压力管道无损检测
压力管道层下腐蚀检测方法介绍
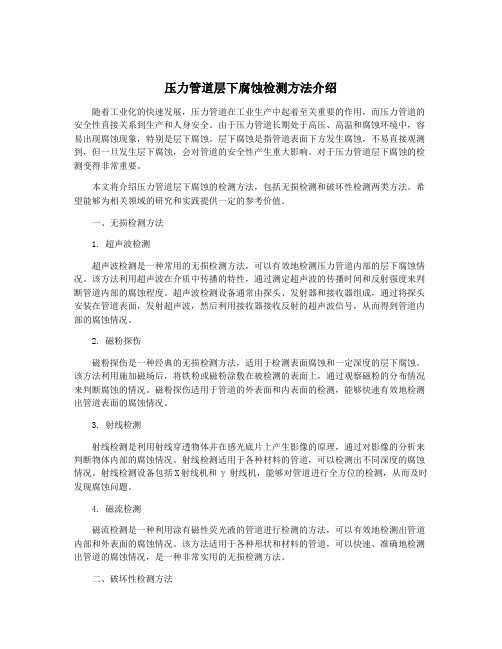
压力管道层下腐蚀检测方法介绍随着工业化的快速发展,压力管道在工业生产中起着至关重要的作用,而压力管道的安全性直接关系到生产和人身安全。
由于压力管道长期处于高压、高温和腐蚀环境中,容易出现腐蚀现象,特别是层下腐蚀。
层下腐蚀是指管道表面下方发生腐蚀,不易直接观测到,但一旦发生层下腐蚀,会对管道的安全性产生重大影响。
对于压力管道层下腐蚀的检测变得非常重要。
本文将介绍压力管道层下腐蚀的检测方法,包括无损检测和破坏性检测两类方法。
希望能够为相关领域的研究和实践提供一定的参考价值。
一、无损检测方法1. 超声波检测超声波检测是一种常用的无损检测方法,可以有效地检测压力管道内部的层下腐蚀情况。
该方法利用超声波在介质中传播的特性,通过测定超声波的传播时间和反射强度来判断管道内部的腐蚀程度。
超声波检测设备通常由探头、发射器和接收器组成,通过将探头安装在管道表面,发射超声波,然后利用接收器接收反射的超声波信号,从而得到管道内部的腐蚀情况。
2. 磁粉探伤磁粉探伤是一种经典的无损检测方法,适用于检测表面腐蚀和一定深度的层下腐蚀。
该方法利用施加磁场后,将铁粉或磁粉涂敷在被检测的表面上,通过观察磁粉的分布情况来判断腐蚀的情况。
磁粉探伤适用于管道的外表面和内表面的检测,能够快速有效地检测出管道表面的腐蚀情况。
3. 射线检测射线检测是利用射线穿透物体并在感光底片上产生影像的原理,通过对影像的分析来判断物体内部的腐蚀情况。
射线检测适用于各种材料的管道,可以检测出不同深度的腐蚀情况。
射线检测设备包括X射线机和γ射线机,能够对管道进行全方位的检测,从而及时发现腐蚀问题。
4. 磁流检测磁流检测是一种利用涂有磁性荧光液的管道进行检测的方法,可以有效地检测出管道内部和外表面的腐蚀情况。
该方法适用于各种形状和材料的管道,可以快速、准确地检测出管道的腐蚀情况,是一种非常实用的无损检测方法。
二、破坏性检测方法1. 金相显微镜检测金相显微镜是一种常用的金属材料显微组织检测仪器,可以对金属材料进行显微观察和分析。
压力管道检验检测流程

压力管道检验检测流程英文回答:Pressure pipeline inspection and testing process is an essential procedure to ensure the safety and reliability of pipelines. It involves various steps and techniques to assess the integrity of the pipeline and identify any potential defects or damages. The following is a general overview of the pressure pipeline inspection and testing process.1. Pre-inspection preparations: Before conducting the inspection, it is crucial to gather all the necessary information about the pipeline, including its design specifications, operating conditions, and any previous inspection records. This information helps in determining the appropriate inspection methods and equipment.2. Visual inspection: The first step is to visually inspect the pipeline for any visible signs of damage orcorrosion. This can be done by walking along the pipeline route and looking for any leaks, cracks, or irregularities. Visual inspection is a preliminary assessment that helps in identifying areas that require further inspection.3. Non-destructive testing (NDT): NDT techniques are used to evaluate the internal condition of the pipeline without causing any damage. Some common NDT methods include ultrasonic testing, magnetic particle testing, and radiographic testing. These techniques help in detecting defects such as cracks, corrosion, or weld defects.4. Pressure testing: Pressure testing is performed to assess the strength and integrity of the pipeline. It involves pressurizing the pipeline with water or another suitable medium to a predetermined pressure and monitoring for any pressure drops or leaks. This test helps in identifying any weak points or potential failures in the pipeline.5. Leakage testing: Leakage testing is conducted to detect any leaks in the pipeline. This can be done bypressurizing the pipeline and using leak detection equipment such as gas detectors or leak detection fluids. Leakage testing ensures that the pipeline is free from any leaks that could compromise its safety and efficiency.6. Documentation and reporting: After completing the inspection and testing, all the findings and observations are documented in a detailed report. This report includes information about the inspection methods used, the results obtained, and any recommendations for repairs or maintenance. The report serves as a record of thepipeline's condition and helps in making informed decisions regarding its operation and maintenance.中文回答:压力管道检验检测流程是确保管道安全可靠的关键步骤。
石油化工压力管道的破坏和无损检测

石油化工压力管道的破坏和无损检测作者:张晓野来源:《城市建设理论研究》2013年第14期【摘要】压力管道在其运行过程中它的安装质量严重的影响了压力管道的运行,所以在压力管道的安装过程中就要执行严格的审查、检查、实验等许多重要的步骤和要点进行控制。
本文重要介绍的在压力管道施工的过程中各个施工安装环节进行监督检查的技巧方法,用此来保证压力管道的安装质量,并借此为压力管道的运行等打下不可摧毁的基础。
压力管道在材质和使用方面受到其材质、参数、安装质量等的影响使其相当的复杂,往往导致了相当多的破坏。
他的破坏有腐蚀破坏,疲劳破坏,蠕变破坏,冲刷磨损减薄破坏和脆性破坏五种形式,而其中的腐蚀破坏和蠕变破坏在五种破坏中又是最主要的破坏。
【关键词】压力管道; 射线; 无损检测; 质量; 控制中图分类号:O213.1 文献标识码:A 文章编号:一、前言当今社会,随着我国国民经济的飞速的发展,从我国产生的石油化工产品不仅从数量上达到了世界的前列,而且从质量上达到了世界的前列。
因此无论是装备还是种类都要考虑到生产的要求,我们也是向这方面付出了很大的努力,并且都取得了相当大的成就,达到了很高的水平。
虽然近年来我国国内的管道铺设在飞速的发展,但是有些技术还是没有足够的成熟,不时的还会有事故的发生,因此这大大地影响了我国石油化工工业的发展,并且我国国内大部分的管道设施都迫切的需要检修,并且达到了一个高峰期,所以此时使检修的水平得到提高,能及时的使隐患消失于开始,这可以有效的保证工业的正常生产,保证人民生命财产安全,防止事故的发生。
二、石油化工压力管道的破坏化工压力管道由于其固有的复杂性,因此引起破坏的因素往往很多,综合分析压力管道的材质、工艺参数、安装质量和使用工况,有助于对管道破坏作出正确的判断,并选择有效和合理的无损检测技术。
通常认为化工压力管道(由于埋设管主要用于压力较低的供水、供气、油料输送和工厂排污,其损伤及破坏形式较为简单,因此本文所谈到的化工压力管道主要是指架设管道)的破坏形式主要有五种:腐蚀破坏,疲劳破坏,蠕变破坏,冲刷磨损减薄破坏和脆性破坏。
压力管道无损检测和焊接技术-最新文档

压力管道无损检测和焊接技术-最新文档压力管道无损检测和焊接技术一、引言加强焊接施工过程的控制,可以有效的减少质量问题。
为保证压力管件的焊接质量,我们还要对其进行检测,本文以下就是压力管道焊接质量问题的分析,并结合在结合实际情况采取有效的预防措施和控制措施,避免严重质量问题的发生;以及焊接施工完成后对其进行的无损检测。
二、压力管道焊接施工中的质量问题及防范措施1、气孔问题防范措施:(1)要保持焊条或焊丝应的干燥,遇特殊情况可以进行烘干的操作,在保温桶存放,限量领取,以防止受潮;(2)在进行焊接操作时要严格的控制施工条件,防止不良气体的进入焊缝;(3)要对压力管道焊口有缺陷的部位可以用砂轮进行打磨处理;(4)焊接时要做好防风措施,特别是风对低氢型焊条的焊接施工有着极大影响,因此更加需要严格防风;5.压力管道的管口必须保持清洁和干燥,不能有铁锈、杂质或油污等。
2、夹渣问题防范措施:(1)组对的间隙不应该太小,尽可能在工艺参数的范围之内采取较大的电流,确保焊接的熔深,并且焊速也不能太快;(2)焊道的打磨不能过多、过薄,并且去除压力管道表面的熔渣,还要注意将压力管道的接头打平。
压力管道焊接时根焊道的打磨不合格,会造成热焊能控制烧穿现象,产生夹渣;(3)焊工应该使用正确的操作手法,合理控制运条角度和摆动幅度,以防止焊接熔深不足,容易产生夹渣;(4)断弧、更换焊条是应进行焊口打磨处理;(5)认真的清理压力管道与焊条上的杂质,以及焊道上的熔渣等,在压力管道焊接前要对焊道的毛茬、杂物以及掉落的渣垢等进行及时的清理,以防止这些杂质进入焊道,产生夹渣的现象,在压力管道的焊接过程中要保持熔池的清晰,确保熔渣的液面与熔池金属能够良好分离;6.焊接施工时的焊接速度不能过快,并且要保证熔深。
3、未焊透问题防范措施:(1)焊接施工时可以根据焊接的规程要求,对坡口尺寸以及钝边厚度进行控制;(2)在压力管道焊接时应该准确的调整和控制运条的角度以及焊接速度,以确保电弧能处于正确的方向。
压力管道的定期检验制度
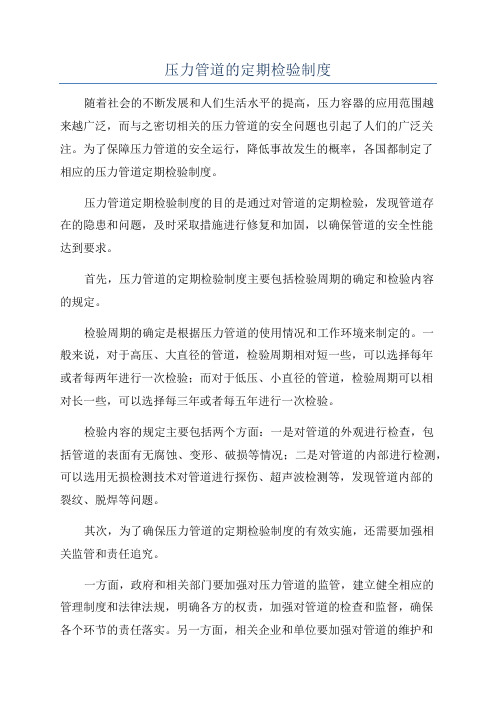
压力管道的定期检验制度随着社会的不断发展和人们生活水平的提高,压力容器的应用范围越来越广泛,而与之密切相关的压力管道的安全问题也引起了人们的广泛关注。
为了保障压力管道的安全运行,降低事故发生的概率,各国都制定了相应的压力管道定期检验制度。
压力管道定期检验制度的目的是通过对管道的定期检验,发现管道存在的隐患和问题,及时采取措施进行修复和加固,以确保管道的安全性能达到要求。
首先,压力管道的定期检验制度主要包括检验周期的确定和检验内容的规定。
检验周期的确定是根据压力管道的使用情况和工作环境来制定的。
一般来说,对于高压、大直径的管道,检验周期相对短一些,可以选择每年或者每两年进行一次检验;而对于低压、小直径的管道,检验周期可以相对长一些,可以选择每三年或者每五年进行一次检验。
检验内容的规定主要包括两个方面:一是对管道的外观进行检查,包括管道的表面有无腐蚀、变形、破损等情况;二是对管道的内部进行检测,可以选用无损检测技术对管道进行探伤、超声波检测等,发现管道内部的裂纹、脱焊等问题。
其次,为了确保压力管道的定期检验制度的有效实施,还需要加强相关监管和责任追究。
一方面,政府和相关部门要加强对压力管道的监管,建立健全相应的管理制度和法律法规,明确各方的权责,加强对管道的检查和监督,确保各个环节的责任落实。
另一方面,相关企业和单位要加强对管道的维护和管理,保证管道的正常运行和安全使用,定期对管道进行检测和维修,及时消除隐患。
最后,为了提高压力管道的安全性能,还需要加强技术研发和人员培训。
一方面,应该加强对压力管道相关技术的研发,引进先进的技术设备和检测手段,提高检测的准确性和精确度;另一方面,还需要加强对相关人员的培训和教育,提高其对管道安全的认识和操作技能,降低人为因素对管道安全的影响。
综上所述,压力管道的定期检验制度对于保障管道的安全运行和预防事故发生具有重要意义。
通过科学合理地确定检验周期和检验内容,加强监管和责任追究,加强技术研发和人员培训,可以有效提高压力管道的安全性能和服务寿命,为人们的生活和生产提供更加可靠的保障。
压力管道焊道复检
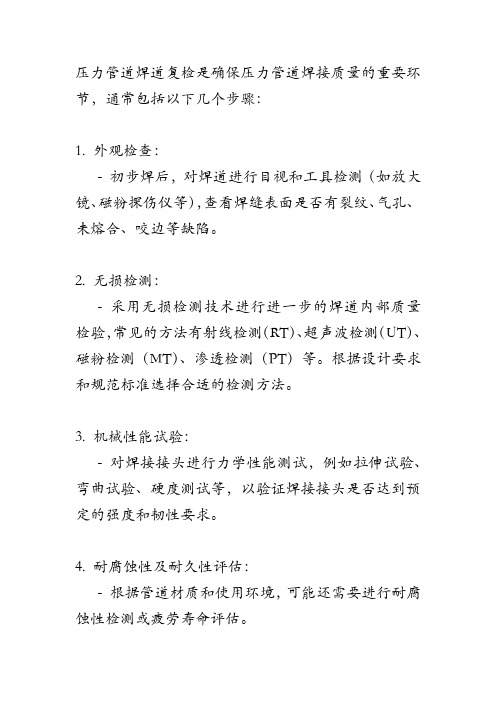
压力管道焊道复检是确保压力管道焊接质量的重要环节,通常包括以下几个步骤:
1. 外观检查:
- 初步焊后,对焊道进行目视和工具检测(如放大镜、磁粉探伤仪等),查看焊缝表面是否有裂纹、气孔、未熔合、咬边等缺陷。
2. 无损检测:
- 采用无损检测技术进行进一步的焊道内部质量检验,常见的方法有射线检测(RT)、超声波检测(UT)、磁粉检测(MT)、渗透检测(PT)等。
根据设计要求和规范标准选择合适的检测方法。
3. 机械性能试验:
- 对焊接接头进行力学性能测试,例如拉伸试验、弯曲试验、硬度测试等,以验证焊接接头是否达到预定的强度和韧性要求。
4. 耐腐蚀性及耐久性评估:
- 根据管道材质和使用环境,可能还需要进行耐腐蚀性检测或疲劳寿命评估。
5. 修复与再检测:
- 如果在上述检测过程中发现焊道存在不符合标准的缺陷,需要按照规定的方法进行修复,并在修复完成后再次进行相关检测,直至合格为止。
6. 记录与报告:
- 记录每次检测的结果,形成完整的焊接质量检测报告,存档备查,同时作为工程验收的重要依据。
7. 第三方检测:
- 在某些情况下,为了保证公正性和权威性,可能还会邀请第三方专业检测机构进行复检工作。
总之,压力管道焊道复检是一个严谨的过程,其目的是通过一系列科学的检测手段,全面确保压力管道的安全可靠运行。
压力管道检验检测方法
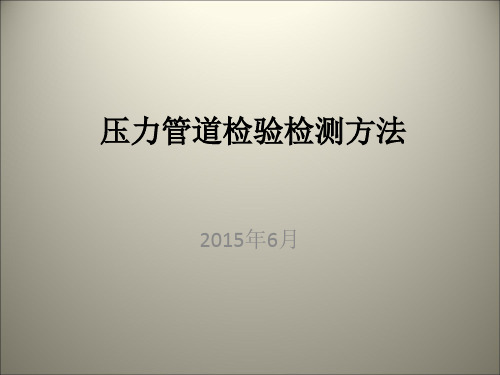
检验方案宏观检查部分内容:
安全附件 • 包括压力表、测温仪表、安全阀、爆破片
装置、紧急切断装置。 • 检查内容:安全附件的完好性,铅封、校
验期限的有效性,安装位置等。
检验方案宏观检查部分内容:
管道安装位置 • 与其他管道或相邻设备之间是否存在碰撞、
摩擦。 • 管道跨越道路管段距离地面的高度应当大
• 焊缝距离弯管(不包括压制、热推或中频弯管) 起弯点不得小于100mm,且不得小于管子外径。
• 环焊缝距支、吊架净距离不应小于50mm。 • 不宜在管道焊缝及其边缘上开孔。
• 穿墙及过楼板的管道应加套管。
检验方案宏观检查部分内容:
焊缝错边 • GC1级管道:外壁错边量应小于壁厚的20%,
且不大于3mm。 • GC2、GC3级管道:外壁错边量应小于壁厚
的25%,且不大于5mm。
检验方案宏观检查部分内容:
焊缝咬边
• GC1级管道:咬边深度不得超过0.5mm。 • GC2级、GC3级管道:咬边深度不得超过
0.8mm。
检验方案宏观检查部分内容:
钢管表面 • 应记录的缺陷:变形、腐蚀、碰伤、皱褶、
重皮以及可见的裂纹、气孔等。 • 蠕胀测点位置、静电接地位置。
求。
检验记录和异常情况处理:
• 检验记录,检验的项目要有相应记录,并 有相关资格人员签字,记录格式要符合规 范要求,记录的信息要充分;
• 异常情况要详细记录,必要时需画图标位, 便于查找;
• 不符合项要有相应处理意见:如修理、改 造、更换、监控使用等,出具检验意见通 知书。
2.放大镜检查
• 方法:采用5—10倍的放大镜对肉眼检查有 怀疑部位进行更细致的检查。
• 目的:发现比较细小的肉眼难以发现的表 面裂纹、蚀坑、气孔。必要时可采用表面 无损检测予以验证。
压力管道需要探伤的标准
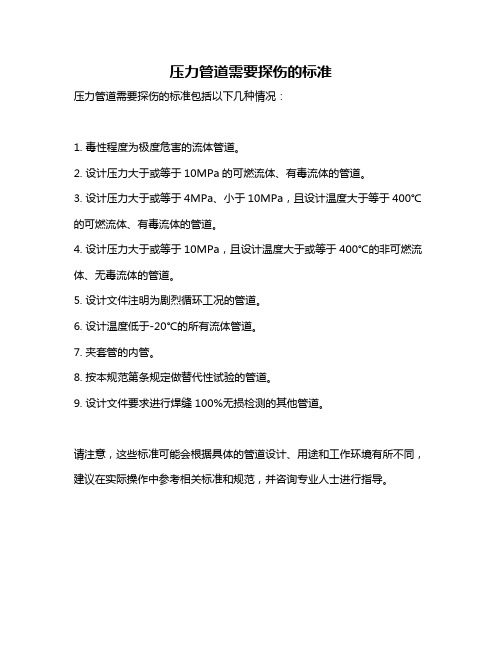
压力管道需要探伤的标准
压力管道需要探伤的标准包括以下几种情况:
1. 毒性程度为极度危害的流体管道。
2. 设计压力大于或等于10MPa的可燃流体、有毒流体的管道。
3. 设计压力大于或等于4MPa、小于10MPa,且设计温度大于等于400℃的可燃流体、有毒流体的管道。
4. 设计压力大于或等于10MPa,且设计温度大于或等于400℃的非可燃流体、无毒流体的管道。
5. 设计文件注明为剧烈循环工况的管道。
6. 设计温度低于-20℃的所有流体管道。
7. 夹套管的内管。
8. 按本规范第条规定做替代性试验的管道。
9. 设计文件要求进行焊缝100%无损检测的其他管道。
请注意,这些标准可能会根据具体的管道设计、用途和工作环境有所不同,建议在实际操作中参考相关标准和规范,并咨询专业人士进行指导。
- 1、下载文档前请自行甄别文档内容的完整性,平台不提供额外的编辑、内容补充、找答案等附加服务。
- 2、"仅部分预览"的文档,不可在线预览部分如存在完整性等问题,可反馈申请退款(可完整预览的文档不适用该条件!)。
- 3、如文档侵犯您的权益,请联系客服反馈,我们会尽快为您处理(人工客服工作时间:9:00-18:30)。
压力管道无损检测
本文由(www.duxingg.com)整理,如有转载,请注明出处。
1.压力管道焊缝外观基本要求
压力管道无损检测前,焊缝外观检查应符合要求。对压力管道焊缝外观和焊接接头表面质量的一般要求
如下:
焊接外观应成型良好,宽度以每边盖过坡口边缘2mm为宜。角焊缝的焊脚高度应符合设计规定,外
形应平缓过渡。
焊接接头表面
(1)不允许有裂纹、未熔合、气孔、夹渣、飞溅存在。
(2)设计温度低于-29度的管道、不锈钢和淬硬倾向较大的合金钢管道焊缝表面,不得有咬边现象。其他
材质管道焊缝咬边深度应大于0.5mm,连续咬边长度应不大于100mm,且焊缝两侧咬边总长不大于该焊缝
全长的10%。
(3)焊缝表面不得低于管道表面。焊缝余高?????? ,且不大于3mm,(为焊接接头组对后坡口的最大宽度)。
(4)焊接接头错边应不大于壁厚的10%,且不大于2mm。
2.表面无损检测
压力管道的表面无损检测方法选用原则:对铁磁性材料钢管,应选用磁粉检测;对非铁磁性材料钢
管,应选用渗透检测。
对有延迟裂纹倾向的焊接接头,其表面无损检验应在焊接冷却一定时间后进行;对有再热裂纹倾向
的焊接接头,其表面无损检验应在焊后及热处理后各进行一次。表面无损检测的应用按照标准要求进行,
其探测对象和应用场合一般如下:
(1)管子材料外表面质量检验。
(2)重要对接焊缝表面缺陷检测。
(3)重要角焊缝表面缺陷检测。
(4)重要承插焊和跨接式三通支管的焊接接头表面缺陷检测。
(5)管道弯制后表面缺陷检测。
(6)材料淬倾向较大焊接接头的坡口检测。
(7)设计温度低于或等于零下29摄氏度的非奥氏体不锈钢管道坡口的检测。
(8)双面焊件规定清根的焊缝清根后检测
(9)当采用氧乙炔焰切割有淬硬倾向的合金管道上的焊接卡具时,修磨部位的缺陷检测。
3.射线检测和超声检测
射线检测和超声检测的主要对象是压力管道的对接接头,以及对焊管件的对接接头。
无损检测方法选用按设计文件规定。对钛、铝及铝合金、铜及铜合金、镍及镍合金的焊接接头检测,
应选用射线检测方法。
对有延迟裂纹倾向的焊缝,其射线检测和超声检测应在焊接冷却一定时间后进行。
当夹套管内的主管有环焊缝时,该焊缝应经营100%射线检测,经试压合格后方可进行隐蔽作业。
管道上被补强圈或支座垫板覆盖的焊接接头,应进行100%射线检测,合格后方可再覆盖。
对规定进行焊接中间检查的焊缝,无损检测应在外观检查合格后进行,射线照相及超声波检测应在
表面无损检测后进行,经检验的焊缝在评定合格后方可继续进行焊接。