DIN EN10204 2005 (含3.1合格证)-金属产品——检验证类型
DIN EN10204 2005 (含3.1合格证)-金属产品——检验证类型

是摘要形式均要得到DIN(柏林)德国标准化研究所的许可。
www.din.de 标准由Beuth出版有限公司(柏林10772)独家销售。
www.beuth.deDIN EN 10204:2005-01国家标准前言欧洲标准EN 10204的修订工作在材料检验(NMP)和钢铁(FES)标准化委员会的积极配合下,在“技术供货条件和质量保证”(秘书处:比利时)技术委员会EC ISS / TC9内进行。
主管的德国标准化委员会是材料检验标准化委员会(NMP)的“取样;验收”工作委员会NMP 892。
对于该标准的应用工作委员会NMP 892做出以下说明:对该标准使用的详细说明在一篇题为“Beuth——备注——检验证书——对DIN EN 10204的备注”的Beuth备注中给出。
该版的重点是:——检验证书概述,使用该标准的基本原则;——从厂家的立场看检验证书;——检验证书的法律地位;——检验证书的联机数据交换。
通过Beuth出版有限公司(柏林10772)购买(通讯地址:Burggrafenstraβe 6, 10787 Berlin)ISBN 3-410-15905-3。
更改对DIN EN 10204:1995-08进行了如下更改:a) 引入“生产厂”,“供货商”和“产品规范”等新概念;b) 减少了检验证书的数量;——删除以前版本中的工厂证书2.3;——以前版本的3.1B由验收检验证3.1代替;——以前版本的3.1A、3.1c和3.2由验收检验证3.2所取代;c) 将德文名称“Sachverständiger”(专家)更改为“Abnahmebeauftragter”(验收代表)。
以前的版本DIN 50049:1951-12,1955-04,1960-04,1972-07,1982-07,1986-08,1991-11,1992-04DIN EN 10204:1995-082欧洲标准EN 102042004年10月ICS 01.110; 77.080.01; 77.120.01 取代EN 10204:1991德文版金属产品——检验证类型该欧洲标准由CEN于2004年8月8日接收。
en 10204 标准

EN 10204 标准全称为"EN 10204:2004 Metallic products - Types of inspection documents",是欧盟针对金属产品制定的质量认证标准。
该标准规定了金属产品应满足的质量要求,以及相应的检验文件类型。
EN 10204 标准分为四个类型,分别为 Type A、Type B、Type C 和 Type D。
每种类型的检验文件都有其特定的适用范围和要求。
1.Type A:适用于所有的金属材料,包括铸件、锻件、焊接件等。
对于 TypeA 的金属材料,制造商需要提交一份详细的制造流程报告,以及每批材料的质量检验报告。
这些报告应包含材料的化学成分、力学性能、尺寸和外观等方面的信息。
2.Type B:适用于经过加工处理的金属材料,例如热处理、表面处理等。
对于 Type B 的金属材料,制造商需要提交一份制造流程报告,以及每批材料的质量检验报告。
这些报告应包含材料的化学成分、力学性能、尺寸和外观等方面的信息,以及加工处理过程中的详细记录。
3.Type C:适用于经过焊接或铸造的金属材料。
对于Type C 的金属材料,制造商需要提交一份详细的焊接或铸造流程报告,以及每批材料的质量检验报告。
这些报告应包含材料的化学成分、力学性能、尺寸和外观等方面的信息,以及焊接或铸造过程中的详细记录。
4.Type D:适用于经过热处理的金属材料。
对于 Type D 的金属材料,制造商需要提交一份热处理流程报告,以及每批材料的质量检验报告。
这些报告应包含材料的化学成分、力学性能、尺寸和外观等方面的信息,以及热处理过程中的详细记录。
EN 10204 标准的认证范围广泛,包括各种金属材料和制品,如钢铁、铝、铜、镍等。
通过EN 10204 认证的金属产品可以在欧盟市场上自由流通和销售,同时也能够提高企业在国际市场上的竞争力。
en10204标准

en10204标准EN10204标准。
EN10204标准是指欧洲标准化组织(European Standardization Organization)制定的关于金属材料的检测和证明的标准。
该标准在全球范围内被广泛应用,特别是在涉及到质量控制和质量保证的领域。
本文将对EN10204标准进行详细介绍,包括其内容、适用范围、意义和实施方法等方面的内容。
EN10204标准主要涉及到金属材料的检测和证明,其中包括了四种不同类型的证明文件,分别是2.1、2.2、3.1和3.2。
2.1和2.2类型的证明文件是由生产商自行签发的,用于证明产品的符合性。
而3.1和3.2类型的证明文件则需要经过第三方机构的检测和验证,用于证明产品的质量和符合性。
这些不同类型的证明文件适用于不同的产品和场合,确保了产品质量的可追溯性和可靠性。
EN10204标准的适用范围非常广泛,涵盖了几乎所有金属材料的生产和使用领域。
无论是在航空航天、汽车制造、建筑工程还是其他工业领域,都可以根据EN10204标准来进行质量控制和证明。
这为各行各业的生产和贸易提供了统一的标准,有利于提高产品质量和降低贸易风险。
EN10204标准的实施方法主要包括了生产商的自检和第三方检测两种方式。
生产商需要建立质量管理体系,并对产品进行全面的自检,以确保产品的符合性和质量稳定性。
同时,第三方检测机构也需要对产品进行抽样检测和验证,为产品的质量提供客观、可靠的证明。
这种双重的质量控制机制保证了EN10204标准的实施效果和可靠性。
EN10204标准的意义在于为金属材料的生产和使用提供了统一的质量控制和证明标准,有利于提高产品质量和降低贸易风险。
通过严格的质量管理和检测验证,可以确保产品的符合性和质量稳定性,为消费者和用户提供更加可靠的产品。
同时,EN10204标准也为企业间的贸易合作提供了统一的规则和标准,有利于促进国际贸易的发展和合作。
总之,EN10204标准是金属材料质量控制和证明的重要标准,对于提高产品质量、降低贸易风险、促进国际贸易合作都具有重要意义。
EN 10204金属产品—检验文件的类型(中文版)

欧洲标准EN 10204-2004金属产品—检验文件的类型CEN欧洲标准化委员会金属产品—检验文件的类型1范围1.1本标准规定了按合同要求提供给需方的适用于所有金属产品(例如,无论采用何种方法生产的板、棒、锻件、铸件)的不同类型的检验文件。
1.2本标准也适用于非金属产品。
1.3本标准与规定了交货技术条件的产品标准一起使用。
注1在检验文件中所列的信息可在相应的标准中找到,例如,对钢产品见EN10168。
注2附录A给出了检验文件间的差异概览。
2术语和定义本标准采用如下标准和定义:2.1非规定检验non-specific inspection生产厂按照自定程序进行的检验和试验,以判定由相同生产工艺所生产的产品是否满足合同的要求。
被检验的产品不一定是实际供货的产品。
2.2规定检验specific inspection是指在交货前,根据合同的技术要求,在交货的产品上或其中的部分产品上进行检验,以验证他们是否符合合同的要求。
2.3生产厂manufacture根据合同和相应产品标准规定的要求生产产品的组织。
2.4中间商intermediary由生产厂进行供货的并且其向需方供货前不对产品进一步加工或加工后不改变需方合同和相关产品标准中规定的产品性能的组织。
2.5产品规范product specification对合同中的要求以书面形式进行详细叙述,例如,法规、标准或其他规范。
3基于非规定检验的检验文件3.1符合合同的声明“2.1”(Declaration of compliance with the order“type2.1”)生产厂声明其供应的产品符合合同的要求(不包括试验结果)的文件。
3.2试验报告“2.2”(Test report“type2.2)生产厂声明其供应的产品符合合同的要求的文件,且文件中提供基于非规定检验的试验结果。
4基于规定检验的检验文件4.1检验证明书3.1 (Inspection certificate 3.type 3.P)由生产厂出具的声明其提供的产品符合合同要求并提供试验结果的文件。
3.1证书标准
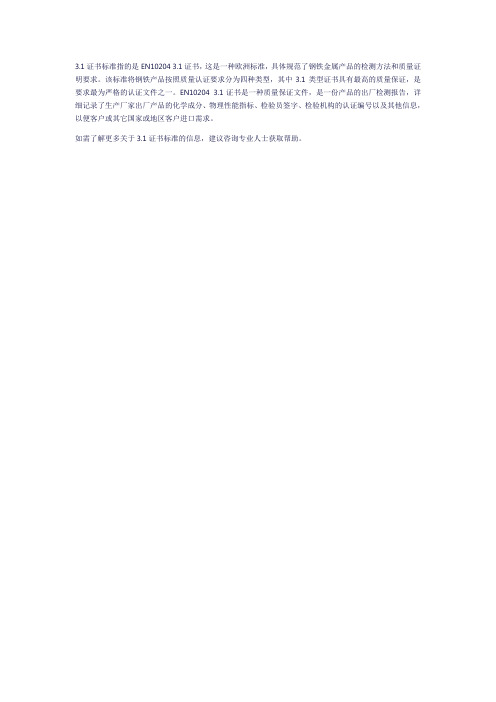
3.1证书标准指的是EN10204 3.1证书,这是一种欧洲标准,具体规范了钢铁金属产品的检测方法和质量证明要求。
该标准将钢铁产品按照质量认证要求分为四种类型,其中3.1类型证书具有最高的质量保证,是要求最为严格的认证文件之一。
EN10204 3.1证书是一种质量保证文件,是一份产品的出厂检测报告,详细记录了生产厂家出厂产品的化学成分、物理性能指标、检验员签字、检验机构的认证编号以及其他信息,以便客户或其它国家或地区客户进口需求。
如需了解更多关于3.1证书标准的信息,建议咨询专业人士获取帮助。
DINEN102042005(含3.1合格证)金属产品设备检验证类型

是摘要形式均要得到DIN(柏林)德国标准化研究所的许可。
www.din.de 标准由Beuth出版有限公司(柏林10772)独家销售。
www.beuth.de国家标准前言欧洲标准EN 10204的修订工作在材料检验(NMP)和钢铁(FES)标准化委员会的积极配合下,在“技术供货条件和质量保证”(秘书处:比利时)技术委员会EC ISS / TC9内进行。
主管的德国标准化委员会是材料检验标准化委员会(NMP)的“取样;验收”工作委员会NMP 892。
对于该标准的应用工作委员会NMP 892做出以下说明:对该标准使用的详细说明在一篇题为“Beuth——备注——检验证书——对DIN EN 10204的备注”的Beuth备注中给出。
该版的重点是:——检验证书概述,使用该标准的基本原则;——从厂家的立场看检验证书;——检验证书的法律地位;——检验证书的联机数据交换。
通过Beuth出版有限公司(柏林10772)购买(通讯地址:Burggrafenstraβe 6, 10787 Berlin)ISBN 3-410-15905-3。
更改对DIN EN 10204:1995-08进行了如下更改:a) 引入“生产厂”,“供货商”和“产品规范”等新概念;b) 减少了检验证书的数量;——删除以前版本中的工厂证书2.3;——以前版本的3.1B由验收检验证3.1代替;——以前版本的3.1A、3.1c和3.2由验收检验证3.2所取代;c) 将德文名称“Sachverständiger”(专家)更改为“Abnahmebeauftragter”(验收代表)。
以前的版本DIN 50049:1951-12,1955-04,1960-04,1972-07,1982-07,1986-08,1991-11,1992-04 DIN EN 10204:1995-08欧洲标准EN 102042004年10月ICS 01.110; 77.080.01; 77.120.01 取代EN 10204:1991德文版金属产品——检验证类型该欧洲标准由CEN于2004年8月8日接收。
en10204 3.1证书 不符合欧洲标准
EN10204是与金属产品的不同类型检验文件相关的欧洲标准。
该标准有2.1、2.2、3.1和3.2的四种类型,其中EN10204-3.1证书适用于板材、薄板、棒材、锻件、铸件等金属产品。
如果金属材料厂没有通过ISO9001或者其产品不符合欧洲材料规范,那么这个工厂是没有权利签发EN10204-3.1证书的。
相反,它需要向第三方认证机构申请并获得EN10204-3.2证书,这样可以证明其产品符合欧洲材料规范。
因此,如果您收到了一个声称符合EN10204-3.1标准的证书,但实际上可能不符合欧洲的材料规范,那么这可能是一个问题。
为了确保您的金属材料满足欧洲的标准,建议您:
1. 仔细检查证书上的信息,确保它是由权威的第三方认证机构签发的。
2. 直接联系认证机构或第三方机构欧测进行批量的测试发证,以确保所购买的材料真正符合欧洲的材料规范。
3. 如果可能的话,考虑从已经获得EN10204-3.2证书的供应商处购买材料,这样可以更有保障。
DIN EN 10204
DIN EN 10204的英文版金属制品检验文件(包括修改版A1:1995)ICS77.140.00说明:金属制品、不锈钢、有色金属材料试验检验文件。
欧洲标准EN 10204:1991包括修改版A1:1995,它具有与DIN标准同等资格。
国家标准前言本标准的编制中相关负责的德国小组为材料试验标准委员会、钢铁标准委员会和有色金属标准委员会。
修改与1992年4月版的DIN50049相比,该标准数目已发生变化且加入了修订本A1。
以前的版本DIN50049:1951-12,1955-04,1960-04,1972-07,1982-07,1986-08,1991-11,1992-04。
英文版金属制品检验文件形式(包括修改版A1:1995)本欧洲标准经CEN(欧洲标准委员会)于1991年8月21日批准,修改版A1在1995年5月11日批准。
CEN成员必须按照CEN/CENELEC的内部规则,该规则中规定了赋予本欧洲标准与国家标准同等地位的条件,这些条件现没有改动。
与国家标准相关的最新一览表及文献目录可从中央秘书处获取。
本欧洲标准现有英、法、德三种语言的官方版本。
任何一种由CEN成员负责译成本国语言且已通告中央秘书处的版本都具有与官方版本的同等地位。
CEN成员是由奥地利、比利时、丹麦、芬兰、法国、德国、希腊、冰岛、爱尔兰、意大利、卢森堡、荷兰、挪威、葡萄牙、西班牙、瑞典、苏格兰及英国的国家标准小组组成。
目录EN10204:1991前言 (2)EN10204:1991/A1:1995 (3)1 总则 (3)1.1 范围 (3)1.2 说明 (3)2 检验文件由制造商或生产部门指定人员进行检测试验后拟定 (4)2.1 满足订单要求的(‘2.1’)的合格证 (4)2.2 试验报告(‘2.2’) (4)2.3 特殊试验报告(‘2.3’) (4)3 检验文件由非生产部门指定人员在特殊试验的基础上进行试验并检查后拟定 (4)3.1 检验合格证 (4)3.2 检验报告 (5)4 由加工者或中间商提供检验文件 (5)5 检验文件的生效 (5)6 检验文件小结 (5)表1 (5)附录A(提供资料的)EN10204中规定的检验报告的不同语言版本 (6)EN10204:1991前言欧洲钢铁标准委员会(ECISS)指导ECISS/TC9技术委员会“交货技术条件及质量控制”。
EN 10204 译文 金属产品—检验文件的类型
金属产品—检验文件的类型金属产品—检验文件的类型1 范围1.1 本标准规定了按合同要求提供给需方的适用于所有金属产品(例如,无论采用何种方法生产的板、棒、锻件、铸件)的不同类型的检验文件。
1.2 本标准也适用于非金属产品。
1.3 本标准与规定了交货技术条件的产品标准一起使用。
注1 在检验文件中所列的信息可在相应的标准中找到,例如,对钢产品见EN 10168。
注2 附录A 给出了检验文件间的差异概览。
2 术语和定义本标准采用如下标准和定义:2.1 非规定检验non-specific inspection生产厂按照自定程序进行的检验和试验,以判定由相同生产工艺所生产的产品是否满足合同的要求。
被检验的产品不一定是实际供货的产品。
2.2 规定检验specific inspection是指在交货前,根据合同的技术要求,在交货的产品上或其中的部分产品上进行检验,以验证他们是否符合合同的要求。
2.3 生产厂manufacture根据合同和相应产品标准规定的要求生产产品的组织。
2.4 中间商intermediary由生产厂进行供货的并且其向需方供货前不对产品进一步加工或加工后不改变需方合同和相关产品标准中规定的产品性能的组织。
2.5 产品规范product specification对合同中的要求以书面形式进行详细叙述,例如,法规、标准或其他规范。
3 基于非规定检验的检验文件3.1 符合合同的声明“2.1”(Declaration of compliance with the order “type 2.1”)生产厂声明其供应的产品符合合同的要求(不包括试验结果)的文件。
3.2 试验报告“2.2”(Test report “type 2.2)生产厂声明其供应的产品符合合同的要求的文件,且文件中提供基于非规定检验的试验结果。
4 基于规定检验的检验文件4.1 检验证明书3.1(Inspection certificate 3.1”type 3.1”)由生产厂出具的声明其提供的产品符合合同要求并提供试验结果的文件。
3.1 证书
1.依据标准:EN 10204:2004 金属产品检验文件的类型EN 10204:2004 Metallic products —Types of inspection documentsEN 10204认证是指金属产品材料认证,它的作用是声名检验结果与订单要求一致。
(Statement of compliance with the order, with indication of results of specific inspection)一般有两种形式的证书:1- EN 10204-3.1证书如果一个金属材料厂通过了ISO 9001认证,且发证机构是欧盟的认证机构,则这个工厂可以向其客户签发EN10204-3.1材料证书。
金属材料厂作为卖家,向买家签发材料证书。
证书上必须体现工厂的客户名称,即有明确的买家。
一个买家需要一张证书。
如果这个金属材料厂没有通过ISO9001或者ISO9001的发证单位不是欧盟认证机构,这个工厂则没有权利签发EN10204-3.1证书,必须向第三方认证机构申请EN10204-3.2证书。
2- EN 10204-3.2证书EN10204-3.2的签发机构必须是欧盟授权机构。
经过对工厂的买家所购的产品类型进行相关测试后,以第三方的身份向工厂的买家声名检验结果与订单相符合。
证书上同样必须体现客户名称和生产工厂名称。
EN10204-3.2证书是向客户证明其产品符合欧洲材料规范的有效证书,一般对于出口的大型设备、压力设备等产品,都需要其原材料供应商提供EN10204-3.2证书,来证明设备上所采用的原材料是符合欧洲规范的。
EN10204证书适用于任何金属材料,比如钢材、焊接件等产品。
2.Certificates in compliance with EN 10204- 3.1. shall include as a minimum- chemical analysis- specification range analysis- mechanical test results- heat treated condition3.条件A 通过ISO9001认证,且需要注册在欧盟国家的机构颁发条件B 需要对产品做材料特殊评估(即PED 4.3所规定)咨询了很多家认证,各方说法不一说法1. 满足条件A即可出具 3.1证书说法2. 满足条件B即可出具 3.1证书说法3. 同时满足条件A,B才可出具3.1证书满足条件B就可以自己出3.1了,但在你获得4.3的过程中,不是如您讲的,简单的进行一些材料评估就可以了,还要对您的工厂体系进行适当的评估:如IO90001,但此认证不一定是要欧洲国家机构颁发。
- 1、下载文档前请自行甄别文档内容的完整性,平台不提供额外的编辑、内容补充、找答案等附加服务。
- 2、"仅部分预览"的文档,不可在线预览部分如存在完整性等问题,可反馈申请退款(可完整预览的文档不适用该条件!)。
- 3、如文档侵犯您的权益,请联系客服反馈,我们会尽快为您处理(人工客服工作时间:9:00-18:30)。
是摘要形式均要得到DIN(柏林)德国标准化研究所的许可。
www.din.de 标准由Beuth出版有限公司(柏林10772)独家销售。
www.beuth.de国家标准前言欧洲标准EN 10204的修订工作在材料检验(NMP)和钢铁(FES)标准化委员会的积极配合下,在“技术供货条件和质量保证”(秘书处:比利时)技术委员会EC ISS / TC9内进行。
主管的德国标准化委员会是材料检验标准化委员会(NMP)的“取样;验收”工作委员会NMP 892。
对于该标准的应用工作委员会NMP 892做出以下说明:对该标准使用的详细说明在一篇题为“Beuth——备注——检验证书——对DIN EN 10204的备注”的Beuth备注中给出。
该版的重点是:——检验证书概述,使用该标准的基本原则;——从厂家的立场看检验证书;——检验证书的法律地位;——检验证书的联机数据交换。
通过Beuth出版有限公司(柏林10772)购买(通讯地址:Burggrafenstraβe 6, 10787 Berlin)ISBN 3-410-15905-3。
更改对DIN EN 10204:1995-08进行了如下更改:a) 引入“生产厂”,“供货商”和“产品规范”等新概念;b) 减少了检验证书的数量;——删除以前版本中的工厂证书2.3;——以前版本的3.1B由验收检验证3.1代替;——以前版本的3.1A、3.1c和3.2由验收检验证3.2所取代;c) 将德文名称“Sachverständiger”(专家)更改为“Abnahmebeauftragter”(验收代表)。
以前的版本DIN 50049:1951-12,1955-04,1960-04,1972-07,1982-07,1986-08,1991-11,1992-04DIN EN 10204:1995-08欧洲标准EN 102042004年10月ICS 01.110; 77.080.01; 77.120.01 取代EN 10204:1991德文版金属产品——检验证类型该欧洲标准由CEN于2004年8月8日接收。
CEN成员有义务执行CEN/CENELEC的商业法则,其中规定了无改动地给予该标准以国家标准之地位的条件。
位于文本最后的国家标准目录和文献目录资料应要求可在中央秘书处或每个CENELEC ——成员处获得。
该欧洲标准有三种正式文本(德文,英文,法文)。
由某个CENELEC——成员自己负责翻译成其本国语言,并通知中央秘书处的其它语言文本具有与正式文本相同的法律地位。
CENELEC——成员为比利时,丹麦,德国,爱沙尼亚,芬兰,法国,希腊,爱尔兰,冰岛,意大利,拉脱维亚,立陶宛,卢森堡,马其他,荷兰,挪威,奥地利,波兰,葡萄牙,瑞典,瑞士,西班牙,捷克共和国,匈牙利,英国和塞浦路斯的国家电气技术委员会。
欧洲标准化委员会管理中心:rue de stassart 36, B-1050布鲁塞尔© 2004CEN——所有的使用权(不管以何种形式和何种参考号:EN 10204:2004D 方法使用)都为全世界的CEN——成员所拥有。
目录页码前言 (5)1 应用范围 (6)3 非特殊检验的检验证 (6)4 特殊检验的检验证书 (7)5 检验证书的确认和转发 (7)6 通过某个经销商转发检验证书 (7)附录A (标准化信息) 检验证的构成 (8)附录ZA (标准化信息)该欧洲标准与EU——规程97/23/EG基本要求之间的关系.. 9参考文献 (11)前言文献EN 10204:2004由秘书处设在IBN的“技术供货条件和质量保证”技术委员会ECISS/TC 9所制定。
本欧洲标准必须具有国家标准的法律地位,要么发布相同的文本,要么于2005年4月前予以确认,并且将可能与之有矛盾的国家标准于2005年4月前予以撤消。
该标准取代EN 10204:1991。
该欧洲标准的制定由欧洲委员会和欧洲自由贸易组织所委托,并支持EU——规程97/23/EG基本要求。
与EU——规程97/23/EG的关系在本标准的标准化信息附录ZA中给出。
重要的更改为:——引入“生产厂”,“供货商”和“产品规范”等定义;——减少了检验证书的数量;——删除以前版本中的工厂证书2.3。
——验收检验证3.1取代以前版本的3.1B;——以前版本的3.1A、3.1C和3.2由验收检验证3.2所取代;根据CEN / CENELEC——业务规程,以下国家的标准化研究所有权接收该欧洲标准:比利时,丹麦,德国,爱沙尼亚,芬兰,法国,希腊,爱尔兰,冰岛,意大利,拉脱维亚,立陶宛,卢森堡,马其他,荷兰,挪威,奥地利,波兰,葡萄牙,瑞典,瑞士,斯洛伐克,斯洛文尼亚,西班牙,捷克共和国,匈牙利,英国和塞浦路斯。
1 应用范围1.1本文件中规定了各种类型的检验证书,可供订货者根据订货协议在各种金属制品如板材,薄板材,棒材,锻件,铸件等供货时使用,与生产方式无关。
1.2该文件也可适用于非金属制品。
1.3该文件要与规定了产品技术供货条件的产品规范一切使用。
备注1 有关检验证书内容方面的资料可从相应的文件中获得,例如:EN 10168(钢检验证书)。
备注2 附录A列出了各种各样的检验证书。
2 定义对于本文件的应用适用以下定义:2.1非特殊检验应通过厂家按照他们觉得合适的方法进行的检验证明,产品是否满足订货时规定的要求,按相同的产品规范和相同的方法所生产。
被检验产品不一定要从所供货品中提取。
2.2特殊检验按照产品规范在供货之前,对所提供之产品或这些产品所属之检验单位进行检验,以确定这些产品是否满足订货时规定的条件。
2.3生产厂根据相应的产品规范特点按照订货要求生产各自产品的单位。
2.4供货商从生产厂家获得产品,不经过继续加工或者如果加工,则应不改变订货中和在服务于订货的产品规范中所确定之性质的条件下提供这些产品的单位。
2.5产品规范在订货自身中和/或通过相关文件如规定,标准和其它规范确定的订货技术要求的总称。
3 非特殊检验的检验证3.1工厂检验证“2.1”由生产厂确认提供的产品符合订货要求,不提供检验结果数据的检验证。
3.2工厂证书“2.2”由生产厂证明提供的产品符合订货要求,并提供非特殊检验结果数据的检验证书。
4 特殊检验的检验证书4.1验收检验证书“3.1”由生产厂提供,用于证明所提供之产品满足订货时所规定之要求,并带有检验结果数据的检验证书。
在产品规范。
业务规程,技术规定和\或订货中确定检验的进行过程和检验单位。
检验证书要得到生产厂的一个与加工部门无关的验收代表所确认。
一个生产厂可以在验收检验证书3.1中引用检验结果,而这些结果是在采用保证可追溯性的方法,并且可提交相应检验证书的前提下,在对他们所使用之原材料和半成品进行特殊检验的基础上得到的。
4.2验收检验证书“3.2”包含试验结果数据的证明书,在该证明书中不仅由与加工部门无关的生产厂验收代表,而且由与加工部门无关的订货单位验收代表或官方规程中确定的验收代表确认,所提供之产品满足订货时所规定的要求。
一个生产厂可以在验收检验证书3.2中引用检验结果,而这些结果是在采用保证可追溯性的方法,并且可提交相应检验证书的前提下,在对他们所使用之原材料和半成品进行特殊检验的基础上得到的。
5 检验证书的确认和转发检验证书必须得到负责人员(人员们)的确认(姓名和职位)。
检验证书的保存和转发必须通过电子邮寄或书面形式实现。
6 通过某个经销商转发检验证书经销商只能转发生产厂所提供之检验证书的原件或复印件,不得有任何改动。
必须给检验证书附上一种验证其产品的适当手段,以保证产品和证书相互一一对应。
允许在以下前提下对检验证书原件进行复制:——采用保证可追溯性的方法——应要求可提供检验证书原件如果进行复制,则允许将原来的提供数量代之以实际提供量。
.'.附录A (标准化信息) 检验证的构成表A.1给出检验证的构成情况表A.1——检验证的构成附录ZA(标准化信息)该欧洲标准与EU——规程97/23/EG基本要求之间的关系该欧洲标准的准备工作是通过CEN的一个欧洲委员会代表进行的,以便满足欧洲议会的EU——规程97/23/EG的基本要求,同时满足有关压力仪方面调整成员国家权利规定的1997年5月29日的EU——建议。
一旦该标准在该规程下在欧洲联合会的官方公报中发布,作为国家标准至少在一个成员国引进,而且与表ZA.1中给出的该标准段落一致,在该标准的应用范围界限内,便满足了与该规程及其所属EFTA——规程之相应基本要求一致的条件。
表ZA.1——该欧洲标准与97/23/EG规程的一致性警告——涉及该欧洲标准的应用范围的其它要求和EU——规程也可能被应用于产品。
a 非特殊检验允许代之以符合材料标准或订货要求的特殊检验。
b 接受过专门评审的与材料有关的材料生产厂质量控制系统通过共同体下设的一个主管部门予以证明。
图ZA.1——与97/23/EG规程附录第4.3小节的一致性.'. 参考文献[1] EN 10168,钢制品——检验证书——数据表及说明。