模具氮化工艺规程
模具氮化及氮化设备
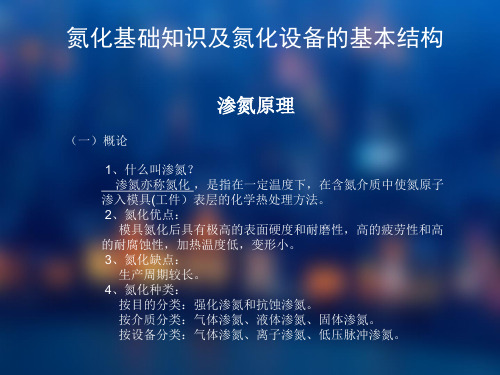
常见问题及预防措施
采用合理的渗氮工艺,避免渗氮层的氮浓度过高,获得 合适的渗氮组织,才能有效提高模具的热疲劳性能。而 不当的渗氮工艺所产生的低劣渗氮层,反而会导致模具 的早期失效。
2、H13模具渗氮层由白色化合物和黑色扩散层组成。 化合物层存在ɛ相,ý相和弥散分布的CrN,Mo2N,VN相。黑 色扩散层存在含氮ý相,脉状氮化物及弥散分布的 CrN,Mo2N,VN相。脉状组织是合金元素和氮原子在原奥氏 体金界偏聚形成合金氮化物。合理控制渗氮时间、温度 和氮势,脉状组织可减少为细小颗粒状。
预防及补救措施
(3)根据工艺试验确定各个阶段的氨分解率,确定 各个阶段保温时间。
常见问题及预防措施
缺陷特征 产生原因
(1)炉温过高,氨含水高 渗氮层出现网状或 波纹状氮化物或针 状鱼骨状氮化物 (2)氨应脱水充分,干燥剂更换或再生 (2)材质晶粒粗大,脱碳层未去除 (3)严控热处理工艺,实行无氧化加热 (3)工件有棱边锐角 (4)避免棱边和锐角 (1)更换氨干燥剂或干燥剂再生 (1)液氨含水量高 (2)表面脱碳层未去除掉 (3)氨分解率过低 (4)退氮处理不当,时间不足 (5)零件表面粗糙有锈蚀 表层脆性过大表面 起泡剥落 (6)原材料带状组织及非金属夹杂物严重 (7)尖角、表层处形成波纹状氮化物或网 状氮化物 (8)白亮层太厚 (9)渗氮层深度不均匀 (2)加大模具加工余量,表面不得有脱碳、贫碳 (3)按技术要求进行退氮处理,降低含氮量 (4)挽救方法:凡不因表面脱碳而引起的脆性可以退氮 处理,允许表面有氧化色,可在空气中冷却,加工余量大 时,可磨掉一些化合物层 (5)将零件清理干净 (6)通过预先热处理,消除原材料缺陷 (7)选用合格原材料 (8)零件尽量采用圆角或倒角 (9)带试样检查,调整工艺参数 (10)保证装炉间隙使炉气畅通、温度均匀
肇庆氮化处理技术要求

肇庆氮化处理技术要求
肇庆氮化处理技术主要应用于金属制品的表面强化处理,提高金属制品的硬度、耐磨性和耐腐蚀性。
氮化处理技术的要求如下:
1.氮化处理应按照制品的要求进行处理,控制氩气、氮气等气氛组成、温度、时间等处理参数。
2.制品应经过清洗、退火等预处理,并在处理前进行质量检验。
3.加工件的表面应光洁无油污,不得有明显的划痕、裂纹和氧化层等缺陷。
4.氮化处理后的制品应经过除渣、清洗等工艺进行表面处理。
5.应保证处理温度、时间、气氛等指标符合技术标准要求,且不得炉膛气氛变化、炉内温度不均等现象。
6.氮气氛处理时应尽量避免铁及其合金部件与不锈钢及钴基合金部件共同处理。
7.处理后的制品应进行硬度、耐磨性和耐蚀性等检测,确保符合相关技术标准的要求。
8.出厂前应进行产品质量鉴定,确保按照要求进行表面强化处理。
模具渗氮处理

模具渗氮处理2011-07-04 16:34渗氮常称为氮化,就是将工件放在含氮介质中,加热到较低温度(480~600℃),使氮渗入其表面,形成以氮化物为主的渗层。
有些钢种的氮化层硬度高达1000~1200HV,渗后不必进行提高硬度的淬火处理。
氮化层的高硬度是因高硬度氮化物弥散分布在基体中所造成的,随渗氮温度温度升高,氮化物片厚度增加,与母相的共格关系开始破坏,硬度降低。
氮化层的耐磨性远高于渗碳层,渗氮工件的变形小,处理后不再进行加工就可以使用,高精度的工件也只需要精磨、研磨或抛光。
在渗氮层中形成大的残余压应力,有利于提高零件的疲劳强度。
渗氮温度一般稍代于淬火钢的回火温度范围。
调质状态的结构钢渗氮时,工件心部保持了状态的回火索氏体组织,在得到高硬度表面的同时具有良好的综合力学性能。
氮化层具一定热硬性,在500℃以下能长时期保持高硬度。
在600℃短时间加热,硬度也不降低,而当温度超过600~625℃时,由于高弥散分布的氮化物的聚集,而使氮化层硬度下降。
为了工件心部具有必要的力学性能,渗氮前一般要进行调质处理,获得回火索氏体组织。
渗氮往往是最后一道工序,因而氮化前要求加工到足够的精度,为了消除加工应力和减少渗氮过程的变形,一般在机械加工后要进行1、2次除应力回火。
根据渗氮的目的,可分强化渗氮(硬渗氮)和抗蚀渗氮,对要求表面硬度高、耐磨性好、热处理变形小的高精度工件,多采用强化渗氮,如精密机床的主轴、镗床的镗杆、发动机缸套、液压泵的分配轴等。
为了提高碳钢、合金钢、塑料模具钢及电工钢工件的抗蚀能力,则对其进行抗蚀渗氮。
抗蚀渗氮适用于对抗蚀性要求不太高的小零件,如仪表、打字机、缝纫机的零件。
抗蚀渗氮是在工件表面获得0.015~0.06mm厚的致密的、化学稳定性好的ε相渗氮层。
对潮湿空气、过热空气、海水、气体燃烧产生的气体具有一定耐蚀能力。
抗蚀渗氮温度比强化渗氮的温度高(550~650℃),渗氮后可以快冷。
渗氮用钢中常加入铬、钼、钨、钒、钛、铝等形成稳定氮化物的元素。
氮化

3.锻工热处理车间在氮化时必须遵守本工艺守则,车间检查站也应按本工艺守则进行检查。
二、氮化前准备
1.所有氮化零件,必须经过调质处理,调质处理按锻件与圆钢件调质热处理工艺守则 (75.14.107)进行。锻件在调质处理前须按锻件热处理工艺守则(75.14.106)进行正火。
2.零件在装炉过程中要注意轻拿轻放,避免零件表面碰伤或产生划痕。
3.氮化零件的装炉量一般不宜过满,要保证分解氨在密封箱内的流通,对阀杆的数量要求炉量不大于300根,且要保证一定间隙。
4.35#钢抗腐氮化时,每箱装2个脆性试样和4个金相试样,金相试样在四个角上。38CrMoAlA钢抗腐氮化及硬化氮化时,每箱装放4个金相试样,放置位置同上。
4.不同产品氮化规范如下:
钢号
种类
一段
二段
三段
温度±10℃
保温时间
分解度%
温度±10℃
保温时间
分解度%
温度±10℃
保温时间
分解度%
35#
抗腐
620
9
50~60
38CrMoAlA
抗腐
560
8
45~55
38CrMoAlA
硬度
530
10
20~30
560
16
50~60
530
6
20~30
5.氮化结束后,停电、继续通入少量氨气,当氮化箱冷至抗腐≤200℃时可关闭氨气,取出氮化零件。
黑龙江北方阀业有限责任公司
氮化技术条件
HBF02-06-07
(代替:HG75.14.108)
受控号:01
编制:张乃波 审核:孟海川 批准 :于庆忠
氮化炉安全操作规程标准范本
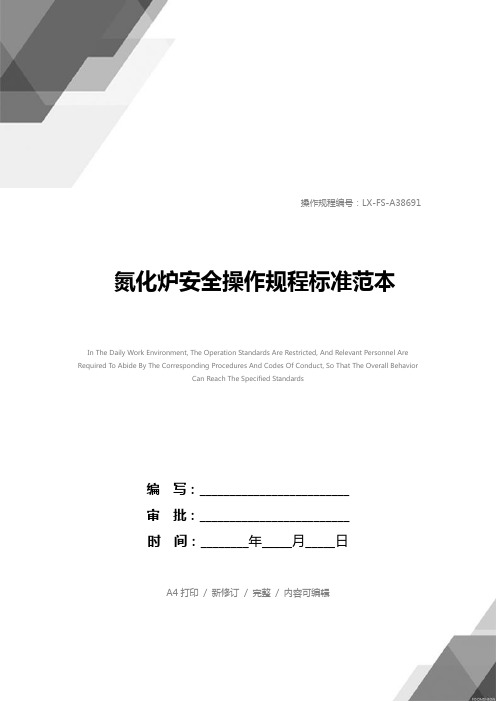
操作规程编号:LX-FS-A38691 氮化炉安全操作规程标准范本In The Daily Work Environment, The Operation Standards Are Restricted, And Relevant Personnel Are Required To Abide By The Corresponding Procedures And Codes Of Conduct, So That The Overall BehaviorCan Reach The Specified Standards编写:_________________________审批:_________________________时间:________年_____月_____日A4打印/ 新修订/ 完整/ 内容可编辑氮化炉安全操作规程标准范本使用说明:本操作规程资料适用于日常工作环境中对既定操作标准、规范进行约束,并要求相关人员共同遵守对应的办事规程与行动准则,使整体行为或活动达到或超越规定的标准。
资料内容可按真实状况进行条款调整,套用时请仔细阅读。
1、清洗模具(1)把模具放入浓度为6%的盐酸中浸10分钟左右,用铜刷洗净再用清水清洗。
(2)用酒精洗模具的工作带(3)等水气干了再装入炉内2、升温通NH3,调节NH3流量,并注意炉内压力的变化及时调整排气闸,使U形压力计保持平衡稳定。
3、NH3瓶减压闸输出压力不超过0.4Mpa,否则会使气爆裂,应保持在0.2Mpa左右。
4、氮化时要注意控制好温度,使炉内温度绝对不超过580℃,否则会造成整炉工作件扔废。
5、调节NH3流量计的原则,水测瓶水位偏多,说明炉内NH3过量,应减少NH3流量,反之,则增加NH3流量,使之符合氮化要求。
6、工作出炉温度应在150℃以下。
7、经常检查炉子排气管有无堵塞及泄露。
8、退氮,在平常使用时,由于炉罐长期渗氮,产生过剩,一般在使用5-7炉后,进行一次退氮,温度加温在700℃左右,不能NH3保温8小时,再降温正常温,退氮时再放入一些碎铁片最佳。
模具氮化工艺操作规程
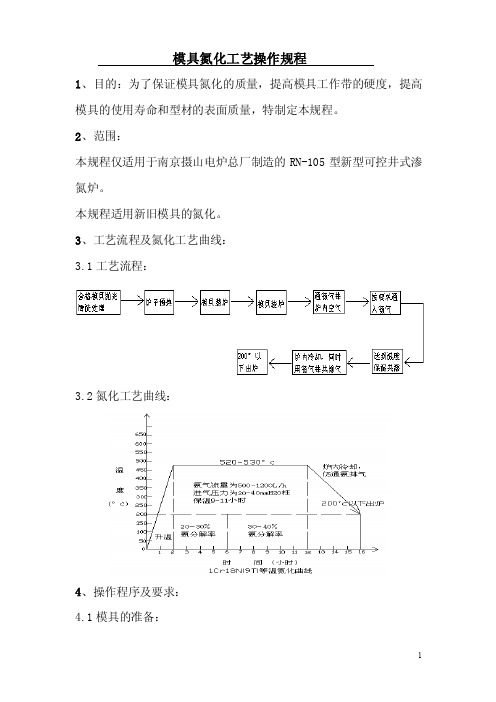
模具氮化工艺操作规程1、目的:为了保证模具氮化的质量,提高模具工作带的硬度,提高模具的使用寿命和型材的表面质量,特制定本规程。
2、范围:本规程仅适用于南京摄山电炉总厂制造的RN-105型新型可控井式渗氮炉。
本规程适用新旧模具的氮化。
3、工艺流程及氮化工艺曲线:3.1工艺流程:3.2氮化工艺曲线:4、操作程序及要求:4.1模具的准备:4.1.1新模具必须经试模合格,模具的型腔内各部位必须抛光,去掉碱垢和尖角,过渡部位要圆滑,未经处理的模具不准氮化。
4.1.2使用过的模具要按4.1.1的要求进行检查,并要重点检查桥位部分和棱角处有无裂纹,确认无误后方能重复氮化处理。
4.1.3模具表面应清洁、无油污、锈蚀和其它脏物,工作带可用酒精或汽油或香蕉水清洗干净,否则不准入炉氮化。
4.2设备气密性检查:氮化前应对加热炉、氮化罐和整个氮化系统的管道接头处进行气密性检查,保证氨气不漏和在管路中畅通无阻。
氨气对人体健康危害极大,空气中氨的含量达10-25%时,遇到火会引起爆炸。
漏气的检查办法时用酚酞试纸浸湿后放在怀疑的漏气处,试纸变红就证明漏气。
4.3炉体和温控系统检查:开炉前必须检查炉体、炉腔、炉盖、升降系统、循环风机、电气控制系统、温控系统、测温系统等是否稳定、可靠、灵活;进气管、出气管、水冷系统、氨气瓶阀门等是否正常完好。
4.4氮化过程的操作:4.4.1将模具吊入氮化罐内,封闭炉盖。
4.4.2把氨气瓶中的液氨经过减压阀,通过氨气干燥柜通入炉内,将炉内的空气排出。
时间为15分钟,氨气的压力为0.2MPα以下。
4.4.3通电升温,炉温升到100℃时,打开冷却水阀。
当炉温升到200-250℃时,保温0.5-1小时,并开动循环风机,将氮化罐和管道中的空气充分排出。
当罐内氨的分解率为零时允许继续升温。
这时可降低氨气流量,保证炉内正压,保证模具不被氧化。
4.4.4当炉温升到450℃左右时,要控制升温速度,同时,应加大氨气流量,使分解率控制在20-30%左右,迅速提高模具表面氮化的浓度。
模具制定工艺规程的具体步骤
模具制定工艺规程的具体步骤装配工艺过程:压入导柱--装导套--压入导套--检验。
1)对零件图进行工艺分析电火花线切割加工型孔工艺过程:(1)毛坯准备(2)刨六面,将毛坯刨成六面体(3)磨上下平面及角尺面(4)钳工划线、并加工销孔和螺钉孔(5)去型孔内部废料(6)热处理(7)平磨上下两面和角尺面(8)电火花线切割加工型孔(9)将加工好的凹模进行稳定回火(10)钳工研磨销孔及凹模刃口,使使型孔达到规定的技术要求。
加工阶段划分:粗加工阶段、半精加工阶段、精加工、光整加工阶段。
/划分目的:保证加工质量、合理使用设备、便于安排热处理。
对刀点:当用夹具时常用与工件零点有固定联系尺寸的圆柱销等进行对刀,则用对刀点作起刀点。
定位:块规角尺定位法、十字划线定位法、定位板定位法。
19、记住数控程序常用的指令代码:G01G02G03G17~19G40~44G90~91万能夹具组成:正弦头、尾架、底座、十字托板(由一双相互垂直的精密丝杆螺母副组成)电极丝初始位置确定:目视法(基准面法、十字基准线法);电阻法。
D、量具的选择:单件小批量使用通用量具;大批使用量规和高生产率的专用检具。
35、电火花线切割机床组成:床身、坐标工作台、运丝机构、工作液循环系统、高频脉冲电源、数字程序控制系统。
10、零件的加工精度包括:尺寸精度、形状精度和位置精度。
1)对产品装配图和零件图的分析与工艺审查正弦精密平口钳:可用于加工平面、斜面、刚性较大的材料。
加工顺序的安排:先粗后精,先主后次,基准先行,先面后孔。
)3)工序卡片:工序加工过程所必须的工艺资料。
7)数值计算工艺方法:a、单电极平动加工法(先高效低损耗电规准进行粗加工--依次改变电规准,加大平动量--最后使用的电极加工规准小,损耗量小)。
正弦分中夹具主要组成部分:正弦头、尾架、底座。
B、夹具的选择:单件小批量生产应尽量选用通用夹具;大批量使用专用夹具。
34、线切割与成形加工相比的特点:a、不需要制专用电极,电极丝可反复使用,成本低。
氮化炉的安全操作规程
氮化炉对各类工件进行处理,处理完的工件变形小、耐磨、耐疲劳,氮化炉的氮化工艺通常是往不锈钢真空密封罐中通入氨气。
氮化炉在使用的过程中,要注意正确合理地操作,因为具有一定的危险性,下面就由南京东升带大家看看氮化炉的安全操作规程。
1、目的明确氮化设备的操作要求,避免设备安全事故和因设备原因而造成的质量事故。
2、适用范围适用于对氮化生产设备的操作控制3、职责3.1 氮化工每天巡查设备状况,指导和监督作业人员按要求作业3.2 氮化工经岗前培训后严格按照本作业指导书的要求作业4、氮化炉操作规程4.1 主要用途:通过液氨加热、风压等工序,使氨获得分解,从而达到提高模具硬度的效果。
4.2 主要技术参数至高允许温度:700℃电压:380V功率:75±10%KW质量:3900kg4.3 操作人:氮化工4.4 操作前的检查项目及准备工作4.4.1 当电炉与控制柜全部就位安装完毕,经专业人员确认无误,并且各项机械、电气、水管、氨气进出管、热电偶、温度仪表经逐项验收并进行了必要的试运转后,才能开始烘炉使用。
4.4.2 了解电路控制柜、仪表等的基本构造及工作原理,熟悉电炉的气线路、氨气管、进出水管、控温系统的布置情况。
4.4.3 保持控制柜的清洁整齐,不允许在其上面放置重物、脏物。
4.4.4 检查风机轴承的水冷与润滑油,确保其不缺油干燥。
4.4.5 检查冷却水管道、氨气介管道和排气管道是否通畅。
4.4.6 检查氨气管道接口,不得有漏气现象。
4.4.7 检查电器线路是否正常;密封圈是否有弹性,无弹性需更换新圈。
4.48 做好[可控井式氮化炉运行日报表]4.5 操作及注意事项4.5.1 切断电源,停止供氮。
4.5.2 打开炉盖,用行吊吊入模具料框,确保料框与炉胆之间的间隔均匀。
4.5.3 关闭炉盖,使密封硅胶圈压入炉子凹槽内,旋紧紧固扳手,压紧炉盖,使之不漏气。
4.5.4 旋开氨瓶高压阀,使压力调至0.4-1.0Mpa,再旋开低压阀,使工作压力调至0.2-0.4Mpa.4.5.5按工艺调仪表设定按钮4.5.6 按工艺规定输入指令,并检查指令是否正确,将手柄调到自动位置,通电升温。
模具氮化工艺规程
模具氮化工艺操作规程
一、范围
1、明确氮化操作规定要求,确保模具氮化质量。
2、适用于模具的氮化处理。
二、操作规程
1、操作前设备检查。
1)在氮化前检查冷却水管道、氨分介管道和排气管道是否畅通。
2)检查氨气管道接口,不得有漏气现象。
3)检查电器线路是否正常;密封圈有否弹性,无弹性需更换新
2、氮化前工件准备:工件在氮化前需清洗干净,程序为:用铁钩勾销孔放入酸中,时间参看工艺,拿出后用砂纸或刷子边洗边冲干净。
洗净后,在水中浸泡5分钟,出水用布抹干,浸入酒精中,出酒精吹干。
3、装框
工件分大小模入框,一般为竖放模具,间隙为≥10mm,注意小心轻放,最上格与最下第二格分别吊上一试样,模具放完后,用铝丝加固,防止模具在吊运中撞落损坏,用吊机把框架吊入炉中,放油阀下炉盖压紧压柄。
4、氮化
1)氨气为1~1.5Mpa,开减压阀0.8~0.12Mpa。
2)按工艺要求设置温度,操作仪表键盘见参考说明书。
3)到保温时间后,每半小时测量一次。
4)保持炉内压力在工艺范围内,如果超出应调节进出气阀门。
5)注意氨流量,不能变化太大。
6)整个氮化过程中,一定要保证冷却水供应,遇到停水须向上级部门反映,迅速排除故障。
5、降温:氮化结束关闭升温开关,按工艺减少氨流量及炉内压力,半小时后开鼓风机,注意打开进出风口。
6、出炉:炉内温度降至180℃以下,关氨气总阀,放松压柄,开炉盖,用吊机吊出模框,待冷至50℃以下取下试样,交试验员待检,模具从框中取出,转运模具仓。
1。
氮化基本原理及操作指南
氮化基本原理及操作指南氮化基本原理及操作指南(仅供参考)一、概论:1、氮化就是把氮渗入钢件表面,形成富氮硬化层的化学热处理过程。
2、氮化处理:氮化处理是利用氨在一定温度下(500-600℃),所分解的活性氮原子向钢的表面层渗透扩散而形成铁氮合金,从而改变钢件表面机械性能(增强耐磨性,增加硬度,提高耐蚀性等)和物理、化学性质。
3、氮化过程:氮化共有三个过程:(1)氨的分解随着温度的升高,氨的分解程度加大,生成活性氮原子。
2NH3→6H+2[N](2)吸收过程钢表面吸收氮原子,先溶解形成氮在α-Fe中的饱和固溶体,然后再形成氮化物。
2mFe+2[N]→2FemN(3)扩散过程氮从表面饱和层向钢内层深处进行扩散,形成一定深度的氮化层。
二、工件如何进行氮化1、组织准备氮化工件在氮化前,必须具有均匀一致的组织,否则氮化层质量不高,通常都是采用调质、(淬火)处理来作为预备热处理。
2、气密性检查氮化前应对加热炉、氮化罐和整个氮化系统的管道接头处进行气密性检查,保证氨气不漏和在管路中的畅通无阻。
3、工件工作面的抛光清洁要求氮化的表面要经过认真的打磨抛光(像镜面一样)及仔细的检查,氮化表面应无油迹、锈蚀、尖角、毛刺、碰伤和洗涤不掉的脏物,对于非氮化面要检查防护镀层是否完整。
要氮化前清洗零件≤2小时,先用干净棉纱擦净油污,再用汽油、酒精或四氯化碳等清洗,也可用稀盐酸或10%碳酸钠(Na2CO3)沸腾的溶液中去油,一般在溶液中煮沸8一10分钟,然后用清水反复洗涤。
另外组织吹干、擦干。
装炉时,对于易变形零件,如杆件,最好垂直吊挂在罐中。
4、防止工件局部氮化有些工件某些部位不需要氮化,可以用以下几种方法加以防止。
(1)镀金属法a,b(略)(2)涂料法a,b,c,d(略)5、通入氨气前应注意事项(1)氨气(液氨):要求水、油总含量≤0.2%,氨(NH3)含量≥99.8%。
(2)保证氨的充足供应量,以利氮化(每公斤液氨每小时可使工件表面积氮化15平方米)。
- 1、下载文档前请自行甄别文档内容的完整性,平台不提供额外的编辑、内容补充、找答案等附加服务。
- 2、"仅部分预览"的文档,不可在线预览部分如存在完整性等问题,可反馈申请退款(可完整预览的文档不适用该条件!)。
- 3、如文档侵犯您的权益,请联系客服反馈,我们会尽快为您处理(人工客服工作时间:9:00-18:30)。
模具氮化工艺操作规程
一、范围
1、明确氮化操作规定要求,确保模具氮化质量。
2、适用于模具的氮化处理。
二、操作规程
1、操作前设备检查。
1)在氮化前检查冷却水管道、氨分介管道和排气管道是否畅通。
2)检查氨气管道接口,不得有漏气现象。
3)检查电器线路是否正常;密封圈有否弹性,无弹性需更换新
2、氮化前工件准备:工件在氮化前需清洗干净,程序为:用铁钩勾销孔放入酸中,时间参看工艺,拿出后用砂纸或刷子边洗边冲干净。
洗净后,在水中浸泡5分钟,出水用布抹干,浸入酒精中,出酒精吹干。
3、装框
工件分大小模入框,一般为竖放模具,间隙为≥10mm,注意小心轻放,最上格与最下第二格分别吊上一试样,模具放完后,用铝丝加固,防止模具在吊运中撞落损坏,用吊机把框架吊入炉中,放油阀下炉盖压紧压柄。
4、氮化
1)氨气为1~1.5Mpa,开减压阀0.8~0.12Mpa。
2)按工艺要求设置温度,操作仪表键盘见参考说明书。
3)到保温时间后,每半小时测量一次。
4)保持炉内压力在工艺范围内,如果超出应调节进出气阀门。
5)注意氨流量,不能变化太大。
6)整个氮化过程中,一定要保证冷却水供应,遇到停水须向上级部门反映,迅速排除故障。
5、降温:氮化结束关闭升温开关,按工艺减少氨流量及炉内压力,半小时后开鼓风机,注意打开进出风口。
6、出炉:炉内温度降至180℃以下,关氨气总阀,放松压柄,开炉盖,用吊机吊出模框,待冷至50℃以下取下试样,交试验员待检,模具从框中取出,转运模具仓。
1。