FMECA失效模式后果与严重度分析方法.pptx
合集下载
第六章失效模式、效应及危害度分析(FMECA)和故障树分析法(FTA)演示教学

4. 严酷度分类
2.3
对失效造成的后果的严重程度进行分类,是较笼统的、定性的分类。
Ⅰ类(灾难性的)——会引起人员死亡或系统毁坏的失效(机毁人亡)。
Ⅱ类(致命性的)——会引起人员严重伤亡、重大财产损失或导致任务失 败的系统严重失效。
Ⅲ类(临界的)——会引起人员的轻度损伤、一定人的财产损失或导致任 务延误或降级的系统轻度损坏。
提前运行; 在规定的时刻开机失效; 间断地工作; 在规定的时刻关机失效; 工作中输出失效(或消失); 输出或工作能力下降; 与系统特性有关的其它失效。
6. FMEA报告 2.5 应将FMEA的主要内容和结果汇编成文,其中包括:
信息来源说明; 被分析对象的定义;
FMEA示例
分析层次;
分析方法说明;
FMEA表;
率来评价FMEA 中确定的失效模式。
3.2
失效模式发生的概率等级可按以下方法划分:
Ⅳ类(轻度的)——不足以导致上述三类后果的失效,但它会导致非计划 维护或修理。
在GB7826-1987中给出的类别的顺序与上述恰相反,即:
轻度 Ⅰ Ⅱ Ⅲ Ⅳ 严重
严酷度的分类和确定有一定的任意性,不同的领域应专门给出严酷2.3 度的 定义。例如,航空发动机的严酷度定义为:
Ⅰ类(灾难性的)——会引起发动机空中停车且不易重新启动的故障。
按每一失效形式的严酷度类别及该失效模式的发生概率所产生的综合 影响来对其划等分类,以便全面地评价各潜在失效模式影响。
CA是FMEA的补充和扩展,未进行FMEA,不能进行CA。
2. 分析方法 相对于FMEA而言,CA侧重于定量分析,当然具体方法包括定性分析和
定量分析两种。
①定性分析方法 在不具备产品可靠性数据(或失效率)时,可按失效模式发生的大致概
潜在失效模式及其后果分析 (FMECA)ppt课件
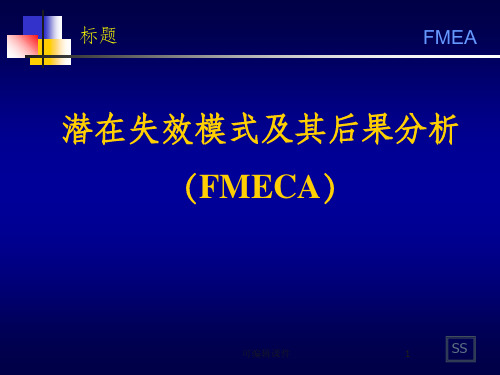
手册提供了应用 FMEA 技术的总体指南,但并没有给出
如何完成每一 FMEA 项目的具体说明,也不是综合性的
参考资料或培训资料。
可编辑课件
8
FMEA参考手册第四版的变化
包含与系统、子系统、接口和零部件等级别的设计相关 的方法,以及与制造和装配的过程相关的方法;
增加索引、示例,重要段落予以标示,更易理解使用;
Avoid TRIAL AND ERROR —— 避免尝试和失误
关注产品系统的可靠性安全性
可编辑课件
14
——有关术语
FMEA
第二讲 有关术语与概念
2.1 可靠性与可靠度 2.2 失效与寿命特征参数 2.3 系统与可靠性模型 2.4 可靠性工程 2.5 失效模式
可编辑课件
15
SS
2.1 可靠性与可靠度
分析该后果的严重程度 (影响和后果分析) ;
采取措施,提高系统的可靠性。
可编辑课件
45
SS
常用失效分析方法
FMEA
按失效原因分类:
—— 直方图、因果图、主次图;
按失效模式影响分类:
—— FMECA、FTA、ETA;
按综合应用分类:
标题
FMEA
潜在失效模式及其后果分析 (FMECA)
可编辑课件
1
SS
引言
FMEA
引言 从神舟载人飞船谈起
可编辑课件
2
SS
引言
FMEA
产品可靠性 —— 现代产品质量的关键.
产品二种质量指标 性能指标 —— 产品完成规定功能所需的性能 可靠性指标 —— 产品性能随时间保持的能力
产品竞争的焦点
可编辑课件
40
失效发生的主要原因分布
FMECA--FMEA( 故障模式影响分析)(课堂PPT)
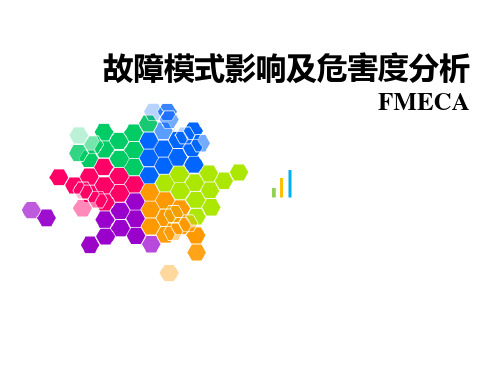
故障模式影响及危害性分析(Failure Mode ,Effects and Criticality analysis , 简记为FMECA)是分析系统中每一产品所有可能产生的故 模式及其对系统造成的所有可能影响,并按每一个故障模式的严 程度及其发生概率予以分类的一种归纳分析方法。
• FMECA是一种自下而上的归纳分析方法; • FMEA和CA。
• FMECA的目的
从产品设计(功能设计、硬件设计、软件设计)、生产(生产可 性分析、工艺设计、生产设备设计与使用)和使用发现各种影响 品可靠性的缺陷和薄弱环节,为提高产品的质量和可靠性水平提 改进依据。
FMECA作用
Tankertanker Design
• 1.保证有组织地定性找出系统的所有可能的故障 模式及其影响,进而采取相应的措施。
页
备注
13
本栏主 要记录 对其它 栏的注 释和补 充说明
实施FMECA应注意的问题
Tankertanker Design
1.强调“谁设计、谁分析”的原则
– “谁设计、谁分析”的原则,也就是产品设计人员应负责完成该 产品的FMECA工作,可靠性专业人员应提供分析必须的技术支持。
– 实践表明,FMECA工作是设计工作的一部分。“谁设计、谁分 析”、及时改进是进行FMECA的宗旨,是确保FMECA有效性的 基础,也是国内外开展FMECA工作经验的结晶。如果不由产品设 计者实施FMECA,必然造成分析与设计的分离,也就背离了 FMECA的初衷。
6.2.3 故障影响分析
Tankertanker Design
1.约定层次的划分
• 约定层次:在进行FMEA之前,应首先规定FMEA从哪个产 品层次开始到那个厂品层次结束,这种规定的FMEA层次 称为约定层次。
• FMECA是一种自下而上的归纳分析方法; • FMEA和CA。
• FMECA的目的
从产品设计(功能设计、硬件设计、软件设计)、生产(生产可 性分析、工艺设计、生产设备设计与使用)和使用发现各种影响 品可靠性的缺陷和薄弱环节,为提高产品的质量和可靠性水平提 改进依据。
FMECA作用
Tankertanker Design
• 1.保证有组织地定性找出系统的所有可能的故障 模式及其影响,进而采取相应的措施。
页
备注
13
本栏主 要记录 对其它 栏的注 释和补 充说明
实施FMECA应注意的问题
Tankertanker Design
1.强调“谁设计、谁分析”的原则
– “谁设计、谁分析”的原则,也就是产品设计人员应负责完成该 产品的FMECA工作,可靠性专业人员应提供分析必须的技术支持。
– 实践表明,FMECA工作是设计工作的一部分。“谁设计、谁分 析”、及时改进是进行FMECA的宗旨,是确保FMECA有效性的 基础,也是国内外开展FMECA工作经验的结晶。如果不由产品设 计者实施FMECA,必然造成分析与设计的分离,也就背离了 FMECA的初衷。
6.2.3 故障影响分析
Tankertanker Design
1.约定层次的划分
• 约定层次:在进行FMEA之前,应首先规定FMEA从哪个产 品层次开始到那个厂品层次结束,这种规定的FMEA层次 称为约定层次。
第四章失效模式后果与严重度

内衬
与外壳分离
与药柱或隔 热层分离
粘接剂不良 粘接控制不良
壳体成形后净化 不够
燃烧速度过高; 内压过高;机 壳在工作过程 中破裂
0.0001
严重
严格执行正常清洗 程序,机巧清洗后 严格检验,确保清 除一切沾染物
例4-2 设计概述: 重新设计一个用于自动变速箱的手动臂。由钢轴(热处
理并外圆磨)和模压成型的塑料臂组成。轴与臂靠花键压装 配合。
第四章 失效模式、后果与严重度分析 (FMECA)
§4-1 概 述 §4-2 失效模式与后果分析 ( FMEA和FMECA )
一、FMEA及FMECA的概念 二、建立FMEA(FMECA)的一般方法 三、FMEA的应用实例 §4-3 失 效 严 重 度 分 析 一、定性分析 二、定量分析 三、严重度矩阵 四、严重度分析的用途
零件功用:手动臂总成把变速器外部的手动选档杆和变速器内 部的传动臂连接起来。由前者向操纵阀体内的手动阀和停车驱 动机构传递运动。作用在臂孔处的最大切向拉力为30磅。
分系统过程 自动变速箱
年型/车型系列 1974年野马牌
制造与设计主管部门
T
有关制造与设计部门
有否外部供货和承制单位 无
分系统工程师 约翰.杜
② 收集生产过程的有关试验统计数据和 用户反馈意见为依据,确定出故障模式(即预 测出故障模式);
③ 分析产生故障原因(即物理失效机理);
④ 制定生产中的消除办法(即检测方法), 使用中的弥补方法(即补偿措施)等;
⑤ 对各故障模式的严重后果(即严酷 度等级)进行评定,必要时可采用投票评分 的方法;
⑥ 对新设计产品与已生产的上述产品的 主要不同之处进行分析,以进行必要的补充。
FMECA--CA(危害性分析)ppt课件
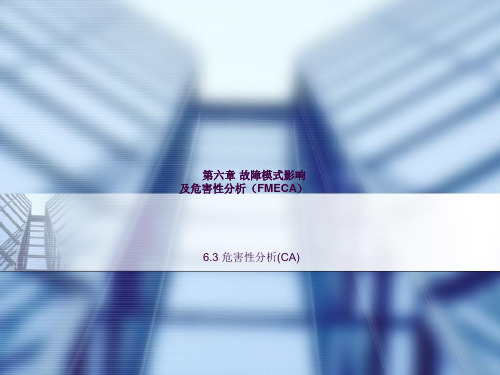
RPN=OPR×ESR×DDR
表6-9 检验难度评分准则
结论
1.故障发生可能性高、故障严重程度高,又难以检出的故障模式,其RPN值较高,从 而危害性较大。
2.对于危害性高的故障模式,应从降低故障发生可能性和故障严重程度及提高该故障 检出可能性三方面提出改进措施。
3.在利用RPN对故障模式进行评定时,可制定一个RPN的门限值,超过此门限值的故 障模式均应采取改进措施。
2.定量分析法
(1)故障模式频数比 故障模式频数比α:是产品故障表现为确定故障模式的比率。即产品的某一故障 模式占其全部故障模式的百分比率。如果考虑某产品所有可能的故障模式,则其 故障模式频数比之和将为1。
模式故障率λm:是指产品总故障率λp与某故障模式频数比α的乘积。
λm=α×λp
表6-10 双极型晶体管故障模式、频数比及其模式故障率
6.3.2 危害性矩阵法
定性分析法:不能获得准确的产品故障 定量分析法:可以获得产品的较为准确的故障数据
数据
1.定性分析法
GJB1391给出的一种定义:
A级:经常发生 >20% B级:有时发生 10% ~20% C级:偶然发生 1% ~10% D级:很少发生 0.1% ~1% E级:极少发生 <0.1%
图6-5中,故障模式M1比故障模式M2的危害性大。
6.3.3 危害性分析的实施 表6-12 危害性分析表
(3)故障模式危害度与产品危害度
1.故障模式危害度:评价单一故障模式危害性 Cm(j)=α×β×λp×t, j=Ⅰ,Ⅱ,Ⅲ,Ⅳ Cm(次j)代数表。了产品在工作时间t内以第i种故障模式发生第j类严酷度类别的故障
2.产品危害度:评价产品的危害性 Cr(j)= ∑Cmi(j) 式中:i=1,2,…,n; n为该产品在第j类严酷度类别下的故障模式总数; j=Ⅰ,Ⅱ,Ⅲ,Ⅳ Cr(j)代表了某一产品在工作时间t内产生的第j类严酷度类别的故障次数。
表6-9 检验难度评分准则
结论
1.故障发生可能性高、故障严重程度高,又难以检出的故障模式,其RPN值较高,从 而危害性较大。
2.对于危害性高的故障模式,应从降低故障发生可能性和故障严重程度及提高该故障 检出可能性三方面提出改进措施。
3.在利用RPN对故障模式进行评定时,可制定一个RPN的门限值,超过此门限值的故 障模式均应采取改进措施。
2.定量分析法
(1)故障模式频数比 故障模式频数比α:是产品故障表现为确定故障模式的比率。即产品的某一故障 模式占其全部故障模式的百分比率。如果考虑某产品所有可能的故障模式,则其 故障模式频数比之和将为1。
模式故障率λm:是指产品总故障率λp与某故障模式频数比α的乘积。
λm=α×λp
表6-10 双极型晶体管故障模式、频数比及其模式故障率
6.3.2 危害性矩阵法
定性分析法:不能获得准确的产品故障 定量分析法:可以获得产品的较为准确的故障数据
数据
1.定性分析法
GJB1391给出的一种定义:
A级:经常发生 >20% B级:有时发生 10% ~20% C级:偶然发生 1% ~10% D级:很少发生 0.1% ~1% E级:极少发生 <0.1%
图6-5中,故障模式M1比故障模式M2的危害性大。
6.3.3 危害性分析的实施 表6-12 危害性分析表
(3)故障模式危害度与产品危害度
1.故障模式危害度:评价单一故障模式危害性 Cm(j)=α×β×λp×t, j=Ⅰ,Ⅱ,Ⅲ,Ⅳ Cm(次j)代数表。了产品在工作时间t内以第i种故障模式发生第j类严酷度类别的故障
2.产品危害度:评价产品的危害性 Cr(j)= ∑Cmi(j) 式中:i=1,2,…,n; n为该产品在第j类严酷度类别下的故障模式总数; j=Ⅰ,Ⅱ,Ⅲ,Ⅳ Cr(j)代表了某一产品在工作时间t内产生的第j类严酷度类别的故障次数。
电子产品故障模式、影响及危害性分析(FMECA).ppt

FMECA是针对产品所有可能的故障,并根据对故障模式的分析,确定每 种故障模式对产品工作的影响,找出单点故障,并按故障模式的严重度及 其发生的概率确定其危害性。所谓单点故障指的是引起产品故障的,且没 有冗余或替代的工程程序作为补救的局部故障。FMECA包括故障模式及影 响分析(FMEA)和危害性分析(CA)。只有在进行FMEA的基础上,才能进行 CA。
2
故障模式、影响及危害性分析(FMECA)的目的和原则
实施FMECA的目的主要是: 1.对于处于开发过程中的产品,主要是在设计过程中找出系统方案的薄弱
环节,进而进行改进设计,使得系统的设计方案达到最优化,同时,可以对 系统可能出现的故障进行预计,在此基础上列出电路所有可能的失效模式。
2.对于已经发生的电路失效,要着重寻找发生失效的原因,分析和鉴定是 元器件的随机失效,还是电路、结构、工艺设计中的缺陷和错误,就可以采 取改进措施,达到设计固有可靠性目标和可靠性增长的目的。
主要内容
故障模式、影响及危害性分析(FMECA)的概念 故障模式、影响及危害性分析(FMECA)的目的和原则 故障模式、影响及危害性分析(FMECA)的方法 应力分析法实施步骤 硬元件分器析法件的计特点数如下法实施步骤 总结
1
故障模式、影响及危害性分析(FMECA)的概念
故障模式、影响及危害性分析(Failure Mode,Effects and Criticality Analysis, 简称FMECA)是在工程实践中总结出来的,以故障模式为基础,以故障影响 或后果为目标的分析技术。它通过逐一分析各组成部分的不同故障对系统工 作的影响,全面识别设计中的薄弱环节和关键项目,并为评价和改进系统设 计的可靠性提供基本信息。
FMECA的实施者需要对系统的硬件结构有着充分的了解,FMECA的实施 过程中应遵循边设计、边分析、边改进和“谁设计、谁分析”的原则。
2
故障模式、影响及危害性分析(FMECA)的目的和原则
实施FMECA的目的主要是: 1.对于处于开发过程中的产品,主要是在设计过程中找出系统方案的薄弱
环节,进而进行改进设计,使得系统的设计方案达到最优化,同时,可以对 系统可能出现的故障进行预计,在此基础上列出电路所有可能的失效模式。
2.对于已经发生的电路失效,要着重寻找发生失效的原因,分析和鉴定是 元器件的随机失效,还是电路、结构、工艺设计中的缺陷和错误,就可以采 取改进措施,达到设计固有可靠性目标和可靠性增长的目的。
主要内容
故障模式、影响及危害性分析(FMECA)的概念 故障模式、影响及危害性分析(FMECA)的目的和原则 故障模式、影响及危害性分析(FMECA)的方法 应力分析法实施步骤 硬元件分器析法件的计特点数如下法实施步骤 总结
1
故障模式、影响及危害性分析(FMECA)的概念
故障模式、影响及危害性分析(Failure Mode,Effects and Criticality Analysis, 简称FMECA)是在工程实践中总结出来的,以故障模式为基础,以故障影响 或后果为目标的分析技术。它通过逐一分析各组成部分的不同故障对系统工 作的影响,全面识别设计中的薄弱环节和关键项目,并为评价和改进系统设 计的可靠性提供基本信息。
FMECA的实施者需要对系统的硬件结构有着充分的了解,FMECA的实施 过程中应遵循边设计、边分析、边改进和“谁设计、谁分析”的原则。
潜在失效模式及后果分析教材(PPT 56页)
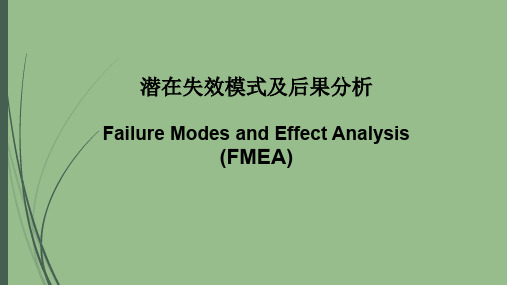
分析的程序(FMECA)于1949年11月9日出 版
• 一种值得信赖的确定系统和设备失效的评估 技术
FMEA 过程
确保在整个产品和过程开发过程中潜在的问题得到 考虑和处理的一种分析方法
风险评估是FMEA方法的一部分
FMEA成功实施的关键因素是及时性,它必须是“事 前”行为,绝非“事后”联系
需要时停止车辆(考虑环境 pavement within specified
车辆超出规定的停止距离 Vehicle stops in excess of specified distance
车辆控制削弱,违反法规 Vehicle control impaired, Regulatory non-compliance
“9”进行修改
• 本栏目用于标识高优先度的失效模式及其相关原因 • 在小组成员开展分析后,本栏目的内容和信息可用于识别特殊特性 • 如果已知时,可以使用客户指定的符号
到了部分阻碍 Activate with no Decreased pad life; diminished vehicle
demand, Vehicle movement is control
vehicle movement on no system denad
在不需要系统时,车辆不能行 驶 Activate with no demand, vehicle cannot move
Function
在规定的距离和规定制动 车辆没有停下来 Vehicle does 车辆控制削弱,违反法规 Vehicle control
压力条件下能够停止车辆 not stop
impaired, Regulatory non-compliance
的行驶 Stop vehicle
• 一种值得信赖的确定系统和设备失效的评估 技术
FMEA 过程
确保在整个产品和过程开发过程中潜在的问题得到 考虑和处理的一种分析方法
风险评估是FMEA方法的一部分
FMEA成功实施的关键因素是及时性,它必须是“事 前”行为,绝非“事后”联系
需要时停止车辆(考虑环境 pavement within specified
车辆超出规定的停止距离 Vehicle stops in excess of specified distance
车辆控制削弱,违反法规 Vehicle control impaired, Regulatory non-compliance
“9”进行修改
• 本栏目用于标识高优先度的失效模式及其相关原因 • 在小组成员开展分析后,本栏目的内容和信息可用于识别特殊特性 • 如果已知时,可以使用客户指定的符号
到了部分阻碍 Activate with no Decreased pad life; diminished vehicle
demand, Vehicle movement is control
vehicle movement on no system denad
在不需要系统时,车辆不能行 驶 Activate with no demand, vehicle cannot move
Function
在规定的距离和规定制动 车辆没有停下来 Vehicle does 车辆控制削弱,违反法规 Vehicle control
压力条件下能够停止车辆 not stop
impaired, Regulatory non-compliance
的行驶 Stop vehicle
第六章失效模式、效应及危害度分析(FMECA)和故障树分析法(FTA).

率来评价FMEA 中确定的失效模式。
3.2
失效模式发生的概率等级可按以下方法划分:
A级:经常发生的事件,概率P>20%; B级:很可能发生的事件,10%<P<20%; C级:偶然发生的事件,1%<P<10%; D级:很少发生的事件,0.1%<P<1%; E级:极不可能发生的事件,0<P<0.1%;
②定量分析方法——危害度Cm计算
第六章失效模式、效应及危害度分析(FMECA)和 故障树分析法(FTA)
§6-1 FMEA与FTA分析方法概述 §6-2 故障模式与影响分析(FMEA) §6-3 危害性分析(CA) §6-4 对FMECA的评价 §6-5 故障树的建立 §6-6 故障树的定性分析 §6-7 故障树的定量分析
§6-1 FMECA与FTA分析方法概述
4.FMEA及FMECA的分析方法
1)表格分析法 2矩阵分析法(本书不详细介绍)
• 表格法是利用表格列出各单元故障模式,再通过故障模 式分析找出由此产生的后果
• 具体步骤:
• (1)绘制分级功能框图
• (2)对分级功能图中的每一个方框,自下而上逐级进行 FMECA分析,指出被分析方框对高一级的隶属等级产的 影响
4. 严酷度分类
2.3
对失效造成的后果的严重程度进行分类,是较笼统的、定性的分类。
Ⅰ类(灾难性的)——会引起人员死亡或系统毁坏的失效(机毁人亡)。
Ⅱ类(致命性的)——会引起人员严重伤亡、重大财产损失或导致任务失 败的系统严重失效。
Ⅲ类(临界的)——会引起人员的轻度损伤、一定人的财产损失或导致任 务延误或降级的系统轻度损坏。
Ⅰ、Ⅱ类故障,单点故障清单;
(单点故障指能导致系统失效的某一产品失效,即处于串联系统中的
3.2
失效模式发生的概率等级可按以下方法划分:
A级:经常发生的事件,概率P>20%; B级:很可能发生的事件,10%<P<20%; C级:偶然发生的事件,1%<P<10%; D级:很少发生的事件,0.1%<P<1%; E级:极不可能发生的事件,0<P<0.1%;
②定量分析方法——危害度Cm计算
第六章失效模式、效应及危害度分析(FMECA)和 故障树分析法(FTA)
§6-1 FMEA与FTA分析方法概述 §6-2 故障模式与影响分析(FMEA) §6-3 危害性分析(CA) §6-4 对FMECA的评价 §6-5 故障树的建立 §6-6 故障树的定性分析 §6-7 故障树的定量分析
§6-1 FMECA与FTA分析方法概述
4.FMEA及FMECA的分析方法
1)表格分析法 2矩阵分析法(本书不详细介绍)
• 表格法是利用表格列出各单元故障模式,再通过故障模 式分析找出由此产生的后果
• 具体步骤:
• (1)绘制分级功能框图
• (2)对分级功能图中的每一个方框,自下而上逐级进行 FMECA分析,指出被分析方框对高一级的隶属等级产的 影响
4. 严酷度分类
2.3
对失效造成的后果的严重程度进行分类,是较笼统的、定性的分类。
Ⅰ类(灾难性的)——会引起人员死亡或系统毁坏的失效(机毁人亡)。
Ⅱ类(致命性的)——会引起人员严重伤亡、重大财产损失或导致任务失 败的系统严重失效。
Ⅲ类(临界的)——会引起人员的轻度损伤、一定人的财产损失或导致任 务延误或降级的系统轻度损坏。
Ⅰ、Ⅱ类故障,单点故障清单;
(单点故障指能导致系统失效的某一产品失效,即处于串联系统中的
- 1、下载文档前请自行甄别文档内容的完整性,平台不提供额外的编辑、内容补充、找答案等附加服务。
- 2、"仅部分预览"的文档,不可在线预览部分如存在完整性等问题,可反馈申请退款(可完整预览的文档不适用该条件!)。
- 3、如文档侵犯您的权益,请联系客服反馈,我们会尽快为您处理(人工客服工作时间:9:00-18:30)。
运输中损坏 搬运中损坏
内压过高
导弹毁坏
推进剂 药柱
断裂 孔穴 粘接面分离
固化残余应力 温度过低 老化
燃烧速度过 高;内压过 高;机壳在 工作过程中 破裂
内衬
与外壳分离
与药柱或隔 热层分离
粘接剂不良 粘接控制不良
壳体成形后净 化不够
燃烧速度过 高;内压过 高;机壳在 工作过程中 破裂
发生概 严重性 率
7
输 入 原 始 资 料
分析 系统 结构 及各 组成 部分 功用
构造 系统 的可 靠性 框图
列出各 功能级 的失效 模式机 理效应
研究 失效 检测 方法
可 能 的 预 防 措 施
致命性 分析
失效模 式概率
致命度 的估计
输出填写
FMECA 表格
FMECA分析过程
8
பைடு நூலகம்
零件材料失效原因的分类
机械因子 弹性变形、塑性变形、蠕变、疲劳、断裂、滑移
E级,极少发生。单一失效模式发生概率小于系统总失效 概率 的0.1%。
17
二、定量分析 1、失效后果概率
失效后果 必然损失 偶然损失 很少损失 无影响
值
1.0
0.1 1.0 0 0.1
0
2、失效模式严重度数字 Cm Pt 106 失效率后果 P 元件失效率×10-6/h为单位 t 任务阶段内的工作时间 失效模式相对频率
1.5
氧化
-
-
-
-
-
绝缘
-
-
1.6
-
12.3
裂痕
0.5
-
-
-
-
磨损
60.2 83.4 8.1
60
25.1
断裂
-
10.0 47.1
20
4.6
其它
-
-
11.5
-
16.1
电位器 27.5 10 25 15 22.5
继电器 12.3 0.4 2.3 2.6 12.3 2.4 17.5 11.9
5
§2 失效模式与后果分析
可能措施
0.0006
严重
严格控制原材料质 量,消除缺陷。进 行耐压试验,采用 合理包装,在运输 中保护发动机
0.0001
严重
严格控制生产过程 ,确保工艺质量, 严格控制在极限温 度之内存储和使用 。
0.0001
严重
严格执行正常清洗 程序,机巧清洗后 严格检验,确保清 除一切沾染物
12
FMECA分析的用途
导致系统功能失效,造成系统或环境重大损失,导致人员伤亡。 能导致系统功能失效,造成系统或环境重大损失,不导致人员 伤亡。 导致系统功能下降,对系统或环境均无显著损害。
导致系统功能下降,对系统或环境均无害。
3
故障模式的分类
1、损坏型故障模式:裂纹、塑性变形、断裂等 2、退化型故障模式:老化、变质、表面防护脱落等 3、松脱型故障模式:松动、脱开、脱焊等 4、失调型故障模式:间隙不适、流量不当、压力不当等 5、堵塞和渗漏型故障模式:堵、渗、漏等 6、功能型故障模式:功能不正常、功能不稳定等 7、其它类型故障模式:润滑不良等
2
失效等级:
故障类型 1 致命故障
2 严重故障 3 一般故障 4 轻微故障
分类原则 导致人身伤亡、重要总成报废、重大经济损失或对 环境造成重大危害。 导致重要总成、零部件损坏,且不可能在短时间内 修复。 导致性能下降,在短时间内修复
一般随车工具在短时间可以修复
失效等级 I II II I IV
严重程度
FMECA
FMEA 失效模式与后果分析 CA 严重度分析
一、FMEA
1、功能FMEA和硬件FMEA 功能FMEA
设计初期 复杂系统
硬件FMEA
6
2、FMEA 程序 FMEA基本程序: 1、确定失效模式 2、绘制系统功能图和可靠性框图 3、确定工作参数和功能 4、查明所有失效模式、发生原因及后果 5、按可能的最坏后果评定失效模式的严重性级别 6、确定失效模式的检测方法及补救预防措施 7、提出修改方案及其他措施 8、提交分析报告
机械磨损
接触不良
平衡状态破坏
相变化、应力松弛
化学反应
腐蚀、氧化、
电应力
电介质击穿、脉冲
热应力
摩擦
渗透
湿气、气体、流体
9
断裂分类: 根据裂纹发展过程 沿晶断裂 穿晶断裂 根据受载性质 疲劳断裂 静载断裂 冲击断裂 根据完全断裂前的宏观变形 脆性断裂 韧性断裂
10
疲劳断裂原因:
疲劳源
裂纹扩 展区
载荷因素: 载荷性质、大小、变化速度等
18
3、产品严重度数字
n
Cr (Pt 106 )
i 1
i 属于某一严重度的失效模式数 n 产品在该严重度下的最后一个失效模式
失效模式、后果与严重度分析 (FMECA)
Failure Mode Effect and Criticality Analysis §1 概述 §2 失效模式与后果分析 §3 严重度分析
1
§1 概述
失效的定义: 1、设备在规定条件下,不能完成其规定的功能; 2、设备在规定条件下,一个或几个不能达到其规定值; 3、由于环境应力变化,导致功能丧失; 4、即使设备在规定条件下具有完成规定功能的能力 ,但因操作者的失误而造成产品功能丧失;
1、在设计管理上的用途
FMECA与线路应力分析的结合是可靠性预测、分配和评定 时的一项原始资料。 FMECA 是评定设计方案的手段 FMECA 是设计评审、质量复查、事故预想的依据和证明 2、在其他用途
安排测试点、制造和质量控制,制定试验计划的一种依据。
制定检测程序、设计诊断装置的基础。 与试验结果和失效分析报告一起进行定性评定。 可靠性维修,后勤保障分析的原始资料。
瞬断区
材质因素:材料的成分、机械性能、冶金特性等 表面因素:表面粗糙度、划痕、碰伤等
几何因素:圆角、倒角等
环境因素:环境介质、环境温度等
11
FMECA分析实例1
例 某一固体火箭发动机由推进剂药柱、内衬和发动机壳组成。绘制其 失效模式后果分析表
项目 失效模式
失效原因
可能后果
发动机 壳
破裂
工艺质量差 材料缺陷
13
14
15
16
§4.3 严重度分析
一、定性分析
A级,常发生。单一失效模式发生概率大于系统总失效 概率的20%。
B级,较常发生。单一失效模式发生概率在系统总失效 概率的10%~20%。
C级,偶尔发生。单一失效模式发生概率在系统总失效 概率的1%~10%。
D级,很少发生。单一失效模式发生概率在系统总失效 概率的0.1%~1%。
故障模式的比率
故障模式比率——产品出现失效模式的百分比
进一步分析失效原因,采取预防措施的可靠依据
4
几种机械零部件的失效模式及其比率
轴承 离合器 连接器 齿轮 发电机
腐蚀
18.7
-
6.3
-
6.3
蠕变
-
-
-
-
-
形变
2.5
6.6
23.7
20
2.1
侵蚀
3.1
-
-
-
-
疲劳
4.4
-
1.7
-
-
摩擦
10.6
-
-
-
内压过高
导弹毁坏
推进剂 药柱
断裂 孔穴 粘接面分离
固化残余应力 温度过低 老化
燃烧速度过 高;内压过 高;机壳在 工作过程中 破裂
内衬
与外壳分离
与药柱或隔 热层分离
粘接剂不良 粘接控制不良
壳体成形后净 化不够
燃烧速度过 高;内压过 高;机壳在 工作过程中 破裂
发生概 严重性 率
7
输 入 原 始 资 料
分析 系统 结构 及各 组成 部分 功用
构造 系统 的可 靠性 框图
列出各 功能级 的失效 模式机 理效应
研究 失效 检测 方法
可 能 的 预 防 措 施
致命性 分析
失效模 式概率
致命度 的估计
输出填写
FMECA 表格
FMECA分析过程
8
பைடு நூலகம்
零件材料失效原因的分类
机械因子 弹性变形、塑性变形、蠕变、疲劳、断裂、滑移
E级,极少发生。单一失效模式发生概率小于系统总失效 概率 的0.1%。
17
二、定量分析 1、失效后果概率
失效后果 必然损失 偶然损失 很少损失 无影响
值
1.0
0.1 1.0 0 0.1
0
2、失效模式严重度数字 Cm Pt 106 失效率后果 P 元件失效率×10-6/h为单位 t 任务阶段内的工作时间 失效模式相对频率
1.5
氧化
-
-
-
-
-
绝缘
-
-
1.6
-
12.3
裂痕
0.5
-
-
-
-
磨损
60.2 83.4 8.1
60
25.1
断裂
-
10.0 47.1
20
4.6
其它
-
-
11.5
-
16.1
电位器 27.5 10 25 15 22.5
继电器 12.3 0.4 2.3 2.6 12.3 2.4 17.5 11.9
5
§2 失效模式与后果分析
可能措施
0.0006
严重
严格控制原材料质 量,消除缺陷。进 行耐压试验,采用 合理包装,在运输 中保护发动机
0.0001
严重
严格控制生产过程 ,确保工艺质量, 严格控制在极限温 度之内存储和使用 。
0.0001
严重
严格执行正常清洗 程序,机巧清洗后 严格检验,确保清 除一切沾染物
12
FMECA分析的用途
导致系统功能失效,造成系统或环境重大损失,导致人员伤亡。 能导致系统功能失效,造成系统或环境重大损失,不导致人员 伤亡。 导致系统功能下降,对系统或环境均无显著损害。
导致系统功能下降,对系统或环境均无害。
3
故障模式的分类
1、损坏型故障模式:裂纹、塑性变形、断裂等 2、退化型故障模式:老化、变质、表面防护脱落等 3、松脱型故障模式:松动、脱开、脱焊等 4、失调型故障模式:间隙不适、流量不当、压力不当等 5、堵塞和渗漏型故障模式:堵、渗、漏等 6、功能型故障模式:功能不正常、功能不稳定等 7、其它类型故障模式:润滑不良等
2
失效等级:
故障类型 1 致命故障
2 严重故障 3 一般故障 4 轻微故障
分类原则 导致人身伤亡、重要总成报废、重大经济损失或对 环境造成重大危害。 导致重要总成、零部件损坏,且不可能在短时间内 修复。 导致性能下降,在短时间内修复
一般随车工具在短时间可以修复
失效等级 I II II I IV
严重程度
FMECA
FMEA 失效模式与后果分析 CA 严重度分析
一、FMEA
1、功能FMEA和硬件FMEA 功能FMEA
设计初期 复杂系统
硬件FMEA
6
2、FMEA 程序 FMEA基本程序: 1、确定失效模式 2、绘制系统功能图和可靠性框图 3、确定工作参数和功能 4、查明所有失效模式、发生原因及后果 5、按可能的最坏后果评定失效模式的严重性级别 6、确定失效模式的检测方法及补救预防措施 7、提出修改方案及其他措施 8、提交分析报告
机械磨损
接触不良
平衡状态破坏
相变化、应力松弛
化学反应
腐蚀、氧化、
电应力
电介质击穿、脉冲
热应力
摩擦
渗透
湿气、气体、流体
9
断裂分类: 根据裂纹发展过程 沿晶断裂 穿晶断裂 根据受载性质 疲劳断裂 静载断裂 冲击断裂 根据完全断裂前的宏观变形 脆性断裂 韧性断裂
10
疲劳断裂原因:
疲劳源
裂纹扩 展区
载荷因素: 载荷性质、大小、变化速度等
18
3、产品严重度数字
n
Cr (Pt 106 )
i 1
i 属于某一严重度的失效模式数 n 产品在该严重度下的最后一个失效模式
失效模式、后果与严重度分析 (FMECA)
Failure Mode Effect and Criticality Analysis §1 概述 §2 失效模式与后果分析 §3 严重度分析
1
§1 概述
失效的定义: 1、设备在规定条件下,不能完成其规定的功能; 2、设备在规定条件下,一个或几个不能达到其规定值; 3、由于环境应力变化,导致功能丧失; 4、即使设备在规定条件下具有完成规定功能的能力 ,但因操作者的失误而造成产品功能丧失;
1、在设计管理上的用途
FMECA与线路应力分析的结合是可靠性预测、分配和评定 时的一项原始资料。 FMECA 是评定设计方案的手段 FMECA 是设计评审、质量复查、事故预想的依据和证明 2、在其他用途
安排测试点、制造和质量控制,制定试验计划的一种依据。
制定检测程序、设计诊断装置的基础。 与试验结果和失效分析报告一起进行定性评定。 可靠性维修,后勤保障分析的原始资料。
瞬断区
材质因素:材料的成分、机械性能、冶金特性等 表面因素:表面粗糙度、划痕、碰伤等
几何因素:圆角、倒角等
环境因素:环境介质、环境温度等
11
FMECA分析实例1
例 某一固体火箭发动机由推进剂药柱、内衬和发动机壳组成。绘制其 失效模式后果分析表
项目 失效模式
失效原因
可能后果
发动机 壳
破裂
工艺质量差 材料缺陷
13
14
15
16
§4.3 严重度分析
一、定性分析
A级,常发生。单一失效模式发生概率大于系统总失效 概率的20%。
B级,较常发生。单一失效模式发生概率在系统总失效 概率的10%~20%。
C级,偶尔发生。单一失效模式发生概率在系统总失效 概率的1%~10%。
D级,很少发生。单一失效模式发生概率在系统总失效 概率的0.1%~1%。
故障模式的比率
故障模式比率——产品出现失效模式的百分比
进一步分析失效原因,采取预防措施的可靠依据
4
几种机械零部件的失效模式及其比率
轴承 离合器 连接器 齿轮 发电机
腐蚀
18.7
-
6.3
-
6.3
蠕变
-
-
-
-
-
形变
2.5
6.6
23.7
20
2.1
侵蚀
3.1
-
-
-
-
疲劳
4.4
-
1.7
-
-
摩擦
10.6
-
-
-