板料冲裁原理与合理间隙_五_
冲压

第一章冲压冲压的定义:室温下,在压力机上通过模具对板料金属(非金属)加压,使之产生塑性变形或分离,从而获得一定尺寸、形状和性能的工件的加工方法,又叫冷冲压或板料冲压。
冲压工艺可用于加工,金属板料,非金属板料.冲压工艺特点:生产效率高;在大量生产中可获得稳定的质量;材料利用率高,生产成本低;可制造复杂形状的工件。
冲压生产的局限性:--制模成本高;--技术要求高;--不适用于单件、小批量生产。
加工硬化:在常温下,随着变形程度的增加,金属材料的强度指标增高,塑性指标降低的现象。
冲压分类:分离工序,成型工序分离工序:冲压过程中,使冲压件与板料在切应力或拉应力的作用下,沿一定的轮廓线相互分离。
分离工序主要指冲裁,包括落料、冲孔、切断、切边、剖切等工序。
普通冲裁:通过破坏分离方式所完成的冲压工序。
精密冲裁:以变形分离方式所完成的冲压工序。
成形工序:在冲压过程中,使毛坯在不破坏的条件下发生塑性变形,成为所需形状与尺寸的工件,同时冲压件应该满足尺寸精度方面的要求。
成形工序主要包括弯曲、拉伸、胀形、翻边等。
落料:用模具沿封闭轮廓线冲切,冲下部分是零件。
用于制造各种平板零件或者成形工序制坯冲孔:用模具沿封闭轮廓线冲切,冲下部分是废料。
用于冲制各类零件的孔形弯曲;把板料沿直线弯曲成各种形状,板料外层受拉伸力,内层受压缩力。
可加工形状复杂的零件毛坯区域的划分:变形区,传力区在成形过程中,毛坯的变形区和传力区是运动变化的,而且还会相互转化。
制定工艺时,必须保证:“弱区先变形,变形区应为弱区”对毛坯变形趋向性的控制,主要有以下几种方法:(1)合理确定毛坯和半成品尺寸(2)改变模具工作部分的几何形状和尺寸(3)改变毛坯与模具接触面之间的摩擦阻力(4)改变毛坯局部力学性能1、什么是冲压?它与其它加工方法相比有什么特点?2、冲压工序可分为哪两大类?他们的主要区别和特点是什么?3、如何控制冲压过程中的变形趋向?板料的冲压性能:指板料对冲压的适应能力、可成形能力间接试验:板料的受力情况和变形特点与实际冲压有一定差别,其试验结果只能间接反映板料的冲压性能。
2.3 冲裁工艺计算
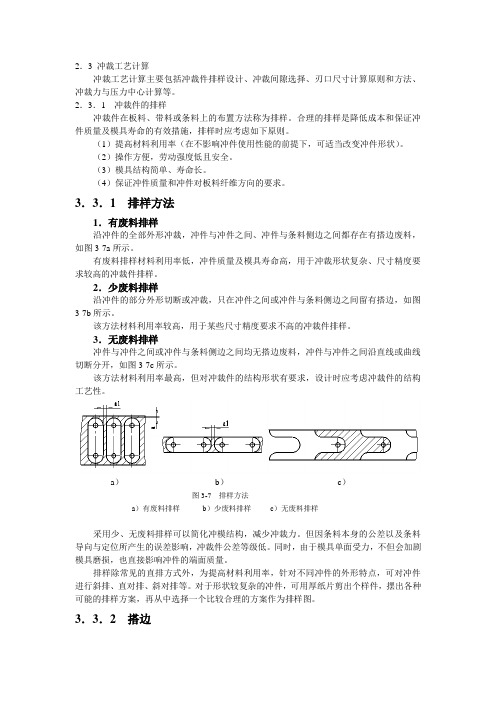
2.3 冲裁工艺计算冲裁工艺计算主要包括冲裁件排样设计、冲裁间隙选择、刃口尺寸计算原则和方法、冲裁力与压力中心计算等。
2.3.1 冲裁件的排样冲裁件在板料、带料或条料上的布置方法称为排样。
合理的排样是降低成本和保证冲件质量及模具寿命的有效措施,排样时应考虑如下原则。
(1)提高材料利用率(在不影响冲件使用性能的前提下,可适当改变冲件形状)。
(2)操作方便,劳动强度低且安全。
(3)模具结构简单、寿命长。
(4)保证冲件质量和冲件对板料纤维方向的要求。
3.3.1 排样方法1.有废料排样沿冲件的全部外形冲裁,冲件与冲件之间、冲件与条料侧边之间都存在有搭边废料,如图3-7a所示。
有废料排样材料利用率低,冲件质量及模具寿命高,用于冲裁形状复杂、尺寸精度要求较高的冲裁件排样。
2.少废料排样沿冲件的部分外形切断或冲裁,只在冲件之间或冲件与条料侧边之间留有搭边,如图3-7b所示。
该方法材料利用率较高,用于某些尺寸精度要求不高的冲裁件排样。
3.无废料排样冲件与冲件之间或冲件与条料侧边之间均无搭边废料,冲件与冲件之间沿直线或曲线切断分开,如图3-7c所示。
该方法材料利用率最高,但对冲裁件的结构形状有要求,设计时应考虑冲裁件的结构工艺性。
a)b)c)图3-7 排样方法a)有废料排样b)少废料排样c)无废料排样采用少、无废料排样可以简化冲模结构,减少冲裁力。
但因条料本身的公差以及条料导向与定位所产生的误差影响,冲裁件公差等级低。
同时,由于模具单面受力,不但会加剧模具磨损,也直接影响冲件的端面质量。
排样除常见的直排方式外,为提高材料利用率,针对不同冲件的外形特点,可对冲件进行斜排、直对排、斜对排等。
对于形状较复杂的冲件,可用厚纸片剪出个样件,摆出各种可能的排样方案,再从中选择一个比较合理的方案作为排样图。
3.3.2 搭边搭边排样中相邻两个零件之间的余料或零件与条料边缘间的余料称为搭边。
搭边的作用是补偿定位误差,保持条料有一定的刚度,以保证零件质量和送料方便。
冲裁工艺与冲裁模冲裁工艺及冲裁件的工艺性

一、冲裁工艺及冲裁件的工艺性
1、概述
1)冲裁——利用装在压力机上的模具,将板料分离的冲压工 艺。 2)包括内容——冲孔、落料、修边、切口、切断等。 落料——从板料上冲下所需形状的零件或毛坯(要冲掉部分) 冲孔——从工件上冲出所需形状的孔(冲掉的部分是废料) 3)用途——可加工平板类零件;为弯曲、拉深、成形等工序 准备毛坯;在成形件上完成刨切、冲孔等。 4)模具
四、排样设计
排样:冲裁件在被冲材料上的布置方法。
在冲压生产中,零件的材料费用占制造成本 的60%以上,所以合理的排样不仅能提高冲 裁件的质量、提高模具寿命,而且时节约使 用材料降低成本的有效措施 。
冲裁工艺与冲裁模冲裁工艺及冲裁 件的工艺性
搭边:排样时零件与零件之间、零件与条料侧 边留下的工艺废料。
)配合加工法中凸、凹模刃口尺寸计算
对于形状复杂冲裁件,为保证凸、凹模 之间的合理间隙值,必须采用配 合加工方式。即首先加工凸、凹模中的一件作为基准件,然后以选定的间 隙配合加工另一件。
冲裁工艺与冲裁模冲裁工艺及冲裁 件的工艺性
冲裁工艺与冲裁模冲裁工艺及冲裁 件的工艺性
配合加工的计算公式
冲裁工艺与冲裁模冲裁工艺及冲裁 件的工艺性
冲裁工艺与冲裁模冲裁工艺及冲裁 件的工艺性
落料与冲孔:
冲裁工艺与冲裁模冲裁工艺及冲裁 件的工艺性
冲裁工艺与冲裁模冲裁工艺及冲裁 件的工艺性
模具图
冲裁工艺与冲裁模冲裁工艺及冲裁 件的工艺性
2、冲裁件的工艺性
冲裁件的工艺性: 指冲裁件在工艺上的适应性,即加工难易程度。良好的工艺性能使材
料消耗少、工序数量少、模具结构简单且使用寿命长、产品质量稳定。
冲裁时,搭边过大,会造成材料浪费,搭边太 小,则起不到搭边应有的作用,过小的搭边, 导致板料被拉进凸、凹模间隙,加剧模具的磨 损,甚至会损坏模具刃口。
冲裁工艺
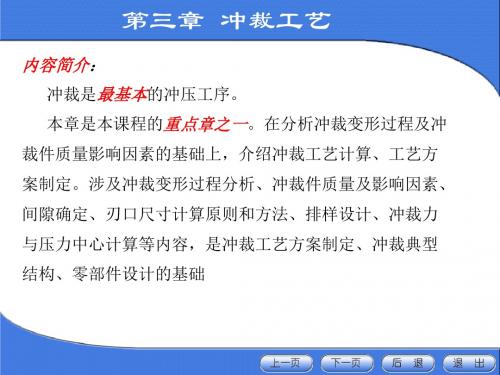
第二章 冲裁工艺与冲裁模设计
第四节 凸模与凹模刃口尺寸的确定
二、凸、凹模刃口尺寸的计算方法(续)
2.凸模与凹模配作法 配作法就是先按设计尺寸制出一个基准件(凸模或凹模), 然后根据基准件的实际尺寸再按最小合理间隙配制另一件。 特点: 模具的间隙由配制保证,工艺比较简单,不必校核
T A ≤ Z max Z min的条件,并且还可放大基准件的制造公差,
(2)材料的性质(回弹小则精度高)
(3)冲裁间隙 (主要影响回弹值及方向) (4)冲裁件的形状(形状越简单精度越高)
第二节 冲裁件的质量分析
二、冲裁件断面质量及其影响因素
1. 断面特征:冲裁件断面一般可以分成4个区。
圆角带a: 刃口附近的材料产生弯曲和伸长变形。 光亮带b:塑性剪切变形。质量最好的区域。 断裂带c:裂纹形成及扩展。 毛刺区d: 间隙存在,裂纹产生不在刃尖,毛刺不可避免。
第一节 冲裁过程分析
二、冲裁时板料的变形过程
间隙正常、刃口锋利情况下,冲裁变形过程可分为三个阶段
1.弹性变形阶段
变形区内部材料应力小于屈服应力 。
2.塑性变形阶段
变形区内部材料应力大于屈服应力。 凸、凹模间隙存在,变形复杂,并非纯塑性剪切变形,还伴随有弯曲、拉 伸,凸、凹模有压缩等变形。
3.断裂分离阶段
第三章 冲裁工艺
概述
冲裁:利用模具使板料沿着一定的轮廓形状产生分离的一种
冲压工序。
基本工序:落料和冲孔。
落料-----若使材料沿封闭曲线相互分离,封闭曲线以内的部分作为冲裁
件时,称为落料; 冲孔-----若使材料沿封闭曲线相互分离,封闭曲线以外的部分作为冲裁 件时,则称为冲孔。
第三章 冲裁工艺
板料冲压基础知识

板料冲压基础知识一、概述板料冲压是一种常用的金属加工方法,通过将金属板料置于冲压机上,利用冲压机的压力将板料冲压成所需形状。
板料冲压广泛应用于汽车制造、家电制造、电子产品制造等领域。
本文将介绍板料冲压的基础知识。
二、板料材料在板料冲压过程中,常使用的板料材料包括钢板、铝板、铜板等。
不同的材料具有不同的性能和特点,选择合适的材料对于冲压过程的成功至关重要。
1. 钢板:钢板具有良好的强度和韧性,常用于制造需要承受较大力度的零部件,如汽车车身和机械设备的外壳。
2. 铝板:铝板具有较低的密度和良好的抗腐蚀性能,常用于制造轻型零部件和外壳,如手机壳和电子产品外壳。
3. 铜板:铜板具有良好的导电性和导热性,常用于制造需要高导电性和散热性能的零部件,如电子元件和散热片。
三、冲压工艺板料冲压过程中,需要进行多道工序,包括模具设计、冲孔、弯曲、拉伸等。
下面将介绍其中的几个常见工艺。
1. 冲孔:冲孔是板料冲压中最常见的工艺,通过模具上的冲头对板料施加力量,使得板料上形成所需的孔洞。
冲孔通常使用冲裁模具,根据所需孔洞的形状和尺寸选择合适的冲头。
2. 弯曲:弯曲是将平板材料弯折成所需形状的工艺。
在弯曲过程中,板料会受到弯曲力矩的作用,使得板料发生弯曲变形。
弯曲过程需要使用弯曲模具,并根据所需弯曲角度和半径来选择合适的模具。
3. 拉伸:拉伸是将板料拉伸成所需形状的工艺。
拉伸过程中,板料会受到拉伸力的作用,使得板料发生拉伸变形。
拉伸过程需要使用拉伸模具,并根据所需形状和尺寸来选择合适的模具。
四、模具设计模具是板料冲压过程中的关键因素之一,模具的设计直接影响冲压产品的质量和效率。
模具设计需要考虑以下几个因素:1. 材料选择:模具材料需要具有足够的硬度和耐磨性,以保证模具的使用寿命。
常用的模具材料包括工具钢、硬质合金等。
2. 结构设计:模具的结构需要合理,以方便冲压过程中的操作和维护。
模具的结构应尽量简单,便于制造和维修。
3. 精度要求:模具的精度要求直接影响冲压产品的尺寸精度和表面质量。
冲裁模具设计方案
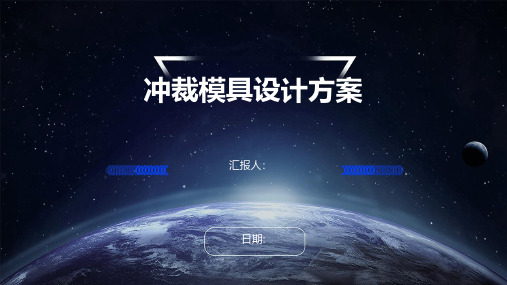
凹模定位板01020304夹板紧固螺栓顶杆弹簧分析图纸选择模具类型设计模具结构030201选择材料和热处理工艺进行试模粗加工热处理备料精加工抛光总装试模冲裁适用于加工各种形状的薄板零件,具有加工精度高、生产效率高、成本低等优点。
但冲裁过程中会产生废料,模具磨损也较快。
冲裁原理及工艺特点工艺特点冲裁原理间隙选择间隙计算冲裁间隙的选择与计算排样设计搭边值选择冲裁件的排样与搭边确定模具类型模具结构形式模具类型与结构形式根据产品形状和尺寸,设计凸模的结构和尺寸,考虑凸模强度、刚度和使用寿命。
凹模设计根据产品形状和尺寸,设计凹模的结构和尺寸,考虑凹模的加工精度和使用寿命。
根据产品要求,设计定位销的结构和尺寸,确保定位销能够准确固定产品位置。
挡料装置设计根据产品要求,设计挡料装置的结构和尺寸,确保挡料装置能够准确控制产品送料位置。
定位销设计VS模具的夹持与固定装置夹持器设计固定座设计模具材料选择模具结构设计模具强度计算模具强度校核模具刚度定义根据冲裁件的材料、厚度和精度要求,确定模具的刚度要求。
模具刚度校核标准模具刚度优化模具刚度校核03模具稳定性优化01模具稳定性定义02模具稳定性校核标准模具的稳定性分析为保证模具的使用寿命,需要选择具有足够硬度的材料,以便抵抗磨损和保持其形状。
模具材料的硬度模具材料的韧性模具材料的抗疲劳性模具材料的耐腐蚀性为了使模具能够承受冲击和弯曲,需要选择具有足够韧性的材料。
由于模具在长期使用中会受到循环应力的作用,因此需要选择具有较好抗疲劳性能的材料。
对于需要接触腐蚀性材料的模具,应选择具有较好耐腐蚀性的材料。
模具材料的选择原则碳素工具钢低合金工具钢高碳高铬工具钢不锈钢常用模具材料及其特性退火淬火正火回火01030204模具材料的热处理工艺复杂零件的冲裁模具设计通常适用于生产批量较大、对精度要求较高的场合。
在设计时,需考虑以下因素1. 材料:选择适合冲裁的材料,如不锈钢、高强度钢等。
第一章 冲裁工艺(1-5,1-6,1-7)
利用结构废料的措施有:
当材料和厚度相同时,在尺寸允许的情况下,较小尺寸的冲 件可在较大尺寸冲件的废料中冲制出来。 在使用条件许可下,也可以改变零件的结构形状,提高材料 利用率,如图2.5.2所示。 7
第一章 冲裁工艺
第五节 冲裁排样设计
二、排样方法
根据材料的合理利用情况,条料排样方法可分为三种: 1.有废料排样(a) 2.少废料排样(b) 3.无废料排样(c、d)
用普通平刃口模具冲裁时,冲裁力F一般按下式计算:
F KLt b
注: F——冲裁力; L——冲裁周边长度; t——材料厚度; b ——材料抗剪强度; K——系数。一般取K=1.3
18
第一章 冲裁工艺
第六节 冲裁力和压力中心的计算
二、卸料力、推件力及顶件力的计算
卸料力: 从凸模上卸下箍着的
料所需要的力。
21
第一章 冲裁工艺
第六节 冲裁力和压力中心的计算
四、降低冲裁力的方法
1.阶梯凸模冲裁
2.斜刃冲裁
3.加热冲裁(红冲)
22
第一章 冲裁工艺
第六节 冲裁力和压力中心的计算
五、冲模压力中心的确定
模具的压力中心: 冲压力合力的作用点。
为了保证压力机和模具的正常工作,应使模具的压力中心与 压力机滑块的中心线相重合。
第一章 冲裁工艺
第六节 冲裁力和压力中心的计算
三、压力机公称压力的确定
压力机的公称压力必须大于或等于各种冲压工艺力的总和Fz
采用弹性卸料装置和下出料方式的冲裁模时: FZ F FX FT 采用弹性卸料装置和上出料方式的冲裁模时: FZ F FX FD 采用刚性卸料装置和下出料方式的冲裁模时: FZ F FT
冲 裁 间 隙
中华人民共和国国家标准GB/T16743—1997冲裁间隙Blanking clearance1 范围本标准规定了金属材料与非金属材料的冲裁间隙值,以及采用此间隙值时冲裁件可以达到的尺寸精度与切面质量水平。
本标准使用于板料厚度为10mm以下的金属与非金属材料平板冲压件的普通冲裁。
2 定义、符号2.1定义冲裁间隙 blanking clearance冲裁模具中凹模与凸模刃口侧壁之间间隙的距离。
图1 冲裁模示意图2.2 符号c-冲裁间隙(单边间隙),mm;t—材料厚度,mm ;τ—材料抗剪强度,mm;R—塌角高度(以料厚的百分比表示);B—光亮带高度;(以料厚的百分比表示);F—断裂带高度(以料厚的百分比表示);α—断裂角,°;h—毛刺高度,mm;f—平面度,mm;上述符号见图1及表1附图。
3 冲裁间隙3.1 金属材料冲裁间隙国家技术监督局1997—03—04批准1977—09—01实施GB/T 16743—19973.1.1金属材料冲裁间隙分类根据冲裁件尺寸精度、剪切面质量、模具寿命和力能消耗等主要因素,将金属材料间隙分成三种类型,即Ⅰ类(小间隙),Ⅱ类(中等间隙),Ⅲ类(大间隙),列于表1。
3.1.2金属材料冲裁间隙档次按金属材料的的种类、供应状态、抗剪强度,给出相应于表1的三类冲裁间隙值,列于表2。
3.2 非金属材料的冲裁间隙常用非金属材料的冲裁间隙值,列于表3 。
4冲裁间隙选用原则与方法4.1选用原则4.1.1 选用合理冲裁间隙值的主要依据是在保证冲裁件尺寸精度和满足剪切质量要求的前提下,考虑模具寿命、模具结构、冲裁件形状等因素所占的权重综合分析后确定。
4.1.2对下列情况,应酌情增减冲裁间隙值:a)在同样条件下,冲孔间隙比落料时可大些;b)冲小孔(一般为孔径小于料厚)时,凸模易折断,间隙应取大些。
但这时要采取有效措施,防止废料回升;c)硬质合金冲裁模应比钢模的间隙大30﹪左右;d)复合模的凸凹模壁单壁时,为防止胀裂,应放大冲孔凹模间隙;e)硅刚片随含硅量增加,间隙相应取大些;f)采用弹性压料装置时,间隙可大些;g)高速冲压时,模具容易发热,间隙应增大,如行程次数超过每分钟200次时,间隙应增大10﹪左右;h)电火花穿孔加工凹模型孔时,其间隙应比磨削加工取小些;i)加热冲裁时,间隙应小些;j)凹模为侧壁刃口时,应比直壁间隙小;k)对需攻丝的孔,间隙应取小些。
冲压工艺及模具
②当Z过大:
拉伸作用强,挤压作用弱,光亮带窄,相对滑动距
离短,冲件弹性恢复与上相反 。凸凹模磨损大为减轻。
③同一间隙Z:凸模端面比凹模端面磨损小。
凸模侧面比凹模侧面磨损大。 为提高模具寿命,一般采用较大间隙。若采用小间隙 应提高模具硬度,模具制造精度高,表面粗糙度低,并改 善润滑条件,以减小磨损。
冲压件尺寸减小,因此,尺寸误差是两者的综合结果。
② 模具制造精度低,工件的尺寸精度无法保证。
冲裁件内外形能达到的经济精度IT11—14,尺寸越大,精度越高,不
同的冲压件尺寸精度所对应的模具制造精度不同。
(3)间隙对弯曲度的影响(图2-11)
Z增大,h增大,为提高制件的平整度,可加压料板或反向压板,要求 太高可以加整形工序。
二、模具间隙
模具间隙——指凸、凹模刃口间的间缝隙,单边用C表
示,双边用Z表示。 间隙是冲裁模设计的关键尺寸。间隙大小对冲裁件质量和 模具使用寿命都有很大影响。
1、间隙对冲裁件质量的影响(断面、尺寸、形状即
弯曲度)
(1)间隙对断面质量的影响(图2-10)
a——Z过小,断面平直,双光亮带,挤长毛刺薄,易去除。 b——Z合理,有一定的斜度,比较平直,光洁,光亮带1/2-1/3。 c——Z过大,斜度大,粗糙,光亮带小,拉长毛刺厚,难去除。
4. 合理间隙的确定
生产中选用一个适当的范围作为合理间隙,只要间隙在这个范围内, 就可冲出良好产品,这个范围的最小值称为最小合理间隙,最大值称为 最大合理间隙。 新设计模具应采用最小值。
⑴ 理论确定法:
根据两裂纹重合,获得良好断面依据。
单边 c=t(1—ho/t)tgβ ho/t——相对压入深度
β ——裂纹与垂线间夹角
板料冲压
冲模在工作过程中必然有磨损,落料件尺寸会 随凹模刃口的磨损而增大,而冲孔件尺寸则随凸模 的磨损而减小。为了保证零件的尺寸要求,并提高 模具的使用寿命:
落料时凹模刃口的尺寸应靠近落料件公差范围 内的最小尺寸;冲孔时,选取凸模刃口的尺寸靠近 孔的公差范围内的最大尺寸。
金属塑性成型工艺-板料冲压 王守仁 2008.3
金属塑性成型工艺-板料冲压 王守仁 2008.3
金属塑性成型工艺-板料冲压 王守仁 2008.3
外缘修整模的凸凹模间隙,单边取0.001~0.01 mm。也可以采用负间隙修整,即凸模刃口尺寸大 于凹模刃口尺寸的修整工艺。
三、切断
切断是指用剪刃或冲模将板料沿不封闭轮廓进 行分离的工序。
剪刃安装在剪床上,把大板料剪切成一定宽度 的条料,供下一步冲压工序用。而冲模是安装在冲 床上,用以制取形状简单、精度要求不高的平板件。
特征与材料(板料材料)塑性的关系:
断面质量受冲裁条件的不同而不同,如: 刃口间隙,刃口形状,锋利程度,冲裁力、 润滑条件,板料质量(表面质量),板料种 类(性能)。
冲压生产要求冲裁件有较大的光亮带, 尺量减少断裂带区域的宽度。
材料塑性愈好,光亮带愈大,断裂带愈 小,同时,圆角毛刺亦增大。
金属塑性成型工艺-板料冲压 王守仁 2008.3
当单边间隙Z增大到材料厚度的15%-20%时, 卸料力为0。
金属塑性成型工艺-板料冲压 王守仁 2008.3
冲裁间隙对冲压的影响 D、间隙对模具寿命的影响
由于工件与凸、凹模侧壁之间有磨擦的存在, 间隙小,磨擦大,模具寿命短。冲裁过程中,凸模 与被冲孔之闻,凹模与落料件之阀均有摩擦,而且闻 隙越小,摩擦越严重。所以过小的间隙对模具寿命 极为不利,而较大的间隙可使凸模与凹模的侧面与 材料间的摩擦减小,井能减缓间隙不均匀的影响,从 而提高模具的寿命。
- 1、下载文档前请自行甄别文档内容的完整性,平台不提供额外的编辑、内容补充、找答案等附加服务。
- 2、"仅部分预览"的文档,不可在线预览部分如存在完整性等问题,可反馈申请退款(可完整预览的文档不适用该条件!)。
- 3、如文档侵犯您的权益,请联系客服反馈,我们会尽快为您处理(人工客服工作时间:9:00-18:30)。
板料冲裁原理与合理间隙(五
陈毓勋赵振择思建军染新华谈惠君荟平面度一相对间隙试验今以挠度f与板材厚度t的比值表示冲裁件的平面度由于凸模与凹模之间的间隙大于零因而在冲裁过程中必然产生弯曲力矩使板料引起塑性弯曲曾经对十种常用材料各进行九种间隙的平面度试验利用工具显微镜(放大50倍)进行挠度的测量其中低碳钢铝所获得的平面度一相对间隙曲线如图318所示对于较软的材料而言两者的变化规律与图318类似相对间隙愈大平面度愈差对于较硬的材料采用合理大间隙比小间隙所获得的平面度要好一些%而当z八二50时f八已超过50%有色金属(除硬铝与纯铝以外)当相对间隙z/t>30%f/t才超过20%而大多数材料的
平面度不超过20%
因此对于有平面度要求的冲裁件其相对间隙不能超过20%
夸38垂直度一相对间隙试验板料在冲裁过程中由于上下刃口产生的裂纹不垂直于板面所以当冲裁件与板料
分离后其断面也不垂直于板面冲裁件断面的垂直度主要决定于相对间
乡娜有
寡母亏
容
产/佃法
炯
。盯
L沪
l,夕夕
岁夕么漏
l~
吝20./司脚
,
儿《今几
/必泳杯,
护留巴乡了尸
,
/
月
孟况f笼)参叫冬吝
/;//日
!l口月
萝赶伶L,
周水吕口今
2
八
`
_.l}
厂~
厂)闷二奋洲尸尸
才r川对相铆
川
盯
,/卜肖肖夕
l1L,踢
卜
/尸/
图318平面度一相对间隙曲线
由试验可见大多数材料在相对间隙z八《10一20%时平面度变化较慢当相对
间隙z八>20%时平面度随着相对间隙增大而
迅速变差尤其是黑色金属中的低碳钢
(如08F与A3)当z八《20%时f八仅为
15
52
铃青娜
{!犷
外`卜
,Y、
尸州吟夕
夕厂
卜
一
如,
l
公T
币渗
弓充〔公〕
图319垂直度一相对间隙曲线(模具工业)1990No12总11
8隙图1列出几种常用材料通过九种间隙
的冲裁试验采用投影仪(放大50倍)进行测量所获得的垂直度一相对间隙试验曲线由试验可见断面的不垂直现象随着相对间隙的增大而增大值得注意的是当相对间隙z八<5%时大部分材料的垂直度x八为负值(亦即落料件上方的尺寸大于下方的尺寸)这是由于断面上部分的回弹量大于下部分所致当相对间隙z/t15~20%时垂直度发生了明显地变化垂直度愈差凸凹模刃口的磨损愈严重影响模具寿命因此除精密冲裁件外在一般情况下应避免冲裁件的垂直度出现负值的现象怪39相对撕裂带一相对间隙试验如前所述在小间隙(z八二5一10%)情况下冲裁件的断面上开始出现撕裂带在大间隙(z八>10%)情况下撕裂带随着相对间隙增大而增大由于板料厚度是一定的所以撕裂带愈大即光亮带愈小撕裂带与板料厚度的比值称为相对撕裂带相对撕裂带的大小主要决定于相对间隙相对间隙对撕裂带的影响如图3一20所示曲线2表示冲孔时在凸模尺寸与冲孔件尺寸相等(6凸孔二O)情况下厚度对合理大
间隙的影响图32曲线1表示落料时在毛刺高度为最小时板料厚度对合理大间隙的影响
物
(次
)
吝
飞
奄图321板料厚度一合理大间隙曲线
(WSPA8
23一12mm
)
落料6凹件二02冲孔6
凸
孔
=0
曲线2表示冲孔时在毛刺高度为最小时厚度对合理大间隙的影响
,一3=I谙爷巴吝
姗淋少
龟丫。,。2
。,。,
“一
瓜`
,,
图320wSPA型钢板相对撕裂带一相时间隙
曲线
1冲孔件t二23m
m2落料件t二23om
3冲孔件t二6mm4落料件t二6mm
t《m
成协
冷互3
10板料厚度一合理大间隙试验
为了探讨板料厚度对合理大间隙的影响曾经对厚度为2334681012mm的wsPA钢板进行试验
图321曲线1表示落料时在凹模尺寸与落料件尺寸相等(6凹件二0)情况下厚
度
对合理大间隙的影响
图322板料厚度一合理大间隙曲线(落料)
(WSPA623~12mmh二hmi)
图323曲线1表示落料时在相对光亮带
为l3/时厚度对合理大间隙的影响
曲线2表示冲孔时在相对光亮带为l/3时厚度对合理大间隙的影响
由上述各图可见在一般情况下厚度
愈大合理大间隙值愈大虽31板料厚度一最小毛刺高度试验落料时板料厚度对最小毛刺高度的影响如表毛冲孑L时板料厚度对最小毛刺高度的影响
如表2
(模具工业)1990No12总118愁43国内外非金属板料冲裁间隙国内外有关单位的非金属材料冲裁间隙数据亦各不相同但均在1一
8
%之间
执4冲裁间隙分类方法
où苍
ǎ
义岁à
吝
248
`口t
,。
护
图323板料厚度一合理大间隙曲线
(WSPA62
3~12mm△八二z/3
)
表1
t(
m
m
)
2
334810012
h。`(nu)00220042004440054006200822表2注(
mm
)2334810l2
hm。(nu)002600255004200480065501266
第四
讲冲裁间隙的分类方
法
狂:概述在冲压模具中冲裁模的比例约50一60%
而冲裁间隙的数值与分布均匀与否是影响冲裁件质量与模具寿命的关键
关于冲裁间隙的分类方法国内外各工厂各不相同合理的分类方法影响模具的设计与制造作者根据国内外目前对于冲裁间隙
的分类方法从生产实际出发加以分析归纳,结合大量的工艺试验提出下列分类法:
大间隙
冲裁裁
孰2国内外金属板料冲裁间隙国内外金属冲裁的间隙数据各不相同
,
其中美国工具与加工工程师协会(ASTME)
的间隙将间隙分为五大类国内有些工厂也
仿照这种分类法制订本单位的冲裁间隙标准本文在此不再详述
作者曾经对国内外关于冲裁间隙的研究情况加以分析在继承前人的研究成果的基础上对板料冲裁问题进行两方面的研究工作一方面从力学分析与微观组织研究了冲裁过程的机理;另一方面在生产条件下对板料冲裁间隙进行大拳的试验研究
为完成各种不同材料与厚度板料的冲裁试验,共设计与制造了三套高精度的尺寸规格不同的试验模具(试件真径为才20之30
必somm)对厚度分别为01一12mm的板料均进行间隙为z八二1一50肠的冲裁试验为了研究如何在简易模具中通过合理大间隙以
延长寿命作者还设计与制造了一系列简易冲裁模其中包括厚板模薄板模薄片模钢带冲模`夹板模局部开孔模以及钢刃口
一锌基合金冲裁模这些模具的试制成功
为
合理大间隙在简易模具上的应用创造了有利条件为保证试验数据的可靠性所有的试验
模具的模架均采用浮动模柄与滚珠导柱以
避免冲床与模架精度对凸凹模之间间隙均匀性的影响每套模具均备有60一70个直径不同的凸模以适应不同厚度与不同间隙的冲裁试验
作者先后对210种不同牌号与厚度的常用金属板料进行冲裁试验各种板料的试验间
隙取值为l一50%各取十种间隙共冲裁1050。个试件测得63QOO个试验数据绘
制了630条试验曲线利用经过处理的数据而获得210种板料的合理间隙值建立了板
料冲裁间隙数据库并编制了手册在大量工艺试验的基础上以试验结果与生产实际为依据作者提出新的冲裁间隙分类法我们认为冲裁间隙可以分为两大类—小间隙冲裁与大间隙冲裁对于厚度在0smm
以下的冲裁件为了确保冲裁件较
高
的质量在二般情况下采用小间瞬冲裁;对于厚度在osmm以上的一般冲裁件在满足
冲裁件质量的前提下为提高模具寿命在一般情况下应尽量采用大间隙仲裁而对于
《模
具
工业》1990N012总ns