2016-2-22 培训--IE标准作业三件套
IE培训教材
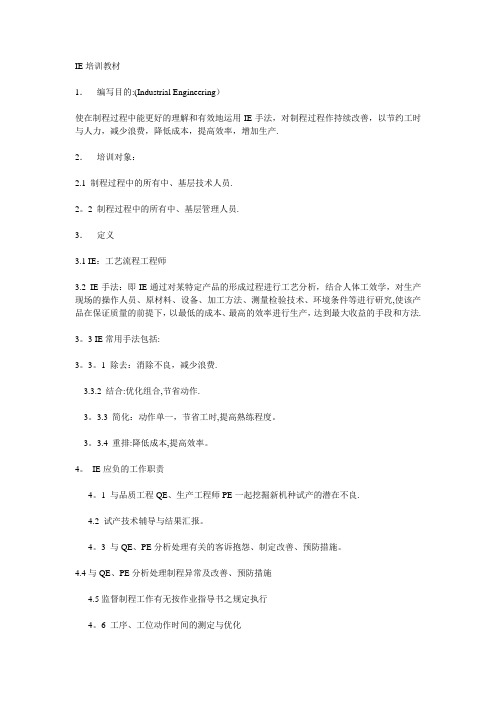
IE培训教材1.编写目的:(Industrial Engineering)使在制程过程中能更好的理解和有效地运用IE手法,对制程过程作持续改善,以节约工时与人力,减少浪费,降低成本,提高效率,增加生产.2.培训对象:2.1 制程过程中的所有中、基层技术人员.2。
2 制程过程中的所有中、基层管理人员.3.定义3.1 IE:工艺流程工程师3.2 IE手法:即IE通过对某特定产品的形成过程进行工艺分析,结合人体工效学,对生产现场的操作人员、原材料、设备、加工方法、测量检验技术、环境条件等进行研究,使该产品在保证质量的前提下,以最低的成本、最高的效率进行生产,达到最大收益的手段和方法.3。
3 IE常用手法包括:3。
3。
1 除去:消除不良,减少浪费.3.3.2 结合:优化组合,节省动作.3。
3.3 简化:动作单一,节省工时,提高熟练程度。
3。
3.4 重排:降低成本,提高效率。
4。
IE应负的工作职责4。
1 与品质工程QE、生产工程师PE一起挖掘新机种试产的潜在不良.4.2 试产技术辅导与结果汇报。
4。
3 与QE、PE分析处理有关的客诉抱怨、制定改善、预防措施。
4.4与QE、PE分析处理制程异常及改善、预防措施4.5监督制程工作有无按作业指导书之规定执行4。
6 工序、工位动作时间的测定与优化4。
7 与QE、PE分析处理产品品质异常及改善方案制定4。
8 在管理代表的辅导下,主导推行ISO9001品质保证系统与5S专案活动. 5.作业内容5.1 工艺审查5。
1.1产品及零部件结构是否合理5。
1.2 零部件的标准化与通用化5.1。
3 精度与光洁度5。
1。
4 选用材料是否合理5.2 工艺验证通过试制鉴定检验工艺规程与工艺装备5.3 工艺方案制订5。
3.1制订工艺方案应考虑的因素5。
3。
1.1 新产品进行工艺加工时采用的设备5。
3.1.2 工艺装备5.3.1.3切削用量5。
3。
1。
4 工艺过程及其它工艺因素5.3。
2 准定工艺方案的标准保证质量的前提下,用最低的成本,最高效率,完成整个工艺加工的过程5.3。
IE之标准化作业

IE之标准化作业标准化作业(1)标准作业三要素此方法是丰田的发明创造,当实现一个流工艺后,需要对多工序同步作业进行标准化,例如当1名作业员操作3台设备作业时,记录作业步骤和标准时间及标准半成品个数的表格是标准作业票。
这个票是由生产部门编制,用于现场的指导监督。
现场用此票教导作业员,进行作业指导。
标准作业包括三个要素:Ⅰ. 标准作业的周期时间Ⅱ. 一个标准作业周期中手工作业顺序Ⅲ. 标准在制品(WIP—Work In Process)的数量。
要素1 标准作业周期指的是需要花费多长时间生产1个产品,由生产数量和设备运转时间决定。
要素2 作业顺序表现出来怎样的加工的顺序。
不是产品流动的顺序。
要素3 标准半成品(WIP)进行作业过程中必要的工序内半成品的最低个数,包括滞留在机器上的部分。
将这三个要素集中起来,班长组长等生产第一线的管理者对此加以分析总结。
同时为了更好地实现标准作业的目的,生产现场在严格执行作业标准的同时,也有权力及义务对效率提出改善及革新的提案,前提是新方法必须有数据证明确实优于现行方法时,才能提出对标准的更新。
切忌现场管理者凭感觉判断任意更改,那样只会给生产造成混乱,严重时影响到生产计划的按期完成。
因此标准作业就是执行作业标准的同时在效率、成本、交期上进行科学改善与革新的方法。
(2)标准作业组合票(SOP)理解标准作业组合票(SOP),它是用来确定作业顺序和周期时间的,SOP表示总加工时间,包括人—机作业时间以及作业者行走的时间。
在SOP基础上建立标准作业图表。
标准作业表描述了整个产品的生产过程,它包括了标准作业的三要素以及其他信息,如重点工位、质量控制点、安全检查点等标准作业的设定中经过以下三个程序步骤:•不同工序的加工能力表•标准作业票•标准作业组合票(Standard Operation)所谓工序能力表是根据不同加工过程的生产能力(加工能力)按工艺顺序罗列出来的表。
在这个表里记录了手工作业时间、机器作业时间(自动运转时间)、更换刀具、生产切换时间等。
3讲标准作业ppt课件

F 12
3.4
G、H、I、J
G 12
38.4
H、I、J
H 12
26.4
I、J
4
I 12
14.4
J
J
8
6.4
5
K
9
41.4
H、I I
H、I
作业 要素
1
2
3
4
5
6
7
8
9 10 11 阶位
1 4 3 2 1 9 5 2 4 3 5 8 46
2 0 3 0 0 9 0 2 4 0 5 8 31
5 0 0 0 0 9 0 2 4 0 5 8 28
标准手持
第13页
2、标准作业三要素三件套
2.2三件套——工序能力表 工序能力表:
又称零件别能力表。表中应列入工序顺序、工序名称、设备号码、基本时间(包含作业者作业时间、 设备运转时间、本工序周期时间)、刀具交换时间、个数及加工能力等项目,使各工序的加工能力 一览无遗。 工序能力表是标准作业中“作业组合”的重要基准,可以说是制定标准作业的第一步。
注意点:
以人为中心;编出顺序;反复进行
第5页
1、标准作业简介
1.2标准作业的目的
简言之:通过有效率的劳动提高生产效率
直接目的:
目的一:明确安全的、低成本的生产优良产品所必须的制造方法。 目的二:将标准作业作为改善的工具使用。
根本目的:
目的一:使用必要的、最小数量的作业人员进行生产——省人化。 目的二:实现与适时生产有关的各工序的同步化——JIT之同期化。 目的三:把在制品的“标准手持量”限制在必要的最小数量——标准手持。
标准手持:
标准手持是指按照作业顺序进行作业时,为了能够反复以相同的顺序、动作作业而在工序内持有的 最小的相关名词 标准作业组合表:
标准作业制作管理改善流程与方法

标准作业的制作、管理及改善流程与方法编制审核批准一、标准作业的制作流程(制作方法见附表)“标准化”对提高效率、实现准时化生产具有十分重要的支撑作用。
“标准化’不仅包括产品标准化、零部件标准化、质量标准化,还包括作业的标准化、在库的标准化。
所谓标准作业,是将作业人员、作业顺序、工序设备的布置、物流过程等问题作最适当的组合,以低廉的成本按照“节拍”为根本,生产出优质产品的一个作业基准,以达到生产目标而设立的作业方法。
它是以人的动作为中心、按没有浪费的操作顺序进行生产的方法。
为了提高效率、消除浪费,需要不断的改善标准作业,通过提高效率实现少人化生产。
因此标准作业是现场管理的依据,也是改善生产现场的基础。
标准作业编制流程:1①以人为本②反复修正③现场编制2、标准作业的三要素①生产节拍②生产顺序③标准在制品数量3、标准作业的目的①明确生产制造的方法,将现场积累的经验标准化②作业改善的工具,没有标准就没有改善③发现浪费二、标准作业的管理流程三、标准作业的改善流程及方法完美无缺的标准作业是没有的,标准作业只是相对于目前情况下最有效的作业方法。
改善标准作业的目的是为了提高效率,即提高每人每小时的产量,但这些产量必须是可销售量。
1、标准作业改善的改善流程:2、现场程序分析改善:3、现场改善着眼点工位改善①现场寻找问题点,减少单个工位的操作浪费②动作的数量能否再减少?③重复的动作(操作)是否同时在进行?④动作(操作)的距离能否再缩短,搬运是否过多、浪费?⑤动作(操作)能否更轻松?4、作业改善在进行程序分析改善时,通常采取5W1H工作法和ECRS分析法。
㈠、5W1H分析法:①Why——为什么干这件事?(目的)。
②What——怎么回事?(对象)。
③Where——在什么地方执行?(地点)。
④When——什么时间执行?什么时间完成?(时间)。
⑤Who——由谁执行?(人员)。
⑥How——怎样执行?采取哪些有效措施?(方法)。
标准作业
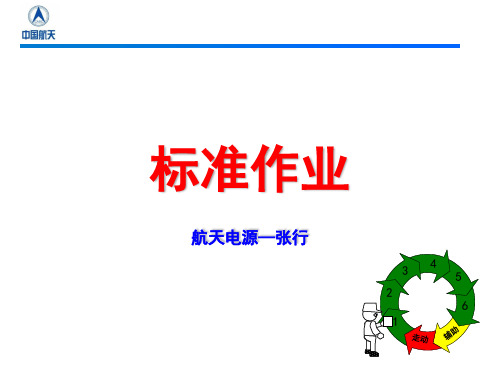
,即指按照作业顺序进行操作时,为了能使生产活动能够以相同的顺
序、动作重复地持续下去,必须在工序内保持有最少限度的在制品 (或待加工品)。
如:正在机械内加工的物品,有时为了质量检查或下工序加工条件的
需要,也必须在工序间设定一定数量的在制品,没有这些标准中间在 库,作业者就不能进行循环作业。 在制品不包含最初工序前的毛坯及最终的成品。
坏例子
A2 ⒁ 好例子 A 3
B1 粗材A ⒃ ⑽ A6 B9 粗材B ⑴ ⑼ A5 B8 ⑻ B7 ⑵ ⑺ B6
B2 ⑶ ⑹ B5
B3 ⑷ ⑸ B4
⒀
⑿ A4
建滔化工集团 Kingboard Chemical Holdings Ltd.
要素之三:标准手持
标准手持——标准在制品量,是指维持正常工作进行的必要的库存量
TT与生产线的实际生产周期、设备生产能力、作业者人
数都没有关系。
建滔化工集团 Kingboard Chemical Holdings Ltd.
案例分享 早会 10min 准备 5min 每日有效工作时数:
工休 10min
中餐 35min 工休 10min 整理 5min 晚会 5min
标准出勤时间:8H即480min
理解要点:
1日的可工作时间又称为运转时间或定时作业时间,这
是一个衡定值;
1日的必要生产量即客户需求量,它是由市场决定的,
即生产节拍根据市场需求量确定;
确定了TT,就决定了每个人在此时间内可完成的工作量,
各生产线和作业人员必须按照生产节拍组织生产,不能 超前,也不能滞后,否则就会出现生产过剩或延误交货;
卸/装/启动
检查
等待
包装 操作工周期时间Operator Cycle Time (OCT)
标准化作业——SOP
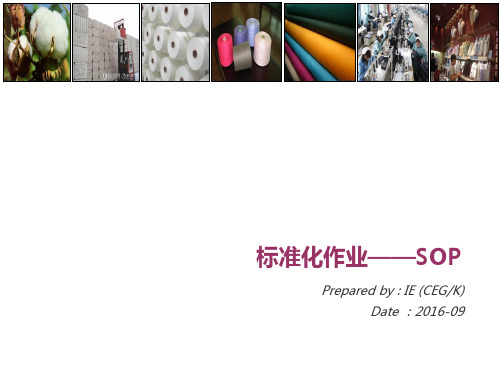
“时间是操作的影子”,多数的“慢”
是由于操作和程序不对头造成的。
——丰田生产方式
丰田安装Camry副座椅的例子:
这道工序被分成7项任务,当车辆以固定的速度通过工作区域 时员工必须在第55秒内完成所有7项任务。
第4项任务应该在31秒前完成,如果员工在第40秒仍然在做 执行第4项任务,那就意味着出现了差错;
小范围: 工序WIP 大范围: 整个流程WIP
标准化作业—— 定义
标准化作业是以人的
动作为中心、并排除在 作业中的浪费,以没有
浪费的操作顺序有效地进 行生产的作业方法。
什么是标 准作业
简单来说:标准化作业是以较少 的工数(工时),生产出高品质 的产品的一种工作方法;
操作方式的差异会导致质量、生产率下降、成本升高,
——破译丰田生产体系的DNA “员工如何作业”
标准化作业—— 三要素 标准化作业
周
作
标
期
业
准
时
顺
存
间
序
量
标准作业—— 三要素
⑴ 生产节拍:
a.节拍时间(T.T) 制单产量目标1000件/10H,TT=36s
b.循环时间(C.T)
制单 工序名称
2799 2799 2799 2799 2799
运领 切领边 修反烫领尖 间领面 切上级领脚
更重要的是,这些差异掩盖了工作方式与结果之间 的关联性,从而妨碍了组织的学习和改进;
——破译丰田生产体系的DNA “员工如何作业”
标准作业—— 核心
改善是标准作业的核心
标准作业是改善生产线的出发 点。
因为标准作业是以人的动作为 中心而制订的,各项作业的时 间如果有出入,则清楚的表明 还有改善的余地。
美的标准化促进持续改善201611培训

标准作业改善的着眼点 纯作业时间
人 缩短C.T(循环时间)
改善的着眼点 改善制造现场的 什么,可以提高品 质、效率?
设备
可运转率
减少每个循环的作业时 间偏差
拖后退的地方只
有一个
品质
缩短M.C.T(设备的 C.T)
缩短准备换夹具的时间 减少设备故障率
减少返修
减少不合格品
标准作业改善的方法论(思路)
“U”形、逆时针布置
设备布置“三不”原则
设备间距小 设备功能够用就好(不追求大而全)
标准作业前准备——物的方面
单个传递 同步化生产(接力式)
中间在库
标准作业前准备——人的方面
作业人员多能工化 多工序操作
循环操作(站立、走、运)
少人化
动作科学(动作经济原则-以最少的劳力得到最大的工作效果)
标准化作业:
“成文的” ——写成文字的,并张贴 在工作场地的。
标准化作业:
思考:
从“当前最佳的方法”这句话能得 到什么启示? 时间 安全
当前
时效性 最佳
质量 成本
什么是标准化作业?
在对作业系统调查分析的基础上,将现行作业 方法的每一操作程序和每一动作进行分解,以科 学技术、规章制度和实践经验为依据,以安全、 质量效益为目标,对作业过程进行改善,从而形
标准化
标准作业的前提条件
以人的动作为中心并且应是反复作业 在机械设备和生产线的运行中,不能有太多的故障
保证质量,尽量减少问题的发生 标准作业是管理生产现场的依据,也是改善生
产现场的基础。遵守标准作业可以保证产品品质、 也决定生产数量、制造成本。
标准化
IE工业工程培训教材-第4章

☺ 所谓作业分析是指为了作业改善及消除浪费而充分理解作业内容中的构成因素及作业的区分,并掌握好其组合是否有浪费,为了进行改善分析要素作业的方法。
☺所谓的要素作业是指作业分割时的一个精确度的单位,一般用秒表测试的最小单位;比如说“夹起配件”或“印A面”等存在的某种目的的最小单位;一般把要素作业可称之为比单位作业小,但又比动作大一个台阶的作业的综合。
1) 通过对作业进行详细分解,调查是否有遗漏,甚至能发现平常作业时是感觉不到的细微的浪费。
2) 根据现象的定量掌握,准确地掌握好目前的方法;为了彻底清除浪费及有效的作业有必要更具体地观察并理解目前的作业。
3) 为了改善要素作业及其周围的工器具、设备、加工条件、配件的精确度等进行第一阶段。
☺ 作业分析分为基本分析和重点分析☺ 基本分析又分为单独作业分析和组合作业分析;组合作业分析又分为人与人的组合作业分析及人与设备之间的组合作业分析。
图I4—1图I4—2(1)将作业按要素作业分割的单位越小越好,但一定要保证能检测到的大小。
(3/100分~5/100分为界限)(2)分为主要目的要素和辅助目的要素①主要目的要素:磨,切削,装配,分割等②辅助目的要素:夹配件,放材料等(3)作业分为作业者要素及设备要素;比如以机加工为中心的作业时又分为人的作业时间和设备作业时间。
(4)尽可能把要素作业分为不同的目的;比如加工、移动、检查、等待等。
(5)分为规则要素及不规则要素①规则要素:每一个作业或一个周期所发生的要素。
例:把配件安装在设备上,把配件从设备上拆除。
②不规则要素:作业中需要,但跟规则或基本要素作业的周期相比无规则间距所发生的因素。
例:用测试仪测数据,刷掉刀架上的铁屑等。
☺首先对测试对象进行充分的预备调查。
(1)调查对象作业是否正常地按规定进行。
(2)调查材料是否与正规的一致。
(3)调查是否使用规定的设备设备或工具。
(4)调查现场配置是否处于规定的状态。
(5)其它条件是否在规定的状态下进行。
- 1、下载文档前请自行甄别文档内容的完整性,平台不提供额外的编辑、内容补充、找答案等附加服务。
- 2、"仅部分预览"的文档,不可在线预览部分如存在完整性等问题,可反馈申请退款(可完整预览的文档不适用该条件!)。
- 3、如文档侵犯您的权益,请联系客服反馈,我们会尽快为您处理(人工客服工作时间:9:00-18:30)。
工时观测表:
工序名称: 区别不同产品不同工序 测定时间: 观测次数:
测量日 2016.01.03 分解编号 观测人 3 4 5 6 7 8 9 10 最小 时间 1/1 制造课 平均 时间
作业要素: 观测的最小的分割单位 换一个人操作也不影响
对象工序
3434 UV 工序
要素作业 r 1
测定时间 2
②
Inkjet喷码
③
运输到FIPG货架
x3x6
标准手持
标准作业票:
谢谢!
0 100 200 300
手动 标 准 作 业 组 合 票 步行 等待
1 T/T 0 C/T 0 产线 能力
1.029 1 27600
制 作 年月日 所 属 35000
1 格10 秒
1000 1100 1200
手动作业 自动作业 等 步 待 行
工序名称
每班要 求产量
作
业
名
称
作
400 500
业
600
时
工时观测表:
测定和统计人的作业时间 步骤1 观察作业内容2~3次(或半小时),把握作业顺序,作业方法及观测位置,确定要素作业[正常作业、异常作业(出现异常情况进行重新拆装配、有质量问题 换件)、不定期作业(如每三台车取一次小件或每十多台取一次标准件)、间歇作业(每五台取一次中小件)]
划分作业要素的原则 1.容易看出动作的起点及终点; 2.有利于提高观测精度; 3.要由同一目标的一系列动作构成; 4.人操作时间和机器操作时间要分开; 5.规则要素和不规则要素要划分清楚; 6.可变要素和不变要素必须分开.
No.
1 从UV传送带取下铝板夹子标识 t r 2 检查产品FIPG外观 t r 3 将铝板放入推车 t r 4 填写跟踪单(结束) t r 5 空推车放置到UV下料位置 t
观测值: 现场观测 不包含异常情况
周期时间
r 是你观测过程中的”时刻“,相邻两“时刻”之间的时差即是该动作单元所用时间; t是若干次时间的平均值。
固定下来,不能随意改变 设备 按照生产工艺进行排布
经过系统的作业培训 人员
做好作业时间测量的准备工作
对作业流程/设备操作非常熟悉 做好物流的标识和摆放 物料 做好在制品管理,包装测试的连贯性 作业方法 固定下来,不能随意改变
确定作业项目及其顺序
做好物流的标识和摆放
人员现在观测位置
根据秒表记录作业项目的时间数据
IE 标准作业三件套
为什么要搞标准作业?目的是什么?有什么好处?
标准作业的必要条件:
① 节拍时间(决定人的动作) ② 作业顺序(不是工序的顺序,而是人的作业顺序) ③ 标准手持(工序内标准在制品库存)
例: 节拍时间TT:运行时间/计划产量 =10小时*3600秒 / 35000片 =1.029 秒/片
工时观测表:
步骤2 将要素作业填入观测用表格,一边看作业情况一边记忆观测点。 (观测点是指各要素作业完成的瞬间)要素作业的观测可能的幅度为2~3秒。 步骤3 观测时间。 * 秒表中途不停,读取要素作业结束时秒表的刻度,填入观测专用表格。 * 观测次数需要10次左右。 * 例外作业的内容・时间每次都要填入。(例外作业为你确定的要素作业以外的作业) 步骤4 算出1个循环的时间。 * 用红字将1个循环时间填入时间栏。 步骤5 确定循环时间。 * 观测10次左右,取其中的最小值,填入要素作业时间栏的最下段。 (要注意,这是可以进行连续作业时间,不含异常值。) 步骤6 算出各要素作业的时间。 * 用红字填入下段。(用下段的时间值减去上段的时间值,其结果填入下段。) 步骤7 确定各要素作业时间。 * 要素作业时间之和,要对应循环时间。(不变更循环时间值。) ‴ 算测量尚未测定的要素作业 ‴例外作业的内容及时间测定 测定和统计自动作业时间 ①测定从按下开关,各个目的作业完成,直到返回原位置的时间。(可以随时进入下一个作业的状态) ②观测次数,以2~3次为宜
工时观测表:
1.每工序步骤的作业实际时间(标准作业规定下操作) 2.每工序步骤的作业平均时间 (培训参考时间) 3.可计算每工序步骤的作业标准时间(平均时间*15%的时间宽放系数)
工序别能力票:
1.作业顺序及工序名称 2.基本时间(手动作业,自动加工,完成时间) 3.加工能力(与需要量比较) 4.显示工序瓶颈(人或者设备?) 5.明确改善点
1 2 3 4
工序别生产能力表
机器 番号
品番号 品名称
手作业时间 分 1 1 秒 1 1 自动时间 分 1 1 秒 1 1 完成时间 秒 122 122
生产线 生产量
刃具交换 个数 个 30 30 时间 秒 100 100
个(人工: )
作成者 技术课 =瓶颈工序 年月日
备注
加工能力最小的工序
加工能力 生产数量 个 265 226
产线名 工程名 作 业 内 容
3434 Inkjet工序 Inkjet房间货架 FIPG货架 开始 结束
标 准 作 业 票
品质检查 安全注意 标准持有
标准持有数 节拍时间
制 作 日 制 作 者
周期时间
作业人数 2
分解编号 3/3
80片
1.029s
0.851s
工序图示
标准作业人数
作业人员 作业顺序
①
下货架运到inkjet设 备旁
工 程 名 称
自动设备的 描述
自动加工时 间 手动作业时 间
加工能力: =总工作时间/(完成时间+交换时间/交换个数) 完成时间 =手动+自动 换模时间
工序名称
工序别能力表:
标准作业组合票:
品 品 番 名 工序 作业 顺续 1 3434 无尘室进料 时 手动 推车从UV后到装入烘箱并激活烘箱程序 1 填写跟踪单(进)及电脑输入 跟踪单返回烘箱 烘箱烘烤设备能力 填写跟踪单(出)及电脑输入 关闭烘箱并将推车挪出烘箱送至冷却房间 自动 间 步行 等待
观测要点:
(1)通过时间观测 ① 依据算出的循环时间,把握每个循环时间的不均 衡及其真正原因。 ② 把握第几次中发生的附带作业(例:空箱处置, 品质检查等)的内容。 (2)通过定点站立观测目的 ① 为降低设备故障与急停,及作业时间的不均衡, 站在能够很好观察生产线状况的位置,在现场现 物中把握真正问题,以便进一步改善。 ② 为减少品质问题,在现场现物中捕捉真正的问题 所在,加以改善。
注:有关要素作业分析的填写 a、不填写准备工作,不填写返回; b 、两秒以内的作业要素可以合并; c、不定期及例外作业(如取十台车的标准件)放在最后算例外作业; d、两个人同时用同一把气枪,有一人等待20秒以上的等待算一个作业 要素; e、在现场发现的问题及时记录; f、步行大于5秒的要素作业单列; g、检查在于5秒的要素作业列出。
物料观测工序的作业时间 填入《时间观测表》 观测和技术每个工序的作业时间 计算作业项目时间实际花费的时间 秒表时间不多往上叠加,不归零 作业项目时间花费时间取最小值作业要素作业时间 计算出一个循环的时间 循环时间取最小值作为工序的作业时间
练习:制作时间观测表的步骤是?
工序别能力表:
新 改 工 序
标准作业组合票:
1.区分每个工序步骤的手动作业时间,自动作业时间,步行时间,等待时间 2.确认人机配比合理性 3. 考量人员工作量分配的均衡性(TT时间内一个作业者可承受的作业范围)
标准作业票:
1.规定工序的标准作业顺序 2.规定工序的标准作业人数 3.规定工序的标准手持数(WIP即不影响该工序作业速度的最少库存数) 4.该工序的周期时间
要点: 1. 以正常作业为基础,异常作业在栏下方单独制作; 2. 极短的作业要素要组合在一起(2秒以内的时间); 3. 要素作业名称(步行不作为作业名称、例外作业用顺书 内不表示) 4. 作业要素太多时要集中控制在序号数量内(14项以内); 5. 一般从取零件或取工具开始,到作业周期完成为止。
标准作业票:
700 800
间
900
1300
1400
1500
作业名称: 按作业顺序填写
2 3 4 5 6 7 8 9 10 11 12 13 14 15 16 17 18 19 20 21 22 23 24 25
时间: 手动作业时间 自动作业时间 步行及等待时间 图示区
合 计
手动 1
步行 0
等待 0
标准作业组合票: