QC七大手法—柏拉图实例
QC培训七大手法01

•有时采用
•2、简易图表包括:柱形图、饼分图、折线图、雷达图、箭条图
•七大手法口决
• 调查集数据 • 柏拉抓重点 • 因果追原因 • 散布看相关 • 分层作解析 • 直方显分布 • 控制找异常
•一、调查表
•既可用于数字数据分 析,又可用于非数字数 据分析的工具
调查表:又叫检查表、核对表、统计分析表。它用来系统 的收集资料、积累数据、确认事实并对数据进行整理分析。
•○•○ •Ⅹ
•○•□
•缺陷符号:● 疵点 ○ 气孔 △ 成形 Ⅹ变形 □ 其它
•5、用于非数字数据分析的调查表实例
•某商场对顾客满意情况的调查表(表格式)
•NO •调查项目
•1 •服务态度差 •2 •商品种类少 •3 •商场环境差 •4 •价格偏高 •5 •服务设施差 •6 •其它
•调查者: 日期:
•测量方法(仪器)
•数据信息系统
PPT文档演模板
QC培训七大手法01
•图形:
•原因类
•主要原
•二层别原
因 •一层原因
因
•结
•果
•说明:因果图由箭条和短语组成
•主箭条右侧短语表示结果
•对应主箭条的箭条为“原因类别 线•指”向原因类别线的箭条为“第一层原 因•指”向第一层原因线的箭条为“第二层原因”以下 类•方推框框住的短语为主要原因:
• 定义:
– 又叫排列图。它是将问题或问题的影响 因素按重要性依次排列的一种简单的图 示技术。它由两个纵坐标、一个横坐标、 几个有序的长方形和一条累计百分比曲 线组成。
•用于数字数据分析的工具
• 遵循“关键的少数和次要的多数”的规律 • 来源于自然科学领域的统计规定
•频数
•频率
品管七大手法之-柏拉图(排列图)

第4章柏拉图 77第4章柏拉图(Pareto Diagram)排列图一、前言由生产现场所收集到的数据,有效的加以分析、运用,才能成为有价值的数据。
而将此数据加以分类、整理并作成图表,充分的掌握问题点及重要原因,则是目前不可或缺的管理工具。
而最为现场人员广泛使用于数据管理的图表为柏拉图。
二、柏拉图的由来意大利经济学家V.Pareto(1848-1923)在1897年分析社会经济结构时,赫然发现国民所得的大部份均集中于少数人身上,于是将所得的大小与拥有所得的关系加以整理。
发现有一定的方程式可以表示,称为[柏拉图法则]。
1907年美国经济学者M.O.Lorenz使用累积分配曲线来描绘[柏拉图法则],也就是经济学所谓的劳伦兹(Lorenz)曲线。
美国品管专家J.M.Juran(朱兰博士)将劳伦兹曲线应用于品管上,同时创出[Vital Few, Trivial Many] (重要的少数,次要的多数)的见解,并借用Pareto的名字,将此现象定为[柏拉图原理]。
[柏拉图]方法,由品管圈(QCC)的创始人日本石川馨博士介绍到品管圈活动中使用,而成为品管七大手法之一。
三、柏拉图的定义1.根据所搜集的数据,按不良原因、不良状况、不良项目、不良发生的位置等不同区分标准而加以整理、分类,从中寻求占最大比率的原因、状况或位置,按其大小顺序排列,再加上累积值的图形。
2.从柏拉图可看出那一项目有问题,其影响度如何,以判断问题的症结所在,并针对问题点采取改善措施,故又称为ABC图。
(所谓ABC分析的重点是强调对于一切事务,依其价值的大小而付出不同的努力,以获至效果;亦即柏拉图分析前面2-3项重要项目的控制)。
78 品管七大手法3.又因图的排列系按大小顺序排列,故又可称为排列图。
四、柏拉图的制作步骤1.柏拉图的制作方法步骤1:决定数据的分类项目。
分类的方式有:(1)结果的分类包括不良项目别、场所别、时间别、工程别。
(2)原因的分类包括材料别(厂商、成份等)、方式别(作业条件、程序、方法、环境等)、人员别(年龄、熟练度、经验等)、设备别(机械、工具等)等。
QC七大手法-4柏拉图

480
480
29
解:
工作内容 催 料A
8月份统计表
时数 153 89 85 51 43 40 19 累计时间 153 242 327 378 421 461 480 影响比率 % 31.9 18.5 17.7 10.6 9.0 8.3 4.0 累计影响比率 % 31.9 50.4 68.1 78.7 87.7 96.0 100.0
17
3、确认改善效果(改善前后比较): 采取改善对策后,重绘一次柏拉图,如采取 的对策有效,柱形图的高度会降低,且横轴 的不合格项目及顺序会变动。 (1)把改善前后的柏拉图排列在一起,即可 评估其改善成效。 (2)确认改善效果时,应注意下列三点: a.柏拉图收集数据的期间及对象要一致。 b.对季节性的变动应列入考虑。 c.对于对策外之要因,也应加以注意,以免 疏忽。
14
100% 170 90% 累 153 不 80% 计 合 136 70% 影 格 119 60% 响 数 102 50% 比 85 40% 例 68 30% (%) 51 20% 34 10% 17 0 不合格项目 收敛 几何 白平衡 敲闪 无画面 画面 其他 不良 失真 不良 倾斜 工 程:电气检查 总检查数:1450 总不合格数:170 期 间:10年3月5日~9日 检 验 者:王** 绘图者:李*
不良项目
收敛不良 几何失真 白平衡 敲闪
无画面
画面倾斜 其他
11
不良
步骤6:绘累计比率。 (1)纵轴右边绘折线终点为100%。 (2)将0~100%间分成10等分,把%的分度记 上(即累计影响比例)。 (3)标出前三项(或四项)之累计影响比例 是否>80%或接近80%。
12
170 153 不 136 合 119 格 102 数 85 68 51 34 17 0 收敛 不合格项目 . 不良
QC七大手法 (排列图)
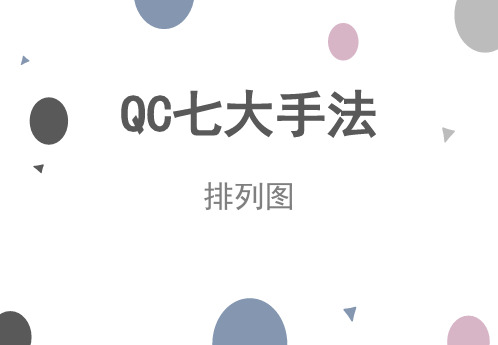
做解析
检查表
●:1号機 ▲:2号機 7月14日 7月15日 7月16日 7月17日 7月18日 7月19日 1号機 2号機 合計
●▲●● ●●
●●
●●▲ ●●
●●●
縫製
14 2
16
●●▲● ▲
仕上がり
●●
●
●●
●●●
11 2
13
●●▲●●●●● ●●● ●▲● ●●●●●●●●●●
汚れ
25 2
27
●●
●
●●●▲●▲●● ●▲
●●
●●
●▲●●●
キズ
19 6
25
●▲●
●▲●
▲●● ●●
●●
▲●
●●
▲●●
その他
11 3
14
合計
26
11
11
11
13
23 80 15 95
集数据
控制图
133.0 132.0 131.0 130.0 129.0 128.0 127.0 126.0
1 2 3 4 5 6 7 8 9 10 11 12 13 14 15 16 17 18 19 20 21 22 23 24 25
并合计。
(8)在每个直方柱右侧上方,标出累计值(累计频数和累计频率百分数),描点,用实线连接,
画累计频数折线(巴雷特曲线)。
(9)在图上记入有关必要事项,如排列名称、数据、单位、作图人姓名以及采集数据时间、主
题、数据合计等等。
频数
200
180
140
● ● ●
●
N=200
100% 75%
80
●
40
50% 25%
QC(旧)七大手法之三——柏拉图

QC (旧)七大手法之三——柏拉图一.定义柏拉图,又称排列图、主次因素图、主次因素分析图或巴雷特图、帕莱托图、帕累特图、帕累托图(Vilfredo Pareto ,1848.7.15-1923.8.19出生在巴黎,卒于瑞士,早年学习自然科学,1868年在都灵大学获工程博士学位,毕业后从事一段工程技术工作,1889年转向研究经济学,1893年任瑞士洛桑大学政治经济教授,1906年后致力于社会学研究)。
柏拉图最早由意大利经济学家Vilfredo Pareto 于1897年在研究19世纪英国社会财富分布状况时,曾用数学的方式表达了收入分配不平等和不均匀的程度而得名,他发现19世纪的英国不到20%的人(即少数人)占有(拥有)超过80%的社会财富(即大量财富),也即著名的20/80或80/20或二八原理(则)。
即80%的结果源于20%的原因。
80/20原理由“混沌理论”得到了解释。
1907年美国经济学家(M〃O〃Lorenz 洛兰茨)又以累计曲线图的形式表示出与之相似的理论(社会所得指数法则)。
两位学者都指出:“世界上大部分财富都集中在很少的一部分人手中”。
1930年美国的品质大师朱兰(J〃M〃Juran)是第一个确认这个“关键的少数和次要的多数”现象的普遍性的人,创造出了“Vital Few,Trivial Many” 名词,并将这一普遍法则命名为“帕累托原理”或“二八原则”,同时也是第一个将此原理应用于质量管理的人(1951~1956年),作为质量改善活动中寻找主要因素的一种工具(即认为影响一个质量问题有很多,其中总有少数原因对质量问题起决定性作用,称为关键的少数)。
亦即从哪里入手解决质量问题,其经济效果最好(即在生产过程中,影响质量的因素常常不止几个,而是十几个,甚至几十个,在这些纷繁庞杂的众多因素中,迅速、准确地找出主要因素的最有效方法就是“柏拉图法”。
它有利于企业抓住关键因素,用有限的资源解决更大的问题,取得更好的经济效益)。
QC七大手法

QC七大手法1 直方图为要容易的看出如长度、重量、时间、硬度等计量的数据之分配情形,所用来表示的图形。
直方图是将所收集的测定值或数据之全距分为几个相等的区间作为横轴,并将各区间内之测定值所出现的次数累计而成的面积,用柱子排起来的图形。
用途:描述数据的分布(平均值,变异,对称),借以判断工序有无异常情况。
并检查该数据是否正常受控,有足够的能力符合客户需求。
具体方法:1、找出最大值,最小值以及数据的个数;2、决定区间的个数=总数开根号;3、决定区间的宽度=(最大值-最小值)/区间个数。
4、作出频次表;5、画出直方图(如图1所示)。
图1. 直方图示意图2 管制图把品质特性的点以记号标示上去,借着该点在管制界限内侧或外侧的情形,可以判断工序是否在控制状态中。
其中,规格界限:来自客户的要求、对于产品质量的控管、每一量测单点都必须在规格界限之内;管制界限:工序变异的自然容许范围、对于制程/机台的控管、每一量测平均值都必须在管制界限之内。
用途:借由管制界限的定制,区分出工序的变异的合理性。
即时监控,并可以在制程异常时立即采取改善对策。
图2. 管制图示意图3 鱼骨图一个质量问题的发生往往不是单纯一种或几种原因的结果,而是多种因素综合作用的结果。
要从这些错综复杂的因素中理出头绪,抓住关键因素,就需要利用科学的方法,从质量问题这个结果出发,集思广益,由表及里,逐步深入,直到找到根源为止。
鱼骨图有如鱼骨增长的方式,有系统地整理工作的结果(特性)以及其原因(要因)。
用途:在改善小组的脑力激荡之下,列举所有可能的异常原因,逐一过滤之后,会发现平常忽略的小毛病,可能就是问题的根源图3. 鱼骨图示意图4 查检图在收集各种数据之后,为确认并能毫无遗漏的查检,将结果制成简单的表格。
用途:可以让数据的收集更为规律、有效;制成的表格更为简明、易懂图4. 查检图示意图5 柏拉图柏拉图能够反映出“少数关键、多数次要”的规律,也就是说柏拉图是一种寻找主要因素、抓住主要矛盾的手法。
QC 七大手法(柏拉图)

品质部 黄丹
2013/12/13
提纲
一、柏拉图基本概念 1.柏拉图的来源及含义 2.柏拉图的定义 3.柏拉图的主要用途 4.柏拉图的制作步骤 二、手绘柏拉图各步骤讲解 三、在Excel中绘制柏拉图实例讲解
2
一、柏拉图基本概念
3
柏拉图基本概念
柏拉图的来源及涵义
• 来源:1897年,意大利学者帕累托分析社会经济结构,发 现绝大多数财富掌握在极少数人手里,称为“帕累托法则 (20/80法则)”。 后来美国质量专家朱兰博士将其应用 到品管上,创出了“Vital Few, Trivial Many”(重要的少数 ,琐细的多数)的名词,称为“柏拉图原理”。
4刮 伤
10
113
7.9%
89.1%
5突 起
8
121
6.2%
ቤተ መጻሕፍቲ ባይዱ
95.3%
6其 他
6
127
4.7%
100%
各项积累数
累计比率 =
×100
总数
10
手绘柏拉图步骤讲解
• 步骤三:绘柱状图表
11
手绘柏拉图步骤讲解
步骤四: 绘积累曲线
12
手绘柏拉图步骤讲解
步骤五: 记入必要事项(完成)
13
三、在Excel中绘制柏拉图实例讲解
• 含义:影响产品质量的因素很多,但这些因素中有的起
关键作用,有的只起次要作用,如何从众多因素中找出起
关键作用的因素?通过绘制柏拉图,将这些影响因素并用
一个图来表达,就能够找到这种关键因素,然后再分别运
用不同的管理方法加以解决。柏拉图法是质量管理最常用
的工具之一。
4
柏拉图分析法实例

壁厚差大, 加工尺寸不 工装不匹配,单滚道磨削
串岗聊天、作业态 度不端正
技能水平偏低
稳定
设备破旧,精度达不 新员工多 工作经验不足
到要求
员工动手能力不 强
品质意识不强
为何效率低、产品不良率高?
仪器检测不对
原则件有误 差,精度底
加工措施不对
温差大,尺寸控制不 好
加工控制措施不当
工艺流程有问题
测
环
法
真因:加工措施不对;加工控制措施不当;工艺流程有问 题;设备老化;工装不匹配。
鱼骨图制作
制作鱼骨图分两个环节:
1、分析问题原因/构造。
A、针对问题点,选择层别措施(如人机料法环等)。 B、按头脑风暴分别对各层别类别找出全部可能原因(原因) C、将找出旳各要素进行归类、整顿,明确其隶属关系。 D、分析选用主要原因。 E、检验各要素旳描述措施,确保语法简要、意思明确。
鱼骨图制作
● 按项目数据大小顺序排列(求各项数据、合计影响度) ● 其他项排在最终
(4)图表纸上记入横轴(项目)、纵轴 (品质、特征、分度)
(5)按数据大小划柏拉图 (6)合计数以折线记入
●右端划上纵轴,折线终点为 100%
●0~100%提成10等分,把%旳 分度记上
(7)记入搜集期间、总检验数、统计者
7、柏拉图制作注意事项
不良率
100 %
80 %
累 计
影
响
度
(%)
A
C
B
D
2、柏拉图由来
意大利经济学家V.Parelo(1848-1923)于1897年分析社会经济结构时,赫然发现国民 所得旳大部份均集中于少数人身上,于是将所得大小与拥有所得旳关系加以整理, 发既有一定旳方程式可以表示,称为“柏拉图法则。” 1923年叛国经济学者M.Oloren使用累积分配曲线来描绘“柏拉图法则”,也就是经济 学所构旳劳伦兹曲线。 美国品管教授J.M.Juran(朱兰博士)将劳伦兹曲线应用于品管上,同时创出“Vital Few Trivial Many”(重要旳少数,琐碎旳多数)旳看法,并借用Parelo旳名字,将此现象 定为“柏拉图原理”。 “柏拉图”方法,由品管圈(QCC)创始人日本石川磬博士简介到品管圈活动中使用, 而成为品管七大手法之一。
- 1、下载文档前请自行甄别文档内容的完整性,平台不提供额外的编辑、内容补充、找答案等附加服务。
- 2、"仅部分预览"的文档,不可在线预览部分如存在完整性等问题,可反馈申请退款(可完整预览的文档不适用该条件!)。
- 3、如文档侵犯您的权益,请联系客服反馈,我们会尽快为您处理(人工客服工作时间:9:00-18:30)。
美 國
98% 95% 94%
臺 灣
95% 96% 93%
大 陸
94% 93% 92%
結果顯示,周師傅的方法配美國材料良品率最高,為98%.
實例二:
法拉利籠衝壓成型品質狀況日報表
日期: 序 廠 班別: □ 白班 生 良 產 品 號 商 制 程 不 良 數 制 程 不 良 率 來 料 不 良 率 □ 夜班 總 拉裂 不 良 1 2 率 眼 嘴 睛 巴 裂 裂 模號: 第一套 □ 制 第二套 □ 程 不 良 項 目 其它
… 124 …
D.決定組距: 組距=全距/組數
E.決定各組之上下組界. 1.最小一組的下組界=最小值-測定值之最小位數/2 2.最小一組的上組界=下組界+組距=123.5+4=127.5 依此類推. F.作次數分配表.(如附表)
附表:
組號 1 組 界 組中點 125.5 Ⅴ Ⅴ 劃 記 次數 10 123.5~127.5
查檢表的種類:
• 1.記錄用查檢表: 主要功用在於根據收集之數據以調查不良項目、不 良主因、工程分布、缺點位置等情形.必要時,對收集的 數據要予以層別.
作業者 機 械 不良種類 日 期 月 月 日 日 尺 寸
A No.1
疵 點 材 料
B
No.2 No.1
尺 疵 材 其 寸 點 料 他
No.2
尺 疵 材 其 寸 點 料 他
15
第三套 □
小 3 前 角 裂 4 后 尾 裂 5 1 變 形 2 缺 料 3 刮 傷 4 壓 傷 5 計
數 數
1 2 3 4 5
實例:
• 某電子廠有批精密零件在下工程裝配時發生困難,經直方 圖分析,超出規格甚多,再將此100個數據,按A,B,C三種機 種別加以層別,發現A機種的產品低於規格下限的很多,而 C機種的產品超出規格上限的很多,B機種的產品完全在規 格內.因此,只要針對A,C兩機種著手改善即可.
QC七大手法
CHART/GRAPH/SHEET – 圖表
一、圖表的功用: 圖表的應用,可以將繁雜的數字情報轉化,以最 簡單的方式表達出來,易看易懂,一目瞭然.在爭取時 間,講求效率的今天,對管理者尤為重要. 二、制作圖表的原則: 圖表的必備條件,是要能認用表者迅速內了 解全盤,把握重點,作出正確的判斷,下訂對策. 所以圖表應簡單明瞭,重點突出.
X
• 3.強負相關: X增大時,Y反而減小,稱為強負相關.
Y X
4.弱負相關: X增大時,Y反而減小,但幅度並不顯著. Y
X
• 5.曲線相關: X開始增大時,Y也隨之增大,但達到某一值后,當X增大 時,Y卻減小. Y X
6.無相關: X與Y之間毫無任何關係. ………… ………… Y ………… X
137 151 147 152 144147 142 142 150 150127 162 160142 140143 126 152 147 149 …
… … … … …
…
… … … … …
…
… … … … …
…
… … … … … …
…
… … … … … …
…
… … … … … …
…
… ... … … … …
達 成 年 度 工 作 目 標
加強生產 作業稽核
品質情報 及時反饋
推動品質 活動
三.柏拉圖:
• 1897年,意大利學者柏拉撬分析社會經濟結構,發現絕大多 數財富掌握在極少數人手里,稱為“柏拉法則”. • 美國質量專家朱蘭博士將其應用到品管上,創出了“Vital Few, Trivial Many”(重要的少數,瑣細的多數)的名詞,稱 為“柏拉圖原理”.
NG 劃“X” 未作業劃“/”
審核
不需點檢項目劃“△” 工務稽查
二.特性要因圖:
• 對於結果與原因間或所期望之效果與對策間的關係, 以箭頭連結,詳細分析原因或對策的一種圖形稱為特性要 因圖,工程魚骨圖或因果圖.
•
它為1952年日本品管權威學者石川馨博士所發明,又 稱“石川圖”.
作法:
機 人
小小因子
四.層別法:
定義:為區別各種不同原因對結果之影響,而以個別原因為主 體,分別作統計分析的方法,稱為層別法.
分類: • 1.時間的層別. • 2.作業員的層別. • 3.機械、設備層別. • 4.作業條件的層別. • 5.原材料的層別. • 6.地區的層別等.
實例一:
材料
人員 周師傅 李師傅 劉師傅
柏拉圖的用途:
• 1.作為降低不良的依據.
• 2.決定改善的攻擊目標. • 3.確認改善效果. • 4.用於發掘現場的重要問題點. • 5.用於整理報告或記錄. • 6.可作不同條件的評價.
柏拉圖應用範圍:
• • • • • • • 1.時間管理. 2.安全. 3.士气. 4.不良率. 5.成本. 6.營業額. 7.醫療.
兩個產品導 入CCD
開始研究 衝件CSI
100%執 證上崗
他山之 石檢討
應用QA Netwo綱
干部學習FMEA
改善品質 記錄稽核
每日始業點檢 點檢結 果反饋 每日IPQC 推動模 作業點檢 具稽核
隨時問題反饋
模具問 題反饋
規格問 QIT活動 品質檢討會 題反饋 10次以上 來料問 推動成立QCC 題反饋 協助生產 18圈以上 品質教育 每周品質 他山之石匯整 訓練 狀況匯整
散布圖的制作方法
制作步驟:
一. 資料搜集
二. 找出數據中的最大值和最小值
三. 畫出縱軸橫軸刻度,計算組距
四. 將各組的對應數據標示在座標上
五. 記下資料和圖的條件.
散布圖的判讀:
• 1.強正相關: X增大,Y也隨之增大,稱為強正相關.
Y X
2.弱正相關: X增大,Y也隨之增大,但增大的幅度不顯著. Y
散布圖判讀注意事項:
• 1.注意有無異常點. • 2.看是否有層別必要. • 3.是否為假相關. • 4.勿依據技術、經驗作直覺的判斷. • 5.數據太少,易發生誤判.
六.直方圖:
• 直方圖是將所收集的測定值或數據之全距分為幾個相等的區間 作為橫軸,並將各區間內之測定值所出現次數累積而成的面積, 用柱子排起來的圖形, 亦稱柱狀圖. 製作步驟: • 1.製作次數分配表: A.由全體數據中找到最大值與最小值.如:200個數據中之 170和124. B.求出全距(最大值與最小值之差).全距=170-124=46 C.決定組數,一般為10組左右,不宜太少或太多. 參照下表進行分組: 數據數 組數
編 號 項目 1 日期 1 2 3 各部位油量是否正常 4 5 6 7 8 9 10 11 121314 15
2
3 4 5 6 7 8 9 10
點檢
操作按鈕功能確認
氣缸及操作手柄是否正常 電機,傳動鏈條聲音是否正常 自動上料系統是否正常 光電感應系統是否正常 自動送料是否到位 手動送料是否正常 放鬆手柄功能確認 各部位之清潔(含內輥輪) OK 劃“O” 點檢人
ABC法應用:
• A.時間管理. • B.倉務管理. • C.其他.
柏拉圖實例:
9 89% 8 7 67% 6 5 50% 4 33% 3 2 1 0 £ ¨ ¤ } ¦ ¸ ¼ Æ Ö ² p ¤ £ ¨ } ² v 3 3 2 1 20% 10% Ø ¤ ¤ o NG 3 33% ò Ã ¤ ä /¤ ò ¨ ë 3 67% Ü § Å Î 2 89% ] ¸ ¥ Ë ¤ £ ¦ X ® æ 1 100% 0% 40% 30% 100% 100% 90% 80% 70% 60%
幾種常用的圖表
100 80 60 40 20 0 第一季 第二季 第三季 第四季 東部 中部 北部
第一季 第二季 第三季 第四季
環境 安全
品質 40 20 0
成本 效率
改善前
改善後
前言:PDCA循環
設立目標(P)
ACTION
PLAN DO CHECK
制定達成目 標的計劃(P)
實施溝通與 教育訓練(D)
80~100 100~250 250以上 6~10 7~12 10~20
附表:
132 162 166 137 145153 148 127 155 136144 157 150 136 126132 127 147144 151
137 150 133 162 147150 157 145 156 152150 167 152142 147142 137148 143 152
品管七大手法所體現的精神
1.用事實與數據說話. 2.全面預防. 3.全因素、全過程的控制. 4.依據PDCA循環突破現狀予以改善. 5.層層分解、重點管理.
一.查檢表:
為了解情況、收集數據, 使用簡單記錄填記並予統計整理, 以作進一步分析或作為核對,檢查之用而設計的一種表格或 圖表. 作法: • 1.明確目的. • 2.決定查檢項目. • 3.決定檢查方式(抽檢、全檢). • 4.決定查驗基準、數量、時間、對象等. • 5.設計表格實施查驗. • 6.記錄下查檢資料.
…
… … … … … …
…
… … … … … …
…
…. … … … … …
…
… … … … … …
…
… … … … … …
…
… … … … … …
…
… … … … … …
…
… … … … … …
…
… … …. … … …
…
… … … … 170 …
…
… … … … … …
…
… … … … … …
…
… … … … … … 最大值 最小值
• 1.追求原因型:
工程人員未切實驗證 定位方式不合理 多次折彎累積偏差 折彎間隙變化影響大 模修人員維修方式不當 品管人員未作CSI驗證