钣金数控冲加工工艺规范-范文
钣金工艺守则

表1:
mm
料厚
毛刺高
料厚
毛刺高
0.1~0.7
≤0.05
1.9~2.5
≤0.18
0.8~1.2
≤0.08
3~4
≤0.25
1.3~1.8
≤0.12
5 以上
≤0.3
6.6、剪切、裁断的单面间间隙应符合表2 的规定。
表2
mm
材料厚度(t)
单面间隙(Z)
0.25
0.05
0.40
0.07
0.50
0.07
1.00
6.4、剪裁好的半成品或成品按不同规格整齐堆放于指定区域或即时送往 下工位,不可随意乱放,以防止规格混料及受压变形。
4
6.5、为减少刀片磨损,钢板板面及台面要保持清洁,剪板机床台面上严 禁放置工具及其他材料。 6.6、剪切板料的宽度不得小于 20 毫米。 6.7、根据生产批量采取合理的套裁方法,先下大料,后下小料,尽量提 高材料的利用率。 6.8、零件为弯曲件或有料纹要求的,应按其料纹、轧展的方向进行裁剪。
第一部分:剪板机下料工艺守则
文件编号:至美—001
一、 目的
推行作业标准化,提高质量控制意识,降低生产操作错误率及其设备维护
保养,实现开料组快速及规范化作业。
二、 适用范围
五金厨具生产部
三、 内容
1、 场地 2、安全及注意事项 3、材料 4、工艺装备及量具 5、工艺
准备 6、工艺过程及规范 7、质量检查及其发生因素
7
图及指导操作工自检的能力 5.3、按工艺选用压力机。 5.4、检查压力机有无异常状况,各种旋钮(按钮)位置是否正确,打料 装置的位置是否正确,电机开动前离合器一定要处于非工作状态。 5.5、检查压力机滑块配合松紧及与下台面高度调平状况 5.6、给压力机各加油孔加油。 5.7、在安装调整冲模时,一定要使压力机的闭合高度大于冲模的闭合高 度。 5.8、在安装冲模时,找好压力中心,调好间隙,紧固在机床上,在紧固 螺栓时,要注意均衡紧固。模座下的垫板要适当、平整、不得堵塞漏件孔。 为了防止在生产过程中下模座和垫板移动,应垫上纸或砂纸(一般裁料厚 在3 毫米以上,模具比较大时用砂纸)。 5.9、在进行冲压作业前要先开几个行程的空车,检查有无异常音响,当 判定正常后再开始生产。若有异常,则找相关人员维修。 5.10、按工艺要求的顺序和要求调好定位装置(可用试冲零件,专用工 具或常用量具及自制检具检测后调整)。
钣金结构设计工艺规范
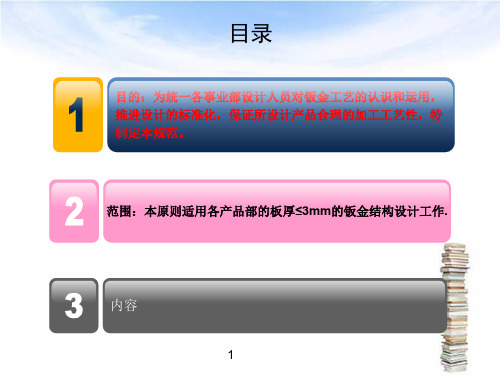
3.台阶加工的处理
对一些高度较低的钣金Z形台阶折弯, 成形长度L不易保证,竖边的垂直度也不 易保证
目前台阶模规格: H=1.8 2.4 3.6 4.2 5.5
9
四.钣金件上的螺母、螺钉的结构形式 1.压铆螺母
名称:花齿压铆螺母 规格型号:S-M3-2
10
8.因目前铝材焊接技术不是很可靠,且焊后工件变形较大,因此建议铝材
零件尽量避免焊接,在满足使用条件下尽量用冷板材料替代。
2
二.孔缺结构设计规范 1.板材上的各种孔优先选用数控冲或冲压通用模具表格上登记的规格(附表)
3
2.对于板厚≤1.5mm的钢板上的螺孔,为获得使用可靠的螺牙,一般采用翻边攻 丝或压铆螺母的方式。 3.折弯件的孔边距一般要求:当加工工序采用先冲孔后折弯时,孔的位置应设 计在折弯变形区外,以避免折弯时孔发生变形,如图应保证孔壁至折弯边的最小 距离为5mm;如特殊需要可先打小孔,折弯后再扩孔。
机架此面不能有焊点凸起
20
2.氩弧焊: 生产效率高,焊点小,主要用于焊接零件各折弯接边(接缝)的加固 连接。
零件各折弯接边(接缝)在图纸上要注明该边上的焊接位置,如折 弯内或折弯外等。
21
3.碰焊: 生产效率高,焊点小,无焊点凸出,但焊点处有微小凹坑。
主要用于焊接较薄(通常为1.0mm以下)零件各折弯搭边叠加一起 的加固连接。
折弯刀 各种厚度材料折弯高H的最小值 与折弯刀槽宽W的大小有关 1.&=0.5mm H=4mm 2.&=1-1.2mm H=5.5mm 3.&=1.5 H=5.5-6mm 4.&=2 H=7mm
5
2.对于二次或二次以上的折弯,经常出现折弯工件与刀具相碰出现干涉, 如下所示黑色部分为干涉部分,这样无法完成折弯,或者因折弯干涉 导致折弯变形,在结构设计时注意避开折弯模。
数控加工工艺规章制度范本
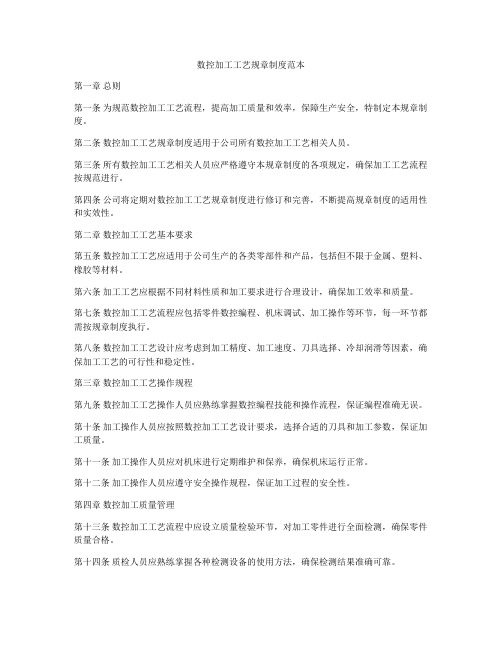
数控加工工艺规章制度范本第一章总则第一条为规范数控加工工艺流程,提高加工质量和效率,保障生产安全,特制定本规章制度。
第二条数控加工工艺规章制度适用于公司所有数控加工工艺相关人员。
第三条所有数控加工工艺相关人员应严格遵守本规章制度的各项规定,确保加工工艺流程按规范进行。
第四条公司将定期对数控加工工艺规章制度进行修订和完善,不断提高规章制度的适用性和实效性。
第二章数控加工工艺基本要求第五条数控加工工艺应适用于公司生产的各类零部件和产品,包括但不限于金属、塑料、橡胶等材料。
第六条加工工艺应根据不同材料性质和加工要求进行合理设计,确保加工效率和质量。
第七条数控加工工艺流程应包括零件数控编程、机床调试、加工操作等环节,每一环节都需按规章制度执行。
第八条数控加工工艺设计应考虑到加工精度、加工速度、刀具选择、冷却润滑等因素,确保加工工艺的可行性和稳定性。
第三章数控加工工艺操作规程第九条数控加工工艺操作人员应熟练掌握数控编程技能和操作流程,保证编程准确无误。
第十条加工操作人员应按照数控加工工艺设计要求,选择合适的刀具和加工参数,保证加工质量。
第十一条加工操作人员应对机床进行定期维护和保养,确保机床运行正常。
第十二条加工操作人员应遵守安全操作规程,保证加工过程的安全性。
第四章数控加工质量管理第十三条数控加工工艺流程中应设立质量检验环节,对加工零件进行全面检测,确保零件质量合格。
第十四条质检人员应熟练掌握各种检测设备的使用方法,确保检测结果准确可靠。
第十五条数控加工工艺流程中如发现加工零件存在质量问题,应及时进行整改和改进,确保质量稳定。
第十六条公司应建立数控加工质量档案,记录每一批加工零件的质量数据,为质量管理提供依据。
第五章数控加工工艺安全管理第十七条数控加工工艺涉及到机床操作等高风险环节,应加强安全管理,确保生产安全。
第十八条加工操作人员应定期接受安全培训和教育,提高安全意识和技能。
第十九条加工操作人员应穿戴符合要求的劳保用品,确保自身安全。
冲压钣金件加工工艺

冲压钣金件加工工艺冲压钣金件是一种常见的工业零部件,适用于各种机械设备中,具有重要的作用。
钣金件加工工艺是制作这种零部件的关键环节,下面就钣金件加工工艺进行详细介绍。
一、冲压钣金件的特点冲压钣金件是采用冲压工艺制作而成的,具有轻质、高强度、精度高、成本低等特点。
在现代工业生产中得到广泛应用,在制造机械设备、电子产品、汽车零件等方面具有重要作用。
二、钣金件加工工艺1、材料准备:冲压钣金件加工需要准备的材料有:一般钢板、不锈钢、铜、铝等。
这些材料的规格和厚度根据工件要求而定。
2、设计图纸:制作每个冲压零件之前,需要先设计出零件的图纸。
设计图纸中需要包括工件的形状、尺寸、工艺要求、成品要求等。
3、数控冲床:数控冲床是冲压钣金件加工中主要的设备。
数控冲床是一种通过程序控制,根据需要的形状和尺寸对材料进行精确冲裁的机床。
数控冲床的工作原理是将材料放在电动滑台和定位销上,用冲床模具对材料进行冲压成形。
4、模具制作:冲床模具是影响冲压钣金件加工效果的重要因素。
一般情况下,制造一个冲孔模具需要经过CAD设计、加工、试模、校正等多个步骤。
5、表面处理:冲压钣金件加工完成后,需要对零件表面进行处理。
一般采用的表面处理方法有热镀锌、镀铬、抛光、油漆等。
三、钣金件加工工艺的优势冲压钣金件加工工艺具有以下优势:1、高效性:冲压钣金件加工速度快,每分钟可以加工数十个工件,生产效率很高。
2、成本低:冲压钣金件加工比其他钣金件加工方式成本更低,每件零件的制作费用更低。
3、精度高:采用数控冲床加工,精度高达0.1mm左右,能够保证工件的精度。
4、稳定性高:通过严格的工艺流程和检测方法确保工件的质量稳定。
总之,钣金件加工工艺在现代工业生产中具有重要的应用价值,只有掌握了这些技术,才能够更好地生产出优质的冲压钣金件,从而为整个工业生产带来更大的效益。
数冲工艺操作规范
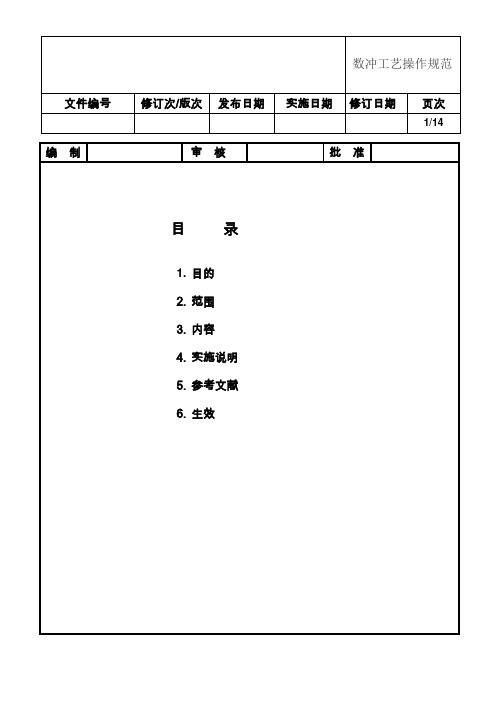
文件编号修订次/版次发布日期实施日期修订日期页次3/141、目的本规范为数控冲床工序提供加工方法的工艺操作指导。
2、范围本规范适用于公司各类钣金产品的生产及质量检验,也可用于指导外购件的验收。
当客户有指定标准时,则以客户标准为准。
3、内容3.1 设备及参数说明数控冲床是一种能够适应产品频繁变化的柔性自动化机床,加工过程所需的各种操作和步骤以及刀具与工件之间的相对位移量都用数字化的代号来表示,通过控制介质(如网络或磁盘)将数字信息送入专用的或通用的计算器,计算器对输入的信息进行处理和运算,发出各种指令来控制机床的伺服系统或其它执行组件,使机床自动加工出所需要的工件或产品。
目前我司现有机床型号有AMADA EM2510NT、AMADA VIPROS357、台励福HPS2500三种。
3.1.1 数冲机床加工范围机床型号X轴行程Y轴行程最大厚度最大工件尺寸AMADA VIPROS-357 1830mm 1270mm 6.35 mm 3660x1270mm AMADA EM2510NT 2500mm 1270mm 3.2 mm 5000x1270mm 台励福 HPS2500 2490mm 1525mm 6.35 mm 4980x1525mm3.1.2 数冲机床夹爪数据3.1.3 数冲机床加工的安全距离当夹爪夹持工件在运动过程中﹐有可能夹爪会被冲到导致损坏﹐因此加工部分和夹爪之间要留出一定的安全距离(详见下表)。
特殊刀具加工时应以实际的上模尺寸为准,必要时可将上模套磨削处理进行避位。
3.1.4 数冲机床刀盘介绍数冲机床的工位在刀盘上的分布一般分为外、中、内三圈,按尺寸分为A 、B 、C 、D 、E 五种类型,一般配置有少数旋转工位。
除了内圈的A 工位外,其它均为有键槽工位。
下图为刀盘实物图。
旋转工位内圈外圈中圈我司三款数控冲床的刀盘工位信息如下表:3.2 数冲工艺要求3.2.1 材料特性与数冲加工的关系影响数冲加工的材料特性是材料塑韧性和材料硬度。
钣金下料工艺流程探讨-加工工艺
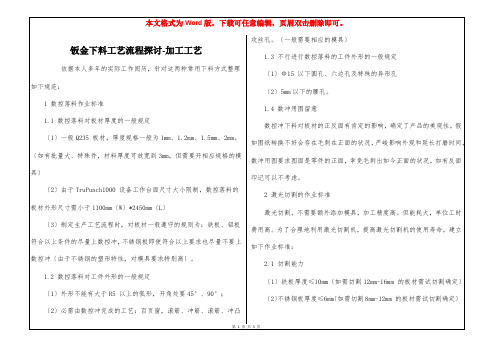
外形简洁的产品应尽可能不上激光切割;批量大、品种单一的产品应 敲落孔预留连接 2mm,不能太大;预留连接点的数量依据敲落孔的尺寸确
考虑不用激光切割。
定;
〔3〕外形冗杂的工件,考虑用激光切割。
2.4.2 激光印记线
〔4〕必需激光和数冲结合的零件,要考虑夹钳和冲头的安全距离〔安
为方便折弯工人折弯及焊接定位,削减工人手工划线,提高。
本文格式为 Word 版,下载可任意编辑,页眉双击删除即可。
钣金下料工艺流程探讨-加工工艺
依据本人多年的实际工作阅历,针对这两种常用下料方式整理 如下规范:
1 数控落料作业标准 1.1 数控落料对板材厚度的一般规定 〔1〕一般 Q235 板材,厚度规格一般为 1mm、1.2mm、1.5mm、2mm。 〔如有批量大、特殊件,材料厚度可放宽到 3mm,但需要开相应规格的模 具〕 〔2〕由于 TruPunch1000 设备工作台面尺寸大小限制,数控落料的 板材外形尺寸需小于 1100mm〔W〕*2450mm〔L〕 〔3〕制定生产工艺流程时,对板材一般遵守的规则为:铁板、铝板 符合以上条件的尽量上数控冲,不锈钢板即使符合以上要求也尽量不要上 数控冲〔由于不锈钢的塑形特性,对模具要求特别高〕。 1.2 数控落料对工件外形的一般规定 〔1〕外形不能有大于 R5 以上的弧形,开角处要 45°、90°; 〔2〕必需由数控冲完成的工艺:百页窗,滚筋、冲筋、滚筋、冲凸
2 激光切割的作业标准 激光切割,不需要额外添加模具,加工精度高。但能耗大,单位工时 费用高。为了合理地利用激光切割机,提高激光切割机的使用寿命,建立 如下作业标准: 2.1 切割能力 〔1〕铁板厚度≤10mm〔如需切割 12mm-16mm 的板材需试切割确定〕 〔2〕不锈钢板厚度≤6mm〔如需切割 8mm-12mm 的板材需试切割确定〕
钣金设计规范及加工工艺(精品)
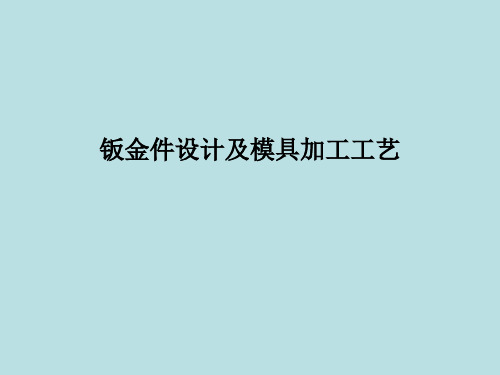
21 CORNER
Bending features
02 BEND
04 CURL
06 OFFSET BENDS
10 HEM
20 TAB
28 U-BEND
Formed features 03 EXTRUDE FORM 07 EMBOSS 08 COINING EDGE 12 LANCE FORM 14 HOOK FEATURE 15 RIB 16 HALF-SHEARING 17 RAISED LETTER ICON 18 DIMPLE 19 STAMPING ICONS 22 CARD GUIDE FORM 23 ROUND HEM 24 EXTRUDED HOLE 25 THREAD FORM 26 GUSSET 27 SPOON
三.鈑金加工設備及相關模具介紹
1.1下料設備--NCT
轉 塔 刀 盤
NCT
NCT
衝孔壓力
200KN
模
板材加工厚度
0.5mm~3.2mm
具
XY軸的加工精度
+/-0.1mm
最大加工板材尺寸
2580mmx1270mm
三.鈑金加工設備及相關模具介紹
ቤተ መጻሕፍቲ ባይዱ
1.2NCT 加工介紹 A. NCT加工半成品排版
B.NCT模具可加工圖元
三.鈑金加工設備及相關模具介紹
2.1 下料設備 --LASER
鐳射頭
噴嘴
切割功率 板材加工厚度 XY軸的加工精度 最大加工板材尺寸
3.0KW 0.1mm~4mm
+/-0.1mm 3000mmx1500mm
三.鈑金加工設備及相關模具介紹
3.1 成形設備----BEND
折 彎 上 模
钣金加工操作规程
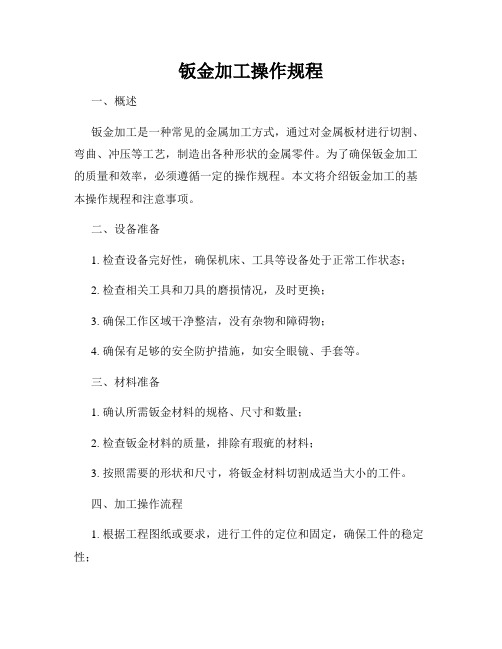
钣金加工操作规程一、概述钣金加工是一种常见的金属加工方式,通过对金属板材进行切割、弯曲、冲压等工艺,制造出各种形状的金属零件。
为了确保钣金加工的质量和效率,必须遵循一定的操作规程。
本文将介绍钣金加工的基本操作规程和注意事项。
二、设备准备1. 检查设备完好性,确保机床、工具等设备处于正常工作状态;2. 检查相关工具和刀具的磨损情况,及时更换;3. 确保工作区域干净整洁,没有杂物和障碍物;4. 确保有足够的安全防护措施,如安全眼镜、手套等。
三、材料准备1. 确认所需钣金材料的规格、尺寸和数量;2. 检查钣金材料的质量,排除有瑕疵的材料;3. 按照需要的形状和尺寸,将钣金材料切割成适当大小的工件。
四、加工操作流程1. 根据工程图纸或要求,进行工件的定位和固定,确保工件的稳定性;2. 根据加工要求,选择合适的刀具和工艺;3. 进行钣金加工操作,包括切割、冲孔、弯曲等;4. 在加工过程中,根据需要对工件进行翻转和调整,确保加工质量;5. 严格按照工艺要求进行加工,确保尺寸和形状的准确性;6. 完成加工后,对工件进行初步的清理、检查和修整。
五、安全事项1. 操作人员必须佩戴安全防护用具,如安全眼镜、手套等;2. 加工过程中,严禁用手直接接触刀具和机床;3. 使用钣金加工机床时,必须熟悉并遵守相关安全操作规程;4. 在使用机床前,必须检查设备的安全保护装置是否完好;5. 若发现设备故障或异常,应及时停机并报告维修人员。
六、常见问题及解决方法1. 切割过程中出现不平整的边缘:检查刀具是否磨损,及时更换刀具;2. 弯曲工艺产生裂纹:检查板材的强度是否符合要求,调整弯曲力度;3. 冲孔孔径不准确:检查冲头尺寸是否正确,冲压力度是否适中。
七、总结钣金加工操作规程对于保证钣金加工质量和效率非常重要。
在操作过程中,必须严格按照设备准备、材料准备、操作流程和安全事项进行操作。
遇到问题时,要及时发现并解决。
只有合理、规范地进行钣金加工操作,才能满足工程需求,提高生产效率。
- 1、下载文档前请自行甄别文档内容的完整性,平台不提供额外的编辑、内容补充、找答案等附加服务。
- 2、"仅部分预览"的文档,不可在线预览部分如存在完整性等问题,可反馈申请退款(可完整预览的文档不适用该条件!)。
- 3、如文档侵犯您的权益,请联系客服反馈,我们会尽快为您处理(人工客服工作时间:9:00-18:30)。
钣金数控冲加工工艺规范-范文
1、模具选择要求:
1.1 模具选择应尽量选择一次可加工完成的模具,以保证加工质量。
(如加工28×28mm切口,可用较小尺寸的方模多次加工,也可选用长方模具加工,但需换刀。
可选用30×30的方模进行一次加工,以减少换刀次数,减小步冲接痕,提高效率和质量)。
1.2 不能一次完成的加工特征,必须选择合适尺寸的模具。
如翻边孔不可一次加工完成,可分成预冲底孔和冲翻边孔两道工步,并且要合理选择模具尺寸。
合理模具尺寸须由设计计算并通过试冲调试得出经验值。
1.3 同一工步的上、下模选择时应选择合理搭配间隙,使用正确下模间隙有以下几点优点:
①延长模具寿命
②推料效果好
③产生毛刺小
④可得到更干净整齐的孔
⑤减少粘料的可能
⑥工件平整
⑦孔的位置更准确
⑧冲孔所需要的冲切力最小。
2、数控冲床加工冲压吨位计算
数控冲床使用模具为无斜刃口冲芯,计算吨位参数名称:冲芯周长(mm)、板材厚度(mm)、材料的剪切强度(kN/mm2)、冲切力(kN)。
换算成公吨:用kN除以9.81。
冲芯周长—-任何形状的各个边长相加材料厚度—-指冲芯要冲孔穿透的板材的厚度。
材料的剪切强度—-板材的物理性质,由板材的材质所确定,可在材料手册总查到。
计算公式:冲芯周长(mm) ×板材厚度(mm) ×材料的剪切强度(kN/mm2)=冲切力(kN) 冲切力(kN)÷9.81=公吨
3、板材数控加工工艺及要求
根据现有自制产品加工要求主要加工工艺有冲圆孔、腰形孔、切边、凸台、压筋、接地标志等。
3.1 冲孔
钣金件常出现成型工艺就是冲圆孔,圆孔大小规格是最多的。
加工的模具规格是按常用性定制的,当某规格频繁使用,将对该规格定制相应的模具。
冲床上最大使用模具规格是Φ76mm,极限规格不推荐使用。
3.2 腰形孔
腰形孔常出现在钣金件中,其主要用途是装配螺丝时预留浮动误差。
新设计图纸时应尽量使用规格的腰形孔,以提高加工质量和加工效率。
常用的腰形孔规格是4.5*10.5mm、3*13 mm、5*12 mm、6*8 mm、8*13 mm、15*25mm。
3.3 切边
切边加工工艺是最常用的加工手段,它主要是分离加工工件和原材料,加工出工件内外轮廓线。
切边加工常使用模具形状有长方形和正方形。
长方形适用于切长边,正方形适用于工件四角及加工内轮廓线。
规格如下:
钣金件要求外观件倒圆,但数控冲床上受到工位数量的限制,不进行倒圆使用倒45o角代替。
3.4 凸台
凸台主要作用是焊接组件时定位,数控冲床加工时需要朝上,保证加工精度。
主要凸台大小是M4、M5。
3.5 压筋
钣金压筋主要是对板材起到加强作用,其作用和焊接加强筋类似,但加强筋使用范围更广,更美观。
压筋工艺加工效率较低,加工过程是以步冲的方法对板材进行冲压。
压筋加工宽度规格有5mm和10mm,加工深度为含板厚5mm。