橡胶发泡技术与常见问题及解决方法(1)
生产橡胶制品常见的质量问题和解决方案
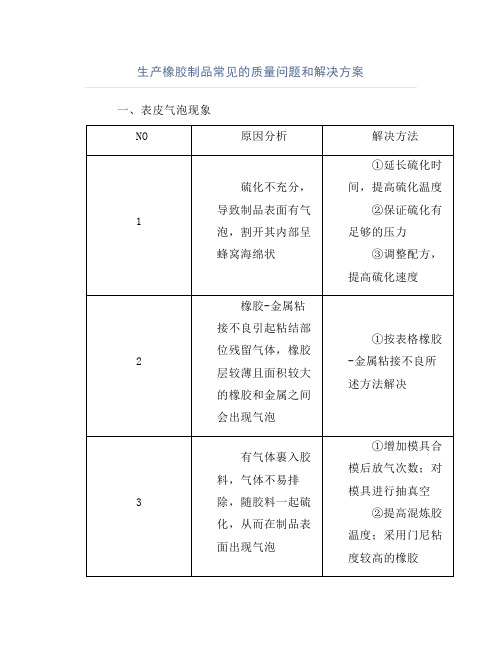
生产橡胶制品常见的质量问题和解决方案一、表皮气泡现象三、分层橡胶制品常见缺陷及解决方法五、缺胶外观不完整,没有填充满七、撕裂、拉毛1过量配合各种助剂在橡胶中的溶解度不同,助剂在橡胶中的溶解度越小,越易出现由过量配合(即橡胶中助剂的含量超过其在橡胶中的溶解度)而引起的喷霜。
过量配合而喷霜时,往往会带动其它组分一起喷出(这种现象称为被动喷霜),尽管这些被动喷霜物在橡胶中远未达到饱和状态。
2温度变化助剂在橡胶中的溶解度随温度变化而变化,一般情况下,温度高时溶解度大,温度降低时溶解度减小。
由于橡胶制品通常在室温下使用,一旦外界温度低于室温,配方中一些助剂的含量接近其溶解度而析出,产生喷霜。
例如夏季生产的胶鞋出厂检验时合格,贮存到冬季却发现喷霜。
3欠硫助剂在橡胶中的溶解状况受硫化条件影响。
以NR为例,在正硫化条件下,交联密度最大,游离硫减小,喷硫几率降低,其它助剂穿梭于三维网络的机会也降低,因而喷霜几率降低;反之,在欠硫状态下,网络交联密度相对较小,喷霜几率相应增大"4老化老化意味着硫化胶三维网络结构的局部因键断裂而受损,从而消弱了网络结构吸附和固锁配合助剂的能力,助剂向表面迁移导致喷霜"5受力不均橡胶受到外力作用时,往往导致应力集中而使表面破裂,使原来呈过饱和状态的配合助剂微粒加速析出,在裂纹表面形成喷霜,并向周边延扩"6混炼不均混炼不均导致配合剂在橡胶中分散不均,局部会出现配合助剂超过溶解度而产生喷霜"预防措施(1)掺用SR:SR对助剂的溶解度高于NR,故掺用部分SR有助于预防NR喷霜。
(2)并用促进剂、防老剂:单用一种助剂,用量过少难以达到效果,用量过多又易出现喷霜,故可以并用几种助剂,达到效果从而减小用量。
(3)利用不同配合助剂在喷霜上的互相干扰制约:不同助剂一起配合使用时,有时会出现相互干涉而有助于抑止喷霜,如软化剂、油膏、再生胶等都具有此功能。
特别是相对分子质量大的助剂能渗透到橡胶大分子的短链中,可有效吸附易喷助剂。
发泡生产中常见问题分析及解决方法

发泡生产中常见问题分析及解决方法一.工艺参数不准可能引起的问题1.模具温度低可能产生的问题。
a.粘接性差b.亏料c.形稳性差2.发泡剂用量不准可能产生的问题。
a.自由泡密度偏低(高)b.亏料(溢料)c.形稳性差,脱模性差3.黑白料比不准可能产生的问题。
a.自由发泡密度偏低(高)b.反应速度偏快(慢)c.亏料(溢料)d.形稳性差e.泡孔结构不正常4.注射压力不准可能产生的问题。
a.料比不正常b.反应速度偏快(慢)c.喷溅d.泡孔结构不正常5.料温不对可能产生的问题a.反应速度偏快(慢)b.料比不正常c.亏料(溢料)d.脱模性不正常二.常见问题原因及处理方法1.粘接性较差即离皮a.模具低温度过低(过高)b.过填充量不够c.发泡系统的选择不当d.错误的黑白料比(黑料过多)e.内胆表面粘接性较差。
如电晕过的HIPS比不电晕的粘接性要强得多2.泡沫溢料即漏料a.过填量过大b.发泡料乳化时间太长,乳化速度太慢c.密封不严d.箱体结构设计及构造不合理3.亏料a.模具温度过低b.过填充不足c.排气不是太好4.尺寸稳定性、泡沫强度较差a.泡沫密度过低b.过填充量不足c.流动性较差,导致过高的泡孔各向异性d.泡沫交联程度不够5.脱模时间较长a.过填充量过大b.箱体设计及构造不合理c.流动性较差导致箱体内某些地方的过填量太大6.泡沫表面气泡偏多a.箱体结构不合理,对料的流动不利,部分地方易形成旋涡而造成气泡产生b.排气不好,造成气体淤积c.发泡料混合不均匀,发泡过程中相关参数变化,不稳d.发泡料的流动性不好,发泡料和发泡剂的相溶性不好7.箱体中梁收缩a.侧板金属厚度或强度太低b.箱体结构不合理,造成料的均一性不够好c.发泡料的流动性不够好d.发泡料本身的压缩强度及尺寸稳定性不好。
8.泡沫开裂a.泡沫太厚,b.过填充量过大,密度太大。
c.脱模时间太短,熟化时间不够。
d.发泡料本身脱模性不够好。
发泡气泡缺陷的解决方法(一)
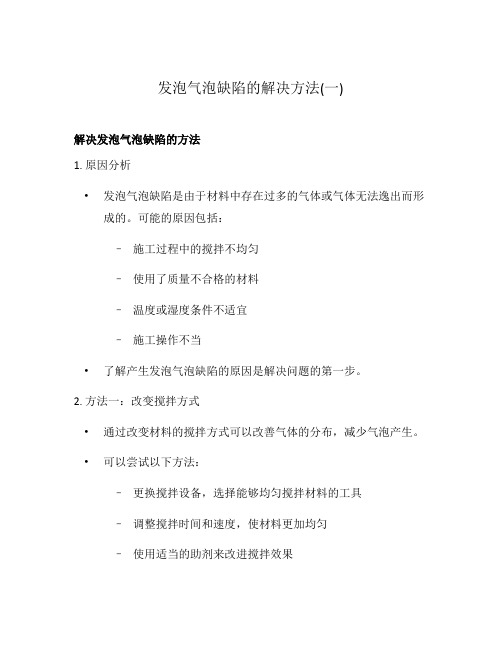
发泡气泡缺陷的解决方法(一)解决发泡气泡缺陷的方法1. 原因分析•发泡气泡缺陷是由于材料中存在过多的气体或气体无法逸出而形成的。
可能的原因包括:–施工过程中的搅拌不均匀–使用了质量不合格的材料–温度或湿度条件不适宜–施工操作不当•了解产生发泡气泡缺陷的原因是解决问题的第一步。
2. 方法一:改变搅拌方式•通过改变材料的搅拌方式可以改善气体的分布,减少气泡产生。
•可以尝试以下方法:–更换搅拌设备,选择能够均匀搅拌材料的工具–调整搅拌时间和速度,使材料更加均匀–使用适当的助剂来改进搅拌效果3. 方法二:优化材料选择•使用质量良好的材料是避免发泡气泡缺陷的关键。
•注意以下几点:–购买来自可靠供应商的材料,确保质量可靠–研究材料的特性和成分,选择适合的材料–严格控制材料的存储条件,避免受潮或受污染4. 方法三:调整环境条件•温度和湿度对发泡气泡缺陷的产生有重要影响。
•可以尝试以下方法调整环境条件:–根据材料的要求,控制施工环境的温度和湿度–使用合适的加热或降温设备来调整温度–采取措施防止湿度过高或过低,例如使用加湿器或除湿器5. 方法四:改进施工操作•施工操作的正确与否直接影响气泡缺陷的产生。
•可以注意以下几点来改进施工操作:–详细阅读和遵守施工说明书和标准操作规程–培训施工人员,提高操作技能和意识–注重细节,例如使用压平工具消除气泡6. 方法五:使用检测工具•使用检测工具可以帮助发现发泡气泡缺陷,并及时解决问题。
•可以使用以下检测工具:–热像仪:检测材料表面的温度差异,发现可能存在气泡的区域–放大镜:观察材料表面细微的气泡–压力计:测量材料中的气体压力,判断是否存在过多气体7. 总结•发泡气泡缺陷是常见的施工问题,但可以通过一些方法来解决。
•通过改变搅拌方式、优化材料选择、调整环境条件、改进施工操作和使用检测工具,可以有效地解决发泡气泡缺陷问题。
•选择合适的方法需要结合具体情况进行综合分析和实践验证。
8. 实例分析•为了更好地理解解决发泡气泡缺陷的方法,以下是一个实例分析:情境描述•施工人员在进行聚氨酯发泡材料的施工过程中,发现出现了大量发泡气泡的缺陷。
橡胶产品基本缺陷产生原因及解决措施

浇口设计不合理
浇口设计不合理,导致充型困难或产 生气孔等缺陷。
模具加工精度低
模具加工精度不高
导致模具配合不良,出现飞边、 溢料等问题。
模具表面粗糙
模具表面粗糙导致制品表面质量差 。
模具材料不当
使用不当材料制作模具,导致制品 不符合要求。
设备性能不良
注射机精度不高
注射机精度不高,导致注射不稳 定,制品出现气泡、银纹等缺陷
配方比例不当
橡胶配方中各种原材料的 比例不当,会影响橡胶产 品的性能。
配方设计不合理
硫化体系不合理
硫化体系是橡胶配方设计 的重要部分,硫化剂、促 进剂等配比不当,会影响 橡胶产品的性能。
补强体系不合理
补强剂的种类和用量不当 ,会影响橡胶产品的强度 和耐磨性等性能。
增塑体系不合理
增塑剂的种类和用量不当 ,会影响橡胶产品的柔软 度和耐寒性等性能。
建立完善的设备维护和保养制度 ,定期对设备进行检查、维修和
更换。
保持生产环境的清洁和卫生,减 少污染和杂质对产品质量的影响
。
加强产品使用及环境监控
对产品使用进行严格的监管和控制,避免滥用和误用。 对产品使用环境进行评估和监控,确保其符合产品要求。
建立完善的质量检测和监控体系,对产品进行定期检查和测试。
压力不均
总结词
压力不均是指在橡胶加工过程中,压力 分布不均匀,导致橡胶制品出现鼓包、 厚度不均等问题。
VS
详细描述
压力不均的原因包括模具设计不合理、压 力控制不稳定、注射速度过快或过慢等。 此缺陷会导致橡胶制品形状变形、精度降 低,影响使用性能和外观质量。
时间控制不当
总结词
时间控制不当是指在橡胶加工过程中,时间控制过长或过短,导致橡胶制品出现老化、不耐用等问题。
橡胶产品基本缺陷产生原因及解决措施
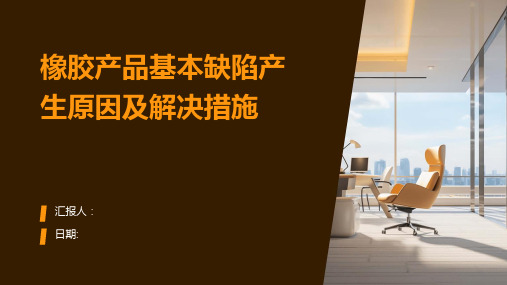
橡胶层之间存在气泡或杂质
3
脱皮
• 外部环境恶劣(如紫外线、氧化等)导致脱皮
脱皮
提高粘合剂质量,确保各层材料粘合牢固 在产品表面添加保护层,提高抗紫外线性能
解决措施
加强原材料和生产过程中的质量控制,避免气泡 产生
CHAPTER 02
原材料及配方因素
原材料质量不良
01
02
03
原材料污染
使用受污染的原材料,如 化学试剂、金属离子等, 会导致产品性能下降。
增塑剂不当
增塑剂种类、用量选择不 当,如石蜡、邻苯二甲酸 酯等,会影响产品加工性 能及物理性能。
配合剂分散不良
粉状配合剂分散不均
粉状配合剂在胶料中分散不均匀,如碳酸钙、滑石粉等,会影响产品外观及性 能。
液体配合剂分散不均
液体配合剂在胶料中分散不均匀,如机油、硅油等,会影响产品加工性能及物 理性能。
调整硫化工艺,确保硫化过程合理
变形
01
原因
02
产品结构设计不合理
硫化过程中内部残留应力未完全消除
03
变形
• 产品受外部环境影响(如温度、湿度等)导致变形
变形
解决措施 采用后硫化工艺消除内部应力
加强产品结构设计,确保稳定性 控制产品存放环境,避免受温度、湿度等影响
脱皮
原因
1
2
橡胶与金属或其他材料粘合不良
优化原材料配方
根据产品性能要求,调整原材料配方,以提高产品性能并减少缺陷 。
建立原材料质量标准
制定详细的原材料质量标准,确保进厂原材料符合生产要求。
优化加工工艺及设备参数
调整加工温度
根据原材料性质和生产要求,合理调整加工温度,以避免过热或过 冷导致的缺陷。
橡胶模压制品常见缺陷及解决方法

喷霜混炼胶或硫化胶内部的液体或固体配合剂因迁移而在橡胶制品表面析出形成云雾状或白色粉末物质的现象。
这是由于硫、石蜡、某些防老剂、软化剂的使用量超出了它们在橡胶中的溶解度而引起的。
为防止喷霜,上述各种配合剂用量要适当,对常见的硫黄喷霜可采用不溶性硫黄加以防止。
在橡胶中适当加入松焦油,液体古马隆等可增加胶料对上述配合剂的溶解度,以减少喷霜现象。
喷霜-定义和由来喷霜又名喷出(blooming),是橡胶加工过程中常见的质量问题,它是指未硫化胶或硫化胶中所含的配合剂迁移到表面并析出的现象。
有时,这种喷出物呈霜状结晶物,故习惯上称“喷霜”。
较多见的喷霜物为硫,因为硫黄是通用橡胶中应用最广泛的硫化剂,且在橡胶中的溶解度低因而容易产生喷霜。
其实从喷出物外观来看,也未必都呈霜状,也有呈油状(软化剂、增塑剂)或粉粒状(多为填充剂、防老剂、促进剂等)的物质喷出,甚至炭黑喷出也有所见。
喷霜-防霜剂硅胶也会有喷霜现象,采用双二四硫化剂(通常用在挤出成型工艺)高温分解后会产生低分子量的酸性物质,其与硅橡胶不相容,在存放过程中会转移到硅胶表面结晶从而出现喷霜。
防霜剂主要成分为碱性物质,通过酸碱中和反应来达到防霜的目的。
高硬度的硅胶往往加入比较多的内脱模剂,遇水也会喷白,水的酸性对此有遏制作用硅橡胶模具制作方法及注意事项模具是快速模具里的一种最为简单的方法,一般是用硅胶将RP原型进行复模,但寿命很短,只有10-30件左右!他具有很好的弹性和复制性能,用硅橡胶复制模可不用考虑拔模斜度,不会影响尺寸精度,有很好的分割性,不用分上下模可直接进行整体浇注。
再沿预定的分模线进行切割取出母模就可以了!室温硫化硅橡胶又分为加成型和缩合型两种!原料及配方采用专用模具硅橡胶,该品系以双包装形式出售,A组份是胶料,B组份是催化剂。
配制时要考虑室温、模具的强度和硬度,以此来确定AB组份的重量配制比例。
室温在20-25度时,A:B=100:1.5。
室低时(但不能低于10度)则适当增加B组份0.1-0.3份。
橡胶发泡技术与常见质量问题

发泡橡胶制品概述发泡橡胶制品以橡胶为基材,采用物理发泡或者化学发泡的方法进行生产,从而得到海绵状的橡胶多孔结构品。
这一技术在目前已经被广泛的应用在各生产行业当中,如汽车门窗密封条、缓冲垫,建筑施工垫片、抗震材料、体育防护设施等。
1、发泡橡胶概念所谓的发泡橡胶也被广泛的称之为橡胶发泡技术,是利用特定的发泡剂来处理橡胶,从而使得橡胶具备特征性能的一种处理手段。
这种技术在目前的生产领域应用较为广泛,是现阶段生产工作中最为常见的一种方法。
2、发泡橡胶制品分类发泡橡胶制品是目前生产领域采用最多的产品之一,其根据孔洞可以分为微孔结构、多孔结构两种。
而微孔结构又可以分为单独发泡制品和连续发泡制品。
根据橡胶的原材料可以将这一制品分为天然橡胶发泡制品、异戊二烯发泡制品、SBR发泡制品、乙丙橡胶发泡制品等。
二、发泡橡胶制品配合分析发泡橡胶制品在当前的社会中应用越来越广泛,其在制取和生产过程中与热塑性塑料发泡有着天壤之别,它存在着一个硫化交联速度与发泡剂分解速度相匹配的问题。
也就是说,一种橡胶材料成功发泡除了与交联速度存在着密切关系之外,橡胶材料的硫化过程与发泡剂分解时候所发生的原理基本上相同的,都是一个对气体膨胀壁产生相应阻力的延伸流程。
1、主体材料的选择在制造的过程中,通常都要求根据制品的具体目标来选择科学的橡胶主体材料,这些材料在选择中要做到柔软、强度适中、弹性量好的天然橡胶制品,同时还要选择一些能够满足制品需求的人工橡胶。
对于耐油发泡制品生产中,除了需要选择合理科学的丁腈橡胶之外,还要分析氯丁橡胶的比例和关系,甚至为了满足某些特殊产品需要,还可以采用两种或者多种橡胶并用的形式。
2、发泡剂的选择发泡剂是整个发泡橡胶制取中最为关键的环节,其选用与工作效率、工作质量息息相关。
一般来说,制的性能良好的发泡制品就必须要选择科学、合理的发泡剂,且发泡剂的使用量、使用方法都要满足目前社会发展要求。
在当前,发泡剂主要包含有有机发泡剂和无机发泡剂两种。
橡胶挤出发泡制品技术详解!

橡胶挤出发泡制品技术详解!橡胶挤出发泡制品技术详解一、发泡胶挤出管的硫化与发泡机理1、硫化与发泡的配合硫化速度与发泡速度要相匹配。
不可一方大幅度快于另一方。
硫化速度过快:发泡剂因受硫化胶强大的机械力无法成功分解出将胶料发泡。
硫化速度过慢:发泡剂在胶料完全或接近与完全未硫化的状态下分解出气体将胶料发泡,但同时胶料的表面也被气体冲破,以至胶管表面不平整或有气孔。
两速度的对比:一般硫化速度需略快于发泡速度,这样一个保证胶管表面的光滑,二可让发泡剂顺利分解出气体将胶料发泡。
2、胶管的发泡过程微波:胶管的发泡主要由微波加热完成。
利用微波的热辐射将胶管从内到外加热,当胶管内部刚开始受热发泡时,胶管靠外的胶料相对温度还较低不至于完全硫化导致胶管发不起来。
这样从内到外的加热方式保证了胶管能够顺利发泡。
在微波对胶管加热发泡的同时也伴随着硫化,只是此时的硫化没有达到最终的硫化深度。
从微波出来后再进入热空气加热段将胶管完成最后的硫化。
以完成胶管的硫化与发泡。
二、配方设计1、生胶生胶的选择,主要需考虑挺性流动性硫化速度挺性:为了能达到需要的挺性不让胶料在硫化曹传输过程中,因为胶料自身重量受压而导致胶料变形。
生胶须选用门尼较高的牌号。
流动性:为了达到挤出所需要的流动性,在选择生胶时因考虑用门尼较低的牌号硫化速度:由于发泡胶通常需要的硫化速度较快,为了满足硫化速度的需要,在选择生胶时需要用第三单体含量较高的牌号。
中合各种因素:我们必须根据胶管的壁厚与大小需要进行选择。
一般情况都选用门尼较高的生胶。
也可高底门尼混用。
2、补强剂一般我们为了胶料的流动性着想,都选用流动性较好的碳黑,比如尼铁隆N550R注:为了胶料的流动性,也可加入一定量的流动助剂。
3、硫化体系发泡胶管的硫化体系通常要求都很快。
必须用到大量的超促及超超促。
其中TDEC(TL)效果为佳。
速度很快焦烧短。
其弊端为存放不安全。
为了使分解出气体更容易将胶料发泡,我们在设计硫化体系时还因注意交联密度问题。
- 1、下载文档前请自行甄别文档内容的完整性,平台不提供额外的编辑、内容补充、找答案等附加服务。
- 2、"仅部分预览"的文档,不可在线预览部分如存在完整性等问题,可反馈申请退款(可完整预览的文档不适用该条件!)。
- 3、如文档侵犯您的权益,请联系客服反馈,我们会尽快为您处理(人工客服工作时间:9:00-18:30)。
橡胶发泡技术与常见问题及解决方法!
橡胶发泡材料又称为橡胶海绵、微孔橡胶或泡沫橡胶,由构成材料本身的连续固相(基质胶)和形成孔隙的流体相(孔隙)所组成。
根据孔洞是否连通,分为开孔发泡材料、闭孔发泡材料和混合孔发泡材料。
发泡橡胶通过适当增加泡孔体积,可以节约橡胶资源,并获得一般硫化橡胶所没有的高压缩率、柔软性等特点,最大限度地发挥橡胶的功能。
橡胶发泡制品的性能和用途很大程度上由橡胶生胶所决定,
天然橡胶(NR)、顺丁橡胶(BR)气味较小,常用于制造生活用品;
丁苯橡胶(SBR)耐磨性好,多用于鞋底材料;
三元乙丙橡胶(EPDM)因耐臭氧性、耐热性、耐候性、低温柔软性等优点,常用于制造汽车密封条、密封圈、隔热产品等;
丁腈橡胶(NBR)耐油、耐热性以及回弹性好,多用于汽车发动机的减震材料;
硅橡胶因可承受300℃高温,用于密封材料、特殊环境中的膨胀连接材料以及隔热、吸振材料等。
发泡橡胶质量轻,具有优异的弹性、柔软性,隔热吸音效果好,被广泛用于密封、减震、隔热、隔音、印染等方面,在航空、汽车、仪器、仪表、家电和包装中广为应用。
制得的发泡材料作为鞋底材料,具有高止滑性的优点。
目前,对橡胶发泡材料配方的研究主要涉及填料、硫化剂、发泡剂等方面。
目前对橡胶发泡材料工艺的研究主要涉及发泡温度、发泡时间、成型工艺(模压、挤出成型)等方面。
橡胶发泡底
橡胶发泡底是用天然或人造橡胶制造的橡胶闭孔或开孔发泡材料制造的铺底面料。
在半个世纪以前,人们将这种材料大量用于球鞋、运动鞋、旅游鞋、解
放鞋、休闲鞋等。
它具有弹性优良、抗撕裂性能好、耐老化、耐腐蚀、电绝缘等性能。
固体橡胶发泡生产橡胶海绵,其原理是在选定的胶料中加人发泡剂或再加入助发泡剂,在硫化温度下发泡剂分解释放出气体,被胶料包围形成泡孔,使胶料膨胀形成海绵。
决定并影响泡孔结构的主要因素有:发泡剂的发气量、气体在胶料中的扩散速度、胶料的黏度以及硫化速度,其中最关键的是发泡剂发气量、产生气体的速度和胶料的硫化速度的匹配。
发泡剂的发气量和分解速度
发泡剂的发气量是指单位质量的发泡剂完全分解所释放出的气体在标准状态下的体积,单位为mL/g。
发泡剂的分解速度是指在一定温度下一定质量的发泡剂单位时间分解释放出的气体量。
由于聚合物本身并不改变发泡剂的分解机理,因此就可不在聚合物中测发泡剂的发气量。
通常是将发泡剂放人一定温度的惰性分散剂(如DOP或矿物油)中,加热一段时间''收集放出的气体,绘制气体体积(换算为标准条件下的体积)
随加热时间发泡剂的分解,分解完全后的气体总体积除以发泡剂的质量就得到发泡剂的发气量。
发泡剂品种不同,粒径不同,温度不同,其分解速度不同。
一般情况下,分解温度低的发泡剂,其分解速度快;对同一种发泡剂,粒径小,温度高,其分解速度快。
发泡剂的发气量与分解速度影响泡孔的大小和结构,发气量大,分解速度快,形成的泡孔大,开孔的概率大。
发泡剂的分解速度与胶料硫化速度匹配的分析。
两者的匹配性影响泡孔的生成和结构。
若发泡剂的分解速度或胶料的硫化速度相差太大,不能配合,则不能发泡。
要实现两者的匹配,做出更好的橡胶制品,选择发泡剂品种和胶料硫化体系是关键。
具体方法有两种:
一是根据硫化温度选择分解温度与之相适应的发泡剂,然后再根据发泡剂在该硫化温度下的分解速度来调整胶料硫化速度,如采用迟效性促进剂和其他促进剂并用硫化体系,可采用调整促进剂的用量来调节硫化速度;
二是在硫化体系确定的情况下,根据硫化速度选择发泡剂品种及合适的粒径。
发泡剂的粒径也是决定发泡剂分解速度的最重要因素之一。
粒径减小,粒子的比表面积增大,热传导效率提高,分解速度加快,因此可通过选择合适的发泡
剂粒径来调节发泡剂的分解速度与胶料硫化速度之间的平衡。
此外,严格控制发泡剂的粒径分布是获得均勾泡孔的关键。
发泡剂AC的平均粒径在2~15fnn之间,不同粒径范围的发泡剂AC。
橡胶发泡时有哪些常见的问题?该如何解决?
问题一:发泡孔不足
1、可能是发泡剂的质量出现了问题,如果出现这种情况,我们要首先检查发泡剂的使用期限,看看该发泡剂是否在使用期限内。
2、可能是胶料可塑造的强度太低。
此时我们要检查胶料的可塑度是否在标准范围内,如果可塑度太低的话,应该在进行补充混合炼制,这样可以增加可塑度,就可以使发泡孔增多。
3、胶料放置时间太久或者放在温度高的地方使发泡剂出现挥发的情况。
出现这种情况应该把该胶料重新进行补充加工。
4、胶料硫化的速度非常快,此时应该调整胶料的配方,协调硫化剂临界温度和发泡剂的分解温度,使二者的速度相互配合减慢硫化速度。
问题二:填充模不足
1、橡胶的使用量不足,此时应该讲胶条一根一根称重,这样来保证胶料的重量达到标准。
2、可能是模具不够光洁或者是模具使用了很久却没有进行相应的清洁工作,使胶料在流动的时候受到了阻力作用。
遇到这种情况应该想办法减小阻力作用使胶料的流动性增强。
发泡橡胶
问题三:发泡孔出现过大或过小的不均匀现象
1、发泡剂出现结团现象,解决方法将结团粒子进行过筛,将比较粗的粒子充分粉粹,然后在对它们进行充分的混炼使它们均匀分散开来。
2、配合剂中含有过多的水分或者空气和其他杂质混在了胶料中。
在这种情况下,应该先把配合剂中过多的水分排除,将胶料中的空气和杂质充分除掉,以此来使它们充分硫化。
3、可能是因为硫化不充分,在模样形成后出现了继续发孔的现象。
此时应该对硫化工艺的条件做出相应的调整,另外要将硫化剂的使用量增加来达到相应的标准。
常见问题四:过硫化或欠硫化
1、过硫化一般表面变色,孔眼较小,硬度较高,产品边缘裂开,产生原因是操作不当,或温度过高,硫化时间太久或仪表失灵,应检查各阀门和仪表是否有问题,再则要严格执行操作规则。
2、欠硫化硫化不足时,出模后气孔内压大于外压,胶料若继续发孔,轻则造成硬度过低,强性差,变形大;重则孔眼爆破。
应检查仪表,阀门是否有问题,严格执行操作规则。
注:发泡制品控制质量指标(1)表观密度,越小越好;(2)机械强度一般为0.5-1.6Mpa;(3)静压缩永久变形;(4)硬度;(5)冲击弹性;(6)连续动疲劳;(7)老化试验(70度*70小时;100度*24小时);(8)低温试验。
经过小编的介绍,相信大家对发泡橡胶出现的一些质量问题的解决方法都有了一定的了解,生活中发泡橡胶出现质量问题是难免的,只要及时的解决这些问题就可以了。