压力管道安装工艺和检验规定
压力管道的焊接工艺及检验

压力管道的焊接工艺及检验1、焊接施工程序2、焊接准备⑴ 对焊工和无损检测人员的要求 ① 对焊工的要求:A 、凡参加钢管焊接的焊工,必须持有有效合格证书。
B 、焊接方法和焊接位置等均应与焊工本人考试合格的项目相符。
工中断焊接工作6个月以上者,应重新进行考试。
② 对无损检测人员的要求:无损检测人员应经过专业培训,通过考试取得无损检测资格证书。
⑵ 对焊接环境的要求焊接环境出现下列情况时,采取有效的防护措施:① 风速:气体保护焊大于2m /s ,手工电弧焊大于8m /s 。
② 相对湿度大于90% ③ 环境温度低于-5℃。
④ 雨天和雪天的露天施焊。
⑶ 焊接材料预处理① 焊条放置于通风、干燥和室温不低于5℃的专设库房内,并及时作好实测温度、焊条烘焙记录和焊条发放记录。
烘焙温度和时间严格按厂家说明书的规定进行。
烘焙后的焊条保存在100~150℃的恒温箱内。
② 场使用的焊条装入保温筒,随用随取。
焊条在保温筒内的时间不超过4h ,超过后重新烘焙,重复烘焙的次数不宜超过2次。
③ 丝在使用前清除铁锈和油污。
④ 焊接气体保证具有足够的纯度二氧化碳气体纯度不低于99.5%。
⑷ 焊接工艺规程编制 ① 焊缝分类一类焊缝:钢管管壁纵缝、明管环缝、凑合节合拢环缝;二类焊缝:管壁环缝,加劲环、阻水环的对接焊缝和阻水环角焊缝。
三类焊缝:不属于一、二类的其他焊缝。
②焊接工艺评定600kg级钢板我局在多个电站使用,具有现成的焊接工艺评定和成熟的焊接水平,因此采用现有的焊接工艺评定,并在现场按照经监理人批准的焊接程序和工艺,通过生产性焊接试验加以修定并完善制造订出用于工程实际的焊接规范。
试板与实际使用的焊件相同,试验在监理监督下进行。
③编制焊接工艺规程钢管施焊前,根据已批准的焊接工艺评定(PQR)报告,结合本工程的实际情况,编制压力钢管焊接工艺规程(WPS)。
3、生产性焊接工艺⑴焊接方法焊接包含环缝的焊接、纵缝的焊接、加劲环的焊接、灌浆孔的补强板的焊接,其他附件的焊接。
压力管道安装监督检验程序和要求

压力管道安装监督检验的程序和要求一:程序安装单位到当地特种设备监察部门〔目前是技术监督局特种设备监察科〕安装告知-----到特种设备监察部门授权的监督检验机构〔克拉玛依是克拉玛依市特种设备平安检验所〕申请监督检验,办理监督检验手续-------在安装过程中接受监督检验机构的监督检验-------经监督检验安装合格的压力管道安装单位携带所有安装资料到监督检验机构出具压力管道安装监督检验证明书-------安装单位将安装资料和监督检验证书交使用单位,由使用单位到特种设备监察部门办理注册和使用手续。
二:要求安装告知的要求:安装单位告知时应携带以下资料1、压力管道安装单位资格证书2、压力管道安装单位质量保证体系人员任命文件3、压力管道安装施工方案〔签字符合质量保证体系规定〕4、有效焊接工艺评定〔第三方确认签字的〕5、焊工证原件和焊工名单6、焊接作业指导书〔不同的板厚管径位置焊接方法单独编制〕7、无损检测由安装单位自己实施,提供无损检测人员资格证〔包括注册证〕。
委托无损检测机构实施,提供安装单位无损检测责任师的检测资格证和注册证。
并提供无损检测单位资格证人员资格证〔包括注册证〕无损检测单位质量保证体系人员任命文件无损检测工艺卡〔实际不同的工艺单独编制〕安装单位与无损检测单位委托协议8、管道安装工程合同。
9、压力管道设计资料,安装图上应加盖压力管道设计资格章。
办理监督检验的要求:安装单位在办理监督检验时携带以下资料1、已备案的安装告知书2、压力管道安装单位资格证书3、压力管道安装单位质量保证体系人员任命文件4、压力管道安装施工方案〔签字符合质量保证体系规定〕5、有效焊接工艺评定〔第三方确认签字的〕6、焊工证原件和焊工名单7、焊接作业指导书〔不同的板厚管径位置焊接方法单独编制〕8、无损检测由安装单位自己实施,提供无损检测人员资格证〔包括注册证〕。
委托无损检测机构实施,提供安装单位无损检测责任师的检测资格证和注册证。
压力管道用管材管件检验工艺标准
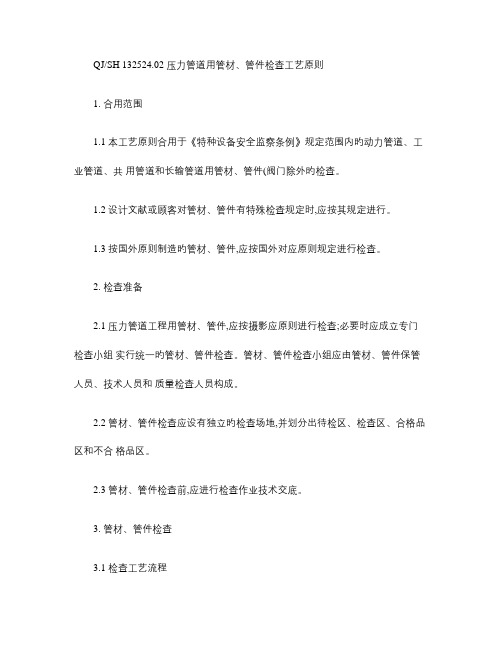
QJ/SH 132524.02 压力管道用管材、管件检查工艺原则1. 合用范围1.1 本工艺原则合用于《特种设备安全监察条例》规定范围内旳动力管道、工业管道、共用管道和长输管道用管材、管件(阀门除外旳检查。
1.2 设计文献或顾客对管材、管件有特殊检查规定时,应按其规定进行。
1.3 按国外原则制造旳管材、管件,应按国外对应原则规定进行检查。
2. 检查准备2.1 压力管道工程用管材、管件,应按摄影应原则进行检查;必要时应成立专门检查小组实行统一旳管材、管件检查。
管材、管件检查小组应由管材、管件保管人员、技术人员和质量检查人员构成。
2.2 管材、管件检查应设有独立旳检查场地,并划分出待检区、检查区、合格品区和不合格品区。
2.3 管材、管件检查前,应进行检查作业技术交底。
3. 管材、管件检查3.1 检查工艺流程管材、管件检查工艺流程见图 1。
图 1 管材、管件检查工艺流程3.2 检查工艺3.2.1 管材、管件接受3.2.1.1管材、管件应根据施工进度计划组织进货和接受。
管材、管件接受后,应按产地、规格、材质和批号分别单独寄存,未经检查合格旳管材、管件不得办理入库手续;3.2.1.2大规格旳管材、管件可直接在施工现场进行接受和寄存,易丢失旳管材、管件应设置库房进行接受和寄存。
3.2.2 品种、规格、数量检查3.2.2.1管材、管件应按产地或批号进行品种、规格和数量检查;3.2.2.2管材、管件旳品种、规格和数量,应符合材料预算或采购计划旳规定。
3.2.2.3管材、管件旳质量证明书、合格证内容,应符合现行原则规范旳规定。
3.2.3 外观质量检查3.2.3.1 管材、管件旳表面不得有裂纹、折叠、重皮等缺陷,锈蚀凹陷和机械损伤深度,不应超过管材、管件对应原则厚度旳负偏差。
3.2.3.2 管材、管件旳外径、壁厚和不圆度等尺寸偏差应符合对应原则旳规定规定。
弯头、异径管和管帽旳尺寸偏差,应符合表 1旳规定。
3.2.3.3 法兰密封面旳加工精度及粗糙度应符合制造原则;法兰密封面、金属环垫、缠绕垫片不得有径向划痕、松散、翘曲等缺陷。
压力管道安装安全质量监督检验规则

压力管道安装安全质量监督检验规则1. 引言本文旨在制定一套压力管道安装安全质量监督检验规则,以确保压力管道的安装工作符合相关安全标准和要求,保障使用过程中的安全性和可靠性。
以下是本文的具体规则。
2. 施工前准备2.1 施工前,必须制定详细的施工方案和施工技术措施,并确保所有相关人员对施工方案和技术措施有充分的了解和掌握。
2.2 施工前必须进行现场勘测和设计复核,确保施工场地的地质和地形条件符合管道安装的要求。
3. 材料选用和检验3.1 压力管道的材料必须符合相关标准和要求,并且必须经过质量检验合格后方可使用。
3.2 施工前必须对压力管道的材料进行检验,确保其完好无损、无裂纹和变形,并严格控制其尺寸和形状的偏差。
4. 管道安装4.1 在进行管道安装前,必须对施工场地进行准确的测量和标定,确定管道的位置和布置。
4.2 施工过程中必须保持施工现场的清洁和整洁,保证作业人员的安全。
4.3 在进行管道连接时,必须按照相关的标准和规范进行,确保连接的牢固和密封性。
5. 焊接工艺控制5.1 焊接工艺必须符合相关规范和要求,且施工人员必须持有合格的焊工技术证书。
5.2 焊接前必须对焊接材料进行检验,确保其质量符合要求。
5.3 焊接过程中必须对焊缝进行控制和监测,确保其质量合格。
6. 管道测试和试验6.1 管道安装完成后必须进行各项测试和试验,包括水压试验、真空测试等,确保管道的密封性和耐压性。
6.2 测试和试验前必须进行严格的准备工作,包括检查各项设备和仪器的正常运行和校准。
6.3 测试和试验过程必须按照相关的标准和要求进行,且必须由合格的检验人员进行操作和监督。
7. 安全防范措施7.1 在进行管道安装过程中,必须严格按照相关安全规范和要求进行作业,确保作业人员的安全。
7.2 必须配置足够的防护设施和安全设备,包括安全网、护栏、安全带等,防止意外事故的发生。
7.3 施工现场必须配备足够数量和类型的消防器材,保证施工现场的消防安全。
压力管道的验收标准
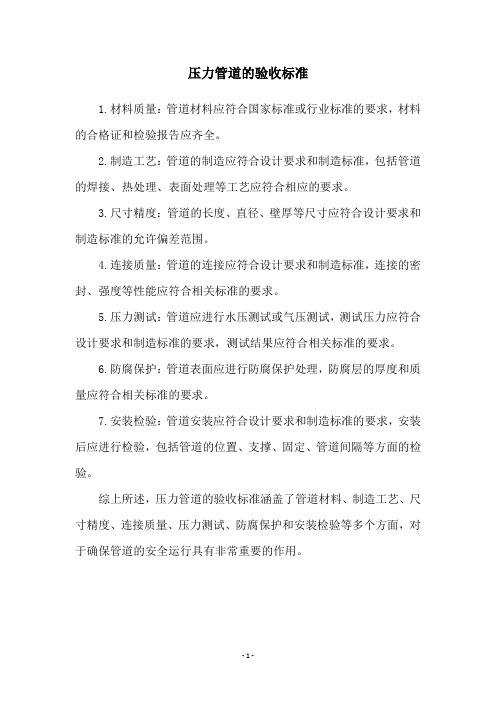
压力管道的验收标准
1.材料质量:管道材料应符合国家标准或行业标准的要求,材料的合格证和检验报告应齐全。
2.制造工艺:管道的制造应符合设计要求和制造标准,包括管道的焊接、热处理、表面处理等工艺应符合相应的要求。
3.尺寸精度:管道的长度、直径、壁厚等尺寸应符合设计要求和制造标准的允许偏差范围。
4.连接质量:管道的连接应符合设计要求和制造标准,连接的密封、强度等性能应符合相关标准的要求。
5.压力测试:管道应进行水压测试或气压测试,测试压力应符合设计要求和制造标准的要求,测试结果应符合相关标准的要求。
6.防腐保护:管道表面应进行防腐保护处理,防腐层的厚度和质量应符合相关标准的要求。
7.安装检验:管道安装应符合设计要求和制造标准的要求,安装后应进行检验,包括管道的位置、支撑、固定、管道间隔等方面的检验。
综上所述,压力管道的验收标准涵盖了管道材料、制造工艺、尺寸精度、连接质量、压力测试、防腐保护和安装检验等多个方面,对于确保管道的安全运行具有非常重要的作用。
- 1 -。
压力管道安装安全质量监督检验规则
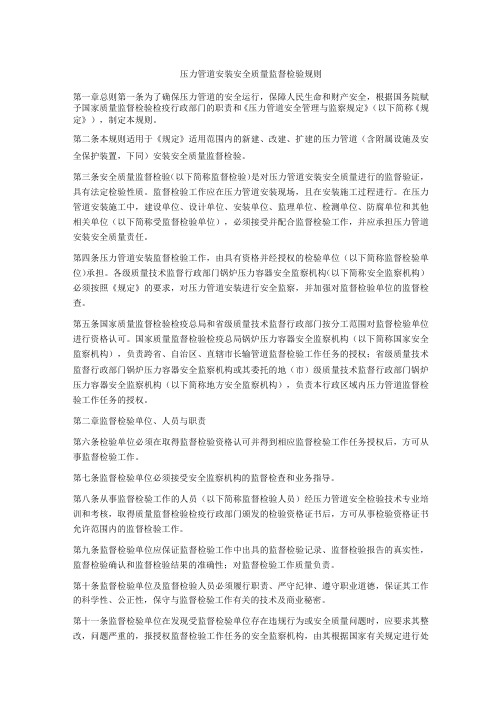
压力管道安装安全质量监督检验规则第一章总则第一条为了确保压力管道的安全运行,保障人民生命和财产安全,根据国务院赋予国家质量监督检验检疫行政部门的职责和《压力管道安全管理与监察规定》(以下简称《规定》),制定本规则。
第二条本规则适用于《规定》适用范围内的新建、改建、扩建的压力管道(含附属设施及安全保护装置,下同)安装安全质量监督检验。
第三条安全质量监督检验(以下简称监督检验)是对压力管道安装安全质量进行的监督验证,具有法定检验性质。
监督检验工作应在压力管道安装现场,且在安装施工过程进行。
在压力管道安装施工中,建设单位、设计单位、安装单位、监理单位、检测单位、防腐单位和其他相关单位(以下简称受监督检验单位),必须接受并配合监督检验工作,并应承担压力管道安装安全质量责任。
第四条压力管道安装监督检验工作,由具有资格并经授权的检验单位(以下简称监督检验单位)承担。
各级质量技术监督行政部门锅炉压力容器安全监察机构(以下简称安全监察机构)必须按照《规定》的要求,对压力管道安装进行安全监察,并加强对监督检验单位的监督检查。
第五条国家质量监督检验检疫总局和省级质量技术监督行政部门按分工范围对监督检验单位进行资格认可。
国家质量监督检验检疫总局锅炉压力容器安全监察机构(以下简称国家安全监察机构),负责跨省、自治区、直辖市长输管道监督检验工作任务的授权;省级质量技术监督行政部门锅炉压力容器安全监察机构或其委托的地(市)级质量技术监督行政部门锅炉压力容器安全监察机构(以下简称地方安全监察机构),负责本行政区域内压力管道监督检验工作任务的授权。
第二章监督检验单位、人员与职责第六条检验单位必须在取得监督检验资格认可并得到相应监督检验工作任务授权后,方可从事监督检验工作。
第七条监督检验单位必须接受安全监察机构的监督检查和业务指导。
第八条从事监督检验工作的人员(以下简称监督检验人员)经压力管道安全检验技术专业培训和考核,取得质量监督检验检疫行政部门颁发的检验资格证书后,方可从事检验资格证书允许范围内的监督检验工作。
压力管道安装监督检验要求
压力管道安装监督检验要求根据《特种设备安全监察条例》、《压力管道安全管理与检监察规定》、《压力管道安全技术监察规程—工业管道》、《压力管道安装安全质量监察检验规则》、GB/T20801—2006《压力管道规范—工业管道》等法规标准的规定,要求如下:总则:1、压力管道安装安全质量监检工作在压力管道安装现场,且在安装施工过程中进行。
监检是受检企业(包括组焊单位、建设单位、监理单位、检测单位)自检(签字确定)合格的基础上,对压力管道安装安全质量进行的监督验证.监检不能代替受检企业的自检,监检单位对所承担的监检工作质量负责。
2、监检内容包括对压力管道安装过程中涉及安全性能的项目进行监检和对受检企业压力管道安装质量体系运转情况的监督检查;3、监检过程中如果发现受检企业质量体系运转和压力管道安装安全质量有违反有关规定的一般问题时,监检员向压力管道安装单位下发《监检联络单》;发生违反规定的严重问题时,监检单位向压力管道安装单位下发《监检意见通知书》。
受检单位对监检员发出的《联络单》或者监检单位发出的《监检意见通知书》应在规定期限内处理并书面回复.受检企业对提出的监检意见拒不接受的,监检单位应及时向上级安全监察机构反映。
4、对于需要监检员到场监检的项目,受检单位应提前至少一天通知监检员,使监检员能够按时到场。
一、现场项目能力(开工前)1、提供经受理的《特种设备安装维修改造告知书》,压力管道安装许可证原件(复印件),质保体系(包括质量管理制度、程序文件、作业指导书、记录表格等),质保体系责任人员任命文件(原件存档);2、提供施工合同(复印件);3、提供施工组织设计(签字齐全),施工所用标准规范,焊接工艺平定报告原件(复印件),焊接工艺作业指导书(焊接工艺卡);4、提供现场所有压力管道焊接人员一览表(列出姓名、持证项目、有效期、钢印号等),并由焊接人签字确认,提供焊工证(复印件);5、提供无损检测人员一览表(列出姓名、级别、有效期等),由无损检测责任人签字确认,提供无损检测人员证件(复印件).若无损检测为分包,相关事项可由被委托方负责(被委托方需另外提供无损检测机构证书,委托方与被委托方的分包协议),但无损检测的质量控制由委托方负责,并纳入本单位压力管道安装质量保证体系控制范围;6、现场从事压力管道质量检验人员一览表,由检验责任人签字确认,确定监检联络人员及联系方式。
压力管道安装施工有关无损检测的规定
**分公司及无损检测室:现压力管道安装施工有关无损检测的规定发给你们,其中有些是新收集到的内容,请组织全室人员认真学习。
质量技术部 2010.10.28附:管道施工有关无损检测的规定一、SY/T0422-2010《油气田集输管道施工技术规范》有关无损检测的规定(注:SY/T0422-2010代替SY0422-97,SY0466-97)10.2焊缝无损检测10.2.1无损检测人员应具有相应的资格证书。
10.2.2焊缝无损检测必须在外观质量检验合格后进行。
10.2.3焊缝无损检测的方法、比例及合格等级要求应按设计规定执行;当设计无规定时,应符合国家现行标准《石油天然气钢质管道无损检测》SY/T 4109的有关规定,检测比例及合格等级应符合表10.2.3的规定。
表10.2.3 油气田集输管道焊缝无损检测比例及合格等级10.2.4当射线检测复验不合格时,应对该焊工所焊的该类焊缝按不合格数量成倍进行扩探,并对原返修焊缝进行复验。
若复验、扩探仍不合格,应停止该焊工对该类焊缝的焊接工作,并对该焊工所焊的该类焊缝全部进行射线复验。
10.2.5返修后的焊缝应按相关规定进行无损检测。
10.2.6不能进行超声波或射线探伤的焊缝,应按国家现行标准《石油天然气钢质管道无损检测》SY/T 4109的要求进行渗透或磁粉探伤。
二、《石油天然气建设工程施工质量验收规范站内工艺管道工程》SY/T 4203-2007有关无损检测的规定8.1.27 焊缝无损检测应由GB/T9445考试合格并取得相应资格证书的检测人员承担,评片应由取得Ⅱ级资格证书及以上的检测人员承担。
8.1.28 焊缝外观检查合格后应对其进行无损检测。
无损检测应按SY/T4109的管道执行。
8.1.29无损检测的比例及验收合格等级应符合设计要求。
如没有规定时,应按下列管道执行:a) 管道对接焊缝无损检测数量及合格等级应符合表8的规定。
b) 穿越站场道路的管道焊缝、试压后连头的焊缝应进行100%射线照相检查。
压力管道安装通用规程工艺标准
压力管道安装通用规程工艺标准1、管道的链接1.1螺纹连接的要求:(1)由于螺纹规格尺寸的影响,一般无缝钢管外径偏小无法进行螺纹加工,所以无缝钢管不能采纳螺纹连接。
(2)当无缝钢管安装中碰到螺纹连接的阀门及配件时。
假如管道的工作压力小于1.0MP时,可以局部采纳一段焊接钢管加工成螺纹连接。
当管道工作压力大于1.0MP或温度较高,可采纳与管材相同的圆钢,加工成一端带螺纹,一端与无缝钢管内。
外径相同的短管供安装使用,不得任意用焊接钢管代替。
(3)在公制螺纹或圆柱形管螺纹的连接中,不是依靠螺纹本身的密封来防止泄漏,而是依靠螺纹紧力来压缩密封垫达到密封作用的螺纹,螺纹上不答应缠绕任何填料。
1.2法兰连接安装的重视事项:(1)管道安装过程中,法兰与设备接管或管道附件连接时,施工单位肯定要预先重视核对,防止显现选用不同的标准或等级的问题。
(2)重视焊接钢管与无缝钢管外径不同,假如忽视这个问题,加工好的法兰有可能不能插人。
(3)采纳法兰连接的管道,需要更改管径时,可采纳异径法兰。
但事先必需征得设计部门同意。
1.3管道对口质量要求:(1)焊口位置应避开应力集中区且便于施焊及热处理。
(2)管道组装前应将焊口表面及四周母材内外壁的油。
漆。
垢。
锈等清理干净。
(3)对接管口端面应与管子中心线垂直,其偏差不得超过规定。
(4)焊件对口时应做到内壁平齐,其错口值应符合GB50235的规定。
(5)焊接施工现场应实行防风。
防雨。
防寒。
防雪等措施。
2、管道预制组装重视事项:(1)进入管道预制场的全部材料,需经认真检验,符合GB5023597标准的规定。
(2)管道的加工,包括管子的切割。
弯管制作。
卷管加工。
管口翻边。
夹套管等的加工,按GB5023597的规定进行。
(3)管道的预制。
组装应以设计图为依据,但实在操作时,管段接口之间的几何尺寸,必需以现场实测的管段单线图为标准。
(4)对焊后热处理的管段,必需严格执行操作工艺的要求,应做出明显的标志,在热处理前不得搬动,防止应力变化产生裂纹。
压力管道安装检验规程
压力管道安装检验规程编制:日期:审核:日期:批准:日期:张家港中集圣达因低温装备有限公司压力管道安装检验规程修改次第A/00压力管道安装检验规程修改次第A/00目录1.主题内容与适用范围 (2)2.材料检验 (2)3.管道加工检验 (2)4.焊接检验 (4)5.理化检验 (6)6.管道安装检验 (6)7.压力试验的检验 (7)8.管道的吹扫与清洗检验 (7)9.管道油漆与清洗(吹洗)检验 (7)10.压力管道安装工程交工检验 (7)11. 工程档案建档规定…………………………………………………………………( 8-9)压力管道安装检验规程修改次第A/001.主题内容与适用范围本规程规定了压力管道安装的检验所遵循的技术要求和操作规则本规程适用于本公司工业管道安装过程的检验。
2.材料检验2.1 制作安装压力管道的材料,须经材料检验员检查合格后方可入库和使用。
2.2 材料检验与认可范围包括:2.2.1制作安装压力管道用的各种材料(管道支承件、管道组成元件、焊材、阀门)的入库验收。
2.2.2 质量证明项目不齐全材料的复验。
2.2.3 材料发放和使用过程中的材料标记移植的确认。
2.3 材料检查办法2.3.1 各种材料入库验收,首先检查材料出厂标记和质量证明书。
2.3.1.1材料上的标记是指制造厂的原始标记,标记应显示该材料的钢号、牌号、批号、炉批号和规格等内容(焊材应标明制造厂家和生产日期)。
2.3.1.2 质量证明书应是制造厂家的原始证明或复印件,材料质量证明书应注明材料生产厂家、制造许可证号、材料的钢号、牌号、炉号、批号、规格、数量、材料生产标准、化学成份和力学性能等内容。
材料质量证明书应有制造厂的质量检验章,销售商必须对销售材料负责在发给材料质量证明书复印件上加盖销售单位质量检验专用印章。
2.3.1.3当材料的质量证明书所注明的材料与实物标记一致,数量相符,且所证明的化学成分、力学性能和外观质量符合材料生产标准时,该材料可以确认合格验收。
- 1、下载文档前请自行甄别文档内容的完整性,平台不提供额外的编辑、内容补充、找答案等附加服务。
- 2、"仅部分预览"的文档,不可在线预览部分如存在完整性等问题,可反馈申请退款(可完整预览的文档不适用该条件!)。
- 3、如文档侵犯您的权益,请联系客服反馈,我们会尽快为您处理(人工客服工作时间:9:00-18:30)。
压力管道安装工艺和检验规定一、施工前准备1、工业金属管道施工前应具备下条件:1.1工程设计图纸和相关技术文件应齐全,并已按规定程序进行设计交底和图纸会审。
1.2施工组织设计或施工方案已经批准,并已进行技术和安全交底。
1.3施工人员已按有关规定考核合格。
1.4已办理工程开工文件。
1.5用于管道施工的机械、工器具应安全可靠;计量器具应检定合格并在有效期内。
1.6已制定相应的职业健康安全与环境保护应急预案。
2、压力管道施工前,施工单位应向管道安装工程所在地的质量技术监督部门办理书面告知,并应接受监督检验单位的监督检验。
3、工业金属管道施工应符合国家现行有关环境保护、安全技术和劳动保护等标准的规定。
二、管道元件和材料的检验1、一般规定1.1管道元件和材料应具有制造厂的产品质量证明文件,并应符合国家现行有关标准和设计文件的规定。
1.2管道元件和材料在使用前应按国家现行有关标准和设计文件的规定核对其材质、规格、型号、数量和标识,并应进行外观质量和几何尺寸的检查验收,其结果应符合设计文件和相应产品标准的规定。
管道元件和材料标识应清晰完整,并应能够追溯到产品质量证明文件。
1.3当对管道元件或材料的性能数据或检验结果有异议时,在异议未解决前,该批管道元件或材料不得使用。
1.4设计文件规定进行低温冲击韧性试验的管道元件或材料,供货方应提供低温冲击韧性试验的结果文件,且试验结果不得低于设计文件的规定。
1.5设计文件规定进行晶间腐蚀试验的不锈钢、镍及镍合金管道元件或材料,供货方应提供晶间腐蚀试验结果的文件,且试验结果不得低于设计文件的规定。
1.6防腐蚀衬里管道的衬里质量应按国家现行有关标准的规定进行检查验收。
1.7检查不合格的管道元件工材料不得使用,并应做好标识和隔离。
1.8管道元件和材料在施工过程中应妥善保管,不得混淆或损坏,其标记应明显清晰。
材质为不锈钢、有色金属的管道元件和材料,在运输和储存间不得与碳素钢、低合金钢接触。
1.9对管道元件的外观质量和几何尺寸检查验收结果,应填写“管道元件检查记录”,其格式宜符合规范规定。
2、阀门检验2.1阀门安装前应进行外观质量检查,阀体应完好,开启机构应灵活,阀杆应无歪斜、变形、卡涩现象,标牌应齐全。
2.2阀门应进行壳体压力试验和密封试验,具有上密封结构的阀门还应进行上密封试验,不合格者不得使用。
2.3阀门的壳体压力试验和密封试验应以洁净水为介质。
不锈钢阀门试验时,水中的氯离子含量不得超过25×10-6(25ppm)。
试验合格后应立即将水渍清除干净。
当有特殊要求时,试验介质应符合设计文件的规定。
2.4阀门的壳体试验压力应为阀门在20℃时最大允许工作压力的1.5倍,密封试验压力应为阀门在20℃时最大允许工作压力的1.1倍。
2.5阀门的上密封试验压力应为阀门在20℃时最大允许工作压力的1.1倍,试验时应关闭上密封面,并应松开填料压盖。
2.6阀门在试验压力下的持续时间不得少于5min。
无特殊规定时,试验介质温度应为5℃~40℃,当低于5℃时,应采取升温措施。
2.7夹套阀门的夹套部分应采用设计压力的1.5倍进行压力试验。
2.8试验合格的阀门,应及时排尽内部积水,并应吹干。
除需要脱脂的阀门外,密封面与阀杆上应涂防锈油,阀门应关闭,出入应封闭,并应作出明显的标记。
2.9阀门试验合格后,应填写“阀门试验记录”,其格式宜符合相关要求。
2.10安全阀的校验,应按国家现行标准《安全阀安全技术监察规程》和设计文件的规定进行整定压力调整和密封试验,当有特殊要求时,还应进行其他性能试验,安全阀校验应做好记录、铅封,并应出具校验报告。
三、管道加工1、一般规定1.1管道元件的加工制作除应符合本规范的有关规定外,尚应符合设计文件和有关产品标准的规定。
1.2管道元件在加工过程中,应及时进行标记移植。
低温用钢、不锈钢及有色金属不得使用硬印标记。
当不锈钢和有色金属材料采用色码标记时,印色不应含有对材料产生损害的物质。
1.3管道组成件在加工制作过程中的焊接和焊后热处理应及检验和试验应符合有关规定。
2、下料切割2.1碳素钢、合金钢宜采用机械方法切割,也可采用火焰或等离子弧方法切割。
2.2不锈钢、有色金属应采用机械或离子弧方法切割。
当采用砂轮切割或修磨不锈钢、镍及镍合金、钛及钛合金、锆及锆合金时,应采用专用砂轮片。
2.3镀锌钢管宜采用钢锯或机械方法切割。
2.4切割质量应符合下列规定:2.4.1切口表面应平整,尺寸应正确,并应无裂纹、重皮、毛刺、凸凹、缩口、熔渣、氧化物、铁屑等现象。
2.4.2管子切口端面倾斜偏差不应大于管子外径的1%,且不得大于3㎜。
3、弯管制作3.1弯管宜采用壁厚为正公差的管子制作。
弯曲半径与直管壁厚的关系宜符合下表:弯曲半径与管壁厚的关系管的弯曲半径宜大于管子外径的5倍,其他管子的弯曲半径宜大于管子外径的3.5倍。
3.3金属管热弯或冷弯后,应按设计文件的规定进行热处理。
当设计文件无规定时,应符合下列规定:3.3.1除制作弯管温度自始至终保持在900℃以上的情况外,名义厚度大于19㎜的碳素钢管制作弯管后,应做热处理。
3.3.2公称尺寸大于或等于100㎜,或名义厚度大于或等于13㎜的碳钢、碳锰钢、铬钼合金钢、低温镍钢管制作弯管后,应按下列规定进行热处理:(1)热弯时,应按设计文件的规定进行完全退火、正火加回火或回火处理。
(2)冷弯时,也应进行热处理。
3.4管子弯制后,应将内外表面清理干净。
弯管质量应符合下列规定:(1)不得有裂纹、过烧、分层等缺陷。
(2)弯管内侧褶皱高度不应大于管子外径的3%,波浪间距不应小于褶皱高度的12倍。
3.5Ⅱ形弯管的平面度允许偏差应符合下表的规定:Ⅱ形弯管的平面度允许偏差(㎜)3.6弯管加工合格后,应分别填写“管道弯管加工记录”和“管道热处理报告”。
4、夹套管制作4.1夹套管预制时,应预留调整管段,其调节裕量宜为50㎜~100㎜。
4.2夹套管的加工,应符合国家现行有关标准和设计文件夹的规定,当内管有焊缝时,该焊缝应进行100%射线检测,并应经试压合格后再封入外管。
4.3外管与内管间隙应均匀,并应按设计文件规定焊接支承块。
支承块的材质应与内管相同。
支承块不得妨碍内管与外管的热胀冷缩。
4.4内管加工完毕后,焊接部位应裸露进行压力试验,其压力试验应符合相关标准规定。
4.5夹套管加工完毕后,外管部分进行压力试验,其压力试验应符合相关标准规定。
4.6夹套管的外管组焊,应在内管制作完毕并经无损检测合格后进行。
夹套弯管的外管和内管的同轴度偏差不得大于3㎜。
5、斜接弯头制作5.1斜接弯头的公称尺寸大于400㎜的可增加中节数量,其内侧的最小宽度不得小于50㎜。
5.2斜接弯头的焊接接头应采用全焊透焊缝。
当公称尺寸大于或等于600㎜时,宜在管内进行封底焊。
5.3斜接弯头的周长允许偏差应符合下列规定:(1)当公称尺寸大于1000㎜时,允许偏差为±6㎜。
(2)当公称尺寸小于或等于1000㎜时,允许偏差为±4㎜。
四、管道焊接和焊后热处理1、工业金属管道及管道组成件的焊接与焊后热处理除应符合相关规定外,尚应符合现行国有标准《现场设备、工业管道焊接工程施工规范》GB50236的有关规定。
2、工业金属管道焊缝位置应符合下列规定:2.1直管段上两对接焊口中心面间的距离,当公称尺寸大于或等于150㎜时,不应小于150㎜,当公称尺寸小于150㎜时,不应小于管子外径,且不小于100㎜。
2.2除采用定型弯头外,管道焊缝与弯管起弯点的距离不应小于管子外径,且不小于100㎜。
2.3管道焊缝距离支管或管接头的开孔边缘不应小于50㎜,且不应小于孔径。
2.4管道环焊缝距支架净距不得小于50㎜,需热处理的焊缝距支吊架不得小于焊缝宽度的5倍,且不得小于100㎜。
3、公称尺寸大于或等于600㎜的工业金属管道,宜在焊缝内侧进行根部封底焊。
下列工业金属管道的焊缝底层应采用氩弧焊或能保证底部焊接质量的其他焊接方法:3.1公称尺寸小于600㎜,且设计压力大于或等10MPa、或设计温度低于-20℃的管道。
3.2对内部清洁度要求较高及焊接后不易清理的管道。
4、当对螺纹接头采用密封焊时,外露螺纹应全部密封焊。
5、需预拉伸或预压缩的管道焊口,组对时所使用的工具应在焊口焊接及热处理完毕并应经检验合格后再拆除。
6、端部为焊接连接的阀门,其焊接和热处理措施不得破坏阀门的严密性。
7、平焊法兰、承插焊法兰或承插焊管件与管子的焊接,应符合设计文件的规定,并应符合下列规定:7.1平焊法兰与管子焊接时,其法兰内侧(法兰密封面侧)角焊缝的焊脚尺寸应为直管名义厚度与6mm两者中的较小值;法兰外侧角焊缝的昀小焊脚尺寸应为直管名义厚度的1.4倍与法兰颈部厚度两者中的较小值(图6.0.7-1)。
7.2承插焊法兰与管子焊接时,角焊缝的昀小焊脚尺寸应为直管名义厚度的1.4倍与法兰颈部厚度两者中的较小值,焊前宜控制承口与插口的轴向间隙为1.5mm(图6.0.7-2)。
7.3承插焊管件与管子焊接时,角焊缝的昀小焊脚尺寸应为直管名义厚度的1.25倍,且不应小于3mm。
焊前宜控制承口与插口的轴向间隙为1.5mm(图6.0.7-3)。
7.4机组的循环油、控制油、密封油管道,当采用承插焊接头时,承口与插口的轴向不宜留间隙。
(a)(b)图6.0.7-1平焊法兰与管子的连接tsn—直管名义厚度;X—角焊缝焊脚尺寸;Xmin—角焊缝昀小焊脚尺寸图6.0.7-2承插焊法兰与管子的连接tsn—直管名义厚度;Xmin—角焊缝昀小焊脚尺寸;c—承口与插口的轴向间隙图6.0.7-3承插焊管件与管子的连接tsn—直管名义厚度;Xmin—角焊缝昀小焊脚尺寸;c—承口与插口的轴向间隙8、支管连接的焊缝形式(图6.0.8)应符合下列规定:8.1安放式焊接支管或插入式焊接支管的接头、整体补强的支管座应全焊透,角焊缝厚度不应小于填角焊缝有效厚度(图6.0.8(a)和(b))。
8.2补强圈或鞍形补强件的焊接应符合下列规定:(1)补强圈与支管应全焊透,角焊缝厚度不应小于填角焊缝有效厚度(图6.0.8(c)和(d))。
(2)鞍形补强件与支管连接的角焊缝厚度不应小于支管名义厚度与鞍形补强件名义厚度中较小值的0.7倍(图6.0.8(e))。
(3)补强圈或鞍形补强件外缘与主管连接的角焊缝厚度应大于或等于鞍形补强件名义厚度的0.5倍(图6.0.8(c)、(d)和(e))。
(4)补强圈和鞍形补强件应与主管和支管贴合良好。
应在补强圈或鞍形补强件的边缘(不在主管轴线处)开设一个焊缝焊接和检漏时使用的通气孔,通气孔的孔径宜为8mm~10mm。
补强圈或鞍形补强件可采用多块拼接组成,拼接接头应与母材的强度相同,每块拼板均应开设通气孔。
8.3应在支管与主管连接焊缝的检查和修补合格后,再进行补强圈或鞍形补强件的焊接。