关键工序控制程序
中联重科关键工序特殊过程控制程序

中联重科关键工序特殊过程控制程序中联重科是国内最大的工程机械制造企业之一,其生产线涉及多个领域和环节,其中关键工序的特殊过程控制非常重要。
这些过程控制程序是为了确保产品质量和生产效率而设计的,下面我们来详细了解一下。
首先是钢材的挑选和处理过程。
中联重科的工程机械使用了大量的钢材材料,而钢材的品质对机械的性能和寿命有着至关重要的影响。
因此,在生产流程中,钢材必须经过精细的挑选和处理,包括材质检测、表面处理、热处理等,在这些过程中,不仅要采用科学的工艺和设备,还要有经验丰富的操作人员,以确保钢材的质量符合标准要求。
其次是焊接工艺的控制。
工程机械在使用中可能会受到强烈的振动和冲击,因此在生产中采用了大量的焊接工艺,这些工艺的控制对产品的安全性和使用寿命有着非常重要的影响。
为了保证焊接接头的质量,中联重科采用了多项措施,包括材料的精细挑选、焊接工艺的优化和严格的检测程序等。
此外,机身的精加工也是关键工序之一。
工程机械的机身精加工需要高精度的设备和技术手段,而中联重科的机身加工流程则采用了数控加工、光电检测等高端技术和设备,以确保机身精度达到最高水平。
最后是整机测试的过程控制。
工程机械是一种大型复杂的设备,其各个部件之间的协调性和整机配合性是整体性能的关键。
为了确保整机的品质和用户的安全,中联重科的工程机械在生产流程中采用了一系列的测试程序,包括机体检查、功能测试、耐久性测试等多项内容,确保产品质量达到标准要求。
总之,中联重科的关键工序特殊过程控制程序是由一整套的措施和流程构成的,这些程序旨在确保产品质量和生产效率。
在实际生产中,我们需要采用科学的方法和严格的流程控制来规范化和优化工艺流程,提高产品质量和用户的体验感。
TS22163特殊关键工序控制程序

文件制修订记录1.0目的对车辆产品生产中关键特殊过程的确认、控制措施及责任分工做出规定,以确保特殊过程持续满足工艺要求。
2.0适用范围本程序适用于公司车辆生产中特殊关键过程的确认及控制。
3.0术语和定义3.1特殊过程:生产和服务过程的输出不能、不易或不能经济地由后续的监视和测量加以验证的过程;3.2关键工序:a.对产品的功能、性能、安全和可靠性有直接影响的生产工序;b.加工精度高、难度大、工艺复杂的工序。
4.0职责4.1质量部负责监督关键工序、特殊过程工艺执行情况;参与关键工序、特殊过程确认。
4.2技术部4.2.1关键工序、特殊过程的识别、确定4.2.2提出关键工序、特殊过程管理要求4.2.3组织关键工序、特殊过程的监控、确认。
4.3设备部提供满足产品生产要求的设备及工作环境,并进行监控;参与关键工序、特殊过程确认。
4.4供应部负责特殊关键过程原材料的控制与管理;参与关键工序、特殊过程确认。
4.5人事部负责特殊过程的人员培训、确认、授权的归口管理;参与关键工序、特殊过程确认。
4.6生产车间4.6.1贯彻实施工艺要求;4.6.2对关键工序、特殊过程工艺纪律执行情况进行检查、监督;4.6.3对新上岗或换岗的人员进行资格确认;对关键工序、特殊过程进行连续监控,填写和保存过程监控记录。
5.0控制程序5.1轨道车辆产品生产的特殊过程有:5.1.1 焊接过程;5.1.2 涂装过程;5.1.3 粘接过程;5.1.4 电线(缆)压接过程;5.2特殊关键过程的控制措施5.2.1 技术部识别生产过程中的特殊过程明确关键工序控制的质量特性、工艺参数,明确关键工序、特殊过程所需的设备、工装、检测器具、过程参数监控要求、工艺方法、环境要求、人员资格及记录要求,经技术部分管领导审核,副总工程师批准后,以技术文件的形式下发,实行动态管理。
5.2.2 技术部牵头组织特殊关键过程能力评定,人事部、设备部、质量部以及生产车间参加;5.2.3 特殊关键过程的操作、检验人员须具备资质,并经授权后持证上岗。
关键工序管理程序
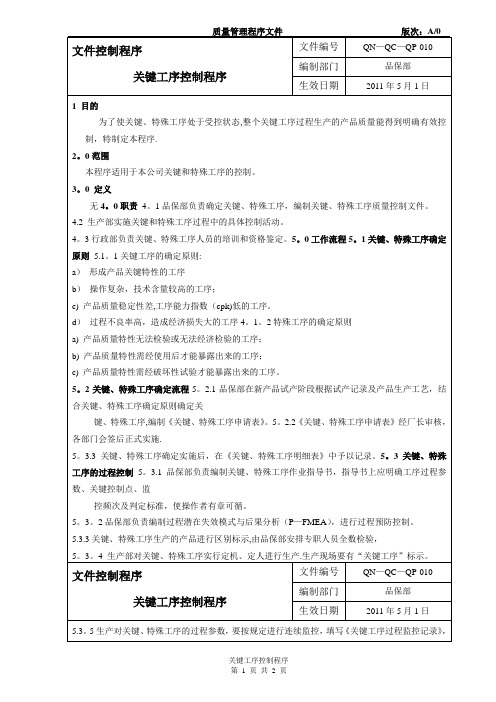
关键工序控制程序
文件编号
QN—QC—QP-010
编制部门
品保部
生效日期
2011年5月1日
1目的
为了使关键、特殊工序处于受控状态,整个关键工序过程生产的产品质量能得到明确有效控制,特制定本程序.
2。0范围
本程序适用于本公司关键和特殊工序的控制。
3。0定义
无4。0职责4。1品保部负责确定关键、特殊工序,编制关键、特殊工序质量控制文件。
出现过程参数异常时应立即停机,并将异常情况报相关部门,协同分析处理。
5。4关键、特殊工序的设备及人员认可5。4。1关键、特殊工序设备的认可
5。4。1。1生产部组织对新购关键、特殊工序的设备进行认可,具体的认可办法按照《设备及设施管理
程序》执行。
5.4.1.2关键、特殊工序设备的点检,具体执行《设备及设施管理程序》。
5。4。2关键、特殊工序操作人员认可
5。4。2.1关键、特殊工序操作人员上岗前需经培训、考核,并取得上岗资格才能持证上岗。具体执行
《人力资源序》
6。2《人力资源管理程序》。
6。3关键特殊工序明细表
6。4过程监控记录
4.2生产部实施关键和特殊工序过程中的具体控制活动。
4。3行政部负责关键、特殊工序人员的培训和资格鉴定。5。0工作流程5。1关键、特殊工序确定原则5.1。1关键工序的确定原则:
a)形成产品关键特性的工序
b)操作复杂,技术含量较高的工序;
c)产品质量稳定性差,工序能力指数(cpk)低的工序。
d)过程不良率高,造成经济损失大的工序4。1。2特殊工序的确定原则
5.3.3关键、特殊工序生产的产品进行区别标示,由品保部安排专职人员全数检验,
5。3。4生产部对关键、特殊工序实行定机、定人进行生产.生产现场要有“关键工序”标示。
CTQ关键工序控制程序

CTQ管理控制程序1 目的为规范本公司CTQ相关作业的管理,保证产品关键特性满足客户要求,降低不良率,特制定本程序。
2 范围适用于本公司内部的CTQ管理项目,以及CTQ管理出现异常的分析,改善及完善相关活动。
3 定义3.1 CTQ定义:Critical-To-Quality)的意思是质量关键特性点,是指为了满足“关键的需求或关键客户流程需求的产品或服务的一组特征,它是从顾客角度出发,影响顾客满意度的质量特性。
”4 权责本规程由品管部、生产部,技术装备部负责实施,其他部门共同遵守。
5 工作程序5.1 CTQ管理项目的选定:对顾客指定的关键特性,作为优先管理。
对影响产品品质的重要工序的特性和工程特性也作相应管理。
5.2 CTQ关键特性管理图的选定根据产品特性及管理需要,公司选用SPC控制均值-极差控制图.产品名称CTQ特性管理标准测定周期曲轴粗加工吸油管孔直径Φ11—Φ11.03 天/次曲轴精加工长轴圆度0.0015 5pcs/2小时/机长轴靠近支撑面圆度0.0025 5pcs/2小时/机长轴外圆粗糙度Ra0.30 5pcs/2小时/机偏心轴圆度0.0015 5pcs/2小时/机偏心轴表面粗糙度Ra0.20 5pcs/2小时/机长轴直径13.988±0.0035pcs/小时/机偏心轴直径13.980±0.0035pcs/小时/机5.3 CTQ工程能力的调查周期及管理项目.在稳定的生产过程中,要求CTQ工程每月测定1 批, 32件/批。
计算CPK过程能力指数,并通过连续的观察,找到潜在的能力不足设备进行改善。
5.4 CTQ工程能力的计算及评价:对于CTQ关键工序,品管部根据程序测定对应的品质特性数据并进行记录,计算出CPK.等级Cpk 判断工程能力的有无措施A Cpk≥1.67 工程能力很充分可维持现状,或想办法减少成本等B 1.33≤Cpk<1.67 工程能力充分是理想状态,维持现状即可.C 1.00≤Cpk<1.33 工程能力不是很充分可考虑采取必要的措施以达到理想状态D 0.67≤Cpk<1.00 工程能力不足. 有必要工程的管理及改善.E Cpk<0.67 工程能力很不足离品质理想状态远. 需进行品质改善,追究原因,做紧急对策●品管部对输入的数据进行收集,须每个月进行工程能力分析,检讨。
质量管理过程中的关键工序控制
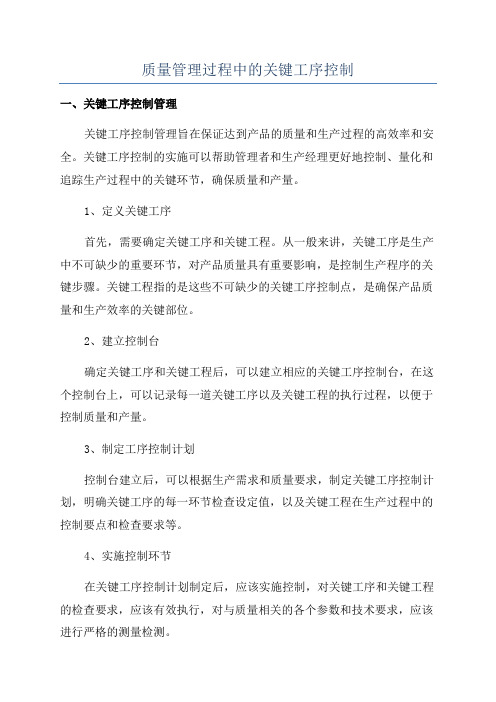
质量管理过程中的关键工序控制
一、关键工序控制管理
关键工序控制管理旨在保证达到产品的质量和生产过程的高效率和安全。
关键工序控制的实施可以帮助管理者和生产经理更好地控制、量化和追踪生产过程中的关键环节,确保质量和产量。
1、定义关键工序
首先,需要确定关键工序和关键工程。
从一般来讲,关键工序是生产中不可缺少的重要环节,对产品质量具有重要影响,是控制生产程序的关键步骤。
关键工程指的是这些不可缺少的关键工序控制点,是确保产品质量和生产效率的关键部位。
2、建立控制台
确定关键工序和关键工程后,可以建立相应的关键工序控制台,在这个控制台上,可以记录每一道关键工序以及关键工程的执行过程,以便于控制质量和产量。
3、制定工序控制计划
控制台建立后,可以根据生产需求和质量要求,制定关键工序控制计划,明确关键工序的每一环节检查设定值,以及关键工程在生产过程中的控制要点和检查要求等。
4、实施控制环节
在关键工序控制计划制定后,应该实施控制,对关键工序和关键工程的检查要求,应该有效执行,对与质量相关的各个参数和技术要求,应该进行严格的测量检测。
关键工序控制程序
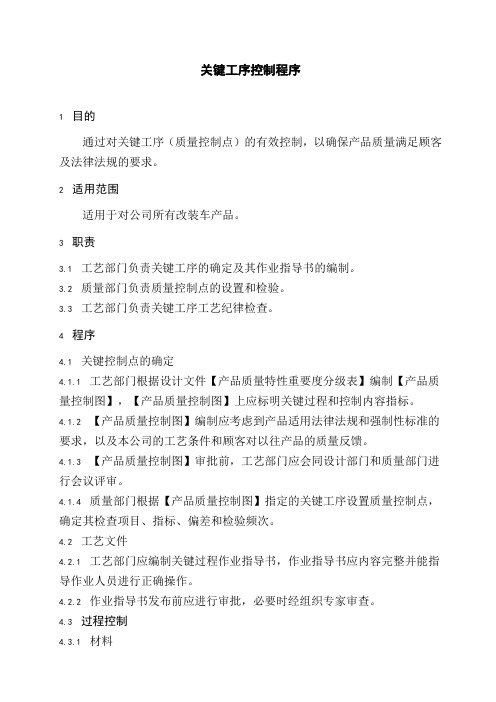
关键工序控制程序1 目的通过对关键工序(质量控制点)的有效控制,以确保产品质量满足顾客及法律法规的要求。
2 适用范围适用于对公司所有改装车产品。
3 职责3.1 工艺部门负责关键工序的确定及其作业指导书的编制。
3.2 质量部门负责质量控制点的设置和检验。
3.3 工艺部门负责关键工序工艺纪律检查。
4 程序4.1 关键控制点的确定4.1.1 工艺部门根据设计文件【产品质量特性重要度分级表】编制【产品质量控制图】,【产品质量控制图】上应标明关键过程和控制内容指标。
4.1.2 【产品质量控制图】编制应考虑到产品适用法律法规和强制性标准的要求,以及本公司的工艺条件和顾客对以往产品的质量反馈。
4.1.3 【产品质量控制图】审批前,工艺部门应会同设计部门和质量部门进行会议评审。
4.1.4 质量部门根据【产品质量控制图】指定的关键工序设置质量控制点,确定其检查项目、指标、偏差和检验频次。
4.2 工艺文件4.2.1 工艺部门应编制关键过程作业指导书,作业指导书应内容完整并能指导作业人员进行正确操作。
4.2.2 作业指导书发布前应进行审批,必要时经组织专家审查。
4.3 过程控制4.3.1 材料关键工序所用原辅材料、配件和半成品应经质量部门检验接收,流入本工序加工前操作人员应予复验,确保其适用性。
复验发现不适用及时标识并通知检验人员。
4.3.2 设备设备管理部门根据工艺要求,配置适宜的设备,确保其精度和加工能力;制造工程部根据工艺要求制造工艺工装。
设备管理部门应编制设备工装安全操作规程、检修计划和维护保养细则。
操作人员按【设备维护保养细则】的要求,对设备工装进行日常维护保养。
设备维修人员应【设备年度检修计划】的要求,对设备工装的功能、精度和安全防护进行周期检修。
4.3.3 人员操作人员应经过培训、考核合格;法律法规对岗位有要求的按其要求执行。
操作人员应能看懂设计文件、工艺文件,应能正确操作设备工装,应知晓质量控制点验收标准。
关键工序控制程序
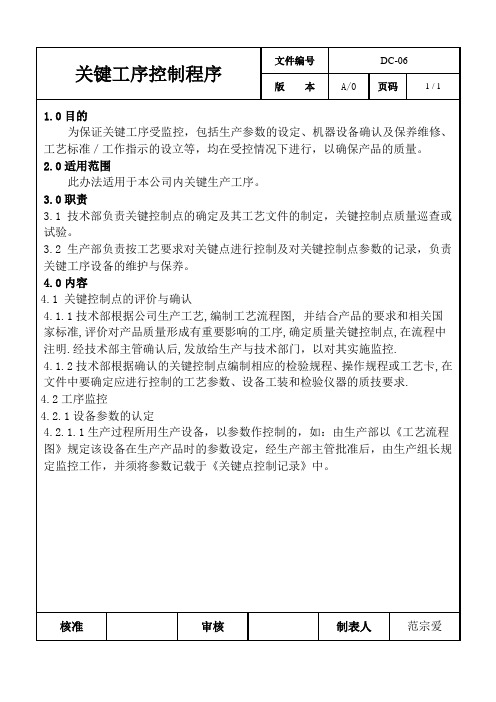
4.2工序监控
4.2.1设备参数的认定
4.2.1.1生产过程所用生产设备,以参数作控制的,如:由生产部以《工艺流程图》规定该设备在生产产品时的参数设定,经生产部主管批准后,由生产组长规定监控工作,并须将参数记载于《关键点控制记录》中。
定期对使用中的设备进行维护和保养,以保持其运行能力,且保存设备维修以及保养记录,具体操作按《设备管理规定》执行。
核准
审核
制表人
核准
审核
制表人
范宗爱
关键工序控制程序
文件编号
DC-07
版本
A-0
页码
2 / 3
核准
审核
制表人
关键工序控制程序
文件编号
DC-7
版本
A-0
页码
3 / 3
熔融加热℃.
焊接加热温度与加热时间的经验调整法建议采用软规范(即加热时
间升高,加热温度降低),具体调整方法是将加热时间确定,将加热温度自低温向高温调整,每焊一次将刚焊后的窗角掰开,观察焊接渣口情况,当渣口刚刚泛黄时,将温度下调5℃即可;
关键工序控制程序
文件编号
DC-06
版本
A/0
页码
1 / 1
1.0目的
为保证关键工序受监控,包括生产参数的设定、机器设备确认及保养维修、工艺标准/工作指示的设立等,均在受控情况下进行,以确保产品的质量。
2.0适用范围
此办法适用于本公司内关键生产工序。
3.0职责
3.1技术部负责关键控制点的确定及其工艺文件的制定,关键控制点质量巡查或试验。
关键工序控制程序
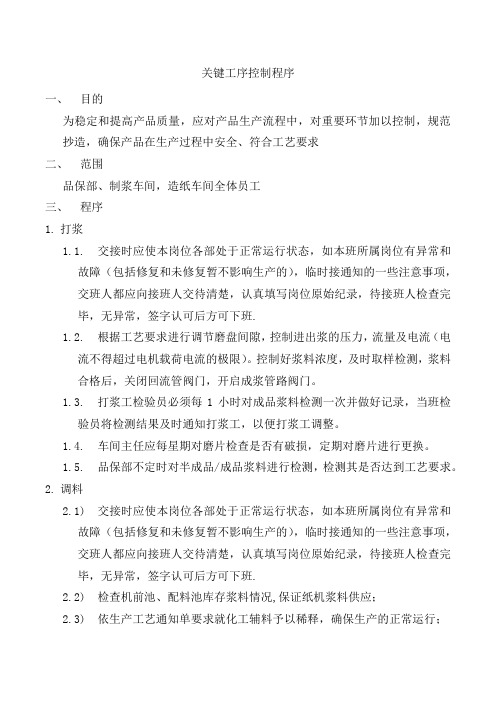
关键工序控制程序一、目的为稳定和提高产品质量,应对产品生产流程中,对重要环节加以控制,规范抄造,确保产品在生产过程中安全、符合工艺要求二、范围品保部、制浆车间,造纸车间全体员工三、程序1.打浆1.1.交接时应使本岗位各部处于正常运行状态,如本班所属岗位有异常和故障(包括修复和未修复暂不影响生产的),临时接通知的一些注意事项,交班人都应向接班人交待清楚,认真填写岗位原始纪录,待接班人检查完毕,无异常,签字认可后方可下班.1.2.根据工艺要求进行调节磨盘间隙,控制进出浆的压力,流量及电流(电流不得超过电机载荷电流的极限)。
控制好浆料浓度,及时取样检测,浆料合格后,关闭回流管阀门,开启成浆管路阀门。
1.3.打浆工检验员必须每1小时对成品浆料检测一次并做好记录,当班检验员将检测结果及时通知打浆工,以便打浆工调整。
1.4.车间主任应每星期对磨片检查是否有破损,定期对磨片进行更换。
1.5.品保部不定时对半成品/成品浆料进行检测,检测其是否达到工艺要求。
2.调料2.1)交接时应使本岗位各部处于正常运行状态,如本班所属岗位有异常和故障(包括修复和未修复暂不影响生产的),临时接通知的一些注意事项,交班人都应向接班人交待清楚,认真填写岗位原始纪录,待接班人检查完毕,无异常,签字认可后方可下班.2.2)检查机前池、配料池库存浆料情况,保证纸机浆料供应;2.3)依生产工艺通知单要求就化工辅料予以稀释,确保生产的正常运行;2.4)根据纸机的开停来控制好单圆网的运行于停止,并调节好浆位;2.5)配料工检验员每缸浆必须检测PH值一次并做好记录;2.6)化工原料在稀释前必须过滤。
化工桶每班必须清洗一次。
2.7)每隔1个小时:检查连续添加化工辅料贮存桶的剩余贮存量,及时按照化工辅料添加浓度稀释待用;2.8)检查计量泵、圆网浓缩机的使用情况,有异常时应及时处理或通知班长。
2.9)每隔2个小时:检查配浆池,抄造池,损纸池各浆池贮浆情况,及时按照生产工艺通知单要求进行配浆;2.10)品保部、车间负责人不定时对车间进行抽检已确保其指标符合要求;3.抄造3.1)交接时应使本岗位各部处于正常运行状态,如本班所属岗位有异常和故障(包括修复和未修复暂不影响生产的),临时接通知的一些注意事项,交班人都应向接班人交待清楚,认真填写岗位原始纪录,待接班人检查完毕,无异常,签字认可后方可下班.3.2)检查各压区的压力和烘缸的进汽压力是否按照工艺要求执行。
- 1、下载文档前请自行甄别文档内容的完整性,平台不提供额外的编辑、内容补充、找答案等附加服务。
- 2、"仅部分预览"的文档,不可在线预览部分如存在完整性等问题,可反馈申请退款(可完整预览的文档不适用该条件!)。
- 3、如文档侵犯您的权益,请联系客服反馈,我们会尽快为您处理(人工客服工作时间:9:00-18:30)。
关键工序控制程序
1 目的
通过对关键工序(质量控制点)的有效控制,以确保产品质量满足顾客及法律法规的要求。
2 适用范围
适用于对公司所有改装车产品。
3 职责
3.1 工艺部门负责关键工序的确定及其作业指导书的编制。
3.2 质量部门负责质量控制点的设置和检验。
3.3 工艺部门负责关键工序工艺纪律检查。
4 程序
4.1 关键控制点的确定
4.1.1 工艺部门根据设计文件【产品质量特性重要度分级表】编制【产品质量控制图】,【产品质量控制图】上应标明关键过程和控制内容指标。
4.1.2 【产品质量控制图】编制应考虑到产品适用法律法规和强制性标准的要求,以及本公司的工艺条件和顾客对以往产品的质量反馈。
4.1.3 【产品质量控制图】审批前,工艺部门应会同设计部门和质量部门进行会议评审。
4.1.4 质量部门根据【产品质量控制图】指定的关键工序设置质量控制点,确定其检查项目、指标、偏差和检验频次。
4.2 工艺文件
4.2.1 工艺部门应编制关键过程作业指导书,作业指导书应内容完整并能指导作业人员进行正确操作。
4.2.2 作业指导书发布前应进行审批,必要时经组织专家审查。
4.3 过程控制
4.3.1 材料
关键工序所用原辅材料、配件和半成品应经质量部门检验接收,流入本工序加工前操作人员应予复验,确保其适用性。
复验发现不适用及时标识并通知检验人员。
4.3.2 设备
设备管理部门根据工艺要求,配置适宜的设备,确保其精度和加工能力;制造工程部根据工艺要求制造工艺工装。
设备管理部门应编制设备工装安全操作规程、检修计划和维护保养细则。
操作人员按【设备维护保养细则】的要求,对设备工装进行日常维护保养。
设备维修人员应【设备年度检修计划】的要求,对设备工装的功能、精度和安全防护进行周期检修。
4.3.3 人员
操作人员应经过培训、考核合格;法律法规对岗位有要求的按其要求执行。
操作人员应能看懂设计文件、工艺文件,应能正确操作设备工装,应知晓质量控制点验收标准。
人力资源部负责操作人员培训和考核。
4.3.4 环境
制造部门应按工艺要求创造适宜工作环境并适时维护,保障产品质量和人身安全。
4.3.5 检验
关键工序采用首检、自检、专检,检验结果记入《质量控制点检验记录卡》。
发现工序异常及时通知车间及质量部门。
对产品质量特性形成的装配过程应形成质量记录,填写《装配质量特性检验记录卡》。
4.4 监督检查
由工艺部门组织相关人员定期对关键工序进行工艺纪律检查,对影响工序质量因素(人、机、料、法、环)日常监督,发现异常签发《工序异常通知单》,督促责任部门及时纠正,以维持工序质量。
5 质量记录
5.1 《质量控制点检验记录卡》5.2 《工序异常通知单》
5.3 《装配质量特性检验记录卡》。