生产线平衡实验报告
生产线平衡改善报告

活动期间 担当者
改善后 将控制盒悬挂于作业台下 (改善內容)
2009.01.31 郝润清,李辉
项目 改善前 改善后
效 C/T 果 PPM 內 M/H 容 UPH
不牢固,不易于设备维修
效 *投资金额:元 果 金 *有, 无形效果(人员,面积,安全,意识,劳动量…等) 额 *投资费 回收期间 ---等 用 金额 标记
2
;Slide 插
组立
ininal插入
;Slide 插 组立/Air ininal插入 机
入及检查
入及检查
blow
1
IN
4,000cm
4,000cm
6
Ⅲ. 改善事例
会社(部署)名 DS S/C
改善对象 改善项目 改善前 控制盒倒于作业台下面 (问题点) 不牢固,不易于设备维修
5
改
善
事
例
S/C MICRO LINE 控制盒摆放(3定5S)
15.47초 7.Button 入,;Grease ;Slide 插 入及检查
5.19;2.91초 11.45초
3,5 Box 及 2.M-
Plate插入, Con't/Tem
组立
ininal插入
4.17초 1.B/ P lat e Air blow
9.94초 8.特性检查
15.51초 7.Button 入,;Grease
23.3
改善前人员不固 定(8~12名变动)
22.4 22.4
2
Ⅱ. 改善活动结果及内容
2-3. S/C 科 Micro LIine改善 Cost Saving (预想削减金额)
구분
기준 단위 (09年01月
生产线平衡实验

套入右后轮
57
盖上车面
29
装右后轮钢圈套入轮胎
58
嵌入车面固定装置
2、模式一
1)模式一说明
模式一是将整辆小车的零件在同一物料箱内,随生产线流动,每个工位只完成事先安排的任务,并随其他零件流向下一工作台。
2)模式一的装配工艺作业任务及操作时间
根据整个玩具车的产品功能结构和产品零件结构表,细分安排如下装配工艺,根据模式一的方式,安排工序,如表所示:
工位
执行工艺编号
耗时(s)
1
1、2、3、4、5、6、7、8、9、10、11
21
2
12、13、14、15、16、45、46、47、48、49
24
3
24、25、26、27、28、29、39、40、41、42、43、44
22
4
17、18、19、20、21、22、23、30、31、32、33、34、35
17
3、模式二
1)模式二说明
模式二是与模式一相反,是将本工作台任务的零件事先准备好及在相同时间段内组装装配,然后依据程序装配。
2)模式二的装配工艺作业任务及操作时间
根据整个玩具车的产品功能结构和产品零件结构表,细分安排如下装配工艺,根据模式一的方式,安排工序,如表所示:
表6装配工艺作业任务表
工艺序号
工序
44
在零件F1上装4个M2螺丝
4
16
工序9
45
阶梯螺丝与垫片套入导轮
2
46
在F2上装左前导轮
3
47
阶梯螺丝与垫片套入导轮
2
48
在F2上装右前导轮
3
49
在零件F1上装4个M2螺丝
4
动态产线平衡工作总结
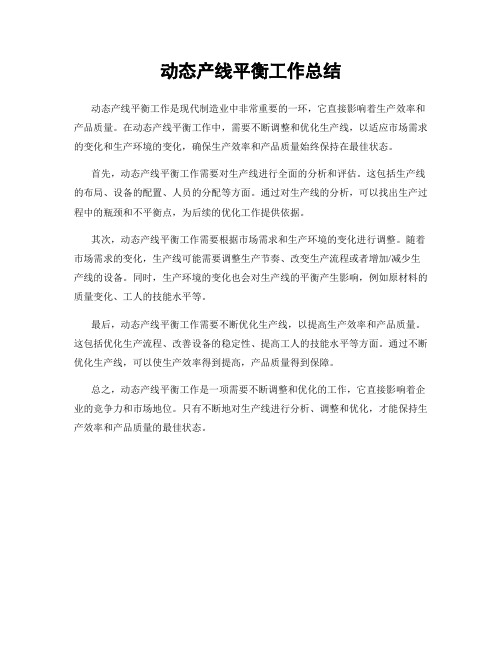
动态产线平衡工作总结
动态产线平衡工作是现代制造业中非常重要的一环,它直接影响着生产效率和产品质量。
在动态产线平衡工作中,需要不断调整和优化生产线,以适应市场需求的变化和生产环境的变化,确保生产效率和产品质量始终保持在最佳状态。
首先,动态产线平衡工作需要对生产线进行全面的分析和评估。
这包括生产线的布局、设备的配置、人员的分配等方面。
通过对生产线的分析,可以找出生产过程中的瓶颈和不平衡点,为后续的优化工作提供依据。
其次,动态产线平衡工作需要根据市场需求和生产环境的变化进行调整。
随着市场需求的变化,生产线可能需要调整生产节奏、改变生产流程或者增加/减少生产线的设备。
同时,生产环境的变化也会对生产线的平衡产生影响,例如原材料的质量变化、工人的技能水平等。
最后,动态产线平衡工作需要不断优化生产线,以提高生产效率和产品质量。
这包括优化生产流程、改善设备的稳定性、提高工人的技能水平等方面。
通过不断优化生产线,可以使生产效率得到提高,产品质量得到保障。
总之,动态产线平衡工作是一项需要不断调整和优化的工作,它直接影响着企业的竞争力和市场地位。
只有不断地对生产线进行分析、调整和优化,才能保持生产效率和产品质量的最佳状态。
动态产线平衡工作总结
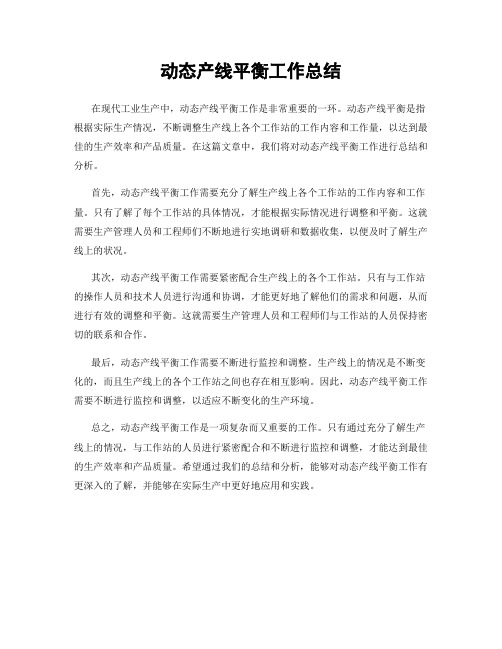
动态产线平衡工作总结
在现代工业生产中,动态产线平衡工作是非常重要的一环。
动态产线平衡是指根据实际生产情况,不断调整生产线上各个工作站的工作内容和工作量,以达到最佳的生产效率和产品质量。
在这篇文章中,我们将对动态产线平衡工作进行总结和分析。
首先,动态产线平衡工作需要充分了解生产线上各个工作站的工作内容和工作量。
只有了解了每个工作站的具体情况,才能根据实际情况进行调整和平衡。
这就需要生产管理人员和工程师们不断地进行实地调研和数据收集,以便及时了解生产线上的状况。
其次,动态产线平衡工作需要紧密配合生产线上的各个工作站。
只有与工作站的操作人员和技术人员进行沟通和协调,才能更好地了解他们的需求和问题,从而进行有效的调整和平衡。
这就需要生产管理人员和工程师们与工作站的人员保持密切的联系和合作。
最后,动态产线平衡工作需要不断进行监控和调整。
生产线上的情况是不断变化的,而且生产线上的各个工作站之间也存在相互影响。
因此,动态产线平衡工作需要不断进行监控和调整,以适应不断变化的生产环境。
总之,动态产线平衡工作是一项复杂而又重要的工作。
只有通过充分了解生产线上的情况,与工作站的人员进行紧密配合和不断进行监控和调整,才能达到最佳的生产效率和产品质量。
希望通过我们的总结和分析,能够对动态产线平衡工作有更深入的了解,并能够在实际生产中更好地应用和实践。
生产线平衡 (2)

生产线平衡
生产线平衡是指在制造过程中,通过合理地分配和安排工
作任务,使得生产线上的工位之间的负荷均衡,从而提高
生产效率和产品质量。
生产线平衡的目标是使得每个工位上的工作时间和工作量
相对均衡,并且生产线的生产节奏能够与市场需求保持一致。
平衡的生产线能够避免工位之间的等待和闲置时间,
减少生产过程中的浪费。
要实现生产线平衡,需要对生产过程进行详细的工作分析,确定每个工位上的工作内容、时间和数量,并结合工人的
技能和经验,合理地分配工作任务。
同时,还需要考虑各
种因素的影响,如不同工序之间的依赖关系、设备的容量
和效率以及工人的疲劳程度等。
生产线平衡可以通过多种方法来实现,包括重新安排工作
顺序、调整工作时间和数量、调整工位布局、提高设备效
率、培训工人等。
同时,可以利用生产线平衡的原理来优
化生产计划和调度,以便更好地满足市场需求和提高生产
效益。
生产线平衡是现代生产管理的重要内容之一,能够有效地
提高生产效率、降低生产成本,提高产品质量和交付能力,进而增强企业的竞争力。
生产线平衡案例分析过程

生产线平衡案例分析过程1. 引言生产线平衡是一种优化生产过程的方法,旨在确保生产线上的工作站之间的工作负载均衡,以提高生产效率和产品质量。
本文将以一个实际案例为例,分析生产线平衡的过程。
2. 案例背景假设某公司生产手机,并且生产线上有三个关键工作站:组装、测试和包装。
每个工作站的工人数量不同,导致工作负载不均衡,组装工作站负责最多的工作量,而测试和包装工作站的工作负载较少。
3. 数据收集为了分析生产线平衡的问题,首先需要收集一些关键数据。
包括每个工作站的工作时间、工人数量以及每个工作站的工作量。
工作站工作时间(分钟)工人数量工作量(数量)组装工作站30 3 200测试工作站25 2 150包装工作站20 2 100通过收集这些数据,可以计算出每个工作站的单位时间工作量,即每分钟能完成的工作量。
根据上表数据,可以得出以下结果:•组装工作站的单位时间工作量为6.67件/分钟(200件/30分钟)•测试工作站的单位时间工作量为6件/分钟(150件/25分钟)•包装工作站的单位时间工作量为5件/分钟(100件/20分钟)4. 分析和优化通过计算每个工作站的单位时间工作量,可以判断哪个工作站是生产线上的瓶颈工作站。
在这个案例中,组装工作站的工作量最大,成为瓶颈,会导致生产线的工作负载不平衡。
为了平衡工作负载,可以采取以下优化措施:•调整工人数量:增加组装工作站的工人数量,以减轻其工作负荷。
•优化工作时间:分析工作时间,寻找减少生产时间的方法,例如改进工艺或引入自动化设备。
•转移工作量:将部分组装工作转移到其他工作站,以平衡各工作站的负载。
5. 优化结果评估经过优化措施的实施后,重新计算每个工作站的单位时间工作量,以评估结果。
工作站工作时间(分钟)工人数量工作量(数量)单位时间工作量(件/分钟)组装工作站30 4 200 5测试工作站25 2 150 6包装工作站20 2 100 5通过调整组装工作站的工人数量,将其增加到4人,重新计算单位时间工作量之后,可以看到组装和包装工作站的工作量现在已经达到了平衡,测试工作站的工作量仍然保持不变。
生产线平衡分析
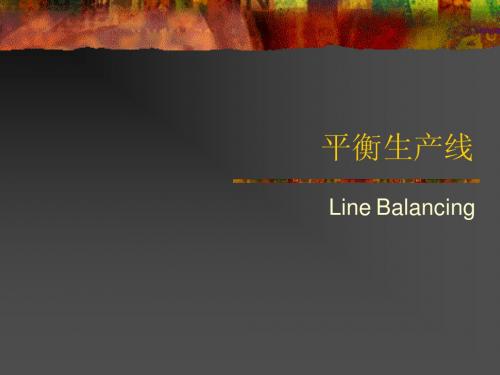
拉平
Line balancing 改善案例
现状调查
现状分析:从作业时间及平衡率看,生产 线的平衡损失比较严重,且作业分工过细, 造成作业内容调整困难。因此在作业改善 上所采取的较直接简便的方法即是合并工 序的内容,调整并取消时间过短工序,以 达到提高平衡,减少工时损失,提高人均 效率的目的。
Line balancing 与“一个流”生产
在生产现场,无论是分工的皮带生产线, 还是手工传递,当平衡率达到85%以上时, 就可以基本实现一个流的生产方式了。
•
Line balancing 的改善原则
平衡率改善的基本原则是通过调整工序的 作业内容来使各工序作业时间接近或减少 这一偏差。 方法 首先应考虑对瓶颈工序进行作业改善,作 业改善的方法,请按照程序分析的改善方 法及动作分析,工装自动化等工程方法与 手段。
将瓶颈工序的作业内容分担给其他工序。 增加各作业人员,只要平衡率提高了,人 均产量就等于提高了,单位产品成本也随 之下降。 合并相关工序,重新排布生产工序,相对 来讲,在作业内容相对较多的情况下容易 拉平衡。 分解作业时间较短的工序,把该工序安排 到其也工序中去。
平衡生产线
Line Balancing
平衡生产线的意义
• • • •
目的 提高作业员及设备工装的工作效率 减少单件产品的工时消耗,降低成本(等 同于提高人均产量); 减少工序的在制品,真正实现“一个流”; 在平衡的生产线基础上实现单元生产,提 高生产应变能力,对应市场变化实现柔性 生产系统;
通过平衡生产线可以综合应用到程序分析、 动作分析、LAYOUT分析,搬运分析、时 间分析等全部IE手法,提高全员综合素质。 Line balancing 的计算 要衡量生产线平衡状态的好坏,我们必须设 定一个定量值来表示,即生产线平衡或平 衡捐失率,以百分率表示。
生产线平衡分析

22
步驟2 每小時量產變異分析
每小時產量變異分析圖
改善前的產量變異 要因改善後的產量變異
P/T縮短後
換線換模 等
財團法人中衛發展中心中區服務處
23
[步驟 3] 生產線平衡的改善(2名作業員以上的生產線)
改善方法說明
• 以上1~2步驟的改善,可能反而使生產線平衡率降低 ,因此在第3步驟針對因省人化而生產線平衡造成的 差異,依照各工程的實際作業時間彙繪製節距圖表:
生產線編成效率
(1) 節奏時間(Tact/Time)的計算:即客戶要求的生產間隔時 間(Pitch Time) 日作業時間(秒/日) T/T= 日需求量(個/日) (2) 編成效率:表示流程作業各工程總合時間與實際需求之比值 各工程作業時間 T/T * 作業人數
財團法人中衛發展中心中區服務處
生產線編成效率=
•生產線要 如繃緊的線 •浪費集中‧ 工作集中化 •省人化
財團法人中衛發展中心中區服務處
16
生產線的生產效率化-改善5步驟
[提升生產效率化的目標]
(1)縮短生產間隔時間(P/T)以符合節奏時間(T/T)
當生產需求量增加,並且不希望利用加班、休假出勤來增加 產量,在原有的作業人員數下,必頇藉由縮短生產的P/T來提 升產量。
14
編成效率之討論
Tact Time:96〞
過 銲 錫
•生產線編成效率 < 70% •80%> 生產線編成效率 > 70% •90%> 生產線編成效率 > 80% •95%< 生產線編成效率
尚未進行改善前的狀態 編成大有問題 尚有改善空間 維持改善的成果
財團法人中衛發展中心中區服務處
15
- 1、下载文档前请自行甄别文档内容的完整性,平台不提供额外的编辑、内容补充、找答案等附加服务。
- 2、"仅部分预览"的文档,不可在线预览部分如存在完整性等问题,可反馈申请退款(可完整预览的文档不适用该条件!)。
- 3、如文档侵犯您的权益,请联系客服反馈,我们会尽快为您处理(人工客服工作时间:9:00-18:30)。
安徽工业大学
生产线平衡实验报告
专业信息管理与信息系统
班级息111
姓名史家成
学号 119094276
日期 2014-4-23
一、概述
1. 实验目的及要求
将所学的生产运作与管理理论综合应用到实际生产系统的规划和运行管理中去,使学生在实训中理解和巩固所学理论知识,培养其在生产线运行调度过程中发现、分析和解决问题的能力,提高学生的专业素养和综合素质。
2. 实验内容
在生产系统实验室的地面生产线上进行三相异步电动机的装配。
二、实验内容完成情况
1.基于三相异步电动机拆装的生产实验
(1)三相异步电动机拆装:简介所装配三相异步电动机的各零部件的名称、拆装方法及注意事项等。
a、按时间过程拆:分别是风扇罩、风扇、前端盖、后端盖和转子、接线盒。
B、按时间过程装:分别是接线盒、后端盖和转子、前端盖、风扇和风扇罩。
(2)工作研究部分
流程程序图
(3)生产过程实训部分
实训内容及记录数据
简介本部分的实训内容及方式(按照车间管理的模式,将全部实训学生分为若干班组,各班组自行商定其作业安排、车间派工、实施方案和具体生产管理过程,然后轮班实训)1)个人方案介绍
简介本次设计的方案,包括小组成员岗位设置、岗位派工、装配流程、工序安排、物流路线等(可附图、表补充说明)
将学生分为车间主任,搬运工,操作工,计时人员;商议作业顺序及作业安排;
各工种就位;电动机组装,检验组装的成品,完成该次试验。
岗位设置及派工:我小组人员,具体分配为一车间主任、四个操作工,六个搬运工,四个计时人员
装配流程及工序安排:组装前后端盖→组装风扇盖→组装接线盒
2)初次方案设计及实施情况
说明本组初次实施的方案的具体内容及其设计依据→绘出装配流程图→完成数据记录表→根据记录数据总结本次方案设计及实施的质量;总结说明本次方案的优缺点由于是初次进行实践,我们并不熟悉每位队员对拆装电动机的熟悉程度,在有些步骤上浪费了一点时间,但我们进行了调整,最终顺利完成了。
3)第二次方案设计同2)一样,绘出装配流程图
将学生分为车间主任,搬运工,操作工,计时人员;商议作业顺序
及作业安排;各工种就位;电动机组装,检验组装的成品,完成该次试验。
岗位设置及派工:我小组人员,具体分配为一车间主任、四个操作工,六个搬运工,四个计时人员
装配流程及工序安排:组装前端盖→组装后端盖→组装风扇罩→组装接
线盒
Ⅲ
小结
对比总结两次方案的优缺点,针对出现的问题给出进一步的优化设计建议第一次只是盲目的进行生产,第二次是在带一次的基础上进行优化的。
第
二次各工种工作时间更为平均
三、思考题
1.能否应用工序同期化方法进行装配时间平衡?如有,写出具体的过程,如不可行,为什么?
答:可以,可以同时进行前端盖和后端盖的装配,最后装配风扇罩,可将前后端分为两道工序
2.计算第一次方案的平衡率?
答:平衡率=sum(1,2,3,4)/(Max(1,2,3,4)*4)=427/(223*4)=47.87%
3.实训中你用到哪些JIT的思想?
答:本方案在实施中运用到JIT思想,每个工序的搬运人员相当于各工位
的物料供应单位,在需要的时候,按照需要将生产所需的零部件送至流水线,这样可以减少物料的出库时间,消除不必要的浪费。
说明: 1.附录2中所有斜体字为提示文字,写报告时应将其删除,但需按提示要求去撰写报告。
2.实习报告中,本组共同的部分,其组内成员可以一起讨论其内容,但必须自己写,严禁直接拷
贝他人的成果,否则按抄袭论处!。