汽车空-空中冷器技术条件
空冷器管束制造及检验关键技术分析
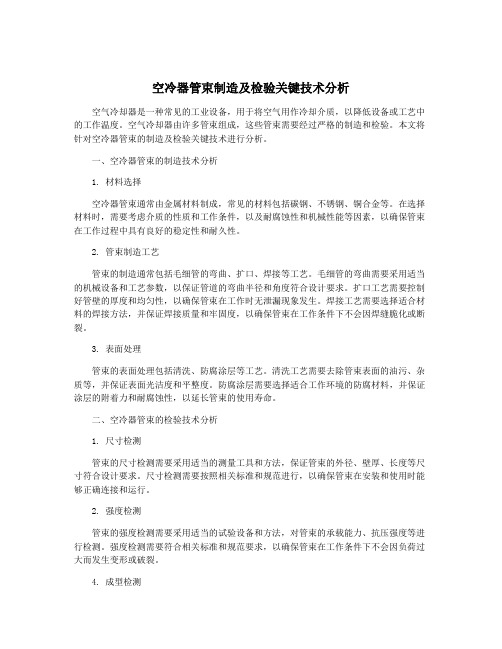
空冷器管束制造及检验关键技术分析空气冷却器是一种常见的工业设备,用于将空气用作冷却介质,以降低设备或工艺中的工作温度。
空气冷却器由许多管束组成,这些管束需要经过严格的制造和检验。
本文将针对空冷器管束的制造及检验关键技术进行分析。
一、空冷器管束的制造技术分析1. 材料选择空冷器管束通常由金属材料制成,常见的材料包括碳钢、不锈钢、铜合金等。
在选择材料时,需要考虑介质的性质和工作条件,以及耐腐蚀性和机械性能等因素,以确保管束在工作过程中具有良好的稳定性和耐久性。
2. 管束制造工艺管束的制造通常包括毛细管的弯曲、扩口、焊接等工艺。
毛细管的弯曲需要采用适当的机械设备和工艺参数,以保证管道的弯曲半径和角度符合设计要求。
扩口工艺需要控制好管壁的厚度和均匀性,以确保管束在工作时无泄漏现象发生。
焊接工艺需要选择适合材料的焊接方法,并保证焊接质量和牢固度,以确保管束在工作条件下不会因焊缝脆化或断裂。
3. 表面处理管束的表面处理包括清洗、防腐涂层等工艺。
清洗工艺需要去除管束表面的油污、杂质等,并保证表面光洁度和平整度。
防腐涂层需要选择适合工作环境的防腐材料,并保证涂层的附着力和耐腐蚀性,以延长管束的使用寿命。
二、空冷器管束的检验技术分析1. 尺寸检测管束的尺寸检测需要采用适当的测量工具和方法,保证管束的外径、壁厚、长度等尺寸符合设计要求。
尺寸检测需要按照相关标准和规范进行,以确保管束在安装和使用时能够正确连接和运行。
2. 强度检测管束的强度检测需要采用适当的试验设备和方法,对管束的承载能力、抗压强度等进行检测。
强度检测需要符合相关标准和规范要求,以确保管束在工作条件下不会因负荷过大而发生变形或破裂。
4. 成型检测管束的成型检测包括毛细管的弯曲半径、角度、扩口均匀性等方面的检测。
成型检测需要采用适当的检测设备和方法,保证管束的成型质量符合设计要求,以确保管束在工作过程中不会因成型不良而发生故障。
空冷器管束的制造及检验关键技术对管束的质量和性能具有重要影响。
空冷凝汽器技术规范书

久泰能源内蒙古有限公司100万吨甲醇10万吨二甲醚项目热电工程50M W抽凝机组直接空冷系统技术规范书久泰能源内蒙古有限公司2007年11月本规范书适用于久泰能源内蒙古有限公司100万吨甲醇10万吨二甲醚项目热电工程汽轮机配套用直接空冷凝汽器系统及系统内附属设备的供货,它提出空冷系统的设计、性能及所属设备的功能、结构、制造、安装和试验等方面的技术要求,以及明确了设计和供货范围、设计接口等。
本规范书仅限于招、投标阶段使用。
1 项目说明1.1 项目名称:久泰能源内蒙古有限公司100万吨甲醇10万吨二甲醚项目热电工程1.2 业主名称:久泰能源内蒙古有限公司1.3 工程概况本项目装机规模为:3×240t/h高温高压循环流化床锅炉+1×50MW抽汽凝汽式汽轮发电机组。
汽轮机由南京汽轮电机(集团)有限责任公司提供。
交货地点为内蒙古自治区鄂尔多斯市准格尔旗大路工业园区该项目施工现场。
2 技术要求2.1 总体要求2.1.1空冷器系统应由卖方保证整体性能,保证所提供的空冷器系统技术性能和经济指标处于国内先进水平,保证系统应持续、安全、高效地运行不低于30 年。
2.1.2 卖方所提供的设备,应是全新、高性能、安全、运行经济、功能完整的空冷器系统,所有设备应无外部变形、振动或腐蚀。
2.1.3卖方负责系统的成套设计,设计时必须考虑空冷器系统的占地面积、重量和连接管道的阻力降,以减少支撑结构的负担和保证汽轮机的正常运行。
2.1.4 卖方应负责供货范围内设备的设计、制造、供货、服务、安装指导、调试和性能测试。
2.1.5 本技术规范为空冷器系统的最低要求,并未规定所有的技术要求和使用标准,在不降低协议提出的安全度与可靠性的条件下,不限制新技术的使用。
2.1.6 本技术规范中所提供的设备,应遵循所有相关规范和标准,以及安装现场所在地的法律和条例,包括卫生、安全和环保(H.S.E)。
卖方应保证遵守。
2.1.7 空冷器系统应满足本技术规范的文字说明、工作范围及附图陈述的所有要求,如果发生矛盾,以较高的要求为准并需由买方确认。
石化空冷器

空气冷却器技术及设备空气冷却器是以环境空气作为冷却介质,对管内高温流体进行冷却或冷凝的设备,它具有不需要水源,适用于高温、高压的工艺条件,使用寿命长,运转费用低等优点。
随着水资源和能源的匮乏以及环保意识的增强,节水、节能、无污染的空气冷却器将会得到更广泛的应用。
一、空冷器的应用与水作为冷却介质的传统工业冷却系统相比,空冷的优缺点如表1和表2所示。
由表可见,在缺水地区(如沙漠地带)或水冷结垢和腐蚀严重的地区,适合采用空冷器。
一般在下述条件下采用空冷比较有利。
(1) 热流体出口温度与空气进口温度之差>15℃。
(2) 热流体出口温度>60℃,其允许波动范围>5℃。
(3) 空气的设计气温<38℃。
(4) 有效对数平均温度差≥40℃。
(5) 管内热流体的给热系数<2300 W/(m2 *℃)。
(6) 热流体的凝固点<0℃。
(7) 管侧热流体的允许压降>10kPa,设计压力>100kPa。
二、空冷器的型式空冷器由管束、风机、构架三个基本部分和百叶窗、风筒、喷淋装置、梯子、平台等辅助部分组成,每个管束有若干排三角形排列的管子,该管子一般是翅片管,也可以是光管。
介质的流向通常是逆流,热流体从管束顶端流入,底部流出,空气由下向上流动,冷却热的工艺介质。
另外还有风机、百叶窗、构架和风箱等部件,风机驱动空气流过管束,百叶窗通过调节进入空冷器的空气量来改善空冷器的调节和适应性能,构架是支撑管束、风机,百叶窗以及其它附属件的钢结构,风箱用于导流空气。
空冷器按管束布置方式可分为水平式和斜顶式;按通风方式可分为鼓风式和引风式;按冷却方式可分为干式、湿式和干湿联合式。
2.1 管束表3管束的型式与代号a 鼓风式水平管束(GP)b 引风式水平管束(YP)c 斜顶管束(X)d 湿式立置管束(SL)e 干湿联合斜置(SX)f 减压塔顶空冷器(YSX)图1 管束型式a:L型翅片管(L)b:LL型翅片管(LL)c:滚花型翅片管(KL)d:双金属轧制翅片管(DR)e:镶嵌型翅片管(G)f椭圆管套矩形片翅片管(TC)g:板翅片翅片管(T60)图2 翅片管型式a 光滑平面法兰b 凹凸面法兰c 榫槽式法兰d 透镜垫式法兰e 梯型槽面法兰图3 法兰密封面型式丝堵式管箱(C)可卸盖板式管箱(K)可卸帽盖式管箱(K2)全焊接圆帽管箱(Q)集合管式管箱(J)图4 管箱型式1.1.2 常用换热元件规格及特性常用换热元件(翅片管)规格(见表2),翅片管翅化比表(见表3),特性比较表(见表4)表2 常用换热元件规格表。
空气冷却器的设计

图 1 最佳管排数算图 图中 : T 1 ———管内热流体入口温度 , K;
t 1 ———空气入口温度 , K; u0 ———总传热系数 (以光管外表面积为基准) ,J / (m2·s·K) 。
一般来讲 ,希望管内流体的凝固点不超过 5 ℃, 流体较干净且不易聚合 。热流体的入口温度 ,一般 以 120~130 ℃左右或以下为好 ,且不宜低于 60~ 80 ℃。热流体出口温度 ,对于干式空冷来讲 ,一般应 使其与设计气温温差大于 20 ~ 25 ℃, 至少要大于 15 ℃,否则不一定经济 。国外亦有人认为[1 ] : 一般 情况下 ,热流体出口温度与周围空气温度相差 17~ 22 ℃比较经济 ,最少也要相差 11~14 ℃。
X1 与出口汽相分率
X2
的算术平均值 。即 : X
=
1 2
( X1 + X2) 。
X1 =
GWV1 GWV1 + GWL1
X2 =
GWV2 GWV2 + GWL2
式中 : hL ———假定管内全部是液体时的膜传热系
数 ,由式 (6) 计算出 hi 代入 。计算时 ,
G = GV1 + GL1 = GV2 + GL2 ,物性数据
算系数 ; A f ———翅片表面积 ,m2 ;
A r ———管子外表面积扣除被翅片所占面积后 的剩余面积 ,m2 。
须指出 ,式中的 λ0 ,μ0 , C0 都是以平均温度选 取的空气物性 。
式 (2) 与式 (3) [3 ] ,误差一般在 5 %左右 。
当采用光管管束时 ,可采用简化公式 (5) 进行近
空冷器认证 标准

空冷器是一种常用于工业生产、公共场所通风换气等领域中的散热设备。
为了确保其安全、稳定运行,国内相关部门对空冷器的规格、技术指标、安全性等方面制定了一系列的行业标准和国家标准。
其中,空冷器国家标准主要是指GB/T 25119-2010《空气冷却设备基本术语、分类和结构》和GB/T 14294-2018《空气冷却设备通用技术条件》两个标准。
1. GB/T 25119-2010《空气冷却设备基本术语、分类和结构》
该标准规定了空冷器的定义、分类、构造、工作原理以及主要技术性能指标,包括换热表面积、通风量、空气侧压降等指标。
该标准适用于一般工况下的空冷器、翅片式空冷器、管式空冷器、热交换器等空气冷却设备的设计、制造和检验。
2. GB/T 14294-2018《空气冷却设备通用技术条件》
该标准详细规定了空冷器的一系列技术要求,包括通风量、散热面积、压降、耐压、耐腐蚀等方面的指标,同时还规定了试验方法、检验规则、标志、包装、运输等要求。
该标准适用于各种类型的空气冷却设备,包括工业散热器、冷凝器、空调蒸发器等。
汽车乘用车冷却系统布置及主要零部件设计规范
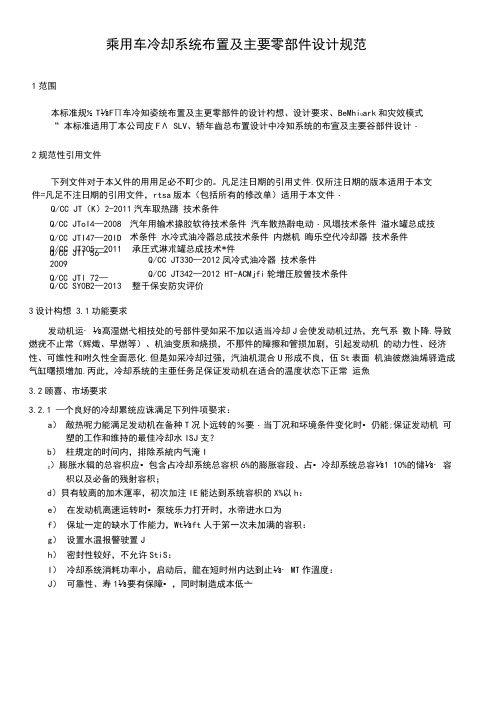
乘用车冷却系统布置及主要零部件设计规范1范围本标准规½T ⅛F∏车冷知姿统布置及主更零部件的设计杓想、设计要求、BeMhi U ark 和灾效模式“ 本标准适用丁本公司皮F Λ SLV 、轿年齒总布置设计中冷知系统的布宣及主要谷部件设计・ 2规范性引用文件下列文件对于本乂件的用用足必不町少的。
凡足注日期的引用丈件.仅所注日期的版本适用于本文 件=凡足不注日期的引用文件,rtsa 版本(包括所有的修改单)适用于本文件・Q/CC JT (K )2-2011汽车取热躊 技术条件汽年用输术掾胶软待技术条件 汽车散热辭电动・风塌技术条件 溢水罐总成技术条件 水冷式油冷器总成技术条件 内燃机 晦乐空代冷却器 技术条件 Q/CC JT33O —2012凤冷式油冷器 技术条件 Q/CC JT342—2012 HT-ACMjfi 轮增圧胶曾技术条件3设计构想 3.1功能要求发动机运∙⅛髙湿燃弋相技处的号部件受如采不加以适当冷却J 会使发动机过热,充气系 数卜降.导致燃疣不止常(辉熾、早燃等)、机油变质和烧损,不那件的障擦和管损加剧,引起发动机 的动力性、经济性、可维性和咐久性全面恶化.但是如采冷却过强,汽油机混合U 形成不良,伍St 表面 机油彼燃油烯驿造成气缸曙损增加.丙此,冷却系统的主亜任务足保证发动机在适合的温度状态下正常 运魚3.2顾喜、市场要求3.2.1 —个良好的冷却累统应诛满足下列件项娶求:a ) 敵热呢力能满足发动机在备种T 况卜远转的%要・当丁况和坏境条件变化时•仍能;保证发动机 可塑的工作和维持的最佳冷却水ISJ 支?b ) 柱規定的时间内,排除系統内气淹IC )膨胀水辑的总容枳应•包含占冷却系统总容枳6%的膨胀容段、占•冷却系统总容⅛1 10%的储⅛∙容 枳以及必备的残射容枳;d )貝有较离的加木運率,初次加注IE 能达到系统容枳的X%以h :e ) 在发动机离速运转时•泵统乐力打开时,水帝进水口为f ) 保址一定的缺水丁作能力,Wt ⅛ft 人于笫一次未加满的容积:g ) 设置水温报警驶置Jh ) 密封性较好,不允许StiS :I ) 冷却系统消耗功率小,启动后,龍在短时州内达到止⅛∙MT 作溫度:J ) 可靠性、寿1⅛要有保障•,同时制造成本低亠Q/CC JToI4—2008 Q/CC JTI47—2OID Q/CC JTl 56—2009Q/CC JTl 72—Q/CC JT305—2011 承圧式淋朮罐总成技术*件 Q/CC SY0B2—2013 整千保安防灾评价3.2.2随右冷却系统的发展,电控冷却系统即将取代传統的冷知系统,冷却系统部件也随之增加" 33相关法规要求相关的法规莹求见本标准在条款中所规范性引用的冇关文件, 4设计要求41冷却系统的总体布直4 1 1冷却系统总布罢主翌考坦两方面:U)空气流通系统:b)冷却術坏系统,4 1. 2在设汁中必须做JiIffir⅛St风系数和冷却液循坏中的散热机力亠4 1.3尽Mffiδ⅛ft进K系敎,总的进址口有效面族和散热器芯休疋面枳之比不小T* 15⅛ CCFKOlI车型实测及验证数Ie).・故热模块茴端需要加导风装負使风能有吹到故热器的正荷秋上,捉高散M器的和用率,冷空气从车头而罩流入,经散热器芯部,空气温反升高,热空气被入机舱,从发动机两側和底部甘出,在布置过程中应特别注说以F二点:H)冷却枳块曲端尽可能不被阻挡,否则会造成空代进代配力增加从而降低JSK^数;D 由于风席丁作后,会造成风朗的前后斥差较人,部分储空气通过周者朮它路轻从后部高乐处冋流到丽端低圧处,所权必须增加密钊装負:C)风扇中心偏离散热器茁部中心不atiiΛ4o轴向护旳过近,否则κ⅛,⅞⅞能不能得封充分发挥,容品左Ift烛养上形成气流“死金",便气流产生人^i⅛i⅛或者iffi流损失亠4 14 —农完整的冷却.系统示心见圈1・系统中的主更不部件布置间隙应符fr Q/CC SY082-2013中飽相关规定。
QC汽车行业标准
QC/T 222-1997
2010/8/16 2010/12/1
工科
113号
[2010]第
4. QC/T 460-2010 自卸汽车液压缸技术条件
QC/T 460-1999
2010/8/16 2010/12/1
工科
113号
[2010]第
3. QC/T 825-2010 自卸汽车液压系统技术条件
2010/8/16 2010/12/1
工科
113号
[2010]第
2. QC/T 223-2010 自卸汽车试验方法
1. QC/T 560-2010 散装水泥车技术条件及性能试验方法
2010年工信部批准发布的行业标准——工科[2010]第113号 代替标准 QC/T 560-1999 QC/T 561-1999 QC/T 223-1997
113号
[2010]第
16. QC/T 833-2010 汽车空调用压力安全阀技术条件
2010/8/16 2010/12/1
工科
113号
2010
O形橡胶密封圈
[2010]第
15. QC/T 666.1- 汽车空调(HFC-134a)用密封件 第1部分: QC/T 666-2000
2010/8/16 2010/12/1
工科
113号
[2010]第
7. QC/T 667-2010 混凝土搅拌运输车技术条件和试验方法 QC/T 667-2000 QC/T 668-2000
8. QC/T 449-2010 保温车、冷藏车技术条件及试验方法 QC/T 449-2000 QC/T 450-2000
9. QC/T 828-2010 汽车空-空中冷器技术条件
发动机中冷器工作原理
发动机中冷器工作原理
发动机中冷器是一种用于降低发动机进气温度的设备,其工作原理是通过利用空气冷却的特性来将高温的进气冷却到较低的温度,以增加发动机的效率和性能。
工作原理如下:
1. 进气道:发动机进气道中的空气首先经过滤空气进入中冷器。
2. 中冷器:中冷器是由一系列高效的冷却管组成的。
热空气在管道中流动时,与管道壁接触并传热。
冷却管外部的空气在冷却器中流动,与管道内部的热空气进行热交换。
这样,热空气会被冷却,降低其温度。
3. 减压器:中冷器之后,气流会进入减压器。
减压器的作用是减小进气流动的速度和压力,从而提供更大的时间和空间进行冷却。
4. 冷却效果:通过中冷器的作用,进气温度将显著下降。
降低进气温度有助于增加稠化燃油蒸汽,提高燃烧效率,并减少气缸燃烧过程中的热负荷。
同时,冷却后的气体密度增加,使得更多的氧气进入涡轮增压器,进一步提高发动机的输出功率和扭矩。
总体而言,发动机中冷器通过降低进气温度,提高压缩空气的密度,增加氧气含量,从而提高发动机的效率和动力输出。
这
使得发动机在工作过程中能够获得更多的能量,提高燃烧效率,进而提升整体性能。
QC T 657-2000 汽车空调制冷装置试验方法
QC/T 657-2000(2000-11-06批准,2001-04-01实施)前言本标准参照日本工业标准JIS D 16l8-1992《汽车空调器试验方法》,在QC/T 72.2-1993《汽车空调制冷装置试验方法》的基础上修订的。
本标准由国家机械工业局提出。
本标准由全国汽车标准化技术委员会归口。
本标准起草单位:长春汽车研究所、东风汽车工程研究院、神龙汽车有限公司、上海德尔福汽车空调系统有限公司、岳阳恒立冷气设备股份有限公司。
本标准主要起草人:付琦、郭亮、方劲、董国平、赵国军。
中华人民共和国汽车行业标准汽车空调制冷装置试验方法 QC/T 657-2000代替QC/T 72.2-19931 范围本标准规定了汽车空调制冷装置(以下简称空调装置)的试验方法。
本标准适用于以调节乘员舱内空气为目的的汽车空调装置。
2 引用标准下列标准所包含的条文,通过在本标准中引用而构成为本标准的条文,本标准出版时,所示版本均为有效。
所有标准都会被修订,使用本标准的各方应探讨使用下列标准最新版本的可能性。
GB/T 1236-1985 通风机空气动力性能试验方法GB/T 3785-1983 声级计的电、声性能及测试方法GB/T 4214-1984 家用电器噪声功率的测定GB/T 7676.1~7676.9-1998 直接作用模拟指示电测量仪表及其附件3 术语3.1 额定制冷量空调装置在规定的试验条件和试验设备下运行.达到稳定状态时,单位时间内蒸发器从空气中吸收的热量。
3.2 送风量测量制冷量时通过蒸发器的送风量。
3.3 量热计采用空气的焓差,测定空调装置降温除湿能力的装置。
3.4 冷却装置由蒸发器和风机组成,或由风机、蒸发器及加热器组成的装置。
3.5 带风机的冷凝器由冷凝器和风机(包括护风圈)组成的装置。
4 试验项目试验项目包括制冷量、风量、压缩机驱动功率及噪声。
5 试验条件5.1 空气状态蒸发器和冷凝器进风口的空气状态应符合表1的规定。
中冷器工作原理
中冷器工作原理
中冷器是一种用于汽车发动机增压系统的重要部件,它的主要作用是降低增压
空气的温度,提高进气密度,从而增加发动机的输出功率。
那么,中冷器是如何工作的呢?接下来,我们将详细介绍中冷器的工作原理。
首先,中冷器工作的基本原理是利用空气冷却的方式,将增压空气的温度降低。
当增压器将空气压缩后,空气的温度也随之升高。
而高温的压缩空气会降低其密度,从而影响发动机的燃烧效率。
因此,中冷器的作用就显得尤为重要。
其次,当增压空气通过增压器后,会进入中冷器的冷却管道。
在冷却管道内,
增压空气会与中冷器中流动的冷却介质进行热交换,从而使增压空气的温度得到降低。
冷却介质通常采用水或者空气,通过循环系统来实现对增压空气的冷却作用。
随后,经过中冷器冷却后的增压空气将进入发动机的进气道。
由于温度降低,
增压空气的密度增加,使得进入发动机燃烧室的空气更加充分,燃烧效率也随之提高。
这样一来,发动机就能够获得更多的氧气,从而实现更充分的燃烧,提高功率输出。
最后,需要指出的是,中冷器的工作原理是基于热力学的基本规律。
通过降低
增压空气的温度,中冷器有效地提高了发动机的进气密度,从而提高了发动机的输出功率。
这种工作原理不仅适用于汽车发动机,也同样适用于航空发动机等领域。
综上所述,中冷器通过降低增压空气的温度,提高了进气密度,从而增加了发
动机的输出功率。
它的工作原理基于热力学的基本规律,通过冷却介质对增压空气进行热交换,实现了对增压空气温度的降低。
因此,中冷器在汽车发动机增压系统中扮演着至关重要的角色,对发动机的性能提升起着关键作用。
- 1、下载文档前请自行甄别文档内容的完整性,平台不提供额外的编辑、内容补充、找答案等附加服务。
- 2、"仅部分预览"的文档,不可在线预览部分如存在完整性等问题,可反馈申请退款(可完整预览的文档不适用该条件!)。
- 3、如文档侵犯您的权益,请联系客服反馈,我们会尽快为您处理(人工客服工作时间:9:00-18:30)。
汽车空-空中冷器技术条件汽车空-空中冷器技术条件1 范围本标准规定了空-空中冷器的技术要求、试验方法、检验规则、标志、包装、运输、贮存以及质量保证。
本标准适用于本公司设计开发的汽车所装用的空-空中冷器总成(以下简称“中冷器”)。
2 规范性引用文件下列文件中的条款通过本标准的引用而成为本标准的条款。
凡是注日期的引用文件,其随后所有的修改单(不包括勘误的内容)或修订版均不适用于本标准,然而,鼓励根据本部分达成协议的各方研究是否可使用这些文件的最新版本。
凡是不注日期的引用文件,其最新版本适用于本标准。
GB 191—2000 包装储运图示标志GB/T 2828.1—2003 计数抽样检验程序第1部分:按接收质量限(AQL)检索的逐批检验抽样计划GB/T 3190—1996 变形铝及铝合金化学成分GB/T 3194—1998 铝及铝合金板、带材的尺寸允许偏差GB/T 3614—1999 铝合金箔GB/T 3880—1997 铝及铝合金轧制板材GB/T 4437.1—2000 铝及铝合金热挤压管第一部分:无缝园管YS/T 69—1993 钎接用铝合金板材Q/XX B102 车辆产品零部件追溯性标识规定3 技术要求3.1 中冷器应按经规定程序批准的图样和技术文件进行制造。
3.2 材料要求中冷器所用的相应材料,应分别满足GB 3880、YS/T 69、GB 4437.1、GB 3614、GB 3194、GB 3190的要求。
3.3 外观表面质量及尺寸3.3.1 铝合金板材的表面质量a) 板材表面不允许有裂纹、裂边、腐蚀、穿通气孔、硝盐痕,不允许有扩散斑点;b) 板材表面允许有轻微的压划痕等缺陷,但缺陷深度不得超过板材厚度的允许偏差,并应保证最小厚度。
3.3.2 钎接用铝合金板材的表面质量a) 板材表面不允许有裂纹、腐蚀、穿通气孔;b) 板材表面允许有轻微的压划痕。
3.3.3 铝合金管的表面质量a) 管材表面应光滑,不允许有裂纹;b) 管材表面的缺陷深度不得超过管材内、外径的允许偏差范围,并应保证管材的最小尺寸。
3.3.4 铝合金箔的表面质量a)铝合金箔的表面应洁净、平整,不允许有裂纹、压折、碰伤和腐蚀斑痕;b)合金箔的表面应整洁,不允许有碰伤、脏污,边部允许有不严重的毛边。
c)合金箔应缠在表面洁净的金属管上,管的内径为75+1mm,外径应不大于80 mm,管长应等于箔宽,但是最长不超过箔宽1.5 mm,直立取放时,不允许层与层间滑动及脱出。
d)合金箔箔卷内的断头次数,每卷不得多于1次。
3.4 外观质量要求3.4.1 冷却管焊缝应牢固、密封。
冷却管外表面应光洁、平直,不允许有明显的凹陷。
冷却管端面应平整、无毛刺、压皱和截面减少的现象。
3.4.2 每条散热带的波峰数允差为±1峰,波峰节距平均允差为±0.15 mm。
中冷器芯子组装好后,上述偏差不得引起芯子高度变化。
3.4.3 紊流片的节距允差为±1 mm,紊流片的波峰数允差±1峰。
3.4.4 散热带、紊流片和冷却管的焊合必须牢固。
散热带和紊流片的波峰节点与冷却管的二平面管壁有效平面长度的焊合率不得低于90%。
3.4.5 每根冷却管中紊流片在整个长度中允许拼接,但在拼接处必须对齐,紊流片装入冷却管后二端不得出现皱折。
波峰错位不得出现挤靠现象。
3.4.6 紊流片装入冷却管后,经芯子装配钎焊,目测外端部应与主板的内底面平齐。
3.4.7 主板与冷却管的焊合必须牢固、密封。
管子二端面应伸出主板内底面5 mm±1.5 mm。
3.4.8 主板与冷却管的焊接处如有脱焊、虚焊,允许用氩弧焊或其它能保证强度的方法补焊;允许紊流片端面出现局部熔包,但由此引起的紊流片端部料厚变化不得超过0.5 mm。
3.4.9 芯子总成经钎焊后,对角线的长度差不得大于5 mm。
3.4.10 左、右气室与芯子总成的氩弧焊接必须牢固、密封。
焊缝应平整,不得有毛刺。
3.4.11 中冷器总成不允许有压伤、碰伤现象。
芯子正面积(高×宽)为0.3 m2以下允许倒卧二处,大于0.3 m2以上允许倒卧三处。
每处倒卧面积不得大于1.5 cm2。
3.5 密封性密封性能检测按4.1进行,不允许有任何漏气。
3.6 耐压力循环疲劳能检测按4.2进行,不能出现裂纹、脱焊、漏水等机械损伤。
3.7 耐振性能检测按4.3进行,不能出现裂纹、脱焊、漏水等机械损伤。
3.8 散热性能应符合发动机的要求。
3.9 高温侧压力降(中冷器内部)应不大于10 kPa。
3.10 按4.6进行清洁度试验时,中冷器的清洁度应满足以下要求:a)杂质最大重量:25.0 mg;b)杂质最大尺寸:3.175 mm;c)杂质最大面积:2.58 mm2。
进行尺寸分析的颗粒包括:沙粒、污垢、斑点、加工碎片、焊渣、炉渣及用探针不易破坏的微粒。
4 试验方法4.1 密封性试验焊接后的中冷器总成喷漆前应进行密封性试验,调整试压夹具与中冷器的中心距相符,将试压夹具套在两进出气口上并夹紧,开通气源并调整试验压力至300 kPa,使中冷器与试压夹具一起浸入水槽内,历时15 s,不允许出现气泡。
4.2 压力循环疲劳试验中冷器冲入常温空气,压力变化范围为0~(300±10) kPa,频率为(0.3~1)Hz,循环50万次,不得发现泄漏和变形.4.3 耐振性能试验试验时,将中冷器内部注满常温水后密封,按实际使用时对中冷器的固定的方式,将中冷器固定在试验台上,以40 m/s2的加速度,在20 Hz、30 Hz、 40 Hz、 50 Hz频率下各振动180 min,共振动12小时,振动方向为垂直上下。
完成12小时振动后,不允许出现泄漏和零件损坏。
4.4 冷热冲击疲劳试验产品充入干燥压缩压缩空气,压力为50 kPa,质量流量(0.35±0.05) kg/g,循环温度在(50±5) ℃~(240±10) ℃之间,循环频率最大30次/h,温度变化速率最小±180 ℃/s,环境温度(25±5) ℃,循环次数不得少于6000次,总成不应发生泄漏。
4.5 压力爆破试验将中冷器的一端气室口连接在静压试验台的出油口上,启动油泵,待试验介质充满整个中冷器油腔后,将另一端气室口堵死。
继续启动油泵,使压力上升至产品泄漏或变形,记录下泄漏的压力和部位,要求压力最小达到600 kPa。
4.6 清洁度试验4.6.1 试验设备试验设备应包括:5.0u定性滤纸、0.5u滤膜、过滤装置、真空过滤瓶、烧杯、实验溶剂(例如甲醇)、分析天平(灵敏度0.1 mg)、烘干箱、干燥箱、镊子、放大设备。
注:甲醇具有很强的挥发性和可燃烧性。
它适用于大多数金属和非金属冷却器零部件。
如果可能,在实验之前,应确定冷却器零部件与甲醇的符合性。
4.6.2 试验步骤a) 实验室用的玻璃器皿和试验区域必须清洁无杂质;b) 用0.5µ 滤膜过滤实验溶剂;c) 将5.0µ 定性滤纸放置在100℃(212℉)的烘干箱中,保持15分钟。
取出滤纸放在干燥器中冷却至20℃(58℉)。
取出滤纸在分析天平上称重,精确到0.1mg。
记录滤纸皮重(WtO);d) 水平放置冷却器,从进气口将过滤后的溶剂注入冷却器,溶剂体积大约是冷却器体积的40%,用盖子堵住进出口;e) 翻转冷却器,使溶剂注入进气室/出气室。
重复10次,确保溶剂经过所有内表面。
翻转冷却器使溶剂从一个气室流过另一个气室再流回第一个气室为1次;f) 从出气口放出溶剂,装入烧杯。
在真空过滤装置中,用事先准备好的称重过的 5.0µ 滤纸过滤该溶剂;g) 经0.5µ 滤膜过滤后的未用溶剂可以进行冷却器以后的实验;h) 从过滤装置上取下滤纸,放入100℃(212℉)的烘干箱中15分钟。
取出滤纸放在干燥器中冷却到20℃(68℉)。
然后取出滤纸在分析天平上称重(Wte),精确到0.1mg ;i) 带杂质的干滤纸的重量(Wte)- 滤纸皮重(WtO)=杂质的重量(Wtd)。
将测量的杂质重量与规定的杂质重量对比,确定是否符合要求;j) 用光学放大设备测量滤纸上最大和最小杂质尺寸。
计算杂质颗粒的面积。
对比测得的颗粒尺寸与规定的颗粒尺寸以及计算的颗粒面积与规定的颗粒面积,确定是否满足要求。
4.7 外观质量检测方法外观质量采用目测法。
5 检验规则5.1 中冷器应经质量检验部门验收合格后,方可出厂。
5.2 检验分类产品检验分出厂检验、型式检验及本公司进货检验。
5.3 出厂检验每只中冷器出厂前应进行外观质量检查、安装形位尺寸检查及气密性试验并核发合格证。
5.4 型式检验在以下任一情况下,应进行型式检验:a)正式生产后,如结构、材料、工艺有较大改变,可能影响产品性能时;b)产品长期停产后,重新进行生产时;c)国家质量监督机构提出进行型式检验的要求时;d)合同有规定时。
5.5 进货检验中冷器入厂时,应进行进货检验。
5.5.1 检验中如有一件一项不合格,允许加倍抽样检验,如仍有一件一项不合格,则该批判定为不合格;如有一件二项不合格或二件各一项不合格,则该批判定为不合格。
5.5.2 进货检验不合格,严禁入库、装配、使用。
必要时,允许逐件检验,合格的可以入库、装车、使用。
5.6 检验项目与抽样方案检验项目与抽样方案见表1。
表1 中冷器检验项目表与抽样方案5.7 判定规则外观表面质量及尺寸按3.3执行,密封性按4.1判定,压力循环疲劳试验按4.2判定,冷热冲击疲劳试验按4.4判定,压力爆破试验按4.5判定,清洁度试验按4.6判定。
6 标志、包装、运输与贮存6.1 标志中冷器上应有符合Q/XX B102规定的标识。
6.2 包装6.2.1 中冷器必须进行清洗和防锈处理后方可进行包装。
外包装均采用木质包装箱,包装箱上应标明:a)制造厂厂名、厂标及地址;b)型号及名称、编号;c)装箱日期、毛质量及数量;d)收货单位及地址。
6.2.2 中冷器应附有检验员签章的产品质量合格证,合格证上应注明:a)制造厂厂名;b)产品名称和型号;c)数量;d)检验员;e)检验日期或出厂批号;f)注意事项。
6.2.3 包装箱内中冷器之间应有隔离措施,中冷器在箱内应固定牢固。
6.2.4 包装储运图示标志“防潮”、“小心轻放”、“堆码层数极限”等应符合GB 191的有关规定,并正确选用和使用不褪色的油漆、油墨等,准确清晰牢固地喷刷在箱面上。
6.3 运输6.3.1应具有防雨措施,以保证在正常储运中不致锈蚀。
6.3.2 中冷器在运输及堆放过程中,应避免强烈冲击振动,防止引起磕碰损坏。
6.3.3 每只中冷器进、出气口应有防尘措施,保持其内部清洁。
6.4 贮存中冷器应存放在通风、干燥、无腐蚀性物质并有防雨、防潮、防火措施的库房内,在正常保管情况下,自出厂之日起,制造厂应保证中冷器在12个月内不致锈蚀。