车削用量选择表大全
切削用量及选择
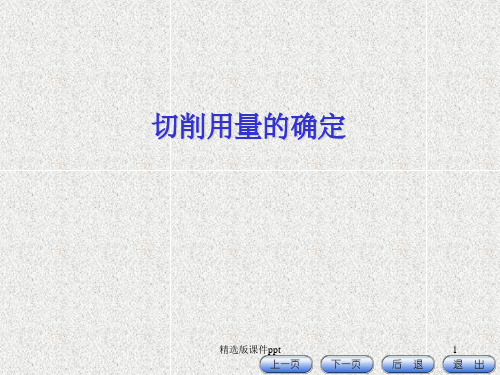
精选版课件ppt
14
3、切削用量对刀具耐用度的影响
(3) 进给量f与刀具耐用度的关系
当增大进给量后,切屑厚度增大,由切屑带着走的热量增 多,同时切屑与前刀面的接触长度增加,散热面积增大。 通过测试得知,切削温度随进给量的增加而升高,但温度 的升高幅度不及切削速度显著。
(4 )背吃刀量ap与刀具耐用度的关系
下课件ppt
33
4.分段切削背吃刀量
如果牙型较深,螺距较大,可分几次进给。每次进给 背吃刀量用螺纹深度减精加工背吃刀量所得的差按递减规 律分配。
螺纹分段切削示意图
常用螺纹切削进给次数与背吃刀量可参考表3-7~表3-9
精选版课件ppt
34
总结
1. 切削用量确定的步骤
背吃刀量的选择 →进给量的选择→切削速度的确定→校验 2. 提高切削用量的途径
13
3、 切削用量对刀具耐用度的影响 (1)刀具耐用度 所谓刀具耐用度,是指一把新刀从开始切削直到磨损量 达到磨损标准为止,在这期间所使用的总的切削时间, 用T表示。
(2) 切削速度vc与刀具耐用度的关系
切削速度是影响刀具耐用度的主要因素,其原因是当提高 切削速度时,单位时间的金属去除率会成正比例增加,刀 具与工件间的摩擦加剧,消耗于金属变形和摩擦的无用功 增加,因而产生过多的热量。因此,提高切削速度的结果 是:摩擦热大量的积聚在切屑底层而来不及传导出去,从 而使切削温度急剧升高,使刀具的耐用度大大降低。
精选版课件ppt
16
切削用量的选择:基本原则
选择切削用量的基本原则是首先选取尽可能大的背吃刀量; 其次要在机床动力和刚度允许的范围内,同时又满足已加 工表面粗糙度的要求的情况下,选取尽可能大的进给量, 最后利用《切削用量手册》选取或用公式计算确定最佳切 削速度。
硬质合金刀具的常用切削用量及注意事项?

硬质合金刀具的常用切削用量及注意事项?
在工厂的实际生产过程中,切削用量一般根据经验并通过查表的方式进行选取,常用硬质合金或涂层硬质合金切削不同材料时的切削用量见下表:
这是常用的切削用量推荐表,W18Cr4V为高速钢
这些参数的选择不仅要看推荐值,更要根据实际加工状况来选择,
需要注意一下几点:
1、主轴转速
可以根据零件上被加工处的直径,并结合零件和刀具的材料特性及切削加工性等条件所限定的切削速度来定。
切削速度除了计算(Vc=πDn/1000)和査切削手册选取外,还可根据实践经验确定,需要注意的是交流变频调速数控车床低速输出力矩小,因而切削速度不能太低。
应根据切削速度可以计算出主轴转速(n=1000Vc/πD)。
2、车螺纹时的主轴转速
在车削螺纹时,主轴转速将受到螺纹的螺距P(或导程)大小、驱动电机的升降频特性,以及螺纹插补运算速度等多种因素影响,故对于不同的数控系统,推荐不同的主轴转速选择范围。
根据以上几点,我们不能完全根据切削手册上的推荐值进行加工,还需要综合分析,避免因为切削参数选择不当造成零件报废。
加工中心切削用量选用表

加工中心切削用量选用
表
The manuscript was revised on the evening of 2021
加工中心切削用量参照表
表1 8-20高速钢立铣刀粗铣切削用量参考值
表2 硬质合金面铣刀加工平面时的切削用量
表3 涂层硬质合金铣刀的切削用量
注:铣削端面时切削深度为轴向切削深度,铣削侧面时切削深度为径向切削深度。
表4 高速钢钻头钻孔时的进给量
加工中心切削用量参照表
表1 8-20高速钢立铣刀粗铣切削用量参考值
表2 硬质合金面铣刀加工平面时的切削用量
表3 涂层硬质合金铣刀的切削用量
注:铣削端面时切削深度为轴向切削深度,铣削侧面时切削深度为径向切削深度。
表4 高速钢钻头钻孔时的进给量。
数控机床加工的切削用量

单元4数控机床加工的切削用量教学目的1、了解数控机床的运动(主运动、进给运动);2、了解数控机床加工刀具的角度及其作用;3、了解数控机床加工中有关切削层的参数及其作用;4、了解数控机床加工中的切削用量及其选用原则。
5、掌握常用不同材料零件在粗加工、半精加工和精加工时的切削用量选用;教学重点1、数控机床加工刀具的角度及其作用;2、数控加工中粗加工、半精加工和精加工时的切削用量选择;教学难点1、刀具的角度及其作用;2、切削用量选用教学方法讲练结合教学内容一、车削加工与刀具1. 车削加工原理在普通车床和一般数控车床上,可以进行工件的外表面、端面、内表面以及内外螺纹的加工。
对于车削中心,除上述各种加工外,还可进行铳削、钻削等加工。
从上述介绍可以看出:在切削过程中,刀具和工件之间必须具有相对运动,这种相对运动称为切削运动。
根据切削运动在切削过程中的作用不同可以分为主运动、和进给运动。
各种机床的主运动和进给运动参见下表。
主运动是指机床提供的主要运动。
主运动使刀具和工件之间产生相对运动,从而使刀具的前刀面接近工件并对工件进行切削。
在车床上,主运动是机床上主轴的回转运动,即车削加工时工件的旋转运动。
2)进给运动进给运动是指由机床提供的使刀具与工件之间产生的附加相对运动。
进给运动与主运动相配合,可以形成完整的切削加工。
在普通车床上,进给运动是机床刀架(溜板)的直线移动。
它可以是纵向的移动(与机床主轴轴线平行),也可以是横向的移功(与机床主轴轴线垂直),但只能是一亇方向的移动。
在数控车床上,数控车床可以同时实现两亇方向的进给,从而加工出各种具有复杂母线的回转体工件。
在数控车床中,主运动和进给运动是由不同的电机来驱动的,分别称为主轴电机和坐标轴伺服电机。
它们由机床的控制系统进行控制,自动完成切削加工。
2. 切削用量切削用量是指机床在切削加工时的状态参数。
不同类型的机床对切削用量参数的表述也略有不同,但其基本的含义都是一致的,如下图所示。
车削加工参数

车削加工参数1切削用量选定原则选择机械加工切削用量就是指具体确定切削工序的切削深度、进给量、切削速度及刀具耐用度。
选择切削用量时,要综合考虑生产率、加工质量和加工成本。
从切削加工生产率考虑:切削深度、进给量、切削速度中任何一个参数增加一倍,都可提高生产率一倍。
从刀具耐用度考虑:应首先采用最大的切削深度,再选用大的进给量,然后根据确定的刀具耐用度选择切削速度。
从加工质量考虑:精加工时,采用较小的切削深度和进给量,采用较高的切削速度。
2车削加工参数2.1车削要素切削速度v:工件旋转的线速度,单位为m/min。
进给量f:工件每旋转一周,工件与刀具相对位移量,单位为mm/r。
切削深度ap:垂直于进给运动方向测量的切削层横截面尺寸,单位为mm。
Ra :以轮廓算术平均偏差评定的表面粗糙度参数,单位为^m。
dw :工件直径,单位为mm。
切削速度与转速关系:jsin nd1000 318_3 m/minlOOOv 3183vH - -- -= ---就』r/minv:切削速度,工件旋转的线速度,单位为m/min。
n:工件的转速,单位为r/min。
d:工件观察点直径,单位为mm。
2.2车削参数45钢热轧状态(硬度:187HB)外圆车削钢调质状态(硬度:28〜32HRC)外圆车削4540Cr钢热轧状态(硬度:212HB)外圆车削28〜32HRC)外圆车削40Cr钢调质状态(硬度:28〜32HRC)内圆车削TC4固溶处理并时效状态(硬度:320〜380HB)外圆车削TC4固溶处理并时效状态(硬度:320〜380HB)内圆车削。
车床的切削用量及单位

车床的切削用量是指在车削加工过程中,每个刀具每转进给量所切削的材料量。
它通常用于控制加工质量和切削效率,是车床加工中非常重要的参数之一。
车床的切削用量通常用以下单位表示:
1. 切削深度(Cutting Depth):单位为毫米(mm)。
切削深度指的是刀具在一次进给中所切削的材料厚度。
2. 进给量(Feed Rate):单位为毫米/转(mm/r)。
进给量指的是刀具每转进给的距离。
3. 切削速度(Cutting Speed):单位为米/分钟(m/min)。
切削速度指的是刀具在单位时间内切削的材料长度。
在实际加工中,切削用量的选择需要根据工件材料、加工要求、刀具类型和车床性能等因素进行综合考虑。
通常情况下,切削用量越大,加工效率越高,但加工质量和刀具寿命也会受到影响;反之,切削用量越小,加工质量和刀具寿命会得到保证,但加工效率会降低。
因此,在实际加工中需要根据具体情况进行选择。
机械加工切削全参数推荐表

常用材料机械加工切削参数推荐表共 26 页2015年9月目录1 切削用量选定原则 (3)2 车削加工切削参数推荐表 (3)2.1 车削要素 (3)2.2 车削参数 (3)3 铣削加工切削参数推荐表 (11)3。
1 铣削要素 (11)3.2 铣削参数 (11)4 磨削加工切削参数推荐表 (20)4.1 磨削要素 (20)4。
2 平面磨削 (20)4。
3 外圆磨削 (21)4。
4 内圆磨削 (22)1 切削用量选定原则选择机械加工切削用量就是指具体确定切削工序的切削深度、进给量、切削速度及刀具耐用度。
选择切削用量时,要综合考虑生产率、加工质量和加工成本.从切削加工生产率考虑:切削深度、进给量、切削速度中任何一个参数增加一倍,都可提高生产率一倍。
从刀具耐用度考虑:应首先采用最大的切削深度,再选用大的进给量,然后根据确定的刀具耐用度选择切削速度。
从加工质量考虑:精加工时,采用较小的切削深度和进给量,采用较高的切削速度。
2 车削加工切削参数推荐表2。
1 车削要素切削速度v:工件旋转的线速度,单位为m/min。
进给量f:工件每旋转一周,工件与刀具相对位移量,单位为mm/r。
切削深度a p:垂直于进给运动方向测量的切削层横截面尺寸,单位为mm。
Ra :以轮廓算术平均偏差评定的表面粗糙度参数,单位为μm.d w :工件直径,单位为mm.切削速度与转速关系:m/minr/minv:切削速度,工件旋转的线速度,单位为m/min。
n:工件的转速,单位为r/min。
d:工件观察点直径,单位为mm。
2.2 车削参数45钢热轧状态(硬度:187HB)外圆车削45钢热轧状态(硬度:187HB)内圆车削45钢调质状态(硬度:28~32HRC)外圆车削45钢调质状态(硬度:28~32HRC)内圆车削40Cr钢热轧状态(硬度:212HB)外圆车削40Cr钢热轧状态(硬度:212HB)内圆车削40Cr钢调质状态(硬度:28~32HRC)外圆车削40Cr钢调质状态(硬度:28~32HRC)内圆车削H62硬化状态(硬度:164HB)外圆车削H62硬化状态(硬度:164HB)内圆车削2A12—T4固溶处理并时效状态(硬度:105HB)外圆车削2A12-T4固溶处理并时效状态(硬度:105HB)内圆车削TC4固溶处理并时效状态(硬度:320~380HB)外圆车削TC4固溶处理并时效状态(硬度:320~380HB)内圆车削3 铣削加工切削参数推荐表3。
数控车削中切削用量的选择
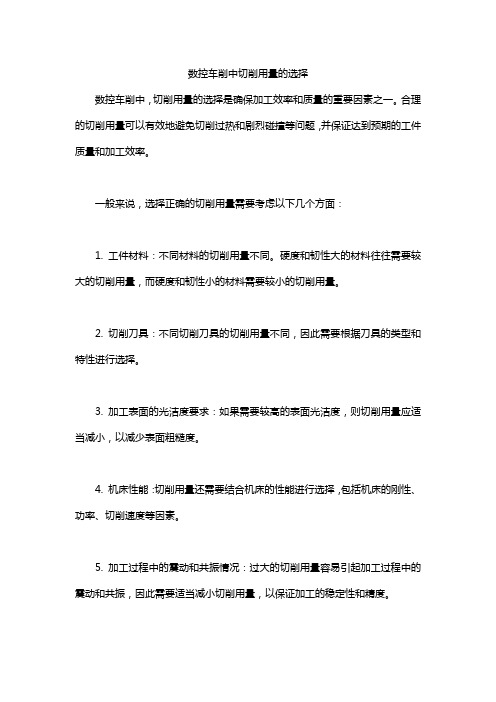
数控车削中切削用量的选择
数控车削中,切削用量的选择是确保加工效率和质量的重要因素之一。
合理的切削用量可以有效地避免切削过热和剧烈碰撞等问题,并保证达到预期的工件质量和加工效率。
一般来说,选择正确的切削用量需要考虑以下几个方面:
1. 工件材料:不同材料的切削用量不同。
硬度和韧性大的材料往往需要较大的切削用量,而硬度和韧性小的材料需要较小的切削用量。
2. 切削刀具:不同切削刀具的切削用量不同,因此需要根据刀具的类型和特性进行选择。
3. 加工表面的光洁度要求:如果需要较高的表面光洁度,则切削用量应适当减小,以减少表面粗糙度。
4. 机床性能:切削用量还需要结合机床的性能进行选择,包括机床的刚性、功率、切削速度等因素。
5. 加工过程中的震动和共振情况:过大的切削用量容易引起加工过程中的震动和共振,因此需要适当减小切削用量,以保证加工的稳定性和精度。
选择合适的切削用量可以帮助实现加工效率和质量的平衡,提高数控车削加工的效率和质量。
- 1、下载文档前请自行甄别文档内容的完整性,平台不提供额外的编辑、内容补充、找答案等附加服务。
- 2、"仅部分预览"的文档,不可在线预览部分如存在完整性等问题,可反馈申请退款(可完整预览的文档不适用该条件!)。
- 3、如文档侵犯您的权益,请联系客服反馈,我们会尽快为您处理(人工客服工作时间:9:00-18:30)。
550-610
130-150 105-120
82-95 135-145 105-115
82-90 115-135 90-105
69-84 85-125 69-100 53-76 67-120 58-105 46-84 95-175 75-135 58-105 100-165 81-125 66-100 135-185 105-135 85-115
0.8~1 0.6~0.9
40
0.4~0.5
—
—
—
16×25
60
0.6~0.8 0.5~0.8 0.4~0.6
—
100
0.8~1.2 0.7~1 0.6~0.8 0.5~0.7
铸铁及铜合 金 20×30
400
1~1.4
1~1.2
0.8~1 0.6~0.8
40
0.4~0.5
—
—
—
60
0.6~0.9 0.5~0.8 0.4~0.7
车床切削速度计算表
加工材质
材质分类 钢的强度或 刀具材质
(钢或铁) 铸铁的硬度
1
1
1
工件最大 外圆直径
(mm)
刀具耐用度 T(min) kMv
150
60
0.65
CV 291
ksv 1
KV
Tm
α
xv p
fyv
0.65
2.27
198 38 21
20.3 110
31 53.3
0.25 0.25
0.3 0.15
0.2 0.2 0.18
0.33
0.66 0.15
0.3 0.8 0.66 0.5 0.45
0.55 0.4
0.125
0.125 0.18
0.18 0.2
0.25 0.3
0.15
0.15 0.1
189.8
158 24
22.7 208
245-305
0.18 0.4 0.5 0.18 0.4 0.5 0.18 0.4 0.5 0.13-0.18 0.25-0.4 0.4-0.5 0.18 0.4 0.5 0.18 0.4 0.5 0.18 0.4 0.5 0.18 0.4 0.5
0.18
105-115 85-90 67-73
105-115 84-90 66-72 90-105 69-84 53-66 76-105 60-84 46-64 58-105 49-100 38-76 87-140 69-15 55-90 84-135 69-110 60-90
0.6
1.4
0.6
1.5
0.7
1.7
0.7
>360~500 1.4
0.7
1.5
0.7
1.5
0.8
1.7
0.8
1、粗加工,表面粗糙度为Ra50~12.5时,一次走刀应尽可能切除全部余量。 2、粗车背吃刀量的最大值是受车床功率的大小决定的。中等功率机床可以达到8~10mm。
高速钢及硬质合金车刀车削外圆及端面的粗车进给量
4
8
1
175~225
4
8
1
125~225
4
8
55-90 41-70 34-55
52 40 30 43-46 34-33 27-30 34-40 23-30 20-26 30-37 24-27 18--21 41-46 32-37 24-27
0.18-0.2 0.4 0.5 0.2 0.4 0.5 0.18 0.4 0.5 0.18 0.4 0.5 0.18 0.4 0.5 0.18 0.4 0.5
YT15 f≤0.3
σ b= 1.65GPa
灰铸铁 190HB
(不用切削 液)
外圆纵车
YT15 f≤0.4
(Kr>0°)
(不用切削 f>0.4 液)
高速钢 f≤0.25
外圆纵车
(不用切削 f>0.25 液) YG6 f≥α p
可锻铸铁
(Kr=0°) (用切削液) f>α p
切断及切槽 YG6(不用液)
4
9--21
0.25
32-56
41-66
8
8--18
0.4
24-43
26-49
高温合金
0.8 200~475
2.5
3.6-14 3--11
0.13 0.18
12-49 9-41
14-58 12-49
外圆车削时切削速度公式中的系数和指数选择表
加工材料 加工形式 刀具材料 进给量
公式中的系数和指数
0.18 0.4-0.5 0.5-0.75
0.1
0.11~0.15 0.15~0.22
2.5~1.25
50~100 0.11~0.16 0.16~0.25 0.25~0.35 >100 0.16~0.2 0.2~0.25 0.25~0.35
铸铁及铜合 金
10~5 5~2.5 2.5~1.25
不限
0.25~0.4 0.4~0.5 0.15~0.25 0.25~0.4 0.1~0.15 0.15~0.25
>12
— — — — — — — — — 0.4~0.6 — — — — — — — 0.7~0.9
4、加工淬硬钢时,进给量应减小。硬度为HRC45-56时,乘以修正系数:0.8, 硬度为HRC57-62,乘以修正系 数:k=0.5。
按表面粗糙度选择进给量的参考值
工件材料
粗糙度等级 切削速度 (Ra) (m/min)
工件材料
车刀刀杆尺 工件 直径寸(mm)(mm) Nhomakorabea≤3
切 3~5
5~8
深 8~12
进给量f mm/r
20
0.3~0.4
—
—
—
40
0.4~0.5 0.3~0.4
—
—
16×25
60
0.5~0.7 0.4~0.6 0.3~0.5
—
100
碳素结构钢
400
、合金结构 钢、耐热钢
20
40
20×30
60
25×25
100
刀尖圆弧半径
0.5
1
2
进给量f mm/r
10~5
≤50 >50
0.3~0.5 0.45~0.6 0.55~0.7 0.4~0.55 0.55~0.65 0.65~0.7
碳钢及合金 碳钢
5~2.5
≤50 >50 ≤50
0.18~0.25 0.25~0.3 0.3~0.4
0.25~0.3 0.3~0.35 0.35~0.5
5、用高速钢车刀加工热处理钢件时,车削速度应减少:正火,乘以系数0.95;
退火,乘以系数0.9;调质,乘以系数0.8。
6、加工钢和铸铁的机械性能改变时,车削速度的修正系数kMv可按表《钢和铸铁的强度和硬度改变时 车削速度的修正系数kM》计算。
7、其他加工条件改变时,车削速度的修正系数见表《车削条件改变时的修正系数》。
88-100
105-120
0.75
115-130 150-160
0.18
90-100
115-125
0.5
70-78
90-100
0.75
115-130 140-155
0.18
88-95
105-120
0.5
69-76
84-95
0.75
135-150 170-185
0.18
105-120 135-145
0.5
—
25×25
100 0.9~1.3 400 1.2~1.8
0.8~1.2 1.2~1.6
1、断续切削、有冲击载荷时,乘以修正系数:k=0.75~0.85 。
0.7~1 1~1.3
0.5~0.8 0.9~1.1
2、加工耐热钢及其合金时,进给量应不大于1mm/r。
3、无外皮时,表内进给量应乘以系数:k=1.1。
外圆车削背吃刀量选择表(端面切深减半)
轴径
≤10 >10~18
≤100
半精
精车
0.8
0.2
0.9
0.2
>100~250
半精
精车
0.9
0.2
0.9
0.3
长
>250~500
半精
精车
1
0.3
1
0.3
>18~30
1
0.3
1
0.3
1.1
0.3
>30~50
1.1
0.3
1
0.3
1.1
0.4
>50~80
1.1
0.3
0.2
0.2 0.1
0.1 0.28
0.28 0.2
0.15 0.2
0.2 0.125
0.125 0.2
0.25 0.28 0.28
0.2
外圆纵车 YG8(不用液)
200~240HB
f>0.4
648
0.2
铝硅合金及 外圆纵车 YG8(不用液) f≤0.4
铸铝合金
f>0.4
388
0.12
262
0.12
注:1、内表面加工(镗孔、孔内切槽 、内表面成形车削)时,用外圆加工的车削
0.4 0.25
0.5
0.2 0.28 0.28
速度乘以系数0.9。
2、用高速钢车刀加工结构钢、不锈钢及铸钢,不用切削液时,车削速度乘以
系数0.8。
3、用YT车刀对钢件切断及切槽使用切削液时,车削速度乘以系数1.4。
4、成形车削深轮廓及复杂轮廓工件时,切削速度乘以系数0.85。