关键工序质量控制
关键工序质量控制点
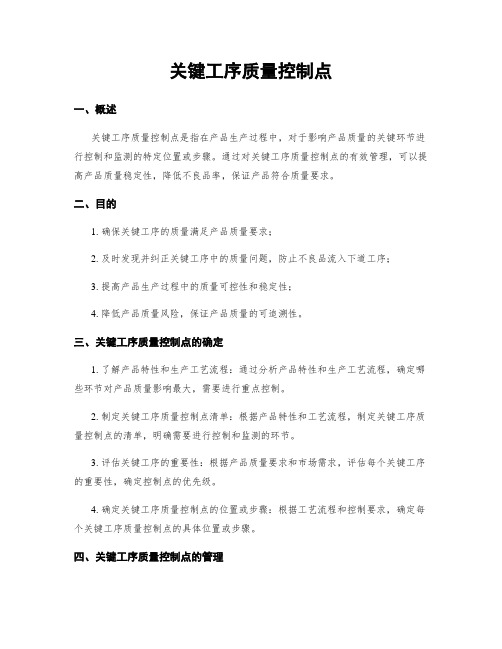
关键工序质量控制点一、概述关键工序质量控制点是指在产品生产过程中,对于影响产品质量的关键环节进行控制和监测的特定位置或步骤。
通过对关键工序质量控制点的有效管理,可以提高产品质量稳定性,降低不良品率,保证产品符合质量要求。
二、目的1. 确保关键工序的质量满足产品质量要求;2. 及时发现并纠正关键工序中的质量问题,防止不良品流入下道工序;3. 提高产品生产过程中的质量可控性和稳定性;4. 降低产品质量风险,保证产品质量的可追溯性。
三、关键工序质量控制点的确定1. 了解产品特性和生产工艺流程:通过分析产品特性和生产工艺流程,确定哪些环节对产品质量影响最大,需要进行重点控制。
2. 制定关键工序质量控制点清单:根据产品特性和工艺流程,制定关键工序质量控制点的清单,明确需要进行控制和监测的环节。
3. 评估关键工序的重要性:根据产品质量要求和市场需求,评估每个关键工序的重要性,确定控制点的优先级。
4. 确定关键工序质量控制点的位置或步骤:根据工艺流程和控制要求,确定每个关键工序质量控制点的具体位置或步骤。
四、关键工序质量控制点的管理1. 制定标准操作规程:针对每个关键工序质量控制点,制定相应的标准操作规程,明确操作步骤、操作要求和质量控制点的监测方法。
2. 培训操作人员:对参与关键工序的操作人员进行培训,确保其了解标准操作规程,并能正确操作和监测关键工序质量控制点。
3. 设立监测点和监测仪器:根据质量控制要求,设立相应的监测点,并配备适当的监测仪器,对关键工序质量控制点进行实时监测。
4. 定期检查和校准:定期对监测仪器进行检查和校准,确保其准确度和可靠性。
5. 数据分析和处理:对关键工序质量控制点的监测数据进行分析和处理,及时发现异常情况并采取相应的纠正措施。
6. 记录和归档:对关键工序质量控制点的监测数据进行记录和归档,以备查证和追溯。
五、关键工序质量控制点的效果评估1. 收集关键工序质量控制点的监测数据:定期收集关键工序质量控制点的监测数据,包括产品质量指标、操作参数等。
重点工序质量控制

重点工序质量控制引言概述:在任何生产过程中,重点工序的质量控制是确保产品质量的关键。
重点工序是指生产过程中对产品性能、外观、可靠性等方面影响较大的工序。
本文将从五个方面详细阐述重点工序质量控制的重要性和具体措施。
一、合理规划工序流程1.1 确定关键工序:通过对产品生产过程的分析,确定对产品质量影响最大的工序,将其定义为关键工序。
1.2 设定工序目标:针对关键工序,制定明确的质量目标,包括产品性能、外观、可靠性等方面的要求。
1.3 制定工序流程:根据产品要求和工艺特点,制定详细的工序流程,确保每一个环节都能得到充分的控制和监督。
二、严格执行操作规程2.1 制定操作规程:针对每一个关键工序,制定详细的操作规程,包括工艺参数、操作步骤、设备要求等内容。
2.2 培训操作人员:对操作规程进行培训,确保操作人员理解并能够正确执行规程,提高操作的准确性和稳定性。
2.3 引入自动化设备:借助自动化设备,减少人为因素对工序的影响,提高操作的一致性和稳定性。
三、建立质量检验体系3.1 制定检验标准:针对每一个关键工序,制定详细的质量检验标准,包括产品尺寸、外观、性能等方面的要求。
3.2 建立检验流程:根据产品特点和工艺要求,建立完整的质量检验流程,确保每一个工序都能得到全面的检验和评估。
3.3 引入先进检测设备:采用先进的检测设备,提高质量检验的准确性和效率,确保产品符合质量要求。
四、加强过程监控和数据分析4.1 实时监控工艺参数:通过采集和监控工艺参数,及时发现工艺异常和变化,及时调整和纠正,确保工序稳定运行。
4.2 数据分析和统计:对工艺参数和质量检验数据进行分析和统计,发现潜在问题和趋势,及时采取措施避免质量问题的发生。
4.3 建立反馈机制:通过与上下游工序的沟通和反馈,及时解决工序间的质量问题,确保整个生产过程的质量稳定。
五、持续改进和优化5.1 设立质量改进小组:组建专门的质量改进小组,定期评估和改进关键工序的质量控制措施,推动工序质量的持续提升。
关键工序质量控制点

关键工序质量控制点一、背景介绍在任何生产过程中,关键工序的质量控制至关重要。
关键工序是指对最终产品质量有重要影响的工序,其质量控制直接关系到产品的性能、可靠性和客户满意度。
因此,建立有效的关键工序质量控制点是确保产品质量的关键一环。
二、关键工序质量控制点的定义关键工序质量控制点是指在关键工序中,对关键工序的输入、加工和输出进行监控和控制的特定位置或者环节。
通过在关键工序中设立质量控制点,可以及时发现和纠正生产过程中的问题,确保产品的一致性和稳定性。
三、关键工序质量控制点的重要性1. 提高产品质量:通过设立关键工序质量控制点,可以及时发现并纠正生产过程中的问题,确保产品符合质量标准。
2. 降低质量风险:关键工序质量控制点可以有效降低生产过程中的质量风险,减少不合格品的产生,提高生产效率。
3. 优化生产流程:关键工序质量控制点有助于识别和改进生产流程中的瓶颈和问题,提高生产效率和产品质量。
4. 提升客户满意度:通过关键工序质量控制点,可以确保产品的一致性和稳定性,提高客户满意度和品牌形象。
四、关键工序质量控制点的设立步骤1. 确定关键工序:首先需要确定哪些工序是关键工序,即对产品质量有重要影响的工序。
可以通过质量数据分析、专家评估等方法来确定关键工序。
2. 确定质量控制点:在关键工序中,根据工序的特点和要求,确定适合设立质量控制点的位置或者环节。
质量控制点应能够准确反映工序的质量状况。
3. 制定质量控制标准:根据产品的质量要求和工序的特点,制定相应的质量控制标准。
质量控制标准应包括质量指标、检测方法、合格标准等内容。
4. 设立质量控制点:在关键工序中设立质量控制点,并安排专人负责监控和控制。
质量控制点应具备合适的检测设备和工具。
5. 实施质量控制:在生产过程中,严格按照质量控制标准进行检测和控制。
对于不合格品,及时采取纠正措施,避免不良品流入下一工序或者最终产品。
6. 监控和改进:定期对关键工序质量控制点进行监控和评估,及时发现和解决问题。
关键工序质量控制点

关键工序质量控制点一、引言关键工序质量控制点是指在生产过程中对关键工序进行质量控制的重要节点。
通过在关键工序中设立质量控制点,可以及时发现和纠正产品质量问题,确保产品质量的稳定和可靠性。
本文将详细介绍关键工序质量控制点的定义、目的、设立原则和具体操作步骤。
二、定义关键工序质量控制点是指在生产过程中对影响产品质量的关键环节进行控制的特定位置或者时间点。
通过对这些关键工序进行监控和控制,可以确保产品在整个生产过程中的质量稳定性和一致性。
三、目的1. 提高产品质量:通过对关键工序进行质量控制,可以及时发现和解决工艺问题,确保产品质量符合要求。
2. 减少质量风险:关键工序质量控制点的设立可以匡助企业预防和降低质量风险,减少不良品率和客户投诉。
3. 提高生产效率:通过对关键工序进行监控和控制,可以提高生产效率,减少生产过程中的浪费和重复工作。
四、设立原则1. 选择关键工序:根据产品特点和生产工艺,选择对产品质量影响较大的关键工序作为控制点。
2. 确定控制参数:根据产品质量要求和工艺要求,确定关键工序的控制参数,如温度、压力、速度等。
3. 制定控制标准:根据产品质量要求和工艺要求,制定关键工序的控制标准,如合格品率、不良品率等。
4. 设立监测方法:选择适当的监测方法,如抽样检验、实时监测、自动化控制等,对关键工序进行监测和控制。
5. 制定纠正措施:当关键工序浮现异常情况时,应及时采取纠正措施,防止不良品的产生和扩散。
五、操作步骤1. 识别关键工序:通过对生产工艺的分析,确定对产品质量影响较大的关键工序。
2. 确定控制参数:根据产品质量要求和工艺要求,确定关键工序的控制参数,并建立相应的记录表格。
3. 制定控制标准:根据产品质量要求和工艺要求,制定关键工序的控制标准,并明确合格品率和不良品率等指标。
4. 设立监测方法:根据关键工序的特点和要求,选择适当的监测方法,如抽样检验、实时监测等。
5. 建立监测记录:建立关键工序的监测记录表格,记录关键工序的监测结果和控制措施。
关键工序质量控制点
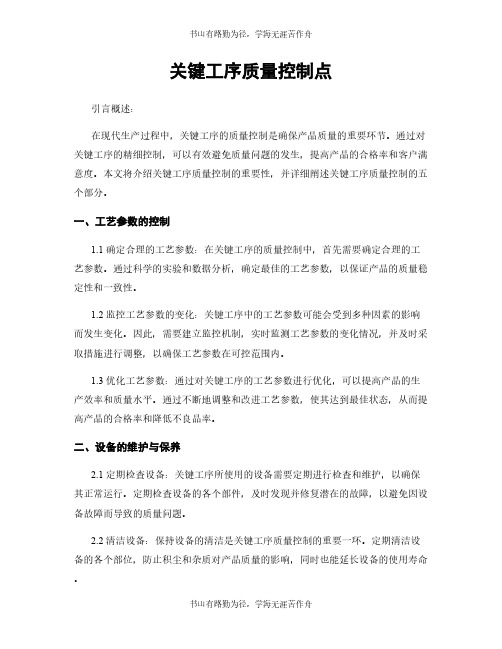
关键工序质量控制点引言概述:在现代生产过程中,关键工序的质量控制是确保产品质量的重要环节。
通过对关键工序的精细控制,可以有效避免质量问题的发生,提高产品的合格率和客户满意度。
本文将介绍关键工序质量控制的重要性,并详细阐述关键工序质量控制的五个部分。
一、工艺参数的控制1.1 确定合理的工艺参数:在关键工序的质量控制中,首先需要确定合理的工艺参数。
通过科学的实验和数据分析,确定最佳的工艺参数,以保证产品的质量稳定性和一致性。
1.2 监控工艺参数的变化:关键工序中的工艺参数可能会受到多种因素的影响而发生变化。
因此,需要建立监控机制,实时监测工艺参数的变化情况,并及时采取措施进行调整,以确保工艺参数在可控范围内。
1.3 优化工艺参数:通过对关键工序的工艺参数进行优化,可以提高产品的生产效率和质量水平。
通过不断地调整和改进工艺参数,使其达到最佳状态,从而提高产品的合格率和降低不良品率。
二、设备的维护与保养2.1 定期检查设备:关键工序所使用的设备需要定期进行检查和维护,以确保其正常运行。
定期检查设备的各个部件,及时发现并修复潜在的故障,以避免因设备故障而导致的质量问题。
2.2 清洁设备:保持设备的清洁是关键工序质量控制的重要一环。
定期清洁设备的各个部位,防止积尘和杂质对产品质量的影响,同时也能延长设备的使用寿命。
2.3 更新设备:随着科技的进步,设备的更新换代是关键工序质量控制的必要措施。
及时更新设备,引入更先进的技术和设备,可以提高生产效率和产品质量水平。
三、操作规程的制定与执行3.1 制定详细的操作规程:关键工序的操作规程应该详细而清晰,包括每个步骤的具体要求和操作方法。
制定操作规程时,要考虑到各种可能的情况和变化,并提供相应的应对措施。
3.2 培训操作人员:关键工序的操作人员需要经过专业的培训,熟悉操作规程和工艺要求。
通过培训,操作人员可以掌握正确的操作方法和技巧,提高操作的准确性和稳定性。
3.3 监督执行情况:制定好的操作规程需要得到严格的执行。
关键工序质量控制点

关键工序质量控制点一、引言关键工序质量控制点是指在生产过程中对关键工序进行质量控制的重要环节。
通过对关键工序的质量控制,可以确保产品的质量符合标准要求,提高生产效率,降低生产成本,增强企业的竞争力。
本文将详细介绍关键工序质量控制点的定义、重要性、选择方法以及实施步骤。
二、定义关键工序质量控制点是指在整个生产过程中,对于影响产品质量的关键工序进行重点监控和控制的环节。
关键工序是指对产品质量影响较大、难以修复的工序,其质量控制点是指在该工序中进行质量监控和调控的特定位置或者时间点。
三、重要性1. 提高产品质量:通过对关键工序进行质量控制,可以及时发现并纠正工艺参数偏差、设备故障等问题,确保产品的质量符合标准要求。
2. 提高生产效率:关键工序质量控制点的设立可以减少不合格品的产生,降低废品率,提高生产效率。
3. 降低生产成本:通过对关键工序进行质量控制,可以避免因不合格品而造成的返工、报废等额外成本,降低生产成本。
4. 增强企业竞争力:通过确保产品质量的稳定性和一致性,企业可以树立良好的品牌形象,提升市场竞争力。
四、选择方法选择关键工序质量控制点的方法可以根据以下几个方面进行考虑:1. 工序影响程度:选择对产品质量影响较大的工序作为关键工序,并在其中设立质量控制点。
2. 工序稳定性:选择工序稳定性较差的工序作为关键工序,并在其中设立质量控制点以提高工序的稳定性。
3. 工序难度:选择工序难度较大的工序作为关键工序,并在其中设立质量控制点以确保工序的可控性。
4. 工序关联性:选择与其他工序关联性较大的工序作为关键工序,并在其中设立质量控制点以保证整个生产过程的质量稳定性。
五、实施步骤1. 确定关键工序:通过对生产过程进行分析和评估,确定对产品质量影响较大的工序。
2. 确定质量控制点:在关键工序中选择特定位置或者时间点,作为质量控制点。
3. 制定质量控制标准:根据产品质量要求和工序特点,制定相应的质量控制标准。
关键工序质量控制点
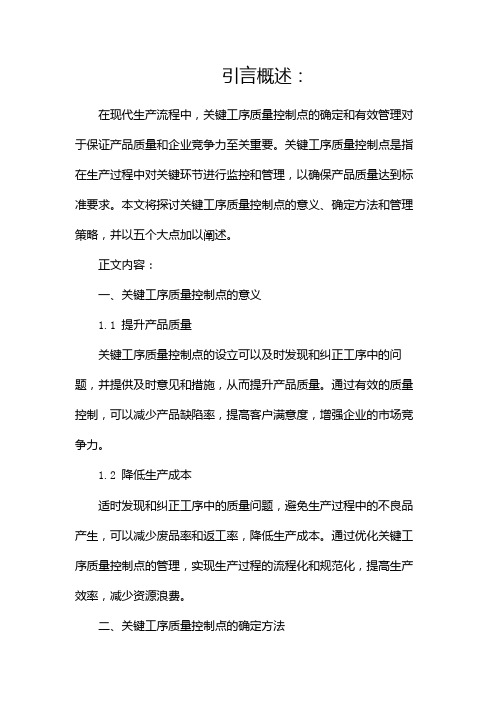
引言概述:在现代生产流程中,关键工序质量控制点的确定和有效管理对于保证产品质量和企业竞争力至关重要。
关键工序质量控制点是指在生产过程中对关键环节进行监控和管理,以确保产品质量达到标准要求。
本文将探讨关键工序质量控制点的意义、确定方法和管理策略,并以五个大点加以阐述。
正文内容:一、关键工序质量控制点的意义1.1 提升产品质量关键工序质量控制点的设立可以及时发现和纠正工序中的问题,并提供及时意见和措施,从而提升产品质量。
通过有效的质量控制,可以减少产品缺陷率,提高客户满意度,增强企业的市场竞争力。
1.2 降低生产成本适时发现和纠正工序中的质量问题,避免生产过程中的不良品产生,可以减少废品率和返工率,降低生产成本。
通过优化关键工序质量控制点的管理,实现生产过程的流程化和规范化,提高生产效率,减少资源浪费。
二、关键工序质量控制点的确定方法2.1 制定工序流程图通过制定详细的工序流程图,包括工序之间的先后顺序和关联关系,以及每个工序所需要的输入和产出物,可以帮助确定关键工序。
2.2 进行风险评估通过风险评估方法,识别工序中的潜在质量风险,并确定可能对产品质量有重要影响的关键工序。
2.3 分析数据和指标通过分析历史数据和指标,了解工序中的变异性和不确定性,并确定对产品质量可能产生显著影响的关键工序。
三、关键工序质量控制点的管理策略3.1 设立监控机制建立合适的监控机制,包括定期检查、过程记录和异常报告等,以确保关键工序在生产过程中得到有效监控和管理。
3.2 培训和技能提升组织相关人员参加培训和技能提升活动,提高其对关键工序质量控制要求的理解和应对能力,确保工序操作的准确性和稳定性。
3.3 制定操作规范制定详细的操作规范,明确工序执行的标准要求和操作步骤,规范工序操作,降低质量风险。
3.4 强调团队合作建立跨部门的合作机制,加强各环节之间的沟通和协作,确保关键工序的信息流通和问题解决。
3.5 持续改进对关键工序进行持续改进,通过引入新的技术和工艺、优化工序流程等方式,提高关键工序的效率和质量。
关键工序质量控制点

关键工序质量控制点一、引言关键工序质量控制点是指在生产过程中,对于影响产品质量的关键工序进行控制和监测的特定点位。
通过对关键工序质量控制点的严格管理,可以确保产品的质量稳定和符合要求。
本文将详细介绍关键工序质量控制点的定义、选择、建立和管理。
二、关键工序质量控制点的定义关键工序质量控制点是指在生产过程中,对于产品质量影响较大,容易引起产品缺陷或者不合格的工序进行重点控制和监测的特定点位。
通过对关键工序质量控制点的监测和控制,可以及时发现和纠正工序中的问题,确保产品质量的稳定和符合要求。
三、关键工序质量控制点的选择选择关键工序质量控制点的过程需要考虑以下因素:1. 工序对产品质量的影响程度:根据工序的重要性和对产品质量的影响程度,确定关键工序质量控制点。
2. 工序的可控性:选择那些能够通过控制和监测手段进行有效控制的工序作为关键工序质量控制点。
3. 工序的稳定性:选择那些工序稳定性较高,不易受外界因素影响的工序作为关键工序质量控制点。
四、关键工序质量控制点的建立建立关键工序质量控制点需要进行以下步骤:1. 确定关键工序:根据产品质量要求和工艺流程,确定哪些工序对产品质量影响较大,需要进行重点控制和监测。
2. 确定控制要点:针对每一个关键工序,确定影响产品质量的关键参数和指标,作为控制要点。
3. 制定控制措施:根据控制要点,制定相应的控制措施,包括工艺参数的设定、操作规程的编制等。
4. 设立监测点位:根据控制要点,确定监测点位的位置和数量,以便及时监测和记录工序的质量数据。
5. 建立记录系统:建立相应的记录系统,记录关键工序的质量数据和控制措施的执行情况。
6. 培训和培养人员:对从事关键工序的人员进行培训和培养,提高其对关键工序质量控制点的认识和操作能力。
五、关键工序质量控制点的管理对关键工序质量控制点进行有效的管理是确保产品质量的关键环节。
以下是关键工序质量控制点管理的要点:1. 定期检查和评估:定期对关键工序质量控制点进行检查和评估,确保其有效性和合理性。
- 1、下载文档前请自行甄别文档内容的完整性,平台不提供额外的编辑、内容补充、找答案等附加服务。
- 2、"仅部分预览"的文档,不可在线预览部分如存在完整性等问题,可反馈申请退款(可完整预览的文档不适用该条件!)。
- 3、如文档侵犯您的权益,请联系客服反馈,我们会尽快为您处理(人工客服工作时间:9:00-18:30)。
板面节点施工要求:
针对现浇混凝土,板面质量和观感要求,确保 该处混凝土密实;同时,重点关注该部位的施工 控制。砼浇捣时采用二次振捣,机械磨平工艺 施工,能控制结构板裂缝及渗漏水缺陷通病。
混凝土结构外形尺 寸偏差--表面不 平整、水泥浆体污
染严重等
1、麻面 : 现象:混凝土表面局部缺浆粗糙,
混凝土麻面、 小气孔。
混凝土麻面 模板未清理铁锈 模板接缝不严等
混凝土结构蜂窝
3、孔洞: 现象:混凝土结构内有空腔,局部
没有混凝土,或蜂窝特别大。 原因:1)在钢筋密集处或预留孔
洞和埋件处,砼浇筑不畅通;2) 未按施顺序和施工工艺认真操 作,产生漏振;3)砼离析,砂 浆分离,石子成堆,或严重跑 浆;4)砼中有泥块、木块等杂 物掺入;5)未按规定下料,一 次下料过多,振捣不到。 预防:1)难于下料的地方,可采 用豆石砼浇筑;2)正确的振捣 严防漏振。3)防止土块或木块 等杂物的掺入;4)选用合理的 下料浇筑顺序;5)加强施工技 术管理和质量检查工作。
8、酥松脱落:
现象:砼结构构件浇筑脱模后,表 面出现酥松、脱落等现象,表 面强度比内部强度低很多。
原因:1)木模板未浇水湿润或润 湿不够;2)炎热刮风天,砼脱 模后,未浇水养护;3)冬期浇 筑砼时,没有采取保温措施。
预防:1)注意以上所分析的原因2) 砼在特殊天气下的施工时,应 制定特殊的施工措施;3)加强 砼的养护及保温工作;4)出现 通病后,制定出处理措施。
或有小凹坑,无钢筋外露。 原因:1)模板表面粗糙或清理不
干净;2)脱模剂涂刷不均匀或 局部漏刷;3)模板接缝拼接不 严,浇筑砼时缝隙漏浆。4)振 捣不密实,砼中的气泡未排出 一部分汽泡停留在模板表面。 预防:1)模板表面清理干净,不 得粘有干硬性水泥等物;2)浇 筑砼前,应用清水湿润模板, 不留积水,严密拼接模板缝隙3) 脱模剂须涂刷均匀,不得漏刷。 4)砼须按操作规程分层均匀振 捣密实,严防漏振,每层砼均 应振捣至汽泡派出为止。
4、缝隙夹层:
现象:施工缝处砼结合不好,有缝隙 或有杂物,造成结构整体性不良
原因:1)浇筑前,未认真处理施 工缝表面;2)捣实不够;3) 浇筑前垃圾未能清理干净。
预防:1)砼浇筑以前,认真清理 模板内的垃圾杂物,并处理好 施工缝表面;2)浇筑过程中, 要振捣密实;同时防止木块等 杂物掉入砼中。3)冬期施工时 要制定冬期施工预防措施,防 止冰雪的夹层。
混凝土松顶
混凝土松顶 蜂窝、孔洞
1、塑性收缩裂缝 : 现象:在结构表面出现形状不规则
长短不一,互不连贯,类似干 燥的泥浆面。大多在砼浇筑初 期(浇筑后4h左右),当砼本 身与外界气温相差悬殊,或本 身温度长时间过高(400以上) 而气候很干燥的情况下出现。 塑性裂缝又称龟裂,严格讲属 于干缩裂缝,出现很普遍。 原因:1)砼浇筑后,表面没有及 时覆盖,受风吹日晒,表面游 离水分蒸发过快,产生急剧的 体积收缩,而此时混凝土早期 强度低,不能抵抗这种变形应 力而导致开裂。 2)使用收缩率 较大的水泥,水泥用量过多
预防:1)依据施工措施进行施工2)支设的模板 要有足够的刚度及强度;3)复核施工放线;4) 砼浇筑时,要有一定的顺序
两个节点施工说明:
由于商品砼坍落度大,在进行地下室底板或顶板翻边部位施 工时,振动棒振捣使砼流座到底板,施工人员往往少振或不 振捣,导致砼不密实,因此形成渗漏薄弱点。
针对大面积车库底板、顶板、平屋面、所有现浇板因商品砼 坍落度大而产生的毛孔及收缩裂缝,导致结构渗漏水现象。
混凝土缝隙夹层
5、却棱掉角: 现象:梁柱板墙和洞口直角处砼局
部掉落,不规整,棱角有缺陷 原因:1)砼浇筑前木模板未湿润
或湿润不够;2)砼养护不好; 3)过早拆除侧面非承重模板; 4)拆模时外力作用或重物撞击, 或保护不好,棱角被碰掉 预防:1)木模板在浇筑砼前应充 分湿润,砼浇筑后应认真浇水 养护;2)拆除侧面非承重模板 时,砼应具有足够的强度;3) 拆模时不能用力过猛过急。注 意保护棱角;吊运时,严禁模 板撞击棱角;4)加强成品保护
2、蜂窝: 现象:混凝土局部酥松,砂浆少,
石子多,石子间出现空隙,形 成蜂窝状的孔洞。 原因:1)混凝土配合比不准确或 骨料计量错误;2)混凝土搅拌 时间短,没有拌合均匀,混凝 土和易性差,振捣不密实;3) 浇筑砼时,下料不当或一次下 料过多,没有分段分层浇筑, 造成混凝土漏振、离析;4)模 板孔隙未堵好,或模板支设不 牢固,模板移位,造成严重漏 浆或墙体烂根。 预防:根据以上分析原因,结合有 关规程规范,进行有效的预防
混凝土缺棱掉角 --棱角不分明、
不工整
混凝土孔洞露筋
混凝土孔洞露 筋、缺棱掉角
7、松顶: 现象:砼柱、墙、基础浇筑后,在
距定面50~100mm高度内出现 粗糙、松散,有明显的颜色变 化,内部呈多孔性,基本上时 砂浆,无石子分布其中,强度 低,影响结构的受力性能和耐 久性,经不起外力冲击和磨损 原因:1)砼配合比不当;2)振捣 时间过长,造成离析;3)砼的 沁水没有排除。 预防:1)设计砼配合比,水灰比 不能过大,以减少沁水性及良 好的保水性;2)掺加加气剂或 减水剂;3)控制振捣时间;4) 采用真空吸水工艺等。
节点施工要求:
针对现浇混凝土,要求其坍落度达到3-5cm时,再进行砼二 次振捣,确保该处混凝土密实;同时,重点关注该部位的施工 控制。砼浇捣时采用二次振捣,机械磨平工艺施工,能控制 结构板裂缝及渗漏水缺陷通病。
注意:坍落度小于3㎝时,禁止二次振捣。
施工控制节点——地下室外墙
施工控制节点——墙柱根部
关键工序质量控制
南通华新建工第二工程有限公司
体会总结如下:
1、混凝土工程 2、砌体工程 3、抹灰整、结构位移或倾斜、 凹凸或膨胀等
原因:1)砼浇筑后没有找平压光2)砼没有达到 强度就上人操作或运料;3)模板支设不牢固, 支撑结构差;4)放线误差较大5)砼浇筑顺序 不对,致使模板发生偏移等。
6、露筋:
现象:钢筋砼结构内部的主筋、副 筋或箍筋等裸露在砼表面。
原因:1)浇筑砼时,垫块发生位 移或数量太少;2)结构构件截 面小,钢筋过密;3)砼配合比 不当,产生离析;4)保护层小 或该处砼漏振;5)木模板在砼 浇筑前未浇水湿润,吸水粘结
预防:1)浇筑砼前,认真检查, 保证钢筋位置及保护层厚度;2) 钢筋密集时,选用适当粒径的 石子;3)浇水润湿木模板。