第5章 重要反应器的演变
史上最全的反应器结构及工作原理图解!
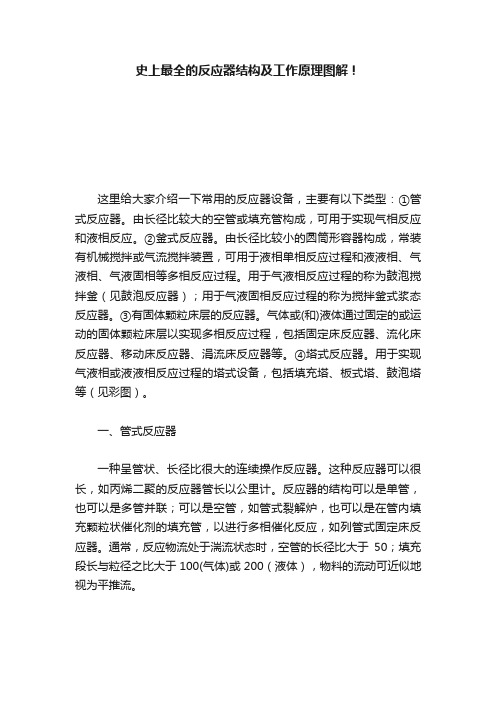
史上最全的反应器结构及工作原理图解!这里给大家介绍一下常用的反应器设备,主要有以下类型:①管式反应器。
由长径比较大的空管或填充管构成,可用于实现气相反应和液相反应。
②釜式反应器。
由长径比较小的圆筒形容器构成,常装有机械搅拌或气流搅拌装置,可用于液相单相反应过程和液液相、气液相、气液固相等多相反应过程。
用于气液相反应过程的称为鼓泡搅拌釜(见鼓泡反应器);用于气液固相反应过程的称为搅拌釜式浆态反应器。
③有固体颗粒床层的反应器。
气体或(和)液体通过固定的或运动的固体颗粒床层以实现多相反应过程,包括固定床反应器、流化床反应器、移动床反应器、涓流床反应器等。
④塔式反应器。
用于实现气液相或液液相反应过程的塔式设备,包括填充塔、板式塔、鼓泡塔等(见彩图)。
一、管式反应器一种呈管状、长径比很大的连续操作反应器。
这种反应器可以很长,如丙烯二聚的反应器管长以公里计。
反应器的结构可以是单管,也可以是多管并联;可以是空管,如管式裂解炉,也可以是在管内填充颗粒状催化剂的填充管,以进行多相催化反应,如列管式固定床反应器。
通常,反应物流处于湍流状态时,空管的长径比大于50;填充段长与粒径之比大于100(气体)或200(液体),物料的流动可近似地视为平推流。
分类:1、水平管式反应器由无缝钢管与U形管连接而成。
这种结构易于加工制造和检修。
高压反应管道的连接采用标准槽对焊钢法兰,可承受1600-10000kPa 压力。
如用透镜面钢法兰,承受压力可达10000-20000kPa。
2、立管式反应器立管式反应器被应用于液相氨化反应、液相加氢反应、液相氧化反应等工艺中。
3、盘管式反应器将管式反应器做成盘管的形式,设备紧凑,节省空间。
但检修和清刷管道比较困难。
4、U形管式反应器U形管式反应器的管内设有多孔挡板或搅拌装置,以强化传热与传质过程。
U形管的直径大,物料停留时间增长,可应用于反应速率较慢的反应。
5、多管并联管式反应器多管并联结构的管式反应器一般用于气固相反应,例如气相氯化氢和乙炔在多管并联装有固相催化剂的反应器中反应制氯乙烯,气相氮和氢混合物在多管并联装有固相铁催化剂的反应器中合成氨。
化学反应器进化和设计的优化方法

化学反应器进化和设计的优化方法化学反应器是化学反应工业中最为重要的设备之一,是实现化学反应过程的场所。
随着科技的发展和化学反应工业的壮大,化学反应器的种类和形式也在不断发展和进化。
本文将介绍化学反应器的进化历程和设计的优化方法。
一、化学反应器的进化历程1. 传统反应器传统反应器是最早出现并被广泛使用的一种反应器。
它们通常采用圆柱形或圆锥形的容器,内部有搅拌器实现混合均匀。
传统反应器的优点是体积小、结构简单、成本低廉等,适用于中小型反应试验和生产。
传统反应器的缺点是反应过程不稳定,传质效果差,操作难度大,易出现安全隐患等问题。
2. 改进型反应器改进型反应器是传统反应器的改良型。
它们可以在传统反应器的基础上进行针对性的改进,以实现更好的反应效果。
例如,在传统反应器内部增加了多个流速不同的管道,可以有效增强液体混合的效果,提高反应效率和稳定性;又如,在反应器内部加入膜技术,可以有效提高反应物的传质速率,从而提高反应效率。
3. 微型反应器微型反应器是一种新兴的反应器类型,它针对传统反应器的缺点进行了根本的解决。
微型反应器由微米级的反应腔组成,反应物质只需要以微量的流量输入进入反应腔内进行反应。
微型反应器的优点是反应速率快、空间均匀、反应效率高等,适用于小型反应试验和产量较小的产品。
4. 超临界反应器超临界反应器是一种高压、高温的反应器,它的工作压力、工作温度都在临界值以上。
超临界反应器的优点是反应过程稳定,反应效率高,反应物质传质速度快等,适用于高附加值产品的生产。
二、化学反应器的优化设计方法1. 反应器尺寸和形状的优化设计在反应器的设计中,反应器的尺寸和形状是非常重要的。
合理的反应器尺寸和形状可以有效提高反应效率,减少生产成本。
反应器的尺寸和形状应该根据具体的反应物质进行设计,以保证反应物质能够充分接触反应,提高反应效率。
同时,反应器的形状也应该灵活选择,以适应不同反应物质的需求。
2. 材料的优化选择材料是反应器的关键组成部分,正确的材料选择可以保证反应器的长期稳定运行。
高分子化学第5章
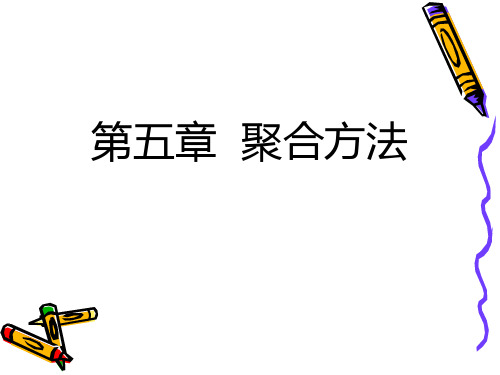
• 主要有聚乙烯醇等合成高分子,及纤维素衍生物、明胶等
–(2)不溶于水的无机粉末
• 主要有碳酸镁、滑石粉、高岭土等
水溶性有机高分子
• 高分子分散剂的作用机理主要是:
–吸附在液滴表面,形成一层保护膜,起着保 护胶体的作用;
–介质的粘度增加,有碍于两液滴的粘合;
–明胶、部分醇解的聚乙烯醇等的水溶液,还 使表面张力和界面张力降低,使液滴变小。
第五章 聚合方法
5.1 引言
聚合反应工程考虑的三个层次:
• 聚合机理和动力学(mechanism and kinetics)
–连锁:自由基、阴、阳离子、配位 –逐步:缩聚、聚加成、开环等
• 聚合过程(polymerization process)
–实施方法:本体、溶液、悬浮、乳液 –相态变化:分散性质、是否沉淀、是否存在界面等
• 丙烯腈连续溶液聚合 ; • 醋酸乙烯酯溶液聚合;
• 丙烯酸酯类溶液聚合。
例1. 聚丙烯腈(PAN)连续溶液聚合
• 连续均相溶液聚合:以51-52%的硫氰化钠(NaSCN)水 溶液为溶剂,AIBN为引发剂,pH5±0.2,温度75~85 ˚C,转化率70~75%。进料单体浓度17%,出料聚合 物浓度13%,脱除单体后直接用于纺制腈纶纤维。 • 连续沉淀聚合:以水为溶剂,过硫酸盐类氧化还原引 发体系,温度40~50 ˚C,转化率80%。聚合产物从反应 体系中沉淀出来,经洗涤、分离、干燥后重新配制成纺 丝溶液用于腈纶纺丝。
–沉淀聚合机理与均相聚合有些不同,主要反 映在凝胶效应上,影响因素和生产控制也有 差异。
• 液相聚合; • 气相聚合; • 固相聚合。
从工程角度考虑(需重视操作方式)
反应器基本理论课件
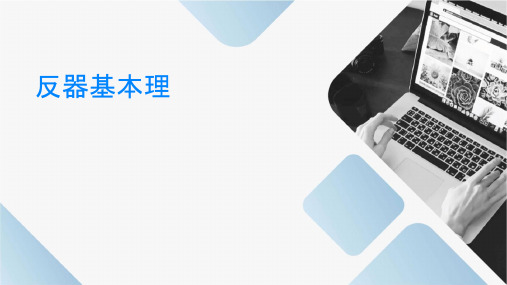
• 反应器概述 • 反应器的基础理论 • 反应器的类型与选择 • 反应器的操作与优化
反器概述
01
反应器的定义和分类
分类
连续反应器(Continuous Reactor):反应物以稳定流速连 续加入,产物也连续流出。
定义:反应器是一种用于进行化 学反应的设备或系统,通过控制 反应条件来促进化学反应的进行, 并获取所需的产物。
批式反应器(Batch Reactor): 反应物一次性加入,反应完成后 产物一次性取出。
半连续反应器(Semi-Batch Reactor):反应物一部分连续加 入,一部分批次加入。
反应器在化工流程中的地位
01
02
03
核心设备
反应器是化工流程中的核 心设备之一,直接影响产 品质量和生产效率。
反应条件控制
评估指标
评估反应器性能的主要指标包括反应器的转化率、选择性、产率等。此外,还需关注反应器的能耗、设备寿命、 操作稳定性等方面的指标。在实际应用中,需根据具体反应体系和需求,综合权衡各方面因素,选择最适合的反 应器类型和设计参数。
04
反器的操作
化
反应器的稳态操作
稳态操作定义
指的是反应器在连续、稳 定的状态下进行操作,各 参数不随时间变化。
适用场景
非均相反应器适用于涉及固-液、固气等反应体系的反应过程,如催化裂 化、气体吸附等。
反应器的选择与评估
选择因素
在选择反应器时,需要考虑反应物的性质、反应条件、产物要求等因素。例如,对于快速反应,宜选择均相反应 器;对于慢反应,宜选择非均相反应器。同时,还需考虑反应器的传热、传质性能,设备的投资与运行成本等因 素。
非理想流动模型
分析实际反应器中可能出现的非理想流动现象,如返混、死区等, 以及这些现象对反应器性能的影响。
第五章 间歇式操作反应器

回顾一下:生化反应器中可进行的反应类型? 再想想:反应器可采取的操作方式?
2、研究反应器的目的?
◆研究生化反应器的基本反应规律
◆研究生化反应器的基本传递规律 ◆研究生化反应器的设计内容及方法
上一内容
下一内容
回主目录
返回
2013-7-25
第5章 间歇式操作反应器>>5.1生化反应器设计概论
上一内容 下一内容 回主目录
返回
2013-7-25
第5章 间歇式操作反应器>>5.1生化反应器设计概论
5.1.1 生化反应器的分类
( 生化反应器可从不同角度分类)
2、按操作方式分类 ■间歇反应器(分批操作反应器):底物一次加入反应器,在反应过
程中无底物和产物的输入和输出,底物和产物的浓度随反应时间变化。
上一内容
下一内容
回主目录
返回
2013-7-25
第5章 间歇式操作反应器>>5.1生化反应器设计概论
5.1.2 生化反应器的基本设计方程
反应器计算的基本内容 确定最佳操作条件与控制方式 操作条件,如反应器的进口物料配比、流量、温度、压 力和最终转化率等工艺条件,直接影响反应器的反应结果,
也影响反应器的生产能力。对正在运行的装置,因原料组
对细胞,有
体系内累 进入体系 离开体系 体系内生 积细胞质量 细胞质量 细胞质量 长细胞质量
上一内容
下一内容
回主目录
返回
2013-7-25
第5章 生化反应器设计与分析>>5.1生化反应器设计概论
生物工程设备第五章 生物反应器的放大与控制

又因为
D ug (VVM ) pL
所以
(VVM )2 ( D1 )23 ( pL2 )
(VVM )1 D2
pL1
QG ug Di2,VL: Di3
第二篇 生物反应设备
第五章 生物反应器的放大与控制
生物反应器的放大过程
1)利用实验室规模的反应器进行种子筛选和 工艺试验;
2)在中间规模的反应器中试验(中试),确 定最佳的操作条件;
3)在大型生产设备中投入生产。
放大的重要性
为生物技术产品从实验室到工业生产的关键。
对一个生物反应过程,在不同大小反应器中进行 生物反应虽相同,但三传有明显差别,从而导致 不同反应器中生物反应速率有差别。
放大倍数实际上就是反应器体积的增加倍数
H1 H2 常数 D1 D2
V2 V1
D2 D1
3
m
所以
H2
1
m3
和
D2
1
m3
H1
D1
H1,H2-模型反应器和放大反应器的高度,m;D1,D2-模型反应 器和放大反应器的内径,m;V1,V2-模型反应器和放大反应器 的体积,m3;
(二)以单位体积液体中搅拌功 率相同放大
ug
60Q0 (273 t) 9.8 104
4
Di 2
273
pL
27465.6(VVM )(273 t)VL Di2 pL
Q0
ug pL Di2 27465.6 (273 t)VL
VVM
ug pL Di2
27465.6 (273 t)VL
(四)以空气线速度相同的原则 进行放大
u g1 u g2
欲使整个生物反应器处于最优条件下进行操作, 必须使反应器中每个细胞都处于最优环境之下, 达到整体优化。
第五章 气-固相催化反应动力学

第五章 气-固相催化反应动力学本章核心内容:介绍了气-固相催化反应的特点、固体催化剂的特征参数和均匀及不均匀吸附等温方程的要点,在此基础上,阐述了不同控制步骤的气-固相催化反应本征动力学方程。
本章的重点在于讨论有关固体催化剂的反应-传质-传热耦合的宏观过程、宏观动力学方程的建立及求解方法。
前已述及,化学反应可分为均相反应和非均相反应两大类。
均相反应动力学因无相间传质传热阻力属于本征动力学范畴,而气固两相催化反应存在相间传递阻力,使可测的主体气流温度和浓度与实际反应值不同,为了描述真实的反应速率,进行有效的气固催化反应器设计,从第五章开始,将学习和讨论气固非均相反应动力学及其反应器设计内容。
本章从它的机理方程入手,详细讨论气固相催化反应宏观动力学规律。
5-1 气-固相催化反应 5-1-1 气-固相催化反应概述所谓气固相催化反应是指在反应条件下,在固体催化剂表面上进行的、反应物和产物均呈气态的一类化学反应。
例如,氮气和氢气在固体铁催化剂表面上进行的合成反应,二氧化硫在固体钒催化剂表面上转化为三氧化硫的反应,合成气在铜基催化剂表面上进行合成甲醇的反应等等,都属于气固相催化反应。
这一类型的催化反应在化工生产中所占的份额相当大,因此气固相催化反应动力学研究及其反应器设计等相关内容成为化学反应工程学的核心内容之一。
气固相催化反应的最大特点莫过于固体催化剂表面这个反应平台,它不仅可以改变反应路径、降低反应活化能,加快反应速率。
因此,在定义气固相催化反应速率时,离不开固体催化剂表面积S 这个参变量的引入,即dtdn S r ii 1±= (5-1) 固体催化剂表面积是固体催化剂的重要性能参数之一,对于特定的催化剂而言,单位质量催化剂所具有的表面积几乎是一个常量,两者之间具有高度的对应关系,所以在定义气固相催化反应速率时,也常常用固体催化剂质量W 替代式(5-1)中的S。
气-固相催化反应动力学研究的目的就是要建立气固相催化反应动力学方程,为气固相催化反应器的开发设计、选型、优化操作与控制提供理论依据。
反应器工程的发展与应用
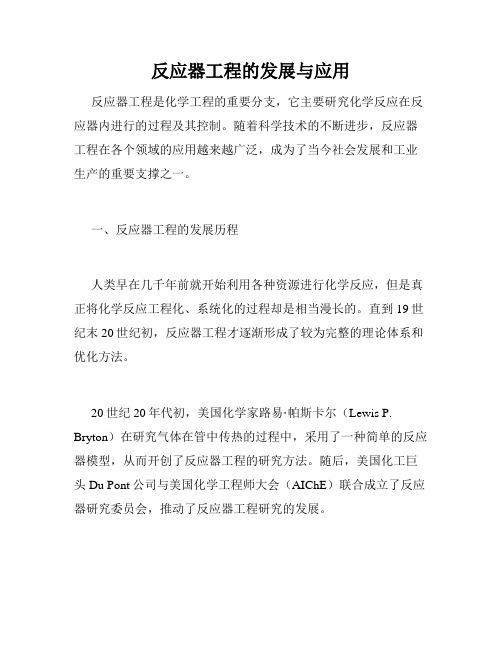
反应器工程的发展与应用反应器工程是化学工程的重要分支,它主要研究化学反应在反应器内进行的过程及其控制。
随着科学技术的不断进步,反应器工程在各个领域的应用越来越广泛,成为了当今社会发展和工业生产的重要支撑之一。
一、反应器工程的发展历程人类早在几千年前就开始利用各种资源进行化学反应,但是真正将化学反应工程化、系统化的过程却是相当漫长的。
直到19世纪末20世纪初,反应器工程才逐渐形成了较为完整的理论体系和优化方法。
20世纪20年代初,美国化学家路易·帕斯卡尔(Lewis P. Bryton)在研究气体在管中传热的过程中,采用了一种简单的反应器模型,从而开创了反应器工程的研究方法。
随后,美国化工巨头Du Pont公司与美国化学工程师大会(AIChE)联合成立了反应器研究委员会,推动了反应器工程研究的发展。
20世纪50年代,俄罗斯科学家M.G.刘宾卡(M.G. Levich)提出了以“果壳层、赋形层和液膜层”为基础的三相反应器模型,为反应器工程研究提供了新的思路。
而到了20世纪70年代,反应器工程的研究已经逐步深入到了多相多组分化学反应的研究,并且已经发展出了适用于不同反应体系下的数值模拟和过程优化方法。
二、反应器工程在工业生产中的应用反应器工程的应用可以涵盖多个领域,比如化工、医药、生物、环保等,以下是其中几个重点方向的简单介绍:1. 化工领域在化工领域,反应器工程研究主要集中在反应工艺的优化、反应机理的解析以及反应机制的模拟等方面。
而在传统的石油化工生产、有机合成等行业中,反应器就是化工生产中贯穿始终的重要装置。
以石化行业为例,炼油、煤化工、化肥、合成树脂、精细化工等工艺都需要反应器作为关键的生产装置。
因此,对反应器工程技术的提高、应用等方面的研究会带来显著的经济和社会效益。
2. 医药领域在医药领域,反应器工程的研究主要是针对制药合成过程的控制和优化。
利用反应器工程的理论和方法,可以针对不同药物引起的问题进行合理分析和解决。
- 1、下载文档前请自行甄别文档内容的完整性,平台不提供额外的编辑、内容补充、找答案等附加服务。
- 2、"仅部分预览"的文档,不可在线预览部分如存在完整性等问题,可反馈申请退款(可完整预览的文档不适用该条件!)。
- 3、如文档侵犯您的权益,请联系客服反馈,我们会尽快为您处理(人工客服工作时间:9:00-18:30)。
1 、三个外循环泵串联:
1949—1956年间,化学反 应工程学尚处于萌芽时期, 所以这一时期产生的第一 阶段的己二酸反应器是由 化学家和机械师设计的,是 串联搅拌槽式反应器。 右图中KA代表环己酮和环 己醇的混合物。由于三个 外循环换热器串联操作, 物料循环速度太低,传热 效果很差,结垢严重,常 常堵塞。
四个外循环泵并联的反应器示意图:
4 、外环流反应器:
鉴于1964年失败的教训,1965年便把每个釜都改 成外循环反应器,即把外循环反应器串联成一组。同 时,新料和循环料均改由多孔喷嘴切线方向进料。结 果节约了能量,使能耗指数比1956年下降60%。
单塔变双塔 :
2 、三相反应器 :
由于新型烃化反应催化剂的出现,人们开始用 搅拌釜进行气,液、固三相烃化反应,以期得到固 相催化剂的良好悬浮。
为简化设备,提高反应器生产能力,将搅 拌釜改成内环流反应器,结果使反应时间缩短 4/5,大大节约了能 量。 可见催化剂和反 应器 研究使烃化反应 工艺 面貌一新。
第6章 重要反应器的演变
LOGO
重要反应器的演变
一、已二酸反应器的演变 二、烃类氧化反应器演变 三、烃化反应器的演变
第一部分、已二酸反应器的演变:
已二酸(Adipic acid )又称肥酸,是工业上最重 要的脂肪族二元羧酸,主要用于生产尼龙66的单体,大 约占己二酸总量的70 %;其它的30 %在制备聚氨酯、合 成树脂、革、聚酯泡沫塑料、塑料增塑剂、润滑剂、食 品添加剂、粘合剂、杀虫剂、染料、香料、医药等领域 得以广泛应用。 目前,己二酸的 年产量已达300 万吨左右,并以 约3 %的年增长 率增长。
第二部分、烃类氧化反应器演变:
烃类液相氧化反应是石油化工厂的支柱之 一。它既是自由基反应,又是连串反应。从自 由基反应来看,要求有一定返混,以积累一定 的自由基浓度,从连串反应来看,要求返混不 能太大,以保证一定的选择性。
1.石蜡氧化
石蜡氧化制合成脂肪酸反应器的发展初期, 是间歇操作的搅拌釜,以期引发和积累一定浓 度的自由基。后因其比传热面积小而改为间歇 操作的鼓泡塔。反应时间约20h,以致给人们 一个印象,认为石蜡氧化是慢反应。
浆态床反应器:
浆态费托(FT)合成反应器的结 构比较简单。其外壳为一圆筒,内设 用于换热的蒸汽盘管、气体分布器和 气液分离器。反应器内装有特殊形式 制备的高活性催化剂。这种粉碎得很 细的催化剂悬浮在液体介质中形成浆 液。正常条件下,液体介质为FT反应 生成的反应蜡。来自天然气重整工段 的H2/CO比为2左右的合成气预热后 从反应器底部经由气体分布器进入由 催化剂和FT合成蜡组成的浆液,上升 的气泡在浆液中与催化剂接触进行合 成反应。反应热由反应器内的冷却蛇 管移出,发生蒸汽。合成蜡产物通过 Sasol开发的独有的分离工艺在反应 器内部从含有催化剂的浆液中分离出 来。
5 、用气流搅拌代替机械搅拌:
从前一设计的实践经验摸索到,如果精 心设计循环速率和喷嘴结构,则机械搅拌 便可省略。当然,反应器的结构尺寸,主 要是高径比发生了变化。 结果使设备结构大大 简化。但是循环管尚 末取消。
6 、活塞流反应器设想:
流化床反应器:
流化床反应器的基本结 构主要包括: (1)气固分离装置(旋风 分离器或内过滤器) (2)内换热器 (3)内部构件(如挡板、 挡网等) (4)壳体 (5)固体颗粒加入和卸出 装置 (6)气体分布板
1963~1964年间发表了该反应的动力学与反应 机理方面的论文,根据该反应是复杂的串联反应的规 律,得出了活塞流反应器最理想的结论。硝酸从第一 隔区加入,醇、酮从各隔区喷入。
这种设计有许多好处:
第一,反应过程中有气泡产生。初生气泡很小, 因此其内应力极大,气泡剧烈震动,可使给热 系数接近核沸腾时的给热系数。此外,排热管 置在反应区(即放热区),可避免堵管。 第二,气泡起搅拌作用,无须机械搅拌。 第三,冷却水走管内,减少应力腐蚀。 第四,利用液位差流动,从而革掉了循环泵。
已二酸反应器的演变:
已二酸主要由环己醇和环己酮(Cyclohexanone and cyclohexanol)用硝酸(Nitrate)氧化而制得。 其反应方程式为:
下面具体从以下几个反应器的演变来介绍己二酸 反应器的演变 :
下图为石蜡氧化制合成脂肪酸反应器的演变:
2 、环己烷氧化:
长期以来,人们在多釜串联反应器内用空气 氧化环己烷,一步生产环己醇和环己酮。后来改 为多塔串联一步生产环己醇和环己酮,单程转化 率只有3%左右,因为环己烷的氧化反应与该氧 化反应的中间产物环己基过氧化氢物分解成环己 醇、酮的分解反应,是相互矛盾的。后来改成由 四个环流反应塔串联生产环己基过氧化氢物,而 另用多釜串联反应器进行过氧化氢物的分解,即 将氧化反应与分解反应在不同的反应器和不同的 反应条件下进行,从而可使过程的单程转化率提 高约30%。
石蜡氧化:
后来石蜡氧化改为多塔串联,气液错流,提高气 体表观速度,使反应时间缩短到12h左右。 近来人们采用多段不泄漏型筛板塔,使表观 气速提高到约30cm/s,结果使反应时间缩短到 5h,反应选择性也提高了。从而纠正了人们认 为烃类氧化反应是慢反应的错误认识。 石蜡氧化为脂肪酸的一般步骤为:
2 、两个外循环泵并联:
1958年,改造成两个泵和两个换热器并联,提 高了物料循环速度,改善了反应器的混合与传热, 使反应器生产能力提高,能耗指数下降36%。
3 、四个外循环泵并联:
由于1958年改造取得了成果,人们认为 似乎只要提高物料循环速度便可提高生产 能力。于是1964年采用四个泵和四个换热 器并联。其结果是适得其反,生产能力只 达到设计能力的2/3,能耗只比1956年下 降22%。而且,操作是灾难性的:第一釜 搅拌器失效,物料被猛烈地冲出第一釜而 在管路中和第二反应釜中发生反应,第二 釜中的泡沫则使气体夹带严重,并由于气 节作用使泵损坏。
这种设计的另一个重要优点:
硝酸浓度的线性变化代替了原先反应器 的阶式变化,即物料流型从近似全混流过渡 到活塞流,从而提高了反应收率。这种反应 器使能耗指数降低89%,与1956年相比,几 乎差一个数量级。可见,反应动力学、流动 模型和气泡等反应及传递特性的基础研究成 果大大地促进了生产力的发展。
7 、内冷却式活塞流反应器:
这个设想,于1971年着手试验,结果产生 了所谓“内冷却式反应器”。实践达到了预 期的高给热系数,能耗指数下降了89%,反 应器生产能力大大提高。在一个1.829米直径 的反应器内的处理量大致相当于1965年时两 个3.355米直径反应器的处理量。反应器结构 大大简化,投资大大减少——省掉了循环泵、 搅拌器、循环冷却管,减少了辅助管线、阀 门及仪表,简化了操作,安全性也更好了。
固定床反应器:
固定床又主要分为以下三种:
三相反应器 :
目前,气- 液- 固三相反应在现代化学工业 中得到广泛应用。如:氧化、氢化、烃化、氯化、 氨解、混合气体转变成为炭氢类化合物的合成 反应以及生物废水的处理过程中均涉及到三相 反应。下面具体介绍三相反应器.
首先,按照物料在过程中的流动方式不同, 将三相反应器分为:涓流床(又叫滴流床)、浆 态床、流化床、携带床和固定床五种。
下图即为内冷却式活塞流反应器的示意图:
演变规律:
从整个发展过程来看,己二酸反应器的 演变可归纳为三个方面: 1、反应物流型由接近全混流改成接近活 塞流,以适应串联反应的内在规律。 2、由深层改为浅层,有利于反应产物的 排出。 3、机械搅拌改为气流搅拌,以节能和减 少动部件。
环己烷氧化:
下图为环己烷空气氧化生产环己醇和环己酮的演变 :
演变规律:
上面两个烃类氧化反应器的演变可归纳为三个方面: 1、反应物流型由全混流变成非全混流,以既满足自由 基引发的内在要求,又满足选择性的要求。 2、使过程由反应控制变为氧的传质控制,既尽量发挥 催化剂的效能,又保证了较好的选择性。 3、由同一条件下同时进行两个要求不同条件的反应改 为在不同条件下分别进行两个不同的反应,充分满足每 个反应的内在规律的要求。 这两个例子再一次告诉我们,流动模型和反应机理等反 应工程学的理论大大促进了生产力的发展。
第三部分、烃化反应器的演变:
烃化反应很多。这里主要讨论芳烃的烃化反应,例 如苯和联苯的烃化反应。
1,单塔变双塔 :
长期以来,苯的烃化反应是在一个连续操作的鼓泡 塔内完成的。在烃化时,同时发生反烃化反应,烃 化与反烃化要求不同的温度和催化剂浓度,因此, 反应的效率很低。近来,将单塔改成双塔串联,第 一塔创造有利于烃化反应的条件,第二塔维持有利 于反烃化的条件。结果使反应收率大大提高了。可 见,反应机理的研究,促进了反应器的不断完善。
浆态床反应器的优点:
浆态反应器的主要优点如下: (1)结构简单,投资较省; (2)克服了固定床管式反应器在反应器大小、生产能力 和操作 压力等方面的限制,一台直径5米的浆态反应 器,其生产能力相当于5台固定床反应器的生产能力之 和; (3)传热和温度控制较好; (4)产物分布较易控制; (5)可以在线添加或移出催化剂; (6)生产同等数量产品时,浆态反应器使用的催化剂只 有固定床反应器的50%,大大节省了催化剂费用.
涓流床反应器:
右图即为涓流床反应器示意图: 涓流床反应器主要有以下几个优点: (1)气液流动均接近活塞流, 可以获得高的 转化率 . (2)液体呈膜状流动,气体反应物通过液相扩 散至固体催化剂外表面的阻力较小 . (3)液固比小, 若存在液相均相副反应时, 不致于对目的产物的收率产生大的影响. (4)压力降较小, 以致整个床层操作压力较 为均匀 . (5)反应热效应大并使床层内反应温度过高 时,可将液相产物再循环或分段加入冷料 进行冷激降温.