模切检验流程及标准
模切检验标准(不良分类)

4. 定义 无
5. 程序 生产部参照《生产过程控制程序》执行; 手工部参照《生产过程控制程序》及各SOP执行; 品保部参照《制程控制程序》《制程检验作业指导书》以及特殊料号SIP执行;
6. 参考文件 6.1《生产过程控制程序》 6.2《制程检验作业指导书》 6.3《制程控制程序》 6.4《产品防护控制程序》 6.5《HSF不合格品之处理(异常处理)管理》
有限公司
页 版 次 次 产品外观检验标准 三级文件 核 审 制 准 核 订 品保部
文件编号 发行日期
1. 目的
制定单位
本指导书规定了产品之外观检验标准及方法,以避免因标准不统一、明确等因素无法满足客户要求;
2. 范围 适用于公司所有成品的生产ቤተ መጻሕፍቲ ባይዱ检、手工全检及品保抽查之检验;
3. 职责 3.1 生产:负责机台生产之成品/包含成品之在线自检; 3.2 生产手工:负责机台生产完后之成品/包含成品手工全检; 3.3 品保:负责机台生产之材料/成品/半成品以及手工全检后产品之巡检抽查;
7. 附表 检附各类别产品外观检验方法和标准
模切检验标准(不良分类)

适用材料 检验工具
所有泡棉类 产品
目视
所有带离型 纸泡棉类产 目视 品
所有泡棉类 产品
目视
所有泡棉类 产品
目视
所有泡棉类 产品
目视
所有泡棉类 产品
目视
所有产品 目视
所有泡棉类 产品
目视
检验方法
判定 结果
取出产品,检查产 品背胶面是否存在 NG 缺胶现象 取出产品,核对产 品离型纸现状是否 NG 与图纸及SOP要求一 取出产品,检查产 品是否存在破损现 NG 象 取出产品,检查产 品是否存在缺胶缺 NG 块现象 取出产品,核对产 品形状是否与图纸 NG 及SOP要求一致 取出产品,对折产 品目视泡棉能否从 NG 底膜上翘起 拿起产品,目视检 测泡棉尺寸是否有 NG 大小边现象. 取出产品,检查产 品是否存在外框未 NG 切断现象
适用材料
检验 工具
所有用背胶 类产品
目视
所有用背胶 类产品
目视
所有用背胶 类产品
目视
所有用背胶 类产品
目视
所有用背胶 类产品
目视
所有带孔类 产品
目视
所有产品 目视
所有胶 类产品
目视
所有胶 类产品
目视
检验方法
判定 结果
取出产品,检查产 品表面是否存在压 NG 痕现象
取出产品,检查产 品胶面是否存在溢 NG 胶现象
适用范围: 五、泡棉类(1/2)
制程及出货 品质控制
缺点别 缺点描述
缺胶
泡棉背胶面无胶
离型纸 未冲断
泡棉离型纸面未冲(切)断
破损
泡棉缺一角或一块
缺角
泡棉缺一角或一块
冲偏(斜) 泡棉形状与实际不符
模切类产品通用检验规范

操作员 工序检验指导书 求的现象;
菲林
案
N/A
2 成形
4、模切或折弯方向要符合图纸、样板; 5、标签产品模切成形时要注意间距、边距符合图纸要求,打印
标签的横边与卷料边缘要保持垂直;
6、模切刀口要保持平整、光滑,不能有变形、毛刺、溢胶等不
良现象;
7、根据要求喷脱模剂,并注意不能污染产品表面;
8、多拼产品成形后要注意排版方式和样板及图纸保持一致;
全检
N/A
终检 FQC
同上
同上
N/A
全检
C=0
6
出货
出货检 验
OQC
同上
同上
N/A
全检
C=0
备注:1、禁止使用存在有害物质污染危险的物品直接接触环保物料/产品表面。2、不同产品必须有清晰的物理隔离和标识,禁止类似产品在同一工作台(区域)检验包
装。
A/0
新增文件
2015/4/修订人
编
制
审核:
:
批准:
首检 PQC 巡检 PQC
同上 同上
同上 同上
同上 同上
首件
N/A
N/A
N/A
文 件
三阶
文件名称:
模切类产品检验规范
文件编号 制订日期 修订日期 版次 页次
序号 检验项目 检验方式 检验员 检验依据/标准
检验内容
检验仪器
抽样方案
判定水准
备注
全检
生产部 检验员
4 全检
样板
1、通过目测、点检规判定表面外观缺陷是否允收; 2、离型纸/膜是否过切?是否方便揭离; 3、背胶是否平整无杂质; 4、保护膜内是否有灰尘、杂质; 5、颜色/纹路/光泽度/透明度是否一致并符合要求; 6、冲裁/模切/排版/卷料方向是否正确
模切检验流程及标准
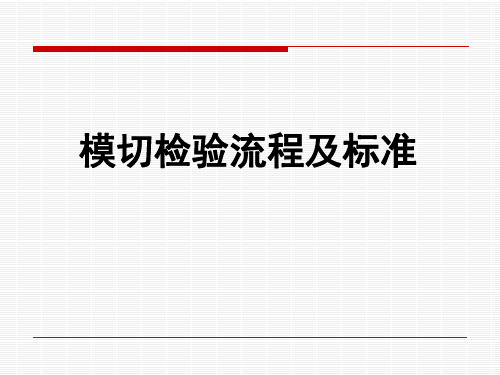
如果平台前后成四角处出现比较严重的压力不均匀现象,则主 要是支撑动平台的四个连杆摆杆高度不一致造成的,此时应打 开模切底座的护罩,检查摆杆是否磨损,如磨损严重则需更换, 否则需要调整四个压力调整斜铁,直到压力一致为止。
模切检验流程及标准
一、模切生产前
1.机长或帮机将产品拉到机台前,准备上纸时,模切PQC看生产工单, 检查标识卡,确认待生产物料为工单要求物料。确认产品保护完 好,无混款现象。
2.检查机台是否拿取资料袋。
二、生产开始时
机长调机生产100PCS-200PCS左右,核对资料袋内容(兰 纸、啤形、内容稿等),减产产品生产效果OK,确认无误后在首 件上签字确认。(具体参照以下首件检验项目)
核对兰纸
核对内容稿
首件签样检验项目
核对兰纸标准位置
核对烫金位置
核对烫金内容
产品成型是否压线
首件签样检验项目
产品成型检查
检查齿刀有无爆裂
有齿刀产品检查齿刀有无不穿或断裂
产品与配套彩盒试装
首件签样检验项目
封套与配套工业版盒试装
签首件
注:不同产品检验项目不同,需要按照资料袋内容和工单要求,及客户特殊要 求进行检验签首件样。
注:签首件时注意产品生产尺寸、产品纸纹方向或坑纹方向,压线饱 满度、是否卡色位,无模切不穿、压线处无掉线,无爆线,掉纸 屑等不良现象
首件签样检是否与啤形相符
核对产品尺寸是否与工单相符
首件签样检验项目
核对坑纹方向/材质是否正确
检查产品压线是否饱满,有无爆线或掉线
手机模切料检测规范
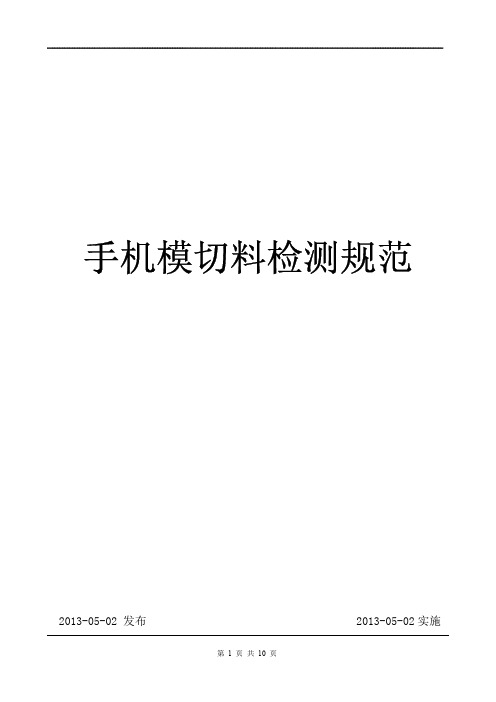
9 冲切不齐
不允许
10 工艺耳(拉手)切断
不允许
11 其它不际效果有出入时,以限度样品为准。
7.3 尺寸要求 a)按图纸要求检测,进料检验时,重点尺寸测量10PCS。 尺寸测量方法:将底纸撕掉,粘贴在平板上面(若是用投影仪测量,需粘贴在透明平板上面。注意一定要贴平整),
测试条件:
环境条件:温度:23c 湿度:55% 辊压条件:辊重:4.5磅 辊速:304.8mm/min (1个来回) 背材:PET膜或铝箔 板材:ASTM标准钢板 拉伸速度:304.8mm/min 判定条件:符合相应牌号规格书要求为合格
7.4.2 动态剪切强度
标准面积的胶带以恒定的速度从试验板材上剪切下来时所需要的力,下为示意图
7.2外观检查要求,见表3 表3
序号
不良项目
规格描述
1
毛边(或拉丝)
L≤0.2mm,视窗区域及摄像头区域不允许明显可视毛边
2 折痕
不允许
3 破裂
不允许
4 色差
轻微允许
5 双面胶未切透
不允许
6 溢胶
不允许
7 底纸冲切不符合要求
标签与模切产品的检验要求

深圳市思达印刷有限公司产品检验规范文件编号:SD-(WF)-53 版本:1.0制定日期:08-2-10制作人:赵刘艳审核人生效日期:08-2-12检验要求客户:伟创力产品系列:印刷标签、模切产品一、规格检验要求All graphic labels or graphics inserts must be inspected and compared to the supplied reference document or to a reference(“gold”)Sample provied 所有图形标签或图形插入必须根据提供的文件或样板要加以核对和比较1. Fixed Graphics Position Tolerance固定图形位公差Use the following tolerances:使用以下偏差:2、Position :+/-0.5mm of the nominal dimension.位置:名义上尺寸+/-0.5mm3、Skew: Maximum 0.5mm per 50 mm linear length.歪斜:每50mm 直线长度最大允许0.5mm4、Orientation: Must be correct orientition.方向:方向必须正确二、条形码的检验要求Printed Label Quality(Thermal Transfer and Laser Printing)标签印刷质量(热转移和激光打印)Requirements for printed bar codes:印刷条码要求:1、Barcodes must be machine readable 100% of the time条形码必须是电脑100 %的可读Barcodes are to meet IPC610D scan Grade B or better条形码要满足IPC610D扫描乙级或更好2、Ink bleeding that causes difficulties to distinguish numbers or letters such as 0,5,6,And 8 is not allowed油墨溢出造成的区分号码或字母诸如区分0,5,6,和8困难是不允许的3、 Printed Lables MUST be “smudge”Proof印刷标签必须是“黑灰”证据SWI recommends the use of white topcoated polyester thermal transfer facedock with a resin based ink ribbon SWI 建议使用白色topcoated聚酯热转移facedock与树脂基油墨丝带The printed lable with barcode or printed information must be able to withstand 16 continuous cycles(approx 5 secs) of being rubbed with firm finger pressure.The lable must not show any sign of smudging ,Bleeding colour or missing colour after this test. Any failure of this test be rejected.印刷标签与条码或印刷资料必须能够经受住以坚定的手指压力16个连续周期(约5秒钟)的摩擦。
模切检验管理及生产科学控制

模切检验管理及生产科学控制------ 主讲:王兆磊一、模切生产的检验控制1.1模切生产前互检1.1.11.机长或帮机将产品拉到机台前,准备上纸时,模切IPQC看生产工单,检查标识卡,确认待生产物料为工单要求物料。
确认产品保护完好,无混款现象。
1.1.2.2.检查机台是否模切图稿与生产工艺单.1.2生产开始时应做好3道检验:首检、巡检、自检1.2.1.首件定义:a.每个工作班、每个工序开始做的第一件或前几件产品;b.一个批次制品开始做的第一件或前几件产品;c.生产设备或工艺装备调整后的第一件或前几件产品(自检合格品)■■■对于大批量生产,“首件”往往是指一定数量的样品。
1.2.2首件检查定义a.对每个工作班、每个工序刚开始或过程发生改变后(如换料、换模版、工艺参数调整等)做的第一件或前几件产品进行的检验;■■■一般要检验连续生产的3-5件产品。
b.在设备或制造工序发生任何变化,以及每个工作班次开始加工前,都要严格进行首件检验。
■■■确认:员工(自查)----主管(确认)---品检员(确认)标识:“首件三检卡”与操作规范,同时挂于“醒目处”作为工作标准。
1.2.3首件检验的要求a.首件检验采用三检制:自检、互检及专检三检制;B.原则上规定送检的产品必须先由操作人员进行“自检”,然后再由班组长或同事进行“互检”,最后由检验员‘专检’,确定合格后方可继续加工后续产品。
C.目前公司实际操作是即对校版后正式生产的第一张产品,按照模切工序的检验标准进行由操作人员进行“自检”全面检查,并由品管人员确认签样。
机长调机生产3PCS-5PCS左右,核对资料袋内容(产品、啤形、内容稿等),检查产品生产效果OK,确认无误后在首件上签字确认。
(具体参照以下首件检验项目)■■■在未确认首件合格以前,对继续生产者要严肃处理!■■■签首件时注意产品生产尺寸、产品纸纹方向或坑纹方向,压线饱满度、是否卡色位,无模切不穿、压线处无掉线,无爆线,掉纸屑等不良现象;■■■不同产品检验项目不同,需要按照资料袋内容和工单要求,及客户特殊要求进行检验签首件样。
模切(自动车)作业标准3
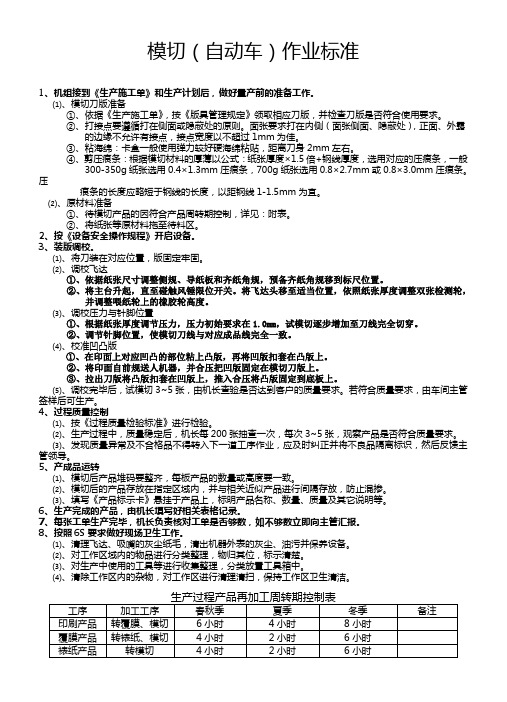
模切(自动车)作业标准1、机组接到《生产施工单》和生产计划后,做好量产前的准备工作。
⑴、模切刀版准备①、依据《生产施工单》,按《版具管理规定》领取相应刀版,并检查刀版是否符合使用要求。
②、打接点要遵循打在侧面或隐蔽处的原则。
面张要求打在内侧(面张侧面、隐蔽处),正面、外露的边缘不允许有接点,接点宽度以不超过1mm为佳。
③、粘海绵:卡盒一般使用弹力较好硬海绵粘贴,距离刀身2mm左右。
④、剪压痕条:根据模切材料的厚薄以公式:纸张厚度×1.5倍+钢线厚度,选用对应的压痕条,一般300-350g纸张选用0.4×1.3mm压痕条,700g纸张选用0.8×2.7mm或0.8×3.0mm压痕条。
压痕条的长度应略短于钢线的长度,以距钢线1-1.5mm为宜。
⑵、原材料准备①、待模切产品的因符合产品周转期控制,详见:附表。
②、将纸张等原材料拖至待料区。
2、按《设备安全操作规程》开启设备。
3、装版调校。
⑴、将刀装在对应位置,版固定牢固。
⑵、调校飞达①、依据纸张尺寸调整侧规、导纸板和齐纸角规,预备齐纸角规移到标尺位置。
②、将主台升起,直至碰触风锤限位开关。
将飞达头移至适当位置,依照纸张厚度调整双张检测轮,并调整喂纸轮上的橡胶轮高度。
⑶、调校压力与针脚位置①、根据纸张厚度调节压力,压力初始要求在1.0mm,试模切逐步增加至刀线完全切穿。
②、调节针脚位置,使模切刀线与对应成品线完全一致。
⑷、校准凹凸版①、在印面上对应凹凸的部位粘上凸版,再将凹版扣套在凸版上。
②、将印面自前规送人机器,并合压把凹版固定在模切刀版上。
③、拉出刀版将凸版扣套在凹版上,推入合压将凸版固定到底板上。
⑸、调校完毕后,试模切3~5张,由机长查验是否达到客户的质量要求。
若符合质量要求,由车间主管签样后可生产。
4、过程质量控制⑴、按《过程质量检验标准》进行检验。
⑵、生产过程中,质量稳定后,机长每200张抽查一次,每次3~5张,观察产品是否符合质量要求。
- 1、下载文档前请自行甄别文档内容的完整性,平台不提供额外的编辑、内容补充、找答案等附加服务。
- 2、"仅部分预览"的文档,不可在线预览部分如存在完整性等问题,可反馈申请退款(可完整预览的文档不适用该条件!)。
- 3、如文档侵犯您的权益,请联系客服反馈,我们会尽快为您处理(人工客服工作时间:9:00-18:30)。
四、模切常见质量问题及解决方法
• 模切散版 所谓散版,是指模切时废边与纸板散开而造成走纸不顺的现象。散 版严重时会影响正常的生产。造成散版主要原因是模切版制版工艺 中的失误和弹性胶条(或海绵)的选择不当;同时,其它因素也可 能造成散版。
–1、模切版制版时,如果活件形状复杂或排列活件很多,而模切连 点很小、很少,则很容易造成模切时散版。此时应适当增加连点数 量,如果可能,应将活件长度方向与纸张传送方向保持一致。
四、模切常见质量问题及解决方法
• 压痕线不规则
– 产生压痕线不规则的原因主要是钢线垫纸上的压痕槽留得太宽, 纸板压痕时位置不定.
模切不良问题
产品纸纹方向错误
模切不良问题
产品爆裂
模切不良问题
爆线
模切不良问题
胶片爆裂
模切不良问题
封套尺寸小
模切不良问题
模切板用错
– 如果压力有轻微的不均匀,可能是由于模切刀、线(钢刀、钢线) 分布不均,造成动平台在模切时受力歪斜所致,此时应在模切版 上加装平衡刀线,使平台受力均匀。
– 如果平台前后成四角处出现比较严重的压力不均匀现象,则主要 是支撑动平台的四个连杆摆杆高度不一致造成的,此时应打开模 切底座的护罩,检查摆杆是否磨损,如磨损严重则需更换,否则 需要调整四个压力调整斜铁,直到压力一致为止。
模切检验流程及标准
一、模切生产前
1.机长或帮机将产品拉到机台前,准备上纸时,模切PQC看生产工单, 检查标识卡,确认待生产物料为工单要求物料。确认产品保护完好, 无混款现象。
2.检查机台是否拿取资料袋。
二、生产开始时
机长调机生产100PCS-200PCS左右,核对资料袋内容(兰 纸、啤形、内容稿等),减产产品生产效果OK,确认无误后在首 件上签字确认。(具体参照以下首件检验项目)
注:签首件时注意产品生产尺寸、产品纸纹方向或坑纹方向,压线饱 满度、是否卡色位,无模切不穿、压线处无掉线,无爆线,掉纸 屑等不良现象
首件签样检验项目
看生产工单
检查是否啤穿
核对产品是否与啤形相符
核对产品尺寸是否与工单相符
首件签样检验项目
核对坑纹方向/材质是否正确
检查产品压线是否饱满,有无爆线或掉线
三、生产过程中和生产完毕
1. PQC每20分钟巡检一次,每次抽检5PCS(手啤300PCS抽5PCS,自动啤1000PCS 抽5PCS) 检查生产过程中产品效果(过程检验参照模切检验指引内容)
2. 生产结束后,确认监督机长做好清线,检查产品是否保护OK。
四、模切常见质量问题及解决方法
• 压力不均匀
核对兰纸
核对内容稿
首件签样检验项目
核对兰纸标准位置
核对烫金位置
核对烫金内容
产品成型是否压线
首件签样检验项目
产品成型检查
检查齿刀有无爆裂
有齿刀产品检查齿刀有无不穿或断裂
产品与配套彩盒试装
首件签样检验项目
封套与配套工业版盒试装
签首件
注:不同产品检验项目不同,需要按照资料袋内容和工单要求,及客户特殊要 求进行检验签首件样。
– 3、钢板不平,模切时压补底过轻/过厚也会导致压力不均匀,过厚会导致啤刀易磨损,
故易产生纸毛现象;过轻,压力偏小,易导致模切不穿。
四、模切常见质量问题及解决方法
• 爆线(爆色) – 爆线是指产品在模切时或成品折叠时,压痕处纸张开裂。这是模 切中经常出现的问题,尤其是在天气干燥的情况下,经常发生。 – 1、纸张脆,含水量低,特别是经过高温磨光的纸张,模切时易爆 线。 – 2、印刷品表面有大面积的蓝或黑等深颜色实地,模切后易爆色、 爆线。 – 3、纸张(板)厚度过大时,容易产生爆线,此时模切钢线高度选 择要合理。 – 4、模切机压力过大时易爆线,此时应减少压力,使废边刚好分离。
–2、如果模切版上的弹性胶条(或海绵)太软,不能顺利弹起纸张, 也会造成散版。此时应选用硬度高、弹性好的优质弹性胶条(或海 绵)
四、模切常见质量问题及解决方法
• 模切时刃口不光滑,甚至起毛
– 1、钢刀质量不良、刃口不锋利、模切适性差是造成刃口不光滑甚 至起毛的重要原因。
– 2、钢刀刃口磨损严重,未及时更换,使钢刀不能正常发挥作用。 应经常检查钢刀刃口的磨损情况,发现磨损严重以至影响模切质 量时,应及时更换新的钢刀。