IATF16949五大核心工具简介及五大工具关系总结
IATF介绍16949的五大核心工具

IATF介绍16949的五大核心工具一是介绍五大工具IATF五大工具16949分别是:过程控制的统计(SPC);测量系统分析(MSA);失效模式及效果分析(FMEA);预先规划产品质量(APQP);批准生产件的程序(PPAP)。
第二,实施五大工具的目的1.SPC(StatisticalProcessControl)(1)对过程进行可靠的评估;(2)确定过程的统计控制界限,判断过程是否失控,过程是否有能力;为过程提供早期报警系统,及时监控过程情况,防止废品发生;减少对常规检验的依赖,定期观察和系统测量方法取代了大量的检验和验证工作。
2.MSA(MeasurementSystemAnalysis)使用测量系统进行分析,以确保测量数据的准确性/质量。
(MSA)方法评估获取测量数据的测量系统;(2)确保使用合适的数据分析方法,例如使用。
SPC实验设计、方差分析、回归分析等工具。
(3)MSA测量系统的分辨率和误差采用数学统计和图表的方法进行分析,以评估测量系统的分辨率和误差是否适合被测参数,并确定测量系统误差的主要成分。
3.FMEA(FailureModeandEffectsAnalysis)(1)作为一种预防措施工具,其目的是发现,评估产品/过程中潜在的故障及其后果;能轻松、低成本地修改产品或过程,从而减少事后修改的危机;(3)找出可以避免或减少这些潜在故障的措施。
.APQP(AdvancedProductQualityPlanning)(1)为了满足产品、项目或合同的要求,在投入新产品之前,用于确定和制定一种结构化的过程,以确保特定产品或系列产品的生产能够满足客户的需求。
为了支持客户满意的产品或服务的开发,提供制定产品质量计划的指南。
5.PPAP(ProductPartApprovalProcess)(1)确定供应商对客户工程设计记录和规范的所有要求是否有正确的认识。
(2)在执行所需生产节拍条件下的实际生产过程中,具有持续满足这些要求的潜力。
IATF169492016五大核心工具
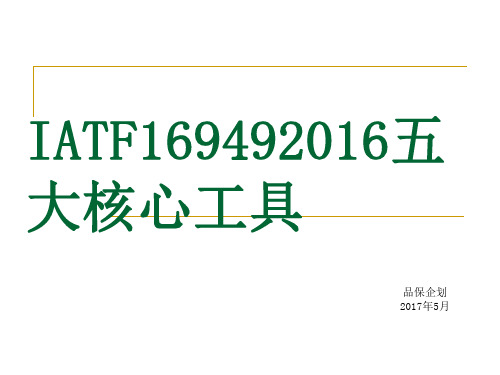
IATF169492016五大核心工具
测量系统 用于对被测特性赋值的操作、程序、量具、设备、 软件及操作人员的集合。
测量系统误差分成五种类型:偏倚、线性、稳定性、重复性和再现性。 盲测法
在实际测量环境下,在操作者事先不知正在对该测量系统进行评定的 条件下,获得测量结果。 基准值 也叫标准值,是一个基准。它可以通过采用更高级别的测量设备(例 如,计量实验室或全尺寸检验设备)进行多次测量,取其平均值来确 定的。 均值极差法 均值和极差法是一种提供测量系统重复性和再现性估计的数学方法。
稳定性 或称漂移,是测量系统在某一阶段时间内,测量同 一基准或零件的单一特性时获得的测量总变差。换 句话说,稳定性就是偏倚随时间的变化。
线性 在设备的预期操作(测量)范围内偏倚的不同被称 为线性。线性可以被认为是关于偏倚大小的变化。
IATF169492016五大核心工具
重复性 传统上,将重复性看作“评价人内”变异。它是由一个 评价人,采用同一种测量仪器,多次测量同一零件的同 一特性时获得的测量变差。它是设备本身固有的变差或 性能。重复性一般指仪器的变差(EV)。事实上,重复 性是从规定的测量条件下连续试验得到的普通原因(随 机误差)变差。
再现性 传统上,把再现性看作“评价人之间”的变异。定义为 由不同的评价人,采用相同的测量仪器,测量同一零件 的同一特性时测量平均值的变差。通常指AV——评价人 变差。
IATF169492016五大核心工具
数值<10%的误差测量系统可接受。 10%≤数值≤30%的误差测量系统可接受或不接受, 决定于
传统上,精密度描述了测量系统在操作范围(大小、量程和 时间)内分辨力、灵敏度和重复性的最终影响。精密度最常用于描述测 量范围内重复测量的预期变差,测量范围也许是大小或时间。
iatf16949五大质量工具详解及运用案例

iatf16949五大质量工具详解及运用案例在汽车行业中,质量管理是至关重要的,因为质量问题可能导致严重的安全隐患和巨大的经济损失。
为了确保汽车制造商和供应商的质量标准,国际汽车任务力量(IATF)制定了一系列质量管理要求,其中包括了五大质量工具,分别是:流程流程图、测量系统分析(MSA)、统计过程控制(SPC)、故障模式与效应分析(FMEA)和8D问题解决方法。
本文将详细介绍这五大质量工具的概念和用途,并提供相关案例以展示它们的运用。
1. 流程流程图(Process Flow Diagram)流程流程图是一种用来描述和分析制造过程的工具,通过可视化地展示各个步骤和流程之间的关系,帮助人们理解整个制造流程,并识别潜在的质量问题和瓶颈。
流程流程图通常以图表的形式呈现,其中包含了输入、输出、关键步骤、检查点和控制点等信息。
案例:一家汽车制造商使用流程流程图来分析其汽车装配流程。
通过绘制装配线的各个步骤和工位,并标注每个步骤的输入和输出,该制造商能够清楚地了解到每个工位的功能和责任。
在制造过程中,该公司发现一个质量问题,通过对流程流程图的分析,他们发现问题出现在一个关键步骤上,因为该步骤的输入与输出不匹配。
通过对该步骤进行调整和改进,该制造商成功地解决了质量问题,提高了产品的质量和效率。
2. 测量系统分析(Measurement System Analysis,MSA)测量系统分析是一种用来评估和确认测量过程的可靠性和准确性的方法。
在汽车制造中,准确的测量是确保产品质量的关键,而测量系统分析则能帮助汽车制造商评估和优化其测量系统,确保其测量结果的可靠性。
案例:一家汽车零部件供应商使用测量系统分析来评估其测量设备的准确性。
通过进行重复性和再现性测试,他们能够确定测量设备的误差和变异程度。
在进行测量系统分析后,该供应商发现一个测量设备存在较大的误差,导致了产品质量的下降。
他们随后采取了纠正措施,修复了该设备,并通过再次进行测量系统分析确认了其准确性和稳定性。
IATF五大核心工具

IATF五大核心工具IATF(International Automotive Task Force)是由全球汽车行业的主要制造商和汽车零部件制造商所联合组成的一个组织。
IATF的目标是通过推动供应商发展来提高汽车质量和安全性。
IATF所推行的质量管理体系,是全球汽车工业所公认的最高水平的质量管理要求,也是目前汽车工业的主流标准。
IATF认证是一种证明汽车供应商具有质量管理体系的证明,是他们能够参与到汽车生产的关键因素之一。
IATF五大核心工具是指要求供应商必须熟练掌握和使用的五个工具。
这些工具是:测量系统分析(MSA)、统计过程控制(SPC)、高级产品质量计划(APQP)、生产部件批准程序(PPAP)和故障模式及影响分析(FMEA)。
下文将介绍这五个核心工具的基本概念和用途。
测量系统分析(MSA)测量系统分析是一种评估测量系统可靠性和稳定性的方法。
其目的是确保测量结果稳态,可靠性和有效性。
MSA分析可以帮助企业评估和提高测量系统性能,从而提高产品和服务质量。
MSA的主要应用包括生产过程中的测量和测试、测量设备定期校准和制造过程的监控。
MSA的方法包括重复性和再现性的测量和分析,误差和偏差的分析和处理,以及不确定性的评估和解决。
MSA分析常用的工具包括直方图、因果图和流程图等。
统计过程控制(SPC)统计过程控制是一种基于统计方法的制造过程控制方法。
SPC的目的是在制造过程中,通过对生产数据进行收集和分析,发现制造过程中的变异,并采取相应控制措施,以确保产品质量稳定和一致。
SPC常用于生产过程中的变异控制、通过数据分析优化生产过程和提升生产效率等方面。
SPC的方法包括测量数据收集,分析和控制。
常用方法包括控制图、直方图、X带R图和P带C图等。
高级产品质量计划(APQP)高级产品质量计划是一种在产品开发初期规划和控制质量的过程。
APQP的目的是确保产品符合用户需求和设计要求。
这种质量管理方法强调全面规划和质量控制,保证产品从外观、性能和质量等多个方面满足用户需求,并满足相关法律法规和安全标准。
16949质量体系五大核心工具

TS16949五大工具分别是:产品质量先期筹划〔APQP〕、测量系统分析〔MSA〕、统计过程控制〔SPC〕、生产件批准〔PPAP〕和潜在失效模式与后果分析〔FMEA〕第一:APQP 产品质量先期筹划一、QFD 简介-简单介绍APQP的背景和根本原那么二、APQP详解〔五个阶段〕1〕工程确实定阶段●立项的准备资料和要求●立项输出的结果和记录2〕产品研发阶段●产品研发需要事先考虑和参考的要求和信息,以确保尽可能预防产品设计问题的产生●产品研发阶段输出的结果和记录3〕过程研发阶段●过程研发需要事先考虑和参考的要求和信息,以确保尽可能预防生产中问题的产生●过程研发阶段输出的结果和记录4〕设计方案确实认●进行试生产的要求和必须的输出结果5〕大规模量产阶段●持续改进三、控制方案●控制方案在质量体系中的重要地位●控制方案的要求第二:MSA 测量系统分析测量系统必须处于统计控制中,这意味着测量系统中的变差只能是由于普通原因而不是由于特殊原因造成的。
这可称为统计稳定性;测量系统的变差必须比制造过程的变差小;变差应小于公差带;测量精度应高于过程变差和公差带两者中精度较高者,一般来说,测量精度是过程变差和公差带两者中精度较高者的十分之一;测量系统统计特性可能随被测工程的改变而变化。
假设真的如此,那么测量系统的最大的变差应小于过程变差和公差带两者中的较小者。
一、MSA的目的、适用范围和术语二、测量系统的统计特性三、测量系统变差的分类四、测量系统变差〔偏倚、重复性、再现性、稳定性、线性〕的定义、图示表达方式五、测量系统研究的准备六、偏倚的分析方法、判定准那么七、重复性、再现性的分析方法、判定准那么八、稳定性的分析方法、判定准那么九、线性的分析方法、判定准那么十、量型测量系统研究指南十一、量具特性曲线十二、计数型量具小样法研究指南十三、计数型量具大样法研究指南十四、案例研究第三:PPAP 生产件批准程序PPAP的目的是用来确定供方是否已经正确理解了顾客工程设计记录和标准的所有要求,并且在执行所要求的生产节拍条件下的实际生产过程中,具有持续满足这些要求的潜能,是目前最完善的供应商选择与控制系统。
iatf 16949 质量管理体系 五大工具

iatf 16949 质量管理体系五大工具
IATF 16949质量管理体系是汽车行业的质量管理体系标准,
它是汽车行业供应链中的一种认可和要求。
它强调了连续改进、缺陷预防和减少变动和浪费的重要性。
其中,五大工具是指在IATF 16949标准中被推荐使用的五种质量管理工具,它们有
助于实现质量目标和持续改进。
1. 流程流程流程管理(FMEAs):失效模式和影响分析(FMEAs)
是一种评估潜在失效模式和其对产品、工艺和系统的影响的方法。
它旨在提前识别可能出现的问题,并采取预防措施来减少潜在的质量问题。
2. 统计过程控制(SPC):统计过程控制是一种监测过程稳定性
和预测可能质量偏差的方法。
它通过收集和分析数据,以及对过程变化进行控制,确保生产的产品符合预定的质量要求。
3. 量测系统分析(MSA):量测系统分析用于评估和确认测量系
统的准确性、精确度和可重复性。
它确保在检测和测量过程中使用的测量系统可靠,并能提供准确的数据。
4. 过程能力(PPAP):生产工序批准程序(PPAP)是一个文件包,用于验证生产过程能力和确认供应商是否满足汽车行业的特定质量要求。
它包括工程评审、样品检验和生产线验证等步骤。
5. 8D问题解决(8D):8D问题解决是一种结构化的方法,用于
解决和纠正质量问题并防止再次发生。
它包括八个步骤,涵盖问题定义、团队组建、原因分析、纠正措施、预防措施等内容。
使用这五大工具,组织可以更好地管理和改进质量,提高生产和产品质量,并满足IATF 16949标准的要求。
干货 IATF16949五大核心工具介绍
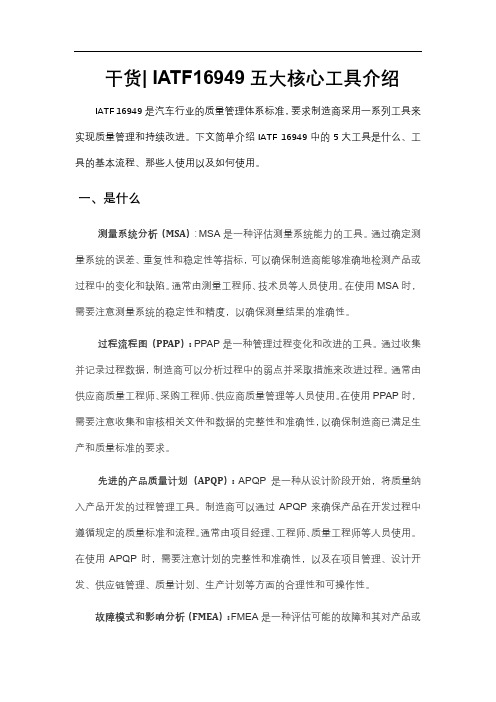
干货| IATF16949五大核心工具介绍IATF 16949是汽车行业的质量管理体系标准,要求制造商采用一系列工具来实现质量管理和持续改进。
下文简单介绍IATF 16949中的5大工具是什么、工具的基本流程、那些人使用以及如何使用。
一、是什么测量系统分析(MSA):MSA是一种评估测量系统能力的工具。
通过确定测量系统的误差、重复性和稳定性等指标,可以确保制造商能够准确地检测产品或过程中的变化和缺陷。
通常由测量工程师、技术员等人员使用。
在使用MSA时,需要注意测量系统的稳定性和精度,以确保测量结果的准确性。
过程流程图(PPAP):PPAP是一种管理过程变化和改进的工具。
通过收集并记录过程数据,制造商可以分析过程中的弱点并采取措施来改进过程。
通常由供应商质量工程师、采购工程师、供应商质量管理等人员使用。
在使用PPAP时,需要注意收集和审核相关文件和数据的完整性和准确性,以确保制造商已满足生产和质量标准的要求。
先进的产品质量计划 APQP):APQP是一种从设计阶段开始,将质量纳入产品开发的过程管理工具。
制造商可以通过APQP来确保产品在开发过程中遵循规定的质量标准和流程。
通常由项目经理、工程师、质量工程师等人员使用。
在使用APQP时,需要注意计划的完整性和准确性,以及在项目管理、设计开发、供应链管理、质量计划、生产计划等方面的合理性和可操作性。
故障模式和影响分析(FMEA):FMEA是一种评估可能的故障和其对产品或过程的影响的工具。
通过FMEA,制造商可以预测和减少潜在的故障,并提高产品的可靠性。
通常由质量工程师、工程师、设计师、供应商等人员使用。
在使用FMEA时,需要注意完整性和准确性,即对可能出现的故障进行充分的分析和评估,以确保产品的可靠性和安全性。
统计过程控制(SPC):SPC是一种在制造过程中监控产品质量的工具。
通过对过程进行实时监控,制造商可以检测和纠正生产过程中的缺陷,并避免不必要的浪费和损失。
IATF16949五大工具之间的关系

IATF16949五大工具分别是:MSA、FMEA、PPAP、SPC、APQP
APQP——质量先期策划
PPAP——生产件批准程序
SPC——统计制程控制
MSA——测量系统分析
FMEA——潜在失效模式分析
这其中以APQP为纽带贯穿始终,其它四大工具分别在总流程的某个重要环节起作用。
APQP中有5个过程:项目策划-----设计开发-----过程设计-----过程确认----量产及持续改进
所以由上可以看出:
一、PPAP和APQP什么关系?
PPAP属于APQP的第四阶段。
二、而SPC,MSA,FMEA和PPAP又什么关系呢?
SPC,MSA,FMEA属于PPAP需要提交的19项材料中的3项。
三、SPC和FMEA的关系是什么?
FMEA的严重程度高,发生频度高,探测力差,那么需要用SPC 控制。
四、SPC和MSA的关系是什么?
需要做好SPC,必须前提是测量系统没有问题。
由此看出,MSA是SPC的前提条件。
以上就是TS16949五大工具之间的关系,理顺这些关系,才能做好TS16949质量体系认证。
- 1、下载文档前请自行甄别文档内容的完整性,平台不提供额外的编辑、内容补充、找答案等附加服务。
- 2、"仅部分预览"的文档,不可在线预览部分如存在完整性等问题,可反馈申请退款(可完整预览的文档不适用该条件!)。
- 3、如文档侵犯您的权益,请联系客服反馈,我们会尽快为您处理(人工客服工作时间:9:00-18:30)。
IATF16949五大核心工具简介及五大工具关系总结
1、统计过程控制(SPC)
SPC是一种制造控制方法,是将制造中的控制项目,依其特性所收集的数据,通过过程能力的分析与过程标准化,发掘过程中的异常,并立即采取改善措施,使过程恢复正常的方法。
实施SPC的目的:
•对过程做出可靠的评估;
•确定过程的统计控制界限,判断过程是否失控和过程是否有能力;
•为过程提供一个早期报警系统,及时监控过程的情况以防止废品的发生;
•减少对常规检验的依赖性,定时的观察以及系统的测量方法替代了大量的检测和验证工作
2、测量系统分析(MSA)
测量系统分析(MSA)是对每个零件能够重复读数的测量系统进行分析,评定测量系统的质量,判断测量系统产生的数据可接受性。
实施MSA 的目的:了解测量过程,确定在测量过程中的误差总量,及评估用于生产和过程控制中的测量系统的充分性。
MSA促进了解和改进(减少变差)。
在日常生产中,我们经常根据获得的过程加工部件的测量数据去分析过程的状态、过程的能力和监控过程的变化;那么,怎么确保分析的结果是正确的呢?我们必须从两方面来保证:
(1)是确保测量数据的准确性/质量,使用测量系统分析(MSA)方法对获得测量数据的测量系统进行评估;
(2)是确保使用了合适的数据分析方法,如使用SPC工具、试验设计、方差分析、回归分析等。
MSA使用数理统计和图表的方法对测量系统的分辨率和误差进行分析,以评估测量系统的分辨率和误差对于被测量的参数来说是否合适,并确定测量系统误差的主要成分。
3、失效模式和效果分析(FMEA)
潜在的失效模式和后果分析(FMEA)作为一种策划用作预防措施工具,其目的是发现、评价产品/过程中潜在的失效及其后果;找到能够避免或减少潜在失效发生的措施并不断地完善。
实施FMEA的目的:
能够容易、低成本地对产品或过程进行修改,从而减轻事后修改的危机。
•找到能够避免或减少这些潜在失效发生的措施;
4、产品质量先期策划(APQP)
APQP是用来确定和制定确保产品满足顾客要求所需步骤的结构化方法。
APQP的功能:为满足产品、项目或合同规定,在新产品投入以前,用来确定和制定确保生产某具体产品或系列产品使客户满意所采取的一种结构化过程的方法。
为制订产品质量计划提供指南,以支持顾客满意的产品或服务的开发。
5、生产件批准程序(PPAP)
生产件批准程序为一种实用技术,其目的是在第一批产品发运前,通过产品核准承认的手续,验证由生产工装和过程制造出来的产品符合技术要求。
实施PPAP的目的:
•确定供方是否已经正确理解了顾客工程设计记录和规范的所有要求。
•并且在执行所要求的生产节拍条件下的实际生产过程中,具有持续满足这些要求的潜能。
五大质量工具是TS16949的核心,是经过证明适用于汽车行业的质量工具,对于提高汽车行业的质量管理水平和竞争力,将起到重要作用。
IATF16949五大工具的关系
这个话题如果没有实践的人一定是弄不清楚的,就算是有实践的人也未必能弄清楚,因为他们的相互交错。
福特用了一百年的时间画出的经典的APQP网络图,可见其用心之最。
在这里我对五大工具做简单的描述希望能给大家一个基本的概念。
APQP是在向整车厂提供新产品的时候,作为零部件公司必须要做的一项工作,意在产品未进行生产之前把所有的问题解决掉,所以它是个复杂的过程,也是需要几个来回反复才会成为最后策划的结果。
FMEA则是在APQP的二三阶段时进行的失效模式分析,包括产品和过程,这里最重要的一点是这个时候产品并未生产出来,而是一种潜在的可能性分析,很多企业总是不习惯这一点,总是把它当成已经在生产的产品去分析。
精益生产促进中心。
SPC,MSA都是在对过程策划的过程中形成的东西,也就是说什么样的过程需要用SPC来控制,一般来说具有特殊特性的过程应该用SPC,当然也不是绝对。
这里需要说明的是控制计划,是APQP策划的结果,在这个结果中必然要用到测量工具,而这些测量工具是否能满足对过程测量的需要,需要用MSA来进行分析,简单地说控制计划中所涉及的测量器具都应该做MSA,然后在最初的控制计划中,也就是试生产的控制计划中,策划的测量工具或所选用的SPC未必能有好的效果,因些可能会进行调整和改进,最后形成正式生产的控制计划。
而正式生产控制计划中的SPC和MSA 应该是能满足批量生产的需要。
简单地说:
APQP是质量计划,但其实也是项目开发的计划。
既然是计划,它的时间起点是项目正式启动的那一时间点到PPAP结束,正常量产后进行总结,认为没有其他问题,可以关闭开发项目的那一时间点为止。
执行人是整个APQP小组。
PPAP是生产件批准程序,只是整个APQP 计划中的一个环节,通常居于APQP计划的后半阶段,一般来讲是APQP计划的核心。
若PPAP没有获得客户的批准,那么APQP的计划基本要泡汤。
因此我们谈论起APQP,总是把它们说在一起:APQP/PPAP。
由此可见PPAP的重要性。
主要执行人是(开发、生产、质量)工程师。
、
FMEA/SPC/MSA都是质量管理的工具。
诚如有朋友指出的,FMEA有DFMEA, PFMEA,这些工作的导入事件多为APQP的初期或中、早期。
它们主要正对的产品的设计、生产工艺或过程而言的。
属于预防性的计划。
MSA很简单,就是校对量、检具。
不要把任何一切都看得很复杂。
SPC 也很简单,就是管制住某几个重要参数,监督它们生产的稳定性。
若发现有较大的波动,则立即采取措施,纠正工艺或生产流程。
MSA与SPC一样,都在PPAP阶段实施比较妥当(太早有很多影响因素导致MSA无效等)。
实施者多为质量工程师。
SPC往往会根据客户的不同要求,在以后正式量产的长期过程中都需要实施下去。