模具加工工艺规程
模具典型零件的加工
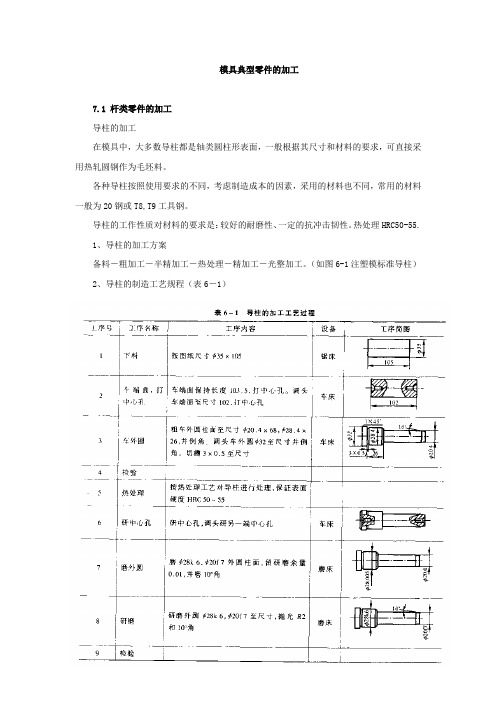
模具典型零件的加工7.1 杆类零件的加工导柱的加工在模具中,大多数导柱都是轴类圆柱形表面,一般根据其尺寸和材料的要求,可直接采用热轧圆钢作为毛坯料。
各种导柱按照使用要求的不同,考虑制造成本的因素,采用的材料也不同,常用的材料一般为20钢或T8,T9工具钢。
导柱的工作性质对材料的要求是:较好的耐磨性、一定的抗冲击韧性。
热处理HRC50-55.1、导柱的加工方案备料-粗加工-半精加工-热处理-精加工-光整加工。
(如图6-1注塑模标准导柱)2、导柱的制造工艺规程(表6-1)导柱的加工工序不是固定不变的,根据不同的生产类型、结构形式和尺寸精度、工厂设备情况,其工序的划分和工艺方法也就不同。
3、导柱加工过程中的定位一般采用设计基准和工艺基准重合的原则,在两端加工中心孔,以两中心孔轴线为各工序的定位基准,中心孔的形状和精度对导柱的加工质量有着直接的关系。
为了确保精加工时的精确定位作用,中心孔在热处理后必须进行对研和修整。
对研中心孔一般采用锥形砂轮或梅花顶尖:4、导柱的研磨一般对于配合精度要求较高的导柱,都要安排研磨工序,以提高表面质量和降低粗糙度。
二、模柄与顶杆的加工模柄的设计已标准化,常用的模柄有:压入式、旋入式、凸缘式、槽形式和浮动式等,和顶杆一样都属于台阶轴类零件,材料选用45钢,热处理HRC40-45,这类零件一般也是采用中心孔作为精加工的定位基准,终加工采用精磨工艺并靠磨端面,保证端面跳动要求。
7.2 套类零件的加工模具中的套类零件主要有:导套、护套和套类凸模等。
导套的材料和导柱一样,一般采用圆钢下料,热处理要求为HRC58-62,制造工艺也不是固定的。
导套的加工方案:备料-粗加工-半精加工-热处理-精加工-光整加工。
7.3 板类零件的加工一、板类零件加工质量的要求模具中各种板类零件较多,如:模座、垫板、固定板、卸料板、推件板等等。
虽然形状、材料、尺寸精度和使用性能要求各不相同,但都是有平面和孔系组成,这类零件的加工质量要求主要有以下几点:①平行度和垂直度要求,一般均按GB1184-80的规定,具体公差执行冷冲模和塑料模的有关国家标准。
第1章 模具制造工艺规程

第1章模具制造工艺规程1.1 模具制造工艺规程编制的基本概念1.1.1生产过程与工艺过程1.生产过程制造模具时,将原材料或半成品转变成为成品的各有关劳动过程的总和称为生产过程。
具体地讲,模具制造是在一定的工艺条件下,改变模具材料的形状、尺寸和性质,使之成为符合设计要求的模具零件,再经装配、试模和修整而得到整副模具产品的过程。
广义的模具生产制造过程还应包括生产技术准备、模具零件加工和模具装配等阶段。
(1)生产技术准备生产技术准备阶段的主要任务是分析模具图样,制订工艺规程;编制数控加工程序;设计和制造工装夹具;制定生产计划,制定并实施工具、材料、标准件等外购和零件外协加工计划。
各种生产服务活动如生产中原材料、半成品和工具的供应、运输、保管以及产品的包装和发运等。
(2)模具零件加工在模具零件加工中,加工的工艺方法非常多,基本可以概括为:1)传统的切削加工,如车、钳、刨、铣、磨等;2)非切削加工,如电加工加工、冷挤压、铸造等;3)数控加工,如数控铣削、加工中心加工等;4)焊接、热处理和其它表面处理等。
根据模具零件的分类加工对象可以分为两种:1)非成形零件加工,结构零件类零件加工。
这些零件大多具有国家或行业标准,部分实现了标准化批量生产。
在模具工艺规划中,根据设计的实际要求和企业的生产实际可选择外购或由本企业加工。
2)成形零件加工,型腔类零件的加工。
如注射模具的成形零件一般结构比较复杂,精度要求高,有些模具型腔表面要求有纹饰图案。
其加工过程主要由成形加工、热处理和表面加工等环节构成。
特种加工、数控加工在模具成形零件加工中应用非常普遍。
(3)模具装配模具装配是根据模具装配图样要求的质量和精度,将加工好的零件组合在一起构成一副完整模具的过程。
除此之外,装配阶段的任务还有清洗、修配模具零件,试模及修整等。
由上述过程可以看出,模具产品的生产过程是相当复杂的。
为了便于组织生产和提高劳动生产率,现代模具工业的发展趋势是自动化、专业化生产。
模具制造工艺规程的编制
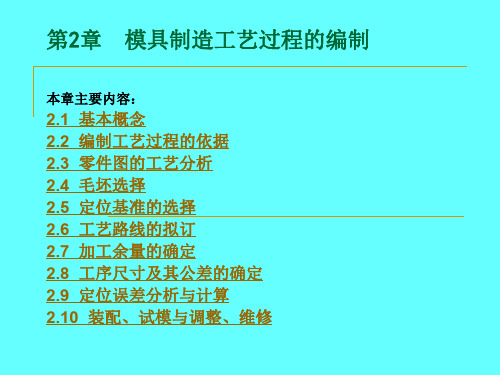
(5)保证工件定位准确、夹紧可靠、操作方便的原则
一、模具制造的生产过程
模具的生产过程,是指将用户提供的产品信息和制件的技术信息 通过结构分析、工艺性分析,设计成模具;并基于此,将原材料经 过加工、装配,转变为具有使用性能的成型工具的全过程。
原材料的 运输、存放
生产准备
毛坯制造
机加工、热
装配
处理
试模
包装、入库
具体地说,模具生产过程分以下六个阶段:(1)模具方案确 定 (2)模具结构设计 (3)生产准备 成型件材料、模块等坯 料加工;标准零、部件配购;根据造型设计,编制NC、 CNC加工代码组成的加工程序;以及刀具、工装等。 (4)模 具成型零件加工 (5)装配与试模 (6)验收与试用。
2. 模具工艺文件的编制
模具工艺规程包括加工工艺规程、装配工艺规程和检 验工艺规程三部分。生产中常以工艺过程卡和工序卡来指 导、规范生产。
编制工艺规程的步骤:
1. 分析研究模具装配图和审查零件图; 2. 确定生产类型;(单件或成批生产)
3. 确定毛坯种类和尺寸; 4. 拟定工艺路线;(定位基准和加工方法)
二、工艺规程编制的原则与依据
1.工艺规程编制的原则 在一定的条件下,以最简便的方法、最快的速度、最少
的劳动量和最少的费用,可靠地加工出符合图纸各项要求 的零件。
2.工艺规程编制的依据
根据必要的技术资料,生产计划(周期、进度、数量), 本厂的生产条件(设备、工人技术水平、生产场地、起重 运输等),结合需要的可能性,因地制宜地全面考虑。
二、模具制造工艺过程及其组成
模具制造工艺过程定义为:直接改变生产对象的形状、尺 寸、相互位置及性能,将其转变为成品或半成品的过程。它是 模具生产过程的主要部分,即从生产准备到验收、试模合格之 前,属于制造工艺过程。
模具高效加工方法与工艺规程制定
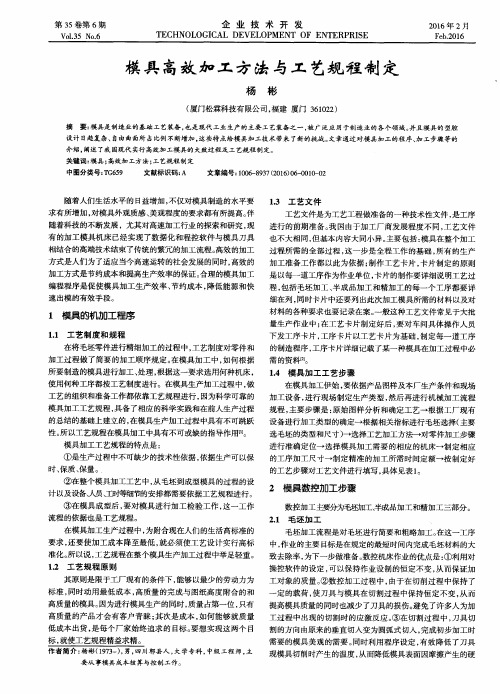
进行准确定位一 选择模具加工需要 的相应 的机床一 制定相应 的工序加工 尺寸一 制定精准 的加工所需 时间定 额一 按制定好 的工艺步骤对工艺文件进行填写 ,具体见表 1。
2 模具 数控 加工 步骤
③在模具成 型后 ,要对模具 进行加工检验工作 ,这一工作 流程 的依据也是 工艺规程 。
在模具加工生产 过程 中,为附合现在人们的生活高标准 的 要求 ,还要使加工成本 降至最低 ,就必须使 工艺设计实行高标 准化 。所 以说 ,工 艺规程在整个模具生产加工过程 中举足轻重。 1.2 工艺 规 程原 则
数控加 工主要分 勐 旺 、半成品加工和精加工 三部分 。 2.1 毛坯 加 工
标准 ,同时动用最低成本 ,高质量 的完成 与图纸高度附合 的和 一 定 的载荷 ,使刀具与模具在切 割过 程中保持恒定不变 ,从而
高质量的模 具。因为进行模具生产 的同时 ,质量 占第一位 ,只有 提高模 具质量 的同时也减少了刀具 的损伤 。避免 了许多人为加
高质量 的产 品才会 有客户青睐 ;其次是成本 ,如何能够就质量 低成本 出货 ,是每个厂家始终追求 的 目标 。要 想实现这两个 目 标 ,就使工艺规程精益求精 。
模具各工序加工操作及质量标准(完整)
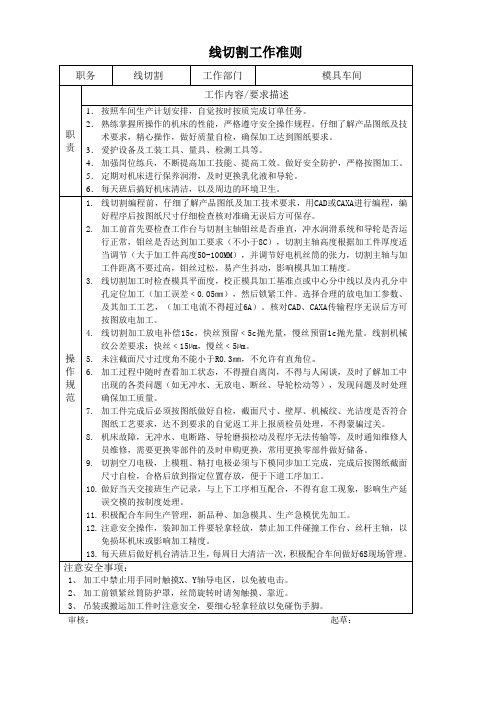
线切割工作准则审核:起草:电火花操作准则划线操作准则审核:起草:铣工/钻工操作准则审核:起草;车工操作准则一、工作内容:1、按照生产图纸先后加工,积极配合加急模具的生产及时完成订单。
2、严格遵守安全操作规程,做好安全防护,按规定穿戴安全防护用品。
3、严格按质量控制标准加工,不断提高加工技能,精心操作,提高工效,做好质量自检,确保加工达到图纸要求。
4、爱护设备及工装工具、量具、检测工具,定期进行保养润滑,定期检修。
5、每天班后搞好机床清洁,以及周边的环境卫生,配合车间做好6S管理。
二、操作规范/技术要求:1、首先仔细了解产品图纸及加工技术工艺要求,熟悉加工操作步骤,选用适合的胚料、刀具、量具提高工作效率。
2、开机前必须仔细检查加工设备运行情况,做好加工前工作准备。
3、模具外型加工尺寸精度表:量(模具成品外圆需精车的要流余量,外圆不需要精车按图加工≤0~–0.5㎜)。
7、粗车下模焊合室按图纸深度留0.5㎜余量精铣,允许公差±0.1㎜,粗车上模公头留拉方余量单边3㎜(以公头截面最长直径为准)。
8、精车上、下模配合贴紧端面(即光面)平整,允许公差﹤0.03㎜,不能有凸凹现象,外形倒角R3,配合止口倒角R1.5,不允许加工直角。
9、平面装配要求:(1)、模具端面平行度应达到GB1184标准规定的6级。
(2)、模具止口对外圆的同轴度达到GB1184标准规定的8级。
(3)、组合上、下模具的同轴度达到GB1184标准规定的13级。
三、注意安全事项:1、加工前必须要做好安全防护措施,佩带好防护罩、眼镜、手套等。
2、开机前检查卡盘、加工件、加工刀具是否锁紧,以免在加工中震动弹出。
审核:起草:工具磨/平面磨操作准则审核:起草:钳工操作准则审核:起草:打磨工操作准则。
冲压模具的加工工艺规程
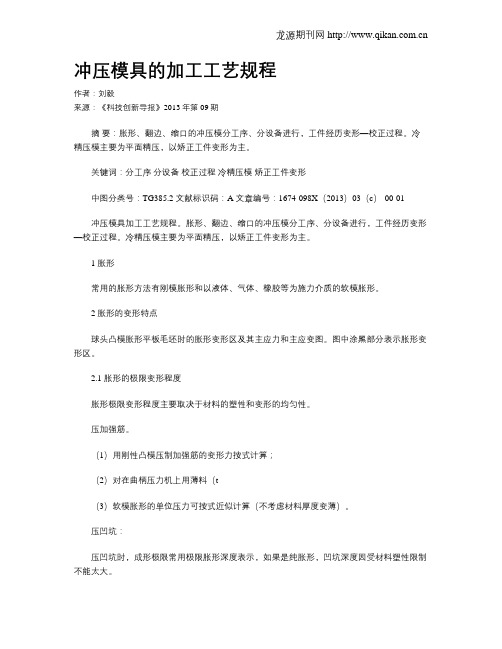
冲压模具的加工工艺规程作者:刘毅来源:《科技创新导报》2013年第09期摘要:胀形、翻边、缩口的冲压模分工序、分设备进行,工件经历变形—校正过程。
冷精压模主要为平面精压,以矫正工件变形为主。
关键词:分工序分设备校正过程冷精压模矫正工件变形中图分类号:TG385.2 文献标识码:A 文章编号:1674-098X(2013)03(c)-00-01冲压模具加工工艺规程。
胀形、翻边、缩口的冲压模分工序、分设备进行,工件经历变形—校正过程。
冷精压模主要为平面精压,以矫正工件变形为主。
1 胀形常用的胀形方法有刚模胀形和以液体、气体、橡胶等为施力介质的软模胀形。
2 胀形的变形特点球头凸模胀形平板毛坯时的胀形变形区及其主应力和主应变图。
图中涂黑部分表示胀形变形区。
2.1 胀形的极限变形程度胀形极限变形程度主要取决于材料的塑性和变形的均匀性。
压加强筋。
(1)用刚性凸模压制加强筋的变形力按式计算;(2)对在曲柄压力机上用薄料(t(3)软模胀形的单位压力可按式近似计算(不考虑材料厚度变薄)。
压凹坑:压凹坑时,成形极限常用极限胀形深度表示,如果是纯胀形,凹坑深度因受材料塑性限制不能太大。
2.2 空心毛坯的胀形空心毛坯胀形是将空心件或管状坯料胀出所需曲面的一种加工方法。
用这种方法可以成形高压气瓶、球形容器、波纹管、自行车三通接头等产品或零件。
3 胀形系数空心毛坯胀形的变形程度用下式表示:式中K-胀形系数,d0-毛坯直径,dmax-胀形后工件的最大直径极限胀形系数与工件切向延伸率的关系式为。
4 胀形力刚模胀形所需压力的计算公式,可根据力的平衡方程式推导得到,其表达式为。
式中:F—所需胀形力,t-材料厚度,H—胀形后高度,μ-摩擦系数,一般μ=0.15~0.20;β-芯轴锥角,一般β=8 °,10 °,12 °,15 °。
5 翻边按变形的性质,翻边分为伸长类翻边和压缩类翻边。
5.1 内孔翻边(1)内孔翻边的变形特点。
模具高效加工方法与工艺规程
h u e od a pin e :s ud’s( e a d cr r s & o s h l p l c s & e mo l a ∞r R a f a y
:hnis c a pL i : 【 f e [ a'od ma hi: i f  ̄ i . c c o l l o: he f ! . 's at c : i c : ng s me y : i
亡 曼计i挫复 杂. 自珂 睦面所卣= 倒 加工拄术的研 冤 断 凡,j 其 凿 加 二 。 高 退
在
制建精度和 表面匝量 ,而 且霉追
折发展的推
求加工表而的 姜观. 着对高速 求已越来越 多 .随
r 艺产生 了E 工
断± 加, 亡 曾 困止 对模 具加工技术提 在舡工机床 、数控 系统 . J 系 具 ±了更高要求, J 即不 仅应保证高
研 ・ ( f 18一 }2 【 1 一 【 05 1 1
辜,蠹 草 言异 宝童 毒菩 : 主主嚣: 帅 拿盖 荠
高模具的加工效率 , 降低模具的制 加工过程中通过利用国外先进的 工 件 ; 造成本 ,减少模具的制 造周期 。 C AD/ AM 软件可通过 以下措 C
在刨康. h进行模甚 套韫等幸郜件, 彤 卜
平面 斜面或 曲面的粗加工等、
部 分加 工工 序在 普通 机床 上 即可 高效 率完成 。 这样就要求我们要编
制一些合理模具 加工工艺 ,以便提
摩 3 I # l 5 J l J ~ I n 蠹 2 ~8 O , 2 0 2 2 一 l摩 1( 珩 1 ( 82 ~ 0 05 I 2l —2
维普资讯
模 具 高 效 加 工 方 法 与 工 艺 规 程
CI C D A ND TEC H NI S EG ULA1 0 NS F E M a C R 1 0 TH
模具加工制作流程
模具加工制作流程一、设计阶段1.根据产品需求和参数,设计师需要绘制产品的三维立体模型和相关的制模图纸。
2.确定模具的型腔结构、尺寸和工艺要求,包括模具的材料、模具的设计寿命等。
3.通过CAD软件制作产品的三维模型,然后进行模型分析和优化,确保模具的结构和功能的可实现性。
4.制作产品的模具图纸,并进行详细的尺寸标注和工艺说明,供加工人员参考。
二、加工准备1.验收和评估模具的设计图纸,确定所需的材料和加工工艺。
2.根据设计图纸的尺寸和要求,制定模具的加工工艺和加工顺序。
3.准备加工所需的材料、刀具和量具等,并进行必要的安全防护措施。
三、加工过程1.根据图纸,进行模具材料的切割和锯割,将材料切割成所需的尺寸。
2.使用数控机床进行加工,根据模具的尺寸和型腔结构,进行车削、铣削、钻孔、线切割等工艺操作,以便将原料加工成合适的模具零件。
3.进行模具部件的加工和组装,包括零件的钳工加工和焊接等。
4.进行模具的加工调试,对模具进行磨削和修正,以提高模具的精度和质量。
5.进行特殊形状和加工难度高的模具零件的加工。
根据不同的加工要求,选择合适的加工工艺,如电火花加工、数控切割等。
四、检验1.对零件进行外观检查,检查零件表面是否有明显的划痕、凹陷或破损。
2.使用测量工具对模具的尺寸进行检测,确保零件的尺寸符合设计图纸的要求。
3.使用适当的设备(如投影仪)进行形状和轮廓的检测,以确保模具的结构和几何形状正确。
4.进行最后的模具检验,并对模具的质量进行评估和验收。
五、试模和调试1.将已制作完成的模具进行组装和安装。
2.调整模具的参数和工作方式,使其适应产品的要求。
3.通过制作测试模具进行试模,测试产品的加工效果和质量。
4.根据试模的结果,对模具进行调整和改进,以提高产品的质量和生产效率。
六、模具维护和保养1.制定模具维护计划,定期对模具进行保养和维修。
2.对模具进行清洁和防锈处理,以延长模具的使用寿命。
3.对模具进行定期检查和维护,修复和更换磨损和损坏的零件。
模具制造工艺 第2版 项目一 模具制造工艺基础
项目一 模具制造工艺基础
模具机械加工工序卡
项目一 模具制造工艺基础
3、制定模具图纸 审查零件图与装配图 * 审查设计图纸的完整性和正确性 * 审查零件的技术要求 * 审查零件的选材是否恰当 * 审查零件的结构工艺性 2、毛坯的选择 3、拟定工艺路线 4、确定工序具体内容 5、填写工艺文件
项目一 模具制造工艺基础
一、模具加工工艺规程概述
1、工艺过程及其组成 将原材料转变为模具成品的全过程称为模具生产 过程。主要包括: 模具方案策划、结构设计 生产技术准备 模具成型件加工 装配与试模 验收与试用
模具生产过程中直接改变生产对象的形状、尺寸、相对 位置和性质等,使其成为半成品或成品的过程,称为工艺 过程。
项目一 模具制造工艺基础
四、选择加工方法时需要考虑的因素 在选择从粗到精的加工方法及过程时,要综合考
虑多方面的因素,重点考虑以下问题:
(1)被加工零件的结构形状和表面的精度 一般所采用加工方法的经济精度,应保证零件
所要求的加工精度和表面质量。 加工经济精度:是指在正常加工条件下(采用
符合质量标准的设备、工艺装备和标准技术等级的工 人,不延长加工时间)所能保证的加工精度。
加工方法及工序顺序凹模镶套零件的主
要尺寸标注都是以零件的轴心线为基准
的,这使得零件加工时容易与设计基准
进行统一
项目一 模具制造工艺基础
六.安排加工顺序
* 先粗后精 * 基准先行 * 先主后次 * 先面后孔 适当安排热处理(预备热处理和最终热处理) 检验、去毛刺、倒棱、清洗、防锈等辅助工序要 按需设置,不能遗漏。 在确定工序数目时,恰当地决定工序集中与工序 分散问题。
二、模具加工工艺规程及作用:
模具工艺规程编制
模具工艺规程编制1. 引言模具工艺规程是指对模具制造过程中所涉及的工艺、工序、工具和设备等进行详细的说明和规定的文件。
它的编制可以为模具制造过程提供明确的工艺指导,并确保模具制造过程的稳定性和可靠性。
本文档旨在介绍模具工艺规程的编制方法和内容要点。
2. 编制方法模具工艺规程的编制方法可以按照以下步骤进行:1.确定编制目的和范围:明确编制该规程的目的,例如提高模具制造效率、降低成本或保证制造质量等,并确定规程的适用范围。
2.收集资料和信息:收集相关的技术资料、工艺参数、设备说明和相关标准等信息,并进行整理和分类。
3.制定编制计划:根据所收集的资料和信息,制定编制计划,明确编制规程的时间节点和责任人。
4.组织编制工作:根据编制计划,组织相关人员进行规程的编制工作。
可以委托经验丰富的技术人员或专业团队来编制规程。
5.内容编写和审核:根据所收集的资料和信息,编写规程的内容,通过内部审核和技术评审,并进行修订和完善。
6.发布和培训:经过审核和修订后,将规程进行发布,并进行相关培训,确保相关人员了解和掌握规程的内容和要求。
7.定期检查和更新:定期对已发布的规程进行检查和评估,及时更新和修订规程,确保其与现行的技术要求和标准保持一致。
3. 内容要点模具工艺规程的内容要点可以包括以下几个方面:3.1. 材料要求对模具制造所使用的材料要求进行详细的说明,包括材料的种类、牌号、规格以及供应商等信息。
同时,还应规定材料的质量检验标准和检验方法,并明确材料的贮存要求和保管措施。
3.2. 设计要求对模具的设计要求进行详细描述,包括模具的尺寸、结构、工作原理等方面的要求。
此外,还应指定模具的工作温度、压力和寿命要求,并规定模具设计所依据的标准和规范。
3.3. 加工工艺对模具的加工工艺进行详细的描述和规定,包括模具零件的加工顺序、加工方法、加工设备和工具的使用等。
此外,还应指定加工工艺中的质量控制要求和检验方法,确保模具的加工质量。
- 1、下载文档前请自行甄别文档内容的完整性,平台不提供额外的编辑、内容补充、找答案等附加服务。
- 2、"仅部分预览"的文档,不可在线预览部分如存在完整性等问题,可反馈申请退款(可完整预览的文档不适用该条件!)。
- 3、如文档侵犯您的权益,请联系客服反馈,我们会尽快为您处理(人工客服工作时间:9:00-18:30)。
模具加工工艺规程
一、模具生产过程的概念
模具的生产过程,是指将用户提供的产品信息和制件的技术信息通过结构分析、工艺性分析,设计成模具;并基于此,将原材料经过加工、装配,转变为具有使用性能的成型工具的全过程。
整个生产过程可用下述框图表示。
原材料的运输、存放生产准备毛坯制造
机加工、热
处理
装配
试模包装、入库
•具体地说,模具生产过程分以下六个阶段。
•(1)模具方案确定分析产品零件结构、尺寸精度、表面质量要求以及成型工艺。
•(2)模具结构设计进行成型件造型、结构设计;系统结构(包括定位、导向、卸料以及相关参数设定等)设计,即总成设计。
•(3)生产准备成型件材料、模块等坯料加工;标准零、部件配购;根据造型设计,编制NC、CNC加工代码组成的加工程序;以及刀具、工装等。
•(4)模具成型零件加工根据加工工艺规程,采用NC、CNC加工程序进行成型加工、孔系加工;或采用电火花、成型磨削等传统工艺进行加工,以及相应的热处理工艺。
•(5)装配与试模根据模具设计要求,检查标准零、部件和成型零件的尺寸精度、位置精度,以及表面粗糙度等要求;按装配工艺规程进行装配、试模。
•(6)验收与试用根据各类模具的验收技术条件标准和合同规定,对模具试冲制件(冲件、塑件等)和模具性能、工作参数等进行检查、试用,合格后则验收。
模具生产过程示意图
二、模具工艺过程
•在模具生产过程中,直接改变制件的形状、尺寸、相互位置、性能的生产过程称为工艺过程。
工艺技术人员应该根据模具的特点和要求、模具生产具体条件和工艺规律等编制工艺技术文件,用于指导生产。
• 1. 模具工艺过程的主要内容
•(1)编制工艺文件模具工艺文件主要包括模具零件加工工艺规程、模具装配工艺要点或工艺规程、原材料清单、外购件清单和外协件清单等。
•模具工艺技术人员应在充分理解模具结构、工作原理和要求的前提下,结合本企业冷、热加工设备条件,本企业生产和技术状态等条件编制模具零件加工和模具装配等工艺文件。
•(2)二类工具的设计和工艺编制二类工具(二级工具)是指加工模具零件和模具装配中所用的各种专用工具。
这些专用的二类工具,一般都由模具工艺技术人员负责设计和工艺编制(特殊的部分由专门技术人员完成)。
二类工具的质量和效率对模具质量和生产进度起着重要的作用。
在客观条件允许下可以利用通用工具改制,注意应该将二类工具的数量和成本降低到客观允许的最小程度。
•经常设计的二类工具有:非标准的铰刀和铣刀、各型面检验样板、非标准量规、仿形加工用靠模、电火花成型加工电极、型面检验放大图样等。
•(3)处理加工现场技术问题处理模具零件加工和装配过程中出
现的技术、质量和生产管理问题是模具工艺技术人员的经常性工作之一。
如解释工艺文件和进行技术指导、调整加工方案和方法、办理尺寸超差和代料等。
在处理加工现场技术问题时,既要保证质量又要保证生产进度。
•(4)试模和鉴定工作模具在装配之后的试模是模具生产的主要环节,模具设计人员、工艺人员和其他人员通过试模中出现的问题,提出解决问题的对策,并对模具的最终技术质量状态作出正确的结论。
二、模具的机械加工工艺过程
•用机械加工方法(主要是切削加工方法)直接改变毛坯的形状、尺寸和表面质量,使其成为合格模具零件的过程,称为模具机械加工艺过程。
•模具的机械加工艺过程是由一个或若干个工序组成,毛坯依次通过这些工序而变成成品。
•(1)工序
•一个或一组工人在同一个工作地点,对一个或同时几个工件所连续完成的那一部分工艺过程称为工序。
•工序不仅是组成工艺过程的基本单元,也是组织生产、核算成本和进行检验的基本单元。
工序的划分基本依据是加工对象或加工地点是否变更,加工内容是否连续。
工序的划分与生产批量、加工条件和零件结构特点有关。
•(2)工步
•对工序进一步划分即为工步。
一道工序(一次安装或一个工位)中,可能需要加工若干个表面只用一把刀具,也可能虽只加工一个表面,但却要用若干把不同刀具。
在加工表面和加工工具不变的情况下,所连续完成的那一部分工序,称为一个工步。
•(3)安装与工位
•确定工件在机床或夹具上占有一个正确位置的过程,称为定位。
工件定位后将其固定,使之在加工过程中保持定位位置不变,即夹紧。
工件的定位和夹紧过程称为装夹。
工件从定位到装夹的整个过程称为安装。
•(4)工步的合并
•需要将工步加以合并的情况包括:
•1、对于性质相同、尺寸相差不大的表面,可以合并为一个工步。
•2、对于那些在一次安装中连续进行的多个相同的加工表面,可以合并为一个工步。
•3、为了提高加工效率和加工质量,用几把刀具同时加工几个表面的工步称为复合工步,在工艺文件上可看作一个工步。
•(5)走刀
•有些工步,由于余量较大或其他原因,需要用同一刀具,对同一表面进行多次切削,则刀具对工件每进行一次切削就是一次走刀。
走刀是工步的一部分,一个工步可包括一次或多次走刀。
三、生产纲领与生产类型
•(1)生产纲领
•机械产品在计划期内应当生产的产品产量和进度计划称为该产品的生产纲领。
零件的生产纲领可按下式计算:
N0=N×n(1+α)(1+β)
式中:N0—机械零件的生产纲领(件);
N—机械产品在计划期内的产量(件);
n—每台机械产品中该零件的数量(件);
α—该零件的备品率(%);
β—该零件的废品率(%)。
•(2)生产类型
•根据产品的生产纲领,模具机械加工的生产类型主要可分为:单件生产和批量生产。
•1、单件生产
•生产的产品品种较多,每种产品的产量很少,同一个工作地点的加工对象经常改变,很少重复生产。
如新产品试制用的各种模具和大型模具等都属于单件生产。
•2、成批生产
•产品的品种不是很多,但每一种产品均有一定的数量,同一个工作地点的加工对象周期性地更换,这种生产称为成批生产。
如模具的标准模架、模座、导柱、导套等属于成批生产。