双碱法脱硫物料平衡计算过程
双碱法烟气脱硫计算

双碱法计算过程标态:h Nm Q /4000030=65℃:h m Q /49523400002736527331=⨯+= 还有约5%的水份如果在引风机后脱硫,脱硫塔进口压力约800Pa ,出口压力约-200Pa ,如果精度高一点,考虑以上两个因素。
1、脱硫塔⑴ 塔径及底面积计算:塔内流速:取s m v /2.3=m v Q r r v vs Q 17.12.314.33600/49532121=⨯==⇒⋅⋅==ππ D=2r=2.35m 即塔径为2.35米。
底面积S=∏r 2=4.3m 2塔径设定为一个整数,如2.5m⑵ 脱硫塔高度计算:液气比取L/G= 4,烟气中水气含量设为8%SO 2如果1400mg/m3,液气比2.5即可,当SO2在4000mg/m3时,选4① 循环水泵流量:h m m l HG Q G L Q /1821000)08.01(495324)/(100033=-⨯⨯=⨯⨯= 取每台循环泵流量=Q 91m 。
选100LZ A -360型渣浆泵,流量94m 3/h ,扬程22.8米, 功率30KW ,2台② 计算循环浆液区的高度:取循环泵8min 的流量,则H 1=24.26÷4.3=5.65m如此小炉子,不建议采用塔内循环,塔内循环自控要求高,还要测液位等,投资相应大一点。
采用塔外循环,泵的杨程选35m ,管道采用碳钢即可。
③ 计算洗涤反应区高度停留时间取3秒,则洗涤反应区高度H2=3.2×3=9.6m④除雾区高度取6米H3=6m⑤脱硫塔总高度:H=H1+H2+H3=5.65+9.6+6=21.3m塔体直径和高度可综合考虑,直径大一点,高度可矮一点,从施工的方便程度、场地情况,周围建筑物配套情况综合考虑,可适当进行小的修正。
如采用塔内循环,底部不考虑持液槽,进口管路中心线高度可设在2.5m,塔排出口设为溢流槽,自流到循环水池。
塔的高度可设定在16~18m2、物料恒算每小时消耗99%的NaOH 1.075Kg。
双碱法脱硫的操作

双碱法脱硫的操作主要工艺过程是:清水池一次性加入氢氧化钠溶剂制成氢氧化钠脱硫液(循环水),用泵打入脱硫除尘器进行脱硫。
3种生成物均溶于水。
在脱硫过程中,烟气夹杂的烟道灰同时被循环水湿润而捕集进入循环水,从脱硫除尘器排出的循环水变为灰水(稀灰浆)。
一起流入沉淀池,烟道灰经沉淀定期清除,回收利用,如制内燃砖等。
上清液溢流进入反应池与投加的石灰进行反应,置换出的氢氧化钠溶解在循环水中,同时生成难溶解的亚硫酸钙、硫酸钙和碳酸钙等,可通过沉淀清除;可以回收,是制水泥的良好原料。
因此可做到废物综合利用,降低运行费用。
用NaOH脱硫,循环水基本上是NaOH的水溶液。
在循环过程中对水泵、管道、设备均无腐蚀与堵塞现象,便于设备运行与保养。
为保证脱硫除尘器正常运行,烟气排放稳定达标,确保脱硫剂有足够使用量是一个关键问题。
脱硫剂用量计算如下:脱硫反应中,NaOH的消耗量是SO2和CO2与其反应的消耗量。
用量需要过量5%以上(按5%计算)。
前面计算的10 t/h锅炉烟气中SO2排放量为42 kg/h,CO2排放是为2 161 kg/h。
SO2和CO2中和反应用氢氧化钠量为:(80×42÷64+80×2 161÷44)×105%=4 180 kg脱硫过程由于NaOH的转换实际消耗是石灰。
折算成生石灰消耗量56×4 180÷80=2 926 kg生石灰日消耗量为70 224 kg综上所述,脱硫过程的碱消耗量是很大的。
但要保证脱硫效率,就必须要保证碱的用量,通过比较双碱法脱硫可以实现脱硫效率高,运行费用相对比较低,操作方便,无二次污染,废渣可综合利用。
所以改进后的双碱法脱硫工艺是值得推荐和推广应用的。
双碱法是采用钠基脱硫剂进行塔内脱硫,由于钠基脱硫剂碱性强,吸收二氧化硫后反应产物溶解度大,不会造成过饱和结晶,造成结垢堵塞问题。
另一方面脱硫产物被排入再生池内用氢氧化钙进行还原再生,再生出的钠基脱硫剂再被打回脱硫塔循环使用。
双碱法脱硫工艺

双碱法脱硫工艺双碱法脱硫工艺技术是目前应用成熟的一种烟气脱硫技术,尤其是在小热电燃煤锅炉烟气污染治理方面应用较为广泛。
脱硫剂初步采用氢氧化钠溶液(含30%NaOH)和生石灰(含90%CaO)。
其工艺原理是:以NaOH溶液为第一碱吸收烟气中的二氧化硫,然后再用生石灰加水熟化成氢氧化钙溶液作为第二碱,再生吸收液中NaOH,副产物为石膏。
再生后的吸收液送回脱硫塔循环使用。
各步骤反应如下:吸收反应:SO2+2NaOH=Na2SO3+H2ONa2SO3+SO2+H2O=2NaHSO3副反应如下:Na2SO3+1/2O2=Na2SO4由于硫酸钠是很难再生还原的,一旦生成就需要补充NaOH。
再生反应用氢氧化钙溶液对吸收液进行再生2NaHSO3+Ca(OH)2=Na2SO3+CaSO3·1/2H2O+3/2H2ONa2SO3+Ca(OH)2+1/2H2O=2NaOH+CaSO3·1/2H2O氧化反应CaSO3·1/2H2O+1/2O2=CaSO4·1/2H2O本双碱法脱硫系统主要由脱硫塔系统(含烟气除雾)、烟气系统、吸收剂供应及制备系统、脱硫液循环及再生系统、脱硫渣处理系统、工艺水系统和电气及仪表控制系统等组成。
技术特点(1)从技术、经济及装置运行稳定性、可靠性上考虑采用生石灰和氢氧化钠作为脱硫剂,保证系统脱硫效率最低可达90%。
(2)采用双碱法脱硫工艺,可以基本上避免产生结垢堵塞现象,减少昂贵的NaOH耗量和降低运行费用。
(3)采用喷雾洗涤方式可在较小的液气比下获得较大的液气接触面积,进而获得较高的脱硫除尘效率;并且,较小的液气比可以减少循环液量,从而减少循环泵的流量,降低了运行成本也减少了造价。
(4)为确保整个系统连续可靠运行,采用优良可靠的设备,以确保脱硫系统的可靠运行.(5)按现有场地条件布置脱硫系统设备,力求紧凑合理,节约用地。
(6)最大限度的把脱硫水循环利用,但是由于烟气中含有一定浓度的盐份和Cl离子,反应塔内部分水分蒸发,因此形成循环水中盐和Cl离子的积累,由于过高的盐和Cl离子浓度会降低脱硫效率和腐蚀反应装置,所以必须调整脱硫循环水水质并补充少量工业用水。
双碱法烟气脱硫物料计算
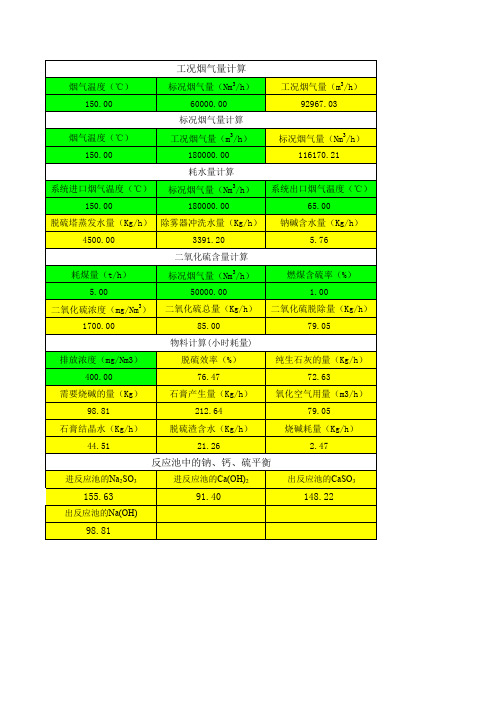
烧碱的量
单位 m m
元/吨 元/吨
% h m2 m/s t t/年 t/年
数值 18.00 4.00 300.00 3000.00 93.00 8000.00 12.56 3.98 632.40 581.02 19.86
85%生石灰的量 t/年
683.55
生石灰费用 万元
44.51
21.26
2.47
反应池中的钠、钙、硫平衡
进反应池的Na2SO3
155.63
进反应池的Ca(OH)2
91.40
出反应池的CaSO3
148.22
出反应池的Na(OH)
98.81
输入值
计算值
锅炉数量
1.00
脱硫塔计算公式
设计参数 塔高 塔径
85%生石灰价格 烧碱价格 脱硫效率 年运行时间
脱硫塔截面积 烟气流速
1700.00
85.00
79.05
物料计算(小时耗量)
排放浓度(mg/Nm3)
脱硫效率(%)
纯生石灰的量(Kg/h)
400.00
76.47
72.63
需要烧碱的量(Kg)
石膏产生量(Kg/h) 氧化空气用量(m3/h)
98.81
212.64
79.05
石膏结晶水(Kg/h)
脱硫渣含水(Kg/h)
烧碱耗量(Kg/h)
工况烟气量计算
烟气温度(℃)
标况烟气量(Nm3/h)
工况烟气量(m3/h)
150.00
60000.00
92967.03
标况烟气量计算
烟气温度(℃)
工况烟气量(m3/h)
标况烟气量(Nm3/h)
双碱液法脱硫计算公式

双碱液法脱硫计算公式
双碱液法脱硫是一种常用的大气污染控制技术,可以将燃煤电厂等工业设施的二氧化硫排放量减少到国家和地方排放标准以下,从而保护环境和人民健康。
双碱液法脱硫的原理是利用碱性溶液(主要包括氢氧化钠和碳酸钙)与二氧化硫发生反应,形成硫酸钙和水,从而达到脱硫的目的。
在反应过程中,必须要控制溶液的浓度和温度才能保证脱硫效果。
具体的计算公式如下:
1. 双碱液法脱硫反应方程式
反应式:NaOH + SO2 + H2O → Na2SO3 + 2H2O
化学方程式:2NaOH + SO2 + 2CO2 → Na2SO3 + Na2CO3 +
2H2O
2. 双碱液法脱硫的常数及限制因素
常数:k1、k2、k3、k4、k5
限制因素:SO2、NaOH、Ca(OH)2的摩尔比、气相速度、溶液浓度、温度、气体分子量、溶液分子量以及反应釜的构造设计等。
3. 双碱液法脱硫效率的计算公式
SO2去除率=1- (Cout/Cin)*100%
其中,Cout为脱除后气流中的SO2浓度(mg/m3),Cin为控制前气流中的SO2浓度(mg/m3)。
4. 双碱液法脱硫量的计算公式
SO2去除量= V*I*(Cin-Cout)
其中,V表示气流体积(m3/s),I表示反应器中溶液的稀释倍数,Cin-Cout表示SO2的浓度差(mg/m3)。
5. 双碱液法脱硫方案比较
在双碱液法脱硫方案中,不同的方案对应着不同的反应器构造、气体流量、溶液循环量、溶液配比等。
需要进行全面比较才能选择
适宜的方案。
以上就是双碱液法脱硫计算公式的相关内容,具体的计算需要
根据实际情况进行调整。
双碱法烟气脱硫物料计算
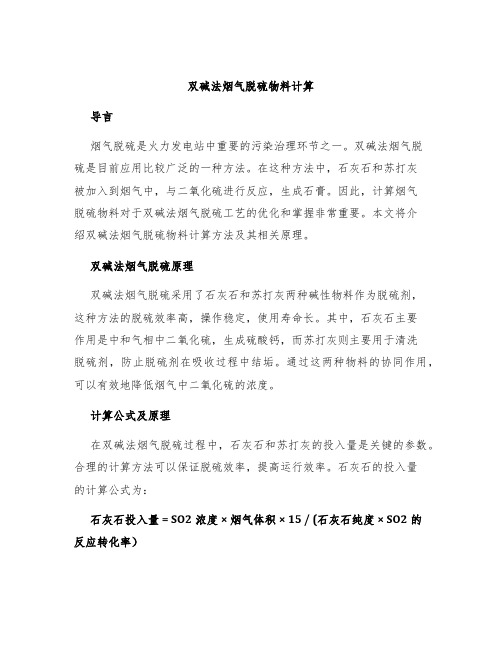
双碱法烟气脱硫物料计算导言烟气脱硫是火力发电站中重要的污染治理环节之一。
双碱法烟气脱硫是目前应用比较广泛的一种方法。
在这种方法中,石灰石和苏打灰被加入到烟气中,与二氧化硫进行反应,生成石膏。
因此,计算烟气脱硫物料对于双碱法烟气脱硫工艺的优化和掌握非常重要。
本文将介绍双碱法烟气脱硫物料计算方法及其相关原理。
双碱法烟气脱硫原理双碱法烟气脱硫采用了石灰石和苏打灰两种碱性物料作为脱硫剂,这种方法的脱硫效率高,操作稳定,使用寿命长。
其中,石灰石主要作用是中和气相中二氧化硫,生成硫酸钙,而苏打灰则主要用于清洗脱硫剂,防止脱硫剂在吸收过程中结垢。
通过这两种物料的协同作用,可以有效地降低烟气中二氧化硫的浓度。
计算公式及原理在双碱法烟气脱硫过程中,石灰石和苏打灰的投入量是关键的参数。
合理的计算方法可以保证脱硫效率,提高运行效率。
石灰石的投入量的计算公式为:石灰石投入量 = SO2浓度 × 烟气体积 × 15 / (石灰石纯度 × SO2的反应转化率)其中,SO2浓度可以通过测定烟气中二氧化硫的浓度来获得。
烟气体积可以通过测定烟气流量和烟气温度计算得出。
15是一个常数,纯度为石灰石的质量纯度,SO2的反应转化率指二氧化硫转化为硫酸钙的转化率。
同样地,苏打灰的投入量可以根据如下公式计算:苏打灰投入量 = SO2浓度 × 烟气体积 × 10 / (苏打灰纯度 × SO2的反应转化率)其中,10是一个常数,苏打灰纯度为该物料的质量纯度。
实际应用举例为了更好地理解双碱法烟气脱硫物料计算方法,我们可以通过一个实际案例进行演示。
假设某发电厂采用双碱法烟气脱硫工艺,脱硫需要使用石灰石和苏打灰两种脱硫剂。
石灰石和苏打灰的质量纯度分别为90%和95%。
某次测定烟气流量为5000m³/h,温度为150℃,二氧化硫的浓度为1.2g/Nm³。
首先,我们可以根据石灰石的投入量公式计算出石灰石的具体质量:石灰石投入量 = 1.2 × 5000 × 15 / (90% × 85%)= 147.06kg/h接下来,我们可以利用苏打灰的投入量公式计算苏打灰的具体质量:苏打灰投入量 = 1.2 × 5000 × 10 / (95% × 85%)= 98.04kg/h综上所述,该发电厂每小时需要投入147.06kg的石灰石和98.04kg 的苏打灰进行脱硫处理。
双碱法脱硫物料平衡计算过程

双碱法脱硫物料平衡计算过程双碱法脱硫是一种常用的烟气脱硫技术,常用的双碱剂为氢氧化钠和氢氧化钙,既可以实现脱除烟气中的SO2,也可以避免单碱法操作中的缺点,如石灰石堵塞等。
在双碱法脱硫过程中,需要进行物料平衡计算,以确保反应体系的合理性和脱硫效率。
以下是双碱法脱硫物料平衡计算的详细过程。
1. 确定反应方程式:双碱法脱硫的基本反应方程式为:Ca(OH)2 + NaOH + SO2 → CaSO3 + 2H2O + NaOH反应中氢氧化钙和氢氧化钠与二氧化硫反应生成硫酸钙和水,并释放出氢氧化钠。
反应中前两个试剂是体积计输送进入吸收塔,后置两个试剂为反应废液,存在管道里输送。
物料平衡计算的目的就是通过上述方程式,计算各个试剂的输入量和产出量。
2. 确定反应条件:在反应中,需要控制反应废液的pH值,以确保反应的顺利进行和产物的纯度。
一般情况下,反应废液的pH值应该在10.5~11.5之间。
此外,还需要控制反应废液的温度,防止因温度过高产生副反应。
3. 计算反应试剂的输入量:在双碱法脱硫过程中,需要输入的试剂有氢氧化钠、氢氧化钙和二氧化硫。
假设反应中氢氧化钠的摩尔数为a,氢氧化钙的摩尔数为b,二氧化硫的摩尔数为c,则反应的总摩尔数为a+b+c。
由此可得,氢氧化钠和氢氧化钙的输入量分别为V1=a*(mol/V)和V2=b*(mol/V),其中V为体积,单位为立方米。
在实际操作中,氢氧化钠和氢氧化钙的输送速率不同,需要考虑到孔板的压损和各个管道的分配。
实际输送量可以通过实验和测量得到,再进行调整。
4. 计算反应产物的输出量:反应废液中产生的产物包括CaSO3、H2O和NaOH。
假设反应中CaSO3的摩尔数为d,水的摩尔数为e,NaOH的摩尔数为f,则反应产物的总摩尔数为d+2e+f。
由此可得,反应产生的NaOH量为V3=f*(mol/V)。
反应废液中的CaSO3可以通过挥发和过滤等方法进行处理,而水也可以通过挥发和蒸汽回收的方式进行处理,以节约资源和降低成本。
双碱法脱硫的操作

双碱法脱硫的操作双碱法脱硫的操作主要工艺过程是:清水池一次性加入氢氧化钠溶剂制成氢氧化钠脱硫液(循环水),用泵打入脱硫除尘器进行脱硫。
3种生成物均溶于水。
在脱硫过程中,烟气夹杂的烟道灰同时被循环水湿润而捕集进入循环水,从脱硫除尘器排出的循环水变为灰水(稀灰浆)。
一起流入沉淀池,烟道灰经沉淀定期清除,回收利用,如制内燃砖等。
上清液溢流进入反应池与投加的石灰进行反应,置换出的氢氧化钠溶解在循环水中,同时生成难溶解的亚硫酸钙、硫酸钙和碳酸钙等,可通过沉淀清除;可以回收,是制水泥的良好原料。
因此可做到废物综合利用,降低运行费用。
用NaOH脱硫,循环水基本上是NaOH的水溶液。
在循环过程中对水泵、管道、设备均无腐蚀与堵塞现象,便于设备运行与保养。
为保证脱硫除尘器正常运行,烟气排放稳定达标,确保脱硫剂有足够使用量是一个关键问题。
脱硫剂用量计算如下:脱硫反应中,NaOH的消耗量是SO2和CO2与其反应的消耗量。
用量需要过量5%以上(按5%计算)。
前面计算的10 t/h锅炉烟气中SO2排放量为42 kg/h,CO2排放是为2 161 kg/h。
SO2和CO2中和反应用氢氧化钠量为:(80×42÷64+80×2 161÷44)×105%=4 180 kg脱硫过程由于NaOH的转换实际消耗是石灰。
折算成生石灰消耗量56×4 180÷80=2 926 kg生石灰日消耗量为70 224 kg综上所述,脱硫过程的碱消耗量是很大的。
但要保证脱硫效率,就必须要保证碱的用量,通过比较双碱法脱硫可以实现脱硫效率高,运行费用相对比较低,操作方便,无二次污染,废渣可综合利用。
所以改进后的双碱法脱硫工艺是值得推荐和推广应用的。
双碱法是采用钠基脱硫剂进行塔内脱硫,由于钠基脱硫剂碱性强,吸收二氧化硫后反应产物溶解度大,不会造成过饱和结晶,造成结垢堵塞问题。
另一方面脱硫产物被排入再生池内用氢氧化钙进行还原再生,再生出的钠基脱硫剂再被打回脱硫塔循环使用。
- 1、下载文档前请自行甄别文档内容的完整性,平台不提供额外的编辑、内容补充、找答案等附加服务。
- 2、"仅部分预览"的文档,不可在线预览部分如存在完整性等问题,可反馈申请退款(可完整预览的文档不适用该条件!)。
- 3、如文档侵犯您的权益,请联系客服反馈,我们会尽快为您处理(人工客服工作时间:9:00-18:30)。
双碱法 计算过程
标态:h Nm Q /4000030=
65℃:h m Q /4952340000273
6527331=⨯+= 还有约5%的水份
如果在引风机后脱硫,脱硫塔进口压力约800Pa ,出口压力约-200Pa ,如果精度高一点,考虑以上两个因素。
1、脱硫塔
(1)塔径及底面积计算:
塔内流速:取s m v /2.3=
m v Q r r v vs Q 17.12
.314.33600/49532121=⨯==⇒⋅⋅==ππ D=2r=2.35m 即塔径为2.35米。
底面积S=∏r 2=4.3m 2
塔径设定为一个整数,如2.5m
(2)脱硫塔高度计算:
液气比取L/G= 4 烟气中水气含量设为8%
SO2如果1400mg/m3,液气比2.5即可,当SO2在4000mg/m3时,选4
①循环水泵流量:h m m l HG Q G L Q /1821000)08.01(495324)
/(100033=-⨯⨯=⨯⨯= 取每台循环泵流量=Q 91m 。
选100LZ A -360型渣浆泵,流量94m 3/h ,扬程22.8米, 功率30KW ,2台
②计算循环浆液区的高度:
取循环泵8min 的流量
H 1=24.26÷4.3=5.65m
如此小炉子,不建议采用塔内循环,塔内循环自控要求高,还要测液位等,投资相应大一点。
采用塔外循环,泵的杨程选35m,管道采用碳钢即可。
③计算洗涤反应区高度
停留时间取3秒
洗涤反应区高度H2=3.2×3=9.6m
④除雾区高度取6米
H3=6m
⑤脱硫塔总高度H=H1+H2+H3=5.65+9.6+6=21.3m
塔体直径和高度可综合考虑,直径大一点,高度可矮一点,从施工的方便程度、场地情况,周围建筑物配套情况综合考虑,可适当进行小的修正。
如采用塔内循环,底部不考虑持液槽,进口管路中心线高度可设在2.5m,塔排出口设为溢流槽,自流到循环水池。
塔的高度可设定在16~18m
2、物料恒算
每小时消耗99%的NaOH1.075Kg。
每小时消耗85%的CaO60.585Kg。
石灰浆液浓度:含固量15%,可得石灰浆液密度1.093。
按半小时配置一次石灰浆液计算,每次配置石灰浆液的体积是185m3。
浆液区的体积是24.26 m3。
石灰浆液按浆液区体积的10% 的流量(即石灰浆液泵的流量为 2.4 m3/h)不间断往塔内输送浆液。
石膏浆液排出泵按浆液区体积的20% 的流量(即石膏浆液排出泵的流量为4.8 m3/h)不间断往塔外输出石膏浆液。
由计算可得每小时产石膏干重0.129吨。
蒸发水分量2.16 m3/h。
除雾器及管道冲洗水量约为3 m3/h。
补充碱液量按按浆液区体积的10% 的流量(即碱液泵的流量为 2.4 m3/h)不间断往塔内输送碱液
进塔部分:石灰浆液2.4 m3/h + 除雾器及管道冲洗水量3 m3/h + 补充碱液量2.4 m3/h 出塔部分:石膏浆液4.8m3/h +蒸发水分量2.16 m3/h
若氧化还原池按两塔5小时排出浆液量计算,则容积应为3.6×2×5=36 m3
如果采用塔外循环,循环水池也即再生、沉淀、碱水池可设定容量为250m3,有效容积200m3,池高度≤4m(便于抽沉淀),循环水停留时间设定为1小时。
石灰采用人工加料,沉淀用离心渣泵或潜水渣泵抽出,采用卧式离心机脱水。