冷轧生产工艺流程
冷轧不锈钢工艺流程介绍

4AP:
退火工艺 Ni系冷带材温: 1050~1150C Cr系冷带材温: 750~1100C 燃料: LPG或NG
酸洗工艺 Ni系冷带: Na2SO4(电解)→HNO3 +HF Cr系冷带: Na2SO4(电解)→HNO3 +HF
Na2SO4(电解)→HNO3
所谓冷轧不锈钢板带生产,不是单纯的“冷 轧”。在冷轧前还要退火、酸洗、修磨等,冷轧后 还要平整、矫直、剪切、垛板等,所以实际上是从 热轧卷开始直到生产出冷轧成品的全过程。
原料黑皮卷
罩式退火炉BAF
十二辊冷轧机 C R M 二十辊冷轧机 C R M
热卷连续退火酸洗线 A P H
修磨机组 C G L
冷卷连续退火酸洗线 A P C 立式连续光亮退火线 B A L
电解(Cr系) 冷轧卷: Na2SO4电解
(2)酸洗: 热轧卷:HNO3+HF(混酸) 冷轧卷:HNO3(电解)、 HNO3 +HF、 HNO3
5、各机组退火酸洗工艺
1AP(C)、2AP:
退火工艺 冷带Ni系材温:1060~1160C 冷带Cr系材温:750~960C 燃料: LPG
酸洗工艺 冷带Ni系: Na2SO4 (电解)→ (HNO3(电解))→ HNO3+HF 冷带Cr系: Na2SO4 (电解)→ HNO3(电解)→ HNO3 (H2O)
不能用罩式炉
4、酸洗
酸洗是冷轧不锈钢的必经工序。现代化宽带不锈 钢生产都是将退火与酸洗设在同一机组连续作业,称 之为连续退火酸洗机组,如AP(H)、AP(C)等。
酸洗的目的:酸洗的目的是去掉热轧及退火过程 中在钢带表面形成的铁鳞,即氧化层。除此之外,酸 洗另一个目的是对不锈钢表面进行钝化处理,提高钢 板耐蚀性。冷轧成品的酸洗尤为重要。
冷轧生产工艺流程是什么

冷轧生产工艺流程是什么引言冷轧是一种常见的金属加工工艺,广泛应用于钢铁、铝等金属材料的加工过程中。
冷轧生产工艺流程指的是将热轧钢板或热处理后的钢板在室温下进行再次加工的过程。
本文将介绍冷轧生产工艺的基本流程及其各个环节的作用和要点。
工艺流程1.原料准备:首先将所需的原料(一般是热轧钢板)按照规格要求进行选择和准备。
原料的质量和尺寸对冷轧加工的成品质量有重要影响。
2.入炉退火:如果原料是热轧钢板,通常需要进行入炉退火。
这一步骤主要是为了消除原料中的应力和改善材料的可加工性。
入炉退火根据材质的不同可分为全退火和局部退火。
3.酸洗:经过入炉退火后,原料表面可能会生成一层氧化皮或铁锈。
因此,在冷轧前需要进行酸洗处理,将原料表面的氧化物去除,以保证冷轧后的表面质量。
4.冷轧:酸洗后的原料进行冷轧加工。
冷轧是指在室温下,通过辊压的方式将原料进行塑性变形。
冷轧的主要目的是改变原料的尺寸和形状,并提高材料的机械性能。
5.淬火和退火:冷轧后的材料可能会存在一定的应力和硬化现象。
为了消除这些问题,需要进行淬火或退火处理。
淬火可提高材料的硬度和强度,而退火则可降低材料的硬度和强度。
6.切割:冷轧加工后的材料根据客户需求,进行相应的尺寸切割。
切割可以采用剪切、切割机等工具进行。
7.表面处理:切割后的材料可能会出现一些表面缺陷,如划痕、氧化等。
为了提高表面质量,可以进行抛光、喷漆等处理。
8.检测和包装:最后,对成品进行质量检测,包装。
检测项目通常包括尺寸、性能等方面的测试。
包装方式根据客户需求和材料特性进行选择。
工艺要点1.质量控制:在冷轧生产过程中,质量控制是至关重要的。
从原材料的选择到成品的包装,每一个环节都需要进行严格的质量控制,以保证产品的质量稳定。
2.设备调试:冷轧生产线中的各种设备需要进行适当的调试,保证其正常运行和稳定性。
设备的调试涉及到辊系的间隙、辊轴的对中、机床的精度等各个方面。
3.工艺参数优化:生产过程中的工艺参数,如辊轧力、辊速比、温度等,对产品的质量有重要影响。
带钢冷轧生产工艺

带钢冷轧生产工艺
带钢冷轧生产工艺
一、引言
带钢冷轧生产工艺是一种广泛应用于钢铁制造的重要技术,它能够将热轧带钢通过一系列的加工工序,生产出具有高精度、高质量的冷轧带钢产品。
这种工艺具有产品尺寸精度高、表面质量好、性能优良等特点,广泛应用于汽车、家电、建筑、机械制造等领域。
本文将对带钢冷轧生产工艺进行详细介绍。
二、带钢冷轧生产工艺流程
带钢冷轧生产工艺主要包括以下步骤:原料准备、酸洗、轧制、退火、平整、精整和检查等。
1. 原料准备
原料准备是冷轧工艺的第一步,包括选择合适的原材料、进行表面处理和厚度调整等。
原料的品质和精度对最终产品的质量和性能有着至关重要的影响。
2. 酸洗
酸洗的目的是去除带钢表面的氧化皮和杂质,以确保轧制过程中的表面质量和性能。
酸洗后的带钢要进行清洗和干燥。
3. 轧制
轧制是冷轧生产的核心环节,通过多道次的轧制,使带钢的厚度、宽度和长度等参数达到要求。
在轧制过程中,要控制好温度、轧制速度和压下量等参数,以保证产品的质量和性能。
4. 退火
退火的目的是调整带钢的机械性能和消除加工硬化现象。
根据不同的产品要求,退火工艺可以选择在常温下进行或有保护气体的加热退火。
5. 平整
平整的目的是进一步调整带钢的表面质量、机械性能和厚度精度。
通过平整处理,可以改善带钢的板形和平整度,提高产品的使用性能。
6. 精整
精整包括剪切、矫直、标识和包装等工序,是产品出厂前的最后处理阶段。
精整的目的是确保产品的尺寸精度、表面质量和外观质量符合要求,便于运输和使用。
冷轧方管制造工艺流程

冷轧方管制造工艺流程冷轧方管是一种常见的钢管制品,广泛应用于建筑、机械制造、汽车制造等领域。
冷轧方管的制造工艺流程包括原材料准备、热轧坯料加工、冷轧成型、矫直、切割和包装等环节。
制造冷轧方管的第一步是原材料准备。
原材料通常为热轧钢带,其主要成分为碳素钢。
在原材料准备阶段,需要对热轧钢带进行检验,包括尺寸、化学成分和力学性能等方面的检测,确保原材料符合要求。
接下来是热轧坯料的加工。
热轧钢带经过剪切机的切割,将其切成一定长度的坯料。
然后,将坯料送入加热炉进行加热,以提高其可塑性和热轧性能。
第三步是冷轧成型。
加热后的坯料通过辊道进入冷轧机组,经过多道次的冷轧,逐渐形成方形的截面。
冷轧过程中,通过调整辊缝,使坯料逐渐变细,并最终形成所需的尺寸和形状。
完成冷轧成型后,需要对方管进行矫直。
矫直是为了消除冷轧过程中产生的应力和弯曲,使方管达到一定的直线度要求。
常见的矫直方法有拉矫和辊矫两种,根据方管的尺寸和要求选择合适的矫直方法。
矫直后,还需要对方管进行切割。
根据客户的需求,将方管切割成所需的长度。
切割通常采用锯床、切割机等设备进行。
最后一步是方管的包装。
经过切割后的方管需要进行包装,以便储存、运输和销售。
通常采用捆扎、打包或用塑料薄膜包装的方式进行。
冷轧方管的制造工艺流程包括原材料准备、热轧坯料加工、冷轧成型、矫直、切割和包装等环节。
每个环节都需要严格控制和操作,以确保方管的质量和尺寸符合要求。
通过科学的制造工艺流程,可以生产出高质量、精确尺寸的冷轧方管,满足不同领域的使用需求。
冷轧生产工艺流程
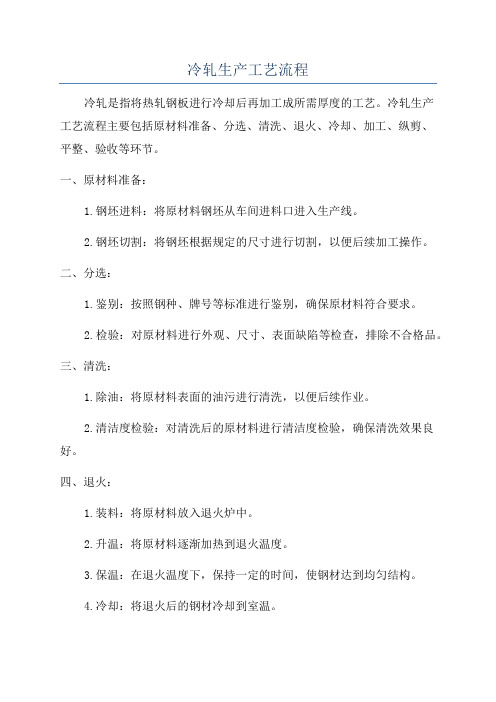
冷轧生产工艺流程冷轧是指将热轧钢板进行冷却后再加工成所需厚度的工艺。
冷轧生产工艺流程主要包括原材料准备、分选、清洗、退火、冷却、加工、纵剪、平整、验收等环节。
一、原材料准备:1.钢坯进料:将原材料钢坯从车间进料口进入生产线。
2.钢坯切割:将钢坯根据规定的尺寸进行切割,以便后续加工操作。
二、分选:1.鉴别:按照钢种、牌号等标准进行鉴别,确保原材料符合要求。
2.检验:对原材料进行外观、尺寸、表面缺陷等检查,排除不合格品。
三、清洗:1.除油:将原材料表面的油污进行清洗,以便后续作业。
2.清洁度检验:对清洗后的原材料进行清洁度检验,确保清洗效果良好。
四、退火:1.装料:将原材料放入退火炉中。
2.升温:将原材料逐渐加热到退火温度。
3.保温:在退火温度下,保持一定的时间,使钢材达到均匀结构。
4.冷却:将退火后的钢材冷却到室温。
五、冷却:1.钢材经过冷却装置,将温度降低到加工所需温度。
2.冷却后的钢材具有较高硬度,适合进行下一步的加工操作。
六、加工:1.热轧压下:将冷却后的钢材送入压下机,通过挤压使钢材变形,达到所需的厚度。
2.冷轧压下:将热轧后的钢材放入冷轧机中,通过辊压使钢材进一步压下,得到更薄的钢板。
3.冷轧拉拔:将冷轧后的钢板放入拉拔机中,通过拉拔使钢板变得更加平整、光滑。
七、纵剪:1.将拉拔后的钢板按照所需长度进行切割,得到相应长度的钢条。
八、平整:1.将剪切后的钢条放入平整机中,通过辊压使钢条恢复到平整状态。
九、验收:1.对平整后的钢条进行检查,确保外观质量无缺陷。
2.对尺寸进行测量,确保符合规定的要求。
3.对硬度进行测试,以检查加工效果和质量。
综上所述,冷轧生产工艺流程包括原材料准备、分选、清洗、退火、冷却、加工、纵剪、平整和验收等环节,通过对原材料的处理和加工操作,最终得到所需的厚度、尺寸和质量满足要求的冷轧钢板。
冷轧生产:纵、横剪
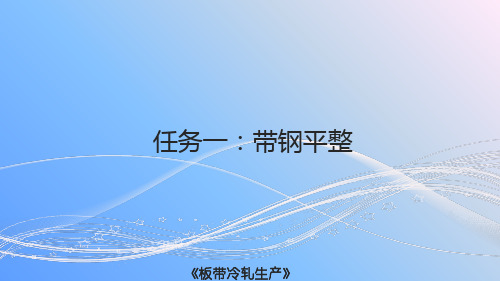
《板带冷轧生产》
带钢纵、横剪
一、横剪 横剪机组是把平整后的钢带剪切成定尺长度的钢板,经矫直和涂油,堆 垛成一定质量的板垛。
带钢纵、横剪
横剪机组生产工艺流程: 上卷→开卷→切边→打印→测厚→飞剪剪切→矫直→质量检查→涂油→分选 →堆垛→辊道输出。
图130 横剪机组示意图
1-上卷小车;2-开卷机;3-转向夹送辊;4-圆盘剪;5-废边卷取机;6-打印机;7-活套;8-飞剪;9-皮带; 10-矫直机;11-涂油机;12-分选皮带;13-下部磁力皮带;14-上部磁力皮带;15-叠瓦皮带;16-堆垛皮带;
17-次品堆垛台;18-优质板堆垛台
带钢纵、横剪
二、纵剪重卷 纵剪重卷,又称分卷,它的作用是把平整后带钢分切为各种宽度和单重的 带钢卷。
带钢纵、横剪
➢ 生产方法: 重卷生产有单卷生产和连续生产两种方式。
➢ 单卷生产的工艺流程: 上卷→开卷→打印→切➢ 连续生产的工艺流程: 上卷→开卷→切边→去毛刺→飞剪切头尾→焊接→拉弯矫直→打印→涂油 →分卷→卷取→捆扎。
带钢纵、横剪
图131 纵剪重卷机组示意图
1-开卷机;2-打印机;3-圆盘剪;4-活套装置; 5-压板;6-制动辊;7-液压横切剪;8-涂油机导向辊;9-卷取机
带钢纵、横剪
图132 重卷机组示意图
1-开卷机;2-圆盘剪;3-去毛刺机;4-飞剪;5-垛板台;6-焊机; 7-拉弯矫直机;8-打印机;9-涂油机;10-横切剪;11-转向夹送辊;12-卷取机
冷轧工艺流程
冷轧工艺流程冷轧工艺流程是将热轧钢卷经过冷处理工艺加工成冷轧钢卷的过程。
下面是一个典型的冷轧工艺流程。
首先,原料是热轧钢卷,它们被运输到冷轧车间,然后通过起重机将热轧钢卷吊装到待切割机上。
待切割机会根据客户的要求将热轧钢卷切割成合适的宽度。
接下来,切割后的热轧钢卷被送入洗涤机中进行洗涤处理,以去除钢卷表面的杂质和污垢。
然后钢卷经过除鳞机的除鳞处理,去除表面的氧化铁皮。
然后是酸洗工艺,将钢卷浸入酸液中,以去除表面的氧化物。
酸洗的关键是控制酸液的浓度和温度,以确保去除氧化物的同时不会对钢卷造成损害。
酸洗后,钢卷通过洗涤机进行冲洗,以去除残留的酸液。
在酸洗和冲洗之后,热轧钢卷需要进行退火处理。
退火的目的是恢复钢材的塑性和韧性,提高冷轧的成形性能。
通常采用间歇式退火工艺,将钢卷放入退火炉中加热到一定温度保温一段时间,然后再通过冷却装置快速冷却至室温。
退火后的钢卷进入轧机,开始冷轧加工。
冷轧是通过轧机将钢卷不断变形,减小其断面尺寸。
一般采用多道次轧制的工艺,每一道次轧制都会使钢卷的厚度减小一定的比例。
同时,通过涂油机将油剂涂在钢卷表面,以减小表面的摩擦力,减少表面的磨损。
最后,冷轧钢卷经过纵剪机进行纵向切割,将宽度合适的冷轧板卷切割成长度适中的冷轧板。
然后经过横剪机进行横向切割,得到客户所需尺寸的冷轧钢板。
整个冷轧工艺流程包括切割、洗涤、除鳞、酸洗、退火、冷轧和切割等多个环节。
每个环节都需要严格控制参数,以确保最终产品的质量符合要求。
通过冷轧工艺,热轧钢卷可以得到更好的表面质量、尺寸精度和机械性能,满足客户对冷轧钢板的需求。
冷轧生产线的工艺流程
说道冷轧产品,相信很多人都不会陌生,但说到冷轧生产线的具体工艺流程,很多人确是知之甚少,因此,为使大家对此有进一步的了解,现整理了以下具体的工艺流程,以供大家了解。
1.立式上料圆圈钢筋经上料架进行上料,换卷时,对原料进行对焊作业。
2.除锈轧制的钢筋经过此设备产生弯曲变形及拉直,使表面氧化皮脱离,提高产品的性能及外观质量。
3.一道轧对钢筋进行第一道轧制,将钢筋减经轧扁,是钢筋成型的前道工序。
4.二道轧目的使钢筋在此工序成型,轧制成符合要求的带肋钢筋。
5.分卷剪按产品要求重量,根据理论长度,进行分卷剪切.6.热处理对带助钢筋回火处理,提高延性及综合机械性能,打外线测温控制。
7.测量直径检测轧制成型的钢筋直径,控制钢筋直径在要求的范围内。
8.矫直测长对成型的带肋钢筋进行矫直并测量长度。
9.收线将直条钢筋收卷成要求的盘卷,两台收线机替运行,连续生产.10.翻转由运卷机械手将收好的盘卷爪抓至翻专台,并翻转90°.11.打包由运卷机械手将盘卷运至打包站,进行捆扎打包。
12.入库由智能系统将盘卷运至卸卷位,实现产品入库管理。
以上就是冷轧生产线有关工艺流程的一些简单介绍,当然,除了以上工艺流程外,在生产一些特殊产品时还有各自的特殊工序。
如轧制硅钢板时,在冷轧前要进行脱碳退火,轧后要进行涂膜、高温退火、拉伸矫直(见张力矫直)与回火等。
河南金迪是专业生产成套冷轧设备的厂家,生产高、中、低速成套冷轧机,轧制CRB600H,CRB800H达到国家新标准,适用于楼层建筑、高铁、桥梁、隧道、高速公路,市场前景应用广阔。
远程全智能控制,大型线速达到600--1000米/分。
终身技术支持,可根据客户本地,钢筋的规格、实际应用情况量身定做。
冷轧钢板生产工艺流程
冷轧钢板生产工艺流程
一、原料准备
冷轧钢板生产的第一个环节是原料准备。
这一步骤包括检查原料钢卷的质量,确认其化学成分、厚度、宽度等参数符合生产要求。
同时,对钢卷进行表面检查,确保无明显的划痕、锈迹或其他缺陷。
对于不合格的原料,需要进行处理或替换。
二、酸洗
原料准备好后,进入酸洗环节。
酸洗的目的是去除钢板表面的氧化铁皮,以利于后续加工。
酸洗过程中,使用酸性溶液对钢板表面进行浸泡或擦刷,然后通过冲洗和中和去除剩余的酸和氧化铁皮。
三、冷轧
酸洗后的钢板进入冷轧环节。
冷轧是在室温下,通过压轧的方式使钢板厚度减薄、表面光洁。
根据产品规格和要求,冷轧过程中需要进行多道次压轧,每次压轧后都需要进行矫直和冷却。
四、退火
冷轧后的钢板需要经过退火处理。
退火是为了消除轧制过程中产生的内应力,改善钢板塑性,使其更适合后续加工。
退火过程中,钢板在适宜的温度和气氛中进行加热和保温,然后缓慢冷却至室温。
五、精整
退火后的钢板进行精整处理。
精整包括平整、剪切、冲压等步骤,目的是进一步提高钢板表面质量,减小不平整度,并使其尺寸符合最终产品要求。
六、质量检测
在生产过程中的各个阶段,都需要进行严格的质量检测。
质量检测包括化学成分分析、物理性能测试、表面质量检查等,以确保最终产品的质量和性能符合
标准要求。
七、存储与运输
最后,经过质量检测合格的冷轧钢板需要进行妥善的存储与运输。
在存储过程中,要避免钢板受到潮湿、锈蚀等影响。
在运输过程中,要确保钢板不会受到损坏或划伤。
冷轧不锈钢工艺流程
冷轧不锈钢工艺流程一、引言冷轧不锈钢是一种常见的金属材料,广泛应用于建筑、制造业和家居装饰等领域。
本文将介绍冷轧不锈钢的工艺流程,包括原材料准备、轧制过程、表面处理和质检等环节。
二、原材料准备冷轧不锈钢的原材料主要是不锈钢卷材,其成分包括铁、铬、镍等元素。
在工艺流程开始前,需要对原材料进行检验和筛选,确保其质量符合要求。
同时,还需要对原材料进行预处理,如去除表面的油污和杂质,以保证后续工艺的顺利进行。
三、轧制过程1. 热轧:首先,将不锈钢卷材加热至一定温度,然后通过轧机进行轧制。
热轧可以使不锈钢卷材变得更加柔软,提高其延展性和塑性,同时也能改善其表面质量。
2. 冷轧:经过热轧后的不锈钢卷材需要进行冷轧处理。
冷轧是指将不锈钢卷材在室温下通过轧机进行轧制。
冷轧可以进一步提高不锈钢的硬度和强度,同时使其表面更加光滑。
四、表面处理冷轧不锈钢在轧制过程中可能会产生一些表面缺陷,如氧化皮、划痕等。
为了提高不锈钢的表面质量,需要进行表面处理。
常见的表面处理方法包括酸洗、抛光和喷砂等。
酸洗可以去除不锈钢表面的氧化皮和污垢,抛光可以使其表面更加光滑,喷砂可以增加其表面粗糙度。
五、质检在冷轧不锈钢的工艺流程中,质检是一个非常重要的环节。
质检的目的是确保不锈钢的质量符合标准要求。
质检包括外观检查、尺寸测量、化学成分分析和力学性能测试等。
只有通过质检合格的不锈钢才能进入下一个生产环节或出厂销售。
六、总结冷轧不锈钢工艺流程包括原材料准备、轧制过程、表面处理和质检等环节。
通过对不锈钢卷材的加工和处理,可以得到质量优良、表面光滑的冷轧不锈钢产品。
这些产品广泛应用于各个领域,为人们的生活和工作提供了便利。
在未来,随着技术的不断进步,冷轧不锈钢的工艺流程也将不断完善,为社会经济的发展做出更大的贡献。