基于PLC的锅炉实时监控系统的设计
基于PLC和IFIX的小区供热锅炉控制系统

基 于 P C 和 I I 的 小 区供 热锅 炉 控 制 系统 L X F
赵 钢 , 徐 杰 , 红 苗 刘 2
( .天 津 市 复 杂控 制 理 论 与 应用 重 点实 验 室 , 津 理 5 大 学 , 津 3 0 8 ; 1 天 - _ 天 0 3 4 2. 天津 光 彩 自控 工 程 有 限公 司 , 津 3 0 8 ) 天 0 3 4
c nr l y tm o a i b ie b I X a Hol S s o to s se f he tng ol r y FI nd ly y PLC f LK ,nd o a OPC o mu c to p oo o wa a o e t c m niain r tc l s d ptd o
中图 分 类 号 : TP1 3 文 献 标 志 码 : B
Bo l r Co r l Sy t m o l g a i g Ba e n PLC a d I X i nt o s e f r Vil e He tn s d o e a n FI
Z HAO Ga g , i L U Ho gmio n XU Je , I n — a
(.i j e aoa r o o t l h o n p l aosi o pia dS s m,i j n esy o T enl・ 1 a i K y Lbrt yfrC nr er ad A pi t n C m l t yt Ta i U i r t f eh o T nn o oT y ci n ce e nn v i o
了 上 、 位 机 供 热 锅 炉 监 控 系 统 ; 、 位 机 之 间 数 据 交 换 借 助 于 OP 下 上 下 C通 信 协 议 实 现 借 助
基于PLC的远程监控与控制系统设计

基于PLC的远程监控与控制系统设计引言现代工业领域中,远程监控与控制系统的设计与实施举足轻重。
随着技术的不断进步,工业自动化程度逐渐提高,企业对于能够远程监控与控制生产过程的系统需求也越来越迫切。
基于可编程逻辑控制器(PLC)的远程监控与控制系统成为工业界的主流选择之一。
本文旨在探讨基于PLC的远程监控与控制系统的设计原理、特点以及实现方法。
PLC的基本原理与特点PLC是一种特定用途的数字计算机,其核心是CPU、存储器、输入/输出(I/O)模块以及通信模块等。
PLC的工作原理为:根据预先设定的控制程序,通过输入模块采集外部信号,经过CPU处理后,再通过输出模块控制外部设备。
PLC具有以下特点:1. 高可靠性:PLC采用可靠的硬件结构和操作系统,能够适应各种恶劣工业环境,并且具备故障自诊断和容错能力。
2. 可扩展性:用户可以根据需要,通过添加不同类型的I/O模块或者通信模块,灵活扩展PLC的功能。
3. 强大的运算能力:PLC的处理速度快,具备多通道输入输出功能,能够处理复杂的控制逻辑。
远程监控与控制系统设计的目标与要求在工业生产中,远程监控与控制系统的设计目标是提高生产效率、减少人为错误、降低成本并确保安全。
因此,设计远程监控与控制系统需要满足以下要求:1. 实时性:远程监控与控制系统需要能够及时响应远程操作指令,并且将实时数据反馈给控制中心。
2. 稳定性:远程监控与控制系统需要稳定运行,不易受到外界干扰,保证生产过程的连续性和稳定性。
3. 安全性:远程监控与控制系统需要具备安全保护措施,防止非法访问、数据泄露以及黑客攻击。
PLC与远程监控与控制系统的结合基于PLC的远程监控与控制系统的设计是将传统的PLC系统与现代网络技术相结合,实现远程操作与监控。
其基本架构如下图所示:[插入一张图,展示基于PLC的远程监控与控制系统的基本架构]远程监控与控制系统的设计步骤设计基于PLC的远程监控与控制系统一般包括以下步骤:1. 系统需求分析:根据企业实际需求,确定远程监控与控制系统的功能和性能要求。
基于PLC的锅炉燃烧控制系统设计_毕业设计论文正文 精品
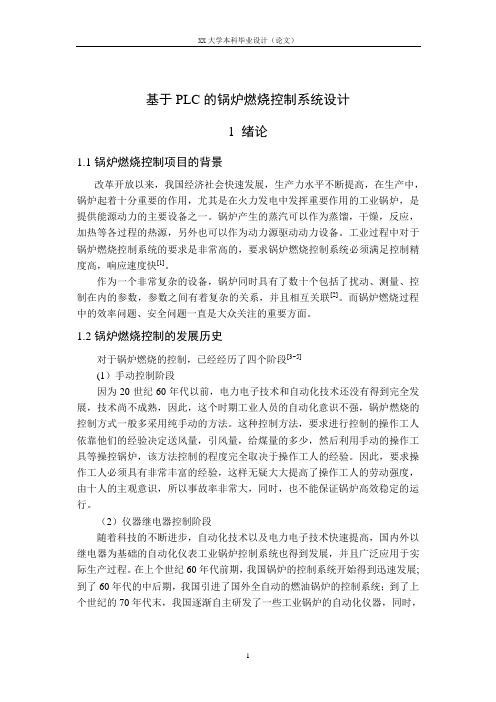
基于PLC的锅炉燃烧控制系统设计1 绪论1.1锅炉燃烧控制项目的背景改革开放以来,我国经济社会快速发展,生产力水平不断提高,在生产中,锅炉起着十分重要的作用,尤其是在火力发电中发挥重要作用的工业锅炉,是提供能源动力的主要设备之一。
锅炉产生的蒸汽可以作为蒸馏,干燥,反应,加热等各过程的热源,另外也可以作为动力源驱动动力设备。
工业过程中对于锅炉燃烧控制系统的要求是非常高的,要求锅炉燃烧控制系统必须满足控制精度高,响应速度快[1]。
作为一个非常复杂的设备,锅炉同时具有了数十个包括了扰动、测量、控制在内的参数,参数之间有着复杂的关系,并且相互关联[2]。
而锅炉燃烧过程中的效率问题、安全问题一直是大众关注的重要方面。
1.2锅炉燃烧控制的发展历史对于锅炉燃烧的控制,已经经历了四个阶段[3~5](1)手动控制阶段因为20世纪60年代以前,电力电子技术和自动化技术还没有得到完全发展,技术尚不成熟,因此,这个时期工业人员的自动化意识不强,锅炉燃烧的控制方式一般多采用纯手动的方法。
这种控制方法,要求进行控制的操作工人依靠他们的经验决定送风量,引风量,给煤量的多少,然后利用手动的操作工具等操控锅炉,该方法控制的程度完全取决于操作工人的经验。
因此,要求操作工人必须具有非常丰富的经验,这样无疑大大提高了操作工人的劳动强度,由十人的主观意识,所以事故率非常大,同时,也不能保证锅炉高效稳定的运行。
(2)仪器继电器控制阶段随着科技的不断进步,自动化技术以及电力电子技术快速提高,国内外以继电器为基础的自动化仪表工业锅炉控制系统也得到发展,并且广泛应用于实际生产过程。
在上个世纪60年代前期,我国锅炉的控制系统开始得到迅速发展;到了60年代的中后期,我国引进了国外全自动的燃油锅炉的控制系统;到了上个世纪的70年代末,我国逐渐自主研发了一些工业锅炉的自动化仪器,同时,在工业锅炉的控制系统方面也在逐步推广应用自动化技术。
在仪表继电器控制阶段,锅炉的热效率得到了提高,并且大幅度的降低了锅炉的事故率。
基于PLC的锅炉温度控制系统毕业设计
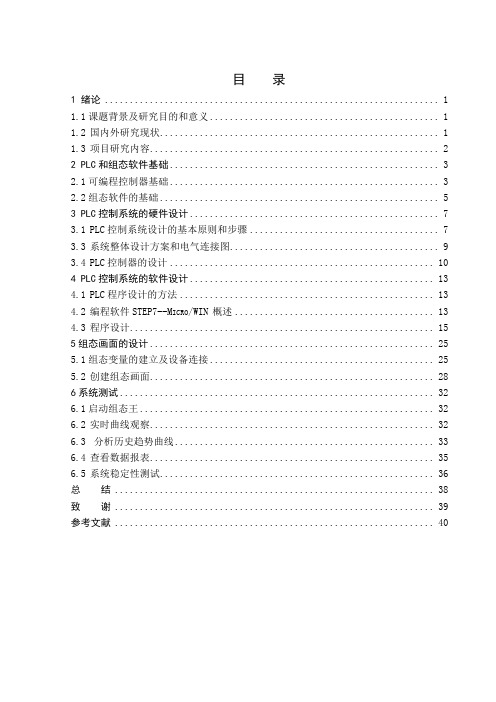
目录1 绪论 (1)1.1课题背景及研究目的和意义 (1)1.2国内外研究现状 (1)1.3项目研究内容 (2)2 PLC和组态软件基础 (3)2.1可编程控制器基础 (3)2.2组态软件的基础 (5)3 PLC控制系统的硬件设计 (7)3.1PLC控制系统设计的基本原则和步骤 (7)3.3系统整体设计方案和电气连接图 (9)3.4PLC控制器的设计 (10)4 PLC控制系统的软件设计 (13)4.1PLC程序设计的方法 (13)4.2编程软件STEP7--M ICRO/WIN概述 (13)4.3程序设计 (15)5组态画面的设计 (25)5.1组态变量的建立及设备连接 (25)5.2创建组态画面 (28)6系统测试 (32)6.1启动组态王 (32)6.2实时曲线观察 (32)6.3分析历史趋势曲线 (33)6.4查看数据报表 (35)6.5系统稳定性测试 (36)总结 (38)致谢 (39)参考文献 (40)摘要从上世纪80年代至90年代中期,PLC得到了快速的发展,在这时期,PLC在处理模拟量能力、数字运算能力、人机接口能力和网络能力得到大幅度提高,PLC逐渐进入过程控制领域,在某些应用上取代了在过程控制领域处于统治地位的DCS系统。
PLC具有通用性强、使用方便、适应面广、可靠性高、抗干扰能力强、编程简单等特点。
PLC在工业自动化控制特别是顺序控制中的地位,在可预见的将来,是无法取代的。
本文介绍了以锅炉为被控对象,以锅炉出口水温为主被控参数,以炉膛内水温为副被控参数,以加热炉电阻丝电压为控制参数,以PLC为控制器,构成锅炉温度串级控制系统;采用PID算法,运用PLC梯形图编程语言进行编程,实现锅炉温度的自动控制。
电热锅炉的应用领域相当广泛,在相当多的领域里,电热锅炉的性能优劣决定了产品的质量好坏。
目前电热锅炉的控制系统大都采用以微处理器为核心的计算机控制技术,既提高设备的自动化程度又提高设备的控制精度。
基于PLC的锅炉供暖监控系统设计

4、监控界面设计技术
4、监控界面设计技术
在上位机监控界面方面,我们采用了组态软件来设计监控界面。组态软件是 一种广泛使用的工业自动化监控软件开发工具,它支持多种图形元素和控件,可 以方便地实现实时数据展示、报警提示、历史数据查询等功能。我们根据锅炉的 实际运行情况,设计了相应的监控界面,并编写了相关的脚本代码,以实现对锅 炉运行数据的实时展示和报警提示等功能。
2、控制技术
2、控制技术
在控制方面,我们采用了PID(比例-积分-微分)控制算法来实现对锅炉的燃 烧和给水控制。PID控制是一种经典的连续控制系统,它通过比较设定值与实际 值之间的误差来计算控制量,实现对被控对象的精确控制。我们根据锅炉的实际 情况,对PID控制算法进行了相应的调整和优化,以实现对锅炉的燃烧和给水系 统的有效控制。
二、关键技术
1、数据采集技术
1、数据采集技术
在数据采集方面,我们采用了高精度传感器和PLC模拟量输入模块,实现了对 锅炉运行参数的实时监测。传感器包括温度传感器、压力传感器和水位传感器等, 它们将采集到的信号通过变送器转换为标准的电信号,再通过PLC模拟量输入模 块输入到PLC中进行数据处理。
一、系统需求与设计
一、系统需求与设计
锅炉供暖系统的主要任务是维持锅炉中水的温度在设定的范围内,同时也要 确保供暖设备的正常运行。因此,系统的需求主要包括:
一、系统需求与设计
1、实时监测锅炉的水温、压力等参数; 2、通过调节锅炉的燃烧器输出,控制水温; 3、保障供暖设备的稳定运行;
一、系统需求与设计
三、应用效果
3、提高了管理效率。通过远程监控锅炉的运行状态,可以在上位机上实现锅 炉的集中管理和监控,从而提高了管理效率。
谢谢观看
基于plc的锅炉控制系统的设计方案
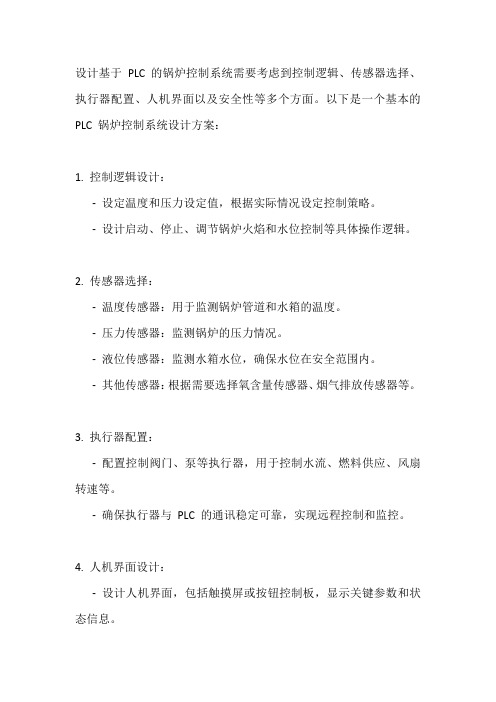
设计基于PLC 的锅炉控制系统需要考虑到控制逻辑、传感器选择、执行器配置、人机界面以及安全性等多个方面。
以下是一个基本的PLC 锅炉控制系统设计方案:1. 控制逻辑设计:-设定温度和压力设定值,根据实际情况设定控制策略。
-设计启动、停止、调节锅炉火焰和水位控制等具体操作逻辑。
2. 传感器选择:-温度传感器:用于监测锅炉管道和水箱的温度。
-压力传感器:监测锅炉的压力情况。
-液位传感器:监测水箱水位,确保水位在安全范围内。
-其他传感器:根据需要选择氧含量传感器、烟气排放传感器等。
3. 执行器配置:-配置控制阀门、泵等执行器,用于控制水流、燃料供应、风扇转速等。
-确保执行器与PLC 的通讯稳定可靠,实现远程控制和监控。
4. 人机界面设计:-设计人机界面,包括触摸屏或按钮控制板,显示关键参数和状态信息。
-提供操作界面,方便操作员设定参数、监控运行状态和进行故障诊断。
5. 安全性设计:-设计安全保护系统,包括过压保护、过温保护、水位保护等,确保锅炉运行安全。
-设置报警系统,当参数超出设定范围时及时警示操作员。
6. 通讯接口:-考虑与其他系统的通讯接口,如SCADA 系统、远程监控系统等,实现数据传输和远程控制。
7. 程序设计:-使用PLC 编程软件编写程序,包括控制逻辑、报警逻辑、自诊断等功能。
-测试程序逻辑,确保系统稳定可靠,符合设计要求。
以上是基于PLC 的锅炉控制系统设计方案的基本步骤,具体设计还需根据实际情况和需求进行调整和优化。
在设计过程中,还需遵循相关标准和规范,确保系统安全可靠、运行稳定。
基于PLC的锅炉供热控制系统的设计

基于PLC的锅炉供热控制系统的设计一、本文概述随着科技的不断发展,可编程逻辑控制器(PLC)在工业自动化领域的应用日益广泛。
作为一种高效、可靠的工业控制设备,PLC以其强大的编程能力和灵活的扩展性,成为现代工业控制系统的重要组成部分。
本文旨在探讨基于PLC的锅炉供热控制系统的设计,通过对锅炉供热系统的分析,结合PLC控制技术,实现对供热系统的智能化、自动化控制,提高供热效率,降低能耗,为工业生产和居民生活提供稳定、可靠的热源。
文章首先介绍了锅炉供热系统的基本构成和工作原理,分析了传统供热系统存在的问题和不足。
然后,详细阐述了PLC控制系统的基本原理和核心功能,包括输入/输出模块、中央处理单元、编程软件等。
在此基础上,文章提出了基于PLC的锅炉供热控制系统的总体设计方案,包括系统硬件选型、软件编程、系统调试等方面。
通过本文的研究,期望能够实现对锅炉供热控制系统的优化设计,提高供热系统的控制精度和稳定性,降低运行成本,促进节能减排,为工业生产和居民生活提供更加安全、高效的供热服务。
也为相关领域的研究人员和技术人员提供有价值的参考和借鉴。
二、锅炉供热系统基础知识锅炉供热系统是一种广泛应用的热能供应系统,其主要任务是将水或其他介质加热到一定的温度,然后通过管道系统输送到各个用户端,满足各种热需求,如工业生产、居民供暖等。
该系统主要由锅炉本体、燃烧器、热交换器、控制系统和辅助设备等几部分构成。
锅炉本体是供热系统的核心设备,负责将水或其他介质加热到预定温度。
其根据燃料类型可分为燃煤锅炉、燃油锅炉、燃气锅炉、电锅炉等。
锅炉的性能参数主要包括蒸发量、蒸汽压力、蒸汽温度等。
燃烧器是锅炉的重要组成部分,负责燃料的燃烧过程。
燃烧器的性能直接影响到锅炉的热效率和污染物排放。
燃烧器需要稳定、高效、低污染,同时要适应不同的燃料类型和负荷变化。
热交换器是锅炉供热系统中的关键设备,负责将锅炉产生的热能传递给水或其他介质。
热交换器的设计应保证高效、稳定、安全,同时要考虑到热能的充分利用和防止结垢、腐蚀等问题。
毕业设计-基于PLC控制的电热锅炉

电热锅炉是把电能转化为热能,把水加热至有压力的热水或蒸汽(饱和蒸汽)的一种电力设备。
电热锅炉无需炉膛、烟道和烟囱,同样无需储存燃料的空间,很大程度上减少了常规燃煤锅炉使用产生的污染。
电热锅炉具有低污染,低噪声,体积小,安装使用便利,自动化程度高,安全可靠,热效率高达98%以上等特点,电热属于一种绿色环保产品。
一些国家在20世纪70年代后期到80年代初期就已经开始研究设计电热锅炉。
中国在80年代中期,开始设计电热锅炉产品,到了90年代中期,许多公司将电热锅炉用来采暖、中央空调和热水供应。
1 绪论1.1电热锅炉的介绍在当今社会,电加热锅炉的使用领域已经越来越广泛了。
它的经济性,安全性和较高的自动化程度越来越受到人们的认同。
可是电加热锅炉的性能优劣充分的反映了电热锅炉的质量好坏。
电加热锅炉已逐渐进入人民的生活,成为洗浴,供热等场所的首选设备。
目前电热锅炉的控制系统多采用以微处理器为核心的PLC控制技术,既提高产品的自动化程度又增加了锅炉的控制精度。
现在使用的大部分电加热锅炉控制系统的设计还不完善,因此需要设计一种全新的、自动化程度较高的电加热锅炉控制系统来代替和完善以前的控制系统。
现在工业生产所使用的控制器大多数是用继电器、接触器为主的控制装置。
使用继电器电路组成的控制系统出现的误操作较多,其可靠性不好。
而该设计所使用的是以PLC来取代原有的控制系统。
控制系统的要求:补水泵和循环泵交替使用,互为备用;缺相报警,水泵停止运行;循环泵主/备用泵能手动选择。
1.2 电热锅炉的分类电热锅炉就是以电为能量来加热的锅炉,即使用清洁的电能转化为热能,从而把常温水加热为高温度热水或具有压力蒸汽的热能电气设备。
电热锅炉分为两大类:LDR(WDR)电热蒸汽锅炉和CLDZ(CWDZ)电热热水锅炉及KS-D电开水锅炉。
其中电开水锅炉又分为KS-D电开水锅炉和XKS-D电蓄热开水锅炉。
电开水锅炉配置微电脑控制器、陶瓷电热管,采用电磁阀作为补水装置配合水位电极、感温探头全自动工作,连续大量供应饮用开水,广泛适用于政府机关、企业、工厂、医院、学校、宾馆、酒店等企事业单位使用。
- 1、下载文档前请自行甄别文档内容的完整性,平台不提供额外的编辑、内容补充、找答案等附加服务。
- 2、"仅部分预览"的文档,不可在线预览部分如存在完整性等问题,可反馈申请退款(可完整预览的文档不适用该条件!)。
- 3、如文档侵犯您的权益,请联系客服反馈,我们会尽快为您处理(人工客服工作时间:9:00-18:30)。
基于PLC的锅炉实时监控系统的设计
摘要:本文主要从锅炉技术的现状及其未来的发展前景、锅炉系统控制方案设计、锅炉控制系统设计三个方面对基于PLC锅炉实施监控系统设计进行了详细的分析。
关键字:锅炉;监控;现状;
前言:因为PLC自动化控制系统本身的优越性,故其在锅炉的实时监控系统的设计中有较强的使用价值。
一、锅炉技术的现状及其未来的发展前景
(一)锅炉技术的现状
传统的工业锅炉大多使用的是继电器--接触器控制,给水、鼓风、引风等基本的控制部分均为现场手动控制,其控制系统通常是由输入电路、控制电路、输出电路与生产现场这四分部分组成。
在以往传统的锅炉生产环节中,老式控制系统运用很普遍,但是随着科技的进步,企业生产量得到扩大,这种控制调节方式在面对逐渐严格与多样化的生产工艺要求时,已经无法起到相应的精确控制,越来越显得落后。
(二)锅炉的发展前景
从经济性上来讲,要求锅炉的能耗小,维护成本低,自动化控制程度高。
从锅炉的技术上讲,整个全自动控制系统要使用高效率、高质量的控制组件来保证,依靠微机技术智能化控制,优化每个凋节量,提高节能效果。
从安全性方面上讲,锅炉控制系统的各个部分能够单独进行控制,但又相互联系,遇到紧急故障时可以单独停止来保证现场的操作人员的安全。
从环保性方面上讲,通过计算机的调节,可以在一定程度上降低锅炉与其他系统设备对环境气候造成的污染,特别是对大气与水质。
二、锅炉系统控制方案设计
(一)锅炉结构介绍
锅炉是种生产蒸汽或热水的换热设备。
在常见的锅炉设备中,链条炉排锅炉的结构紧凑、系统成熟、性能稳定等特点,使得它被运用的尤为广泛。
(二)锅炉水位控制方案设计
1、锅炉汽包水位控制要求
汽包水位存锅炉的运行过程中起着十分重要的作用,决定着锅炉的工作质量。
汽包水位作为锅炉安全运行的前提条件,如果太低则会破坏锅炉的水循环,引发水冷壁管破裂和锅体干烧等现象,如果汽包受此影响损坏,还会引发爆炸;水位过高会使得汽水混合物元法正常分离,产生“带水”蒸汽,引起过热管壁结垢,从而会使相关负载设备的传动叶片损坏。
2、锅炉汽包水位控制方案设计
三级冲量控制系统与单冲量、双冲量控制系统有明显的优越性,虽然双冲量控制系统可以克服单冲量控制系统无法克服的“虚假水位”问题,但是它还是无法做到对调节阀的静态补偿和无法及时克服给水系统的干扰。
因此工业锅炉汽包水位控制一般都采用三冲量控制的方式,即为在双冲量水位调节控制系统的基础上加入给水流量信号构成的三冲量控制系统:汽包水位为主冲量信号、给水流量为回馈信号、蒸汽流量为前馈信号。
(三)锅炉燃烧控制方案设计
1、锅炉燃烧控制要求
工业锅炉是一个多输入输出、非线性的复杂控制对象,当某个参数变化时,其他的参数都会做出相应的改变,各个参数之间相互关系错综复杂,并且相互影响。
锅炉燃烧过程中的主要控制任务是给煤控制、给风控制和炉膛负压控制。
实现燃料量控制调节蒸汽压力,送风量控制调节烟气含量以及引风量控制炉膛负压,并有效克服了彼此间的干扰,保证锅炉经济安全运行的同时又能使产生的蒸汽可以满足设备负荷的需求。
2、主蒸汽压力控制方案设计
锅炉主蒸汽压力是整个燃烧控制系统的重要调节参数之一,引起蒸汽压力变化的因素有许多,给煤量、蒸汽流量是其中主要的两个原因。
3、送风控制方案设计
送风调节的目标是维持系统风煤比处于规定范围以保证煤粉燃烧的经济性。
但因为烟氧量主要由送风量决定,因为在控制时不能及时调节烟氧量,所以采用由烟气含氧量为主回路,送风量为副回路构成的串级控制,并结合比值控制调节送风量和给煤量,优化送风控制系统,保证烟氧量处于稳定值。
4、引风控制方案设计
引风量控制系统的主要任务在于调节控制引风调节阀,确保引风量始终稳定在规定范围,由此维持炉膛负压的稳定。
一旦炉膛内燃烧情况发生变化,炉膛负
压就会立即发生波动,因此要使锅炉能正常运行就必须控制炉膛负压。
(四)锅炉过热蒸汽温度控制方案设计
1、过热蒸汽温度控制方案要求
锅炉过热蒸汽温度控制系统的任务是维持过热器出口蒸汽温度在规定范围内,并保证过热器管壁温度始终处在安全值。
过热蒸汽温度控制一般采用减温水流量调节法来实现。
减温器等相关设备结构简单,操作起来简便快捷,因此通过减温水来调节过热器出口蒸汽温度的办法应用较为广泛。
在安装减温器时应尽可能靠近蒸汽的出口,确保过热器工作的安全。
2、过热蒸汽减温器的安装设计
为了保护过热器、提高蒸汽温度调节的灵敏性,过热蒸汽温度控制系统都采用前后两个喷水减温器。
第一个减温器安装在前屏过热器后面,调节幅度和惰性都较大。
因为末级的过热器热惯性小,第二个减温器安装在末级过热器前方,以便迅速调节出口蒸汽温度。
汽温控制一般采用两个调节器串联互相配合的工作模式,彼此协调,当一级减温器出现扰动时,它立即进行调节,随后二级减温器对扰动再次调节。
相较于单控制系统来说,优势明显。
三、锅炉控制系统设计
(一)锅炉控制系统硬件设计
1、硬件型号选定
(1)电动机
存锅炉汽包水位控制系统和燃烧控制系统中,电动机是主要的动力设备。
选择了合适的电动机才能保证供水准确、给煤适当,让锅炉运作更为稳定安全。
(2)变频器
变频器是实现变频器是利用电力半导体器件的通断作用将工频电源变换为另一频率的电能控制装置,能实现对交流异步电机的软起动、变频调速、提高运转精度、改变功率因子、过流/过压/超载保护等功能。
(3)变送器
变送器就是把传感器输出的信号转化成能被控制设备接收的数字信号的一种信号转化组件,它可以把传感器的非电量输入变成电流或电压信号,同时将这些电信号放大后传送给控制和监测设备。
大多实时监测信号都南变送器发出,但是不同的模拟量信号需要相应的传感器结合对应的变送器来产生。
变送器多种多
样,常见的工控变送器有压力变送器,流量变送器,电流变送器,电压变送器等。
(4)调节阀
根据传动能源的不同,调节阀可以分为气动调节阀、电动调节阀和液动调节阀二类。
其中液动和气动调节阀应用最为广泛,具有结构简单,动作迅速,性能可靠稳定,适用丁防火防爆场合等特点。
(5)开关电源
锅炉控制系统中,除了需要接入二相交流电以外,一些控制器件的电源为DC24V。
(6)PLC
主要由机架、CPU模块、信号(I/O)模块、功能模块、接口模块、通信处理器、电源模块和程序设计计算器组成,通过CPU模块或通信模块借口,PLC被连接到通信网路,可以与计算机、其他PLC或其他设备进行通信与控制。
西门子S7—300以极高的性价比在国际国内市场占有很大的份额,在我国的各工控行业得到了广泛的应用,其自身的功能指令灵活多变,基本适用于所有控制场合,而日.具有强大的扩展空间,可以解决一系列工业领域的控制难题
2、锅炉控制系统硬件设计
从电源接头引入380V电源为锅炉控制系统供电,为了保证设备的安全和不被瞬时过人的电流损坏,必须接入过流保护装置确保电流过大时能够及时断电。
当电气设备存自身出现故障时会使回路电流过大,此时熔断器动作,及时切断回路,保证供电回路和电动机的安全。
对于变频器的接线,因此首先应该将变频器的电源端与380V交流电源相连,利用PLC 输出控制变频器,进而控制电机的启停与转速的快慢,实现对参数的调节。
(二)锅炉系统软件设计
1、在给水控制上,采用电动机控制给水,并准备故障备用电机一台。
2、燃烧控制系统方面,通过变频器的调速来控制给煤电机的启停及给煤量,炉排电机也由电机结合变频器控制调节,保证经济节能的运作。
3、锅炉安全系统方面,为了保证过热的止常工作,通常会限制过热蒸汽的温度,并由减温水来调节控制。
(三)软件程序设计
根据一般课题要求,通过所编程序实现燃料量控制调节蒸汽压力,送风量控制调节烟气含量以及引风量控制炉膛负压的设计,并有效克服彼此间的干扰。
FC1:气泡水位控制系统
程序段1:给水电机I启停
程序段2:给水电机I故障无法运行时,启动设备用给水电机Ⅱ
程序段3:气泡水位低于低水位上限I,打开给水调节阀
程序段4:气泡水位高于高水位上限I,打开出水调节阀
程序段5:气泡水位超出警戒水位范围时,给水电机停机
程序段6:将对应参数传送到控制器并由其对相关变频器进行调节
FC2:燃烧系统控制系统
程序段1:给煤电机启停
程序段2:炉排电机启停
程序段3:炉膛温度数据、蒸汽流量数据采集
程序段4:将采集的对应参数传送到控制器并由其对相关变频器进行调节
程序段5:送风机Ⅰ启停
程序段6:送风机Ⅱ启停
程序段7:送风压力资料、给煤量数据采集
程序段8:将采集的对应参数传送到控制器并由其对相关变频器进行调节
程序段9:引风机启停
程序段10:送风压力资料、炉膛负压数据采集
程序段11:将采集的对应参数传送到控制器并由其对相关变频器进行调节
FC3:过热蒸汽控制系统、
程序段1:过热蒸汽温度数据采集
程序段2:将采集的对应参数传送到控制器并由其对阀门的开度进行调节
四、结论
对锅炉进行实施监控控制系统设计,要进行综合考虑,对遇到的问题及时予以解决,在实际运行过程中不断提高锅炉控制系统的技术水平,保证整个系统的稳定与安全。
参考文献:
[1] 邹丹丹. 基于PLC锅炉监控系统研究[M]. 黑龙江八一农垦大学.2010(4)
[2] 欧阳源敏; 丁维明.锅炉实时监控系统的研究与实现[J] 能源研究与利用.2001(9)。