PCB电镀-化铜
PCB工艺电镀一次铜工艺介绍

PANEL PLATING PROCESS
1000
WHAT IS PULSE PLATING? Amps 0
-1000
电流以脉冲的方式输出,达到瞬间
-2000
反电解的效果,使电路板上高电流
-3000
Amps
区造成之差异减至最低。
0.5 sec 10 sec
36
PANEL PLATING PROCESS DC 与 PULSE电镀间的差异
Manganate:
Mn6+ + 4 e- Mn2+
Manganese dioxide:
Mn4+ + 2 e- Mn2+
還原劑可以為 Glyoxal, H2O2 or Hydroxylamine sulfate.
insoluble MnO2
Cu
Mn2+ (soluble)
Cu
9
DESMEAR PROCESS Neutralizer / 中和槽 :
DEBURR设备配置图:
风刀 超音波 风刀 刷磨段
水洗 高压水洗 水洗 超音波 中压 水洗
5
除胶渣(DESMEAR)
WHAT IS SMEAR?
钻孔时树脂产生高温超过Tg
值,而形成融熔状,冷却后
凝固形成胶渣。
Cu
功能 :
去除鑽孔後殘留孔內之基材膠渣 形成孔壁微粗糙度
DESMEAR基本流程:
Sweller
H O
+HNH +HNH +HNH +HNH
Positive charged conditioning polymer
10
DESMEAR PROCESS DESMEAR 后以电子显微镜观察之孔壁粗化清洁情形
PCB电镀铜锡工艺资料
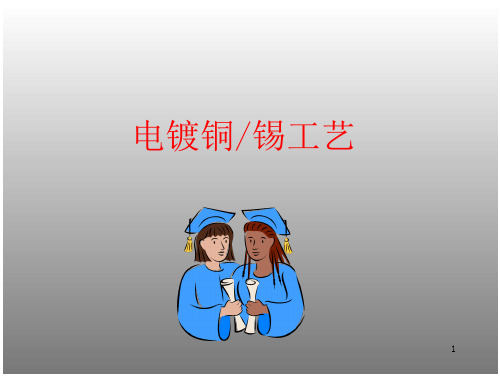
34
电镀铜溶液的控制
n 赫尔槽试验(Hull Cell Test)
n仅高电流密度区烧焦,试片的其它区域仍然正常----Copper Gleam 125T-2(CH) Additive 低 n改正方法:添加1ml/l Copper Gleam 125T-2(CH) Additive
: 濃度太低,Байду номын сангаас液導電性差,鍍液分 散能力差。
濃度太高,降低Cu2+的遷移率,電流 效率反而降低,❹對銅鍍層的延伸 率不利。
: 濃度太低,鍍層出現台階狀的粗糙 鍍層,易出現針孔和燒焦;濃度太 高,導致陽極鈍化,鍍層失去光澤 。
: (後面專題介紹)
11
操作條件對酸性鍍銅效果的影響
溫度
溫度升高,電極反應速度加快,允許電流密度提高,鍍 層沉積速度加快,但加速添加劑分解會增加添加劑消耗,鍍層結 晶粗糙,亮度降低。
31
电镀铜溶液的控制
n 赫尔槽试验 (Hull Cell Test)
阴极-
阳极+
32
电镀铜溶液的控制
n 赫尔槽试验(Hull Cell Test)参数
n — 电流: 2A n — 时间: 10分钟 n — 搅拌: 空气搅拌 n — 温度: 室温
33
电镀铜溶液的控制
n 赫尔槽试验(Hull Cell Test)
28
电镀铜溶液和电镀线的评价
n 热冲击测试
测试步骤
(1) 裁板16""x18"’ (2) 进行钻孔; (3) 经电镀前处理磨刷; (4) Desmear + PTH + 电镀; (5) 经电镀后处理的板清洗烘干; (6) 每片板裁上、中、下3小片100mm x 100mm测试板;
化学镀铜的目的及工艺流程介绍

化学镀铜的目的及工艺流程介绍化学镀铜(Eletcroless Plating Copper)通常也叫沉铜或孔化(PTH)是一种自身催化性氧化还原反应。
首先用活化剂处理,使绝缘基材表面吸附上一层活性的粒子通常用的是金属钯粒子(钯是一种十分昂贵的金属,价格高且一直在上升,为降低成本现在国外有实用胶体铜工艺在运行),铜离子首先在这些活性的金属钯粒子上被还原,而这些被还原的金属铜晶核本身又成为铜离子的催化层,使铜的还原反应继续在这些新的铜晶核表面上进行。
化学镀铜在我们PCB制造业中得到了广泛的应用,目前最多的是用化学镀铜进行PCB的孔金属化。
化学镀铜的主要目的是在非导体材料表面形成导电层,目前在印刷电路板孔金属化和塑料电镀前的化学镀铜已广泛应用。
化学镀铜层的物理化学性质与电镀法所得铜层基本相似。
化学镀铜的主盐通常采用硫酸铜,使用的还原剂有甲醛、肼、次磷酸钠、硼氢化钠等,但生产中使用最普遍的是甲醛。
化学镀铜的工艺流程:一、镀前处理1.去毛刺钻孔后的覆铜泊板,其孔口部位不可避免的产生一些小的毛刺,这些毛刺如不去除将会影响金属化孔的质量。
最简单去毛刺的方法是用200~400号水砂纸将钻孔后的铜箔表面磨光。
机械化的去毛刺方法是采用去毛刺机。
去毛刺机的磨辊是采用含有碳化硅磨料的尼龙刷或毡。
一般的去毛刺机在去除毛刺时,在顺着板面移动方向有部分毛刺倒向孔口内壁,改进型的磨板机,具有双向转动带摆动尼龙刷辊,消除了除了这种弊病。
2.整孔清洁处理对多层PCB有整孔要求,目的是除去钻污及孔微蚀处理。
以前多用浓硫酸除钻污,而现在多用碱性高锰酸钾处理法,随后清洁调整处理。
孔金属化时,化学镀铜反应是在孔壁和整个铜箔表面上同时发生的。
如果某些部位不清洁,就会影响化学镀铜层和印制导。
PCB电镀-化铜

此六图均为SAP 3+2+3切片图;左上为1mil细线与内核板之50倍整体画面。中上 为200倍明场偏光画面,右上为暗场1000倍的呈现,其黑化层清楚可见。左下为 1000倍常规画面,中下为200倍的暗场真像。右下为3000倍ABF的暗场画面,底垫 为1/3oz铜箔与厚电镀铜,铜箔底部之黄铜层以及盲孔左右之活化钯层与化铜层均 清晰可见。
7.盲孔外层孔环 8.通孔孔径 9.通孔孔环 10.Build-up层厚度 11.Core层厚度
印刷电路板各种产品的技术规格要求
PCB类别 最小线宽/线距 最小孔径 孔位精度 曝光对位精度
Desktop PC
100/100μm
0.25mm 0.20mm 盲孔120 μm 0.15mm 盲孔100 μm 盲孔75μm
PTH 孔金属化 传统的 PTH
去钻污 – Securiganth P/P500/MV/BLG
工艺流程 – 功能
只有三个工艺步骤:
溶胀 高锰酸盐 蚀刻 还原
溶胀
使树脂易被高锰酸盐蚀刻攻击
高锰酸盐蚀刻
去除钻污和树脂
还原
除去降解产物和清洁/处理表面. (清洁 / 蚀刻玻璃)
去钻污 – Securiganth P/P500/MV/BLG
去钻污 – Securiganth P/P500/MV/BLG
高锰酸盐蚀刻 – 溶胀之后 – 不经过蚀刻
去钻污 – Securiganth P/P500/MV/BLG
高锰酸盐蚀刻 – 150 秒蚀刻之后
去钻污 – Securiganth P/P500/MV/BLG
高锰酸盐蚀刻 – 240 秒蚀刻之后
还原之后
传统的 PTH
PCB电镀工艺流程

PCB电镀工艺流程PCB电镀工艺流程是在印刷电路板(PCB)制造过程中的最后一个重要工艺环节。
电镀工艺主要是为了提高PCB的导电性能、耐腐蚀性和表面质量,以便满足电子产品中对高可靠性和耐久性的要求。
下面将详细介绍PCB电镀工艺的流程。
首先是预处理部分。
这一步骤主要是为了去除PCB表面的污垢、氧化物、油脂等杂质,以便于后续工艺的进行。
预处理通常包括以下几个步骤:1.清洁:使用溶液或化学品将PCB表面的污垢和油脂去除。
2.酸洗:使用酸性溶液去除PCB表面的氧化物和金属污染物。
3.去氧化:将PCB浸泡在去氧化溶液中,去除PCB表面的氧化层。
接下来是化学镀铜。
这是为了在PCB表面形成一层均匀的铜层,以提高PCB的导电性能。
化学镀铜通常分为以下几个步骤:1.均匀化处理:为了提供一个合适的表面形状和结构,以便于后续的电镀过程。
在这一步骤中,通常会在PCB表面涂覆一层金属催化剂。
2.化学镀铜:PCB浸入含有金属铜离子的电解液中,金属铜离子在电解液中被还原为铜金属,沉积在PCB表面。
3.沉积调节:通过调节电解液中的添加剂浓度和操作条件,控制铜层的均匀性和厚度分布。
然后是锡镀。
锡镀是为了提高PCB表面的耐腐蚀性和焊接性能。
锡镀通常包括以下几个步骤:1.表面处理:通过酸洗和化学活化处理,去除PCB表面的氧化物和污染物。
2.镀锡:PCB浸入含有锡离子的电解液中,锡离子在电解液中被还原为锡金属,在PCB表面生成均匀的锡层。
3.镀锡后处理:主要是通过热处理或化学处理,使锡层表面平整、致密,并提高焊接性能。
最后是金属保护层的制备。
这一步骤主要是为了保护PCB表面镀铜和镀锡层,防止其在运输和使用过程中受到腐蚀。
金属保护层通常包括以下几个步骤:1.表面处理:通过酸洗和化学活化处理,去除PCB表面的氧化物和污染物。
2.镀金属:PCB浸入含有金属离子的电解液中,金属离子在电解液中被还原为金属,沉积在PCB表面形成保护层。
3.镀金属后处理:通过热处理或化学处理,使金属保护层表面平整、致密,并提高耐腐蚀性能。
PCB化学镀铜背光详解

PCB化学镀铜背光详解线路板 PCB 制作是一个复杂的,多级加工的过程,在生产过程中控制不当 就可能产生很多的报废和品质缺陷。
无论是使用传统的化学铜 PTH 还是新式的 直接电镀 制程,电镀前的通孔和盲孔的金属化是一个复杂的操作过程。
为保证 生产线产量最大化, 使用合理的检测方法和手段来使整个流程良好有效运作是必 要的。
另外,控 制流程中每个处理处理步骤的参数和每个部分处理后的处理效 果的确认评估是一样重要。
这需要对生产线现场有清晰直接的了解:包括对现场 制程难以想象的多次仔 细检查,现场的原材料的不断变化和提供经过确认的各 个制程的控制方法。
对 PTH 制程镀通孔的沉积覆盖率的评估和监控(PTH process)是一个十分 重要的质量控制的检查, 这样可以确保化学铜沉积处理后的镀层可以有效的提供 后续镀通孔的导电和其他性能要求,也可以及时发现生 产线的一些无法预知的 问题及时地在该环节流程进行必要的或者可能返工处理。
定期的进行背光和前光检测来监控化学铜沉积质量和覆盖率,是预防和 有 效减少化学铜制程镀层 不良缺陷的最佳方法。
背光测试可以检查出生产线上化 学铜的沉积不良或者不完整的镀层(背光不良,化学铜沉积不连续),前光测试 可 以看到化学铜沉积覆盖不良区域的位置(如环氧树脂或者玻璃纤维)和化学 铜的沉积状况,亦即环氧树脂,玻璃纤维和内层铜环处的化学铜结合状况。
使用 合理有效 地背光测试方法, 可以有效监控和检测来自PTH生产线的产品的整个 沉铜覆盖率/背光状况的变化,可以使用相对较少检测频率检查出生产线上少量, 不确定的孔 无铜问题,例如可能因为钻孔不良,钻孔毛刺/披锋,钻污等造成的。
取样频率:虽然对生产过程中的每个挂具/挂篮都取样来监控化学铜镀层质量是最好, 但是这也是不太现实的。
每个客户需要根据他们的品质要求来建立一个合理适当 的取样频率,既可以确保生产线在客户的品质要求的制程控制范围,也可以在使 用较少的取样频率和必须的检测成本之间取得平衡。
电镀铜和化学镀铜的性能分析和影响因素
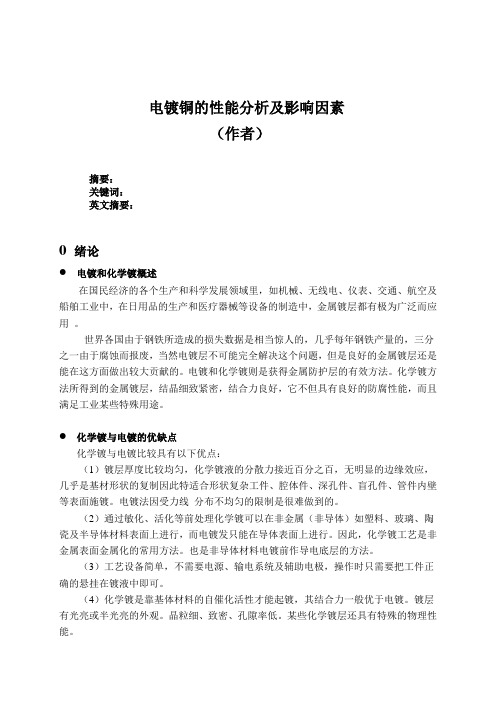
电镀铜的性能分析及影响因素(作者)摘要:关键词:英文摘要:0 绪论●电镀和化学镀概述在国民经济的各个生产和科学发展领域里,如机械、无线电、仪表、交通、航空及船舶工业中,在日用品的生产和医疗器械等设备的制造中,金属镀层都有极为广泛而应用。
世界各国由于钢铁所造成的损失数据是相当惊人的,几乎每年钢铁产量的,三分之一由于腐蚀而报废,当然电镀层不可能完全解决这个问题,但是良好的金属镀层还是能在这方面做出较大贡献的。
电镀和化学镀则是获得金属防护层的有效方法。
化学镀方法所得到的金属镀层,结晶细致紧密,结合力良好,它不但具有良好的防腐性能,而且满足工业某些特殊用途。
●化学镀与电镀的优缺点化学镀与电镀比较具有以下优点:(1)镀层厚度比较均匀,化学镀液的分散力接近百分之百,无明显的边缘效应,几乎是基材形状的复制因此特适合形状复杂工件、腔体件、深孔件、盲孔件、管件内壁等表面施镀。
电镀法因受力线分布不均匀的限制是很难做到的。
(2)通过敏化、活化等前处理化学镀可以在非金属(非导体)如塑料、玻璃、陶瓷及半导体材料表面上进行,而电镀发只能在导体表面上进行。
因此,化学镀工艺是非金属表面金属化的常用方法。
也是非导体材料电镀前作导电底层的方法。
(3)工艺设备简单,不需要电源、输电系统及辅助电极,操作时只需要把工件正确的悬挂在镀液中即可。
(4)化学镀是靠基体材料的自催化活性才能起镀,其结合力一般优于电镀。
镀层有光亮或半光亮的外观。
晶粒细、致密、孔隙率低。
某些化学镀层还具有特殊的物理性能。
电镀也具有其不能为化学镀代替的优点:(1)可以沉积的金属及合金品种远多于化学镀。
(2)价格比化学镀低得多。
(3)工艺成熟,镀液简单、易于控制。
化学镀铜的应用领域及进展铜具有良好的导电、导热性能,质软而韧,有良好的压延性和抛光性能。
为了提高表面镀层和基体金属的结合力,铜镀层常用作防护、装饰性镀层的底层,对局部渗碳工件,常用镀铜来保护不需要渗碳的部位。
1)印刷线路板通孔金属化处理目前化学镀铜在工业上最重要的应用是印刷线路板(PrintedCircuit Board,简称PCB)的通孔金属化过程,使各层印刷导线的绝缘孔壁内沉积上一层铜,从而使两面的电路导通,成为一个整体。
PCB印制电路板电镀铜及镍金工艺
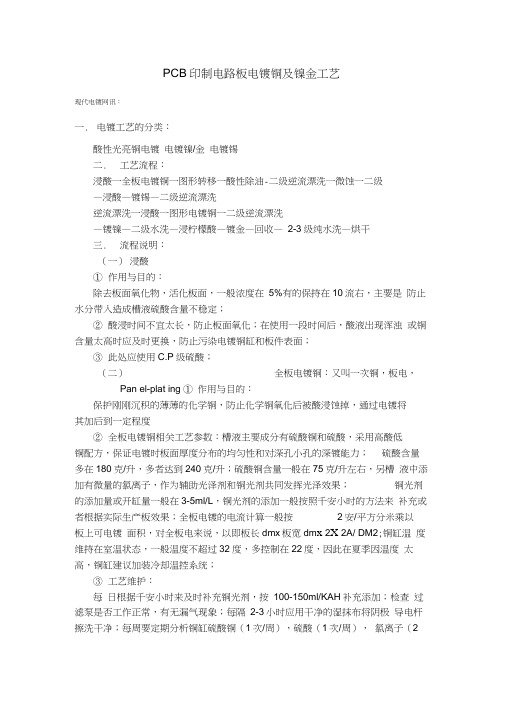
PCB印制电路板电镀铜及镍金工艺现代电镀网讯:一.电镀工艺的分类:酸性光亮铜电镀电镀镍/金电镀锡二.工艺流程:浸酸一全板电镀铜一图形转移一酸性除油-二级逆流漂洗一微蚀一二级—浸酸—镀锡—二级逆流漂洗逆流漂洗一浸酸一图形电镀铜一二级逆流漂洗—镀镍—二级水洗—浸柠檬酸—镀金—回收—2-3级纯水洗—烘干三.流程说明:(一)浸酸①作用与目的:除去板面氧化物,活化板面,一般浓度在5%有的保持在10流右,主要是防止水分带入造成槽液硫酸含量不稳定;②酸浸时间不宜太长,防止板面氧化;在使用一段时间后,酸液出现浑浊或铜含量太高时应及时更换,防止污染电镀铜缸和板件表面;③此处应使用C.P级硫酸;(二)全板电镀铜:又叫一次铜,板电,Pan el-plat ing ① 作用与目的:保护刚刚沉积的薄薄的化学铜,防止化学铜氧化后被酸浸蚀掉,通过电镀将其加后到一定程度②全板电镀铜相关工艺参数:槽液主要成分有硫酸铜和硫酸,采用高酸低铜配方,保证电镀时板面厚度分布的均匀性和对深孔小孔的深镀能力;硫酸含量多在180克/升,多者达到240克/升;硫酸铜含量一般在75克/升左右,另槽液中添加有微量的氯离子,作为辅助光泽剂和铜光剂共同发挥光泽效果;铜光剂的添加量或开缸量一般在3-5ml/L,铜光剂的添加一般按照千安小时的方法来补充或者根据实际生产板效果;全板电镀的电流计算一般按2安/平方分米乘以板上可电镀面积,对全板电来说,以即板长dmx板宽dm x 2X 2A/ DM2;铜缸温度维持在室温状态,一般温度不超过32度,多控制在22度,因此在夏季因温度太高,铜缸建议加装冷却温控系统;③工艺维护:每日根据千安小时来及时补充铜光剂,按100-150ml/KAH补充添加;检查过滤泵是否工作正常,有无漏气现象;每隔2-3小时应用干净的湿抹布将阴极导电杆擦洗干净;每周要定期分析铜缸硫酸铜(1次/周),硫酸(1次/周),氯离子(2次/周)含量,并通过霍尔槽试验来调整光剂含量,并及时补充相关原料;每周要清洗阳极导电杆,槽体两端电接头,及时补充钛篮中的阳极铜球,用低电流0。
- 1、下载文档前请自行甄别文档内容的完整性,平台不提供额外的编辑、内容补充、找答案等附加服务。
- 2、"仅部分预览"的文档,不可在线预览部分如存在完整性等问题,可反馈申请退款(可完整预览的文档不适用该条件!)。
- 3、如文档侵犯您的权益,请联系客服反馈,我们会尽快为您处理(人工客服工作时间:9:00-18:30)。
7.盲孔外层孔环 8.通孔孔径 9.通孔孔环 10.Build-up层厚度 11.Core层厚度
印刷电路板各种产品的技术规格要求
PCB类别
Desktop PC Notebook
Mobile (HDI/FPC)
BGA Flip Chip
最小线宽/线距
最小孔径
孔位精度
100/100μm
0.25mm
75/75μm 50/50μm
ABF表面完成0.3-0.5μm化学铜之后即可进行干膜光阻的压 贴,随后进行曝光与显像而取得众多线路与大量盲孔的镀 铜基地,以便进行线路镀铜与盲孔填铜。
咬掉部份化铜后完成线路
完成填充盲孔与增厚线路的镀铜工序后,即可剥除光阻而直接 进行全面性蚀该。此时板面上非线路绝缘区的化学铜很容易蚀 除,于是在不分青红皂白全面铳蚀下,线路的镀铜当然也会有 所消磨但还不致伤及大雅。所呈现的细线不但肩部更为圆滑连 底部多余的残足也都消失无踪,品质反倒更好!此等一视同仁 通面全咬的蚀该法特称为Differential Etching。
印刷线路板化铜电镀工艺及技术
Contents
1.线路板的结构及技术要求 2.线路板线路形成工艺介绍 3.线路板曝光工艺 4.线路板显影/蚀刻/去膜工艺 5.PCB 化铜工艺介绍 6.PCB 电镀工艺介绍
多层PCB的结构
1.Build-up层线宽 2.Build-up层线距 3.Core层线宽 4.Core层线距 5.盲孔孔径 6.盲孔内层孔环
SAP (半加成法)与MSAP(改良型半加成法)介绍 SAP与MSAP工艺采用Build-up工艺制作。其中SAP的主要材料为 ABF(Ajinomoto Build-up Film)和液态树脂;MSAP工艺的主要 材料为超薄铜覆铜板(基材为BT、FR-5等,铜厚≤5μm)
ABF材料
BUM液态树脂
覆铜板
线路形成工艺的种类及应用范围
盖孔法 •······ 干膜前处理
压膜 曝光 显影 蚀刻 去膜 •······
SAP •······
化学沉铜
化学清洗
干膜前处理
去膜
压膜 曝光
闪蚀 •······
显影
镀铜
MSAP •······
减薄铜蚀刻
化学清洗
干膜前处理
去膜
压膜 曝光
闪蚀 •······
显影
镀铜
线路形成工艺的种类及应用范围
线路形成工艺的种类及应用范围
Tenting Process (干膜盖孔法)介绍: 普通PCB、HDI、FPC及Substrate Core层等产品,使用的基材为 FR-4(难燃性环氧树脂覆铜板) 、RCC(涂覆树脂覆铜板)、 FCCL(柔性基材覆铜板)等材料。 FR-4:
RCC:
FCCL:
线路形成工艺的种类及应用范围
0.20mm 盲孔120 μm
0.15mm 盲孔100 μm
25/25μm
盲孔75μm
±125μm ±75μm ±75μm ±50μm
12/12μm
盲孔50μm
±20μm
曝光对位精度 ≥±50μm ≥±30μm ≥±25μm ±15μm ±10μm
线路形成工艺的种类及应用范围
1.Tenting Process (干膜盖孔法) 适用于PCB、FPC、HDI等 量产最小线宽/线距 35/35μm
此六图均为SAP 3+2+3切片图;左上为1mil细线与内核板之50倍整体画面。中上 为200倍明场偏光画面,右上为暗场1000倍的呈现,其黑化层清楚可见。左下为 1000倍常规画面,中下为200倍的暗场真像。右下为3000倍ABF的暗场画面,底垫 为1/3oz铜箔与厚电镀铜,铜箔底部之黄铜层以及盲孔左右之活化钯层与化铜层均 清晰可见。
PTH 孔金属化 传统的 PTH
去钻污 – Securiganth P/P500/MV/BLG
工艺流程 – 功能
溶胀
高锰酸盐 蚀刻 还原
只有三个工艺步骤:
溶胀
使树脂易被高锰酸盐蚀刻攻击
高锰酸盐蚀刻
去除钻污和树脂
还原
除去降解产物和清洁/处理表面. (清洁 / 蚀刻玻璃)
线路形成工艺的种类及应用范围
SAP (半加成法)与MSAP(改良型半加成法)介绍
SAP 与MSAP工艺的区别是,SAP的基材上面是没有铜层覆盖的,在制作线路前需在线路表面沉积 一层化学铜(约1.5μm),然后进行显影等工艺; MSAP基材表面有厚度为3~5μm厚度的电解铜, 制作线路前需用化学药水将铜层厚度咬蚀到2μm。
2.Semi-Addictive Process(半加成法) 适用于WB Substrate、Flip Chip Substrate 量产最小线宽/线距 12/12μm
3.Modified Semi-Addictive Process (改良型半加成法) 适用于CSP、WB Substrate、Flip Chip Substrate 量产最小线宽/线距 25/25μm
覆晶载板除胶渣的动作
与一般PCB并无太大差异, 仍然是预先膨松(Swelling)、 七价锰(Mn+7)溶胶与中和 还原(Reducing)等三步。
不同者是一般PCB只处理
通孔或盲孔的孔壁区域, 但覆晶载板除了盲孔之孔 壁外,还要对全板的ABF
表面进行整体性的膨松咬 蚀,为的是让1μm厚的化
铜层在外观上更形粗糙, 而令干膜光阻与电镀铜在 大面积细线作业中取得更 好的附着力。
目的:将可感光的干膜贴附于铜 面上
目的:将设计之影像图形,转移至 基板的干膜上
目的:将没有曝到光之干膜去除
目的:将显影后之线路镀满
目的:将多余的干膜去除
目的:将化铜层蚀刻掉
雷射成孔及全板面式除胶渣
ABF熟化后的膜厚约在30~70μm之间,薄板者以30~40μm较常用一般 双面CO2雷射完工的2~4mil烧孔,其孔形都可呈现良好的倒锥状。无 铜面之全板除胶渣(Desmearing)后,其全板面与孔壁均可形成极为粗糙 的外观,化学铜之后对细线路干膜的附着力将有帮助。
Tenting Process (干膜盖孔法)介绍
前处理
压膜
曝光
目的:清洁铜面,粗化铜面, 增加干膜与铜面的结合力
显影
目的:将感光干膜贴附在铜面上
蚀刻
目的:将设计的影像图形通过UV光 转移到PCB的干膜上
去膜
目的:将设计的影像图形通过UV光 转移到PCB的干膜上
目的:将没有覆盖干膜的铜面去除
目的:将铜面残留的干膜去除