(工艺技术)2020年万吨双氧水装置工艺设计
万吨双氧水装置工艺设计

万吨双氧水装置工艺设计引言双氧水(H2O2)是一种重要的氧化剂,在工业和日常生活中广泛应用。
万吨双氧水装置是一种用于大规模生产双氧水的装置,其工艺设计至关重要。
本文将介绍万吨双氧水装置的工艺设计原则和关键步骤。
装置概述万吨双氧水装置主要包括氢氧化、蒸馏、稳定和储存等关键步骤。
下面将对每个步骤的工艺设计进行详细介绍。
氢氧化工艺设计氢氧化是万吨双氧水装置的第一步,其目的是将氢气与过氧化氢反应生成双氧水。
在氢氧化过程中,反应温度、压力和反应物浓度的控制非常重要。
常见的氢氧化工艺是气相法和液相法。
气相法可以通过氢气与过氧化氢气体相混合后进入气相反应器进行反应。
液相法是将过氧化氢溶解在水中形成液相反应体系,然后通过加热与氢气反应生成双氧水。
蒸馏工艺设计蒸馏是将反应生成的双氧水进行分离纯化的关键步骤。
在万吨双氧水装置中,常采用多级蒸馏塔进行双氧水的分馏,以得到高纯度的双氧水。
蒸馏过程中,需要考虑操作温度、压力和塔板的设计。
通过调节不同级别的蒸馏塔,可以实现对双氧水中杂质的有效分离。
稳定工艺设计稳定是将蒸馏后的高纯度双氧水进行稳定处理,以防止其分解和失效。
稳定工艺通常使用稳定剂进行反应,可选择邻苯二酚等化合物。
稳定剂的选择要考虑其与双氧水的反应速率、稳定性和成本等因素。
稳定工艺中,需要控制反应温度和稳定剂浓度等参数,以保证双氧水的长期稳定性。
储存工艺设计在储存过程中,双氧水需要保持其高纯度和稳定性。
储存设施一般采用不锈钢罐进行存储,同时考虑到储罐压力的控制和安全性。
在储存过程中,需要定期检测双氧水的含量和稳定性,并采取相应的措施进行调整和维护。
工艺设备选择万吨双氧水装置的工艺设备选择非常关键,需要考虑生产规模、工艺要求和经济性等因素。
氢氧化步骤可以选择合适的反应器和控制系统,蒸馏步骤需要选择高效的蒸馏塔和精确的温度/压力控制设备,稳定步骤可以选择适合的反应器和稳定剂供给系统,储存步骤需要选择耐腐蚀性好的不锈钢储罐和相应的压力控制设备。
20万吨氧化沟法污水处理厂工艺设计
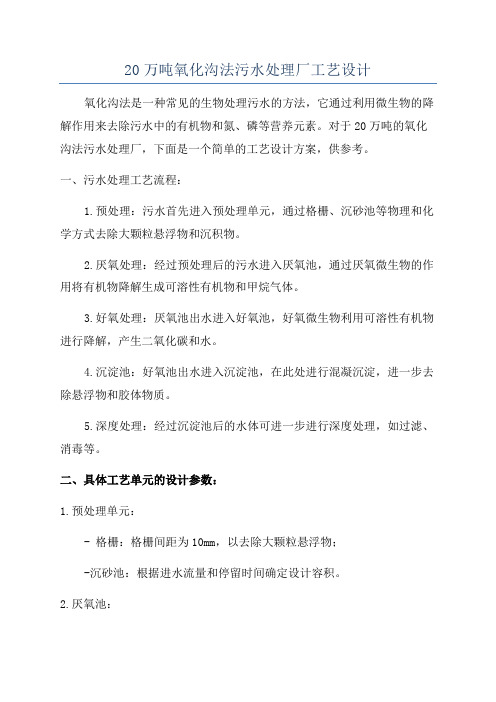
20万吨氧化沟法污水处理厂工艺设计氧化沟法是一种常见的生物处理污水的方法,它通过利用微生物的降解作用来去除污水中的有机物和氮、磷等营养元素。
对于20万吨的氧化沟法污水处理厂,下面是一个简单的工艺设计方案,供参考。
一、污水处理工艺流程:1.预处理:污水首先进入预处理单元,通过格栅、沉砂池等物理和化学方式去除大颗粒悬浮物和沉积物。
2.厌氧处理:经过预处理后的污水进入厌氧池,通过厌氧微生物的作用将有机物降解生成可溶性有机物和甲烷气体。
3.好氧处理:厌氧池出水进入好氧池,好氧微生物利用可溶性有机物进行降解,产生二氧化碳和水。
4.沉淀池:好氧池出水进入沉淀池,在此处进行混凝沉淀,进一步去除悬浮物和胶体物质。
5.深度处理:经过沉淀池后的水体可进一步进行深度处理,如过滤、消毒等。
二、具体工艺单元的设计参数:1.预处理单元:- 格栅:格栅间距为10mm,以去除大颗粒悬浮物;-沉砂池:根据进水流量和停留时间确定设计容积。
2.厌氧池:-池容积:根据单位体积有机负荷和停留时间确定;-搅拌方式:采用机械搅拌或气力搅拌。
3.好氧池:-池容积:根据单位体积有机负荷和停留时间确定;-曝气方式:通常采用曝气槽和曝气机进行气候迈气。
4.沉淀池:-池容积:根据单位流量和停留时间确定;-混凝剂投加:根据水质情况确定混凝剂的种类和投加量。
5.深度处理:-过滤:采用石英砂过滤器或纤维滤池;-消毒:常用的消毒方式有氯消毒、紫外线消毒等。
三、运行控制和监测参数:1.水质监测:对进、出水进行常规的水质监测,包括COD、氨氮、总磷等指标。
2.调节控制:根据实际情况及时调整进水量、池容积、曝气量等参数,以保证处理效果。
3.污泥处理:对厌氧池和好氧池产生的污泥进行处理,如浓缩、脱水、消化等。
总结:以上是一个20万吨氧化沟法污水处理厂的工艺设计方案,其中涉及到了预处理、厌氧处理、好氧处理、沉淀池和深度处理等工艺单元。
根据实际情况和要求,还需要结合当地的环境要求和处理效果进行调整。
万吨年双氧水装置φ4500φ5200×42000萃取塔萃取塔制造安装施工工艺

5.2.1组对场地平面布置
为了确保塔体制造质量,组对场地需砼地面约400m2,厚200mm。组对场地设在萃取塔基础的北侧(见图4)。塔体组对找正及施焊时需搭设遮阳棚300m2,棚高8m。场地布置如图4所示。
5.2.2运输
(1)第1、2、3、4大段节的重量分别为25.9t、23.6t、11.3t、7t。用30t平板车1台、50t吊车1台、30t吊车1台完成4大段筒体的倒运工作,分别将各大段筒体由预制场运至安装现场。
万吨年双氧水装置φ4500φ5200×42000萃取塔萃取塔制造安装施工工艺
2.5万吨/年双氧水装置
φ4500/φ5200×42000萃取塔
制造安装施工工艺
1、萃取塔结构简述
Φ4500/Φ5200×42000萃取塔为2.5万吨/年双氧水(折100%浓度)装置中的关键设备,能否生产出符合设计浓度(27.5%)的双氧水(H202)即决定于此塔。该萃取塔的工作压力为常压,工作介质为H2O、H2O2。该塔总高42m,由裙座、φ4.5m及φ5.2m不锈钢筒体组成,其材质为0Cr18Ni10Ti。塔内设置51层塔盘,每层塔盘由支承环、支承梁及塔板构成。该塔总重量105t,其直径、高度及生产能力目前尚属国内及亚洲地区双氧水生产装置中的同类塔之首。
φ4500段塔体焊接完成后,将位于塔盘700mm层间的人孔开孔,φ500人孔短管及补强圈暂不安装。
5.3塔盘支承环安装
5.3.1用筒体轴线投影法校验内壁方位线
(1)φ4500塔体内壁的0°线已在筒体组对时划出,尚需将90°、180°、270°方位线划于筒内壁。划法为:
以0°线为基准,将壁内园分为4等分,分别在筒体的两端及中部分取等分,将相应三点分别连成三条直线。包括原已划定的0°线,即已构成4条方位线。
20万吨过氧化氢可研

20万吨/年过氧化氢装置说明13、主要技术经济指标4、过氧化氢产品用途过氧化氢是一种重要的化工产品,由于它分解后所产生的氧具有漂白、氧化、消毒、杀菌等多种功效,且具有无副产物,无须特殊处理等特点,广泛用于造纸、纺织、化工等工农业生产。
5、性能规格及质量标准过氧化氢,俗称双氧水,分子式为H2O2,分子量34.016,外观为五色透明液体,无毒,对皮肤有一定的侵蚀作用,产生灼烧感和针刺般疼痛。
过氧化氢是一种强氧化剂,当遇重金属、碱等杂质时,则发生剧烈分解,并放出大量的热,与可燃物接触可产生氧化自燃。
过氧化氢易被催化分解,分解速度随温度升高而加快。
浓度为27.5%的过氧化氢产品,其质量指标符合国家标准GB1616-88,具体指标下表。
分析方法按国家标准(GB1616)产品外观:无色透明6、生产规模规模效益可降低生产成本,生产规模又受市场的销售情况制约,同时亦受企业投资能力等因素影响,根据市场和综合各因素,该项目生产规模确定为27.5%过氧化氢20万吨/年。
此规模既可有效地降低成本,工程建设投资适中,为适宜的经济规模。
7、原材料、辅助材料和动力技术要求及消耗过氧化氢生产成本为623.8+76=699.8元,目前市场价格为1000-1050元8、主要设备明细9、焦炉煤气制天然气,在不补碳的情况下每小时产生1。
2万m3氢气,氢气的纯度比较高,含硫很低(S<0.1PPm),这是很难得的化工原料。
考虑到本公司有苯类产品,若要深加工就存在加氢的可能。
20万吨/年过氧化氢每小时需氢气5000-5250m3,尚有近7000m3/h氢气可做他用。
过氧化氢装置的公用工程的规模比较小、其消耗也低。
投资估算:该工程项目建设总投资估算为16450万元,费用如下:稀品工段:8800万元设备费用:6000万元土建费用:1200万元安装、管件费用:1000万元仪表费用:600万元空压站:900万元纯水站0低温水站:600万元贮罐区:1000万元开车费用:3600万元(工作液、钯触媒、氧化铝等)不可预见费用:500万元浓品工段450万元设计费用:600万元。
过氧化氢生产工艺的几点技改经验
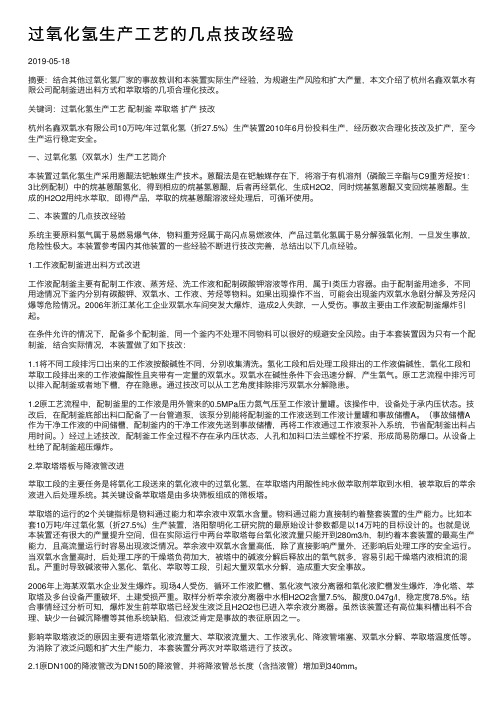
过氧化氢⽣产⼯艺的⼏点技改经验2019-05-18摘要:结合其他过氧化氢⼚家的事故教训和本装置实际⽣产经验,为规避⽣产风险和扩⼤产量,本⽂介绍了杭州名鑫双氧⽔有限公司配制釜进出料⽅式和萃取塔的⼏项合理化技改。
关键词:过氧化氢⽣产⼯艺配制釜萃取塔扩产技改杭州名鑫双氧⽔有限公司10万吨/年过氧化氢(折27.5%)⽣产装置2010年6⽉份投料⽣产,经历数次合理化技改及扩产,⾄今⽣产运⾏稳定安全。
⼀、过氧化氢(双氧⽔)⽣产⼯艺简介本装置过氧化氢⽣产采⽤蒽醌法钯触媒⽣产技术。
蒽醌法是在钯触媒存在下,将溶于有机溶剂(磷酸三⾟酯与C9重芳烃按1:3⽐例配制)中的烷基蒽醌氢化,得到相应的烷基氢蒽醌,后者再经氧化,⽣成H2O2,同时烷基氢蒽醌⼜变回烷基蒽醌。
⽣成的H2O2⽤纯⽔萃取,即得产品,萃取的烷基蒽醌溶液经处理后,可循环使⽤。
⼆、本装置的⼏点技改经验系统主要原料氢⽓属于易燃易爆⽓体,物料重芳烃属于⾼闪点易燃液体,产品过氧化氢属于易分解强氧化剂,⼀旦发⽣事故,危险性极⼤。
本装置参考国内其他装置的⼀些经验不断进⾏技改完善,总结出以下⼏点经验。
1.⼯作液配制釜进出料⽅式改进⼯作液配制釜主要有配制⼯作液、蒸芳烃、洗⼯作液和配制碳酸钾溶液等作⽤,属于Ⅰ类压⼒容器。
由于配制釜⽤途多,不同⽤途情况下釜内分别有碳酸钾、双氧⽔、⼯作液、芳烃等物料。
如果出现操作不当,可能会出现釜内双氧⽔急剧分解及芳烃闪爆等危险情况。
2006年浙江某化⼯企业双氧⽔车间突发⼤爆炸,造成2⼈失踪,⼀⼈受伤。
事故主要由⼯作液配制釜爆炸引起。
在条件允许的情况下,配备多个配制釜,同⼀个釜内不处理不同物料可以很好的规避安全风险。
由于本套装置因为只有⼀个配制釜,结合实际情况,本装置做了如下技改:1.1将不同⼯段排污⼝出来的⼯作液按酸碱性不同,分别收集清洗。
氢化⼯段和后处理⼯段排出的⼯作液偏碱性,氧化⼯段和萃取⼯段排出来的⼯作液偏酸性且夹带有⼀定量的双氧⽔。
双氧⽔在碱性条件下会迅速分解,产⽣氧⽓。
双氧水装置的安全设计
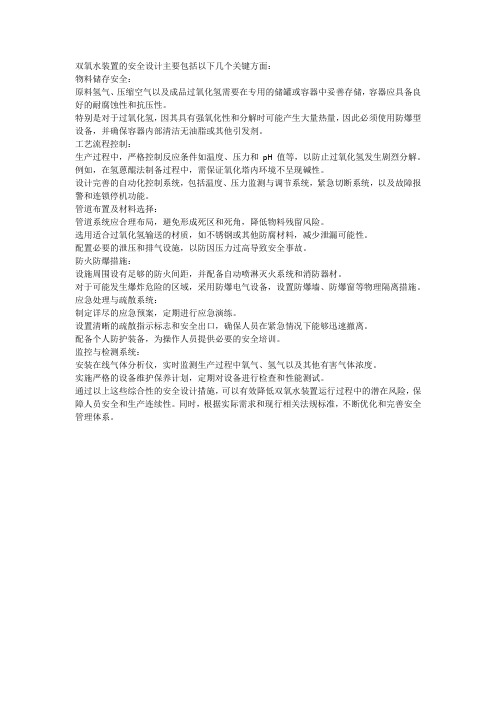
双氧水装置的安全设计主要包括以下几个关键方面:物料储存安全:原料氢气、压缩空气以及成品过氧化氢需要在专用的储罐或容器中妥善存储,容器应具备良好的耐腐蚀性和抗压性。
特别是对于过氧化氢,因其具有强氧化性和分解时可能产生大量热量,因此必须使用防爆型设备,并确保容器内部清洁无油脂或其他引发剂。
工艺流程控制:生产过程中,严格控制反应条件如温度、压力和pH值等,以防止过氧化氢发生剧烈分解。
例如,在氢蒽醌法制备过程中,需保证氧化塔内环境不呈现碱性。
设计完善的自动化控制系统,包括温度、压力监测与调节系统,紧急切断系统,以及故障报警和连锁停机功能。
管道布置及材料选择:管道系统应合理布局,避免形成死区和死角,降低物料残留风险。
选用适合过氧化氢输送的材质,如不锈钢或其他防腐材料,减少泄漏可能性。
配置必要的泄压和排气设施,以防因压力过高导致安全事故。
防火防爆措施:设施周围设有足够的防火间距,并配备自动喷淋灭火系统和消防器材。
对于可能发生爆炸危险的区域,采用防爆电气设备,设置防爆墙、防爆窗等物理隔离措施。
应急处理与疏散系统:制定详尽的应急预案,定期进行应急演练。
设置清晰的疏散指示标志和安全出口,确保人员在紧急情况下能够迅速撤离。
配备个人防护装备,为操作人员提供必要的安全培训。
监控与检测系统:安装在线气体分析仪,实时监测生产过程中氧气、氢气以及其他有害气体浓度。
实施严格的设备维护保养计划,定期对设备进行检查和性能测试。
通过以上这些综合性的安全设计措施,可以有效降低双氧水装置运行过程中的潜在风险,保障人员安全和生产连续性。
同时,根据实际需求和现行相关法规标准,不断优化和完善安全管理体系。
双氧水生产工艺流程与工艺指标
双氧水生产工艺流程与工艺指标第一节工艺流程来自循环工作液泵(P1401AB)的工作液,经循环工作液袋式过滤器(X1402D)、循环工作液过滤器(X1402ABC)滤除可能夹带的固体杂质后,流经工作液热交换器(E1105)、工作液预热器(E1102),将其预热到需要的温度后与经氢气缓冲罐分离水分、氢气过滤器(X1102)净化的氢气同时进入氢化塔(T1101)顶部。
整个氢化塔由三节触媒床组成,每节塔顶部设有液体分布器、气液分布器,以使进入塔内的气体和液体分布均匀。
根据工艺需要,氢化时可使用三节触媒床中的任意一节(单独)或两节(串联),必要时也可同时使用三节(串联),这主要根据氢化效率及生产能力的要求及触媒活性而定。
例如当使用上、中节时,工作液与氢气,先进入上节塔顶部,并流而下通过塔内触媒层,由上塔底流出,再经塔外连通管进入中节塔顶部,再从中节塔底流出,进入氢化液气液分离器(V1103)。
从氢化塔(T1101)出来的氢化液和未反应的氢气(称氢化尾气),连续进入氢化液气液分离器(V1103)进行气液分离,尾气由分离器顶部排出,经氢化尾气冷凝器(E1104)冷凝其中所含溶剂后,进入冷凝液计量罐(V1101),溶剂留于其中。
尾气再经尾气流量计控制流量后直接放空,氢化液气液分离器(V1103)中的氢化液,经自控仪表控制一定液位后,借助氢化塔内压力分出10%,先流经氢化液白土床(V1104),而后与其余的90%一起都通过氢化液过滤器(X1103ABC),之后再经氢化液袋式过滤器(X1103D),滤除其中可能夹带的少量触媒粉末和氧化铝粉末,再通过工作液热交换器(E1105)将其热量传给循环工作液泵来的工作液或者后处理工作液,然后进入氢化液贮槽(V1105)。
在此,溶解在氢化液中的少量氢气被解析出来,经过放空气冷凝器(E1106)、氢化液液封、阻火器放空。
借助循环氢化液泵(P1101AB)将氢化液气液分离器(V1103)中的部分氢化液被返回到氢化塔(T1101)中,增加塔内喷淋密度以使塔内温度均匀,氢化效率稳定及消耗氢化塔内的氧气,使操作安全。
双氧水生产工艺介绍
(2)工作液构成(配制) • 系统使用的工作液由载体(2-乙基蒽醌和四氢2-乙基蒽醌) 及溶剂组成。溶剂又由磷酸三辛酯和重芳烃组成。其中 磷酸三辛酯为极性溶剂,用于溶解氢蒽醌类;重芳烃为 非极性溶剂,用于溶解蒽醌类。 • 溶剂比:重芳烃:磷酸三辛酯=75:25-80:20 ; • 重芳烃:660-680 mL/L; • 磷酸三辛酯:210-230 mL/L; • 2-乙基蒽醌(EAQ):110-140 g/L; • 四氢2-乙基蒽醌(THEAQ):40-75% 。
• (4)蒽醌法:美国杜邦公司于1953年建成投产 第一套装置,国内由黎明化工研究院开发成功, 在 1971 年由北京氧气厂投产 。其工艺是2-烷基 蒽醌与有机溶剂配制成工作溶液,在压力为 0.30MPa下,温度55-65℃,钯催化剂存在下,通 入氢气进行氢化,再与空气进行氧化,经萃取、 再生、精制成为双氧水成品。
(7)氢气
• • • • • • • • • (1)纯度:≥98.5% (2)氮含量:≤ 1.6% (3)甲烷含量:≤ 2.0 % (4)氧含量:≤ 0.4% (5)氯含量:≤ 10 ppm (6)CO2:≤25 ppm (7)CO:≤10 ppm (8)总硫:≤ 0.1 ppm (9)汞:≤ 0.1 ppm
4、双氧水生产方法
• (1)无机反应法:无机法是最早用于制备双氧水的方法,即
用硫酸或磷酸酸化过氧化钡或其他无机过氧化物来制得双氧水, 同时形成不溶于水的钡盐或其它物质。其反应方程式如下: BaO2+H2SO4 → BaSO4+H2O2 NaO2+H2SO4+10H2O → Na2SO4· 10H2O+H2O2
双氧水装置简介
内 蒙 古 庆 华 腾 格 里 精 细 化 工 分 公 司
原辅材料及产品
• 原辅材料简介⑵
1、氢气:无色、无味气体,比空气轻,具有最大的扩散速度,熔 点-259.200C,沸点-252.800C,闪点-1500C,自燃点4000C, 与空气混合可形成爆炸混合物,爆炸极限4.1%-75%,氢气着 火时,应立即通入惰性气体,并逐渐关闭氢气,直至最后彻 底切断气源,不允许立即关闭气源。 纯度:≥99%(V/V) CH4:<1%(V/V) CO+ CH4 :<20ppm 2、空气:无尘、无锈、无油 3、脱盐水: 总硬度:≤0.02mg/kg 电导率:≤1×10-6s/cm PH值:6 ~ 7
•
内 蒙 古 庆 华 腾 格 里 精 细 化 工 分 公 司
流程叙述
• 本装置采用固定床钯触媒蒽醌法生产工艺。工艺原理是:以 2-乙基蒽醌和四氢2-乙基蒽醌(初期为0)为载体,重芳烃和 磷酸三辛酯为混合溶剂,配制成一定组成的工作液。该工作 液与氢气分别进入装有钯触媒的固定床内,进行氢化反应, 得到相应的氢蒽醌溶液(称氢化液)。氢化液中的氢蒽醌与 空气中的氧气发生氧化反应生成双氧水。同时氢化液中的氢 蒽醌还原成原来的蒽醌,此时的工作液称氧化液。由于双氧 水在水和工作液中的溶解度不同,用纯水萃取含有双氧水的 工作液得到27.5%wt的双氧水水溶液(称萃取液),该萃取 液经重芳烃净化除去可溶性有机杂质即得到成品,被萃取后 的氧化液称为萃余液,萃余液经后处理除去水份、再生后循 环使用。在氢化过程中,部分2-乙基蒽醌转化为四氢2-乙基 氢蒽醌,经氧化后得到四氢2-乙基蒽醌,可反复被氢化、氧 化成双氧水,一定量的四氢2-乙基蒽醌的存在,将有利于提 高氢化反应速度和抑制其它副产物的生成。
7、钯-催化剂
双氧水装置简介讲解
纯度(主要是三甲苯的异构体):≥99%
里
密度:0.87—0.88g/ml
精
沸程:160—200℃
细
碘值:≤2% 总硫含量:≤5ppm
化 5、磷酸三辛酯:分子式:C24H51O4P;结构式:[C4H9CH(C2H5)CH2O]P=O;
工
分子量:434.65;
分
外观:无色透明液体,基本无味 纯度:≥99% (w/w)
精
度和压力的控制要根据触媒活性情况和生产负荷的要求由低逐渐提 高。
细 氢化塔分离段液相出料分为两路:一路由氢化液循环泵抽出经过循
化
环氢化液过滤器过滤、循环氢化液换热器冷却后打进氢化塔,循环
工
氢化液的目的是调节氢化塔的温度、增加喷淋密度、稳定氢化效率
分
以及避免局部过度氢化。另一路靠压差经氢化液过滤器过滤、氢化 液冷却器冷却后进入氢化液受槽,此路氢化液在进入过滤器前约10
格
里
精
细
化
工
分
公
司
内
氢化工序
蒙
古 从后处理工序来的工作液进入工作液冷却加热器,然后从顶部进入
庆
氢化塔 。
华 自界区来的氢气进入缓冲过滤罐后从顶部进入氢化塔 。
腾
氢气与工作液在塔中充分反应,并流而下由氢化塔下部出料,从氢 化塔出来的氢化液和未反应的氢气进入氢化塔分离段进行气液分
格
离。
里 氢化反应压力控制在0.27-0.30MPa(g),温度控制在40-70℃。温
腾
气喘。与蒽醌直接接触后,可使皮肤对光敏感,但无刺激作 用。
格
外观:浅黄色或米黄色粉末或晶体。Βιβλιοθήκη 里纯度: ≥ 99%
- 1、下载文档前请自行甄别文档内容的完整性,平台不提供额外的编辑、内容补充、找答案等附加服务。
- 2、"仅部分预览"的文档,不可在线预览部分如存在完整性等问题,可反馈申请退款(可完整预览的文档不适用该条件!)。
- 3、如文档侵犯您的权益,请联系客服反馈,我们会尽快为您处理(人工客服工作时间:9:00-18:30)。
安徽淮化精细化工股份有限公司4万吨/年双氧水生产装置
工艺规程
吉林市双鸥化工有限公司
二OO三年五月
吉林市双鸥
化工有限公司
实施日期:2003年6月15日第四次修订第一版
名称双氧水生产工艺规程文件编号
第 4 页共48页
纯度(主要是三甲苯的异构体):≥99%密度:0.87—0.88g/ml
沸程:160—200℃
碘值:≤2%
总硫含量:≤5ppm
2.2. 2—乙基蒽醌
外观:浅黄色或米黄色粉末或晶体。
分子式:C16H12O2
分子量:236.27
结构式:O
C2H5
O
初熔点:≥107℃
苯中不溶物含量:≤0.1%
纯度:≥98%
硫含量:≤10ppm
铁含量:≤5ppm
吉林市双鸥
化工有限公司
实施日期:2003年6月15日第四次修订第一版
名称双氧水生产工艺规程文件编号
第9 页共48页
且可反复被氢化、氧化生成双氧水,一定量的四氢2—乙基蒽醌的存在,将有利于提高氢化反应速度和抑制其它副产物的生成。
3.2化学反应
A.氢化反应
条件:催化剂(钯),温度为40--70℃,压力0.27—0.3MPa(G)
反应方程式:
O OH
C2H5
+H2
0.27—0.3MPa(G)C2H5
O 40--70℃Pd OH
吉林市双鸥
化工有限公司
实施日期:2003年6月15日第四次修订第一版
名称双氧水生产工艺规程文件编号
第10 页共48页
B.氧化反应
条件:温度为45—55℃,压力0.22—0.3MPa(G)反应方程式:
OH O
C2H5
+O20.22—0.3MPa(G C2H5
+H2O2
OH 45--55℃O
生产双氧水辅助工艺主要包括:碳酸钾溶液的配制和回收、成品包装、工作液配制等。
附表五双氧水水溶液的密度(克/毫升)0℃
附表五双氧水水溶液的密度(克/毫升)25℃
附表六双氧水浓度换算(g/l--%)
附表六双氧水浓度换算(g/l--%)
附表六双氧水浓度换算(g/l--%)
附表六双氧水浓度换算(g/l--%)。