测量齿圈径向跳动的各种方法讲解
齿轮跳动测量
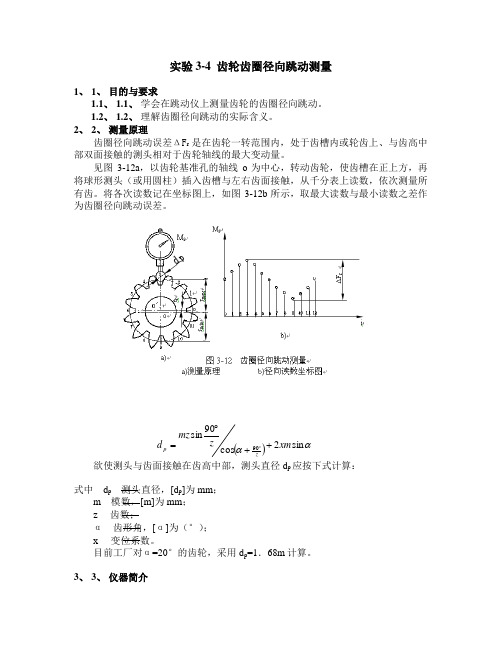
实验3-4 齿轮齿圈径向跳动测量1、 1、 目的与要求1.1、 1.1、 学会在跳动仪上测量齿轮的齿圈径向跳动。
1.2、 1.2、 理解齿圈径向跳动的实际含义。
2、 2、 测量原理齿圈径向跳动误差ΔF r 是在齿轮一转范围内,处于齿槽内或轮齿上、与齿高中部双面接触的测头相对于齿轮轴线的最大变动量。
见图3-12a ,以齿轮基准孔的轴线o 为中心,转动齿轮,使齿槽在正上方,再将球形测头(或用圆柱)插入齿槽与左右齿面接触,从千分表上读数,依次测量所有齿。
将各次读数记在坐标图上,如图3-12b 所示,取最大读数与最小读数之差作为齿圈径向跳动误差。
欲使测头与齿面接触在齿高中部,测头直径d p 应按下式计算:式中 d p 测头直径,[d p ]为mm ;m 模数,为mm ;z 齿数; α 齿形角,[α]为(°);x 变位系数。
目前工厂对α=20°的齿轮,采用d p =1.68m 计算。
3、 3、 仪器简介 ()ααsin 2cos 90sin90xm z mz d z p ++︒=︒测量齿圈径向跳动可用跳动检查仪,也可用万能测齿仪等具有顶针架的仪器。
图3-13为跳动检查仪。
被测齿轮与心轴一起顶在左右顶针之间,两顶针架装在滑板上。
转动手轮1,可使滑板及其上支承载物一道左右移动。
其座后螺旋立柱上套有表架,千分表7可装在表架前夹头8的孔中,并靠螺钉夹紧。
扳动拨杆6可使千分表放下进入齿槽或抬起退出齿槽。
图3-13 跳动检查仪1-手轮 2、3-螺钉 4-螺母 5-可转测量架 6-拨杆 7-千分 8-夹头 9-顶针跳动检查仪的测量范围:可测工件的最大直径为150mm (小型)或300mm (大型),两顶尖间的最大距离为150mm (小型)或418mm (大型);千分表的分度值i=0.001mm ;示值范围为1mm 。
仪器附有不同直径的球形测头,用于测量各种模数的齿轮。
附有各种杠杆,用于测量锥齿轮和内齿轮的齿圈跳动。
齿轮齿圈径向跳动的测量实验报告
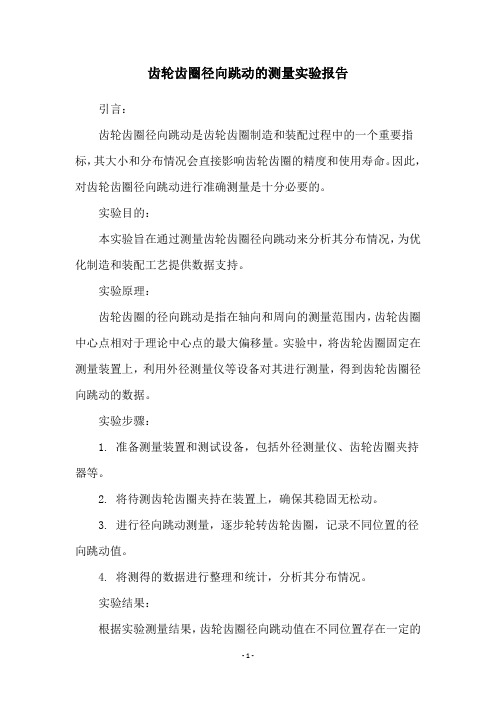
齿轮齿圈径向跳动的测量实验报告
引言:
齿轮齿圈径向跳动是齿轮齿圈制造和装配过程中的一个重要指标,其大小和分布情况会直接影响齿轮齿圈的精度和使用寿命。
因此,对齿轮齿圈径向跳动进行准确测量是十分必要的。
实验目的:
本实验旨在通过测量齿轮齿圈径向跳动来分析其分布情况,为优化制造和装配工艺提供数据支持。
实验原理:
齿轮齿圈的径向跳动是指在轴向和周向的测量范围内,齿轮齿圈中心点相对于理论中心点的最大偏移量。
实验中,将齿轮齿圈固定在测量装置上,利用外径测量仪等设备对其进行测量,得到齿轮齿圈径向跳动的数据。
实验步骤:
1. 准备测量装置和测试设备,包括外径测量仪、齿轮齿圈夹持器等。
2. 将待测齿轮齿圈夹持在装置上,确保其稳固无松动。
3. 进行径向跳动测量,逐步轮转齿轮齿圈,记录不同位置的径向跳动值。
4. 将测得的数据进行整理和统计,分析其分布情况。
实验结果:
根据实验测量结果,齿轮齿圈径向跳动值在不同位置存在一定的
差异,但总体来说,跳动值分布较为均匀,未出现明显的异常情况。
结论:
通过对齿轮齿圈径向跳动的测量和分析,可以得出其分布情况较为均匀的结论。
这对于制造和装配工艺的优化提供了较为实际的参考意义。
同时,实验中使用的测量方法和设备也可为相关领域的研究和开发提供依据。
齿圈径向跳动实验报告
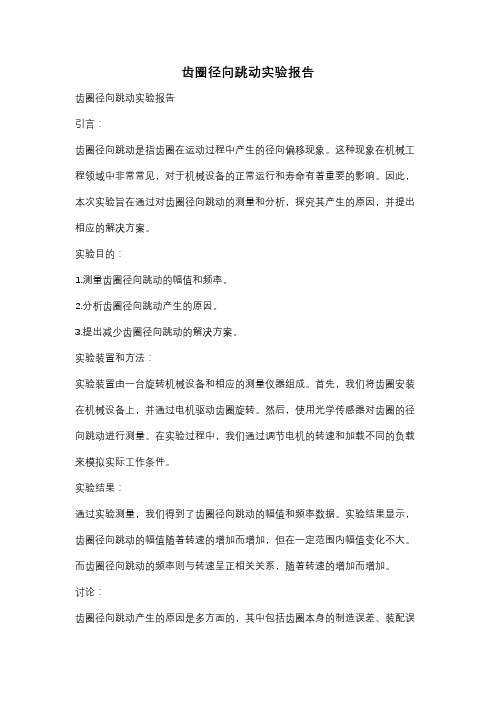
齿圈径向跳动实验报告齿圈径向跳动实验报告引言:齿圈径向跳动是指齿圈在运动过程中产生的径向偏移现象。
这种现象在机械工程领域中非常常见,对于机械设备的正常运行和寿命有着重要的影响。
因此,本次实验旨在通过对齿圈径向跳动的测量和分析,探究其产生的原因,并提出相应的解决方案。
实验目的:1.测量齿圈径向跳动的幅值和频率。
2.分析齿圈径向跳动产生的原因。
3.提出减少齿圈径向跳动的解决方案。
实验装置和方法:实验装置由一台旋转机械设备和相应的测量仪器组成。
首先,我们将齿圈安装在机械设备上,并通过电机驱动齿圈旋转。
然后,使用光学传感器对齿圈的径向跳动进行测量。
在实验过程中,我们通过调节电机的转速和加载不同的负载来模拟实际工作条件。
实验结果:通过实验测量,我们得到了齿圈径向跳动的幅值和频率数据。
实验结果显示,齿圈径向跳动的幅值随着转速的增加而增加,但在一定范围内幅值变化不大。
而齿圈径向跳动的频率则与转速呈正相关关系,随着转速的增加而增加。
讨论:齿圈径向跳动产生的原因是多方面的,其中包括齿圈本身的制造误差、装配误差、工作负载不均匀等。
首先,齿圈的制造误差会导致齿圈的几何形状不规则,从而引起径向跳动。
其次,装配误差会使得齿圈与其他部件之间的配合不完美,进一步增加了径向跳动的可能性。
最后,工作负载不均匀会使得齿圈在运动过程中承受不均匀的力,从而引起径向跳动。
解决方案:针对齿圈径向跳动问题,我们可以采取以下几种解决方案。
首先,优化齿圈的制造工艺,减少制造误差,提高齿圈的几何精度。
其次,加强装配过程的控制,确保齿圈与其他部件之间的配合精度。
最后,通过合理设计工作负载分布,减少齿圈受力不均匀的情况,从而降低径向跳动的发生。
结论:通过本次实验,我们对齿圈径向跳动进行了测量和分析,并提出了相应的解决方案。
齿圈径向跳动是机械工程领域中一个重要的问题,对于机械设备的正常运行和寿命有着重要的影响。
通过优化制造工艺、加强装配过程的控制以及合理设计工作负载分布,我们可以有效地减少齿圈径向跳动的发生,提高机械设备的工作效率和寿命。
径向跳动的介绍及其测量方法

---专业提供 SPC 数据分析软件等机械测量解决方案
员该零件不符合生产规格要求, 需要进一步去完善,这就可以进一步提高测量效 率。
以上是对径向跳动的定义以及测量方法等内容进行了详细的介绍, 在上文提到的 径向跳动的两种测量方法中, 其中利用我们的数据分析仪来直接连接百分表是目 前提高径向跳动检测效率的一种新方法, 不但可以减少由于人工操作所造成的误 差,还可以大大提高检测效率,可以真正实现机械加工测量的数字化。如需更深 入了解这方面的应用, 可直接与我们的工作人员联系,我们将非常乐意为您解答 您所提出的问题!
---专业提供 SPC 数据分析软件等机械测量解决方案
2) 开始测量, 转到零件一周, 数据分析仪会自动采集仪读取测量的最大最小值, 多测量几个位置。 3)数据处理:数据采集仪软件里已嵌入计算径向跳动误差的公式在里面,数据 分析仪会自动计算跳动误差值,无需人工去计算跳动误差值。 4)分析结果:数据采集仪会自动根据所测得的跳动误差值,以轴类零件规定的 跳动公差值进行比较, 一旦跳动误差值大于跳动公差值, 则系统会自动报警, 表示该轴类零件测量结果不合格。 5)测量完成后将工件拿下,收好偏摆仪百分表以及数据采集仪,清除在偏摆仪 上留下的污量径向跳动的优势: 1)无需人工用肉眼去读数,可以减少由于人工读数产生的误差; 说明:由于测量径向跳动时,需要测量到最大值跟最小值,最后的径向跳动 值为 Fr = rmax - rmin , 但是如果由人工去读数时, 很难直接判断出哪次是最大值, 哪次是最小值,这就需要多次去测量去判断,这样就很容易判断错误,而且当一 台偏摆仪一次性连接几个百分表来同时测量时,那工作量会更大,更容易出错。 直接利用数据采集仪连接百分表,采集仪就会自动读取测量的最大值跟最小值, 完全不需要人工去操作。
齿轮径向跳动的测量实验报告
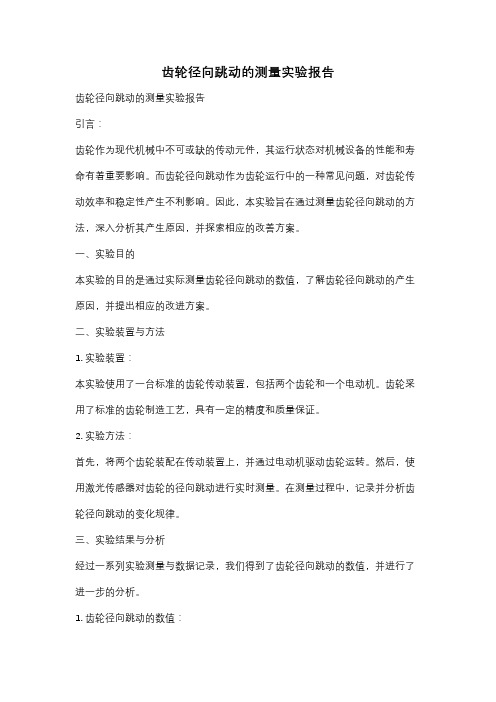
齿轮径向跳动的测量实验报告齿轮径向跳动的测量实验报告引言:齿轮作为现代机械中不可或缺的传动元件,其运行状态对机械设备的性能和寿命有着重要影响。
而齿轮径向跳动作为齿轮运行中的一种常见问题,对齿轮传动效率和稳定性产生不利影响。
因此,本实验旨在通过测量齿轮径向跳动的方法,深入分析其产生原因,并探索相应的改善方案。
一、实验目的本实验的目的是通过实际测量齿轮径向跳动的数值,了解齿轮径向跳动的产生原因,并提出相应的改进方案。
二、实验装置与方法1. 实验装置:本实验使用了一台标准的齿轮传动装置,包括两个齿轮和一个电动机。
齿轮采用了标准的齿轮制造工艺,具有一定的精度和质量保证。
2. 实验方法:首先,将两个齿轮装配在传动装置上,并通过电动机驱动齿轮运转。
然后,使用激光传感器对齿轮的径向跳动进行实时测量。
在测量过程中,记录并分析齿轮径向跳动的变化规律。
三、实验结果与分析经过一系列实验测量与数据记录,我们得到了齿轮径向跳动的数值,并进行了进一步的分析。
1. 齿轮径向跳动的数值:实验结果显示,齿轮径向跳动的数值在不同工况下有所差异。
在正常运行状态下,齿轮径向跳动的数值较小,通常在0.01mm以下。
而在高速运转或负载较大的情况下,齿轮径向跳动的数值会明显增大,甚至超过0.1mm。
2. 齿轮径向跳动的原因:通过对实验结果的分析,我们发现齿轮径向跳动的主要原因是齿轮的制造和装配误差,以及齿轮与轴之间的间隙。
制造误差包括齿轮的几何形状和表面质量等方面的偏差,而装配误差则包括齿轮的安装位置和相对角度等方面的误差。
这些误差会导致齿轮在运转中产生不稳定的径向力,从而引起齿轮径向跳动。
3. 改进方案:为了减小齿轮径向跳动的数值,我们可以采取以下改进方案:(1)提高齿轮的制造精度:通过优化齿轮的制造工艺和加工设备,减小齿轮的制造误差,提高齿轮的几何形状和表面质量,从而减小齿轮径向跳动的数值。
(2)优化齿轮的装配方式:在齿轮的装配过程中,采用精确的定位和调整方法,确保齿轮的安装位置和相对角度的准确性,减小齿轮的装配误差,从而减小齿轮径向跳动的数值。
齿圈径向跳动误差的测量实验
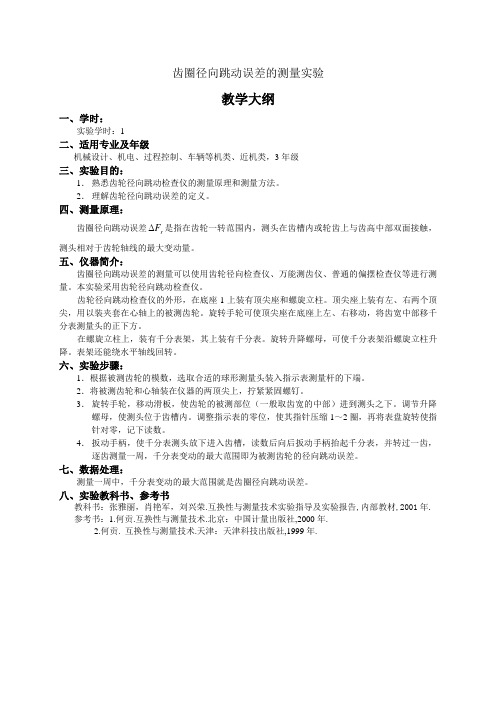
齿圈径向跳动误差的测量实验教学大纲一、学时:实验学时:1二、适用专业及年级机械设计、机电、过程控制、车辆等机类、近机类,3年级三、实验目的:1. 熟悉齿轮径向跳动检查仪的测量原理和测量方法。
2. 理解齿轮径向跳动误差的定义。
四、测量原理:齿圈径向跳动误差r F 是指在齿轮一转范围内,测头在齿槽内或轮齿上与齿高中部双面接触,测头相对于齿轮轴线的最大变动量。
五、仪器简介:齿圈径向跳动误差的测量可以使用齿轮径向检查仪、万能测齿仪、普通的偏摆检查仪等进行测量。
本实验采用齿轮径向跳动检查仪。
齿轮径向跳动检查仪的外形,在底座1上装有顶尖座和螺旋立柱。
顶尖座上装有左、右两个顶尖,用以装夹套在心轴上的被测齿轮。
旋转手轮可使顶尖座在底座上左、右移动,将齿宽中部移千分表测量头的正下方。
在螺旋立柱上,装有千分表架,其上装有千分表。
旋转升降螺母,可使千分表架沿螺旋立柱升降。
表架还能绕水平轴线回转。
六、实验步骤:1.根据被测齿轮的模数,选取合适的球形测量头装入指示表测量杆的下端。
2.将被测齿轮和心轴装在仪器的两顶尖上,拧紧紧固螺钉。
3. 旋转手轮,移动滑板,使齿轮的被测部位(一般取齿宽的中部)进到测头之下。
调节升降螺母,使测头位于齿槽内。
调整指示表的零位,使其指针压缩1~2圈,再将表盘旋转使指针对零,记下读数。
4. 扳动手柄,使千分表测头放下进入齿槽,读数后向后扳动手柄抬起千分表,并转过一齿,逐齿测量一周,千分表变动的最大范围即为被测齿轮的径向跳动误差。
七、数据处理:测量一周中,千分表变动的最大范围就是齿圈径向跳动误差。
八、实验教科书、参考书教科书:张雅丽,肖艳军,刘兴荣.互换性与测量技术实验指导及实验报告,内部教材,2001年. 参考书:1.何贡.互换性与测量技术.北京:中国计量出版社,2000年.2.何贡. 互换性与测量技术.天津:天津科技出版社,1999年.。
实验齿轮齿圈径向跳动.doc
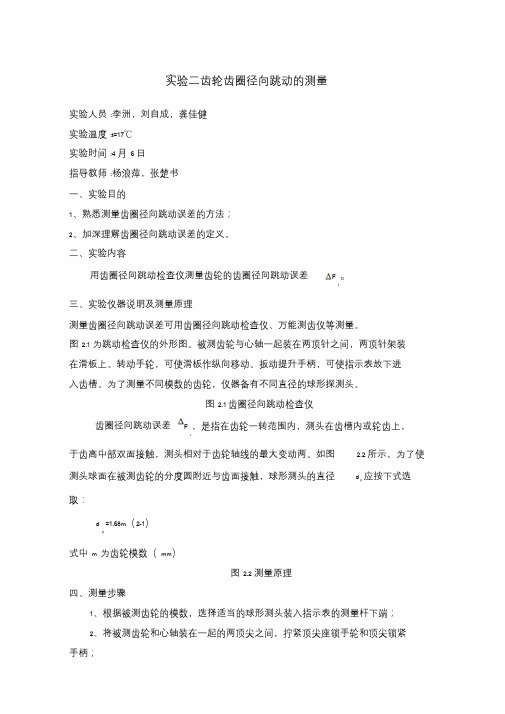
实验二齿轮齿圈径向跳动的测量实验人员:李洲,刘自成,龚佳健实验温度:t=17℃实验时间:4月6日指导教师:杨浪萍,张楚书一、实验目的1、熟悉测量齿圈径向跳动误差的方法;2、加深理解齿圈径向跳动误差的定义。
二、实验内容用齿圈径向跳动检查仪测量齿轮的齿圈径向跳动误差F。
r三、实验仪器说明及测量原理测量齿圈径向跳动误差可用齿圈径向跳动检查仪、万能测齿仪等测量。
图2.1为跳动检查仪的外形图。
被测齿轮与心轴一起装在两顶针之间,两顶针架装在滑板上。
转动手轮,可使滑板作纵向移动。
扳动提升手柄,可使指示表放下进入齿槽。
为了测量不同模数的齿轮,仪器备有不同直径的球形探测头。
图2.1齿圈径向跳动检查仪齿圈径向跳动误差F,是指在齿轮一转范围内,测头在齿槽内或轮齿上,r于齿高中部双面接触,测头相对于齿轮轴线的最大变动两。
如图 2.2所示。
为了使测头球面在被测齿轮的分度圆附近与齿面接触,球形测头的直径d p应按下式选取:d=1.68m(2-1)p式中m为齿轮模数(mm)图2.2测量原理四、测量步骤1、根据被测齿轮的模数,选择适当的球形测头装入指示表的测量杆下端;2、将被测齿轮和心轴装在一起的两顶尖之间,拧紧顶尖座锁手轮和顶尖锁紧3、旋转手轮,调整滑板位置,使球形测量头位于齿宽中部。
借升降螺母和提升手柄。
使是指表下降,直至测头伸入齿槽内且与齿面接触。
调整指示表,使其指针压缩约1-2 圈,拧紧表架后面的紧固旋钮;4、球形测头伸入齿槽最下方即可读数,每测完一齿,抬起提升手柄,使球形测头进入第二个齿槽与齿面接触,以此类推,逐齿测量并记录指示表的读数;5、根据齿轮的技术要求,查出齿圈径向跳动公差F r ,判断被测齿轮的合格性。
五、被测对象图2.3 被测对象齿轮基本参数见表1-1。
表2-1齿轮基本参数六、被模数m 齿数Z 压力角α齿轮精度径向跳动误差测数据记录员:刘3 18 20 12 171μm自成表2-2第一次测量数据序号读数(um)序号读数(um)1 28 10 1352 22 11 1303 61 12 1124 64 13 1035 91 14 866 104 15 617 124 16 208 131 17 99 114 18 3齿圈径跳误差F r (um)135-3=132合格性结论合格,在公差范围内。
1.15齿轮径向跳动的测量[11页]
![1.15齿轮径向跳动的测量[11页]](https://img.taocdn.com/s3/m/8bac7302ddccda38376baff7.png)
3.测量 抬起扳手3,使指示表2升高,把被测齿轮13转过一个齿槽。
然后,放下扳手3,使测头进入这个齿槽内,与齿槽双面接 触,并记下指示表的示值,。这样逐齿槽地依次测量所有 的齿槽,并把读数填入表1-35中。
合),然后把心轴安装在两个顶尖5之间。注意调整这两个顶尖之 间的距离,使心轴无轴向窜动,且能转动自如。 松开螺钉11,转动手轮12,使滑台9移动,以便使测头大约位于 齿宽中间。然后,将螺钉11锁紧。
五、实验步骤
2.调整量仪指示表的示值零位 放下扳手3,松开螺钉16,转动螺母15,使指示表测头随表
一、实验目的
(1)了解齿圈径向跳动检查仪的工作原理, (2)掌握齿圈径向跳动的测量方法, (3)加深对齿圈径向跳动定义的理解。
二、实验量仪说明
齿轮径向跳动可以使用齿轮径向跳动测量仪、万能测齿仪来测量。 本实验采用卧式齿轮径向跳动测量仪进行测量。
卧式齿轮径向跳动测量仪的外形如图1-118所示。测量时,把被 测齿轮13用心轴4安装在两个顶尖座7的顶尖5之间(齿轮基准孔与心 轴成无间隙配合,用心轴轴线模拟体现该齿轮的基准轴线)。指示表 2的位置固定后,使安装在指示表测杆上的球形测头或圆锥角等于 (为标准压力角)的锥形测头在齿槽内于接近齿高中部与齿槽的左、 右齿面接触。测头尺寸的大小应与被测齿轮的模数相适应,以保证测 头在接近齿高中部与齿槽双面接触。用测头逐齿槽地测量它相对于齿 轮基准轴线的径向位移,该径向位移由指示表2的示值反映出来。指 示表的最大与最小示值之差即为齿轮径向跳动的数值。
- 1、下载文档前请自行甄别文档内容的完整性,平台不提供额外的编辑、内容补充、找答案等附加服务。
- 2、"仅部分预览"的文档,不可在线预览部分如存在完整性等问题,可反馈申请退款(可完整预览的文档不适用该条件!)。
- 3、如文档侵犯您的权益,请联系客服反馈,我们会尽快为您处理(人工客服工作时间:9:00-18:30)。
---专业提供 SPC 数据分析软件等机械测量解决方案
易出错。 直接利用数据采集仪连接百分表,采集仪就会自动读取测量的最大值跟 最小值,完全不需要人工去操作。
2)无需人工去处理数据,数据采集仪会自动计算出齿圈径向跳动值。 说明:齿圈径向跳动计算公式已嵌入数据采集仪软件中,当测量完毕后数据采集 仪会马上计算出齿圈径向跳动值, 无需人工再去把测量的数据输入电脑进行数据 分析,可以减少人工计算数据的繁琐工作,而且测量效率高。
利用数据采集仪连接百分表来测量齿圈径向跳动的优势: 1)无需人工用肉眼去读数,可以减少由于人工读数产生的误差; 说明:由于测量齿圈径向跳动时,需要测量到最大值跟最小值,最后的齿圈 径向跳动值为 Fr = rmax - rmin , 但是如果由人工去读数时,很难直接判断出哪次 是最大值, 哪次是最小值, 这就需要多次去测量去判断, 这样就很容易判断错误, 而且当一台偏摆仪一次性连接几个百分表来同时测量时,那工作量会更大,更容
---专业提供 SPC 数据分析软件等机械测量解决方案
4、测量步骤: 1) 按被测齿轮模数选择适当的测头,将测头装在指示表上; 2) 移动顶针架滑板 12,使被测齿轮位于测头之下.并按上节所述,调节指示表架 的上下和角位置,然后紧固立柱 1 后面的调节螺钉,再转动 指示表右下角的 微调手轮 3 进行微调,使指针指零; 3) 逐齿测量,逐一记下读数,填入报告表中。 4) 求出齿圈实际跳动值,并作出结论。 5) 处理测量结果并判断合格性。
3、仪器的调整与使用 本仪器主要由顶针架 14 和 指示表 2 及其安装支架两大部分组成.将带心轴的被 测齿轮安装在两顶尖 78 上拧紧螺钉 9 和 10,心轴顶尖孔与顶尖间无间隙。安装 时要注意勿使齿轮下落砸坏仪器。 1)根据被测齿轮是圆柱还是圆锥齿轮,安置好指示表支架 5 的角向位置,同时按 被测齿轮的直径大小转动升降螺母 6,是指架作上下移动,并固定在某一适当 位置,以指示表侧头与被测齿轮在齿间内接触\表针大致向零度数为度.
---专业提供 SPC 数据分析软件等机械测量解决方案
测量齿圈径向跳动的各种方法讲解
---专业提供 SPC 数据分析软件等机械测量解决方案
摘要:主要介绍齿圈径向跳动的测量方法,包括传统的人工读数方法以及如何利 用太友科技数据采集仪连接百分表来实现高效测量齿圈径向跳动。
一、 齿圈径向跳动
齿圈径向跳动是指齿轮在一转范围内,测头在齿槽内活在轮齿上与齿高中部与 齿的双面接触,测头相对于齿轮轴心线的最大变动量。它主要反映齿轮运动误差 中因基圆的几何偏心所引起的径向误差分量。合公法线长度变动相组合可评定 6-8 级精度的齿轮,倘单独控制则只能评定 9 级以下低精度的齿轮。
Fr = rmax - rmin
合格条件: Fr ≤ Fr 为合格
方法二:利用数据采集仪连接百分表实现高效测量 1、 测量仪器 偏摆仪、百分表、QSmart 数据采集仪。
2、测量原理 数据采集仪会从百分表中自动读取测量数据的最大值跟最小值, 然后由数据采集 仪软件里的计算软件自动计算出所测产品的径向圆跳动误差, 最后数据采集仪会 自内, 如果所测径 向圆跳动误差大于径向圆跳动公差值,采集仪会自动发出报警功能,提醒相关操 作人员该产品不合格。
3)测量结果报警,一旦测量结果 Fr 大于 Fr 时,数据采集仪就会自动报警。 说明: 只有当 Fr ≤ Fr 时, 该零件才算符合生产要求, 才算合格, 反之则不合格。 一旦测量结果大于齿圈径向跳动公差值时,数据采集仪就会发出报警功能,提醒 相关人员该零件不符合生产规格要求,需要进一步去完善,这就可以进一步提高 测量效率。
3、测量步骤 1)将偏摆仪活动顶尖定位手柄松开;
---专业提供 SPC 数据分析软件等机械测量解决方案
2)将活动顶尖及固定顶尖之间的距离调节到与工件长度相当的位置;
3)锁紧活动顶尖定位手柄;
---专业提供 SPC 数据分析软件等机械测量解决方案
4)压下轴固定手柄,将工件两端中心孔对齐两顶尖,放开轴固定手柄,将工件 固定好;
二、 齿圈径向跳动测量方法
测量齿圈径向跳动 的工作原理与测量径向跳动相似,通常可以在 通用的跳动仪 上测量。 方法一:传统人工读数方法 1、仪器设备
---专业提供 SPC 数据分析软件等机械测量解决方案
2、测量原理: 齿圈径向跳动 Fr 是指在齿轮一转范围内,测头在齿槽内或齿轮上,于齿高中部 双面接触, 测头相对于齿轮轴心线的最大变动量。它主要是由齿轮加工中毛坯安 装的几何偏心和齿轮机床工作台的跳动或插齿刀的偏心等引起的。 这种误差将使 齿轮传动一周范围内传动比发生变化,属于长周期误差。为了测量各种不同模数 的齿轮,仪器备有大小不同可换的球形测量头,此外仪器还备有两支杠杆。 外接触杠杆——成直角三角形,用于测量端面及伞齿轮; 内接触杠杆——成直角形,用于测量内孔的跳动及内齿轮的跳动。 本实验因是测量圆柱直齿轮齿圈径向跳动,不需要选用内外接触杠杆。测量时直 接把球形侧头接在指示表的量杆下即可。
2)根据被测齿轮模数大小,选择相应直径的指示表侧头.为使测头在齿轮分度圆 处接触,测头直径按式 d=1.68 m 决定. 3)测量时应上翻扳手 4,提起指示表测头后 才可将齿轮转过一齿,在将扳手轻 轻放下,使测头与齿面接触.指示表侧头调零(旋动微调手轮3)开始逐齿测取 读数,直至侧扁全部齿间为止。最后当指示表侧头回到调零齿间时,表上读 数应为零。若偏差超过一个格值应检查原因,并重新测量。 4)在全部读数记录中,取其最大值与最小值之差,即为被测齿轮的齿圈径向跳 动 Fr
5)将百分表安装到表座上;
6)调节表座杆,使百分表底端轻触到待测圆柱面,并将百分表调零.
---专业提供 SPC 数据分析软件等机械测量解决方案
7)用数据采集仪连接好百分表:
8)开始测量,转到零件一边,采集仪会自动采集仪读取测量的最大最小值,多 测量几个位置。 9)数据处理:数据采集仪软件里已嵌入计算圆跳动误差的公式在里面,采集仪 会自动计算圆跳动误差值,无需人工去计算跳动误差值。 10)分析结果:数据采集仪会自动根据所测得的跳动误差值,以轴类零件规定的 圆跳动公差值进行比较,一旦圆跳动误差值大于圆跳动公差值,则系统会自 动报警,表示该轴类零件测量结果不合格。 11)测量完成后将工件拿下,收好偏摆仪百分表以及数据采集仪,清除在偏摆仪 上留下的污垢,并做好导轨和顶尖的润滑工作。
以上讲述了齿圈径向跳动的两种测量方法, 在实际测量中还要根据实际情况和设 备选择合适的测量方法, 但最终目的都是尽可能的减小齿圈径向跳动误差,在节 约成本的情况下,提高径向跳动的精度,达到生产所需要的精度值,其中利用数 据采集仪连接百分表来测量是操作最简单,效率最高一种方法。