【精益生产英文】高效看板系统的5大准则
精益管理五大原则

精益管理五大原则全文共四篇示例,供您参考第一篇示例:精益管理(Lean Management)作为一种高效的管理理念,旨在通过减少浪费、提高效率和质量,实现组织的持续改进。
精益管理的五大原则是其核心理念之一,它们为组织提供了指导方针,帮助其实现更高水平的生产和运营效率。
本文将从各个角度对精益管理的五大原则进行详细介绍,帮助读者深入了解这一管理理念。
第一大原则是价值的识别(Value Identification)。
从顾客的角度出发,理解顾客对产品或服务的真正需求,是企业精益管理的出发点。
意味着企业需要聚焦于生产出顾客愿意购买且愿意支付的产品,而不是盲目地追求规模和产量。
这一原则的核心是通过深入洞察顾客需求、消除无价值的活动,实现价值的最大化。
在实践中,企业需要通过对市场的调研和顾客的反馈,不断优化产品和服务的设计,以确保其能够真正满足市场需求。
第二大原则是价值流的映射(Value Stream Mapping)。
价值流是指将一系列的活动和过程连接起来,产生出顾客信任和愿意支付的产品或服务的全过程。
价值流映射的目的是识别出整个价值流程中的浪费和瓶颈,以便能够全面地优化生产过程。
通过价值流映射,企业能够清晰地了解整个价值流程,识别出影响生产效率和质量的问题,为后续的改进工作提供方向。
第三大原则是流程的拉动(Pull System)。
流程的拉动是指根据实际需求进行生产,而不是依据预测的需求进行批量生产。
这一原则的核心是避免过度生产和库存的积累,通过拉动式生产,使生产与需求之间形成有效的匹配。
通过采用拉动式生产模式,企业能够减少库存积压带来的浪费和成本,保持生产过程的灵活性和高效率。
第四大原则是追求卓越(Pursuit of Perfection)。
追求卓越是精益管理的长期目标和使命。
企业需要不断追求卓越,改善工作流程,提高产品质量,降低成本和交付时间,让企业在竞争中保持优势地位。
这一原则的核心是以不断改进和创新为动力,推动组织朝着更高水平的效率和质量发展。
精益生产的五大原则是什么
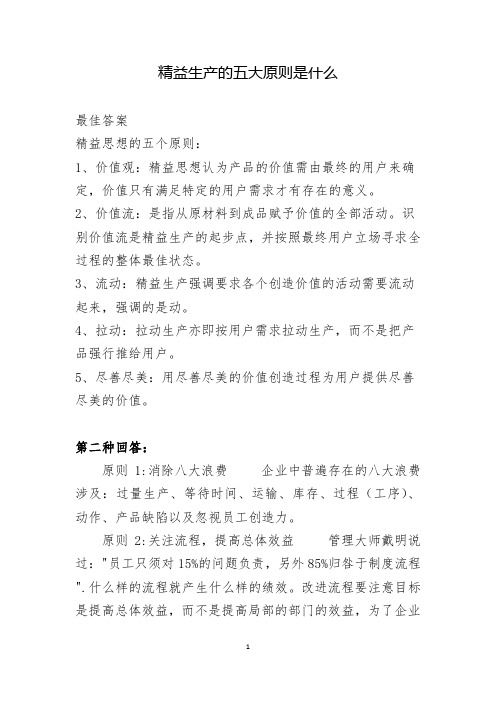
精益生产的五大原则是什么最佳答案精益思想的五个原则:1、价值观:精益思想认为产品的价值需由最终的用户来确定,价值只有满足特定的用户需求才有存在的意义。
2、价值流:是指从原材料到成品赋予价值的全部活动。
识别价值流是精益生产的起步点,并按照最终用户立场寻求全过程的整体最佳状态。
3、流动:精益生产强调要求各个创造价值的活动需要流动起来,强调的是动。
4、拉动:拉动生产亦即按用户需求拉动生产,而不是把产品强行推给用户。
5、尽善尽美:用尽善尽美的价值创造过程为用户提供尽善尽美的价值。
第二种回答:原则1:消除八大浪费企业中普遍存在的八大浪费涉及:过量生产、等待时间、运输、库存、过程(工序)、动作、产品缺陷以及忽视员工创造力。
原则2:关注流程,提高总体效益管理大师戴明说过:"员工只须对15%的问题负责,另外85%归咎于制度流程".什么样的流程就产生什么样的绩效。
改进流程要注意目标是提高总体效益,而不是提高局部的部门的效益,为了企业的总体效益即使牺牲局部的部门的效益也在所不惜。
原则3:建立无间断流程以快速应变建立无间断流程,将流程中不增值的无效时间尽可能压缩以缩短整个流程的时间,从而快速应变顾客的需要。
原则4:降低库存需指出的是,降低库存只是精益生产的其中一个手段,目的是为了解决问题和降低成本,而且低库存需要高效的流程、稳定可靠的品质来保证。
很多企业在实施精益生产时,以为精益生产就是零库存,不先去改造流程、提高品质,就一味要求下面降低库存,结果可想而知,成本不但没降低反而急剧上升,于是就得出结论,精益生产不适合我的行业、我的企业。
这种误解是需要极力避免的。
原则5:全过程的高质量,一次做对质量是制造出来的,而不是检验出来的。
检验只是一种事后补救,不但成本高而且无法保证不出差错。
因此,应将品质内建于设计、流程和制造当中去,建立一个不会出错的品质保证系统,一次做对。
精益生产要求做到低库存、无间断流程,试想如果哪个环节出了问题,后面的将全部停止,所以精益生产必须以全过程的高质量为基础,否则,精益生产只能是一句空话。
精益生产的五大基本原则

精益生产的五大基本原则精益生产是一种以减少不必要的浪费、提高效率和质量为目标的生产管理方法。
它起源于日本的丰田汽车公司,后来被广泛应用于制造业和服务业。
精益生产有五大基本原则,包括价值定义、价值流、流程流、拉动和持续改进。
1. 价值定义(Value Definition)精益生产的第一个基本原则是明确价值,即了解客户对产品或服务的需求和期望。
只有明确了价值,企业才能确保它们所生产的产品或提供的服务是有意义的。
价值定义需要从客户的角度出发,深入了解他们的需求,并确保所有生产活动都与创造价值的目标一致。
2. 价值流(Value Stream)价值流是指产品或服务从原材料到最终交付给客户的所有流程。
它包括所有加工、运输和等待时间。
精益生产的第二个原则是通过细致的价值流分析来识别并消除不必要的浪费。
通过这样的分析,企业可以找到造成浪费的瓶颈和问题,并提供解决方案以简化生产流程,提高效率。
3. 流程流(Flow)流程流是指产品或服务在生产过程中的流动,从而实现连续和连贯的生产。
精益生产的第三个原则是通过优化流程来提高效率。
这可以通过减少环节、降低库存和加强协作来实现。
完善的流程流可以减少等待时间和排队时间,加速生产,从而提高整体效率。
4. 拉动(Pull)拉动是指根据客户需求来进行生产和供应的原则。
精益生产的第四个原则是把生产过程变成可以反应客户需求的拉动系统,而不是以推动和预测为基础的推动系统。
拉动系统通过减少库存和等待时间来提高效率,并减少需求与供应之间的误差。
5. 持续改进(Continuous Improvement)持续改进是精益生产的第五个基本原则,也是整个精益生产理念的核心。
它强调不断寻找改进的机会和方法,并将改进作为持续性的活动。
持续改进可以通过以下方式实现:收集和分析数据,识别问题和机遇,提出解决方案并执行,最后评估成果并回馈到下一轮改进循环中。
总结而言,精益生产的五大基本原则包括价值定义、价值流、流程流、拉动和持续改进。
精益生产五大原则

精益生产五大原则精益生产(Lean Production)是一种以提高生产效率和质量为目标的生产管理方法,由日本丰田汽车公司创始人之一,著名企业家丰田太郎提出。
它以节约资源、降低浪费、提高员工参与度和持续改善为核心原则。
精益生产有五大原则,分别是价值流思维、流程的流动、拉动生产、零库存和持续改善。
第一,价值流思维(Value Stream Thinking)。
价值流是指顾客购买产品时愿意为之付费的所有活动的集合。
价值流思维的目标是通过分析生产过程中各个环节的价值流,消除不必要的环节和浪费,最大限度地提升价值创造的效率。
价值流思维强调整个价值链的优化,关注价值的流动而非单个环节的效率。
通过全面理解价值流程,找出不增值的环节并削减,将生产过程中的各个环节无缝连接起来,使价值在生产过程中能够顺畅地流动。
第二,流程的流动(Flow)。
流程的流动强调的是产品在生产过程中的流动,要求消除所有阻碍产品流动的因素。
流动原则要求缩短产品从原材料到最终成品的生产周期,减少产品的停滞和等待时间,从而提高生产效率。
流程的流动中还强调对生产过程中的瓶颈环节进行监控和管理,确保每个环节都能够顺畅流动,以保证整个生产过程的连续性。
第三,拉动生产(Pull Production)。
拉动生产原则是指在生产过程中,根据顾客需求,通过减少库存和根据实际需求实时生产,实现生产活动的“拉动”。
相较于推动式生产,拉动式生产更加灵活,能够根据市场需求来调整生产计划,减少库存积压,降低库存成本。
拉动式生产也能够有效避免过量生产和“刷单”等现象,提高资源利用效率。
第四,零库存(Zero Inventory)。
零库存是指在供应链中减少或消除库存的原则。
零库存原则的目标是通过减少库存数量和减少库存滞留时间,减少资金占用和库存积压的问题。
零库存原则在精益生产中十分重要,它通过拉动式生产、批量生产、精确计划等手段,保持库存的最低水平,以减少非价值增加的资金、时间和空间的浪费。
精益生产之看板管理的使用规则

精益生产之看板管理的使用规则看板是JIT生产方式中独具特色的管理工具,看板的操作必须严格符合规范,否则就会陷入形式主义的泥潭,起不到应有的效果。
为了使看板充分发挥其功能和作用,必须制订必要的措施、并且能严格遵守,这是运用看板管理的前提条件,具体来说,看板使用的规则有:一、后工序向前工序取货为了改变以往那种前工序向后工序送货的传统做法,实施看板管理,必须由后工序在必要的时候到前工序领取必要数量的零部件,以防止产需脱节而生产不必要的产品。
为确保这条规则的实行,后工序还必须遵守下面三条具体规定:第一,禁止不带看板领取零部件;第二,禁止领取超过看板规定数量的零部件;第三,实物必须附有看板。
二、不良品不交给下道工序这就是说,上工序必须为下工序生产百分之百的合格品。
如果发现生产了不良品,必须立即停止生产,查明原因,采取措施,防止再次发生,以保证产品质量,防止生产中的不必要浪费。
三、前工序只生产后工序所领取数量的产品各工序只能按照后工序的要求进行生产,而不生产超过看板所规定数量的产品,以控制过量生产和合理库存、彻底排除无效劳动。
四、进行均衡化生产均衡生产是看板管理的基础。
实施看板管理,只对总装配线下达生产数量指令,因而其担负生产均衡化的责任,为了准确地协调生产,及时满足市场多变的需求,最好利用电子计算机分析各种因素,制订确切的均衡化生产计划。
五、必须使生产工序合理化和设备稳定化为了保证对后工序供应百分之百的合格品,必须实行作业标准化、合理化和设备稳定化,消除无效劳动,提高劳动生产率。
六、必须根据看板进行微调由于各工序的生产能力和产品合格率高低不同,必须在允许范围内进行微调,即适当地进行增减的调整,并且尽量不给前工序造成很大的波动而影响沟衡生产。
看板是JIT生产方式中独具特色的管理工具,看板的操作必须严格符合规范,否则就会陷入形式主义的泥潭,起不到应有的效果。
为了使看板充分发挥其功能和作用,必须制订必要的措施、并且能严格遵守,这是运用看板管理的前提条件,具体来说,看板使用的规则有:1.后工序向前工序取货为了改变以往那种前工序向后工序送货的传统做法,实施看板管理,必须由后工序在必要的时候到前工序领取必要数量的零部件,以防止产需脱节而生产不必要的产品。
精益生产的五大原则与七大浪费

精益生产的五大原则与七大浪费精益生产是一种管理技术和方法,旨在通过最小化浪费,提高效率和质量,实现持续改进。
它包括五大原则和七大浪费,下面将分别介绍。
精益生产的五大原则是:1. 建立价值:了解客户需求,仅生产客户需要的产品和服务,而不是无用的产品。
2. 建立价值流:分析价值流程,消除不必要的步骤和操作,确保产品或服务流程的顺畅和高效。
3. 实现流程流畅:通过减少排队、延迟和等待时间来优化生产过程,确保产品在最短的时间内完成。
4. 追求完美:不断追求高质量和卓越,通过标准化工作和持续改进来达到完美。
5. 尊重员工:尊重和信任员工,让员工参与决策和持续改进过程,以提高积极性和工作满意度。
精益生产还强调七大浪费的避免,这些浪费包括:1. 运输浪费:指的是产品或材料的不必要移动,如多次搬动或长距离搬运。
2. 库存浪费:指的是过多的库存,包括原材料、半成品或成品,浪费了存储空间和资金。
3. 过程浪费:指的是不必要的步骤、操作或暂停,导致生产过程低效。
4. 等待浪费:指的是工人、设备或信息的等待时间,导致生产延迟和资源浪费。
5. 过度加工浪费:指的是超出客户需求的过度处理和加工,浪费了时间和资源。
6. 缺陷浪费:指的是产品或服务的缺陷造成的修复、返工或废弃,浪费了资源和人力。
7. 运动浪费:指的是工人的不必要移动、伸展或追踪物品,增加了工作的困难和耗时。
通过遵循精益生产的五大原则和避免七大浪费,企业可以提高效率、降低成本、提供更高质量的产品和服务,并不断改进和创新。
这将使企业在竞争激烈的市场中保持竞争优势,并满足客户的需求和期望。
精益生产是一种全面优化企业运作流程的管理方法。
它的目标是通过最大限度减少浪费,提高效率和质量,从而为企业创造更大的价值。
精益生产的核心理念之一是追求卓越,通过不断的改进和创新来满足客户需求。
以下将详细介绍精益生产的五大原则以及七大浪费。
1. 建立价值这一原则强调企业应了解客户的需求并满足其期望。
精益看板生产管理方式有几项规则
精益看板生产管理方式有几项规则看板管理方式经丰田公司在制造现场的反复实践,有其运行的前提条件,也就是所谓的看板规则。
第一规则:不合格品绝对不流到下一道工序(100%合格品)若制造了不良品,由于投入了大量的材料、设备、劳动力因而给公司造成极大的浪费。
因此,如果发现不良品,则不可再次制造相同的不良,应该立即制定再发防止的对策。
为了要彻底地消除不良品,“不让不良品流到后工序”的第一规则是非常重要的一件事。
其理由是,遵守了第一个原则,那么:①制造不良的工序,可立即被发现有不良的产生;②若相反,后工序仍不停线,或是不良品积压在本工序内,而导致不良品增多,成本上升,因此管理者不得不一致实施再发防止对策。
第二规则:后道工序取用(需要的东西、需要时、需要量来进行取用)在必要的时候,由后工序来取用必要的量。
按以往的方式,在不必要的时间,制造超出需求的量,由前工序供给后工序会造成不必要的浪费,让作业者做出多余的加班,使多余的在库品在一旁闲置,设备也增加过多的负荷。
这样,也无法清楚地分析设备能力的瓶颈,然而更大的损失是制造了不必要的产品。
为了消除各种浪费,第二规则是非常重要的,为了要确切遵守此项规则,必须要明确正确的做法。
在这里首先要遵守第一规则“不让不良品流到后工序”及时发现在自工序内所制造的不良品。
对于这一点,后工序所需要的时间与数量,以前无法在自工序内掌握。
也就是说,必须及时获得前工序何时需要、何种数量的部件。
因而必须要将这种情报通知给各个工序,此时,所谓生产相应部门便出现了,同时所谓的生产计划,也成了生产信息分发给个相关人员。
各生产线的稼动率或不良率、工作日等生产要素也作为信息传递到生产管理环节。
然而,生产预定与现实往往不一致,由于变更生产计划比较繁琐,法及时对应。
因此在许多生产现场造成无法顺利生产、及时供货等问题。
无用的信息处处泛滥,使制造现场到处摆满闲置的产品。
如果将“供给后工序”的想法加以改变,由后工序向前工序“在必要的时候,取用需要的量”。
精益生产之看板管理三原则
精益生产之看板管理三原则
“何物,何时,生产多少数量,以何方式生产、搬运”。
这就是看板管理所要传达的重要信息。
它首先是丰田JIT生产模式的重要工具,然后发展为精益生产的主要管理方法之一。
看板管理目的是在同一道工序或者前后工序之间进行物流或信息流的传递。
JIT是一种拉动式的管理方式,
主生产计划确定后会向各个生产车间下达生产指令,然后每一个生产车间又向前面的各道工序下达生产指令,最后再向仓库管理部门、采购部门下达相应的指令。
这些生产指令的传递都是通过看板来完成的。
看板的使用原则有三点:
•没有看板指令不生产,也不运送;
•看板的数据反馈表与实物产品在一起才有效;
•前工序按照看板反馈表单的指令进行顺序生产。
随着信息技术的飞速发展,看板方式由实物看板更多被电子看板所取代。
看板管理扩大外延就是目视化管理,一定规模企业已越来越重视利用这些管理工具来提升企业总体管理水平,不知道你坐在的企业是否也加入了应用?
(寒窗曙灭九微火,九微片片飞花琐。
)。
看板管理的五大原则
看板管理的五大原则看板管理就像是一场精心编排的魔术表演,而那五大原则就是魔术师手中的神秘道具。
第一大原则是可视化。
这就好比是把管理这个神秘的黑盒子打开,让一切都暴露在阳光下。
你看,可视化就像是给企业的流程穿上了透视装,所有的工作、流程、进度都赤裸裸地展现在大家面前。
没有什么能够隐藏,就像在一个透明的玻璃房子里,每个人的一举一动都清晰可见。
工作就像一个个调皮的小怪兽,在可视化的“照妖镜”下无处遁形。
第二原则是限制在制品数量。
这就像是给一场疯狂的派对限制人数一样。
如果在制品数量太多,那就像是派对里挤进了无数不请自来的人,乱成一锅粥。
限制它,就像是门口站着一个严厉的保安,只允许合适数量的“宾客”入场,这样工作场地才不会拥挤不堪,一切才能井井有条。
第三是流动性原则。
工作的流动得像山间清澈的溪流一样顺畅。
要是堵住了,那可不得了,就像交通堵塞时马路上一堆乱成一团的汽车。
每个环节都要像接力赛中的运动员,快速而准确地把“接力棒”传递下去,绝不能拖拖拉拉,不然整个工作流程就会像一个气喘吁吁的胖子,怎么也跑不快。
拉动原则也很有趣。
这就像是在拉一头倔驴,不过是聪明地拉。
不是盲目地推动工作,而是让下游的需求像美味的胡萝卜一样,吸引着上游的工作进行。
下游喊一声“我要这个”,上游就像听到指令的小跟班,立刻把东西送过来,而不是自顾自地拼命生产,最后生产出一堆没人要的东西,就像做了一堆没人吃的黑暗料理。
最后是完善性原则。
这是让整个看板管理不断进化的魔法。
就像一个人不断地给自己的形象升级一样,看板管理也要不断地查漏补缺。
发现问题就像发现脸上的痘痘一样,要赶紧解决,让整个管理体系像一个越来越精致的美女或者帅哥,永远保持迷人的魅力。
看板管理的这五大原则就像五个性格各异却又配合默契的小伙伴,它们手拉手,一起把企业的管理从混乱带向有序,从低效带向高效。
它们就像一套神奇的组合拳,每一拳都打在管理的关键点上,让企业能够在激烈的市场竞争这个大舞台上,跳出最精彩的舞蹈。
精益求精--看板管理
精益求精,止于至善!
精益生产(Lean Production)
第三章 看板管理
一、看板概念、类型和功能 二、工序内看板和工序间领取看板 三、信号看板 四、外协领取看板 五、特殊看板
精益生产(Lean Production)
一、看板概念、类型和功能
看板(Kanban)是传递信号控制生产的工具,可以是某 种“板”,也可以是能表示某种信息的任何其他形式。
出口位置号 (POST NO.12)
零部件号:A232-6085C(上盖板) 箱型:3型(绿色) 标准箱内数:12个/箱 看板编号:2 # /5张
使用工序 总装 2 #
入口位置号 (POST NO.4)
3精、益双生看产(板Le工an作Pr系odu统ct(ioPn3) 6图3-10)
依靠工序内生产看板和工序间领取看板分别来传递生产指令和搬运指令 的生产信息系统称为双看板系统。
通过外协看板的方式,从最后一道工序慢慢往前拉动, 直至供应商。因此,有时候企业会要求供应商也推行 JIT生产方式。
外协领取看板的数量计算与工序间领取看板数量的计算 方法一致。
精益生产(Lean Production)
外协领取看板数量的计算
N
D C
(T
P
Ts )
(3-7)
N为外协领取看板的数量;T为订货周期,也称为看板周
精益生产(Lean Production)
工序间生产看板:定期订货法
M D(L T) S
N D (L T Ts ) C
M为基准量;D 为平均日需求量;L为采购提前期;T为定
货间隔期,S为安全库存量;N为看板的数量; Ts为安全
库存时间;C为盛放物料容器的容量。
- 1、下载文档前请自行甄别文档内容的完整性,平台不提供额外的编辑、内容补充、找答案等附加服务。
- 2、"仅部分预览"的文档,不可在线预览部分如存在完整性等问题,可反馈申请退款(可完整预览的文档不适用该条件!)。
- 3、如文档侵犯您的权益,请联系客服反馈,我们会尽快为您处理(人工客服工作时间:9:00-18:30)。
【精益生产英文】高效看板系统的5大准则请看正文The kanban method, also known in Japanese as 'kamban’ and translates into the equivalent of 'signboard’ in Chinese, is a concept that stresses visualization of a person or team that is available to take on new work. This concept is closely related to just-in-time (JIT) and Lean production, both of which utilize it as a scheduling system which tells a manufacturer what needs to be produced, when it should be produced and exactly how much of it needs to be produced.看板方法,日语中被称为“kamban”,翻译成中文就是“看板”。
看板,是一种用来强调个人或者团队可以接受新工作的理念。
“看板”这一理念,与准时制生产方式(JIT)及精益生产密切相关。
准时制生产方式及精益生产,都被用作为调度系统,告诉生产商什么时候需要生产,以及到底需要生产多少。
Ideally, the kanban system controls the overall value chain starting from the raw materials supplier to the final consumer of the goods or services. Ensuring that there is control helps to avoid disruption of supply as well as overstocking of inventory at any stage of the manufacturing process.理想情况下,看板系统控制从原料供应商到最终消费者的商品或者服务的整体价值链。
一定要确保有控制,这将有助于避免供应的中断,并有助于避免在制造过程中任一阶段的库存积压。
In particular, kanban gives particular attention to any bottlenecks in the process that could result in a slowdown of production or inefficiency in operation. The ultimate aim is to obtain a higher level of throughput and lower delivery times without sacrificing quality by following the following principles that guide the kanban system.尤其是,看板能让我们特别关注流程中的瓶颈问题,瓶颈问题则会导致生产放缓与运作低效,而终极目标则是:遵循影响看板系统的5大原则,在没有牺牲质量的情况下,获得更高的生产能力,并缩短交付时间。
A kanban system typically examines state changes within the work process. These are a general reflection of any change in an activity that generates information on the states of the work. For instance, the activity of analysis generates specific information. When it reaches a point of diminishing returns, the work is now defined as 'analyzed,’ and is then changed into a new activity that will generate additional information such as design or testing. This process of punctuating the arrival of information is what kanban practitioners use to visualize workflow.看板系统,通常会检查工作流程中的状态变化。
这些是对生成工作状态信息的活动的变化的综合反映。
例如,分析的活动会生成特定的信息。
在达到递减点的时间,工作被定义为“分析”,然后,变成新的活动,将产生额外的信息,诸如,设计或者测试。
信息的穿插过程,是看板系统的实践者用来可视化工作流程。
By limiting work in progress we put in place a pull system within part of, or the entire workflow. This system can be implemented using a variety of methods including DBR, CONWIP or kanban, among others. Regardless of this, the essential thing to remember is that the WIP within each state of the flow needs to b e limited while any new work available is 'pulled’ into the next state as soon as the WIP provides sufficient capacity.通过限制在制品,我们在部分或者整个工作流程中使用拉动系统。
拉动系统,可以通过使用多种方法来实现,包括DBR、CONWIP,或者看板等。
无论如何,要记住的是,在每个流程状态的WIP都需要被限制,而一旦WIP能提供足够的容量,任何适当的新工作都被拉到下一个状态。
备注1.DBR是TOC(约束理论)中的一种管理方法,Drum-Buffer-Rope,简称 DBR,中文直译为“鼓、缓冲、绳子方法”。
DBR是TOC应用于制造工厂排程时的一个计划、排程与实施的方法论,它恰当地抓住TOC排程的技巧,使之在工厂层面易于理解和执行。
正是这种简单化使DBR非常有效。
2.CONWIP,即Constant Work In Progress,意思是:定量在制品法。
CONWIP,是美国西北大学的Spearman等人在上世纪90年代提出,其本质是一种推动/拉动混合的策略。
The flow of each work item from each stage to the next within the workflow needs to be continually monitored and accurately reported. Flow means movement of goods and activities and, in this case, what is of the biggest interest is the speed and smoothness of the movement. The ideal situation is for the flow to be fast and smooth. Fast and smooth flow is an indication that the kanban-based system is generating value in the shortest possible time and minimizing the risk and cost caused by delays. What’s more,it is being achieved in a predictable way.从一个阶段到下一个阶段,每个工作条目的工作流程,都需要被连续地监控和准确地报告。
流程,意味着商品与活动的移动,在这种情况下,最让人关注的是运动的速度和平稳,而理想的情况是流动要快速而平稳。
快速和平稳的流动,是看板系统在最短的时间内产生价值,并将由延迟引起的风险与成本最小化一种指示。
更重要的是,其正在以一种可预测的方式来实现。
Until the exact mechanisms or processes of an organizations operation are explicitly laid out, it is almost impossible to talk about improvements. If there is no clear understanding of how things work or how the work is actually done, discussion of problems with the process will be anecdotal, subjective and emotional. By offering an explicit understanding, kanban makes it possible to have a discussion of the issues that is objective, rational and based on empirical evidence.在明确组织运作的确切机制或者流程之前,谈论改进几乎不可能的事情。
如果没有清楚地了解事物是如何运作,以及工作实际上是怎么完成的,那么,讨论流程中的问题,将是不正式的、主观的,并带有情绪的。
通过准确的理解,基于经验证据,看板让我们客观、理性的讨论问题成为一种可能。
Ultimately limiting of the work in progress is what stimulates any discussion of process problems. Anything that impedes the flow of work, or introduces perturbations which cause the flow to be inconsistent will make limiting WIP a major challenge. The team then has two options: break the WIP limit, ignore the issue and proceed, or to face the problem together, have an informed discussion and suggest improvements by consensus.最终限制在制品,是激励流程讨论问题的原因。