高炉渣余热利用技术的现状及发展趋势 余热发电
2024年高炉余压发电市场前景分析

2024年高炉余压发电市场前景分析介绍高炉余压发电是一种利用高炉炼铁过程中产生的高压余热,通过适当的装置和设备转化为电能的技术。
随着我国钢铁工业的快速发展和节能减排政策的实施,高炉余压发电技术逐渐得到重视。
本文将分析高炉余压发电市场的发展前景。
市场需求1.节能减排政策的推动:随着环境保护意识的增强,钢铁行业需要采取节能减排措施。
高炉余压发电作为一种利用废热资源的技术,能够有效减少钢铁生产过程中的能源消耗和二氧化碳排放,符合节能减排政策的要求。
2.能源供给紧张:我国能源供给紧张,电力需求不断增长。
高炉余压发电可以增加钢铁企业自身的电力供应能力,减少对外购电的需求,缓解能源供给紧张的问题。
3.经济效益:高炉余压发电技术可以将废热转化为电能,提高钢铁企业的自给能力,减少能源成本。
此外,高炉余压发电技术还可以通过售电获取收入,进一步提高经济效益。
技术发展1.技术成熟度提高:随着高炉余压发电技术的不断发展和应用,其成熟度逐渐提高。
传统的蒸汽轮机和发电机组已经得到广泛应用,并且不断有新的技术和设备问世,如透平发电技术、余压发电机组等,进一步提高了高炉余压发电技术的效率和可靠性。
2.投资成本降低:随着技术的成熟和市场规模的扩大,高炉余压发电设备的生产和安装成本逐渐降低。
此外,政府对于节能减排的政策和经济刺激措施也为企业投资高炉余压发电提供了支持,进一步降低了投资成本。
市场前景1.市场规模扩大:随着我国钢铁行业的持续快速发展,高炉余压发电市场规模不断扩大。
据统计,我国钢铁企业中有相当一部分已经采用高炉余压发电技术,但整体普及率还不高,有很大的市场潜力。
2.政策支持力度加大:我国政府高度重视节能减排工作,通过出台一系列的政策文件和经济刺激措施来推动高炉余压发电技术的应用和普及。
政策的支持力度加大将促进高炉余压发电市场的快速发展。
3.国际市场需求增加:随着全球对于环境保护和可持续发展的需求增加,高炉余压发电技术也得到了国际市场的关注。
2024年余热发电市场分析现状

余热发电市场分析现状1. 引言余热发电是一种利用工业生产过程中的余热,通过发电机转化为电能的技术。
近年来,随着能源消耗和环境污染的日益加剧,余热发电作为一种清洁高效的能源利用手段备受关注。
本文将对余热发电市场的现状进行分析,并探讨其发展前景。
2. 余热发电市场规模与增长趋势据统计数据显示,全球余热发电市场规模自2010年以来持续增长。
截至2020年,全球余热发电市场规模已超过100亿美元,并有望在未来几年内进一步增长。
亚太地区是全球余热发电市场的主要增长动力,其中中国以其庞大的工业生产和亟需解决能源问题的背景成为全球最大的余热发电市场。
3. 余热发电市场的现状3.1 技术发展在余热发电技术方面,传统的蒸汽余热发电技术仍然占据主导地位,但逐渐出现了新型技术的应用。
例如,有机朗肯循环(ORC)技术和热电联供(CHP)技术已经在一些工业领域得到应用,并取得了良好的效果。
此外,新型材料和热交换技术的不断应用也推动了余热发电技术的进一步发展。
3.2 市场驱动因素余热发电市场的发展受到多方面因素的驱动。
首先,能源需求的增长以及对能源安全和环境保护的要求推动了余热发电的发展。
其次,各国政府出台的能源政策和环保政策为余热发电的发展提供了支持。
此外,技术进步和成本的降低也促使了余热发电市场的快速增长。
3.3 面临的挑战尽管余热发电市场发展迅速,但仍然面临一些挑战。
首先,技术成熟度不足和高投资成本限制了余热发电技术的应用范围。
其次,缺乏相关政策和法规的支持使得一些潜在的余热发电项目无法得到有效推进。
此外,一些工业企业对余热发电技术的接受度仍然较低。
4. 余热发电市场的未来发展4.1 市场前景展望未来,余热发电市场有望继续保持快速增长的势头。
一方面,随着技术的不断改进和成本的降低,余热发电将逐渐成为工业企业的标配设施。
另一方面,能源需求的增长和环境保护的要求将进一步推动余热发电市场的发展。
4.2 发展趋势未来余热发电市场的发展将呈现以下几个趋势。
高炉渣综合利用现状及发展趋势

高炉渣综合利用现状及发展趋势闫兆民,周扬民,杨志远,仪垂杰(青岛理工大学,青岛266033)摘 要:介绍高炉渣干法与湿法处理工艺及其余热利用方式的国内外研究和应用现状,评述了底滤法(O CP)、因巴法(INBA )典型的水淬法工艺,重点概括了风淬法、双滚筒法、离心粒化法3种干法处理技术的研究进展和发展趋势。
最后得出结论:离心粒化处理工艺在充分利用高炉渣的高品质热源同时,不会产生硫化氢、二氧化硫等有害气体,不会造成水资源的浪费,是今后高炉渣处理工艺的发展趋势。
关键词:高炉渣;干法粒化;热量回收中图分类号:X756 文献标识码:A 文章编号:1001 1447(2010)02 0053 04Present situation and development trend of blast furnaceslag comprehensive utilizationYAN Zhao min,ZH OU Yang min,YA NG Zhi yuan,YI Chui jie(Qingdao T echno logy U niversity,Qingdao 266033,China)Abstract:This paper introduces the research and application status of dry and w et blast fur nace slag treatment pr ocesses,as w ell as their w aste heat utilization w ays bo th hom e and o bro ad.The typical w ater quenching slag treatm ent metho ds,including OCP,IN BA are com mented,w ith fo cus on three kinds of dry g ranulation processing technolog y,i.e air blast gr anulation,tw in dr um g ranulatio n and centr ifugal granulation.Finally ,it is co ncluded that the centrifug al g ranulatio n can not only make full use of high quality heat source,but also avoid pr oducing H 2S 、SO 2and o ther harmful gases,and it can sav e w ater consumption as w ell.T herefore,the centrifugal g ranulation can be considered the trend o f blast furnace slag treatment process for the future.Key w ords:blast furnace slag;dry granulation;heat recycle 基金项目:钢铁研究联合基金重点项目(50934010)作者简介:闫兆民(1984-),男,硕士生,主要从事高炉渣余热回收的研究.高炉渣是钢铁冶炼过程的主要副产品,每炼出lt 生铁大约产生300~350kg 的高炉渣[1],按照我国年生铁年产量46944万t 计算[2],产渣量达14000万t 。
高炉渣显热回收利用现状与展望

分 是 硅酸 盐和 铝 酸盐 。当炉 温达 到 1400~1600 ̄ .
炉 料 熔 融 ,矿 石 中 的脉 石 ,焦 炭 中 的灰 分 ,助 溶 剂 和 其他 不 能 进 入 生 铁 中 的 杂质 形 成 以硅 酸 盐 和 铝 酸 盐 为主 浮 在 铁 水 上 面 的熔 渣 。高 炉 渣 的主 要 化 学成 分为 CaO、SiO 、A1 0,和 MgO,合 计超 过 了 炉 渣 组 成 的 95%。根 据 矿 石 及焦 炭灰 分 成 分 之 不 同 ,可 能 会 有 较 多 的其 他 化 合 物 如 TiO:、BaO 和 CaF2等 , 以及 少 量 的 MnO,FeO、CaS等 【3】。 承钢 高 炉渣 中还 含 有 TiO:和 V O ,酒泉 高 炉渣 中 含 有 Bao,CaF2等 。 1.2 高炉 渣的矿 物组 成
第 1期 2018年 2月
高洋等: 高炉渣显热 回收利 用现状 与展 望
·13·
蔷 薇辉 石 (MnOSO )矿 物等 。
2 高炉渣 的处理方法
目前 ,我 国 的 高炉 渣 的处 理 方 法 主 要 分 为 干 渣 和水 淬渣 两种 方式 。
由于 干渣 法 的 处理 方 法 易产 生 大 量 渣 棉 和 硫 化 氢气 体污 染 环境 ,而 且对 资源 的利 用率 也 不高 。 生产 的干 渣 量多 ,需要一 套完 整 的运渣 设 备 。因此 , 只 有 在 水 渣 系 统 有 故 障 才 会 使 用 。水 渣 法 大 致 分 为 4种方 式 :底滤 法 、因 巴法 、拉萨 法 、图拉 法 f4】。
关键 字:高炉渣 ;显 热回收;物理换热法 ;化学 回收法 ;干法粒化技术 doi:10.3969/j.issn.1000—6532.2018.01.003
高炉熔渣余热回收技术发展过程及趋势

高炉熔渣余热回收技术发展过程及趋势随着工业化进程的不断发展,高炉熔渣余热回收技术也在不断地发展和完善。
本文将从技术发展的历程和未来趋势两方面来探讨高炉熔渣余热回收技术的发展。
一、技术发展的历程高炉熔渣余热回收技术是一种利用高炉熔渣余热进行能量回收的技术。
它的发展历程可以分为以下几个阶段:1、初期阶段高炉熔渣余热回收技术最初是在20世纪初期开始出现的。
当时,人们主要采用的是换热器来回收高炉熔渣的余热。
然而,这种技术存在着很多问题,例如换热器的效率低、易受污染等。
2、中期阶段20世纪50年代,人们开始尝试采用“干法”和“湿法”两种方式来回收高炉熔渣的余热。
其中,“干法”主要是采用热风炉或热气轮机等设备来回收余热,而“湿法”则是采用热水或蒸汽等介质来回收余热。
这些技术在当时已经相对成熟,但仍存在着一些问题,如能量回收效率低、设备成本高等。
3、现代阶段进入21世纪后,高炉熔渣余热回收技术得到了更加广泛的应用和推广。
此时,人们开始采用先进的技术手段,如热泵、超临界流体回收等,来提高余热回收效率和设备的可靠性。
同时,人们也开始注重技术的环保性和经济性,力求实现能源的可持续利用。
二、未来趋势未来,高炉熔渣余热回收技术将呈现以下几个趋势:1、高效化随着科技的不断进步,高炉熔渣余热回收技术的效率将会得到进一步提高。
未来,人们将会采用更加先进的技术手段,如超临界流体回收、热泵等,来提高余热回收效率,实现更加高效的能量回收。
2、环保化在未来,高炉熔渣余热回收技术将更加注重环保性。
人们将会采用更加环保的技术手段,如低温余热回收、废热再利用等,来减少对环境的污染,实现绿色能源的利用。
3、智能化未来,高炉熔渣余热回收技术将更加智能化。
人们将会采用先进的智能控制系统,来实现设备的自动化操作和监控。
同时,人们也将会利用大数据和人工智能等技术,对设备的运行状态进行实时监测和分析,以实现设备的优化运行和维护。
总之,高炉熔渣余热回收技术是一项非常重要的能源回收技术。
利用高炉冲渣水余热采暖技术现状

高炉渣 的主要成分是氧化镁 、 氧化钙 、 三氧化二 铝, 约占炉渣总量的9 5 %, 出渣温度在1 4 5 0 ~1 6 5 0℃。 炉渣的处理主要采用水力冲渣方式 , 这一过程 中产生 温度在7 0  ̄9 0 o C 的冲渣热水 。 高炉冲渣水余热热源温 度较低 , 但流量巨大 , 并且水中蕴含 的化学物质对普通 钢材具有一定的腐蚀性 , 因此做好高炉冲渣水余热 的 回收工作 , 不仅能够有效减少能源浪费, 还可以保护周
陈 超, 丁翠娇 , 朱善合
4 3 0 0 8 0 ) ( 武汉钢铁集 团公 司武钢研究院 , 湖北 武汉
摘要: 高炉在生产过程 中产生大量 的冲渣水 , 同时排放了大量的热量 , 做好高 炉冲渣水余热 回收工作 意义 重大。 本文 阐述 当前 高炉冲 渣水余热采暖的主要方式 和利用现状 , 分析各种利用方式的优 缺点及存在问题 , 为类似工程的开展提供参考 。
边环境 , 意义十分重大 。 关于冲渣水 的余热利用方式 , 主要有取暖、 发电和海水淡化三种 , 目前广为利用的方 式是利用冲渣水余热进行采暖。
图 1 高炉冲渣水直接换热 系统
1 高炉 冲渣 水 余 热 采 暖 的途 径
自2 0 世纪8 0 年 代 以来 , 邯钢 、 宣钢 、 鞍钢 、 济钢 、 通
C H E N C h a o , D I N G C u i j i a o , Z H U S h a n h e ( R & D C e n t e r o f WI S C O, Wu h a n 4 3 0 0 8 0 , C h i n a )
Ab s t r a c t : Wi t h o p e r a t i o n o f b l a s t f u na r c e ,a l a r g e n u mb e r o f s l a g l f u s h i n g w a t e r i s p r o d u c e d,wh i c h e x h a u s t l o t s o f h e a t . I t i s s i g n i f i c a n t t o r e c y c l e t h e wa s t e h e a t o f s l a g l f u s h i n g w a t e r . I n t h i s a r t i c l e ,t h e u t i l i z i n g mo d e s ,u t i l i z a t i o n s t a t u s a n d t h e a d v a n t a g e s a n d d i s a d v a n t a g e s o f e a c h me t h o d a r e p r e s e n t e d,w h i c h c a n p r o v i d e r e f e r e n c e o f e n g i n e e r i n g a p p l i c a t i o n . Ke y wo r d s : b l a s t f u r n a c e ;s l a g l f u s h i n g w a t e r ;w a s t e h e a t
高炉冲渣水余热利用现状分析
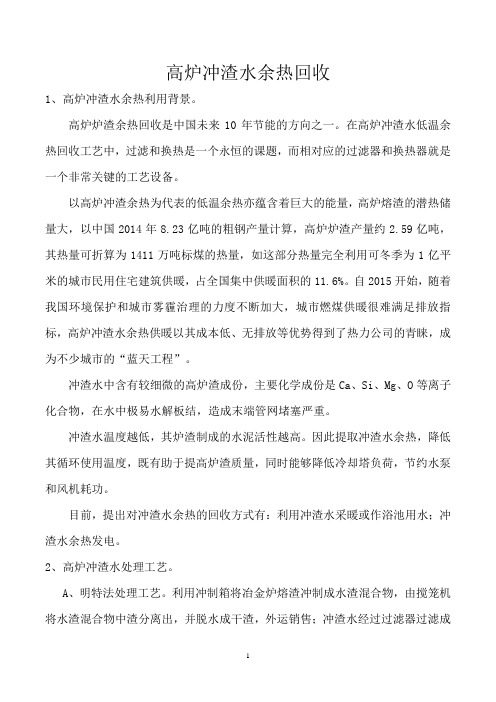
高炉冲渣水余热回收1、高炉冲渣水余热利用背景。
高炉炉渣余热回收是中国未来10年节能的方向之一。
在高炉冲渣水低温余热回收工艺中,过滤和换热是一个永恒的课题,而相对应的过滤器和换热器就是一个非常关键的工艺设备。
以高炉冲渣余热为代表的低温余热亦蕴含着巨大的能量,高炉熔渣的潜热储量大,以中国2014年8.23亿吨的粗钢产量计算,高炉炉渣产量约2.59亿吨,其热量可折算为1411万吨标煤的热量,如这部分热量完全利用可冬季为1亿平米的城市民用住宅建筑供暖,占全国集中供暖面积的11.6%。
自2015开始,随着我国环境保护和城市雾霾治理的力度不断加大,城市燃煤供暖很难满足排放指标,高炉冲渣水余热供暖以其成本低、无排放等优势得到了热力公司的青睐,成为不少城市的“蓝天工程”。
冲渣水中含有较细微的高炉渣成份,主要化学成份是Ca、Si、Mg、O等离子化合物,在水中极易水解板结,造成末端管网堵塞严重。
冲渣水温度越低,其炉渣制成的水泥活性越高。
因此提取冲渣水余热,降低其循环使用温度,既有助于提高炉渣质量,同时能够降低冷却塔负荷,节约水泵和风机耗功。
目前,提出对冲渣水余热的回收方式有:利用冲渣水采暖或作浴池用水;冲渣水余热发电。
2、高炉冲渣水处理工艺。
A、明特法处理工艺。
利用冲制箱将冶金炉熔渣冲制成水渣混合物,由搅笼机将水渣混合物中渣分离出,并脱水成干渣,外运销售;冲渣水经过过滤器过滤成干净水,由冲渣泵循环供冲制箱冲渣使用。
明特法水渣处理系统作为第三代水渣处理技术(即水渣领域的最新技术),其主要特点是彻底克服渣池法(第一代水渣处理技术:平流法、侧滤法、底滤法)、转鼓法(第二代水渣处理技术:INBA、图拉法)的不足,以全自动化方式对水渣进行处理。
即通过操作员的一个按钮动作,使水渣的分离自动完成,实现从设备出来的渣为干渣;出来的水为干净水,直接循环使用。
B、嘉恒法处理工艺。
由高炉放出的高温熔渣经熔渣沟流到出铁厂平台边缘的冲制箱前方,被冲制箱喷出的急速水流水淬,形成渣水混合物。
2023年炉渣资源化利用行业市场分析现状

2023年炉渣资源化利用行业市场分析现状炉渣是一种常见的工业废物,包括煤矸石、冶炼渣、钢渣等。
炉渣资源化利用是将这些废物转化为有价值的产品或用于生产过程的原料的过程。
随着环境保护和可持续发展的重要性的增强,炉渣资源化利用行业市场正在迅速发展。
首先,炉渣资源化利用行业市场的现状是庞大的。
根据行业研究报告,全球炉渣资源化利用市场在2019年达到了290亿美元,并预计到2027年将增长至370亿美元。
这个巨大的市场规模主要是由于炉渣资源化利用可以减少废物的排放,同时还可以获得可回收物质或能源。
此外,一些国家和地区也出台政策支持炉渣资源化利用,促进了市场的发展。
其次,炉渣资源化利用行业市场的主要驱动因素是环境保护和可持续发展的要求。
随着全球环境问题的日益严重,减少废物排放和资源回收利用成为了各国的共同目标。
炉渣资源化利用可以将大量的工业废物转化为有价值的产品或能源,从而减少对自然资源的依赖,降低环境污染。
此外,炉渣资源化利用还可以降低生产成本,提高企业的竞争力,符合可持续发展的理念。
然而,炉渣资源化利用行业市场也面临着一些挑战。
首先是技术难题。
由于炉渣的成分复杂多样,炉渣资源化利用过程需要先进的技术和设备来处理和分离炉渣中的有价值成分。
此外,由于炉渣的特性和来源的差异,炉渣资源化利用的技术和设备需要根据不同的情况进行调整和优化,增加了技术研发的难度和成本。
其次是市场竞争。
由于炉渣资源化利用市场潜力巨大,吸引了众多企业投身其中,导致市场竞争激烈。
一些大型企业通过技术创新和规模扩大来取得竞争优势,而一些小型企业则面临技术研发和资金支持的困难。
为了应对这些挑战,炉渣资源化利用行业应加强技术研发和创新,提高炉渣资源化利用技术和设备的效率和可靠性。
此外,政府和相关机构应加大对炉渣资源化利用行业的支持和鼓励,推动行业发展和市场竞争力的提高。
同时,加强行业交流和合作,促进企业之间的资源共享和合作,降低市场竞争的风险。
- 1、下载文档前请自行甄别文档内容的完整性,平台不提供额外的编辑、内容补充、找答案等附加服务。
- 2、"仅部分预览"的文档,不可在线预览部分如存在完整性等问题,可反馈申请退款(可完整预览的文档不适用该条件!)。
- 3、如文档侵犯您的权益,请联系客服反馈,我们会尽快为您处理(人工客服工作时间:9:00-18:30)。
高炉渣余热利用技术的现状及发展趋势摘要:本文系统的分析了高炉渣湿法与干法处理工艺及其余热利用的国内外现状,简述了底滤法(OCP)、因巴法(INBA)、拉萨法(RASA)、图拉法(TYNA)等典型的水淬法工艺,总结了水淬渣方式存在的诸多弊端,对风淬法、双内冷却转筒粒化法、Merotec 熔渣粒化流化法、机械粒化法、连铸连轧法、化学法等干法处理技术的研究进展和发展现状进行了总结。
最后得出结论: 离心粒化等干式余热回收技术在利用高炉渣的高品质热源时,不会造成水资源的浪费, 不会产生硫化氢、二氧化硫等有害气体,在克服水渣法固有缺点的同时,还可以得到玻璃化程度高的高附加值成品渣,是今后高炉渣余热回收工艺的发展趋势。
关键词:高炉渣;余热利用;水淬;干式粒化1 前言中国目前是全球最大的钢铁生产国。
中国钢铁产量已连续16年保持世界第一,并且遥遥领先于其他国家。
同时伴随我国高炉冶炼生产排出的含丰富热能的高炉渣数量也是巨大的,从节能与环保以及提高钢铁厂的经济效益的角度来看,对高炉渣的热量进行回收和高炉渣的资源化利用是十分必要的。
炉渣的出炉温度一般在1400~1550℃之间。
每吨渣含(1260~1880)×103kJ的显热,相当于60kg标准煤的热值[1]。
每生产1吨生铁要副产0.3吨高炉渣,每生产1吨钢要副产0.13吨钢渣[2],以目前我国的钢铁产量6.83亿吨进行计算,可产生2.9亿吨以上的高炉渣和转炉渣,其显热量相当于1740万吨标准煤,尽管并非可以全部回收高炉渣的热能,但若能部分回收利用,其节能效益也是显著的,非常具有市场开发潜力。
就目前应用大量应用水淬技术情况来看,这部分高温热源显然是被浪费了,该高温热源就温度品质来说,完全符合高品位能源的要求,如果能回收这部分热量得以重新利用,就可以为社会和企业带来可观的经济、社会和环保效益。
开展余热余能的回收利用不仅是钢铁企业节约能源降低成本,提高竞争力的重要手段,而且也符合国家钢铁工业的政策要求。
在我国的钢铁工业“十二五”发展规划中明确指出要大力发展清洁生产和循环经济,积极研发和推广使用节能减排和低碳技术,加强废弃物的资源化综合利用[2]。
在节能减排方面提出以下几个重要指标,单位工业增加值能耗和二氧化碳排放分别下降18%,重点统计钢铁企业平均吨钢综合能耗低于580千克标准煤,吨钢耗新水量低于4.0立方米,吨钢二氧化硫排放下降39%,吨钢化学需氧量下降7%,固体废弃物综合利用率97%以上。
在钢铁工业的节能减排技术方面重点提到了高炉渣、钢渣等显热回收利用技术、冶金渣综合利用技术和余热余压综合利用技术等。
2 高炉渣处理现状目前我国常见的处理高炉渣的方法有干渣坑冷却法和水冲渣法。
干渣坑冷却法将熔融的高炉渣倒入干渣坑空冷,凝固后水冷。
此法污染地下水源,降温时放出大量水蒸气,同时释放大量的H2S和SO2气体,腐蚀建筑、破坏设备和恶化工作环境,一般只在事故处理时使用该法。
我国90%的高炉渣都采用水冲渣法处理,得到的水渣用于生产水泥、渣砖、矿渣微粉和隔热填料。
高炉渣水淬方式很多,主要处理工艺有:底滤法(OCP)、因巴法(INBA)、拉萨法(RASA)、图拉法(TYNA)等。
尽管冲渣工艺在不断的发展,但其技术的核心还是对高炉熔渣进行喷水水淬,冷却、粒化成水渣,然后进行水渣分离,冲渣的水经过沉淀过滤后再循环使用。
2.1底滤法底滤法是在冲制箱内用多孔喷头喷射的高压水对高炉渣进行水淬粒化,然后进入沉渣池(图1)。
沉渣池中的水渣由抓斗抓出堆放在干渣场继续脱水,沉渣池内的水及悬浮物由分配渠流入过滤池。
过滤后的冲渣水经集水管由泵加压送入冷却塔冷却后重复使用。
底滤法的滤池的总深度较低;机械设备少,施工、操作、维修都较方便;循环水质好,水渣质量好;冲渣系统用水可实现100%循环使用,没有外排污水,有利于环保。
其缺点是占地面积大,系统投资也较大[3]。
1—高炉; 2—抓斗吊车; 3—冲渣器;4—水溢流;5—贮料斗;6—粒化器;7—冲洗空气入口;8—水出口图1底滤法水渣处理工艺示意图2.2拉萨法拉萨法为英国RASA公司与日本钢管公司共同开发的炉渣处理工艺,1967 年首次在日本福山钢铁厂1号高炉(2004m3 )上使用(图2)。
拉萨法的工艺流程为:高炉熔渣由渣沟流入冲制箱,与压力水相遇进行水淬。
水淬后的渣浆在粗粒分离槽内浓缩,浓缩后的渣浆由渣浆泵送至脱水槽脱水;浮在分离槽水面的微粒渣由溢流口流入中间槽,由中间槽泵送到沉淀池,经沉淀后,用排泥泵送回脱水槽,同粗粒分离器送去的渣水混合物一起进行脱水,脱水后水渣由卡车外运[4]。
1—水渣槽;2—喷水口;3—搅拌槽;4—输渣泵;5—循环槽搅拌泵;6—搅拌槽搅拌泵;7—冷却塔;8—循环水槽;9—沉降槽;10—冲渣给水泵;11—冷却泵;12—分配器;13—脱水槽;14—汽车;15—排泥泵图2 拉萨法水渣处理工艺示意图该法炉渣处理量大、水渣质量较好,技术上有一定进步。
但该法因工艺复杂、设备较多、电耗高及维修费用大等缺点,在新建大型高炉上已不再采用。
2.3 图拉法图拉法粒化渣工艺是俄罗斯图拉厂所创,其工艺思想是通过机械力将熔渣粒化并喷水冷却产生水渣(图3)。
该法与其他水淬法不同,在渣沟下面增加了粒化轮,炉渣落至高速旋转的粒化轮上,被机械破碎、粒化,粒化后的炉渣颗粒在空中被水冷却、水淬,产生的气体通过烟囱排出[5]。
该法最显著特点是彻底解决了传统水淬渣易爆炸的问题。
熔渣处理在封闭状态下进行,循环水量少,动力能耗低,成品渣质量好[6]。
1—熔渣沟; 2—粒化器;3—排气筒;4—脱水器;5—热水池;6—胶带机;7—成品槽图3 图拉法水渣处理系统示意图2.4 因巴法因巴法水渣处理系统是二十世纪八十年代初由比利时西德玛(SDIMAR)公司与卢森堡保尔-乌斯(APUL-WURTH)公司共同开发的一项渣处理技术,1981年在西德玛公司投入运行[7]。
因巴法分为热因巴、冷因巴和环保型因巴三种类型(见表1)[3]。
典型因巴法炉渣处理系统见图4 所示。
表1 因巴法炉渣处理工艺类型因巴法流程为:高炉熔渣由熔渣沟流入冲制箱,经冲制箱的压力水冲成水渣进入水渣沟,然后经滚筒过滤器脱水排出。
该法布置紧凑,可实现整个流程机械化、自动化,水渣质量好;冲渣水闭路循环,泵和管路的磨损小;无爆炸危险,渣中含铁量高达20%时,该系统还能安全地进行炉渣的粒化;彻底解决烟尘、蒸汽对环境的污染,达到零排放的目标。
1—冲制箱; 2—水渣沟; 3—水渣槽; 4—分配器; 5—转鼓过滤器; 6—缓冲槽;7—集水槽; 8—热水池; 9—冷却塔; 10—冷水池; 11—胶带机; 12—成品槽图4 因巴法水渣处理系统示意图表2为上述几种典型高炉渣处理湿法工艺的主要技术指标,就目前来看,图拉法安全性能最高(渣中带铁达40%时,仍能正常工作);而投资费用最大的环保型因巴法在技术上最为成熟,实际应用的高炉亦较多[3]。
但水冲渣法无法从根本上改变粒化渣耗水的工艺特点,炉渣物理热基本全部散失,冲渣过程中S02、H2S等污染物的排放不但影响作业环境而且对空气造成污染。
水淬渣方式存在以下诸多弊端:1) 浪费了高炉渣所含有的高品质余热资源。
1350℃~1450℃的液态高炉渣由出渣口排出,靠高压水将其破碎并冷却,在如此高的温度下,大部分的液态水迅速气化成水蒸气排放到大气中,浪费了该部分水蒸气含有的大量热量, 以目前我国年产生2.9亿吨高炉渣和转炉渣计算,其显热量相当于1740万吨标准煤。
2) 浪费大量水资源。
水冲渣过程中水压大于0.2MPa,渣水之比为1:1,每吨渣需消耗新水0.8~1.2吨,循环用水量10t左右。
中国目前高炉生铁产量超过6.8亿吨,全年高炉渣产量约2亿吨,用于水淬渣的新水消耗量约2亿吨。
3) 产生SO2及H2S等有害气体,除环保型INBA法外的其他水渣系统均将冲渣过程产生的含硫蒸汽直接排入大气中,不同INBA法随蒸汽排入大气的硫化物量分别为(具体数值与高炉原料条件有关):热水INBA法为250g/t,普通冷水INBA法为25g/t,最环保的环保型INBA法也有5g/t,按目前的炉渣产生量即使全部采用最环保的INBA法,全年将排放1450tSO2,目前的SO2的排放现状是此数值的几十倍计。
因此,利用干法将高炉渣粒化作为水泥原料,同时高效利用炉渣显热,减少对环境的污染,是高炉渣处理的发展趋势。
表2 几种高炉渣处理方法技术经济指标比较3 高炉渣干法粒化余热回收技术干式粒化工艺是在不消耗新水情况下,利用高炉渣与传热介质直接或间接接触进行高炉渣粒化和显热回收的工艺,几乎没有有害气体排出,是一种环境友好的新式处理工艺。
目前高炉渣干法处理工艺主要有:风淬法、双内冷却转筒粒化法、Merotec 熔渣粒化流化法、机械粒化法、连铸连轧法、化学法等。
20世纪70年代国外就开始研究此法,但目前尚无一种真正实现工业化。
3.1风淬法风淬法是利用高速空气将熔渣冲击破碎并回收余热的方法[8]。
日本钢管和三菱重工从1977年开始联合开发了转炉渣风碎粒化余热回收系统(图6),并于1978年在日本钢管福山厂3号炼钢厂建立了处理能力为30t/h实验厂[9]。
之后两家公司于1981年在福山厂建成了最大处理能力为80t/h的商业化工厂[10]。
整个余热回收流程包括预处理、风碎、余热回收、后处理4个处理工序。
该流程的工业试验中,总热回收率达到了81.3%。
图6日本钢管与三菱重工联合开发的转炉钢渣风碎粒化工艺流程图1982年日本新日铁、NKK、川崎、住友、神户和日新制钢6大钢铁公司开展了计划为期6年的高炉熔渣显热综合回收技术研究,目的是在回收高炉渣余热的同时,制造水泥原料等高附加值的炉渣产品。
该工艺流程图如图7所示[11],熔渣在被风碎后通过多段流化床回收渣粒余热。
从余热回收的效果来看,回收的热空气的余热回收效率为62.6%;从渣粒的品质来看,不含渣棉的渣粒玻璃体率为96%~98%,水泥胶砂的强度测试表明,利用风碎高炉渣得到的炉渣水泥与市售的普通高炉渣水泥具有同等的强度。
在大量试验的基础上,研究者针对400Om3级,处理能力为150t/h的炉渣余热回收系统进行了经济性分析,但目前并没有该工艺商业化的报道[12]。
图7日本6大钢铁公司联合开发的高炉渣风碎粒化余热回收流程示意图风淬法在粒化过程中动力消耗很大,风碎与水淬相比冷却速度很慢,为了防止粒化渣在固结之前粘连到设备表面上,就要加大设备的尺寸[13]。
风淬法得到的粒化渣的颗粒直径分布范围较宽,不利于后续处理。
3.2旋转滚筒法熔渣粒化工艺NKK双冷却转筒粒化工艺最早由日本钢管公司(NKK)开发,其工艺流程如图8所示[11]。
温度为1500℃左右的液态高炉渣经渣槽流入位于转鼓 B1 和 B2 之间形成的渣池,转鼓连续转动,通过挡板(A)来控制熔渣的液位,熔渣随转鼓的转动被带出并在转鼓表面成膜,在转鼓内通过一种高沸点有机液体(烷基联苯)来快速冷却附着在转鼓表面的渣膜,随后冷却的玻璃相炉渣由一种脱膜工具从转鼓上剥离落入料斗,得到的成品渣温度约为900℃。