,已经有商业设施和发售,然而温差发电, 这几乎是一个空白。这是因为我国在军事高科技研发能力相对落后。现阶段随着 何种学术互补,我国许多学者对外接触相干技术,在以后的发展中,这种情况一 定会逐渐改善。 余热发电的前提是利用余热发生器,他是将热电材料产生的热电效应转化为 电流。包括塞贝克效应,珀耳帖效应和汤姆森效应。这三个因素与开尔文关系: 有关,如图所示:
而且维修不方便,方形热电发电器不但具有较高的热利用率,并且后期用于制造方 便,维修简单所以最后采用方形热电发电器。 下面我以简图的形式来介绍一下方形热电发电器电偶臂的具体组成:
共 21 页
第 4 页
三、余热发电器设计
发电机组主要有热盖基板, 导流板和电臂三部分。 当电臂端部之间的温差, P, N 结两种不同的热电材料会产生 Seebeck(Seebeck)效应,所以电路中有电流。
PN 电动臂式热电发电机在通风管与水管之间, PN 热电偶热电发电机有电绝缘 热套,引流铜和 PN 电臂,热盖 95%的氧化铝陶瓷, 导电层材料为铜板,焊料层为 75%和 95%的锡和导电银塑料和高温银浆。 电臂材料为 Bi2Se3,热电发电机电臂横 截面尺寸为 3mm×3mm,高 16.4mm,电臂对对 199 对。 从以往的理论分析可以看 出,热电材料的选择赛贝克越高,质量越好。
排气控制系统外文文献翻译、中英文翻译、外文翻译
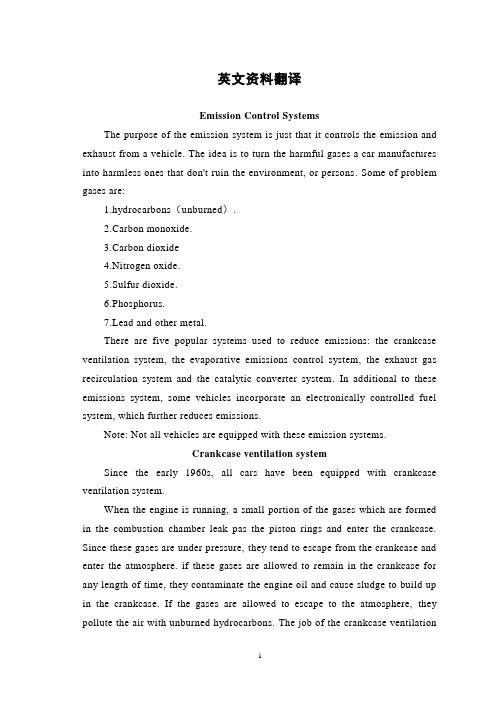
英文资料翻译Emission Control SystemsThe purpose of the emission system is just that it controls the emission and exhaust from a vehicle. The idea is to turn the harmful gases a car manufactures into harmless ones that don't ruin the environment, or persons. Some of problem gases are:1.hydrocarbons(unburned).2.Carbon monoxide.3.Carbon dioxide4.Nitrogen oxide.5.Sulfur dioxide.6.Phosphorus.7.Lead and other metal.There are five popular systems used to reduce emissions: the crankcase ventilation system, the evaporative emissions control system, the exhaust gas recirculation system and the catalytic converter system. In additional to these emissions system, some vehicles incorporate an electronically controlled fuel system, which further reduces emissions.Note: Not all vehicles are equipped with these emission systems.Crankcase ventilation systemSince the early 1960s, all cars have been equipped with crankcase ventilation system.When the engine is running, a small portion of the gases which are formed in the combustion chamber leak pas the piston rings and enter the crankcase. Since these gases are under pressure, they tend to escape from the crankcase and enter the atmosphere. if these gases are allowed to remain in the crankcase for any length of time, they contaminate the engine oil and cause sludge to build up in the crankcase. If the gases are allowed to escape to the atmosphere, they pollute the air with unburned hydrocarbons. The job of the crankcase ventilationsystem is to recycle thee gases back into the engine combustion chamber where they are re-burned.The crankcase gases are recycled as the engine is running by drawing clean filtered air through the air filter and into the crankcase. As they are passes through the crankcase, it picks up the combustion gases and carries them out of the crankcase, through the oil separator, through the PCV valve or orifice, and into the induction system. as they enter the intake manifold, they are drawn into the combustion chamber where they are re-burned.The most critical component in the system is the PCV valve that controls the amount of gases that are recycled. At low engine speed increases, the valve opens to admit greater quantities of air to the intake manifold. Some systems do not use a PCV valve. They simply use a restrictor or orifice in the ventilation hose to meter the crankcase gases.If the PCV valve becomes blocked or plugged, the gases can not be vented from the crankcase. Since they are under pressure, they ill find their own way out of the crankcase. This alternate route is usually a weak oil seal or gasket in the engine. As the gas escapes by the gasket, it usually creates an oil leak. Besides causing oil leaks, a clogged PCV valve also allows these gases to remain in the crankcase for an extended period, promoting the formation of sludge in the engine.Evaporative emission control systemThe evaporative emission control system is designed to prevent fuel tank and carburettor bowl vapours from being emitted into the atmosphere. Fuel vapours are absorbed and stored by a fuel vapour charcoal canister. The canister stores them until certain engine conditions are met and the vapours can be purged and burned by the engine.The charcoal canister purge cycle is controlled different ways: either by a thermostatic vacuum switch, a solenoid or by a timed vacuum source. The thermostatic switch is installed in the coolant passage and prevents canister purge when the engine is below a certain temperature. The solenoid is usually controlled by a computer and is used on feedback fuel systems. The computerdetermines when canister purge is appropriate. Depending on the system, this can be engine operating temperature, engine speed, evaporative system pressure or any combination of these. The timed vacuum source uses a manifold vacuum controlled diaphragm o control canister purge. When the engine is running, full manifold vacuum is applied to the top tube of the purge valve which lifts the valve diaphragm and opens the valve.A vent located in the fuel tank, allows fuel vapours to flow to the charcoal canister. a tank pressure control valve, used on some high altitude applications, prevents canister purge when the engine is not running. The fuel tank cap does not normally vent to the atmosphere, but is designed to provide both vacuum and pressure relief.Air injection systemIntroducing a controlled amount of air into the exhaust system promotes further oxidation of the gases. This in turn reduces the amount of carbon monoxide and water, the harmless by-products of combustion. Some system use an air pump, while other use negative exhaust pulses to draw air.The air pump, usually driven by a belt, simply pumps air under a pressure of only a few pounds into each exhaust port. Between the nozzles and the pump is a check valve to keep the hot exhaust gases from flowing back into the pump and hoses thereby destroying them. Most pumps also utilize a gulp valve or a diverter valve. Early system used a gulp valve while later systems use diverter valves. They both operate on the same principle. During deceleration, as the throttle is closed, the explosion in the exhaust system could occur that could blow the muffler apart. During deceleration, the air is either diverted into the atmosphere or into the intake system.On pulse air system, clean air is drawn through a silencer, the check valve and then into the exhaust ports. The negative exhaust pulses opens the reed valve in the check valve assembly, allowing air to flow into the exhaust port.Some feedback-controlled vehicles utilize an oxidizing catalytic converter. Under certain operating conditions, the air is diverted into the catalytic converter to help oxidize the exhaust gases.Exhaust gas re-circulation systemThe EGR system's purpose is to control oxides of nitrogen which are formed during the combustion process. NOx emissions at low combustion temperatures are not severe, but when the combustion temperatures go over 2,500F, the production of NOx in the combustion chambers shoots way up. The end products of combustion are relatively inert gases derived from the exhaust gases. these are redirected ,(under certain conditions) through the EGR valve and back into the combustion chamber. These inert gases displace a certain amount of oxygen in the chamber. Since not as much chamber. These inert gases displace a certain amount of oxygen in the chamber. Since not as much oxygen is present, the explosion is not as hot. This helps lower peak combustion temperatures.The EGR valve can either be actuated by a vacuum diaphragm, a solenoid or stepper motor. On feedback controlled vehicles, the EGR system is controlled by the computer.Catalytic converterThe catalytic converter is a muffler-like container built into the exhaust system to aid in the reduction of exhaust emissions. The catalyst element is coated with a noble metal such as platinum, palladium, rhodium or a combination of hem, when the exhaust gases come into harmless substances such as water and carbon dioxide, oxidizing catalysts into H2O and CO2.While catalytic converters are built in a variety of shapes and sizes, they all fall into two general types, the pellet, or bead type and the monolithic type. Construction may differ slightly, but the object is the same -to present the largest possible surface area to passing exhaust gases. Older vehicles use bead type converters. The exhaust gas must pass through a bed of these pellets. This type of converter is rather restrictive. The cross-section of a monolithic type converter resembles a honeycomb. The exhaust gases are exposed to a greater amount of surface area in these converters; as a result they are more efficient. They also tend to be less restrictive.Dual exhaust systemThe advantage of a dual exhaust system is that the engine exhausts morefreely, thereby lowering the backpressure, which is inherent in an exhaust .with a dual exhaust system, a sizable increase in engine horsepower can be obtained because the breathing capacity of the engine is improved, leaving less exhaust gases in the engine at the end of each exhaust stroke. This in turn, leaves more room for an extra intake of the air-fuel mixture.Hyperboloid gearOn the passenger vehicle main gear box uses the hyperbolic curve gear generally. This is because the hyperbolic curve gear and the spiral bevel gear compare, former revolution noise few, work steadier, turns the tooth intensity high, moreover also has the drive gear spool thread to be possible the relative driven gear disalignment characteristic, this point to be extremely important regarding the automobile technical performance, engineer may in not change the engine the position size to be possible to change the driving axle directly the ground clearance, also is changes the entire vehicle the ground clearance.some automobiles main gear box hyperbolic curve gear off-sets amounts to more than 30 millimeters, in the maintenance certain ground clearance situation, may reduce the drive gear and the drive shaft position, causes the automobile body center of gravity to reduce, is advantageous in enhances the automobile high speed travel the stability. Two gears spool threads intersection driving pulley displaces to underSome automobiles produce the passenger vehicle and movement on the identical frame, its chassis parameter transformation also has used hyperbolic curve gear this characteristic. Because has these merits, at present the automobile driving axle already tended to uses the hyperbolic curve gear, in fact recent years imported the automobile basically was uses the hyperbolic curve gear, the domestically produced automobile also has many vehicle types to use the hyperbolic curve gear, and already more and more were many in center, on the heavy freight vehicle obtains the use.When the hyperbolic curve gear works, between the tooth face can have in a big way skids relatively, also the tooth face pressure is very big, the tooth face lubricant film is easily destroyed. In order to reduce the friction, enhances theefficiency, must have to use includes guards against the abrasion chemical additive the special-purpose hyperbolic curve gear oil, cannot use other gear oil to replace, otherwise will cause the tooth face rapid attrition and the abrasion, seriously will affect the automobile the running status.Further developmentManufacturers around the world are seeking significant improvements in conventional automotive technologies, and Chinese manufacturers risk falling behind if they fail to sustain comparable research efforts on conventional power train systems. The Chinese automotive industry also should strengthen its efforts to develop improved diesel and spark ignition technology in cooperation with its joint venture partners. Researchers should focus on .among other things, advanced gasoline and diesel engine technologies, an ultra-low-emission gasoline engine system, diesel particulate filters, de-NO catalysts, selective catalytic reduction (SCR), and improved in-engine combustion management. Industry must develop the capability to model the vehicle power train system in order to optimize its overall performance, including fuel economy, and vehicle drivability. The automobile's further development will be determined by already existing and steadily increasing requirements, by additional further requirements and by the technical possibilities for meeting these requirements. The following focal point for development and research efforts can be discerned. Further improvement of the automobile through product innovation is in all classic functions, performance, fuel economy, environmental impact, safety, comfort, and reliability.中文翻译排气控制系统排放控制系统的目的只是为了控制车辆废气的排放。
汽车发动机外文翻译文献
汽车发动机外文翻译文献(文档含中英文对照即英文原文和中文翻译)AUTOMOTIVE ENGINE1 Engine Classification and Overall MechanicsThe automobile engines can be classified according to: (1) cycles, (2) cooling system, (3) fuel system, (4) ignition method, (5) valve arrangement, (6) cylinder arrangement, (7) engine speed.Engines used in automobiles are the internal combustion heat engines. The burning of gasoline inside the engine produces high pressure in the engine combustionchamber. This high pressure force piston to move, the movement is carried by connecting rods to the engine crankshaft. The crankshaft is thus made to rotate: the rotary motion is carried through the power train to the car wheels so that they rotate and the car moves.The engine requires four basic systems to run (Fig. 2-1). Diesel engines require three of these systems. They are fuel system, ignition system (except diesel), lubricating system and cooling system. However, three other related systems are also necessary. These are the exhaust system, the emission-control system, and the starting system. Each performs a basic job in making the engine run.Fig. 2-1 The engine construction2 Engine Operating PrinciplesFig. 2-2 Engine termsThe term “stroke” is used to describe the movement of the piston within the cylinder. The movement of the piston from its uppermost position (TDC, top dead center) to its lowest position (BDC, bottom dead center) is called a stroke. The operating cycle may require either two or four strokes to complete. Most automobile engines operate on the four stroke cycle (Fig. 2-2).In four-stroke engine, four strokes of the piston in the cylinder are required tocomplete one full operating cycle. Each stroke is named after the action. It performs intake, compression, power, and exhaust in that order (Fig. 2-3).Intake stroke Compression stroke Power stroke Exhaust strokeFig. 2-3 Four-stroke-cycle gasoline engine1. The intake strokeThe intake stroke begins with the piston near the top of its travel. As the piston begins its descent, the exhaust valve closes fully, the intake valve opens and the volume of the combustion chamber begins to increase, creating a vacuum. As the piston descends, an air/fuel mixture is drawn from the carburetor into the cylinder through the intake manifold. The intake stroke ends with the intake valve close just after the piston has begun its upstroke.2. Compression strokeAs the piston is moved up by the crankshaft from BDC, the intake valve closes. The air/fuel mixture is trapped in the cylinder above the piston. Future piston travel compresses the air/fuel mixture to approximately one-eighth of its original volume (approximately 8:1 compression ratio) when the piston has reached TDC. This completes the compression stroke.3. Power strokeAs the piston reaches TDC on the compression stroke, an electric spark is produced at the spark plug. The ignition system delivers a high-voltage surge of electricity to the spark plug to produce the spark. The spark ignites, or sets fire to, the air/fuel mixture. It now begins to burn very rapidly, and the cylinder pressure increases to as much as 3-5MPa or even more. This terrific push against the piston forces it downward, and a powerful impulse is transmitted through the connecting rod to the crankpin on the crankshaft. The crankshaft is rotated as the piston is pushed down by the pressure above it.4. Exhaust strokeAt the end of the power stroke the camshaft opens the exhaust valve, and the exhaust stroke begins. Remaining pressure in the cylinder, and upward movement of the piston, force the exhaust gases out of the cylinder. At the end of the exhaust stroke, the exhaust valve closes and the intake valve opens, repeating the entire cycle of events over and over again.3 Engine Block and Cylinder Head3.1 Engine BlockThe engine block is the basic frame of the engine. All other engine parts either fit inside it or fasten to it. It holds the cylinders, water jackets and oil galleries (Fig. 2-4). The engine block also holds the crankshaft, which fastens to the bottom of the block. The camshaft also fits in the block, except on overhead-cam engines. In most cars, this block is made of gray iron, or an alloy (mixture) of gray iron and other metals, such as nickel or chromium. Engine blocks are castings.Fig. 2-4 V6 engine blockSome engine blocks, especially those in smaller cars, are made of cast aluminum. This metal is much lighter than iron. However, iron wears better than aluminum. Therefore, the cylinders in most aluminum engines are lined with iron or steel sleeves. These sleeves are called cylinder sleeves. Some engine blocks are made entirely of aluminum.3.2 Cylinder SleevesCylinder sleeves are used in engine blocks to provide a hard wearing material for pistons and piston rings. The block can be made of one kind of iron that is light and easy to cast while the sleeves uses another that is better able to stand up wear and tear. There are two main types of sleeves: dry and wet (Fig. 2-5).Dry sleeve Wet sleeveFig. 2-5 Cylinder sleeve3.3 Cylinder HeadThe cylinder head fastens to the top of the block, just as a roof fits over a house. The underside forms the combustion chamber with the top of the piston. In-line engine of light vehicles have just one cylinder head for all cylinders; larger in-line engines can have two or more. Just as with engine blocks, cylinder heads can be made of cast iron or aluminum alloy. The cylinder head carries the valves, valve springs and the rockers on the rocker shaft, this part of valve gear being worked by the pushrods. Sometimes the camshaft is fitted directly into the cylinder head and operates on the valves without rockers. This is called an overhead camshaft arrangement.3.4 GasketThe cylinder head is attached to the block with high-tensile steel studs. The joint between the block and the head must be gas-tight so that none of the burning mixture can escape. This is achieved by using cylinder head gasket. Gaskets are also used to seal joins between the other parts, such as between the oil pan, manifolds, or water pump and the blocks.3.5 Oil PanThe oil pan is usually formed of pressed steel. The oil pan and the lower part of cylinder block together are called the crankcase; they enclose, or encase, thecrankshaft. The oil pump in the lubricating system draws oil from the oil pan and sends it to all working parts in the engine. The oil drains off and run down into the pan. Thus, there is a constant circulation of oil between the pan and the working parts of the engine.4 Piston Assembly, piston rings , The piston pin ,Connecting Rods, Crankshafts And Flywheel4.1 PistonPiston rings and the piston pin are together called the piston assembly (Fig. 2-6).Fig. 2-6 Piston, piston rings and connecting rodThe piston is an important part of a four-stroke cycle engine. Most pistons are made fr om cast aluminum. The piston, through the connecting rod, transfers to the crankshaft the force created by the burning fuel mixture. This force turns the crankshaft.To withstand the heat of the combustion chamber, the piston must be strong. It also must be light, since it travels at high speeds as it moves up and down inside the cylind er. The piston is hollow. It is thick at the top where it takes the brunt of the heat and th e expansion force. It is thin at the bottom, where there is less heat. The top part of the piston is the head, or crown. The thin part is the skirt. Most pistons have three ring gro oves at the top. The sections between the ring grooves are called ring lands.4.2 piston ringspiston rings fit into ring grooves near the top of the piston. In simplest terms, pisto n rings are thin, circular pieces of metal that fit into grooves in the tops of the pistons. In modern engines, each piston has three rings. (Piston in older engines sometimeshad four rings, or even five.) The inside surface of the ring fits in the groove on the pi ston. The ring's outside surface presses against the cylinder walls. Rings provide the n eeded seal between the piston and the cylinder walls. That is, only the rings contact th e cylinder walls. The top two rings are to keep the gases in the cylinder and are called compression rings. The lower one prevents the oil splashed onto the cylinder bore fro m entering the combustion chamber, and is called an oil ring.4.3 The piston pinThe piston pin holds together the piston and the connecting rod. This pin fits into th e piston pin holes and into a hole in the top end of the connecting rod. The top end of t he rod is much smaller than the end that fits on the crankshaft. This small end fits insi de the bottom of the piston. The piston pin fits through one side of the piston, through the small end of the rod, and then through the other side of the piston. It holds the rod firmly in place in the center of the piston. Pins are made of high-strength steel and hav e a hollow center. Many pins are chrome-plated to help them wear better.A piston pin fits into a round hole in the piston. The piston pin joins the piston to the connecting ro d. The thick part of the piston that holds the piston pin is the pin boss.4.4 Connecting RodsThe connecting rod little end is connected to the piston pin. A bush made from a soft metal, such as bronze, is used for this joint. The lower end of the connecting rod f its the crankshaft journal. This is called the big end. For this big-end bearing, steel-ba cked lead or tin shell bearings are used. These are the same as those used for the main bearings. The split of the big end is sometimes at an angle, so that it is small enough t o be withdrawn through the cylinder bore. The connecting rod is made from forged all oy steel.4.5 CrankshaftsThe crankshaft is regarded as the “backbone” of the engine (Fig. 2-7). The crankshaft, in conjunction with the connecting rod, converts the reciprocating mo tion of the piston to the rotary motion needed to drive the vehicle. It is usually made fr om car-bon steel which is alloyed with a small proportion of nickel. The main bearing journals fit into the cylinder block and the big end journals align with the connecting rods. At the rear end of the crankshaft is attached the flywheel, and at the front end ar e the driving wheels for the timing gears, fan, cooling water and alternator. The throw of the crankshaft, i.e. the distance between the main journal and the big end centers, controls the length of the stroke. The stroke is double the throw, and the strokelength is the distance that the piston travels from TDC to BDC and vice versa.Fig. 2-7 The crankshaft4.6 FlywheelThe flywheel is made from carbon steel. It fits onto the rear of the crankshaft. As well as keeping the engine rotating between power strokes it also carries the clutch, w hich transmits the drive to the gearbox, and has the starter ring gear around its circumf erence. There is only one working stroke in four so a flywheel is needed to drive the c rankshaft during the time that the engine is performing the non-power strokes.5 Valve SystemFig. 2-8 Parts of the valve trainThe valve operating assembly includes the lifters or cam followers, pushrods, rocker arms and shafts or pivot, valve and springs etc. The purpose of this to open and close the intake and exhaust ports that lead to the combustion chambers as required (Fig. 2-8). Valve mechanisms vary depending on the camshaft location. When the camshaft is positioned in the engine block, valve lifters are mounted in the openings above the camshaft. Pushrods are connected from each valve lifter to a pivoted rocker arm mounted above each valve. A lobe on the camshaft is positioned directly below each valve lifter. A typical camshaft drive has a sprocket bolted to the end of the camshaft, and a matching sprocket is attached to the end of the crankshaft. Those two sprockets may be meshed together or surrounded a steel chain to have the camshaft drive. When the lower part of the camshaft lobe is rotating under the valve lifter, the valve spring holds the valve closed.汽车发动机1发动机的分类和整体力学汽车发动机可根据如下因素进行分类:(1)循环系统,(2)冷却系统,(3)燃油系统,(4)点火方式,(5)气门布置,(6)气缸排列,(7)发动机转速。
中英文文献翻译-发动机冷却系统
中英文文献翻译-发动机冷却系统1S u m m a r i z eOutli ne use s a m ore compact desi gn along w ith the engi ne and has in a bi g w ay, the engi ne produces the w aste he at de nsity also obvi ousl y i ncre ases al ong with it. S ome essenti al re gi ons, i f around a row of ty re v al ve radi ate s the questi on to have fi rst to conside r, the cooli ng sy ste m eve n i f appears the small bre akdow n al so possi bl y to cre ate the di saste r in such re gion conse que nce. The e ngi ne cooli ng sy ste m radi ati on ability gene rall y shoul d sati sfy w he n the engi ne full load radi ati on dem and, be cause thi s ti me e ngine produces the quantity of he at is bi g gest. Howe ve r, w he n parti al l oads, the curre nt capacity w hi ch the cooli ng sy ste m can have the powe r loss, whi ch the w ate r pum ping stati on provi des the re fri ge rant current capacity surpasses nee ds. W e hoped starts the starting ti me to be as far as possi ble short. B e cause engi ne ti me di scharges poll utant m ore , the oil consum pti on is also bi g. T he cooling sy stem structure has a m ore tre mendous infl uence to the e ngi ne cold starting ti me.2C h a r a c t e r i s t i c s of m od e r n e n g in e c oo l in g s y s t e mM ode rn e ngi nes serie s characteri sti c tradition cooling sy ste m function reli abl y prote cts the engi ne, but also shoul d have the functi on w hi ch the i mprove ment fuel e conom y and reduces discharges. There fore, the m odern cooli ng sy stem must sy nthesize under the consi deration the factor: Engi ne inte rior fri cti on l oss; C ooli ng syste m w ater pump powe r; B urning boundary conditi on, li ke combusti on cham ber tem pe rature, complete density , complete te mpe rature . The advance d cooling sy ste m uses sy ste m atize d, the modular desi gn method, the ove rall pl an conside re d e ach i nfl ue nce factor, cause s the cooling sy stem both to guarantee the e ngi ne norm al w ork, and enhance s the engi ne e ffi cie ncy and the reducti on di scharge s.2 .1 T h e t e m p e r a t u r e s se t p o in tTempe ratures hy pothe ses fi ring i n bursts m otive operati ng tem pe rature l i mit value are de cide d by a row of tire v al ve the peri pheral re g i on m axi mum tem perature. T he m ost ide al situation is according to the metal tempe rature but is not the refri gerant te mpe rature control cooling sy ste m, like thi s can prote ct the e ngi ne w ell.B ecause the cooling sy ste m hy pothe sis cooli ng te mpe rature i s by the full l oad ti me m ost is bi g i s the foundati on, there fore, engi ne and cooling sy s tem in parti al l oads ti me is at not too the perfe ct conditi on, w hen urban distri ct travel and l ow spee d travel, can have the hi gh oil consumpti on and di scharge. S upposes the fixe d point through the change re fri ge rant tem perature to be possible to i mprove the engine and the cooling sy ste m in parti al l oads time perform ance. A ccording to a row of ty re v al ve the peripheral re gion tem pe rature li mit v alue, m ay elevate either reduce the re fri ge rant or the metal te mpe rature supposes the fixe d point. Ele v ates or reduced tem pe rature all re spe cti vel y has the characte risti c, this i s decide d the goal w hi ch achie ved to the hope .2 .2 E n h a n c e s t h e t e m p e r a tu r eEnhance s the tem pe rature to suppose the fixe d-point enhance ment operati ng te mpe rature to suppose the fixe d point is one ki nd of com parison the method w hi ch wel come. Enhance s the tempe rature to have m any meri ts, it dire ctl y affects the e ngine l oss and the cooli ng sy stem e ffe ct as well as the e ngi ne di schargi ng form ation. W ill enhance the operati ng te mpe rature to enhance the e ngine M ac re duce the engi ne to rub we ars, reduces the engine fuel oil consum pti on. The rese arch indi cated that, the e ngi ne operating te mpe rature to rubs the l oss to have the ve ry treme ndous i nflue nce. Discharges the te mpe rature the re fri ge rant to enhance to 150 ℃ , causes the cy l i nde r te m perature to ele vate to 195 ℃ , the oil consumption drops 4% -6% . M ai ntains the refri gerant te m perature i n 90 -1 15 ℃ scope, causes the engine m achine oil the m axi mum te mpe rature is 14 0 ℃ , then oil consumpti on in partial loads ti me drops 10% . Enhances the operati ng te mpe rature al so obvious infl ue nce cool ing sy ste m the pote ncy. Enhances the refri ge rant or the metal te mpe rature can i mprove the engi ne and di spe rse the ste am he at transfer transmission the effe ct, re duce s the re fri g erant the speed of fl ow, reduces the w ate r pump the rate d power, thus re duce s the engi ne the pow e r di ssi pation. In addition, m ay sele ct the diffe rent method, furthe r re duces the re fri ge rant the speed of flow .2 .3 R e d u c e th e t e m p e r a t u r e s se t p o i n tR educed te m peratures suppose the fi xed point to reduce the cooli ng sy stem the ope ra ti ng tem perature to be possi ble to e nhance the engine charge e ffi ciency , re duce s the inlet te mpe rature. Thi s to the com bustion proce ss,the fuel oil effi cie ncy and discharges adv antage ousl y . T he reduced tem perature supposes the fi xed poi nt to be all owed to save the engine m ove me nt cost, enhances the part servi ce li fe. The rese arch indi cate d, if the cy linde r he adte mpe rature re duce s to 50 ℃ , the i gnition angle of advance m ay 3 ℃ A but not have the engi ne knock ahe ad of time , the charge effi cie ncy enhances 2 % , the e ngi ne ope rati onal factor i mprove ment, is hel pfulto the opti mize d com pre ssi on rati o and the paramete r choi ce, obtai ns the bette r fue l oil effi ciency anddischarges the pe rform ance.2 .4 P r e c i se c oolin g sy s t e mPre cise cooling sy stem s pre ci se cooli ng sy ste m mainl y m ani fests i n the cooli ng j acket s tructural desi gn and in the refri gerant spee d of fl ow desi gn. In pre cise cooling system, hot e ssenti al are a, i f around a row of ty re valve, the re fri ge rant has an gre ate r spee d of fl ow , the he at transfer effi cie ncy is hi gh, the refri gerant gradie ntof tem pe ra ture changes sli ghtl y . S uch e ffe ct comes from to re duce these pl ace re fri ge rant channels the l ate ral secti on, e nhances the spee d of fl ow, re duce s the current capacity . T he pre ci se cooli ng sy ste m desi gn ke y lies in the de termi nation cooli ng j acke t the size, the choi ce m atch cooling w ate r pum p, guaranteed the sy ste m the radi ati on ability can satisfy w hen the l ow spee d bi g load essenti al re g i on operating te m perature de m and. The engi ne refri gerant spee d of fl ow range of vari ati on is quite bi g , from ti me 1 m /s to m axi mum w ork rate time 5 m /s. The re fore shoul d conside re d the cooli ng j acket and the cooling sy stem whole that, m utuall y suppleme nted, displ ay bi gge st pote nti al. The rese arch indi cate d that, uses the pre cise cooling sy stem , i n the engi ne entirew ork rotational spee d scope , the refri gerant curre nt capacity m ay drop 4 0% . C ove rs the cool ing j acket to theai r cy linde r the pre cise de si gn, m ay m ake the ordi nary spee d of fl ow to e nhance from 1 .4 m /s to 4 m /s , gre atl y enhances the cy l inde r cove r or cap the rm al conducti vity , cy l inde r cove r or cap metal te mpe rature drop to60 ℃ .2 .5 Div e r g e n c e s t y p e s c oolin g s y s t e mDiverge nce s ty pe s cooli ng sy ste m dive rge nce ty pe cooli ng sy stem for othe r one ki nd of cool ing sy ste m. In this ki nd of cooli ng sy ste m, the hi ne oil te mpe rature , will cy l i nde r cove r or cap frie ndl y cy li nde r body cools by respective return route , the cyl inder cover or cap friendl y cyli nder body has the di ffe rent tem perature. T hedive rge nce -li ke cooli ng sy ste m has the uni que supe ri ority , m ay cause e ngi ne e ach part to suppose the fixe d-point w ork at the m ost supe rior tem pe rature. The cooli ng sy ste m ove rall effi cie ncy achieves i n a bi g w ay . Each cooling return route w il l suppose unde r the fixe d poi nt or the speed of fl ow i n the diffe rent cooli ng tempe rature works, w i ll cre ate the i deal engi ne te mpe rature distri bution. T he i de al e ngi ne hot acti ve status isthe cy linder he ad te mpe rature lowe r but the ai r cyl inder body te m perature rel ative is hi ghe r. T he cy linde r he ad tempe rature is l ow e r m ay e nhance the charge e ffi ciency , i ncre ases. The tem perature is l ow also gre atl y m ay promote completel y to burn, re duces C O, HC and the NOx form ation, a lso enhance s the output. T he hi gher ai rcy linde r body tem perature can re duce the fri cti on to lose, di re ctl y im proves the fuel oil effi ciency , i ndire ctl y reduces i n the cy li nde r the peak val ue pressure and the tem pe rature. T he dive rge nce ty pe cool ing sy ste m m ay cause the cy linder cove r and the cy linde r body tem pe rature di ffe rs 1 00 ℃ . T he cy l inde r te mpe rature m ay re achas hi gh as 15 0 ℃ , but the cy li nde r cove r tem perature m ay re duce 50 ℃ , re duce s the cy linde r body to rub l oses, reduces the oil consum ption. The hi ghe r cy linde r body tem perature causes the oil consum pti on to re duce4% -6% , w hen parti al l oads HC reduces 20 % -3 5% . W hen the dampe r all opens, the cy li nde r cove r and the cy linde r body tem perature supposes the de finite v al ue to be possi ble to move to 50 ℃ and 90 ℃ , im prov es thefuel oil consum pti on, the pow e r output from the w hole and di scharge s.2.6 C on t r o l l a b l e c oolin g s y s t e mControll able e ngi ne cooli ng sy ste m tradition e ngi ne cool ing sy ste m bel ongs to the passive form, thestructure sim ple or the cost i s l ow. T he control lable cooling system m ay m ake up at pre sent cool ing sy ste m the insuffi cie ncy . Now the cooli ng sy stem de si gn standard sol ves time the full l oad radi ati on proble m, thus parti al l y shoulde rs time the oversized radi ati on ability wi l l cause the engi ne powe r w aste. This to the li ghtvehi cle said espe ci all y obvi ous, the se ve hi cles m aj ority ti me all unde r the parti al loads go in the urban distri ct, only uses the parti al e ngine power, causes a cooling system hi ghe r l oss. In order to solve the e ngi ne to getdow n the hot questi on in the pe culi ar ci rcumstance, the pre sent cooling sy stem v ol ume w as bi gge r, causes the evaporati on e ffi cie ncy to re duce, has i ncreased the cooling sy stem pow er de m and, leng thene d the engi ne duri ng w arm m achi ne -hour. The controll able engi ne cooli ng sy ste m gene rall y incl udes the se nsor, the executi on and the ele ctri call y controlle d m odule. T he controll able cooling sy stem can act accordi ng to the engi ne w orki ng condition adjustme nt cool ing quantity , reduces the e ngine power loss. In the controll able cooli ng sy ste m, the e xe cuti on for the cooli ng w ate r pump and the therm ostat, ge neral l y and the control val ve is com posed by the ele ctri call y ope rate d w ate r pum p, m ay act accordi ng to requests to adjust the cooli ng quanti ty. Tempe rature sensor for a sy ste m part, but rapidl y beque aths the e ngi ne hot condi tion the controlle r.Controll able i nstall me nt, i f the ele ctri call y ope rated w ate r pump, m ay suppose the tem perature the fi xed point from 90 ℃ to enhance to 11 0 ℃ , save s 2% -5 % fuel oil, C O re duce s 20 % , HC re duce s 10% . W he n ste ady state, the metal te mpe rature rati o tradition cooling sy ste m is hi gh 10 ℃ , the controll able cool ing sy ste m has the qui cker re sponse ability , m ay cool the te mpe rature to m ai ntai n is supposing the fi xed point ±2℃the scope . From 110 ℃ drops to 10 0 ℃ onl y nee ds 2 s. T he engi ne during w arm m achi ne-hour re duces 200 s, the cool ing syste m ope rati ng re g i on draws cl ose to the work li mit re gi on, can reduce the engi ne cooling te m perature and the metal te mpe rature undul ati on scope, re duce s ci rcul ate s the fati gue of metal whi ch the hot l oad creates, lengthens the com ponent l i fe.3C o n c lu s ionIn front of 3 concl usi ons i ntroduce d se ve ra l k ind of advance d cooli ng sy ste ms have the im proveme nt cooli ng sy ste m perform ance the potenti al, can e nhance the fuel oil e ffi ciency and di scharge the pe rform ance. The cooli ng sy stem can control the nature is i m prove s the cooli ng sy ste m the key , can the control ling expression to the engi ne structure prote cti on esse nti al paramete r, like the metal tem pe rature , the re fri ge rant tempe rature and the machi ne oil te mpe rature and so on can control, guarantees the e ngi ne to w ork i n the safety m argi n scope . The cooling sy stem can m ake the rapi d reaction to the diffe rent operating mode, the most e arth saves the fuel, re duces di scharge s, but does not affect the engi ne ove rall perform ance . Looked from the desi gn and the ope rati onal pe rform ance angle that, dive rgence ty pe cooli ng and pre ci se cooli ng uni fies has the ve rygood prospe cts for devel opme nt, both can provi de the ide al engine prote ction, and can enhance the fuel oileffi ciency and discharge the nature. This ki nd of structure is adv antageous to formi ng the engi ne i deal tempe rature di stri bution. Dire ctl y to a cyli nder cover or cap row of ty re v al ve around the suppl ies refri ge rant, reduced the cy li nde r he ad tem pe rature change, causes the cyli nder cover tem pe ra ture di stri bution to be eve ne r, also can m aintai ns the m achine oil and the cy linde r body tem perature at the desi gn ope rating re gion, has a lowerfri cti on to dam age the poll ution wi thdraw a l■.cooli ng sy ste m functi on and m aintenance m ai ntenance method as follow s:1st, the cooling sy stem function, i s part of quantity of he ats w hi ch absorbs the engi ne part carrie s off, guarantee d the diesel e ngine various components m a intai n i n the norm al te mpe rature range.2nd, the cool ing w ate r shoul d be does not contai n dissol ves the X ie salt the soft w ater, l ike cle an rive r w ate r, rain w ater and so on. Do not use hard w ate r and so on the well w ater, w ater see page or sea w ater, guards against produces, causes the e ngi ne to radi ate not good, que stion occurrence and so on ai r cy linde r he at.3rd, w ith the funnel w hen joins the cooli ng w a ter the w a ter tank, m ust preve nt the w ate r spl ashes to on the engi ne and the radi ator, preve nte d on the radi ator fi n and the organism accum ul ates the dust, smears, affe cts the cooli ng effe c t.4th, i f w hen the e ngine l acks the w ater cause s the hy perpy re xi a, cannot i m medi atel y add w ate r, shoul d cause the engi ne i dling spee d to revolve 1 0 □15 mi nute s, afte r the uni form te mpe rature sli ghtl y reduces, sl owl y does not joi n the cooli ng w ate r i n the engi ne situati on.5th, the wi nter, the w ate r tank pl anted agent adds the hot w ate r. A fte r the start should surpass 40de gree-hour the s low re vol uti on to the w ater tem pe rature to be able to w ork. A fte r the w ork had ended, must put the completel y cooling w ate r.6th, must re gul arl y el imi nate i n the w ate r tank , must fre que ntl y scour the sludge to the forced-ai r cool ing engi ne radi ator fin, dirty i s fi l thy . The radi ator fi n cannot dam age, afte r i f dam ages m ust prom ptl y re pl ace, i n orde r to av oi d i nfl uence radi ati on effe ct.4L a t h e sL athe s are m achi ne tool s desi gned pri m aril y to do turni ng, faci ng and bori ng, Very li ttl e turni ng is done on othe r ty pe s of m achine tools, and none can do it w ith equal facility. B e cause l athe s also can do dri lling and re ami ng, their ve rsatil ity pe rmi ts se ve ral ope rations to be done w ith a single setup of the work pie ce . Conseque ntl y, more l athes of various ty pesare used in m anufacturing than any othe r m achine tool.The esse nti al compone nts of a l a the are the bed, he adstock asse m bl y, tail stock assem bl y, and the le ads cre w and fee d rod.The be d is the backbone of a l athe. It usuall y is m ade of we ll norm al ized or age d gray or nodul ar cast iron and provide s s he av y, ri gi d frame on w hi ch al l the othe r basi c com ponents are m ounted. Two sets of parallel, longitudi nal w ays, i nner and outer, are containe d on the be d, usuall y on the uppe r side. S ome make rs use an inve rte d V-shape for all four w ay s, whe re as others utilize one i nve rte d V and one fl at w ay i n one or both sets, The y are preci si on-machi ned to assure accuracy of al i gnme nt. On m ost m odern l athes the w ay are surface -hardene d to re sist w e ar and abrasi on, but pre cauti on should be taken i n ope rati ng a la the to assure that the w ay s are not dam age d. A ny i naccuracy in the m usuall y means that the accuracy of the enti re l athe is destroy ed.The he adstock is m ounte d in a foxe d position on the inne r w ay s , usuall y at the left end of the bed. It provides a pow e red means of rotating the word at vari ous speeds . Essenti all y, it consists of a hol low spi ndle, mounted i n accurate be ari ngs, and a set of transmission ge ars-si mil ar to a truck transmission—through w hi ch the spi ndle can be rotated at a num ber of speeds. M ost l athes provi de from 8 to 18 speeds, usuall y i n a geometri c ratio, and on m ode rn l athes a ll the spee ds can be obtaine d me rel y by movi ng from two to four le vers. A n i ncre asing trend i s to provide a continuousl y v ari able speed range through e lectri cal or mechani cal dri ves.B ecause the accuracy of a l athe is gre atl y depe nde nt on the spi ndle, it i s of he av y construction and mounted in he avybe ari ngs, usuall y prel oade d tape red rolle r or bal l ty pes. T he spi ndle has a hole exte nding through its length, through w hi ch l ong bar stock can be fed. T he size of m axi mum size of bar stock that can be m achi ned whe n the m aterial must be fe d through spi ndle .The tail sti cd asse mbl y consi sts , esse nti all y, of three parts.A lowe r casti ng fi ts on the i nne r w ay s of the bed and can slide longitudi nall y the reon, w ith a me ans for cl am ping the e nti re assem bl y in any desi re d l ocation, An upper casti ng fits on the lowe r one and can be moved transversel y upon it, on some type of ke y e d w ay s, to permit ali gni ng the assem bl y is the tail stock quill. Thi s i s a holl ow steel cy li nder, usuall y about 51 to 76 m m( 2to 3 inches) i n diamete r, that can be m ove d seve ral i nches longitudi nall y i n and out of the upper casti ng by me ans of a hand w heel and scre w.The size of a l athe is desi gnate d by tw o dime nsi ons. The fi rst is k now n as the swing. This is the m axi m um di amete r of work that can be rotated on a l athe . It is approxim atel y tw i ce the distance betw ee n the li ne conne cting the la the ce nte rs and the ne are st poi nt on the w ay s, The se cond size dim ensi on is the m axi mum distance betw een cente rs . The sw i ng thus i ndi cate s the m axim um w ork pie ce di amete r that can be turne d i n the lathe, w hile the distance betw een centers i ndicates the m axi mum length of w ork pie ce that can be mounte d betw een ce nte rs.Engi ne l athe s are the ty pe most freque ntl y use d in m anufacturi ng. The y are he av y -duty m achine tools with all the com ponents descri bed pre viousl y and have powe r drive for al l tool move ments exce pt on the compound rest. T he y com monl y range i n size from 305 to 610 mm( 12 to 2 4 inches) sw ing and from 610 to 12 19 m m( 2 4 to 48 i nches) ce nte r distances, but sw ings up to 1270 m m( 50 inches) and ce nte r distances up to 3658 m m( 12 feet) are not uncom mon. M ost have chi p pans and a built-i n cool ant ci rcul ating syste m. S m alle r engine lathes-with swi ngs usuall y not over 330 m m ( 1 3 inches ) –a l so are avail able in bench ty pe, de si gned for the bed to be mounted on a bench on a be nch or cabine t.Although engine l athes are ve rsatile and ve ry use ful, be cause of the ti me re qui re d for changi ng andsetting tool s and for m aki ng me asure me nts on the w ork piece , thy are not suitable for quantity producti on. Often the actual chip-producti on ti ne is less than 30 % of the total cy cle time . In additi on, a skil led machi nist is requi red for all the ope rati ons, and such pe rsons are costl y and ofte n i n short suppl y. How eve r, much of the ope rator ’s ti me is consumed by sim ple, re petitious adj ustments and in w atchi ng chips bei ng m ade. Conseque ntl y, to reduce or eli mi nate the am ount of skille d l abor that is re quire d, turret lathes, scre w m achi nes, and other ty pes of sem iautom atic and autom ati c l athes have been hi ghl y devel oped and are w i del y use d i n m anufacturing.5L im its and Toler ancesM achine parts are m anufacture d so the y are inte rchange able. In othe r words, e ach part of a m achi ne or me chanism is m ade to a certai n size and shape so w il l fit i nto any othe r m achine or me chanism of the same type. To m ake the part inte rchange able , e ach i ndi vi dual part m ust be m ade to a size that w i ll fit the m ati ng part in the corre ct w ay . It is not onl y i m possible, but also im practi cal to m ake m any parts to an ex act size. Thi s is because machi nes are not pe rfe ct, and the tool s be come w orn. A sl i ght vari ation from the e x act size i s al way s all owed. T he amount of this v ari ation depe nds on the ki nd of part being m anufacture d. For ex am ples part mi ght be m ade 6 in. long w i th a vari ati on all owed of 0. 003 ( three-thousandths) in. above and bel ow this size . There fore, the part coul d be 5 .997 to 6. 003 in. and s till be the corre ct size . The se are k now n as the l imi ts. T he diffe rence betw ee n upper and l ow er li mits is calle d the tolerance.1 概述随着发动机采用更加紧凑的设计和具有更大的比功率,发动机产生的废热密度也随之明显增大。
发动机类外文文献翻译
400 Commonwealth Drive, Warrendale, PA 15096-0001 U.S.A.Tel: (724) 776-4841 Fax: (724) 776-5760SAE TECHNICAL PAPER SERIES2000-01-1546Lightweight Engine Design StrategiesW. Schöffmann, F. Beste and R. MarquardAVL List GmbH, AustriaReprinted From: 2000 Future Car Congress Proceedings CD-ROM2000 Future Car CongressArlington, VirginiaApril 2-6, 2000The appearance of this ISSN code at the bottom of this page indicates SAE’s consent that copies of the paper may be made for personal or internal use of specific clients. This consent is given on the condition,however, that the copier pay a $7.00 per article copy fee through the Copyright Clearance Center, Inc.Operations Center, 222 Rosewood Drive, Danvers, MA 01923 for copying beyond that permitted by Sec-tions 107 or 108 of the U.S. Copyright Law. This consent does not extend to other kinds of copying such as copying for general distribution, for advertising or promotional purposes, for creating new collective works,or for resale.SAE routinely stocks printed papers for a period of three years following date of publication. Direct your orders to SAE Customer Sales and Satisfaction Department.Quantity reprint rates can be obtained from the Customer Sales and Satisfaction Department.T o request permission to reprint a technical paper or permission to use copyrighted SAE publications in other works, contact the SAE Publications Group.No part of this publication may be reproduced in any form, in an electronic retrieval system or otherwise, without the prior written permission of the publisher.ISSN 0148-7191Copyright © 2000 Society of Automotive Engineers, Inc.Positions and opinions advanced in this paper are those of the author(s) and not necessarily those of SAE. The author is solely responsible for the content of the paper. A process is available by which discussions will be printed with the paper if it is published in SAE T ransactions. For permission to publish this paper in full or in part, contact the SAE Publications Group.Persons wishing to submit papers to be considered for presentation or publication through SAE should send the manuscript or a 300word abstract of a proposed manuscript to: Secretary, Engineering Meetings Board, SAE.Printed in USAAll SAE papers, standards, and selected books are abstracted and indexed in the Global Mobility Database2000-01-1546Lightweight Engine Design StrategiesW. Schöffmann, F. Beste and R. MarquardAVL List GmbH, Austria Copyright © 2000 Society of Automotive Engineers, Inc.ABSTRACTDuring the past years advances in fuel efficiency of car engines did not result in the expected reduction in overall fuel consumption of new car generations. One reason is the increasing vehicle weight. In an overall-weight analysis of an automobile the engine and as part of it, the crankcase represents a single component with a high weight reduction potential. This paper discusses weight reduction strategies using lightweight materials and modern design approaches.The application of lightweight materials for new crankcase concepts implies comprehensive design considerations to achieve weight reductions as close as possible to the potential of the selected material. A specific approach for inline and V-engine crankcase concepts is discussed in detail. Engine weight reduction can also be achieved through substituting large and therefore heavy engines with small high performance engines. Modern technologies applied to existing engine concepts increase the power-weight ratio, the engine’s capability and therefore its marketing value.New lightweight design strategies allow a significant reduction of engine mass compared to conventional concepts and represent an important contribution to reduce the overall vehicle weight.INTRODUCTIONThe demands on the automobile have increased significantly in terms of ecological aspects and are generally set to continue with regard to future transportation concepts. This customer-induced pressure is accompanied by tightened legal requirements especially in the USA and in Europe. In anticipating this fact, answers need to be found to the central question of fuel consumption, emissions and recycling strategies. Progress was made in the development of car engines during the past years. A significant increase in power output in combination with decreased specific fuel consumption and emissions have been obtained through enormous development efforts. The most remarkable advances were achieved through applying direct injection, exhaust-gas turbo charging and multi-valve technology to high performance diesel engines [1. ]. The resulting engine efficiency increases were not translated into vehicle efficiency improvements when a new car model replaced its precursor with a comparable performance. One reason for the stagnating or even decreasing overall vehicle efficiency is an increase of 15-20% in the mass of cars over the past 15 years (Figure 1). Despite the growing use of lightweight materials and the designers’ sensitivity towards lightweight construction, the weight reductions have been more than compensated. Reasons for this include :•additional vehicle features•improved safety and security•improved comfort aspects in regard to NVH •increased power output to maintain or improve car performance•improved reliabilityFigure 1.Vehicle weight increase [Data corresponding to 2. ]This development is not reversible. The continuously growing customer demands and stricter standards support the trend toward heavier cars. Therefore, it is important to identify the most convenient way to reduce the mass of a car engine while maintaining the engine’s performance. Special attention was given to the crankcase, which contributes 20-25% to the overall engine weight. Most challenging is the diesel engine crankcase. Peak firing pressures of up to 16MPa result in the comparably highest specific part loads.Figure 2 shows the weight contribution of the core components of a typical 2 liter gasoline engine. One dominant part is the crankcase yielding a potential for weight reductions of 10-12% based on the cast-iron version.Figure 2.Weight contributions of main engine componentsThe conditions of use for each material need to be improved and the applicability of new, lightweight materials must be evaluated from technical as well aseconomic viewpoints. The purpose of weight reduction is not merely reduced consumption and emissions and improved vehicle performance, it is also suitable to reduce the costs of individual components. This paper discusses the conception of modern high performance engines with regard to the achievable weight reductions.ENGINE CONCEPTEngines with a high power-weight ratio and torque have the highest potential to reduce the engine weight. Direct injection and exhaust gas turbo charging are the key technologies for a maximum power density of modern diesel engines. Four-valve technology should be considered for cylinder diameters of 75mm and above to facilitate an increased power-weight ratio (Pe/m) relative to standard drive units while observing tightened emission laws. Figure 3 displays the growing power-weight ratio for an engine during its production life cycle achieved with only small changes to the base engine structure.The scope for further increases in power-weight ratio and engine torque through technologies such as direct injection and turbo-charging is being narrowed as more stringent emission regulations are enacted. Therefore,structural approaches will win a growing importance to engine development in future. Modern crankcase concepts employing lightweight materials and adapted design concepts are one central contribution to the necessary vehicle weight reductions.Figure 3.Power density progressLIGHTWEIGHT DESIGN CONCEPTS – Different single or combined strategies can be employed to effectively reduce the weight of a typical car engine. Figure 4displays the four main approaches for a lightweight concept. The basic engine concept, the component design and the material are strongly linked due to the accompanying calculations of structural strength and acoustic behavior.Figure 4.Weight reduction strategiesThe dominant boundary conditions for crankcase design result form the production process and functional requirements. Innovative design approaches are essential to utilize the potentials of lightweight materials resulting from their advantage in material density.Because of higher material costs and the in some cases more costly processing simple material substitution from ferrous to lightweight materials yields higher component costs. Only the combined use of lightweight materials and an innovative approach to engine concept and component design results in a lighter and cheaper component (Figure 5).Figure 5. Component optimization and lightweight costsThe effort to find the optimum design for specific lightweight material properties is often limited due to additional requirements imposed by engine familyconcepts. Dedicated production lines, for example, call for constant main dimensions such as bore spacing and top deck height. Nevertheless, increasing the marketing value of an existing crankcase is also feasible through material substitution while keeping the machining and assembly process constant. Redesigning needs to be performed only on the casting itself to adapt it to the changed material properties (Figure 6).Figure 6.Material substitution CI→ Aluminum [3. ]Crankcase design revisions with some flexibility in the machining process and new crankcase designs allow significantly more freedom in the crankcase concept.One example is the make of a crankcase following the AVL trussing concept [4. ]. The main core package comprises a single-piece crank core with two stiff grid cores on each side (Figure 7). The AVL trussing system unites a high weight reduction potential with a stiff structural concept. Other advantages are the acoustic behavior and the design of the oil drain channels with connecting horizontal galleries allowing the integration of the crankcase ventilation.Figure 7.Core package of the AVL trussing conceptAt first this trussing concept was designed as a material optimized concept for compacted graphite iron (CGI)crankcases [5. ] but has also proven to be a base design for gray cast iron (CI) crankcases [6. , 7. and 8. ].A material-sensitive top deck design of a CGI crankcase is shown in Figure 8. In structurally stressed areas the deck thickness is crowned between 10-14mm to obtain good acoustic behavior and to reduce the top deck weight [9. ]. Areas with minor stresses were made with the minimum wall thickness of 3.5mm. A weight-optimized design of crankcase flange areas is of higher significance for the lightweight potential compared to the costly reduction of the minimum wall thickness.Figure 8.T op deck designMATERIAL CONCEPTS – Figure 9 shows a variety of possible crankcase materials and design concepts and their fundamental effect to the component weight.Figure 9.Effect of crankcase material and designCGI offers, despite nearly identical material densities with CI, the superior material strength and a potential weight advantage of about 10% if combined with a consequent lightweight design approach. The shown compound concepts constitute special solutions. A complex skeleton frame made of a ferrous material carries the gas and bolt forces and integrates cylinder liners and threat bosses for the cylinder head and main bearing wall bolts. For the Steel compound (St comp) solution the sealing outer skin is made of cast-in sheet metal [10. ] and the skeleton frame of the Aluminum compound (Al comp) solution is enveloped with an aluminum alloy. The applicability of both concepts for standard low-cost inline crankcases is limited due to the additional costs caused by the complex skeleton frame. An alternative to this technologyfacilitating lightweight materials even for high-speed diesel engines are less complex, separate inlays made of CGI or spherical graphite iron (SGI) in each main bearing wall excluding the cylinder liners.T oday, aluminum, with a weight reduction potential of up to 40%, substitutes the former proven ferrous designs.Especially die-cast crankcases made of secondary aluminum with cast-in CI liners have proven to be a suitable solution for mass production. Decisive reasons beside the dominant weight-reduction potentials are •superior thermal conductivity•potential for advanced manufacturing technologies supporting complex and filigree structures like cast-in oil feeds•high integration potential•tighter range of tolerances possible •marketing advantageMagnesium, the lightest material suitable for crankcases,constitutes a design challenge especially for high-speed diesel engines. Basic risks in the use of magnesium naturally exist, but research programs for mass production magnesium crankcases normally result in beneficial design solutions for the aluminum version.Nevertheless, the current value of the minimum wall thickness for aluminum and magnesium makes it impossible to reduce the weight according to the materials full potential.Selecting the material for a typical crankcase involves defined design parameters as well as the question if the specific properties of the pre-selected material fulfill the requirements of the engine to that component. T able 1summarizes the main material properties. Decisive for the structural stiffness is the ratio of Y oung’s modulus and material density. The tensile strength and Y oung’s modulus mainly influence the static strength of the crankcase and the maximum main bearing and cylinder-head bolt forces. Main parameter for the dynamic strength and the endurable peak firing pressure is the bending endurance limit of the material (fatigue limit).Other important material properties for crankcase designT able parison of main material propertiesCompacted Graphite Iron(GGV 40)Secondary Aluminum(AlSi9Cu3)Magnesium (sand casting alloy)Y oung’s Modulus [kN/mm2]130 - 1607545T ensile Strength [N/mm2]300 - 500200 - 240160 - 180Bending Endurance [N/mm2]160 - 21070 - 9045 - 55Density [kg/dm3]7.1 – 7.42.751.75include thermal conductivity, mechanical and thermal endurance strength, creep resistance at high temperatures, damping coefficient, thermal expansion coefficient, corrosion resistance against cooling fluids,mineral oil and salt water, specific weight and last not least the castability.DESIGN CONCEPTS – The current standard for gasoline inline crankcases is a high-pressure die cast Al crankcase with cast in CI liners and thick main bearing shells of 4.5mm or inlays representing a modern lightweight concept with small potential for further weight reduction. The crankshaft bearings are implemented as a bedplate (Figure 10, left) or as a deep-skirt concept with cut-free main bearing walls and an aluminum ladder frame connecting the skirts (Figure 10, right). One remaining potential of about 0.5kg per cylinder can be found in replacing the CI liners by aluminum liners or by a thermal sprayed coating. Replacing the CI liners also benefits the heat dissipation from the combustion chambers by avoiding microscopic gaps between the CI liners and the surrounding material. Substituting the crankcase material with magnesium reduces the weight further.Figure 10.In-line gasoline crankcase conceptsThe common material for diesel inline crankcases with peak firing pressures of up to 16MPa is CI. Modern crankcases correspond to the deep-skirt concept mentioned above with SGI bearing caps and an aluminum ladder frame (Figure 11, left).This crankcase design concept is based on the tunnel-concept of the technological demonstration engine AVL LEADER [11. and 12. ]. The purpose of this concept is the acoustic decoupling of the main bearing walls excited by high combustion gas forces and the sound radiating outer crankcase structure. This design results in a relative flexible main bearing wall while the “tunnel”constitutes a structure with a high torsional and bending stiffness. A one-piece tunnel crankcase as cast for the first prototype of the AVL-LEADER engine is unacceptable for modern high volume production.Therefore, the shown production optimized crankcase requires a two-piece design [13. ], oil-pump and suction pipe can be integrated in the ladder frame.Figure 11.In-line diesel crankcase conceptsThe use of aluminum alloys for diesel and aluminum inline crankcases within one engine family offers the chance of a combined production. T oday aluminum is the standard material for gasoline crankcases. But the broad use for high-speed diesel engines is still prevented by questions regarding the achievable strength of the main bearing wall, the warping of cylinder liners and top deck and the al behavior.High potential to reduce the crankcase weight while ensuring the high structural stiffness has the compound concept. Investigations are currently conducted for a sand-cast aluminum/magnesium compound crankcase.The crankcase shown in Figure 11, right is designed as a bolt-through concept and optionally includes inlays in bedplate and/or crankcase to support the main bearing shells. Thread bosses integrated in these inlays are also capable to replace the bolt-through joint to avoid costly assembly procedures.Latest production gasoline V-engine crankcases are built, as are the their inline versions, of a high-pressure die cast aluminum crankcase and bedplate with only a small potential for further weight reductions by replacing the CI liners. Currently most diesel V-engine crankcases are made of CI, due to their high peak firing pressures. Bedplate designs with the separation plane through the crankshaft centerline and deep-skirt designs with SGI bearing caps have proven to be suitable concepts. Four bolts per main bearing and in case of single bearing caps additional horizontal bolts are essential to relieve the load on the cross guides of the bearing caps. Because of its superior material properties CGI is increasingly taken into consideration for diesel V-engine crankcases. A significant weight reduction relative to CI is possible especially in the high loaded areas around the main bearings. Different design solutions for diesel V-engine crankcases were compared using the finite element analysis.The chosen sand cast crankcase for this investigation is designed for a 90° V8-Engine (Figure 12, left). The finite element analysis considers four bolts per main bearing wall and a thick bearing shell of 4mm to reduce thermal expansion of the main bearings.Figure 12.V-engine crankcase designsFINITE ELEMENT ANALYSISExtensive finite element analyses were conducted for thehalf-cylinder 3D models of the inline and V-engine crankcases. The finite analysis model consists of thecrankcase and bedplate sections, the half of the bearing shells and of the cylinder head and main bearing bolts (Figure 13). Special attention was given to the critical area around the main bearing wall to calculate the endurable peak firing pressures.The finite element models of the different variants were loaded with static main bearing bolt forces calculated for different peak firing pressures and with dynamic loads taking different engine temperatures into account. The peak firing pressure limits listed below resulted from the calculated safety factors and the main bearing deformations under static and dynamic load. The different variants analyzed in this investigation were necessary to take different lightweight materials –secondary aluminum (AlSi9Cu3), warm hardening aluminum (AlSi10Mg wa), a sand cast magnesium alloy –and compound versions with SGI and CGI inlays into consideration. Figure 14 summarizes the results.Previous calculations resulted in a limit of 13.5MPa for the in-line high-pressure die-cast crankcases of a production diesel and gasoline engine family. This bedplate design was analyzed with reinforcing inlays.Figure 14.Peak firing pressure limits (cylinder spacing/bore = 1.12)The investigations of the inline crankcase (shown in Figure 11, right) yielded a peak firing pressure limit of 11.5MPa when using the sand-cast magnesium alloy without reinforcement. The secondary aluminum (AlSi9Cu3) reached its limit at 13.0MPa and peak firing pressures of up to 14.5MPa require the warm hardening aluminum alloy (AlSi10Mg wa) if no inlays are used. CGI or SGI inlays embedded in the aluminum or magnesium alloy base structure will allow peak firing pressures of 15MPa or more to be achieved.The design of V-engine crankcases for aluminum and magnesium alloys is, because of V-engine design features, more demanding than for inline crankcases.Each main bearing wall has to withstand the load of two cylinders instead of one, the necessary offset of the two cylinder banks weakens the wall structure and bolt through solutions with a straight force transmission (cylinder head – main bearing cap) are not possible.These constraints reduce the expectable peak firing pressure limits compared to their inline counterpart.Figure 13. Finite element modelsDue to their principal use in upper class vehicles, V-engines normally allow slightly higher costs for their components. The cast-in CGI or SGI skeleton frame is suitable to increase the peak firing pressure limit to 14MPa and above (Figure 12, right). The offset of cylinder-head bolts and main bearing wall strongly encourages the use of a complex frame instead of separate inlays for each main bearing wall. An additional reduction in the crankcase weight of about 0.5kg/cylinder is feasible if sprayed multi-component liners, aluminum liners or a thermal coating are used instead of the skeleton frame integrated liners.SUMMARY/CONCLUSIONSThe potential of ferrous crankcases even with thin-wall technologies is limited in comparison with lightweight materials because of the achievable minimum wall thickness. Aluminum alloys offer, in addition to their low material density, the possibility of a combined production of gasoline and diesel engines versions within one engine family. The critical aspects of the use of lightweight materials for modern crankcases are the achievable strength of the main bearing wall especially for high-speed diesel engines, the warping of cylinder liners and top deck and the acoustic behavior of lightweight crankcases.The application of lightweight materials for V-engine crankcases is restricted in terms of the achievable strength. If no reinforcing measures are implemented, the finite element analysis results suggest peak firing pressure limits of 14.5MPa for in-line and of 14.0Mpa for V-engine crankcases. Additional reinforcing inlays (of SGI or CGI) in the main bearing wall are essential to withstand the high peak firing pressures (15.0MPa and more) of modern high-speed diesel engines. Complex cast-in skeleton frames are suitable only for V-engine crankcases where the primary use in upper class vehicles allows slightly higher component costs. The skeleton frame is best able to compensate for the cylinder bank offset and to carry the load of two cylinders per main bearing wall. Optionally the cylinder liners can be an integrated part of the skeleton frame.The lightest material suitable for crankcases, magnesium, constitutes a design challenge especially for high-speed diesel engines. Research programs continue to work on design solutions for magnesium crankcases to exploit its potential.The development of lightweight crankcases is not a merely a question of the selected material, but of the overall concept and design of an engine. The lightweight concepts presented in this paper are increasingly being introduced to volume production and underline the strategy to commit to lightweight design of crankcases especially for modern high-speed diesel engines.REFERENCES1.R. Glanz, P. Wünsche, “Vier Ventile für den PKWDieselmotor mit direkter Einspritzung (Passenger car diesel engines with four-valve technology and direct injection)”, Vortrag im Haus der T echnik in Essen, 24th February 19942.R. Porro, “Magnesium in car design: cost vs. weightsaving”, Automotive Engineering International, August 1998, pp. 533.R. Arndt, K. Kusenbauch, R. Rösch, M. Stenzel, “DasAluminium-Kurbelgehäuse der Audi-Vierzylinder mit 1,6 und 1,8l Hubraum (The aluminum crankcase of the Audi 1,6 and 1,8l four cylinder engine)”, MTZ, October 1997, pp. 6004.Austrian Registration of Design A T 002 105 U1 andA T 002 109 U15.R. Marquard, H. Sorger, M. McDonald, “Crank it up”,Engine T echnology International, June 1998, pp. 58 6.F. Anisits, K. Borgmann, H. Kratochwill, F.Steinparzer, “Der neue BMW Vierzylinder Dieselmotor (The new BMW four cylinder diesel engine)”, MTZ-Special BMW, 1998, pp. 1047.F. Anisits, K. Borgmann, H. Kratochwill, F.Steinparzer, “Der neue BMW Sechszylinder Dieselmotor (The new BMW six cylinder diesel engine)”, MTZ, November 1998, pp. 6988.H. Henkel, F. Winter, “Sechszylinder Dieseltriebwerkvon BMW (The BMW six cylinder diesel engine)”, MTZ, November 19989.H. Sorger, H. Hick, “ Future T rends for EngineDesign”, Sintercast Compacted Graphite Iron Proceedings, Bad Nauheim, November 199810.Austrian Registration of Design A T 002 544 U111.P. Wünsche, K. Wojik, “AVL-LEADER: Die neuePKW-Dieselgeneration konstruiert für niedrige Emissionen (AVL-LEADER: The new generation of passenger car diesel engines, designed for low emissions)”, 14th Internationales Wiener Motorensymposium, 199312.F. König, K. Wojik, “Der HSDI-Motor AVL-LEADER imFahrzeug (The HSDI engine AVL-LEADER in a passenger car)”, 16th Internationales Wiener Motorensymposium, 199513.F. Brandl, W. Schoeffmann, K. Isono, Y. Ohtani,“Noise Reduction of Diesel Engines by Structure Modifications of the Cylinder Block”, JSAE 9838462 14.R. Marquard, W. Schöffmann, F. Beste, …Leichtbau –eine neue Herausforderung für PKW-Hochleistungsdiesel-motoren“, 20th Internationale Wiener Motorensymposium, 6.-7. May 199915.F. Beste, W. Schöffmann, R. Marquard, …Modernengine design using lightweight materials“, 32nd ISA T A, 14.-18. June 1999。
汽车发动机舱热管理研究与优化
某车型发动机舱热管理研究与优化摘要:本文研究了某车型发动机舱流场对热敏零部件的影响,通过整车热平衡试验验证热敏零部件的性能,应用商用软件STAR CCM+软件模拟整车的流场,并针对试验中存在风险的零部件进行优化。
分析结果表明:发动机悬置处的温度最高可达到102℃,超过材料的耐热极限,由于发动机下护板阻隔了底盘底部气流,导致排气系统表面流过的气流较少。
通过对发动机舱下护板的优化,有效的提高零部件表面风速,降低了热敏零部件的风险,使其满足设计要求。
关键词: 热平衡试验;热敏零部件;发动机下护板;整车外流场Research and Optimization on Thermal Management of a New Vehicle Model Engine CompartmentAbstract:The influence of underhood flow field on thermo-sensitive parts are researched, verify the performance of thermo-sensitive parts by thermal balance test, simulate the whole vehicle flow field by the software STAR CCM+ and optimize the parts which have risk The analysis shows that, the highest temperature of engine mounting can reach 102 ℃ that has exceeds the temperature limit. As the underhood plate keep the airflow from the bottom of the chassis, which leading to less air flow on the surface of the exhaust system. Effectively improve the surface wind speed on parts by optimizing the underhood plate, reduce the risk of Thermo-sensitive parts, and satisfy the design requirements.Key words: Thermal balance test, Thermo-sensitive parts, Underhood plate, External flow field前言车辆在行驶时,发动机工作产生大量的热量,尤其是在爬坡这样的恶劣工况下,如果热量不能够及时排出,会严重影响汽车的性能[1]。
- 1、下载文档前请自行甄别文档内容的完整性,平台不提供额外的编辑、内容补充、找答案等附加服务。
- 2、"仅部分预览"的文档,不可在线预览部分如存在完整性等问题,可反馈申请退款(可完整预览的文档不适用该条件!)。
- 3、如文档侵犯您的权益,请联系客服反馈,我们会尽快为您处理(人工客服工作时间:9:00-18:30)。
Optimization of engine thermal management systemEngine thermal management is from the angle of the whole system, integrated control engine, turbocharger and exhaust, cooling system and engine cabin heat transfer etc., improve circulation efficiency, reducing heat load, change control engine components of high and low temperature limit, temperature distribution and regularity, improves the cooling capacity of the engine's colleagues, keep the engine in good power nature, economy and emission performance and reliability.Application of engine thermal management system technology, can effectively heat transfer system involved in the engine as a comprehensive system of consideration and get the accurate boundary parameters of the engine each fluid system, precise control of temperature and heat flux of each system, can guarantee the safe and efficient operation of the key components and system control. And the optimization of the heat transfer process, reduce the size and power consumption of cooling system, reasonable utilization of heat energy, reduce waste emissions, improve energy efficiency, reduce environmental pollution. There is significant difference between engine thermal management and traditional engine cooling system. From engine cooling to engine thermal management is not only a technological progress, but also a breakthrough in management and design ideas. Engine thermal management technology has become an important measure of engine energy saving, emission reduction, power performance, reliability and engine life.The cooling fan mechanical drive cooling system in the traditional fan from the engine crankshaft through a belt drive, the cooling air depends on engine speed and engine speed is proportional to, rather than the actual engine operation cooling capacity, unable to accurately control the air flow through the radiator, thereby it is difficult to make the engine work in the best temperature, resulting in emissions is too high, the fuel economy and engine performance deterioration. In addition to the outside of the traditional cooling fan cooling sensitivity adjustment is not high, the power loss is also large, serious power consumption, such as power consumption of the fan can reach the total output power of the engine 10%. In order tosolve the problems appeared in the self controlled electric fan, the electric fan speed according to the coolant temperature and air conditioning cycle parameters to adjust, through the sensor and computer chip according to the engine temperature control operation, to provide the best cooling medium flow and fan speed to adjust cooling capacity, reduce heat loss, the engine at low temperature when the power loss, and excessive wear, inhibit the engine overheating, reducing noise and fuel consumption. The cooling fan of transforming the traditional control mode for intelligent control, the cooling capacity of cooling fan with engine cooling and automatic precise adjustment, improved engine preheating velocity, water temperature too hot or too cold to prevent, to maintain the best working temperature, but also avoid wasting a lot of energy, which reduce the fan 90% power consumption, save fuel 10%. In addition, in order to improve the efficiency of cooling fan, replace the arc straight blade cooling fan with a plastic fan wing; with wing section plastic and streamlined hood, the formation of streamline flow in the fan airflow entrance, can improve the efficiency of hydraulic fan. Finally, the efficiency of electric fan is 85%.The traditional mechanical driven cooling water pump is driven by V or gear, and the running speed is proportional to the engine speed. Many studies show that the traditional water pump in water only 5% of the time is right, not the precise control of the flow through the radiator cooling medium, so it is hard to make the engine work at the optimum temperature, fuel economy and engine performance. The electronic control pump driven by the motor, the flow can be independently controlled. The electric pump without crankshaft drive, the installation location is flexible, can optimize the water pump characteristic design, at the same time because there is no gear or belt wheel drives, reduces cycle lateral V belt and gear of the pump bearing load capacity, reduce the loss of driving. According to the requirements of engine cooling, not only the speed of cooling water is supplied by the electronic control pump, but also the cooling state of the part load and the high speed condition is avoided, and the unnecessary power consumption is reduced. Guo Xinmin on the domestic loader cooling system control device is studied, in order to achieve automatic adjustment of cooling water pump speed regulating overflow flow proportional relief valve according to the temperature of cooling water by using scm. The results show that, when thetemperature is low, the control can reduce the preheating time by 50%, increase the heating speed, and save the fuel in the preheating stage by 43%. In 1999 Valeo proposed a new electronic tuning system in the engine to improve engine cooling performance. It realizes the separation of the pump and cylinder, flow and ventilation device of the pump to adjust and control the engine ECU, convenient pump installation, and away from the cylinder heat source, the pump can be made of plastic, which can reduce the cost and reduce the weight of the pump, the pump speed changes with temperature to achieve the change, further reducing the heat loss and mechanical loss, reduce pollution and fuel consumption. Stepanoff has put forward the design theory of high efficiency centrifugal pump and axial flow pump, which can improve the efficiency of engine cooling water pump to 75% by changing the shape of impeller and improving the surface finish. Japan NISSAN, this theory developed a water pump based on the structure by reducing the size of pump, the company also improved by increasing the number of blades, blade curve design, the maximum pump efficiency reached 75%.The thermostat thermostat function is automatically adjusted according to the cooling water into the radiator temperature of the water, change the water cycle range, to adjust cooling capacity of the cooling system, ensure that the engine work in the suitable temperature range. The thermostat is a key component to control the cooling flow path of the engine cooling system, but at present most of the thermostat using paraffin as temperature sensing medium, the existence of "delay" and "hysteresis", unable to meet the precise control of the cooling system, the engine fuel consumption, service life shorten. In order to further improve the cooling efficiency of the engine, electronic thermostat came into being. The control system of the temperature controller is composed of a sensor, a motor and a control module, which can control the coolant flow rate according to the coolant temperature or the temperature of the engine parts. When the engine is running, the control unit according to the calculated values obtained by the sensor signal conditioning unit load voltage to the temperature, the dissolution rate by controlling the load voltage to control the size of paraffin, then effectively quickly and accurately control the size of the circular opening, so that all parts of the engine is always in the optimal temperature range, in order to improve thecombustion efficiency of fuel oil increase the air intake quantity, reduce wear and prolong the service life of the engine. In 1997, the United States University of Oakland X-ZHOU and B.CAHLON et al introduced hysteretic delay differential equations to describe the dynamic characteristics of the thermostat in the engine cooling system in the work process, and gives the numerical solution of the model algorithm. 2002 ~ 2006, the United States Clemson University John R.Wagner et al. Carried out the engine cooling system intelligent thermostat. They use the servo motor to drive the gear and screw, and then screw the rotation of the movement into the piston (spool) of the telescopic movement, so as to achieve the size of the cooling fluid circulation channel switch. In 2009, T.Mitchell et al. Compared the effects of 4 different types of thermostat arrangement on the performance of the engine cooling system under the condition of warm air. They are in the use of paraffin thermostat, electric two way valve, electric three-way valve and do not install thermostat, respectively, in the 4 cases of engine warm-up test. Their study suggests that the use of electric three-way valve in this form, the engine warm-up time and fuel economy performance of the best. In 2004, Tsinghua University, Luo Jianxi, Zhang Yangjun et al. Analyzes the influence of thermostat on dynamic performance of the engine they pointed out: the effect of interaction of delayed nonlinear dynamic characteristics and the system of the thermostat, causing the engine dynamic characteristics of complex thermal system. When the temperature of the thermostat is short, the temperature deviation is small, and the temperature of the thermostat is weak, the inlet temperature of the engine is small, the time needed for stability is short, and the adjustment effect is good.The cooling water cooling fluid flow, pressure and reasonable flow field distribution have a direct impact on the cooling effect of the engine. The engine passes the water jacket to the cooling system, and the reasonable design of the water jacket is the key factor to the cooling effect of the engine. The water jacket structure reasonable first to ensure the uniformity of water jacket wall thickness, wall due to heat in some areas caused by the unreasonable distribution of the water jacket wall thickness of the engine stress occurred the situation; secondly, to ensure the rationality of the water jacket cavity, the cooling liquid can be normal flow in the water jacket, no flow dead, caused by overheating in some parts of theengine; in addition to ensure water supply to all parts of the engine should be reasonable, each cylinder of the engine combustion chamber wall temperature as possible. Improved engine cooling water jacket structure for flow field distribution right, can improve engine thermal load and thermal stress, prevent engine damage, improve the engine service life of the parts, engine power and fuel economy. Couetouse H. et al. Proposed the design of a split flow system in 1984, that is, the steam cylinder head and the cylinder body have different cooling loops, which are suitable for the cylinder head and cylinder body with different temperatures. This is due to the lower cylinder head temperature is conducive to air intake and improve emissions, while the higher cylinder temperature is conducive to reducing friction losses, improve fuel economy. The advantage of the split cooling water jacket system is to make the engine work at the best temperature setting point, and achieve the high cooling efficiency. The experimental results show that the flow of cooling fluid temperature of the cylinder head is reduced to 50 DEG C, and the flow of cooling fluid temperature of the cylinder body is 80 DEG C, the compression ratio increased from 9 to 12, can realize the part load condition, saving 7%, saving 5% idle full load power output increased by 10% of the target. Clough M.J. put forward the concept of "precision cooling" as early as 1992, that is, to minimize the cooling to achieve the best temperature distribution. The key is to determine the exact design of cooling system cooling water jacket size, selection of cooling water pump, cooling capacity, ensure the system can meet the engine at low speed and high load of key areas of the working temperature of the demand. The results show that the coolant flow rate can be decreased by 40% in the whole working speed range. The potential advantage of precision cooling is to increase the speed of the machine, reduce the thermal stress and heat loss. The friction coefficient and the power consumption of the cooling water pump can be reduced, and the average effective pressure and the antiknock property can be improved. Clough of a four valve gasoline engine cylinder body and a cylinder cover for transformation, to achieve precise cooling water jacket, the volume is reduced by 64%, the pump power consumption decreased 54%, the warm-up time is reduced by 18%. Whether it is an accurate cooling system or a shunt cooling system, it is necessary to improve the engine cooling water jacket to optimize the flow of coolant. From the point of view of design and application, thecombination of split cooling and precise cooling has a good prospect, which is favorable to the formation of an ideal engine temperature distribution, which meets the requirements of the engine to the future cooling system.At present, the material of thermal management system is relatively single, and the radiator material is usually copper, aluminum and aluminum alloy. The design method of the traditional radiator has reached the limit, so it is urgent to develop a new and efficient cooling concept to improve the cooling performance.Nanofluid nanofluid is a kind of engineering heat transfer fluid, which is formed by dispersing nano metal particles in the traditional heat transfer fluid (water, ethylene glycol mixture and oil). Argonne National Laboratory (Argonne) is developing a nano particle to improve the thermal conductivity of engine coolant and oil. The test results show that the thermal conductivity can be increased by 40%. Leong using nano fluid as the research of engine cooling fluid, the total heat transfer coefficient and the heat transfer rate than base fluid for ethylene glycol has greatly improved, Reynolds number in the air side and the radiator coolant side were 6000 and 5000, copper nanoparticles 2% to enable the heat transfer is enhanced by 3.8%, the estimation of air windward area reduced by 18.7% air radiator. At the same time, the application of nanofluids in the engine cooling system can reduce the size and weight of the cooling system of the heavy-duty vehicle by 10%, so the combustion efficiency of the engine will be increased by 5%. The use of nanofluids can also use a higher temperature of the cooling liquid to reduce heat loss. The application of the high temperature radiator reduces the size of the radiator by 30%, thereby reducing the flow resistance of the air, reducing the flow loss of the cooling fluid and the loss of the driving fan, and saving the fuel consumption by about 10%. Figure 4 shows the thermal conductivity ratios of different nanofluids (metal particles and oxide particles) k/k. (K. The relationship between the thermal conductivity of ethylene glycol and the volume fraction of nanoparticles.Aokeliqi National Laboratory (ORNL-0ak Ridge National graphite foam Laboratory) developed a unique graphite foam, can greatly improve the heat transfer coefficient. The graphite foam density is 0.2 ~ 0.6g/cm fand thermal conductivity is 40-187/m.K. Because the foam honeycomb mesh structure, large contact surface (>4 m /g), radiator made of graphitefoam is the overall heat transfer coefficient will increase more than 10 times than the traditional radiator.Klett and so on with graphite foam made of a 22.9cm x 17.78cm 15.27cm heat exchanger (radiator), installed in the 588kW V8 racing engine, replacing the original 68.6cm x 48.3cm x 7.6cm radiator. Under the condition of the speed of 290km/h, the water temperature is 99.4 degrees Celsius, the cooling water flow rate is only 57.5L/min, the fan air flow is only the original 2.3%. The overall heat transfer coefficient is 10 times higher than that of the traditional radiator. Therefore, the cross-sectional area of 48CM x 69cm car radiator, with the same amount of heat dissipation, the size can be reduced to 20cm x 20cm. This reduces the size, quality, and cost of the radiator, thereby increasing fuel efficiency.发动机热管理系统优化发动机热管理是从系统整体角度,集成控制发动机的燃烧、增压与进排气、冷却系统和发动机舱等的传热,提高循环效率,减低热负荷,控制发动机部件高低温极限、温度分布及其规律变化,在提高发动机的冷却能力的同事,保持发动机良好的动力性、经济性、排放性能和可靠性。