COUPLING
Coupling,各种联轴器,英文版的

Shaft couplings will be used under the following conditions: 1. With shafts having collinear axis, that is, axis in the same straight line, rigid or flexible couplings of various form are used. 2. With shafts having intersecting axis, a Universal Coupling is employed. 3. With shafts whose axes are parallel and at a relatively small distance apart, the double slider crank principle of mechanism is used. A shaft coupling should have the following requirements: 1. It should be easy to connect or disconnect. 2. It should transmit the full power of the shaft. 3. it should hold the shafts in perfect alignment. 4. It should have no projecting parts.
This flexible-disk coupling contains at least one disk attached at its outside to one of the two rotary parts connected therewith and is splined adjacent its inside periphery to the other of said parts. The splines let the disk expand naturally under centrifugal stress, independently of said other part. They have preferably straight radical profiles, so that the increased expansion of the disk avoids backlash. The couplings may be used in pairs, as common-place, or also singly. The flexible disks are subjected to various stresses, of which the stress set up by centrifugal inertia is a major component. It is customary to rigidly weld the disks at their inner portion to one of the two parts connected by the coupling. The invention departs from this custom. It lets the disks expand naturally without being tied to the expansion of said one part. As this decreases the stress on the disks it enables them to carry increased load.
偶合器(Coupling)-联轴器

偶合器(Coupling)偶合器(Coupling)是利用某种介质,将原动机的动力传给从动机的机械装置。
以液体为工作介质的一种非刚性联轴器,又称联轴器。
性能1、具有减缓冲击和隔离扭振的性能;可以使电机起动有一个延迟时间,缓慢加速,减少骤然起动而引起的零件间的相互冲击。
2、具有使电机轻载起动性能:由于偶合器的泵轮力矩与其转速的平方成正比,故当起动瞬间泵轮因转速低而力矩甚微,电机近似于带泵轮空载起动,所以起动时间短,起动电流小,起动平稳,尤其适合起动大惯量沉重负载。
3、具有过载保护性能:由于偶合器无机械直接连接,当外负荷超过一定限度后,泵轮力矩便不再上升,此时电机照常转动,输出减速直至停止,从电源吸取的功率转化为热能使偶合器升温,直至易熔塞喷液,从而输入与输出被切断,保护了电机,工作机不受损坏,从而降低了机器故障率,维护费用和停工时间,延长了电机荷工作机使用寿命。
4、具有节电的性能:由于偶合器有效地解决了电机起动和“大马拉小车”的现象,与刚性传动相比至少可降低一个电机机座号,加上可以降低起动电流和持续时间,降低对电网的冲击节能率达10—20%,尤其在起动大惯量沉重负载时更为显著。
限矩型液力偶合器的特点:除轴承和油封外,无任何机械磨檫,使用寿命长,故障率低,不需特殊维护保养。
常见类型编辑液力偶合器的实质是离心泵与涡轮机的组合。
主要由输入轴、输出轴、泵轮、涡轮、外亮、辅室及安全保护装置等构成。
输入轴一端与动力机相连,另一端与泵鸵相连:输出轴一端与涡轮相连,另一端与工作机相连。
泵轮与涡轮对称布置,轮内布置一定数量的叶片。
外亮与泵轮固联成密封腔,腔内充填工作液体以传递动力;当原动机通过输入轴带动泵轮旋转时,充填在工作腔内的工作液体受离心力和工作轮叶片的作用由半径较小的泵轮入口被加速加压抛向半径较大的泵轮出口,同时液体的动量矩产生增量,即偶合器泵轮将输入的机械能转化成了液体动能:当携带液体动能的工作液体由泵轮出口冲向对面的涡轮时,液流便沿涡鸵叶片所形成的流道做向心流动,同时释放液体动能转化成机械能驱动涡轮旋转并带动负载做功。
coupling分为两种:运动耦合和分布耦合

coupling分为两种:运动耦合和分布耦合coupling分为两种:运动耦合和分布耦合;是对接触问题的⼀种简化⽅式,⼀般来讲,分布耦合处的刚度⼩于运动耦合处的刚度;【1】运动耦合:即在此区域的各节点与参考点之间建⽴⼀种运动上的约束关系。
【2】分布耦合:在此区域的各节点与参考点之间建⽴⼀种约束关系,但是对此区域上各节点的运动进⾏了加权处理,使在此区域上受到的合⼒和合⼒距与施加在参考点上的⼒和⼒矩相等效。
换⾔之,分布耦合允许⾯上的各部分之间发⽣相对变形,⽐运动耦合中的⾯更柔软。
31.3.2 Coupling constraintsProducts: Abaqus/Standard Abaqus/Explicit Abaqus/CAEReferences“Surfaces: overview,” Section 2.3.1*COUPLING*KINEMATIC*DISTRIBUTING“Defining coupling constraints,” Section 15.15.4 of the Abaqus/CAE User's ManualOverviewThe surface-based coupling constraint:couples the motion of a collection of nodes on a surface to the motion of a reference node;is of type kinematic when the group of nodes is coupled to the rigid body motion defined by the reference node;is of type distributing when the group of nodes can be constrained to the rigid body motion defined by a reference node in an average sense by allowing control over the transmission of forces through weight factors specified at the coupling nodes;automatically selects the coupling nodes located on a surface lying within a region of influence;can be used with two- or three-dimensional stress/displacement elements; andcan be used in geometrically linear and nonlinear analysis.Surface-based coupling definitionsThe surface-based coupling constraint in Abaqus provides coupling between a reference node and a group of nodes referred to as the “coupling nodes.” This option provides the same functionality as the kinematic coupling constraint and the distributing coupling elements (DCOUP2D, DCOUP3D) in Abaqus/Standard with a surface-based user interface. The coupling nodes are selected automatically by specifying a surface and an optional influence region. The procedure used to define the coupling nodes is discussed below.For a distributing coupling constraint, the distributing weight factors are calculated automatically if the surface is an element-based surface. In such a case the weight factors are based on the tributary area at each coupling node, except for a surface along a shell edge, where the weight factors are based on the tributary edge length. Furthermore, the distributing weight factors can be modified using one of several weighting methods, which allow the forces transferred to the coupling nodes to vary inversely with the radial distance from the reference node.Typical applicationsThe coupling constraint is useful when a group of coupling nodes is constrained to the rigid body motion of a single node. The coupling constraint can be employed effectively in the following applications:To apply loads or boundary conditions to a model. Figure 31.3.2–1 illustrates the use of a kinematic coupling constraint to prescribe a twisting motion to a model without constraining the radial motion.Figure 31.3.2–1 Kinematic coupling constraint.Figure 31.3.2–2 illustrates a distributing coupling constraint used to prescribe a displacement and rotation condition ona boundary where relative motion between the nodes on the boundary is required. In this example a twist is prescribedat the end of the structure that is expected to warp and/or deform within the end surface.Figure 31.3.2–2 Distributing coupling constraint.To distribute loads on a model, where the load distribution can be described with a moment-of-inertia expression.Examples of such cases include the classic bolt-pattern and weld-pattern distribution expressions.To apply dimensionality transitions between continuum and structural elements. For example, a distributing coupling allows flexible coupling between structural and solid elements.To model end conditions. For example, modeling a rigid end plate or modeling plane sections of a solid to remain planar can be done easily with a kinematic coupling definition.To simplify modeling of complex constraints. In a kinematic coupling definition the degrees of freedom that participate in the constraint may be selected individually in a local coordinate system.To model interactions with other constraints, such as connector elements. For example, a hinged part may be modeled more realistically by two distributing coupling definitions, whose reference nodes are connected by a hinge connector element. The load transfer then occurs between two “clouds” of nodes, rather than between two single nodes.“Substructure analysis of a one-piston engine model,” Section 4.1.10 of the Abaqus Example Problems Manual,illustrates this use of connector elements in conjunction with coupling constraints to model a one-piston engine. Defining the coupling constraintDefining a coupling constraint requires the specification of the reference node (also called the constraint control point), the coupling nodes, and the constraint type. The coupling constraint associates the reference node with the coupling nodes. A name must be assigned to the constraint and may be used in postprocessing with Abaqus/CAE. A node number or node set name may be specified for the reference node. If a node set is specified, the node set must contain exactly one node. The reference node for a kinematic coupling constraint has both translational and rotational degrees of freedom. The surface on which the coupling nodes are located can be node-based; element-based; or, in Abaqus/Explicit, a combination of both surface types. You can specify an optional radius of influence that limits the coupling nodes to a specific region on the surface. Details on how coupling nodes are defined by specifying an influence region are discussed below.The constraint type can be either kinematic or distributing, as discussed below.Input File Usage:Use the following options:*COUPLING, CONSTRAINT NAME=name, REF NODE=n,SURFACE=surface*KINEMATIC or*DISTRIBUTINGAbaqus/CAE Usage:Interaction module: Create Constraint: Coupling: Coupling type: Kinematic or DistributingSpecifying a region of influenceBy default, coupling nodes belonging to the entire surface are selected for the coupling definition. You can limit the coupling nodes to lie within a spherical region centered about the reference node by defining a radius of influence.The procedure by which coupling nodes are selected for the constraint definition depends on the surface type:For a node-based surface, all the nodes defined by the surface definition that fall within the influence region areselected for the coupling definitions.For an element-based surface, the surface facets that are either fully or partially inscribed by the influence region are determined. All nodes belonging to these facets, whether or not these nodes fall within the influence region, areselected for the coupling nodes. When the influence radius is less than the distance to the closest coupling node, Abaqus selects all nodes belonging to the closest facet. If the projection of the reference node on the surface falls on an edge or a vertex of multiple facets, all nodes belonging to these facets adjoining the edge or vertex are included in the coupling definition.A distributing coupling constraint must include at least two coupling nodes. If fewer than two coupling nodes are found,Abaqus issues an error message during input file preprocessing.Input File Usage:*COUPLING, CONSTRAINT NAME=name, REF NODE=n,SURFACE=surface, INFLUENCE RADIUS=rAbaqus/CAE Usage:Interaction module: Create Constraint: Coupling: Influence radius: SpecifyKinematic coupling constraintsKinematic coupling constrains the motion of the coupling nodes to the rigid body motion of the reference node. The constraint can be applied to user-specified degrees of freedom at the coupling nodes with respect to the global or a local coordinate system.Kinematic constraints are imposed by eliminating degrees of freedom at the coupling nodes. In Abaqus/Standard once any combination of displacement degrees of freedom at a coupling node is constrained, additional displacement constraints—such as MPCs, boundary conditions, or other kinematic coupling definitions—cannot be applied to any coupling node involved in a kinematic coupling constraint. The same limitation applies for rotational degrees of freedom. This restriction does not apply in Abaqus/Explicit. See “Kinematic constraints: overview,” Section 31.1.1, for more information.Input FileUsage:Use both of the following options to define a kinematic coupling constraint:*COUPLING*KINEMATICfirst dof, last dofFor example, the following coupling constraint is used to constrain degrees of freedom 1, 2, and 6 on surfacesurfA to reference node 1000:*COUPLING, CONSTRAINT NAME=C1, REF NODE=1000, SURFACE=surfA*KINEMATIC1, 26,Abaqus/CAE Usage:Interaction module: Create Constraint: Coupling: Coupling type: Kinematic: toggle on the degrees of freedomTranslational degrees of freedomTranslational degrees of freedom are constrained by eliminating the specified degrees of freedom at the coupling nodes. When all translational degrees of freedom are specified, the coupling nodes follow the rigid body motion of the reference node.Rotational degrees of freedomRotational degrees of freedom are constrained by eliminating the specified degrees of freedom at the coupling nodes. All combinations of selected rotational degrees of freedom result in rotational behavior identical to existing MPC types: Selection of three rotational degrees of freedom along with three displacement degrees of freedom is equivalent to MPC type BEAM.Selection of two rotational degrees of freedom is equivalent to MPC type REVOLUTE in Abaqus/Standard.Selection of one rotational degree of freedom is equivalent to MPC type UNIVERSAL in Abaqus/Standard.In Abaqus/Standard internal nodes are created by the kinematic coupling to enforce the constraints that are equivalent to MPC types REVOLUTE and UNIVERSAL. These nodes have the same degrees of freedom as the additional nodes used in these MPC types and are included in the residual check for nonlinear analysis.Specifying a local coordinate systemThe kinematic coupling constraint can be specified with respect to a local coordinate system instead of the global coordinate system (see “Orientations,” Section 2.2.5). Figure 31.3.2–1 illustrates the use of a local coordinate system to constrain all but the radial translation degrees of freedom of the coupling nodes to the reference node. In this example a local cylindrical coordinate system is defined that has its axis coincident with the structure's axis. The coupling node constraints are then specified in this local coordinate system.Input File*COUPLING, ORIENTATION=localUsage:For example, the following input is used to specify the kinematic coupling constraint shown in Figure31.3.2–1:*ORIENTATION, SYSTEM=CYLINDRICAL, NAME=COUPLEAXIS0.0, -1.0, 0.0, 0.0, 1.0, 0.0*COUPLING, REF NODE=500, SURFACE=Endcap,ORIENTATION=COUPLEAXIS*KINEMATIC2, 3Abaqus/CAE Usage:Interaction module: Create Constraint: Coupling: Edit: select local coordinate systemConstraint direction and finite rotationIn geometrically nonlinear analysis steps the coordinate system in which the constrained degrees of freedom are specified will rotate with the reference node regardless of whether the constrained degrees of freedom are specified in the global coordinate system or in a local coordinate system.Distributing coupling constraintsDistributing coupling constrains the motion of the coupling nodes to the translation and rotation of the reference node. This constraint is enforced in an average sense in a way that enables control of the transmission of loads through weight factors at the coupling nodes. Forces and moments at the reference node are distributed either as a coupling node-force distribution only (default) or as a coupling node-force and moment distribution. The constraint distributes loads such that the resultants of the forces (and moments) at the coupling nodes are equivalent to the forces and moments at the reference node. For cases of more than a few coupling nodes, the distribution of forces/moments is not determined by equilibrium alone, and distributing weight factors are used to define the force distribution.The moment constraint between the rotation degrees of freedom at the reference node and the average rotation of the cloud nodes can be released in one direction in a two-dimensional analysis and one, two, or three directions in a three-dimensional analysis. In a three-dimensional analysis you can specify the moment constraint directions in the global coordinate system or in a local coordinate system. All available translational degrees of freedom at the reference node are always coupled to the average translation of the coupling nodes.In a three-dimensional Abaqus/Standard analysis if all three moment constraints are released by specifying only degrees of freedom 1 through 3, only translation degrees of freedom will be activated on the reference node. If only one or two rotation degrees of freedom have been released, all three rotation degrees of freedom are activated at the reference node. In this case you must ensure that proper constraints have been placed on the unconstrained rotation degrees of freedom to avoid numerical singularities. Most often this is accomplished by using boundary conditions or by attaching the reference node to an element such as a beam or shell that will provide rotational stiffness to the unconstrained rotation degrees of freedom.In Abaqus/Explicit releasing one or more of the moment constraints may lead to significant computational performance degradation. This is also the case when other constraints intersect the cloud of coupling nodes. In these cases, the degradation in performance is particularly noticeable when a large number of such distributed couplings are present in the model or when the size of the constrained “cloud” is large. For that matter, when the modeling conditions mentioned above are encountered, the size of the coupling nodes cloud is limited to 1000. To alleviate the released moment constraint issue,the following modeling technique can be used (also available in Abaqus/Standard): constrain all moments in the distributed coupling and use an appropriate connector element at the reference node (such as REVOLUTE, HINGE, CARDAN or BUSHING) to model released moments at the coupling's reference node. This technique has also the advantage of being able to specify finite compliance such as elasticity, plasticity or damage in the “released” rotational component.Input FileUsage:*DISTRIBUTINGfirst dof , last dof If no degrees of freedom are specified, all available degrees of freedom are coupled. If you specify one or morerotation degrees of freedom but not all available translation degrees of freedom, Abaqus issues a warning message and adds all available translation degrees of freedom to the constraint.For example, the following coupling constraint is used to constrain degrees of freedom 1–5 on the reference node1000 to the average translation and rotation of surface surfA :*COUPLING , CONSTRAINT NAME=C1, REF NODE=1000, SURFACE=surfA *DISTRIBUTING1, 5In this example the moment constraint between the reference node and the coupling nodes will be released in the 6-direction but will be enforced in the 4- and 5-directions. This provides a “revolute-like” rotation connection between the reference node and the coupling nodes (see “General multi-point constraints,” Section 31.2.2).Abaqus/CAE Usage:Interaction module: Create Constraint : Coupling : Coupling type : Distributing : toggle on the rotational degrees of freedom (Abaqus/CAE automatically constrains the translational degrees of freedom)Node-based surfaceUser-defined weight factors are used for node-based surfaces. The cross-sectional areas specified in the surface definition are used as the weight factors (see “Node-based surface definition,” Section 2.3.3).Element-based surfaceFor element-based surfaces the weight factors are calculated by Abaqus. The default weight distribution is based on the tributary surface area at each coupling node, except for a surface along a shell edge where the weight distribution is based on the tributary edge length. The procedure used to calculate the default weight factors is designed to ensure that if a radius of influence is prescribed, the default weight distribution varies smoothly with the influence radius.Calculating the default distributing weight factors The procedure to calculate the distributing weight factors depends on whether or not an influence radius is specified.If no influence radius is specified, the entire surface is used in the coupling definition. In this case all nodes located on the surface are included in the coupling definition and the distributing weight factor at each coupling node is equal to the tributary surface area.If an influence radius is specified, the default distributing weight factors at the coupling nodes are calculated as follows:1. A “participation factor” is calculated for each surface facet. The participation factor is defined below.2. The tributary nodal area (or tributary edge length along a shell edge) at each facet node is computed and ismultiplied by the facet participation factor.3. The coupling node distributing weight factor is computed as the sum of the corresponding facet nodal areas(calculated above) for all joining facets.Calculating the facet participation factorThe participation factor defines the proportion of the facet's area that contributes to the distributing weight factors when an influence radius is specified. The participation factor varies between zero and one.To define the participation factor, the distance of the facet node closest to the reference node, , and the distance of the facet node farthest from the reference node, , are calculated.If , where is the influence radius, all facet nodes lie within the influence region; and a participation factor of one is used.If , none of the facet nodes lie within the influence region; and the participation factor is set to zero.If , the facet is partially inscribed in the influence region; and the facet is assigned a participation factor equal to .If all coupling nodes fall outside the influence radius (i.e., for all facets), Abaqus selects all nodes belonging to the closest facets (as outlined under “Specifying a region of influence”) and uses a participation factor equal to one.Weighting methodsYou can modify the default weight distribution defined above. Various weighting methods are provided that monotonically decrease with radial distance from the reference node. For each case the default weight distribution that is based on the tributary surface area (or tributary edge length along a shell edge) is scaled by the weight factor . If the weighting method is not specified, a uniform weighting method is used in which all weight factors are equal to 1.0.Linearly decreasing weight distributionA linearly decreasing weighting schemewhere is the weight factor at coupling node i, is the coupling node radial distance from the reference node, and is the distance to the furthest coupling node.Input File Usage:*DISTRIBUTING, WEIGHTING METHOD=LINEARAbaqus/CAE Usage:Interaction module: Create Constraint: Coupling: Coupling type: Distributing: Weighting method: LinearQuadratic polynomial weight distributionA quadratic polynomial weight distribution defined byInput File Usage:*DISTRIBUTING, WEIGHTING METHOD=QUADRATICAbaqus/CAE Usage:Interaction module: Create Constraint: Coupling: Coupling type: Distributing: Weighting method: QuadraticMonotonically decreasing weight distributionA monotonically decreasing weight distribution according to the cubic polynomial Input File Usage:*DISTRIBUTING, WEIGHTING METHOD=CUBICAbaqus/CAE Usage:Interaction module: Create Constraint: Coupling: Coupling type: Distributing: Weighting method: CubicSpecifying a local coordinate systemThe distributing coupling constraint can be specified with respect to a local coordinate system instead of the global coordinate system (see “Orientations,” Section 2.2.5). Figure 31.3.2–2 illustrates the use of a local coordinate system to release the moment constraints between the reference node and the coupling nodes in the local 4- and 6-directions, providing a “universal-like” rotation connection. In this example a local rectangular coordinate system is defined that has its local y-axis coincident with the global z-axis. The moment constraint is specified in this local coordinate system.Input FileUsage:*COUPLING, ORIENTATION=localFor example, the following input is used to specify the distributing coupling constraint shown in Figure31.3.2–2:*ORIENTATION, SYSTEM=RECTANGULAR, NAME=COUPLEAXIS0.0, 1.0, 0.0, 0.0, 0.0, 1.0*COUPLING, REF NODE=500, SURFACE=Endcap,ORIENTATION=COUPLEAXIS*DISTRIBUTING1, 35, 5Abaqus/CAE Usage:Interaction module: Create Constraint: Coupling: Edit: select local coordinate systemDefining the surface coupling methodThere are two methods available to couple the motion of the reference node to the average motion of the coupling nodes: the continuum coupling method and the structural coupling method. The continuum coupling method is used by default. Continuum coupling methodThe default continuum coupling method couples the translation and rotation of the reference node to the average translation of the coupling nodes. The constraint distributes the forces and moments at the reference node as a coupling nodes force distribution only. No moments are distributed at the coupling nodes. The force distribution is equivalent to the classic bolt pattern force distribution when the weight factors are interpreted as bolt cross-section areas. The constraint enforces a rigid beam connection between the attachment point and a point located at the weighted center of position of the coupling nodes. For further details, see “Distributing coupling elements,” Section 3.9.8 of the Abaqus Theory Manual.Input File Usage:*DISTRIBUTING , COUPLING=CONTINUUMAbaqus/CAE Usage:Coupling the motion of the reference node to the average motion of the coupling nodes is not supported in Abaqus/CAE.Structural coupling methodThe structural coupling method couples the translation and rotation of the reference node to the translation and the rotation motion of the coupling nodes. The method is particularly suited for bending-like applications of shells when the coupling constraint spans small patches of nodes and the reference node is chosen to be on or very close to the constrained surface. The constraint distributes forces and moments at the reference node as a coupling node-force and moment distribution. For this coupling method to be active, all rotation degrees of freedom at all coupling nodes must be active (as would be the case when the constraint is applied to a shell surface) and the constraints must be specified in all degrees of freedom (default). In addition, for the constraint to be meaningful, the local (or global) z-axis used in the constraint should be such that it is parallel to the average normal direction of the constrained surface.With respect to translations, the constraint enforces a rigid beam connection between the reference node and a moving point that remains at all times in the vicinity of the constrained surface. The location of this moving point is determined by the approximate current curvature of the surface, the current location of the weighted center of position of the coupling nodes (see “Distributing coupling elements,” Section 3.9.8 of the Abaqus Theory Manual), and the z-axis used in the constraint. This choice avoids unrealistic contact interactions if multiple pairs of distributed coupling constraints are used to fasten shell surfaces (see “Breakable bonds,” Section 33.1.9, for more details).With respect to rotations, the constraint is different along different local directions. Along the z-axis (twist direction), the constraint is identical to the one enforced via the continuum coupling method (see “Distributing coupling elements,” Section 3.9.8 of the Abaqus Theory Manual). By contrast, the rotational constraint in the plane perpendicular to the z-axis relates the in-plane reference node rotations to the in-plane rotations of the coupling nodes in the immediate vicinity of the reference node. This choice provides a more realistic (compliant) response when the constrained surface is small and deforms primarily in a bending mode.Input File Usage:*DISTRIBUTING, COUPLING=STRUCTURALAbaqus/CAE Usage:Coupling the motion of the reference node to the average motion of the coupling nodes is not supported in Abaqus/CAE.Moment release and finite rotationIn geometrically nonlinear analysis steps the coordinate system of the degrees of freedom that define the moment releaserotates with the reference node regardless of whether the global coordinate system or a local coordinate system is used. Colinear coupling node arrangementsThe distributing coupling constraint transmits moments at the reference node as a force distribution among the coupling nodes, even if these nodes have rotational degrees of freedom. Thus, when the coupling node arrangement is colinear, the constraint is not capable of transmitting all components of a moment at the reference node. Specifically, the moment component that is parallel to the colinear coupling node arrangement will not be transmitted. When this case arises, a warning message is issued that identifies the axis about which the element will not transmit a moment.LimitationsA distributing coupling constraint cannot be used with axisymmetric elements with asymmetric deformation. Thiselement type is not compatible with the distributing coupling constraint.A distributing coupling definition with a large number of coupling nodes produces a large wavefront inAbaqus/Standard. This may result in significant memory usage and a long solution time to solve the finite element equilibrium equations.A distributing coupling constraint cannot involve more than 46,000 degrees of freedom in Abaqus/Standard, whichimplies an upper limit of 23,000 nodes per constraint for two-dimensional and axisymmetric cases and an upper limit of 15,333 nodes per constraint for three-dimensional cases.。
联轴器英语词汇和句子(中英对照)
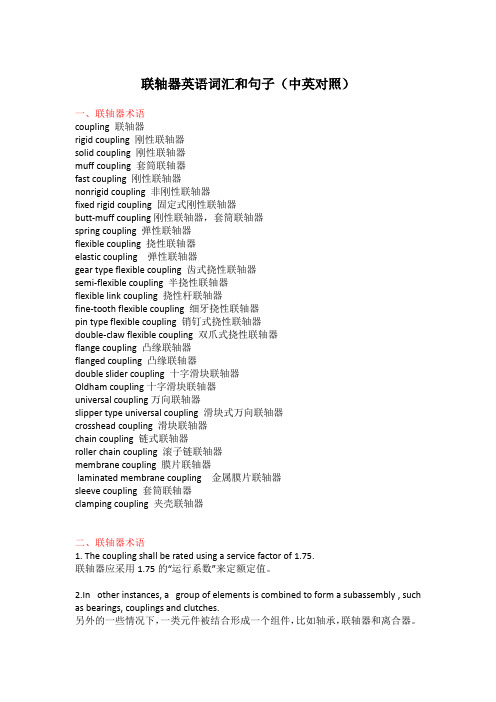
联轴器英语词汇和句子(中英对照)一、联轴器术语coupling 联轴器rigid coupling 刚性联轴器solid coupling 刚性联轴器muff coupling 套筒联轴器fast coupling 刚性联轴器nonrigid coupling 非刚性联轴器fixed rigid coupling 固定式刚性联轴器butt-muff coupling刚性联轴器,套筒联轴器spring coupling 弹性联轴器flexible coupling 挠性联轴器elastic coupling 弹性联轴器gear type flexible coupling 齿式挠性联轴器semi-flexible coupling 半挠性联轴器flexible link coupling 挠性杆联轴器fine-tooth flexible coupling 细牙挠性联轴器pin type flexible coupling 销钉式挠性联轴器double-claw flexible coupling 双爪式挠性联轴器flange coupling 凸缘联轴器flanged coupling 凸缘联轴器double slider coupling 十字滑块联轴器Oldham coupling十字滑块联轴器universal coupling万向联轴器slipper type universal coupling 滑块式万向联轴器crosshead coupling 滑块联轴器chain coupling 链式联轴器roller chain coupling 滚子链联轴器membrane coupling 膜片联轴器laminated membrane coupling 金属膜片联轴器sleeve coupling 套筒联轴器clamping coupling 夹壳联轴器二、联轴器术语1. The coupling shall be rated using a service factor of 1.75.联轴器应采用1.75的“运行系数”来定额定值。
coupling的用法

coupling的用法
"coupling" 是一个名词,表示两个或多个事物之间的相互关联、联系或耦合。
它可以用于描述不同领域和概念中的相互关系。
以下是 "coupling" 的几种常见用法:
1.物理学中的耦合:
o Magnetic coupling(磁耦合)
o Energy coupling(能量耦合)
2.工程学中的耦合:
o Mechanical coupling(机械耦合)
o Thermal coupling(热耦合)
3.计算机科学中的耦合:
o Data coupling(数据耦合)
o Functional coupling(功能耦合)
4.社会学和心理学中的耦合:
o Social coupling(社会耦合)
o Emotional coupling(情感耦合)
此外,"coupling" 还可以在其他专业领域中有特殊用法,如化学、系统论等。
具体用法可能因上下文和领域而有所不同。
需要注意的是,"coupling" 一词通常用来表示事物之间的相互关联和交互性。
它可以指物理上的连接或依赖关系,也可以指概念上的共同作用或相互影响。
偶联 coupling

偶联coupling一个化学反应发生时其它反应以化学计量学的关系相伴进行的现象。
主要用于如下三种情形:[1]氧化与还原的偶联。
电子供体AH2在氧化成A时,电子受体B必须还原成BH2,此时称这二个反应为偶联。
例如在醇发酵中3-磷酸甘油醛的脱氢与乙醛的还原以NAD+为媒介由二个脱氢酶的作用相偶联。
[2]氧化还原反应或分解反应与磷酸化反应相偶联。
在生物体内酶反应中可看到放能反应的进行与由ADP和正磷酸生成ATP(吸能反应)相偶联。
这是由一个酶直接作用,或由二种以上的酶作用经由中间物的生成而进行的,这样的偶联因为直接把反应的自由能以高能磷酸键的形式贮存,所以是重要的。
还有与逆反应的偶联,即与ATP的分解相偶联,发生吸能的合成和氧化还原反应,或肌肉收缩、主动运输等。
偶联反应偶联反应(英文:Coupling reaction),也作偶连反应、耦联反应、氧化偶联,是由两个有机化学单位(moiety)进行某种化学反应而得到一个有机分子的过程.这里的化学反应包括格氏试剂与亲电体的反应(Grinard),锂试剂与亲电体的反应,芳环上的亲电和亲核反应(Diazo, Addition-Elimination),还有钠存在下的Wutz反应,由于偶联反应 (Coupling Reaction)含义太宽,一般前面应该加定语.而且这是一个比较非专业化的名词. 狭义的偶联反应是涉及有机金属催化剂的碳-碳键生成反应,根据类型的不同,又可分为交叉偶联和自身偶联反应。
进行偶联反应时,介质的酸碱性是很重要的。
一般重氮盐与酚类的偶联反应,是在弱碱性介质中进行的。
在此条件下,酚形成苯氧负离子,使芳环电子云密度增加,有利于偶联反应的进行。
重氮盐与芳胺的偶联反应,是在中性或弱酸性介质中进行的。
在此条件下,芳胺以游离胺形式存在,使芳环电子云密度增加,有利于偶联反应进行。
如果溶液酸性过强,胺变成了铵盐,使芳环电子云密度降低,不利于偶联反应,如果从重氮盐的性质来看,强碱性介质会使重氮盐转变成不能进行偶联反应的其它化合物。
coupling
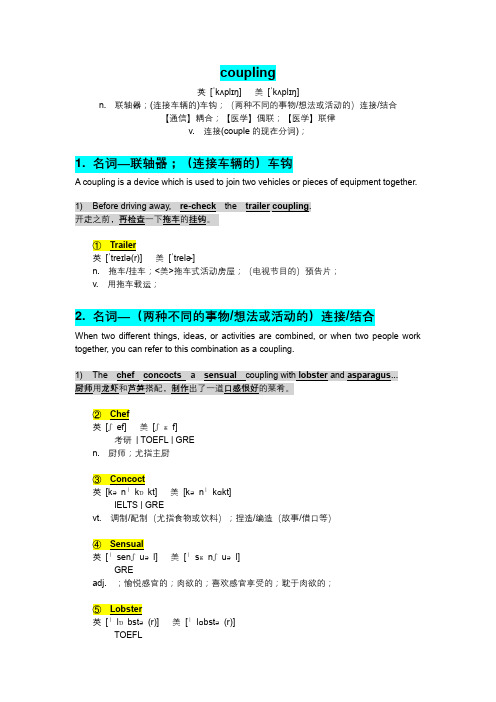
coupling英[ˈkʌplɪŋ] 美[ˈkʌplɪŋ]n. 联轴器;(连接车辆的)车钩;(两种不同的事物/想法或活动的)连接/结合【通信】耦合;【医学】偶联;【医学】联律v. 连接(couple的现在分词);1. 名词—联轴器;(连接车辆的)车钩A coupling is a device which is used to join two vehicles or pieces of equipment together.英[ˈtreɪlə(r)] 美[ˈtrelɚ]n. 拖车/挂车;<美>拖车式活动房屋;(电视节目的)预告片;v. 用拖车载运;2. 名词—(两种不同的事物/想法或活动的)连接/结合When two different things, ideas, or activities are combined, or when two people work together, you can refer to this combination as a coupling.英[ʃef] 美[ʃɛf]考研| TOEFL | GREn. 厨师;尤指主厨英[kənˈkɒkt] 美[kənˈkɑkt]IELTS | GREvt. 调制/配制(尤指食物或饮料);捏造/编造(故事/借口等)英[ˈsenʃuəl] 美[ˈsɛnʃuəl]GREadj. ;愉悦感官的;肉欲的;喜欢感官享受的;耽于肉欲的;英[ˈlɒbstə(r)] 美[ˈlɑbstə(r)]TOEFLn. 龙虾;龙虾肉;英[əˈspærəgəs] 美[əˈspærəɡəs]GREn. 芦笋;英[ʌnˈi:zi] 美[ʌnˈizi]CET4 | CET6 | 考研| IELTSadj. 焦虑不安的/不自在的;(局势或关系)不稳定的/动荡的;英[spɔ:n] 美[spɔn]TOEFL | GREv. (鱼、蛙等)产(卵);产生/引起/导致;n. (鱼、蛙等)卵;英[reɪˈʒi:m] 美[reˈʒim, rɪ-]CET6 | 考研| IELTS | TOEFL | GREn. (尤指未通过公正选举的)政权/政体;(机构/公司等的)组织方法/管理体制;[医]养生法;3. 行业术语:【通信】耦合两个电路或器件的接合或连锁。
COUPLING

专利名称:COUPLING发明人:VOGEL, HERIBERT 申请号:EP02719961.1申请日:20020228公开号:EP1365847A2公开日:20031203专利内容由知识产权出版社提供摘要:The invention relates to a coupling, particularly for connecting a rotor (221) of an ultralight model helicopter to a drive motor. Said coupling comprises a first drive element (202), which can be set in rotation by a drive motor (214) and comprising at least one drive shaft (204), to which a driving torque supplied by the drive motor (214) can be at least partially transmitted. The invention provides that: a) a torque transmission to the at least one drive shaft (204) is effected via a running wheel (206); b) an actuating device (207, 209) exerts a variable force (F) onto the running wheel (206) in order to press the running wheel (206), if necessary, against the first drive element (202), and; c) the force (F) is varied using a magnetic field, which can be influenced by the electrical control of at least one coil (205) that is a component of the actuating device (205, 209).申请人:VOGEL, HERIBERT地址:Mozartstr. 1/1 71711 Steinheim DE国籍:DE代理机构:Schurack, Eduard F.更多信息请下载全文后查看。
- 1、下载文档前请自行甄别文档内容的完整性,平台不提供额外的编辑、内容补充、找答案等附加服务。
- 2、"仅部分预览"的文档,不可在线预览部分如存在完整性等问题,可反馈申请退款(可完整预览的文档不适用该条件!)。
- 3、如文档侵犯您的权益,请联系客服反馈,我们会尽快为您处理(人工客服工作时间:9:00-18:30)。
叶轮叶片
12. 选择所有节点并把节点的坐标系改变到总体柱坐标系: 12a. 选择所有节点:
– – Utility Menu > Select > Everything 或使用命令: NSEL,ALL
Workshop Supplement
INTRODUCTION TO ANSYS 5.7 - Part 2
January 30, 2001 Inventory #001444 W2-8
2A. 耦合
叶轮叶片
10. 在X=0(或者在柱坐标系中 r=0)的节点上约束UX 和UY : 10a. 在X=0选择节点:
– – Utility Menu > Select > Entities ... 或使用命令: NSEL,S,LOC,X,0
– Main Menu > Preprocessor > Element Type > Add/Edit/Delete … • [Add ...] – 选择 “Structural Solid” 和 “Brick 20node 95”,然后按 [Apply] – 选择 “Not Solved” and “Mesh Facet 200”,然后按[OK] • 选择[Options ...] • Set K1 = “TRIA 6-NODE”,然后按[OK] • [Close] 或使用命令: /PREP7 ET,1,SOLID95 ET,2,MESH200 KEYOPT,2,1,5
NROTAT,ALL
January 30, 2001 Inventory #001444 W2-10
2A. 耦合
叶轮叶片
13. 关闭节点耦合符号:
– Utility Menu > PlotCtrls > Symbols … • 在对话框中选择 “For Individual:”和 “Miscellaneous”, 然后选择 [Ok]
12b. 把激活坐标系设置为总体柱坐标系:
– – Utility Menu > WorkPlane > Change Active CS to > Global Cylindrical 或使用命令: CSYS,1
12c.改变节点坐标系到总体柱坐标系:
– – Main Menu >Preprocessor > -Modeling- Move / Modify > -Rotate Node CS- To Active CS + • [Pick All] 或使用命令:
– Main Menu > Preprocessor > Coupling / Ceqn > Offset Nodes … • 设置KCN=1
Workshop Supplement
INTRODUCTION TO ANSYS 5.7 - Part 2
•
–
设置 DY=30
• 选择[OK] 或使用命令: CPCYC,ALL,0.0001,1,0,30
/POST1
PLNSOL,S,EQV
January 30, 2001 Inventory #001444 W2-13
2A. 耦合
叶轮叶片
17. 画出2号体(叶片)的 von Mises 应力:
– – Utility Menu > Select > Entities Sele Below (to select everything below selected volumes)
• • – – – – • 在对话框中选择[OK] 选择[Close] 选择[Close]
Utility Menu > Plot > Elements Utility Menu > Select > Everything Utility Menu > Plot > Elements 或使用命令: CHECK,ESEL,WARN EPLOT ESEL,ALL EPLOT
–
January 30, 2001 Inventory #001444 W2-4
2A. 耦合
叶轮叶片
4. 使用VSWEEP对体volume 2进行网格剖分:
– – Main Menu > Preprocessor > MeshTool … • 选择 “Hex”(六面体)和 “Sweep”(扫掠),然后选择 [Sweep] 或使用命令: VSWEEP,2 Main Menu > Preprocessor > MeshTool … • 智能尺寸”等级置为4 • Mesh置为 Areas • 选择“Tri” 和 “Free”,然后按 [Mesh] 或使用命令: SMRT,4 AMESH,1
练习 2A
耦合
叶轮叶片
2A. 耦合
叶轮叶片
说明 • • 对叶轮的 30°扇区使用耦合。
Workshop Supplement
INTRODUCTION TO ANSYS 5.7 - Part 2
确定叶片在绕Z轴1000弧度/秒角速度载荷下的 von Mises 应力分布。
January 30, 2001 Inventory #001444 W2和材料特性
Workshop Supplement
January 30, 2001 Inventory #001444 W2-3
INTRODUCTION TO ANSYS 5.7 - Part 2
2A. 耦合
叶轮叶片
1. 按教师指定的工作目录,用“cp-blade”作为作业名,进入 ANSYS。 2. 恢复“cp-blade.db1”数据库文件:
•
• • • • • –
[OK]
拾取11号面 (或者在ANSYS输入窗口键入 “11”后按 [Enter]键) 在拾取对话框中选择[OK] 设置 KCN=1 设置DY=30 按[OK]
或使用命令: MSHCOPY,AREA,1,11,1,0,30
January 30, 2001 Inventory #001444 W2-6
Workshop Supplement
INTRODUCTION TO ANSYS 5.7 - Part 2
–
–
Main Menu > General Postproc > Plot Results > -Contour Plot- Nodal Solu ...
或使用命令: VSEL,S,,,2 ALLSEL,BELOW,VOLU PLNSOL,S,EQV
January 30, 2001 Inventory #001444 W2-11
2A. 耦合
叶轮叶片
15. 存储数据库并获取解答:
– – Pick the “SAVE_DB” button in the Toolbar Main Menu > Solution > -Solve- Current LS (or select: Utility Menu > File > Save as Jobname.db)
Workshop Supplement
INTRODUCTION TO ANSYS 5.7 - Part 2
•
–
设置 CP = “Off”
• 选择[OK] 或使用命令: /PBC,CP, ,0
14. 检查单元:
– Main Menu > Preprocessor > -Meshing- Check Mesh > Sel Bad Elems …
– – Utility Menu > File > Resume from … 或使用命令: RESUME,cp-blade,db1
Workshop Supplement
INTRODUCTION TO ANSYS 5.7 - Part 2
3.
进入前处理器,分别定义单元类型1为SOLID95, 单元类型2为MESH200。对MESH200单元 设置KEYOPY(1) = 5 :
January 30, 2001 Inventory #001444 W2-14
2A. 耦合
叶轮叶片
18. 画出1号体(基座)的 von Mises 应力:
– – Utility Menu > Select > Entities Sele Below (to select everything below selected volumes)
2A. 耦合
叶轮叶片
16.进入后处理器,画出 von Mises 应力:
– – Main Menu > General Postproc > Plot Results > -Contour Plot- Nodal Solu ... 或使用命令:
Workshop Supplement
INTRODUCTION TO ANSYS 5.7 - Part 2
叶轮叶片
19. 选择全部实体并把结果扩展 360 度 :
– – Main Menu > Preprocessor > Loads > -Loads- Apply > -Structural- Displacement > On Nodes + 或使用命令: D,ALL,UZ
January 30, 2001 Inventory #001444 W2-9
2A. 耦合
Workshop Supplement
INTRODUCTION TO ANSYS 5.7 - Part 2
•
• –
查看 “/STATUS Command” 然后关闭对话框
选择[OK]
• 选择[Close] - 关闭黄色信息框完成求解 或使用命令: SAVE /SOLU SOLVE