奥钢联连铸设备结构特点及制作难点分析
连铸机简介及检验要点

连铸机简介及检验要点文章以连铸机中的弯曲段为例,简要阐述了连铸机的发展方向。
在加工生产过程中总结了弯曲段的检验要点及其严格把关对轧制板坯的重要性,希望对该方面的研究以及轧制板坯提供一些理论依据。
标签:连铸机;弯曲段;检验据相关资料统计,连铸设备的应用比例在世界范围内在以每年4%的比例增长,同时生产出高品质、高质量连铸坯的技术和质量控制体系也已经成熟并确立,而且连铸连轧的生产方式也將逐步实现,连铸连轧技术在世界范围内倡导节能环保的大环境下必将得以迅速的发展及应用,此项技术在降低能耗缩短生产周期方面有着得天独厚的优势,在板坯、方坯、异形坯等各中厚板类连铸机发展的同时,薄板坯、板带连铸机也正在兴起,连铸技术的发展方向必将朝着紧缩式流程,即薄板坯的连铸连轧方向发展。
连铸机技术也必将朝着集约化、模块化、高节能的方向发展。
连铸机主要的技术形式主要有源自“西马克德马克”公司的CSP(compact strip production)、ISP(inline strip production)技术;源自“西门子奥钢联”公司的CON-ROLL(continous casting and rolling);源自“达涅利”公司的FTSRQ(flexible thin slab rolling for quality)和源自“蒂森”同“三星”公司共同研发的TSP (tippins-samsung process)。
我公司引进的合作制造连铸机的技术形式为西门子奥钢联公司的CON-ROLL(continous casting and rolling)技术,即“连铸连轧”技术。
在这项技术中的主要连铸设备组成为弯曲段、弧形段、矫直段和水平段。
由于篇幅的限制,本文将以弯曲段为主要说明对象来说明连铸机的工作特点和工作特性以及设备检验中的要点。
弯曲段是位于结晶器和弧形段之间,用来对通过其间的铸流起支撑、冷却和引导作用的设备,其主要部件有外弧框架、内弧框架、铸流导辊、保护罩和部件配管等。
连铸机设备常见问题

16.结晶器摩擦阻力如何测定?
结晶器拉坯阻力的在线监测,是预报漏钢的重要手段,下面 介绍应变片测定法。 应变片贴在振动机构的拉杆上,加速度传感器安放在振动 机构的振动台上,然后将信号放大记录并加以显示,如图 2-11a。信号放大记录并加以显示,其记录如图2-11b所示, M为结晶器位移、V为速度、F为摩擦阻力、Vc为拉坯速 度。由图中可见摩擦阻力随结晶器处于正滑动和负滑动不 同运动状态时而正负交变,并有规则的变化,当阻力突然 增大,表示坯壳与结晶器有粘结;当阻力突然变小,表明 坯壳被拉断。这种异常的变化对预报漏钢很有价值,国外 有的钢厂用这个办法作为漏钢的在线监测手段。
正弦式振动得到广泛的应用,因为它有如下的优点: (1)在运动过程中没有稳定运动阶段,因而有利于脱模,但也有一段负滑脱阶 段,使被拉裂的坯壳起到焊合作用。 (2)结晶器运动的加速度必然按余弦规律变化,所以过渡点比较平稳,没有很 大冲击。 (3) 正弦振动可以用曲柄连杆机构来实现,结构比较简单,易于加工和维修。 因此,正弦式振动,可以提高振动频率,减少振痕深度,改善铸坯表面质量。
9.什么叫负滑脱(或称负滑动)?
当结晶器下振的速度大于拉坯速度时,铸坯 对结晶器的相对运动为向上,即逆着拉坯 方向的运动,这种运动称负滑脱或称负滑 动。如图2-14所示,Vm为结晶器振动速度 曲线,V为拉捧速度,在图中当时间大于
((π/2)/ω)-(tm/2)时进入了负滑脱,tm为负
滑脱时间。
10.结晶器振动机构有哪些型式?
12.连铸机高度由哪几部分组成?
连铸机的高度与连铸机的型式有关。 立式连铸机的高度是指由结晶器上口到地下运输辊道之间的距离,其 中包括:结晶器长度、二次冷却区长度、同步切割行程、定尺长度以 及地下运输辊道高度之和。当浇100×100~300×300mm方坯时, 其总高约在17~30m之间。由于立式连铸机要求铸坯在切割处必须全 部 凝固,否则会出现大事故,也就是说从结晶器液面到切割处之间的 距 离必须大于冶金长度,而冶金长度又与拉坯速度和铸坯厚度成正比,因 此拉速越高,铸坯越厚,其冶金长度就越长,铸机高度就越高。由 于 立式连铸机是早期采用的机型,目前除浇注某些合金钢仍用立式外,皆 被弧形等其它机型所取代。 弧形连铸机的高度由结晶器长度、弧形半径、矫直区高度(对多点矫直 或连续矫直)之和,一般在l0m左右。 对超低头机型,由于采用多段式连续矫直或多点矫直,其弧形半径大 为缩小,总高度也较低,其高度h<25H(H为铸坯厚度)。 对薄板坯连铸机,由于铸坯很薄,冶金长度较短,总高在7m左右。
连铸工作中的问题与总结
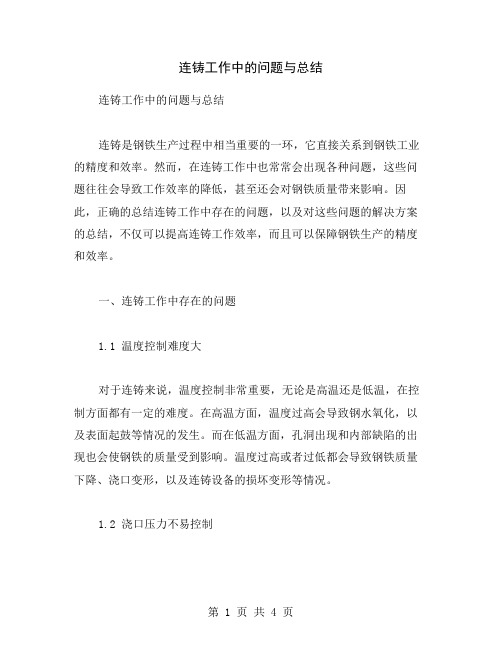
连铸工作中的问题与总结连铸工作中的问题与总结连铸是钢铁生产过程中相当重要的一环,它直接关系到钢铁工业的精度和效率。
然而,在连铸工作中也常常会出现各种问题,这些问题往往会导致工作效率的降低,甚至还会对钢铁质量带来影响。
因此,正确的总结连铸工作中存在的问题,以及对这些问题的解决方案的总结,不仅可以提高连铸工作效率,而且可以保障钢铁生产的精度和效率。
一、连铸工作中存在的问题1.1 温度控制难度大对于连铸来说,温度控制非常重要,无论是高温还是低温,在控制方面都有一定的难度。
在高温方面,温度过高会导致钢水氧化,以及表面起鼓等情况的发生。
而在低温方面,孔洞出现和内部缺陷的出现也会使钢铁的质量受到影响。
温度过高或者过低都会导致钢铁质量下降、浇口变形,以及连铸设备的损坏变形等情况。
1.2 浇口压力不易控制在连铸过程中,浇口的压力也是一个很重要的因素。
因为,当浇口的压力不稳定的时候,就会导致钢水流速的不稳定,出现一些问题,如不稳定的流速就会导致钢铁坯面整平不良、表面有凸起等问题;如果压力太大,就会导致过削钢铁表面,影响钢铁的外观质量。
1.3 浇注速度控制困难在连铸中,加工铸坯的速度对钢水流体的控制也会有影响。
高速浇注增加了钢水氧化和钢水粘滞度的风险,同时也并不利于钢水的混匀,会对钢铁产品的质量产生负面影响。
低速浇注的阻力较大,只能增加钢水流体的切应力,不能达到良好的混合效果。
因此,快并不一定好,慢也不一定准确,调节浇注速度是一项十分困难的任务。
1.4 非均匀铸坯厚度虽然连铸设备可以控制铸坯的厚度,但越往两端,铸坯的厚度也越难控制。
对于非均匀厚度的铸件,在铸造过程中,可能会出现鱼鳞状的铸态,严重影响铸件表面质量。
同时,厚度的不均匀也会导致温度不均匀,进一步影响铸坯质量。
二、针对问题的解决方案2.1 温度控制温度控制是一项非常重要的工作,如果能保持均衡的温度,并且能够避免过高或者过低的温度,就可以使得铸坯的质量得到保证。
连铸产品缺陷的原因分析及改进

201管理及其他M anagement and other连铸产品缺陷的原因分析及改进马 昆(唐钢型线事业部,河北 唐山 063000)摘 要:市场经济的日臻成熟以及生产工艺的不断提升使得客户对于产品质量提出了更高的要求,因铸坯缺陷而导致的质量问题也日益凸显,质量纠纷层出不穷,严重危害到企业的信誉,并由此而造成一定的经济损失。
当前,市场竞争益发激烈,要想满足市场及客户对连铸产品的需求,就必须提高铸坯的质量,进而打破企业经营困境,提升企业竞争实力。
为此,本文着重分析导致连铸产品缺陷的原因,并提出针对性改进措施。
关键词:连铸;缺陷;措施中图分类号:TG335.9 文献标识码:A 文章编号:11-5004(2019)07-0201-2收稿日期:2019-07作者简介:马昆,男,生于1981年,唐山人,工程师,本科,研究方向:冶金工程。
当前,我国经济已步入快速发展的轨道,国家基本建设逐步加快,极大地推动了工业企业的发展,并由此而拉动了钢铁行工业的快速发展。
当前,无论是钢铁的生产还是钢铁的消费,我国都排在世界首列。
连铸连轧作为一门综合技术是由炼钢、连铸及轧制等各个流程整合而来的,当前日臻成熟的技术优势能够有效提升整个轧材生产过程的工艺质量,还有助于工艺流程的优化和缩短,使得轧材生产系统进一步简化,进而使得能耗降低,生产成本得以有效节约。
就生产工艺而言,无需对连铸生产的板坯进行冷却和精整处理,只需直接用轧机对其热装热送后材料进行轧制即可。
如此一来,为确保连铸连轧具有较高的协调性和紧凑型,必须对连铸板坯从铸机到轧机之间的时间间隔进行有效控制。
相比较于其他板材的生产工艺,连铸连轧工艺中可以用来对铸坯质量问题进行检测和处理的时间十分有限,因此必须在生产过程中加大对铸坯表面及内部质量的控制力度,而要实现这一目的,就必须加快确立无缺陷铸坯制造技术。
然而,在具体实践中,连铸板坯需要经历一个相当复杂的生产流程,其产品质量受到各个环节生产工艺的影响,而现有连铸设备及工艺水平还有待提升,使得连铸板坯的生产很难有效避免裂纹、气泡、夹杂、中心缺陷等问题的出现,严重的甚至影响接下来的轧制工艺。
连铸机的特点
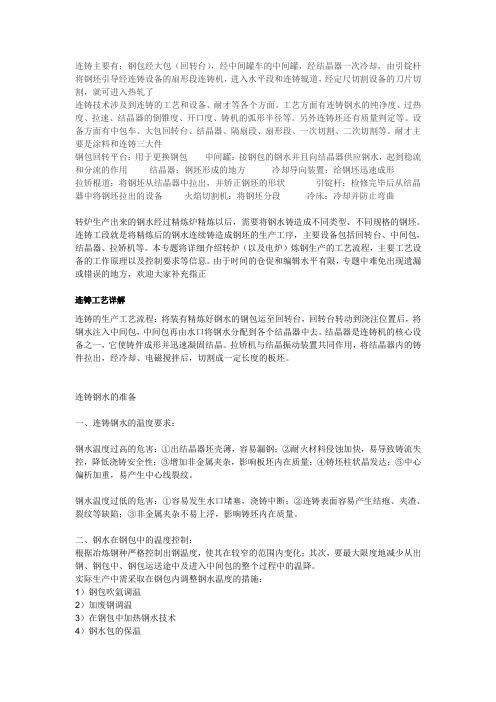
连铸主要有:钢包经大包(回转台),经中间罐车的中间罐,经结晶器一次冷却,由引锭杆将钢坯引导经连铸设备的扇形段连铸机,进入水平段和连铸辊道,经定尺切割设备的刀片切割,就可进入热轧了连铸技术涉及到连铸的工艺和设备、耐才等各个方面。
工艺方面有连铸钢水的纯净度、过热度、拉速、结晶器的倒锥度、开口度、铸机的弧形半径等。
另外连铸坯还有质量判定等。
设备方面有中包车、大包回转台、结晶器、隔扇段、扇形段、一次切割、二次切割等。
耐才主要是涂料和连铸三大件钢包回转平台:用于更换钢包中间罐:接钢包的钢水并且向结晶器供应钢水,起到稳流和分流的作用结晶器:钢坯形成的地方冷却导向装置:给钢坯迅速成形拉矫棍道:将钢坯从结晶器中拉出,并矫正钢坯的形状引锭杆:检修完毕后从结晶器中将钢坯拉出的设备火焰切割机:将钢坯分段冷床:冷却并防止弯曲转炉生产出来的钢水经过精炼炉精炼以后,需要将钢水铸造成不同类型、不同规格的钢坯。
连铸工段就是将精炼后的钢水连续铸造成钢坯的生产工序,主要设备包括回转台、中间包,结晶器、拉矫机等。
本专题将详细介绍转炉(以及电炉)炼钢生产的工艺流程,主要工艺设备的工作原理以及控制要求等信息。
由于时间的仓促和编辑水平有限,专题中难免出现遗漏或错误的地方,欢迎大家补充指正连铸工艺详解连铸的生产工艺流程:将装有精炼好钢水的钢包运至回转台,回转台转动到浇注位置后,将钢水注入中间包,中间包再由水口将钢水分配到各个结晶器中去。
结晶器是连铸机的核心设备之一,它使铸件成形并迅速凝固结晶。
拉矫机与结晶振动装置共同作用,将结晶器内的铸件拉出,经冷却、电磁搅拌后,切割成一定长度的板坯。
连铸钢水的准备一、连铸钢水的温度要求:钢水温度过高的危害:①出结晶器坯壳薄,容易漏钢;②耐火材料侵蚀加快,易导致铸流失控,降低浇铸安全性;③增加非金属夹杂,影响板坯内在质量;④铸坯柱状晶发达;⑤中心偏析加重,易产生中心线裂纹。
钢水温度过低的危害:①容易发生水口堵塞,浇铸中断;②连铸表面容易产生结疱、夹渣、裂纹等缺陷;③非金属夹杂不易上浮,影响铸坯内在质量。
金属结构工程加工制作特点和难点分析及解决措施
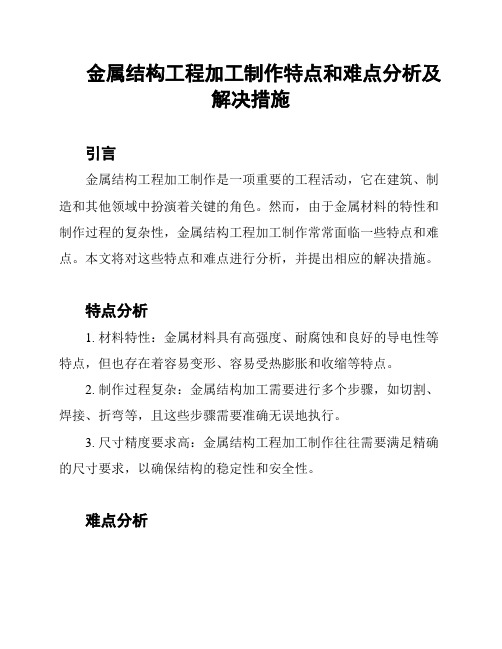
金属结构工程加工制作特点和难点分析及
解决措施
引言
金属结构工程加工制作是一项重要的工程活动,它在建筑、制造和其他领域中扮演着关键的角色。
然而,由于金属材料的特性和制作过程的复杂性,金属结构工程加工制作常常面临一些特点和难点。
本文将对这些特点和难点进行分析,并提出相应的解决措施。
特点分析
1. 材料特性:金属材料具有高强度、耐腐蚀和良好的导电性等特点,但也存在着容易变形、容易受热膨胀和收缩等特点。
2. 制作过程复杂:金属结构加工需要进行多个步骤,如切割、焊接、折弯等,且这些步骤需要准确无误地执行。
3. 尺寸精度要求高:金属结构工程加工制作往往需要满足精确的尺寸要求,以确保结构的稳定性和安全性。
难点分析
1. 设计与加工不匹配:由于设计和加工环节之间的信息传递不畅,导致可能出现设计与加工之间不匹配的情况,进而影响结构质量。
2. 制作工艺选择困难:由于金属结构的复杂性,选择合适的制
作工艺往往是一个困难的决策。
3. 操作技术要求高:金属结构加工需要熟练的操作技术和经验,对操作人员的要求较高。
解决措施
1. 加强设计与制作间的沟通与协作,确保设计和加工之间的一
致性。
2. 提高技术人员的专业水平,加强对制作工艺的研究和掌握,
以选择最佳的制作工艺。
3. 建立标准化的操作规程,培训操作人员,提高其技术水平与
操作能力。
结论
金属结构工程加工制作具有一些特点和难点,但通过合理的分
析和解决措施,这些问题是可以克服的。
加强沟通协作、提高技术
水平和标准化操作是提高金属结构工程加工制作质量的关键因素。
济钢奥钢联连铸机电气系统

济钢奥钢联连铸机电气系统概述1#连铸机自动化控制设备按区域总体分成四大部分:公用系统、铸流系统、仪表系统、后部输送系统。
公用系统主要包括:大包回转台升降回转控制、中包罐车升降行走控制、中包预热站升降升温控制、主液压站运行控制、滑动水口液压站运行控制、1#润滑站运行控制等。
铸流系统主要包括:结晶器调宽控制、结晶器振动控制、扇形段以及驱动辊压下控制、扇形段ASTC智能控制、拉矫驱动以及铸流跟踪控制、引锭收发控制、结晶器液位控制、蒸汽烟气抽引控制等。
仪表系统主要任务是完成连铸机的设备冷却、铸坯二次冷却、各气体介质测量检测控制等功能。
后部系统主要完成:板坯在辊道上的自动输送运转控制、一次切割行走升降切割控制、二次切割行走升降切割控制、去毛刺机升降回转控制、打号机行走打号控制、跺板台卸板台升降运转控制、过跨车行走控制、后部液压运转控制、2#润滑运转控制等功能。
下面,将按设备主体功能分述各设备的自动化控制实现原理。
第一节大包回转台一、概述大包回转台系统分为大包台的旋转;大包台臂的升降;大包盖操作机构的旋转和升降;大包滑动水口;大包长水口操作机构等组成,1.两个大包臂使用各自的升降系统和共用一个旋转系统。
大包台用于将钢包旋转到浇铸位而另一个臂则用于接收天车吊运的钢包。
大包台的旋转由液压马达驱动,液压马达通过比例控制阀进行调速,位置检测由增量型编码器和限位开关控制。
大包臂的升降由电磁阀控制的液压缸的升降来实现。
2.大包盖是为了减少钢包内钢水温度散失而盖在钢包上的设备,大包盖臂的旋转是由比例阀控制实现调速的,位置的检测是由增量型编码器和限位开关实现的;臂升降运动是由电磁阀控制液压缸动作来实现的。
3.大包滑动水口系统用于调节从大包中流入中包的钢水流量。
大包滑动水口控制系统在每个大包臂上由相应的液压驱动系统实现对水口开口度的调节,液压缸的动作是由电磁阀控制的。
4.大包长水口操作机构用于将长水口固定在大包滑动水口上,一个液压升降油缸为固定长水口提供必要的压力。
连铸工艺与设备1

连铸工艺与设备1连铸工艺与设备1连铸是一种现代钢铁生产工艺,是通过连续浇铸技术将液态钢铁直接铸造成连续坯,进而实现高效率的钢材生产。
连铸工艺与设备是该工艺实施所必需的组成部分,对于钢铁企业的生产效率和质量控制具有重要影响。
连铸工艺的主要步骤包括:浇注、结晶器、凝固、拉伸、切割和冷却等。
首先,通过浇注将液态钢铁注入结晶器中,结晶器中装有冷却剂,使钢水迅速冷却并凝固形成坯料。
然后,通过拉伸机械将坯料进行拉伸,拉伸过程中继续凝固,最终形成长期坯料。
接下来,切割机械将长期坯料切割成合适的长度,并通过冷却设备对坯料进行冷却,使其达到适宜的温度。
连铸工艺与设备应具备以下特点:高效率、高质量和节能环保。
首先,高效率是指连铸工艺与设备能够实现高产量和高利用率。
连铸工艺可以连续生产钢材,大大提高了生产效率。
而连铸设备的设计和制造应该保证设备的稳定性,减少故障和停工时间。
其次,高质量要求连铸工艺与设备能够实现钢材的一致性和均匀性。
结晶器的设计和冷却剂的使用都需要考虑坯料的凝固速度和结晶质量。
同时,拉伸机械的控制能够保证坯料的拉伸速度均匀,从而保证钢材的质量。
最后,节能环保是指连铸工艺与设备应该尽可能减少能源消耗和环境污染。
例如,在冷却过程中可以利用循环水来降低能耗,并且对废水进行处理。
近年来,随着工业技术的不断发展,连铸工艺与设备也得到了提升和改进。
连铸工艺的铸造速度和坯料尺寸得到了提高,可以生产出更大尺寸的钢材。
同时,连铸设备的自动化程度不断提高,减少了人工操作,提高了生产效率和安全性。
在连铸过程中,还可以采用一些先进的监测仪器和控制系统,对铁水的成分、温度和流动情况进行实时监测,从而保证钢材质量的稳定性和一致性。
总之,连铸工艺与设备是实现高效率、高质量和节能环保的钢铁生产的重要组成部分。
随着技术的发展,连铸工艺与设备也在不断改进和完善,为钢铁企业的发展提供了强大的支持。
同时,工艺与设备的优化也促进了钢铁产业的可持续发展。
- 1、下载文档前请自行甄别文档内容的完整性,平台不提供额外的编辑、内容补充、找答案等附加服务。
- 2、"仅部分预览"的文档,不可在线预览部分如存在完整性等问题,可反馈申请退款(可完整预览的文档不适用该条件!)。
- 3、如文档侵犯您的权益,请联系客服反馈,我们会尽快为您处理(人工客服工作时间:9:00-18:30)。
奥钢联(SV AI)式连铸设备结构特点及制作难点分析
常州宝菱重工机械有限公司李鹏
【摘要】对奥钢联(SV AI)式连铸设备的结构特点及制作难点分析,便于项目主管在管理项目中有针对性的把握设备的重点、难点。
关键词:SV AI板坯连铸机大包中间罐扇形段制作流程主要零件
本人主要从事连铸设备的技术管理工作,负责了许多国内外项目的转化设计和技术管理。
连铸设备目前主要有四种类型:奥钢联(SV AI)式、西马克(SMSD)式、达涅利(DDD)式和SPCO式。
在项目管理过程中遇到各式各样的板坯连铸机设备,在这里我着重介绍奥钢联(SV AI)式板坯连铸机设备的制造流程。
例如墨西哥AHMSA连铸、巴西CSA 连铸、巴西Acominas连铸、南钢3#连铸、太钢2150连铸出坯区设备等。
奥钢联板坯连铸机主要由大包回转台、中间罐、中间罐车、结晶器、结晶器振动装置、弯曲段、弧形段、矫直段、水平段、支撑框架(俗称大、小香蕉)、引锭杆、引锭杆收集系统、火焰切割前辊道、火焰切割机、火焰切割辊道、输出辊道、板坯打印机、板坯称重装置等组成。
现将关键设备组成及制造难点简单说明如下:一、大包回转台与中间罐车:
大包回转台主要零件:底座、回转体、上部连杆、大包臂、连杆支架等。
中间罐车主要零件:走行框架、提升框架
主要制作流程:
备料划线落料切割坡口折弯、圈圆等法兰、圆筒及侧板组件单体拼装焊接成形MT、UT自检整体拼装、焊接MT、UT自检辅助筋板拼装、焊接矫正打磨焊缝MT、UT整体检查退火处理MT、UT复检喷丸涂装防锈(底漆)金加工划线粗加工精加工划线钻孔攻丝检验涂装(中间漆及第一道面漆)待装配
备料:Q345D+Z向板为主,大部分要求UT探伤,以舞阳钢板为主。
落料:采用数控气割
坡口:V、X、K形坡口半自动气割,J、U形坡口机床加工。
焊接:CO2气体保护焊。
UT探伤:按ASME标准。
预热温度:100~150℃
加工用机床:
大型加工件:底座、回转体、走行框架、提升框架:XK2750、HCW3-250NC 其余主要零件:MIP2800/6000、W200HC(HD)、HC471
大包回转台装配流程:
底座与回转轴承组装大包臂润滑配管回转体装配连杆支架组装合装大包臂安装平台装配配管配线保护罩单装试动作解体涂装包装发运
中间罐车装配流程:
车轮组装工装准备轨道安装走行框架与车轮装配提升油缸装配提升框架装配调整与称重装置装配平台装配配管配线动作试验解体涂装包装发运
二、结晶器与弯曲段:
主要零件:左侧支撑墙、右侧支撑墙、固定侧支撑墙、自由侧支撑墙、背板;内弧框架、外弧框架、辊套、芯轴、T形销轴。
结晶器左、右侧支撑墙以Q345B为主材料焊接而成,固定、自由侧支撑墙以
0Cr18Ni9钢板焊接为主,背板以0Cr18Ni12Mo2Ti与Q345B焊接而成。
结晶器主要零件制作流程:
备料划线落料切割坡口零件焊前加工划线、拼装定位焊、焊接(可分阶段组装)矫正水压试验UT探伤退火处理UT 探伤涂装防锈金加工划线粗加工PT检查精加工划线钻孔攻丝水压试验检验涂装(中间漆及第一道面漆)待装配
落料:0Cr18Ni9、0Cr18Ni12Mo2Ti钢板主要以钻排孔留余量落料
焊前加工:以不锈钢钢板焊前加工为主。
水压试验:准备试水工装,试验压力12Bar,保压半小时
UT探伤:不锈钢焊缝焊前与焊后进行100%UT探伤
退火:450±10℃,保温4小时,去应力。
PT探伤:粗加工后焊缝进行100%PT探伤
弯曲段框架零件制作流程:
备料划线落料切割坡口折弯等零件焊前加工划线、拼装定位焊、焊接(可分阶段组装)矫正粗加工堆焊不锈钢退火处理涂装防锈金加工划线粗加工装铜套精加工划线钻孔攻丝检验涂装(中间漆及第一道面漆)待装配
备料:Q345B厚度240mm钢板采用舞阳钢厂的钢板或锻坯。
如采用锻坯,则先将锻坯进行机加工达图样要求后,再进行框架的拼焊。
退火前粗加工:主要加工要求堆焊的平面,保证堆焊层厚度的均匀。
装铜套:图纸尺寸要求高,必须镶铜套后再精加工才能满足铜套尺寸要求。
弯曲段辊子制作流程:
锻造(正火)粗加工UT检查调质粗加工堆焊退火硬度检查粗加工精加工检验(PT或MT)装配
锻造:材料采用20CrMo
堆焊:为了提高堆焊辊的过钢量,我公司新开发了以N代C的堆焊材料,使堆焊层晶粒细化、硬度高、均匀性好,具有无晶间腐蚀、抗高温热疲劳和较高的抗回火稳定性能,从而延长连铸辊的使用寿命。
堆焊前制作堆焊试块,对堆焊层进行化学成份分析、金相分析、硬度检查,合格后方可堆焊。
弯曲段芯轴及T形销轴零件制作流程:
锻造(正火)粗加工UT检查调质硬度检查粗加工精加工孔加工检验装配
三、扇形段(弧形段、矫直段、水平段)与支撑框架:
1)扇形段主要零件:内弧框架、外弧框架、轴承座、辊套、芯轴、导柱、拉杆、
压下框架、调整板。
框架的主要制作流程
备料划线落料切割坡口折弯等零件焊前加工划线、拼装定位焊、焊接(可分阶段组装)矫正粗加工堆焊拼焊轴头水压试验退火处理涂装防锈金加工划线粗加工精加工
划线钻孔攻丝水路封闭焊接水压试验检验涂装(中间漆及第一道面漆)待装配
水路封闭焊接:加工时会有铁屑进入水路,封闭水路前必须清理干净,检查确认后进行水密封性焊接并逐路进行保压试验。
轴承座主要制作流程:
备料划线落料轴承座焊前加工(包括水路)拼装不锈钢盖板、定位焊、焊接水压试验水路保护粗加工精加工划线钻孔攻丝水压试验检验涂装(中间漆及第一道面漆)待装配
扇形段其它主要零件:
拉杆:材料30Cr2Ni2Mo,调质处理,抗拉强度要求1100~1200N/mm2
调整板:材料2Cr13,调质处理,抗拉强度要求750~900N/mm2
2)支撑框架主要零件:大、小香蕉片状框架、联接梁、自动水联接
片状框架主要制作流程:
备料划线落料坡口加工大板拼焊(UT、MT)零件拼装、焊接矫正退火喷丸涂装(底漆)粗精加工合装精加工床检涂装(中间漆)待装配
大板拼焊:由于尺寸较大,钢板采购困难,只能采有两板拼焊的方式,全熔透焊接,焊后进行UT与MT检查。
合装:两组框架合装在一起进行加工,更易保证同尺寸要求及相对位置精度。
加工、装配与发运:制作整套专用工装并发至现场。
四、扇形段的组装、调试流程及注意事项
确认箱子规格、数量以上是本人在技术管理工作中的一些积累,希望能在工作中不断完善、深化。